Have you ever dreamt of building intricate metal objects straight out of a digital file? Well, that dream is now a reality with the advent of Tecnologia de impressão 3D SLM. Imagine skipping traditional metalworking methods like casting, machining, and welding, and instead, creating complex, high-performance metal parts layer by layer using a laser beam. Sounds like science fiction, right? But SLM is rapidly transforming the manufacturing landscape, revolutionizing how we design and produce everything from lightweight aerospace components to intricate medical implants.
Introduction to Tecnologia de impressão 3D SLM
SLM, also known as Direct Metal Laser Sintering (DMLS), belongs to a family of 3D printing processes called Powder Bed Fusion (PBF). Unlike filament-based 3D printing for plastics, SLM utilizes a bed of fine metal powder. A high-powered laser beam selectively melts the powder particles together, following a digital blueprint layer by layer, until the entire 3D object is built.
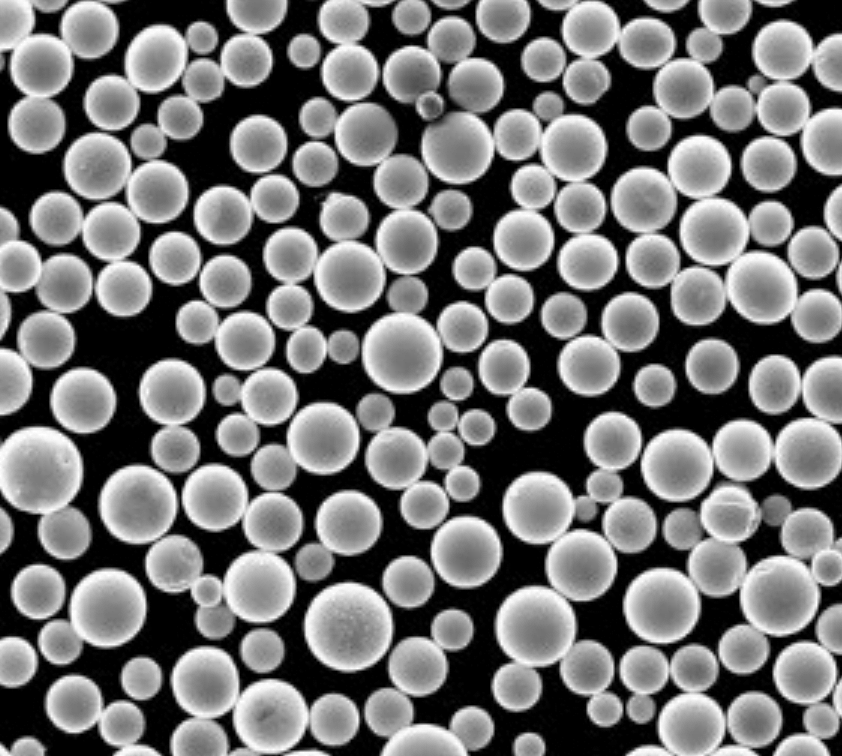
O princípio de Tecnologia de impressão 3D SLM
Here’s a breakdown of the magic that happens inside an SLM 3D printer:
- Data Slicing: The first step involves slicing a 3D CAD model into incredibly thin layers, typically ranging from 20 to 100 micrometers thick. Each layer represents a 2D cross-section of the final object.
- Powder Bed Preparation: A thin layer of metal powder is spread evenly across a platform using a blade or roller mechanism. This layer thickness corresponds to the slice thickness from the CAD model.
- Laser Melting: A high-powered laser beam scans the powder bed according to the 2D data for each layer. The laser melts the powder particles in designated areas, fusing them together to create the desired geometry.
- Layer by Layer Creation: After melting, the platform lowers by one layer thickness, and a new layer of powder is deposited. The laser then repeats the melting process on this new layer, fusing it to the previous one. This cycle continues until the entire 3D object is built, layer by layer.
- Pós-processamento: Once the printing is complete, the build platform is removed from the machine. The printed part may require support structures for removal, which are then carefully removed. Depending on the application, the part may also undergo additional finishing processes like heat treatment or machining for optimal surface quality and dimensional accuracy.
The Advantages of SLM 3D Printing Technology
SLM offers several compelling advantages over traditional metalworking methods:
- Liberdade de conceção: Unlike traditional methods limited by subtractive processes (removing material), SLM allows for the creation of complex geometries with intricate internal features and lightweight lattice structures. This opens doors for innovative and highly functional designs.
- High-Performance Parts: SLM produces near-net-shape, fully dense metal parts with excellent mechanical properties comparable to wrought metals. This makes them ideal for demanding applications where strength, weight, and performance are critical.
- Rapid Prototyping and Customization: SLM allows for the quick production of functional prototypes, accelerating the design and development cycle. Additionally, it enables on-demand and customized metal parts, perfect for low-volume production needs.
- Eficiência do material: SLM utilizes only the necessary amount of metal powder, minimizing waste compared to subtractive processes. Un-melted powder can often be recycled and reused, further enhancing resource efficiency.
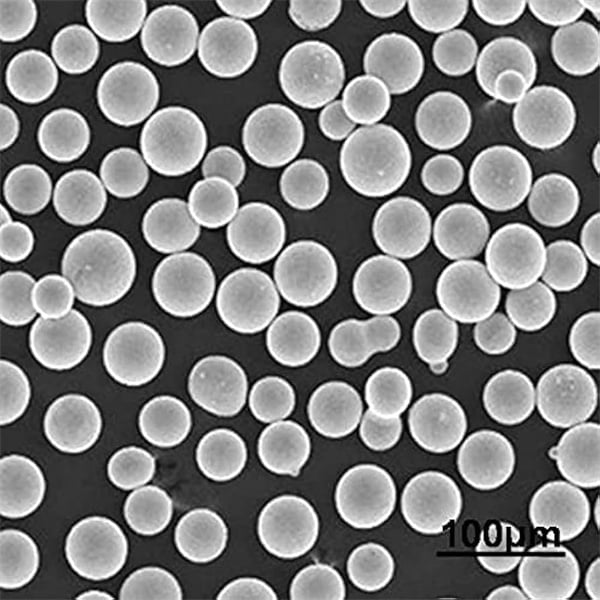
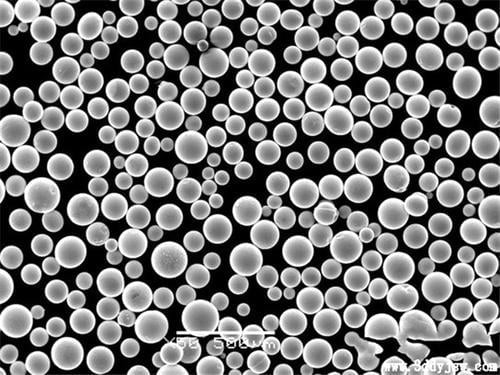
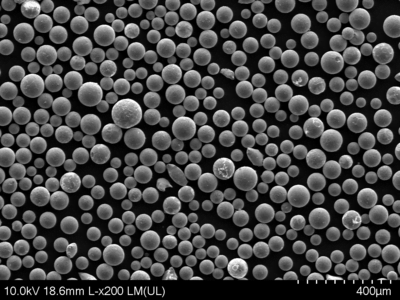
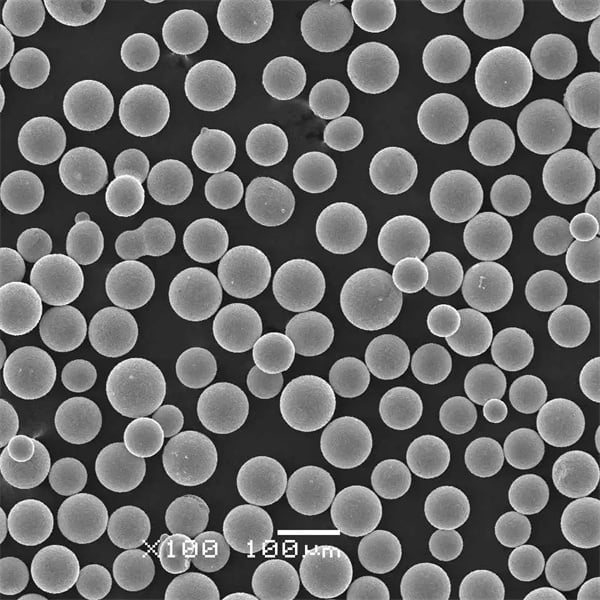
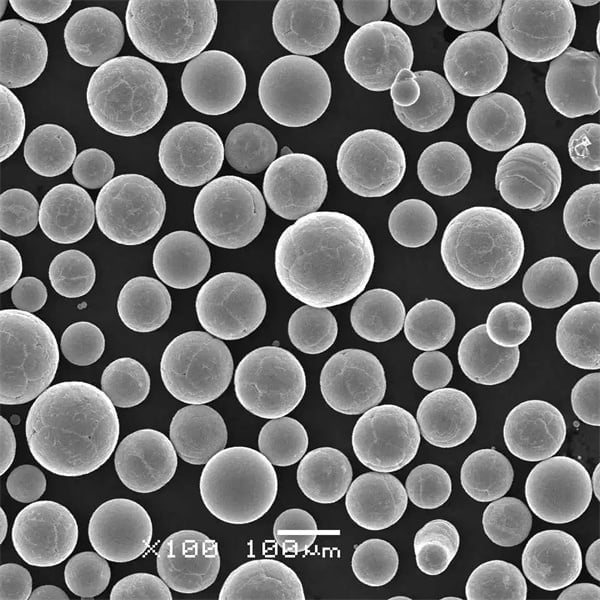
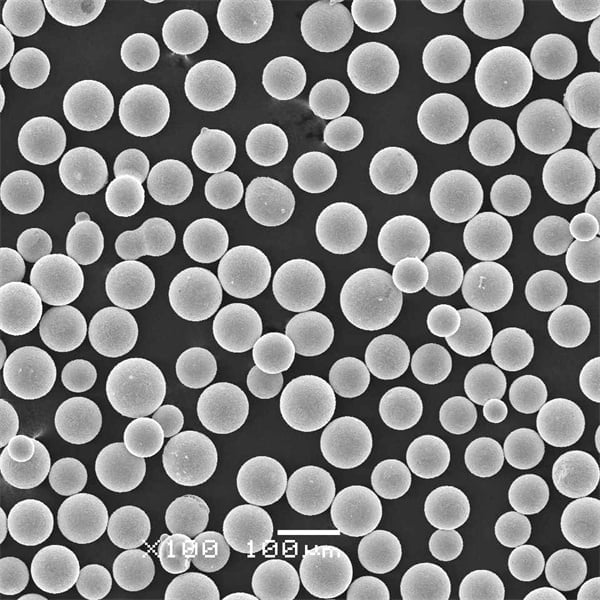
Aplicações de Tecnologia de impressão 3D SLM
SLM’s capabilities are making waves across various industries:
- Aeroespacial: The ability to create lightweight, high-strength components like turbine blades and engine brackets makes SLM a game-changer in aerospace, leading to fuel efficiency improvements and performance optimization.
- Médica: SLM is revolutionizing medical device manufacturing by enabling the creation of customized implants like prosthetics and dental bridges with excellent biocompatibility and precise fit.
- Automotivo: SLM is paving the way for lighter, stronger car parts like gear housings and brake calipers, contributing to improved fuel efficiency and driving performance.
- Bens de consumo: SLM is finding its way into the production of high-end consumer goods like customized jewelry, sports equipment, and even bike frames, offering unique design possibilities and exceptional durability.
The Future Development Trends of SLM 3D Printing Technology
The future of SLM is bright, with ongoing research and development pushing the boundaries of this technology:
- Multi-Laser Systems: Machines equipped with multiple lasers are being developed to increase printing speed and productivity, making SLM more cost-competitive for larger-scale production runs. Imagine churning out complex metal parts at a significantly faster pace, opening doors for wider adoption across industries.
- Materiais avançados: Research is ongoing to expand the range of materials compatible with SLM. This includes exploring new metal alloys with even higher strength-to-weight ratios, improved corrosion resistance, and biocompatibility for advanced medical applications. Think of crafting medical implants that perfectly match a patient’s bone structure or creating aerospace components that can withstand extreme temperatures and harsh environments.
- Avanços de software: The development of more sophisticated software for SLM is crucial. This includes improved simulation tools for predicting build behavior, minimizing distortion, and optimizing support structures. Additionally, advancements in design software specifically tailored for SLM can further unlock the potential for creating intricate and highly functional metal parts.
- Sustainability Considerations: The environmental impact of SLM is a growing focus. Research is underway to develop more efficient powder handling systems and recycling processes to minimize waste and resource consumption. Imagine a future where SLM becomes an even more sustainable manufacturing option, contributing to a circular economy.
Desafios e considerações para Tecnologia de impressão 3D SLM
While SLM offers incredible potential, there are challenges to consider:
- Custo elevado: SLM machines and metal powders can be expensive, making this technology less accessible for smaller companies or prototyping applications compared to traditional methods. As the technology matures and adoption widens, we can expect a decrease in costs, but for now, it’s a significant investment.
- Machine Complexity: Operating and maintaining SLM machines requires skilled personnel with a deep understanding of the technology and metalworking principles. This can be a hurdle for companies looking to integrate SLM into their production lines.
- Rugosidade da superfície: SLM-printed parts can exhibit a slightly rough surface finish compared to traditionally machined parts. While post-processing techniques can improve surface quality, it adds to the overall production time and cost.
- Limitações de tamanho da peça: Current SLM machines have limitations on the size of parts they can produce. While advancements are being made, very large metal components might still be better suited for traditional manufacturing methods.
Choosing Between SLM and Other Metalworking Techniques
The decision to use SLM depends on several factors:
- Parte Complexidade: For intricate geometries with internal features, SLM offers unparalleled design freedom compared to subtractive processes like machining.
- Volume de produção: For high-volume production runs, traditional methods like casting might be more cost-effective. However, SLM shines for low-volume, customized parts or rapid prototyping needs.
- Requisitos de material: The type of metal and its desired properties will influence the choice. SLM offers a growing range of materials, but traditional methods might still have a wider selection for specific applications.
- Desempenho da peça: Para aplicações que requerem peças leves e de alta resistência com geometrias complexas, a SLM é uma opção atraente. No entanto, para peças mais simples em que a resistência não é uma preocupação importante, os métodos tradicionais podem ser suficientes.
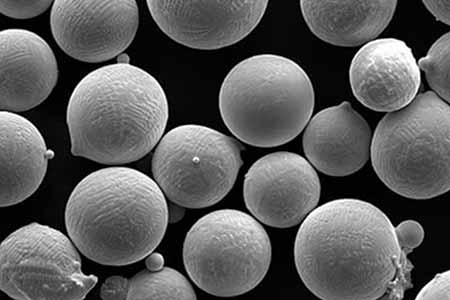
Perguntas Frequentes
Aqui estão algumas das perguntas mais comuns sobre a tecnologia SLM, respondidas de forma clara e concisa:
Questão | Resposta |
---|---|
Que tipos de metais podem ser utilizados na SLM? | Uma vasta gama de metais é compatível com a SLM, incluindo aço inoxidável, titânio, ligas de alumínio, ligas de níquel e até metais preciosos como o ouro e a platina. |
Qual é a resistência das peças impressas por SLM? | As peças impressas por SLM podem atingir excelentes propriedades mecânicas, comparáveis às dos metais forjados. A sua resistência depende do material escolhido, mas podem ser incrivelmente fortes e duradouras. |
A SLM é segura? | A impressão SLM envolve lasers de alta potência e pós metálicos, pelo que são essenciais precauções de segurança adequadas. Isto inclui a utilização de equipamento de proteção e a garantia de uma ventilação adequada para evitar a exposição a partículas de pó. |
Quais são as opções de acabamento de superfície para peças SLM? | As peças SLM podem ser pós-processadas com várias técnicas, como jato de areia, polimento e maquinagem, para obter o acabamento superficial e a precisão dimensional pretendidos. |
Como é que a SLM se compara a outras tecnologias de impressão 3D para metal? | Existem outros métodos de impressão 3D de metal, como o jato de aglutinante ou a deposição de metal. |
Sobre a 3DP mETAL
Categoria do produto
CONTACTE-NOS
Tem dúvidas ? Envie uma mensagem para nós agora mesmo! Após o recebimento de sua mensagem, nós processaremos sua solicitação com toda a equipe.