Imagine crafting complex, high-performance objects layer by layer, not through traditional subtractive manufacturing, but by meticulously adding material. This is the magic of Additive Manufacturing (AM), also known as 3D printing. But at the heart of this revolutionary technology lies a crucial ingredient: Additive Manufacturing Powders. These fine-grained particles, meticulously crafted from metals, polymers, and even ceramics, are the building blocks that bring 3D designs to life.
Pó para manufatura aditivas
Additive manufacturing powders come in a dazzling array of materials, each boasting unique properties that cater to specific applications. Let’s delve into the fascinating world of some of the most popular metal powders used in AM:
1. Titanium Powders (Ti-6Al-4V):
The undisputed champion of the AM metal powder arena, Titanium-6 Aluminum-4 Vanadium (Ti-6Al-4V) powder offers an unbeatable combination of strength, low weight, and excellent corrosion resistance. This makes it the go-to choice for demanding applications in the aerospace, medical, and automotive industries. Imagine crafting lightweight yet incredibly strong aircraft components, or creating biocompatible implants that seamlessly integrate with the human body – Ti-6Al-4V powder makes it possible.
2. Stainless Steel Powders (316L):
For applications that require exceptional resistance to rust and corrosion, 316L stainless steel powder reigns supreme. This versatile powder boasts superior mechanical properties and can withstand harsh environments, making it ideal for the marine, chemical processing, and construction industries. Think intricate components for ships that brave the salty seas, or durable pipes for chemical plants – 316L stainless steel powder ensures these creations can withstand the test of time.
3. Inconel Powders (IN625):
When the heat is on, literally, Inconel 625 (IN625) powder steps up to the challenge. This nickel-chromium-based superalloy powder thrives in extreme temperatures and harsh environments. Its exceptional heat resistance, oxidation resistance, and creep strength make it a favorite for aerospace, gas turbine, and power generation applications. Picture searing hot jet engine components or durable parts for power plants – IN625 powder ensures these creations can function flawlessly under immense thermal stress.
4. Aluminum Powders (AlSi10Mg):
For applications where lightweighting is paramount, Aluminum Silicon Magnesium (AlSi10Mg) powder shines. This aluminum alloy powder offers a favorable strength-to-weight ratio, making it ideal for the automotive and aerospace industries. Imagine crafting components for fuel-efficient cars or lightweight aircraft structures – AlSi10Mg powder helps reduce overall weight, leading to improved performance and fuel efficiency.
5. Cobalt Chrome Powders (CoCr):
Biocompatibility takes center stage with Cobalt-Chrome (CoCr) powder. This metal powder combination offers excellent corrosion resistance, wear resistance, and biocompatibility, making it a popular choice for medical and dental applications. Think long-lasting hip replacements or durable dental implants – CoCr powder ensures these medical marvels can integrate seamlessly with the human body and endure for years to come.
6. Nickel Powders:
Offering a balance of strength, ductility, and conductivity, pure nickel powder finds applications in various industries. Its excellent electrical conductivity makes it suitable for creating electrical components, while its ductility allows for intricate part geometries. Imagine crafting intricate electrodes or complex heat exchangers – nickel powder offers the versatility needed for such diverse applications.
7. Copper Powders:
Renowned for its exceptional thermal and electrical conductivity, copper powder is a natural fit for electronics and heat management applications. Think intricate heat sinks for electronics or efficient electrical components – copper powder ensures optimal heat dissipation and efficient current flow.
8. Tool Steel Powders:
For creating durable tools and wear-resistant components, tool steel powders come into play. These powders offer exceptional hardness, wear resistance, and toughness, making them ideal for crafting cutting tools, dies, and molds. Imagine long-lasting drill bits or durable molds for shaping plastic parts – tool steel powder ensures these creations can withstand heavy wear and tear.
9. Precious Metal Powders (Gold, Silver):
Beyond functional applications, Additive Manufacturing powders can cater to aesthetics as well. Precious metal powders like gold and silver open doors to creating intricate jewelry pieces and decorative objects. Imagine crafting a personalized gold ring with a complex design or a detailed silver figurine – precious metal powders allow for the creation of unique and beautiful objects.
10. Refractory Metal Powders (Tungsten, Tantalum):
For applications that demand exceptional high-temperature strength e resistance to molten metals, refractory metal powders like tungsten and tantalum take center stage. These powders boast incredibly high melting points and can withstand extreme temperatures, making them ideal for crucibles, furnace components, and welding electrodes. Imagine crafting crucibles that can hold molten steel or durable electrodes for high-temperature welding – refractory metal powders ensure these creations can function flawlessly in the hottest environments.
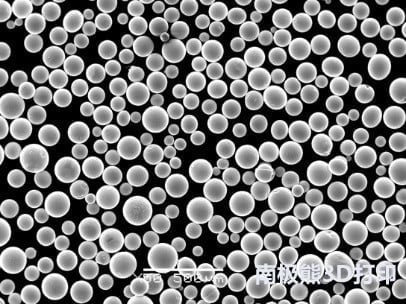
Properties and Applications
Beyond the specific metal powders, a deeper understanding of their properties and applications is crucial. Here’s a table summarizing some key aspects:
Pó metálico | Composição | Principais propriedades | APLICATIVOS |
---|---|---|---|
Titanium-6 Aluminum-4 Vanadium (Ti-6Al-4V) | Ti (base), Al (6%), V (4%) | High strength, low weight, excellent corrosion resistance | Aerospace components, medical implants, automotive parts |
Aço inoxidável (316L) | Fe (base), Cr (16-18%), Ni (10-14%), Mo (2-3%) | Excelente resistência à corrosão, boas propriedades mecânicas | Marine components, chemical processing equipment, construction parts |
Inconel 625 (IN625) | Ni (base), Cr (20-24%), Fe (balance), Mo (9%), Nb (3.15%) | Exceptional heat resistance, oxidation resistance, creep strength | Aerospace components, gas turbine parts, power generation equipment |
Aluminum Silicon Magnesium (AlSi10Mg) | Al (base), Si (9-13%), Mg (0.3-0.7%) | Favorable strength-to-weight ratio, good castability | Automotive components, aerospace structures, lightweight parts |
Cromo Cobalto (CoCr) | Co (base), Cr (27-30%) | Excellent biocompatibility, corrosion resistance, wear resistance | Medical implants (hip replacements, dental implants) |
Níquel | Ni (base) | Strength, ductility, good electrical conductivity | Electrical components, heat exchangers, intricate parts |
Cobre | Cu (base) | Condutividade térmica e elétrica excelentes | Heat sinks, electrical components, intricate heat management systems |
Aço para ferramentas | Varies depending on type (e.g., tungsten, molybdenum) | Alta dureza, resistência ao desgaste, tenacidade | Cutting tools, dies, molds for shaping plastic parts |
Precious Metals (Gold, Silver) | Au (Gold), Ag (Silver) | Malleability, ductility, high aesthetic value | Jewelry making, decorative objects, intricate artistic creations |
Refractory Metals (Tungsten, Tantalum) | W (Tungsten), Ta (Tantalum) | Very high melting points, exceptional high-temperature strength | Crucibles for molten metals, furnace components, welding electrodes |
Choosing the Right Powder: A Balancing Act
Selecting the optimal metal powder for your AM project requires careful consideration of several factors. Here’s a breakdown of some key aspects to ponder:
- Propriedades desejadas: What are the critical properties your final product needs? Strength, weight, corrosion resistance, or something else entirely? Identifying these needs will guide your powder selection.
- Requisitos de inscrição: What will the final product be used for? Understanding the application’s demands will help you narrow down powder choices.
- Compatibility with AM Process: Different AM processes have varying powder requirements. Ensure the chosen powder is compatible with your specific AM technology (e.g., laser melting, electron beam melting).
- Cost and Availability: Metal powders can vary significantly in cost and availability. Factor in both aspects when making your decision.
Advantages and Limitations of Additive Manufacturing Powders
Like any technology, Additive Manufacturing powders come with their own set of advantages and limitations. Let’s explore both sides of the coin:
Vantagens:
- Liberdade de design: AM powders enable the creation of complex geometries that are often impossible with traditional manufacturing methods.
- Leveza: Certain powders like aluminum alloys can significantly reduce the weight of final parts compared to conventional methods.
- Eficiência do material: AM processes minimize material waste compared to subtractive manufacturing techniques.
- Performance Optimization: Parts can be designed with specific properties and internal structures thanks to the flexibility of powder selection.
- Personalização em massa: AM allows for the creation of customized parts in small batches, ideal for prototyping and niche applications.
Limitações:
- Custo: Metal powders can be expensive, and AM processes themselves can be more costly compared to traditional manufacturing for high-volume production.
- Acabamento da superfície: AM-produced parts may require additional post-processing steps to achieve a desired surface finish.
- Limitações de tamanho da peça: Current AM technologies may have limitations on the size of parts that can be produced.
- Disponibilidade do material: Not all metals and alloys are readily available in powder form for AM applications.
- Complexidade do processo: Operating and maintaining AM equipment can require specialized skills and expertise.
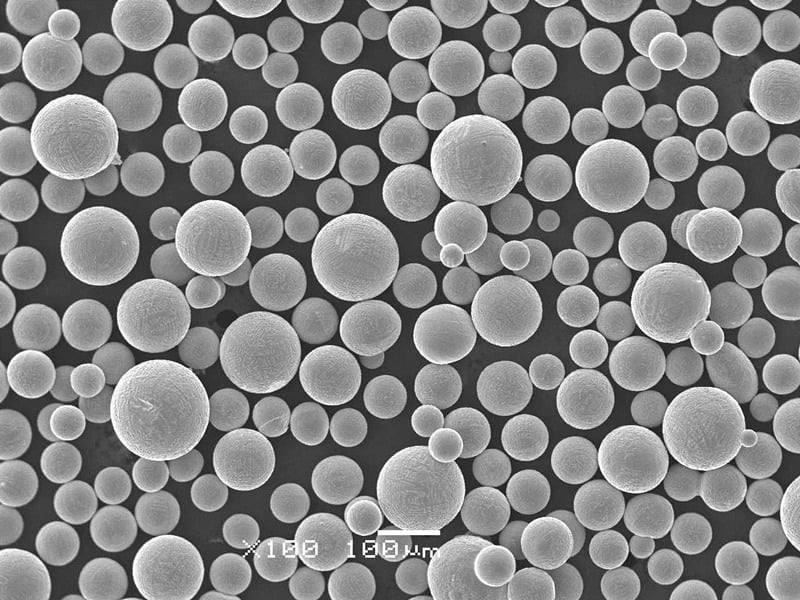
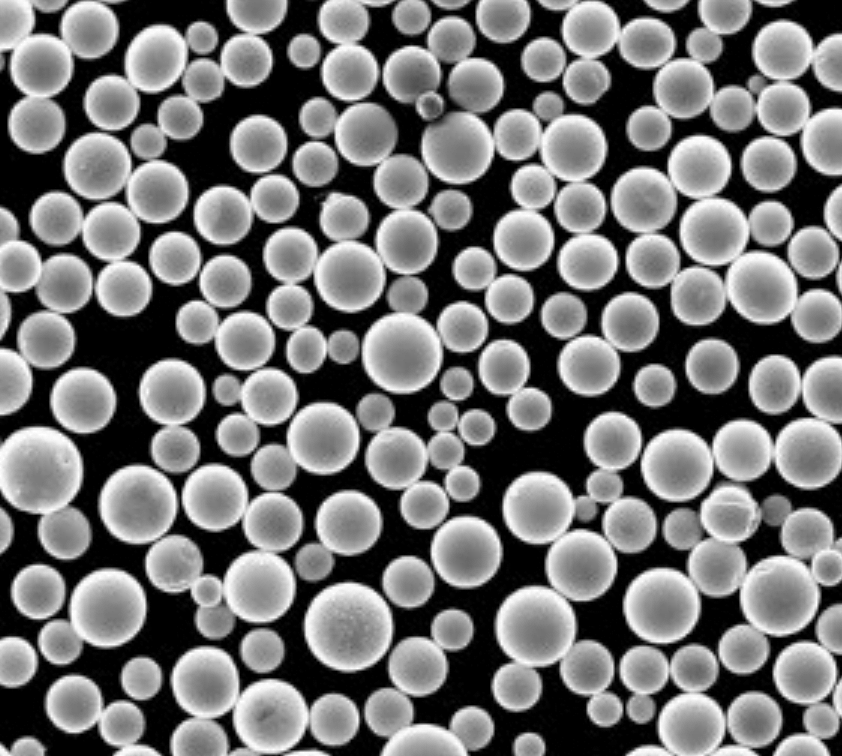
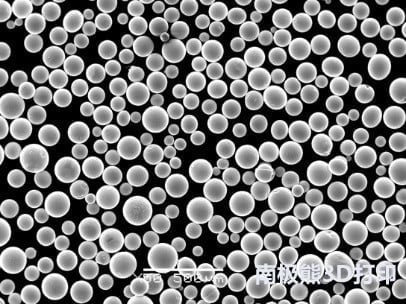
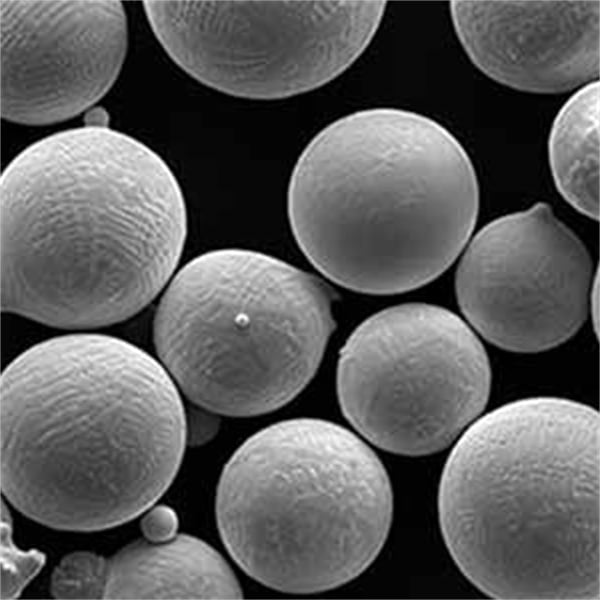
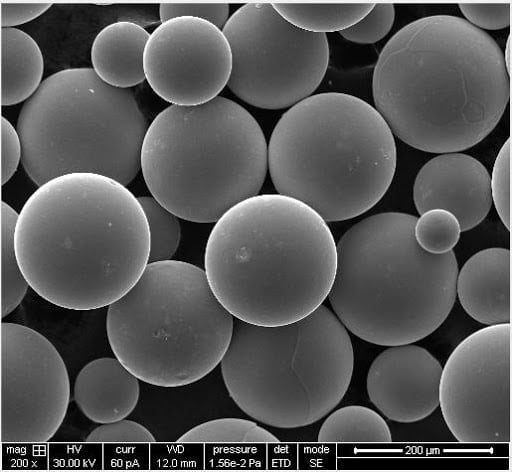
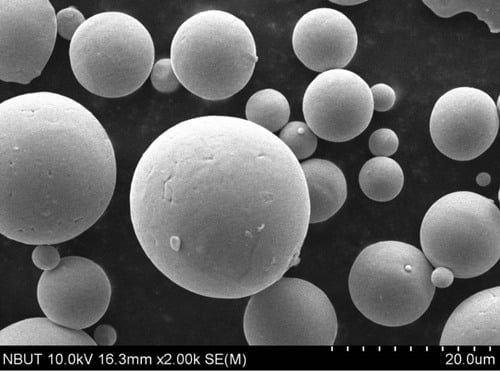
Additional Considerations for Success
While the choice of powder is crucial, it’s just one piece of the puzzle. Here are some additional factors to consider for a successful AM project:
- AM Machine Selection: Different AM machines have varying capabilities and limitations. Choose a machine that aligns with your project requirements and powder selection.
- Process Parameters: Optimizing the AM process parameters like laser power, scan speed, and layer thickness significantly impacts the final part’s properties.
- Post-processing Techniques: Depending on the application, post-processing steps like heat treatment, machining, and surface finishing may be necessary.
- Projeto para manufatura aditiva (DfAM): Designing parts specifically for AM can unlock the full potential of the technology, maximizing benefits and minimizing limitations.
The Future of Additive Manufacturing Powders: A World of Potential
The realm of Additive Manufacturing powders is constantly evolving. Here’s a glimpse into some exciting developments on the horizon:
- Development of New Powders: Researchers are continuously developing new metal powders with improved properties, including higher strength, better corrosion resistance, and even multi-material capabilities.
- Nanopowders: Powders with even finer particle sizes (nanoparticles) offer the potential for creating parts with exceptional mechanical properties and surface finishes.
- Recycled Powders: Sustainability is becoming a key focus. The development of efficient methods for recycling and reusing metal powders from AM processes will be crucial.
The Final Word: Unleashing the Potential of Pós para manufatura aditiva
Additive Manufacturing powders are the building blocks of a revolutionary technology. By understanding the different powder options, their properties, and the factors influencing successful AM projects, you can unlock the vast potential of this transformative technology. From creating lightweight and high-strength components to crafting intricate medical implants and personalized jewelry, Additive Manufacturing powders are pushing the boundaries of what’s possible, one layer at a time.
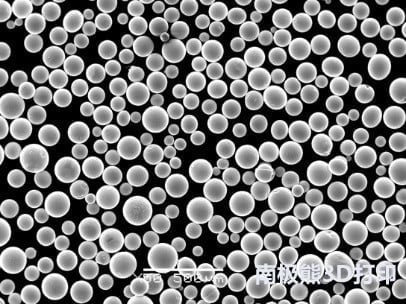
FAQ
Q: What are the different types of Additive Manufacturing powders?
A: Additive Manufacturing powders come in a vast array of materials, including metals, polymers, and even ceramics. This article focused on some of the most popular metal powders used in AM, including titanium, stainless steel, inconel, aluminum, and more.
Q: How are Additive Manufacturing powders made?
A: The specific manufacturing process for metal powders can vary depending on the material. Common methods include gas atomization, water atomization, and plasma atomization. These processes involve transforming molten metal into a fine mist that rapidly solidifies into tiny spherical particles.
Q: Are there any safety considerations when handling Additive Manufacturing powders?
A: Yes, some metal powders can be hazardous if inhaled. Proper safety protocols, including using personal protective equipment like respirators and working in well-ventilated areas, are essential when handling metal powders.
Q: What is the future of Additive Manufacturing powders?
A: The future of Additive Manufacturing powders is bright! We can expect to see the development of new powder materials with enhanced properties, the increased use of recycled powders for sustainability, and the exploration of even finer nanopowders for creating parts with exceptional characteristics.
Sobre o 3DP mETAL
Categoria do produto
ENTRE EM CONTATO
Alguma dúvida? Envie-nos uma mensagem agora! Após receber sua mensagem, processaremos sua solicitação com toda equipe.