Bi2O3 powder, also known as bismuth trioxide powder, is a unique material finding increasing use in the realm of Metal Injection Molding (MIM). Imagine crafting intricate, near-net-shape metallic components with the precision of plastic injection molding – that’s the power of MIM. And Bi2O3 powder plays a crucial role in this transformative technology.
This comprehensive guide delves deep into the world of Bi2O3 powder for MIM, exploring its properties, applications, advantages, limitations, and various commercially available models. Buckle up and get ready to dive into the fascinating world of MIM and the role Bi2O3 powder plays within it!
Understanding Bi2O3 Powder
Bi2O3 powder boasts a bright yellow hue and a chemical formula of Bi2O3, signifying a composition of two bismuth atoms bonded to three oxygen atoms. Think of it as tiny building blocks, ready to be assembled into complex metallic structures.
Here’s a table summarizing the key characteristics of Bi2iO3 powder:
Propriedade | Descrição |
---|---|
Fórmula química | Bi2O3 |
Aparência | Bright yellow powder |
Densidade | 9.32 g/cm³ |
Ponto de Fusão | 820 °C |
Ponto de ebulição | 1900 °C |
But what truly sets Bi2O3 powder apart is its ability to decompose during the MIM process. This decomposition plays a vital role in creating high-density, complex metallic parts.
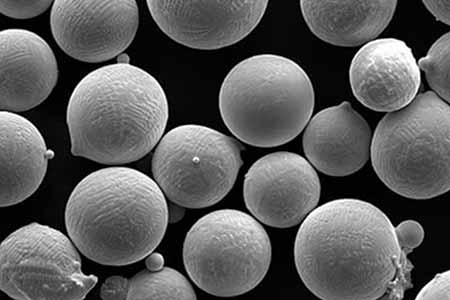
Como Bi2O3 Powder Makes it Happen
Metal Injection Molding (MIM) is a revolutionary manufacturing technique that bridges the gap between traditional metalworking and plastic injection molding. It allows for the production of intricate, near-net-shape metallic components with exceptional detail and dimensional accuracy.
Here’s a simplified breakdown of the MIM process:
- Powder Mixing: Bi2O3 powder is meticulously blended with fine metal powders and a binder system. The binder acts as a glue, holding the metal and Bi2O3 particles together during molding.
- Moldagem por injeção: The meticulously mixed feedstock is injected into a precisely designed mold cavity under high pressure. This step mirrors the process used in plastic injection molding.
- Desbobinamento: The binder is removed through a thermal or chemical debinding process. Imagine gently peeling away the glue, leaving behind a fragile metal skeleton.
- Sinterização: The debindered part undergoes a high-temperature sintering process. This critical step allows the metal particles to fuse together, densifying the structure and achieving the desired mechanical properties.
Now, let’s delve deeper into the magic of Bi2O3 powder. During sintering, Bi2O3 decomposes, leaving behind volatile bismuth oxide byproducts that escape the part. This decomposition creates tiny pores within the metal matrix, facilitating the escape of trapped binders and promoting better densification. Think of it as microscopic channels that allow the binder to escape, leading to a denser, stronger final product.
Applications of Bi2O3 Powder in MIM
Bi2O3 powder finds application in a diverse range of MIM products due to its unique properties. Here are some prominent examples:
- Electronic Components: Bi2O3 powder is used in the MIM production of electronic connectors, lead frames, and housings for various electronic devices. Its ability to create intricate shapes and achieve high density makes it ideal for these applications.
- Dispositivos médicos: The medical device industry leverages Bi2O3 powder for MIM production of surgical instruments, implants, and dental components. Its biocompatible nature (depending on the specific metal powder used) and ability to achieve intricate geometries make it a valuable asset.
- Aeroespacial e Defesa: The demanding aerospace and defense sectors utilize Bi2O3 powder for MIM production of lightweight, high-strength components like gears, blades, and engine parts. Its ability to create complex shapes with good mechanical properties makes it suitable for these critical applications.
- Automotive Parts: Bi2O3 powder contributes to the MIM production of complex automotive components like transmission parts, fuel injectors, and engine components. Its role in achieving high density and intricate shapes is crucial for these applications.
- Bens de consumo: Even everyday consumer goods can benefit from Bi203 powder in MIM. Think of intricate watch components, complex fasteners, and durable sporting goods components – Bi2O3 powder can play a role in their production.
As MIM technology continues to evolve, we can expect to see even more innovative applications for Bi2O3 powder emerge across various industries.
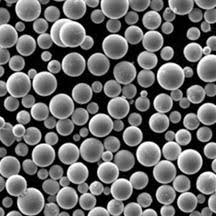
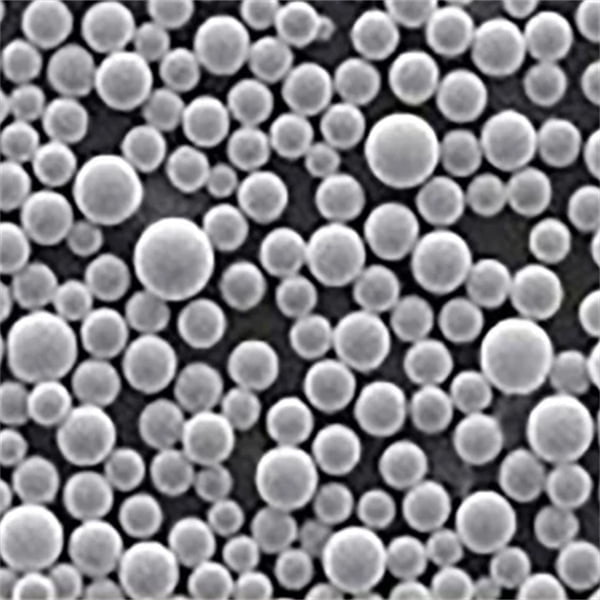
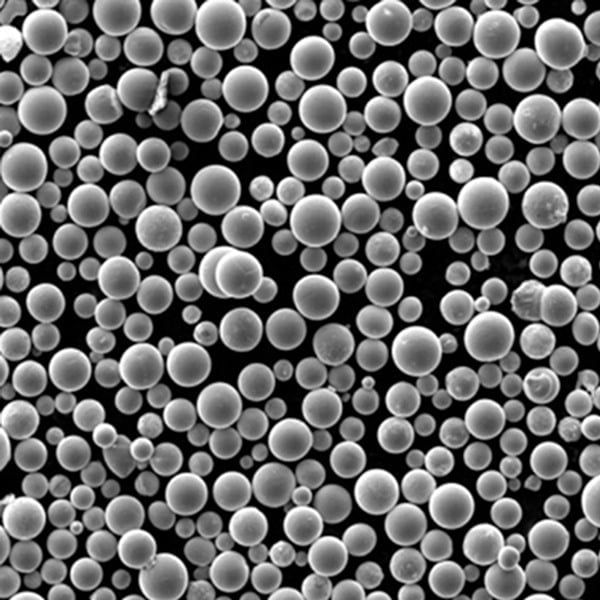
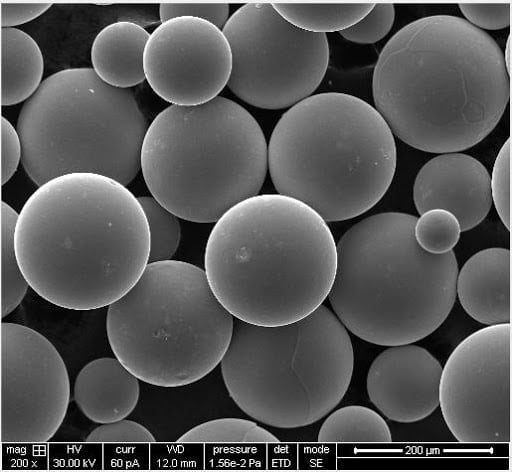
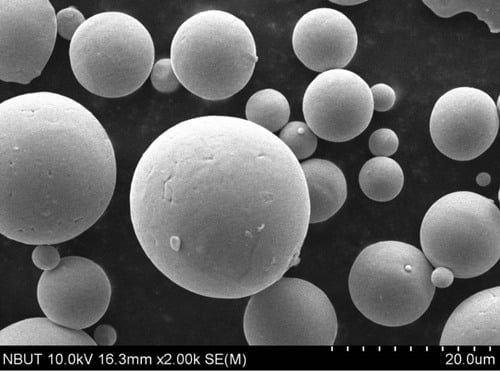
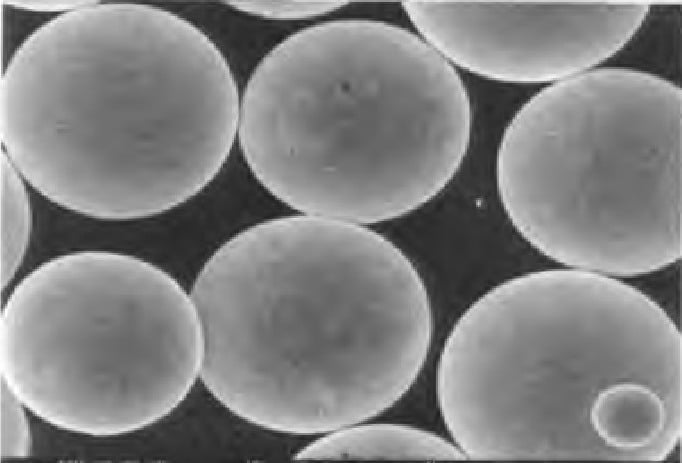
Commercially Available Bi2O3 Powder Modelos
Here’s a breakdown of some commercially available Bi2O3 powder models, highlighting their key features and potential applications:
Fabricante | Model Name | Descrição | APLICATIVOS |
---|---|---|---|
Elementos americanos | Bi2O3-10 | High purity (99.99%) Bi2O3 powder with a median particle size of 10 microns. Offers excellent thermal stability and good flowability for efficient MIM processing. | Ideal for various MIM applications requiring high density and dimensional accuracy, such as electronic components, medical devices, and aerospace parts. |
Alfa Aesar | 42404 | Electronic grade Bi2O3 powder with a purity of 99.995%. Features a controlled particle size distribution for consistent performance in MIM processes. | Well-suited for MIM production of electronic components that demand high purity and precise geometries, like connectors and lead frames. |
Sigma-Aldrich | 308077 | Reagent grade Bi2O3 powder with a purity of 99.5%. Offers a cost-effective option for less critical MIM applications where high purity is not a top priority. | Can be suitable for MIM production of automotive parts, consumer goods, and other applications where cost considerations play a role. |
Nanoscale Materials | US8002 | Nano sized Bi2O3 powder with a primary particle size of 50-100 nanometers. This ultrafine powder can enhance densification during MIM sintering, potentially leading to higher strength and improved mechanical properties. | Holds promise for MIM production of high-performance components demanding exceptional strength and dimensional accuracy, such as aerospace parts and medical implants. However, careful handling and processing techniques may be required due to the powder’s nanoscale nature. |
US Research Nanomaterials Inc. | US7034 | Bismuth (III) oxide powder with a surface area of 10-20 m²/g. The high surface area can promote faster decomposition during MIM sintering, potentially accelerating the debinding process. | May be advantageous for MIM applications where faster processing times are desired. Further research is needed to evaluate its impact on final part properties. |
Merck | 103621 | Bi2O3 powder with a purity exceeding 99.9%. Offered in various particle size options (e.g., <5 microns, 10-20 microns) to cater to specific MIM needs. | Provides flexibility for MIM applications requiring different particle size distributions. Finer powders can be beneficial for achieving intricate geometries, while coarser powders may offer better flowability for efficient molding. |
Cerac Inc. | B3007 | High-purity (99.95%) Bi2O3 powder specifically designed for MIM applications. Features a tightly controlled particle size distribution and excellent flow properties for consistent performance. | Caters specifically to the needs of MIM processes, potentially offering superior results compared to more general-purpose Bi2O3 powders. |
Suzhou Lvjia Speciality Materials | Bismuth Oxide Powder (Bi2O3) | Chinese manufacturer offering Bi2O3 powder with customizable purity and particle size options. May be a cost-effective alternative for specific MIM applications. | Provides a budget-friendly option for MIM production, but thorough quality control is essential to ensure consistent performance. |
Important Note: This table provides a general overview of some commercially available Bi2O3 powder models. It’s crucial to consult the specific manufacturer’s data sheets and technical specifications for detailed information on purity, particle size distribution, and other relevant properties before selecting a Bi2O3 powder for your specific MIM application.
Vantagens e limitações do Bi2O3 Powder in MIM
Bi2O3 powder offers several advantages for MIM applications:
- Promotes Densification: The decomposition of Bi2O3 during sintering creates pores that facilitate binder removal, leading to a denser final product with improved mechanical properties.
- Enhanced Flowability: Bi2O3 powder generally exhibits good flowability, which aids in uniform powder distribution during injection molding, contributing to dimensional accuracy and repeatability in the final parts.
- Custo-benefício: Compared to some other debinding additives, Bi2O3 powder can be a cost-effective option, especially for non-critical MIM applications.
However, there are also limitations to consider:
- Potential for Bismuth Contamination: Residual bismuth oxide byproducts from Bi2O3 decomposition may remain in the final MIM part, potentially affecting electrical conductivity or other properties depending on the specific application.
- Process Optimization Required: The optimal amount and particle size of Bi2O3 powder need to be carefully determined for each MIM application to achieve the desired balance between densification and minimal residual bismuth content.
- Environmental Considerations: Bi2O3 decomposition during MIM sintering generates volatile bismuth oxide byproducts. Proper ventilation and exhaust treatment systems are crucial to comply with environmental regulations and worker safety standards.
Comparing Bi2O3 Powder with Alternative Debinding Techniques
While Bi2O3 powder is a popular choice for MIM debinding, it’s not the only option. Here’s a brief comparison with some alternative methods:
Thermal Debinding:
- Descrição: This method relies on controlled heating to remove the binder from the MIM feedstock. Different polymers with varying thermal decomposition profiles can be used as binders.
Vantagens:
- Relatively simple and well-established process.
- No additional debinding agent (like Bi2O3 powder) required, potentially reducing costs.
Limitações:
- Precise temperature control is critical to avoid premature binder decomposition or part distortion.
- May not be suitable for all binder materials or complex geometries where trapped binders are difficult to remove.
Chemical Debinding:
- Descrição: This approach utilizes specific chemical solvents to dissolve the binder from the MIM feedstock.
Vantagens:
- Can be effective for removing binders that are difficult to decompose thermally.
- May offer better control over the debinding process compared to thermal methods.
Limitações:
- Requires careful selection of solvents to ensure compatibility with the metal powder and minimal environmental impact.
- Proper disposal of spent solvents is crucial to comply with environmental regulations.
Water-Soluble Binders:
- Descrição: This method utilizes water-soluble binders that can be removed from the MIM feedstock through a water leaching process.
Vantagens:
- Environmentally friendly approach as water is the primary debinding agent.
- May simplify waste disposal compared to other debinding methods.
Limitações:
- Limited selection of water-soluble binders with good performance for MIM applications.
- Water leaching may not be suitable for all geometries, particularly those with internal channels or complex features.
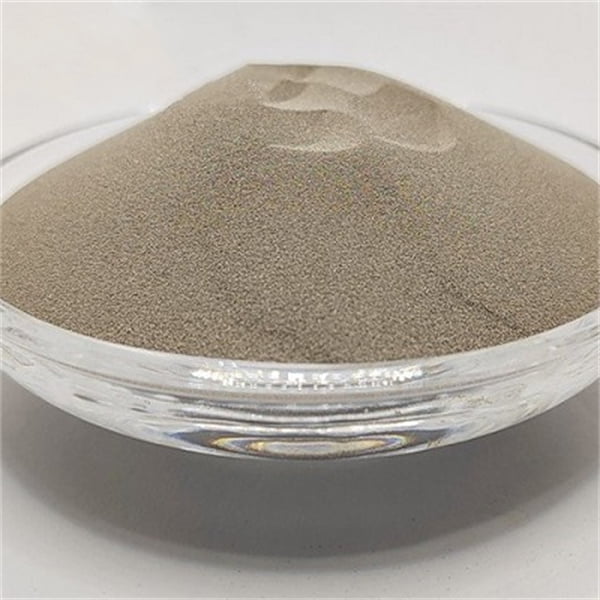
Choosing the Right Debinding Technique
The optimal debinding technique for a specific MIM application depends on various factors, including:
- Metal powder material: Different metal powders may exhibit varying compatibility with different debinding methods.
- Binder type: The selection of the debinding technique hinges on the properties and decomposition behavior of the chosen binder.
- Geometria da peça: Complex geometries may necessitate specific debinding approaches to ensure complete binder removal.
- Regulamentações ambientais: Compliance with environmental regulations regarding solvent emissions and waste disposal is essential.
Bi2O3 powder offers a versatile and cost-effective debinding solution for various MIM applications. However, it’s crucial to weigh its advantages and limitations against alternative methods to select the most suitable approach for your specific needs.
FAQ
Q: What is the typical purity level of Bi2O3 powder used in MIM?
A: Bi2O3 powder for MIM applications typically boasts a high purity level, often exceeding 99.5%. Some manufacturers offer even higher purity grades (e.g., 99.99%) for specific applications where minimal contamination is critical.
Q: Does particle size of Bi2O3 powder impact the MIM process?
A: Yes, particle size plays a crucial role. Finer Bi2O3 powders can enhance densification during sintering but may also affect flowability during injection molding. Conversely, coarser powders may offer better flowability but potentially hinder densification. Selecting the optimal particle size distribution depends on the specific MIM application and desired final part properties.
Q: Are there any safety considerations when handling Bi2O3 powder?
A: Bi2O3 powder is generally considered non-hazardous. However, it’s recommended to follow proper handling procedures to minimize inhalation risks. Wearing dust masks and safety glasses during handling and processing is advisable.
Q: Can Bi2O3 powder be recycled or reused in MIM?
A: The feasibility of recycling Bi2O3 powder recovered from the MIM process depends on various factors, including the level of contamination and the specific recycling technology employed. Further research is needed to establish efficient and cost-effective Bi2O3 powder recycling methods for MIM applications.
Sobre o 3DP mETAL
Categoria do produto
ENTRE EM CONTATO
Alguma dúvida? Envie-nos uma mensagem agora! Após receber sua mensagem, processaremos sua solicitação com toda equipe.