Alguma vez você já sonhou em construir algo camada por camada, com metal fundido como tinta e um braço robótico como pincel? Pois bem, Deposição de energia direcionada (DED) torna essa ficção científica uma realidade. O DED é um processo revolucionário de impressão 3D que está transformando a fabricação, permitindo a criação de estruturas metálicas complexas com precisão e flexibilidade inigualáveis.
Este artigo se aprofunda no fascinante mundo da DED, explorando seus princípios fundamentais, as vantagens que oferece em relação aos métodos tradicionais e as diversas aplicações que está encontrando em vários setores.
O princípio básico da deposição de energia direcionada (DED)
Imagine um feixe de laser de alta potência, como uma versão superalimentada de um apontador laser, focado em um ponto específico. Agora, imagine um fio ou pó de metal sendo continuamente alimentado por um bocal bem próximo ao feixe de laser. Quando o feixe de laser atinge o material de alimentação de metal, ele o derrete instantaneamente. Esse metal derretido é então meticulosamente depositado em uma plataforma, camada por camada, seguindo um plano digital. Com cada camada se solidificando rapidamente, a estrutura 3D desejada toma forma.
Veja a seguir um detalhamento dos principais componentes envolvidos na DED:
- Fonte de energia: Lasers, feixes de elétrons e arcos de plasma são as fontes de energia mais comuns usadas na DED. Cada uma delas oferece vantagens e considerações exclusivas, dependendo do material e da aplicação desejados.
- Material de matéria-prima: O DED pode lidar com uma ampla variedade de ligas metálicas, incluindo titânio, aço, alumínio e superligas de níquel. A escolha do material depende das propriedades desejadas para o produto final, como força, peso e resistência à corrosão.
- Sistema de entrega: O bocal desempenha um papel fundamental, guiando o material de alimentação no caminho da fonte de energia e garantindo uma deposição precisa.
- Controle por computador: Todo o processo DED é meticulosamente controlado por um software de computador. Esse software traduz o arquivo de design 3D em uma série de instruções, determinando o movimento do braço robótico, a saída da fonte de energia e a taxa de fluxo da matéria-prima.
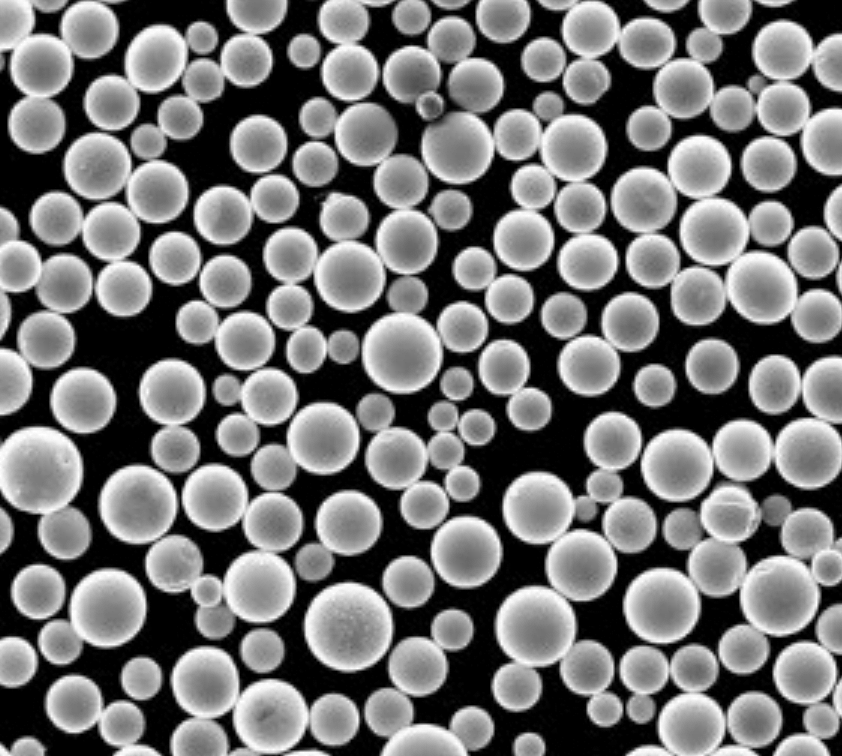
Vantagens da deposição de energia direcionada (DED)
O DED oferece um conjunto atraente de vantagens em comparação com os métodos tradicionais de fabricação, como usinagem e fundição. Vamos explorar alguns dos principais benefícios:
- Liberdade de design: Diferentemente das técnicas subtrativas, como a usinagem, a DED é aditiva. Isso significa que você não está limitado pela forma inicial de um bloco de matéria-prima. A DED permite que você crie geometrias complexas com recursos internos e detalhes intrincados que seriam impossíveis ou muito caros de se obter com os métodos tradicionais.
- Eficiência do material: O DED apresenta uma eficiência excepcional de material. Com a deposição precisa, há um desperdício mínimo em comparação com as técnicas subtrativas que geram uma quantidade significativa de sucata. Isso se traduz em economia de custos e em um processo mais ecológico.
- Estruturas leves: A DED é excelente na criação de estruturas leves e resistentes. Ao projetar estrategicamente os recursos internos ocos, as peças DED podem atingir taxas excepcionais de resistência em relação ao peso, o que as torna ideais para aplicações como aeroespacial e de transporte.
- Prototipagem rápida: O DED permite a criação rápida de protótipos funcionais diretamente a partir de modelos digitais. Isso elimina a necessidade de longos processos de ferramental, acelerando o ciclo de design e desenvolvimento.
- Manufatura quase em forma de rede: O DED pode produzir peças muito próximas de suas dimensões finais, minimizando a necessidade de etapas extensas de pós-processamento, como a usinagem. Isso se traduz em tempos de produção mais rápidos e custos gerais mais baixos.
- Reparo e restauração: A capacidade do DED de depositar material com precisão o torna ideal para o reparo de componentes metálicos danificados. Isso aumenta a vida útil dos equipamentos existentes e reduz a necessidade de substituições completas.
Aplicações da deposição de energia direcionada (DED)
A versatilidade do DED é realmente notável. Aqui está uma visão geral de algumas das aplicações interessantes em diferentes setores:
- Aeroespacial: O DED está sendo usado para criar componentes leves e de alta resistência para aeronaves, como suportes, nervuras de asa e peças de motor. Essa tecnologia está ajudando a otimizar a eficiência e o desempenho do combustível no setor aeroespacial.
- Automotivo: O DED está encontrando aplicações na criação de peças personalizadas para veículos de corrida e no reparo de componentes danificados em carros de alto desempenho.
- Médico: A DED está revolucionando o campo médico ao permitir a criação de próteses e implantes personalizados que são perfeitamente adaptados a cada paciente.
- Petróleo e gás: O DED é usado para reparar e revestir componentes críticos no setor de petróleo e gás, prolongando sua vida útil e aumentando sua resistência a ambientes adversos.
- Ferramentas: O DED pode ser usado para criar moldes e matrizes complexos com canais de resfriamento conformes, melhorando a eficiência e a velocidade de produção em vários processos de fabricação.
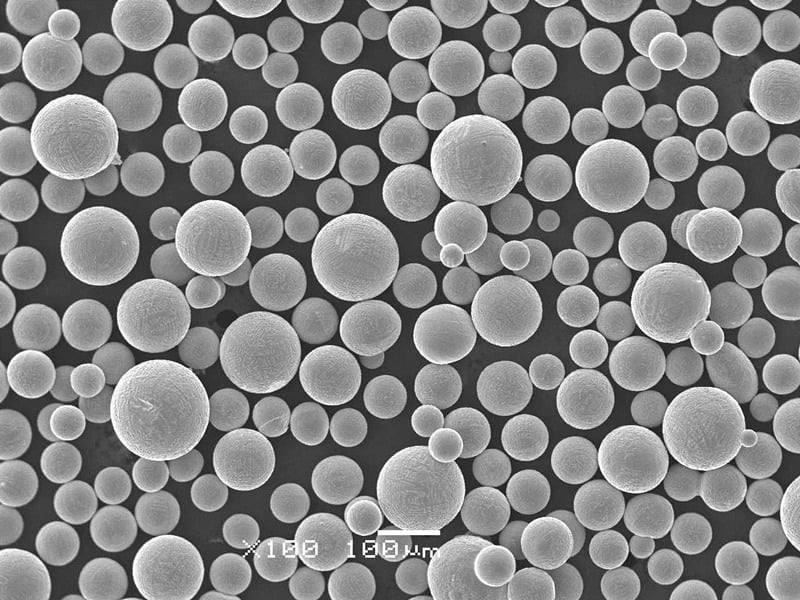
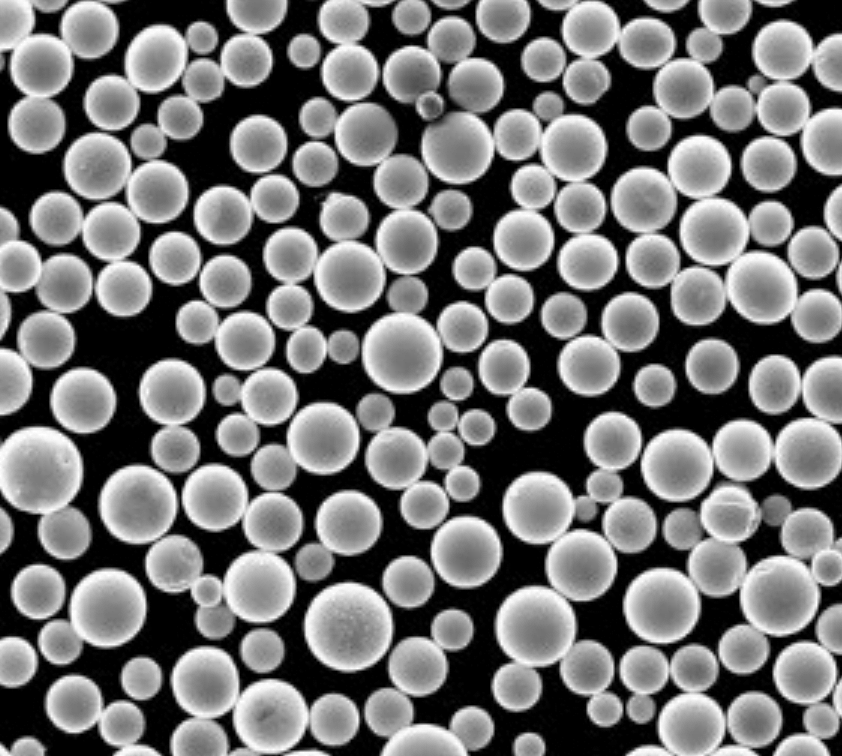
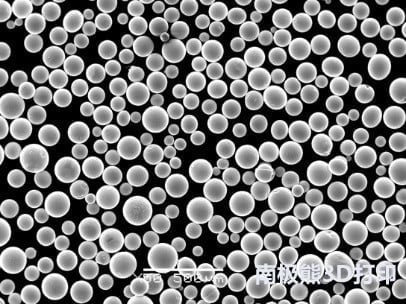
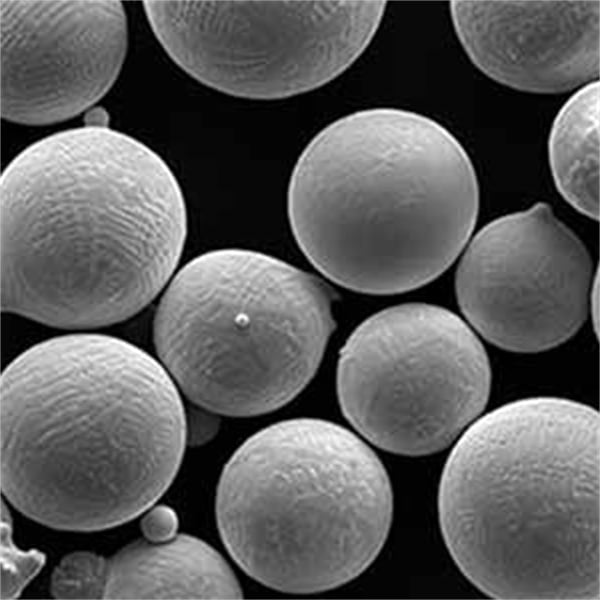
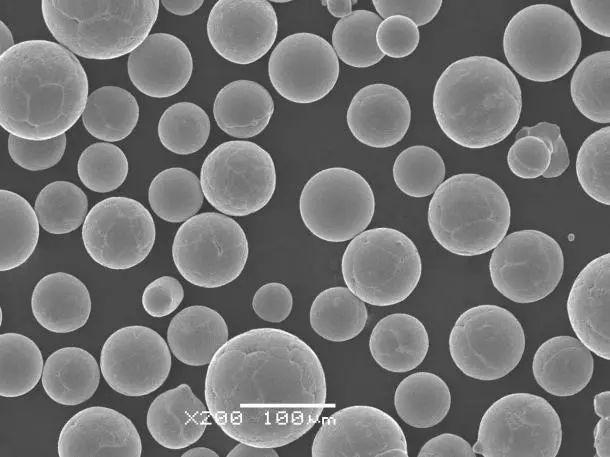
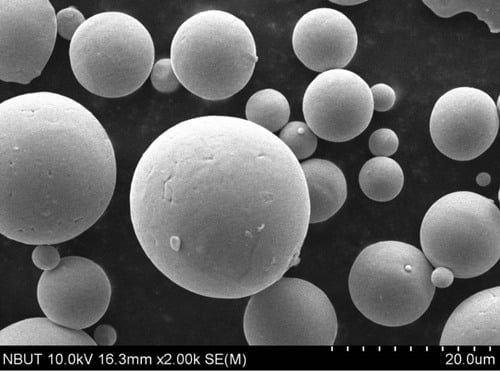
Considerações sobre a DED
Embora a DED ofereça inúmeros benefícios, é essencial considerar alguns fatores importantes antes de mergulhar nessa tecnologia.
Custo: As máquinas DED podem ser caras em comparação com os equipamentos de fabricação tradicionais. No entanto, a economia de custos com a eficiência do material, a liberdade de design e a redução do pós-processamento podem tornar a DED uma opção atraente a longo prazo, especialmente para peças complexas e de alto valor.
Propriedades do material e considerações sobre a DED
A capacidade da DED de trabalhar com uma ampla variedade de metais é uma vantagem significativa. No entanto, é fundamental entender como o processo DED pode afetar as propriedades do material do produto final em comparação com os métodos tradicionais. Aqui estão algumas considerações importantes:
- Estrutura do grão: A rápida fusão e solidificação do metal no DED pode resultar em uma estrutura de grãos mais finos em comparação com os metais fundidos ou forjados. Essa estrutura de grãos mais finos pode melhorar as propriedades mecânicas, como resistência e ductilidade da peça DED. No entanto, ela também pode tornar o material mais suscetível a rachaduras por tensão em determinadas aplicações.
- Estresse residual: O processo DED envolve aquecimento e resfriamento localizados, o que pode introduzir tensão residual na peça. A tensão residual não controlada pode levar a empenamento e distorção. Os processos DED geralmente incorporam tratamentos térmicos pós-deposição para gerenciar a tensão residual e otimizar as propriedades finais da peça.
- Acabamento da superfície: O acabamento da superfície de uma peça DED depende de vários fatores, incluindo a fonte de energia, o material de alimentação e os parâmetros de deposição. As peças DED podem ter um acabamento de superfície ligeiramente mais áspero em comparação com as peças usinadas. No entanto, as técnicas de pós-processamento, como usinagem ou polimento, podem ser usadas para obter um acabamento de superfície mais suave, se exigido pela aplicação.
Diferentes técnicas de DED e suas aplicações
Embora o princípio básico da DED permaneça o mesmo, há diversas variações na tecnologia, dependendo da fonte de energia utilizada. Veja a seguir um detalhamento das três principais técnicas de DED:
- DED a laser (L-DED):
- Utiliza um feixe de laser de alta potência como fonte de energia.
- Oferece excelente controle e precisão, tornando-o adequado para a criação de geometrias e características complexas.
- Adequado para aplicações que exigem acabamentos de superfície de alta qualidade, como implantes médicos e componentes aeroespaciais.
- Em comparação com outras técnicas de DED, a L-DED pode ser limitada na taxa de deposição e pode não ser ideal para aplicações em larga escala.
- DED por feixe de elétrons (EB-DED):
- Emprega um feixe de elétrons focalizado dentro de uma câmara de vácuo para derreter o material de alimentação.
- Oferece penetração mais profunda e taxas de deposição mais altas em comparação com o L-DED.
- Isso torna o EB-DED uma boa opção para a criação de estruturas de paredes espessas e para o reparo de componentes grandes.
- No entanto, o requisito da câmara de vácuo aumenta a complexidade e o custo do processo EB-DED.
- DED por arco de plasma (PA-DED):
- Utiliza um arco de plasma de alta temperatura como fonte de energia.
- Oferece as taxas de deposição mais rápidas entre as técnicas de DED, tornando-a adequada para aplicações em larga escala e de alto rendimento.
- O PA-DED também pode lidar com uma variedade maior de matérias-primas metálicas em comparação com o L-DED e o EB-DED.
- No entanto, o PA-DED pode ter uma zona de calor mais ampla em comparação com outras técnicas de DED, levando a um acabamento superficial mais áspero e a um tamanho de grão potencialmente maior no material depositado.
O futuro da deposição de energia direcionada
A DED ainda é uma tecnologia relativamente nova, com imenso potencial de crescimento e inovação. Aqui estão algumas tendências interessantes que estão moldando o futuro da DED:
- DED multimaterial: Os pesquisadores estão explorando maneiras de combinar diferentes técnicas de DED ou até mesmo integrar a DED a outros processos de manufatura aditiva para criar peças multimateriais com propriedades personalizadas em diferentes regiões. Imagine um componente aeroespacial leve com um núcleo de alta resistência e uma camada externa resistente à corrosão, tudo fabricado em um único processo de DED.
- Processos híbridos de DED: A integração da DED com tecnologias de usinagem ou monitoramento in-situ é bastante promissora. O controle de processos em tempo real e os recursos de fabricação adaptáveis permitiriam que a DED produzisse peças de alta qualidade com precisão e eficiência ainda maiores.
- Padronização e qualificação: Com o aumento da adoção da DED, será fundamental estabelecer processos padronizados e procedimentos de qualificação. Isso garantirá a confiabilidade e a repetibilidade das peças DED para aplicações críticas em setores como o aeroespacial e o médico.
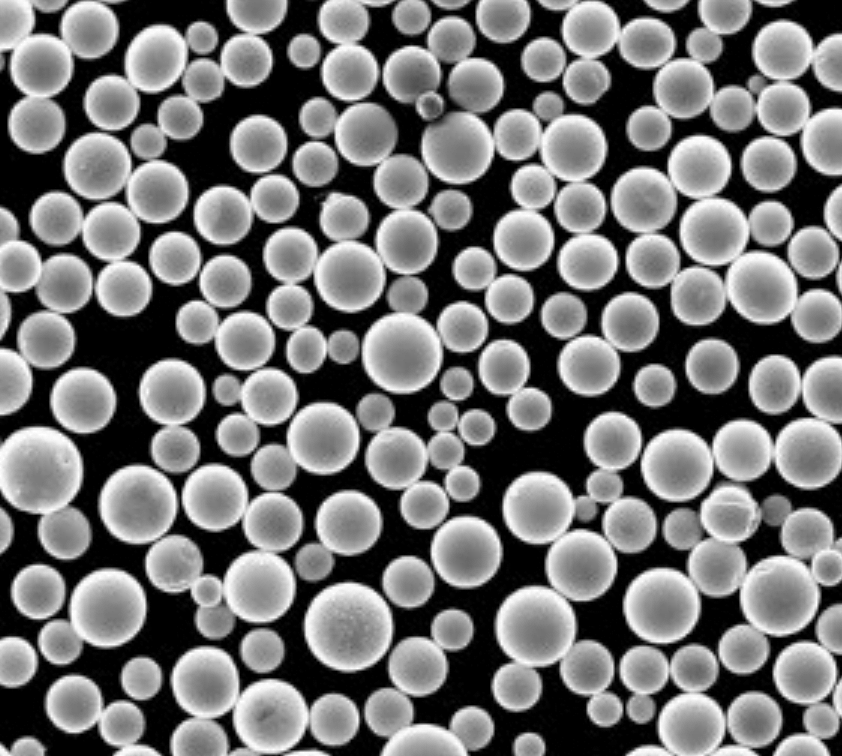
FAQ
Pergunta | Resposta |
---|---|
Quais são os benefícios do DED em relação aos métodos tradicionais de fabricação? | O DED oferece liberdade de projeto, eficiência de material, capacidade de criar estruturas leves, prototipagem rápida, fabricação de formas quase líquidas e recursos de reparo. |
Quais são algumas das aplicações da DED? | O DED é usado nos setores aeroespacial, automotivo, médico, de petróleo e gás e de ferramentas. |
Quais fatores devem ser considerados ao usar a DED? | O custo, as propriedades do material (estrutura do grão, tensão residual, acabamento da superfície) e a escolha da técnica DED (laser, feixe de elétrons, arco de plasma) são considerações importantes. |
Sobre o 3DP mETAL
Categoria do produto
ENTRE EM CONTATO
Alguma dúvida? Envie-nos uma mensagem agora! Após receber sua mensagem, processaremos sua solicitação com toda equipe.