Visão Geral
Inconel 718 is a high-strength, corrosion-resistant nickel-chromium material used at temperatures ranging from cryogenic to 1200°F. It is widely known for its impressive combination of tensile, fatigue, creep, and rupture strength, making it a popular choice for demanding applications in industries such as aerospace, marine, and chemical processing. But what makes Inconel 718 so special? Let’s dive deep into its characteristics, properties, and applications to understand why it’s a material of choice for many engineers and manufacturers.
Types and Composition
Inconel 718 is available in various forms, including bar, sheet, plate, tube, and metal powder. Its composition is primarily nickel (50-55%) and chromium (17-21%), with significant amounts of iron, niobium, and molybdenum.
Formulário | Composição |
---|---|
Bar | Nickel (50-55%), Chromium (17-21%), Iron (Bal), Niobium (4.75-5.5%), Molybdenum (2.8-3.3%) |
Sheet | Nickel (50-55%), Chromium (17-21%), Iron (Bal), Niobium (4.75-5.5%), Molybdenum (2.8-3.3%) |
Plate | Nickel (50-55%), Chromium (17-21%), Iron (Bal), Niobium (4.75-5.5%), Molybdenum (2.8-3.3%) |
Tubo | Nickel (50-55%), Chromium (17-21%), Iron (Bal), Niobium (4.75-5.5%), Molybdenum (2.8-3.3%) |
Pó metálico | Nickel (50-55%), Chromium (17-21%), Iron (Bal), Niobium (4.75-5.5%), Molybdenum (2.8-3.3%) |
In addition to these primary components, Inconel 718 also contains trace amounts of aluminum, titanium, and cobalt, which enhance its overall performance.
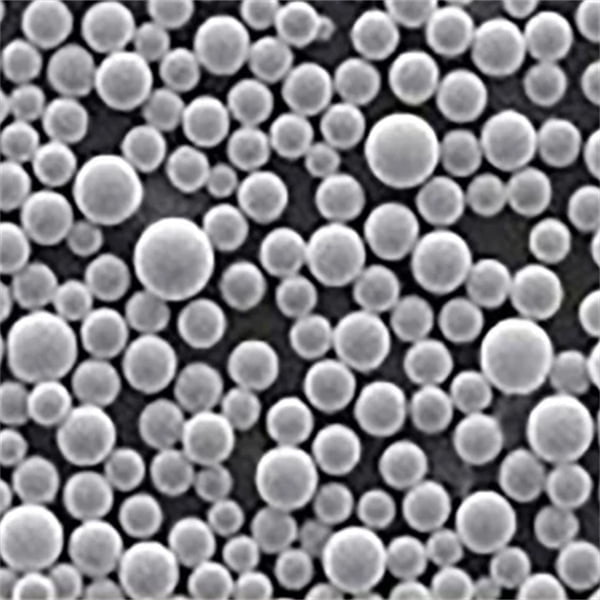
Propriedades e características
Inconel 718 is renowned for its excellent mechanical properties and high resistance to thermal oxidation and corrosion. Here’s a detailed look at its key characteristics:
Propriedade | Valor |
---|---|
Resistência à Tração | 135 ksi (930 MPa) |
Limite de escoamento | 70 ksi (480 MPa) |
alongamento | 12-15% |
Dureza | 330-360 HB |
Condutividade térmica | 11.4 W/m·K |
Faixa de fusão | 1260-1340°C |
Densidade | 8,19 g/cm³ |
Specific Heat Capacity | 435 J/kg·K |
Módulo de elasticidade | 200 GPa |
Coeficiente de expansão térmica | 13.0 µm/m·K (at 20-1000°C) |
Resistência à oxidação | Excellent up to 1200°F (650°C) |
Resistência à corrosão | Superior in most corrosive environments, particularly in oxidizing and reducing conditions |
Aplicativos de Inconel 718 Material
Inconel 718’s unique combination of properties makes it suitable for a variety of demanding applications. Here are some of the most common uses:
Aplicativo | Descrição |
---|---|
Aeroespacial | Used in gas turbine engines, rocket motors, spacecraft, and high-temperature fasteners |
Marinha | Components exposed to saltwater environments, including valves, pumps, and propeller shafts |
Processamento químico | Heat exchangers, reactors, and other equipment exposed to corrosive chemicals |
Petróleo e gás | Downhole components, wellhead equipment, and other high-stress, high-temperature applications |
Geração de energia | Turbine blades, rings, and other parts in steam and gas turbines |
Nuclear translated to Portuguese (Brazil) is "Nuclear." | Reactor core components, control rod drive mechanisms, and other critical reactor parts |
Automotivo | Turbocharger rotors, exhaust valves, and other high-temperature components |
Especificações, tamanhos, classes e padrões
Inconel 718 is available in various sizes, grades, and standards to meet different industry requirements.
Especificação | Tamanho | Nota | Padrão |
---|---|---|---|
Bar | 1/4″ to 8″ diameter | UNS N07718 | ASTM B637, AMS 5662/5663 |
Sheet | 0.018″ to 0.156″ thick | UNS N07718 | ASTM B670, AMS 5596/5597 |
Plate | 0.25″ to 4″ thick | UNS N07718 | ASTM B670, AMS 5596/5597 |
Tubo | 0.5″ to 3″ OD | UNS N07718 | ASTM B163, ASTM B516, AMS 5589 |
Pó metálico | 15-53µm, 45-150µm | UNS N07718 | AMS 5662/5663 |
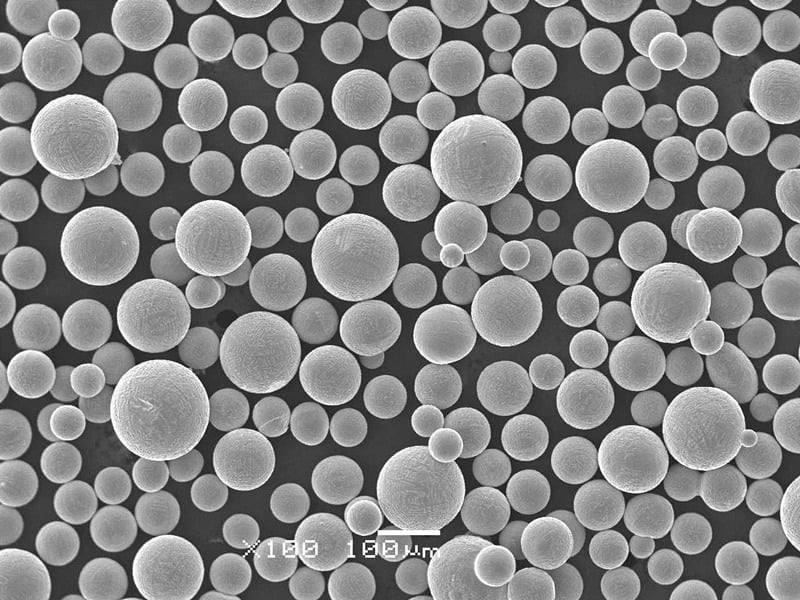
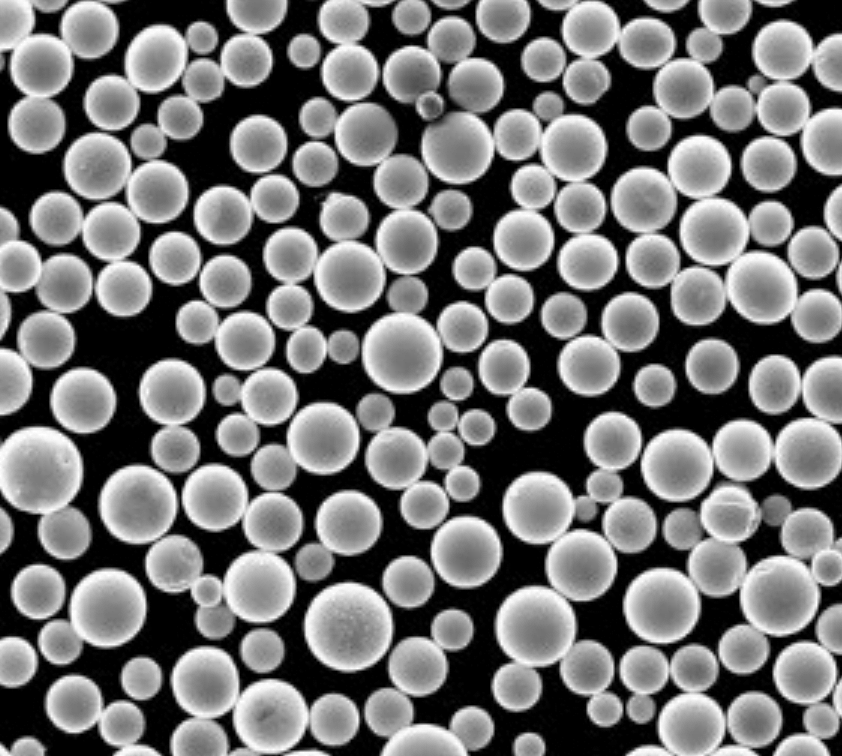
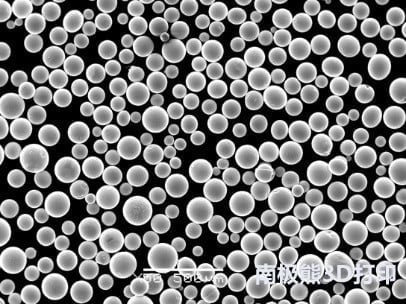
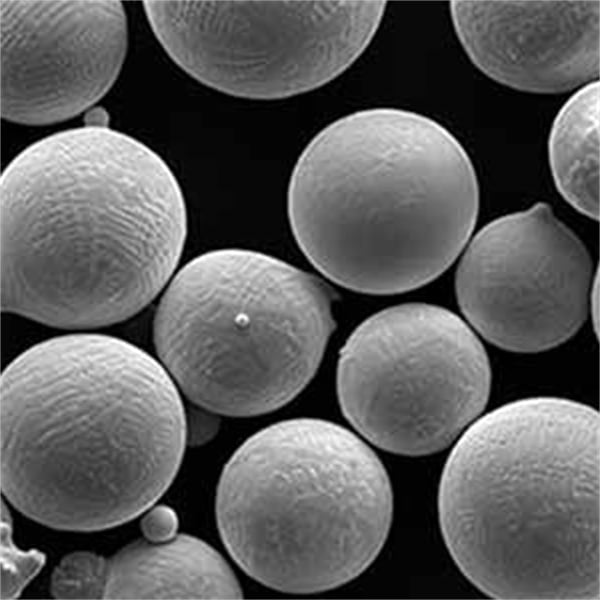
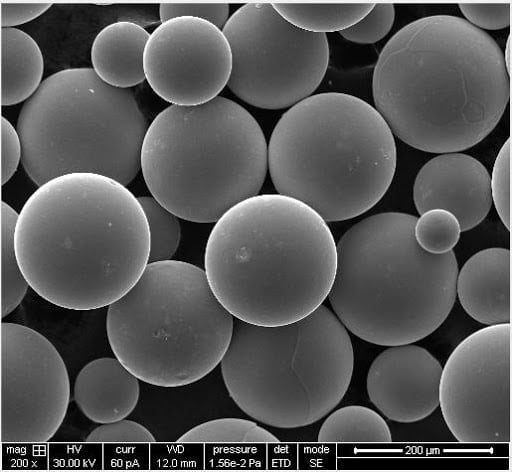
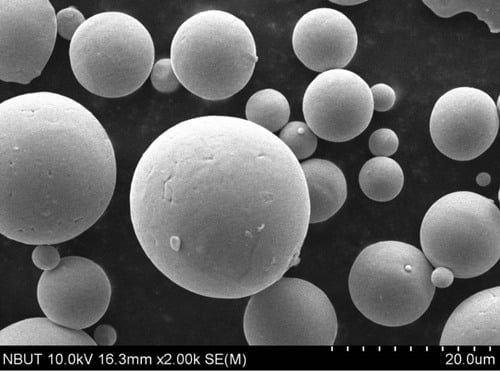
Detalhes de fornecedores e preços
Pricing for Inconel 718 varies based on the form and quantity purchased. Here’s a snapshot of typical suppliers and pricing:
Fornecedor | Formulário | Preço (por kg) | Contato |
---|---|---|---|
Special Metals Corp. | Bar, Sheet | $80 – $100 | [email protected] |
Haynes International | Plate, Tube | $90 – $110 | [email protected] |
Ligas especiais da ATI | Pó metálico | $100 – $120 | [email protected] |
Metais VDM | All Forms | $85 – $105 | [email protected] |
Rolled Alloys | Bar, Plate | $88 – $108 | [email protected] |
Vantagens e desvantagens do Inconel 718 Material
Every material has its pros and cons. Let’s explore the advantages and limitations of Inconel 718:
Vantagens do material Inconel 718
- Alta resistência: Inconel 718 maintains its strength over a wide temperature range, making it ideal for high-stress applications.
- Excelente resistência à corrosão: Its resistance to oxidation and corrosion in various environments extends the lifespan of components.
- Boa soldabilidade: Unlike some other high-strength alloys, Inconel 718 can be welded without loss of ductility.
- Aplicações versáteis: Its properties make it suitable for a broad range of industries, from aerospace to chemical processing.
Desvantagens do material Inconel 718
- Custo: Inconel 718 is more expensive than many other materials, which can be a limiting factor for some applications.
- Usinabilidade: Due to its high strength and hardness, machining Inconel 718 can be challenging and requires specialized equipment and techniques.
- Densidade: Its relatively high density can be a drawback in applications where weight is a critical factor.
Modelos específicos de pós metálicos
Here are ten specific Inconel 718 metal powder models, each with its unique characteristics:
- ATI 718 Powder: Known for its high purity and consistent particle size distribution, ideal for additive manufacturing and repair applications.
- Höganäs 718 Powder: Features excellent flowability and packing density, suitable for powder bed fusion processes.
- Sandvik Osprey 718 Powder: Offers superior oxidation resistance and high-temperature strength, perfect for aerospace applications.
- Carpenter Powder Products 718: Known for its fine microstructure and high fatigue resistance, ideal for critical aerospace components.
- AP&C 718 Powder: Provides excellent mechanical properties and is optimized for electron beam melting (EBM) processes.
- Praxair TruForm 718: Features high sphericity and low oxygen content, making it suitable for direct metal laser sintering (DMLS).
- LPW Technology 718 Powder: Offers tight control over chemistry and particle size, ensuring high performance in additive manufacturing.
- GKN Hoeganaes AncorAM 718: Known for its high consistency and performance in binder jetting applications.
- Tekna 718 Powder: Provides excellent flow characteristics and is designed for laser powder bed fusion (LPBF) processes.
- Erasteel 718 Powder: Features high cleanliness and is ideal for hot isostatic pressing (HIP) and additive manufacturing applications.
Comparação de prós e contras, vantagens e limitações
Here’s a comparison of Inconel 718’s pros and cons against other similar materials like Hastelloy X and Incoloy 825:
Recurso | Inconel 718 | Hastelloy X | Incoloy 825 |
---|---|---|---|
Resistência a altas temperaturas | Excellent (up to 1200°F) | Very Good (up to 1500°F) | Good (up to 1000°F) |
Resistência à corrosão | Superior | Excelente | Muito bom |
Soldabilidade | Bom | Moderado | Bom |
Custo | Alto | Muito alto | Moderado |
Maquinabilidade | Challenging | Moderado | Bom |
Densidade | Alto | Alto | Moderado |
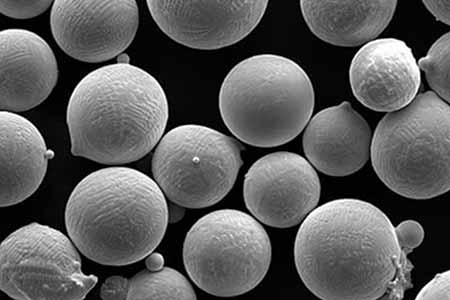
Perguntas frequentes
Pergunta | Resposta |
---|---|
What is Inconel 718 used for? | It is used in aerospace, marine, chemical processing, oil and gas, power generation, and automotive applications. |
How does Inconel 718 resist corrosion? | It has a high chromium content which forms a protective oxide layer, enhancing its corrosion resistance. |
O Inconel 718 pode ser soldado? | Yes, it can be welded using appropriate techniques, maintaining its ductility and strength. |
Why is Inconel 718 expensive? | Its high cost is due to the complex manufacturing processes and the expensive raw materials used in its composition. |
What are the alternatives to Inconel 718? | Alternatives include Hastelloy X, Incoloy 825, and other nickel-chromium-based superalloys. |
Is Inconel 718 suitable for cryogenic applications? | Yes, it retains its toughness and strength at cryogenic temperatures. |
Como o Inconel 718 é fabricado? | It is produced through processes such as casting, forging, and powder metallurgy. |
What industries benefit most from using Inconel 718? | Aerospace, marine, chemical processing, oil and gas, and power generation industries benefit the most. |
What is the difference between Inconel 718 and Inconel 625? | Inconel 718 has higher strength due to the addition of niobium, whereas Inconel 625 is more corrosion-resistant. |
How do you machine Inconel 718? | Machining requires specialized equipment, slow cutting speeds, and the use of carbide tools to manage its hardness. |
Conclusão
Inconel 718 stands out as a versatile, high-performance material capable of withstanding extreme conditions. Its superior mechanical properties, excellent corrosion resistance, and high strength make it indispensable across various high-stress industries. Despite its higher cost and challenging machinability, the benefits it offers in terms of durability and performance often outweigh these limitations. Whether it’s in the sky, deep sea, or in the heart of a chemical plant, Inconel 718 continues to prove its worth as a material of choice for engineers and manufacturers worldwide.
Sobre o 3DP mETAL
Categoria do produto
ENTRE EM CONTATO
Alguma dúvida? Envie-nos uma mensagem agora! Após receber sua mensagem, processaremos sua solicitação com toda equipe.