Imagine a world where complex, near-net-shape metal components could be produced with the speed and design freedom of plastic injection molding. That’s the reality of MIM manufacturing, a revolutionary process that’s transforming countless industries. This article delves deep into the fascinating world of MIM, exploring its intricacies, applications, and why it might be the perfect fit for your next project.
Unveiling the Magic: An Overview of MIM Manufacturing
Metal injection molding (MIM) is a near-net-shape manufacturing technique that combines the best aspects of metalworking and plastic injection molding. Here’s the gist:
- Central elétrica de pó: Metal powders, as fine as flour, are meticulously chosen based on the desired final properties. We’ll explore a variety of metal powders later.
- Binder Magic: These metal powders are meticulously blended with a polymeric binder, creating a feedstock that resembles Play-Doh. This binder plays a crucial role in holding the metal particles together during molding.
- Molding the Magic: The feedstock is then injected into a precisely designed mold cavity under high pressure and heat, mimicking the process of plastic injection molding.
- The Debinding Dance: Once the part cools and solidifies, the binder is meticulously removed through a thermal or chemical debinding process. Imagine a magician pulling a rabbit out of a hat, except here, the “rabbit” is a complex metal component!
- Sintering Symphony: The final step involves sintering, where the part is exposed to high temperatures in a controlled atmosphere. This fuses the metal particles together, resulting in a robust and near-final shape.
MIM offers a compelling solution for manufacturers seeking a balance between complexity, cost-effectiveness, and high-performance metal parts. But is it the right fit for your project? Let’s delve deeper.
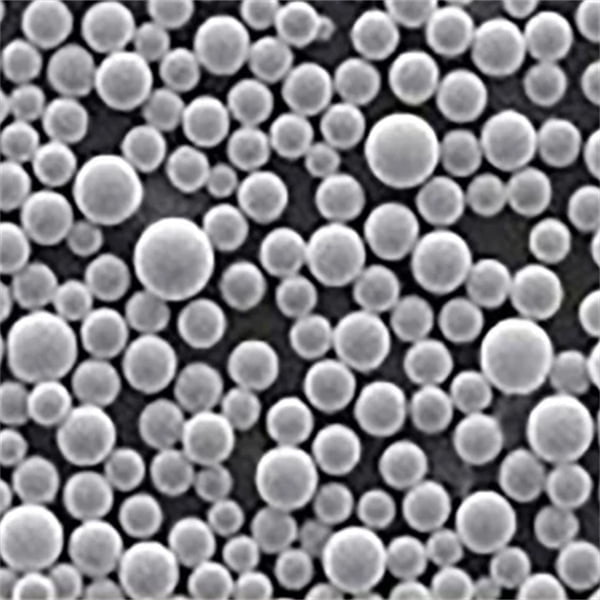
A Menagerie of Metal Powders: Choosing the Right Fit
The magic of MIM hinges on the selection of the right metal powder. Here’s a glimpse into some of the most common metal powders used in MIM, each with its unique properties:
Common Metal Powders in MIM
Pó metálico | Descrição | Propriedades | APLICATIVOS |
---|---|---|---|
Low-Alloy Steel | The workhorse of MIM, offering a good balance of strength, affordability, and machinability. | Affordable, strong, machinable | Gears, sprockets, fasteners, housings |
Aço inoxidável | Offers excellent corrosion resistance, making it ideal for harsh environments. | Corrosion-resistant, good strength | Medical devices, valves, pump components |
Aço para ferramentas | Renowned for its high wear resistance, perfect for components that experience friction. | High wear resistance, good hardness | Cutting tools, dies, gears |
Ligas de níquel | Boast exceptional high-temperature strength and corrosion resistance. | High-temperature strength, corrosion-resistant | Aerospace components, heat exchangers, turbine blades |
Cobre | An excellent conductor of heat and electricity, making it ideal for electrical applications. | Alta condutividade elétrica e térmica | Electrical connectors, heat sinks, brazing materials |
Titânio | A lightweight metal with exceptional strength-to-weight ratio and biocompatibility. | Leve, resistente e biocompatível | Biomedical implants, aerospace components, sporting goods |
Tungstênio | Renowned for its extreme density and high-temperature strength. | High density, high-temperature strength | Ballistic applications, weights, welding electrodes |
Inconel | A family of nickel-chromium superalloys offering exceptional high-temperature strength and oxidation resistance. | High-temperature strength, oxidation-resistant | Componentes de motores a jato, trocadores de calor, equipamentos de processamento químico |
Kovar | A controlled-expansion iron-nickel-cobalt alloy designed to match the thermal expansion of glass. | Matched thermal expansion to glass | Electronic packages, optoelectronic devices |
Molibdênio | A high-melting point metal with good strength and electrical conductivity at high temperatures. | High melting point, good strength, high-temperature conductivity | High-temperature furnace components, electrical contacts |
This is just a sampling of the vast array of metal powders available for MIM. The selection process hinges on the desired properties of the final component. For instance, if you require a gear that can withstand high loads, low-alloy steel might be the perfect choice. Conversely, if corrosion resistance is paramount, stainless steel would be a better fit.
A Symphony of Applications: Where MIM Shines
MIM’s ability to produce complex, near-net-shape metal components makes it a valuable tool across various industries. Here are some of the most common applications of MIM, continuing from the previous section:
Indústria | Exemplos de aplicação |
---|---|
Automotivo | Gears, sprockets, fasteners, valve components, fuel system components |
Dispositivos médicos | Surgical instruments, implants (dental, orthopedic), bone screws, housings for pacemakers |
Eletrônicos de consumo | Connectors, housings for mobile phones and cameras, watch components, heat sinks |
Aeroespacial e Defesa | Engine components, turbine blades, gears for landing gear systems, firearm components |
Firearms | Triggers, hammers, safeties, small internal components |
Telecomunicações | RF components, connectors, housings for electronic modules |
Óleo e gás | Downhole components, wellhead equipment, valves |
The beauty of MIM lies in its versatility. Beyond these established applications, MIM is constantly pushing boundaries. For instance, researchers are exploring its potential in:
- Microfluidics: Fabrication of intricate microchannels for medical devices and lab-on-a-chip applications.
- Biocompatible Implants: Advancements in biocompatible metal powders are paving the way for MIM-produced implants that seamlessly integrate with the human body.
- Leveza: The aerospace industry is leveraging MIM to create lightweight, high-strength components for next-generation aircraft.
As MIM technology matures, we can expect even more innovative applications to emerge, further solidifying its place as a transformative manufacturing process.
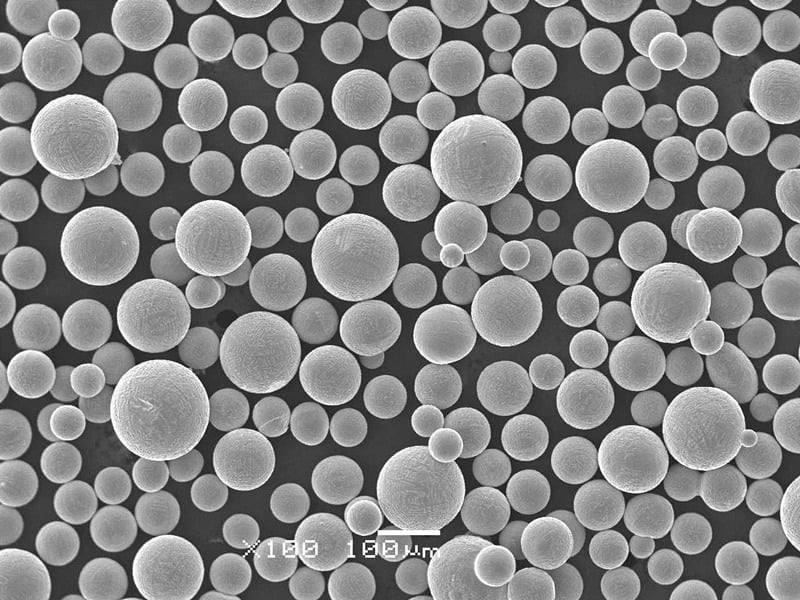
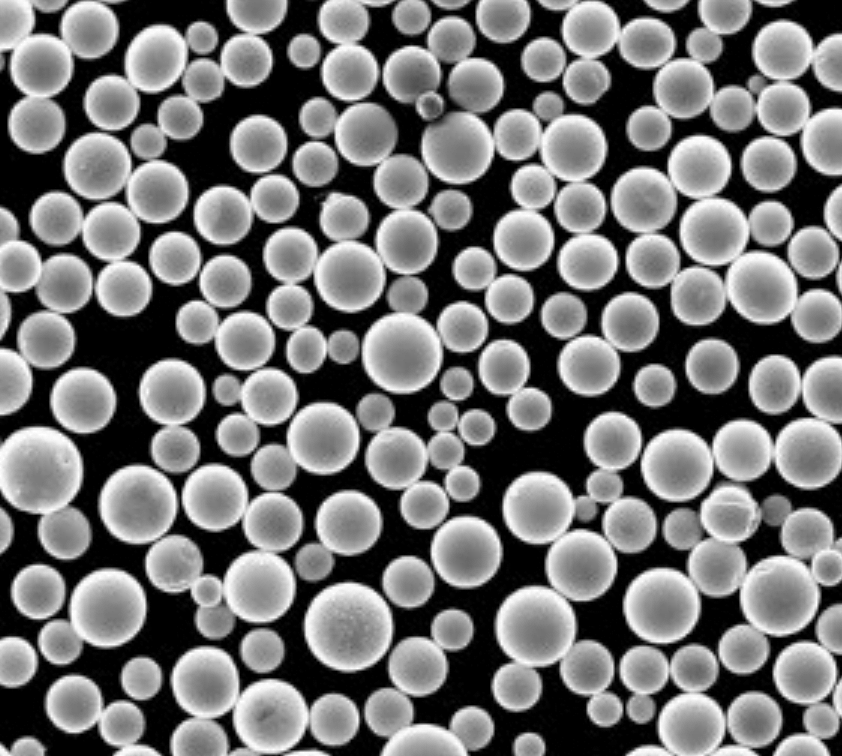
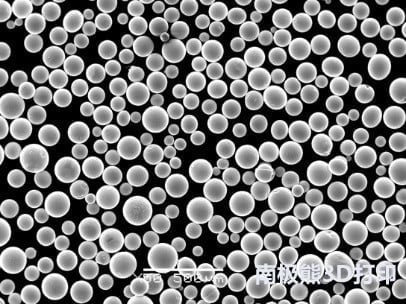
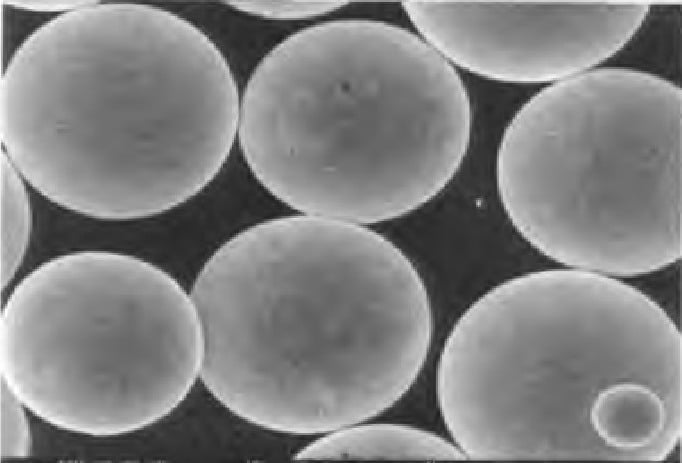
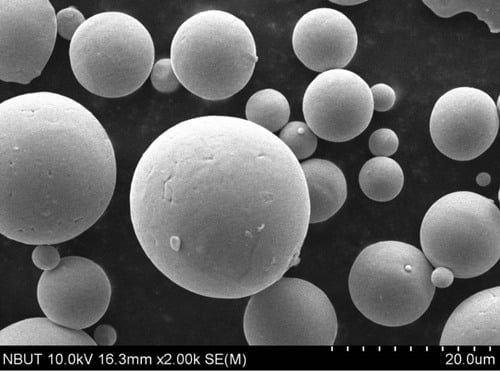
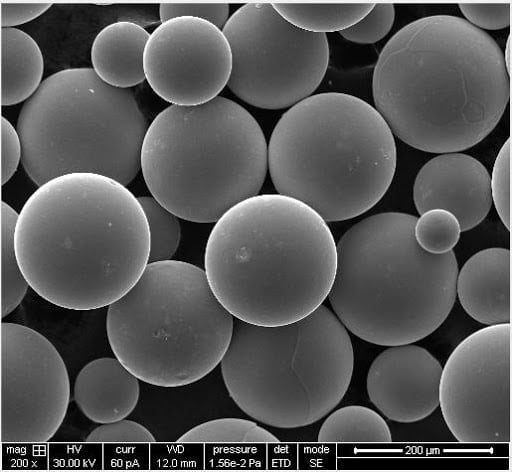
Pros and Cons of MIM
Every manufacturing process has its own set of advantages and limitations. MIM is no exception. Here’s a breakdown of the key pros and cons to consider when evaluating MIM for your project:
Vantagens de Fabricação MIM
- Liberdade de design: MIM allows for the creation of intricate shapes with tight tolerances, rivaling the complexity achievable with plastic injection molding.
- Custo-efetividade: For high-volume production of complex parts, MIM can be a cost-effective alternative to traditional metalworking techniques like machining or casting.
- Versatilidade do material: A wide range of metal powders can be used in MIM, catering to diverse performance needs.
- Alta precisão: MIM parts can be produced with tight tolerances, reducing the need for post-processing.
- Waste Reduction: MIM minimizes material waste compared to traditional machining processes.
Desvantagens de Fabricação MIM
- Custos de ferramentas: The upfront cost of developing MIM molds can be high, especially for complex parts.
- Production Lead Time: The process of developing and validating MIM components can be longer compared to some traditional methods.
- Limitações de tamanho da peça: MIM is best suited for small to medium-sized parts, typically with a maximum size of a few inches.
- Acabamento da superfície: MIM parts may require additional post-processing to achieve a desired surface finish.
Making the Choice: MIM vs. Other Manufacturing Processes
When deciding if MIM is the right fit for your project, it’s important to compare it to alternative manufacturing processes. Here’s a quick comparison of MIM with some common contenders:
- Usinagem: MIM offers a cost-effective alternative for high-volume production of complex parts, whereas machining excels for low-volume or custom components and allows for larger part sizes.
- Casting: Casting is a good option for high-volume production of simpler shapes, while MIM shines in creating intricate geometries. Material selection is also broader with casting.
- Metal Additive Manufacturing (3D Printing): Both MIM and 3D printing offer design freedom, but MIM is generally faster and more cost-effective for high-volume production. 3D printing caters to smaller batch sizes and highly customized parts.
The ideal choice hinges on your specific project requirements: part complexity, production volume, budget, and desired material properties. Consulting with an experienced MIM manufacturer can help you navigate this decision-making process.
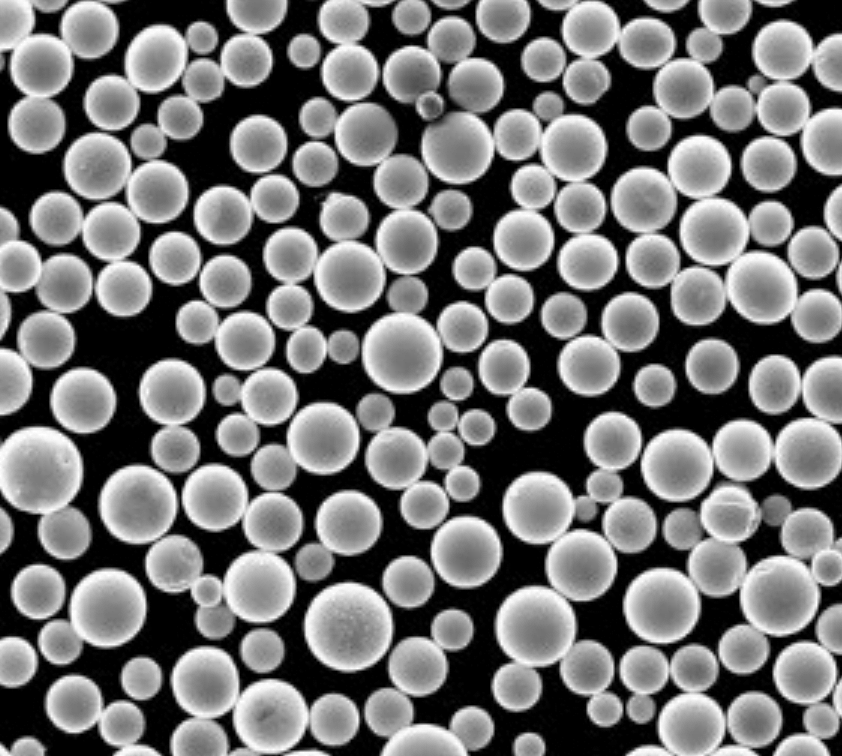
FAQ
Here are some of the most commonly asked questions about MIM manufacturing, presented in a clear and concise table format:
Pergunta | Resposta |
---|---|
What are the size limitations of MIM parts? | MIM parts are typically limited to a few inches in size, although advancements are pushing these boundaries. |
What is the minimum order quantity for MIM production? | Minimum order quantities (MOQs) can vary depending on the complexity of the part and the manufacturer. |
How long does it take to develop a new MIM part? | The development timeline for a new MIM part can range from several weeks to a few months. This depends on the complexity of the part, the chosen metal powder, and the manufacturer’s experience. |
What are the surface finish options for MIM parts? | MIM parts can achieve a variety of surface finishes through post-processing techniques like tumbling, polishing, and plating. The achievable finish depends on the desired aesthetics and functional requirements. |
Is MIM suitable for prototyping? | MIM can be a viable option for prototyping complex metal parts, especially when multiple iterations are needed. However, the upfront tooling cost might be higher compared to rapid prototyping techniques like 3D printing for simple prototypes. |
What are some of the emerging trends in MIM manufacturing? | Advancements in metal powder development, such as biocompatible powders and those offering improved strength-to-weight ratios, are expanding MIM’s applications. Additionally, micro-MIM technology is enabling the creation of even smaller and more intricate components. |
What are the environmental benefits of MIM? | Compared to traditional machining processes, MIM generates less material waste and can utilize recycled metal powders, contributing to a more sustainable manufacturing approach. |
The Future of MIM: A Material Magic Show
MIM manufacturing is on a steady ascent, continuously evolving and refining its capabilities. As metal powder technology progresses, offering even more diverse properties, MIM’s potential seems limitless. Here’s a glimpse into what the future might hold for this transformative process:
- Micro-MIM Mania: Micro-MIM, a specialized technique for fabricating miniature components, is poised to revolutionize industries like microfluidics and medical devices. Imagine intricate microchannels for lab-on-a-chip applications or biocompatible micro-implants, all produced with the precision and efficiency of MIM.
- Material Mashup: The development of composite metal powders, combining different metals or incorporating ceramic elements, will unlock entirely new performance possibilities for MIM parts. Imagine a gear with the strength of steel and the wear resistance of a ceramic coating, all fabricated in a single MIM run.
- Sustainable Spotlight: As environmental consciousness takes center stage, MIM’s inherent advantages in material utilization and potential for using recycled powders will make it an even more attractive manufacturing choice.
MIM is not just a manufacturing process; it’s a gateway to a world of design freedom, material innovation, and sustainable production. As this technology continues to evolve, we can expect even more exciting possibilities to emerge, solidifying MIM’s place as a cornerstone of modern manufacturing.
Sobre o 3DP mETAL
Categoria do produto
ENTRE EM CONTATO
Alguma dúvida? Envie-nos uma mensagem agora! Após receber sua mensagem, processaremos sua solicitação com toda equipe.