Molybdenum metal powder, a greyish, fine-grained material, might not be the star of the material science show, but behind the scenes, it plays a crucial role in countless industrial applications. Imagine a world without smartphones, high-speed bullets, or jet engines – molybdenum metal powder contributes to the strength, durability, and performance of these marvels of modern engineering.
This article delves into the fascinating world of molybdenum metal powder, exploring its properties, applications, and the different forms it comes in. We’ll unveil the reasons behind its popularity and shed light on its advantages and limitations. So, buckle up and get ready for a deep dive into the mighty molybdenum!
Molybdenum Metal Powder: An Overview
Molybdenum (Mo) is a silvery-white transition metal renowned for its exceptional strength, high melting point (around 2623°C or 4713°F), and remarkable resistance to corrosion. Molybdenum metal powder is a finely divided form of this element, typically produced by reducing molybdenum oxides with hydrogen gas. This process yields a versatile material with a high surface area, making it ideal for various industrial applications.
Here’s a quick snapshot of molybdenum metal powder:
- Composição: Primarily molybdenum (Mo) metal, with trace impurities depending on the manufacturing process.
- Propriedades: High strength, high melting point, excellent corrosion resistance, good electrical conductivity.
- Aplicativos: Used in powder metallurgy, electronics, aerospace, and lubrication.
- Benefícios: Enhances strength, high-temperature performance, and corrosion resistance in various products.
- Drawbacks: Can be flammable in powder form, requires specific handling procedures.
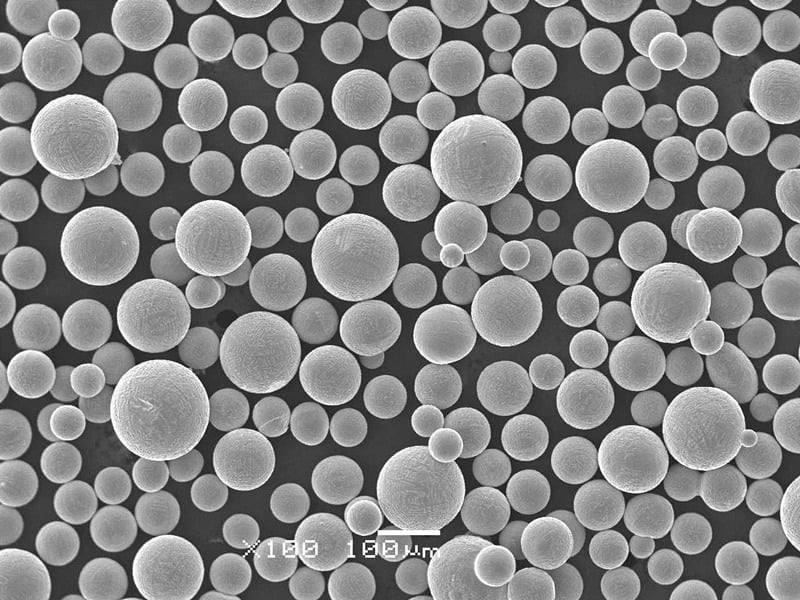
As nuances composicionais de Molybdenum Metal Powder
Molybdenum metal powder, like most industrial materials, isn’t always 100% pure molybdenum. The exact composition can vary depending on the manufacturing process and desired properties. Here’s a breakdown of the typical constituents:
Componente | Proportion | O impacto |
---|---|---|
Molibdênio (Mo) | 99.0% – 99.95% | Primary component, responsible for the material’s key properties. |
Oxigênio (O) | Up to 0.5% | May be present as residual oxides, can affect powder flow and sintering behavior. |
Carbono (C) | Up to 0.3% | Can improve strength and hardenability, but high levels can lead to brittleness. |
Nitrogênio (N) | Up to 0.1% | May enhance high-temperature properties but can also promote nitride formation. |
Ferro (Fe) | Traces | Common impurity, minimal impact on most applications. |
These minor variations can influence the final product’s characteristics. Manufacturers often tailor the composition to achieve specific properties for their intended applications.
A Gallery of Molybdenum Metal Powder Models
Molybdenum metal powder isn’t a one-size-fits-all solution. Manufacturers offer a variety of models with distinct properties and applications. Here’s a closer look at ten prominent models:
Model 1: High Purity Molybdenum Powder (HP Mo Powder)
- Descrição: Boasts a minimum molybdenum content of 99.95%, making it ideal for applications demanding exceptional purity, like electronic components and crucibles for high-temperature melting.
- Aplicativos: Electronic components, crucibles for high-temperature melting, sputtering targets.
Model 2: Standard Grade Molybdenum Powder
- Descrição: Offers a good balance between purity (typically 99.0% Mo) and cost-effectiveness. It’s a popular choice for general-purpose powder metallurgy applications.
- Aplicativos: Gears, bearings, structural components, heat sinks.
Model 3: Carbon-Doped Molybdenum Powder
- Descrição: Contains a controlled amount of carbon (up to 0.3%) to enhance strength and hardenability. It’s suitable for applications requiring high mechanical performance.
- Aplicativos: High-strength fasteners, cutting tools, armor components.
Model 4: Nitrogen-Doped Molybdenum Powder
- Descrição: Incorporates small amounts of nitrogen (up to 0.1%) to improve high-temperature properties like creep resistance. This model finds use in demanding aerospace applications.
- Aplicativos: Turbine blades, rocket engine components, heat shields.
Model 5: Atomized Molybdenum Powder
- Descrição: Produced by rapidly quenching molten molybdenum gas into a fine powder. This method yields spherical particles with excellent flow characteristics, ideal for powder metallurgy processes.
- Aplicativos: Similar to standard grade molybdenum powder, but with improved flowability.
Model 6: Reduced Molybdenum Oxide Powder (MoO2 Powder)
- Descrição: A precursor to molybdenum metal powder, MoO2 powder is an intermediate product obtained by roasting molybdenum ore. It’s often used in applications where subsequent reduction to metallic molybdenum is required.
- Aplicativos: Production of molybdenum metal powder, pigments, catalysts.
Model 7: Micronic Molybdenum Powder
- Descrição: Features an exceptionally fine particle size, typically ranging from 1 to 10 microns. This fine powder offers a high surface area, making it suitable for applications like catalysis and electrical contacts.
- Aplicativos: Catalysts in chemical reactions, electrical contacts, friction modifiers.
Model 8: Submicron Molybdenum Powder
- Descrição: An even finer version of molybdenum powder, with particle sizes below 1 micron. Due to its extremely high surface area, this model is used in specialized applications requiring exceptional reactivity.
- Aplicativos: Advanced catalysts, conductive inks for printed electronics, pyrotechnic devices.
Model 9: Hyperpure Molybdenum Powder
- Descrição: The pinnacle of purity, boasting molybdenum content exceeding 99.99%. This model is used in critical applications where even trace impurities can significantly impact performance.
- Aplicativos: Optical components, nuclear reactor components, high-performance electronics.
Model 10: Alloyed Molybdenum Powder
- Descrição: Molybdenum powder can be blended with other metals to create unique alloys with tailored properties. Common alloying elements include nickel, iron, and chromium.
- Aplicativos: Electrodes for arc welding, high-performance cutting tools, heat-resistant components.
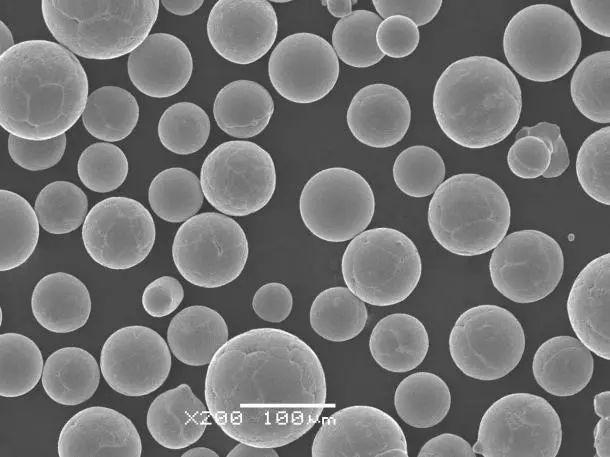
Choosing the Right Molybdenum Metal Powder Model
Selecting the ideal molybdenum metal powder model hinges on the specific application. Here are some crucial factors to consider:
- Pureza: Higher purity grades offer superior performance but come at a premium cost. Standard grades provide a balance between cost and functionality for many applications.
- Tamanho da partícula: Finer powders offer a larger surface area, which can be beneficial for applications like catalysis. However, coarser powders might be easier to handle and process for powder metallurgy.
- Elementos de liga: Adding specific elements can enhance strength, high-temperature performance, or other properties depending on the desired outcome.
Consulting with a reputable molybdenum powder supplier can help you navigate these factors and select the optimal model for your needs.
the Strengths of Molybdenum Metal Powder
Molybdenum metal powder boasts a compelling list of advantages that make it a valuable material across various industries. Let’s delve into some of its key strengths:
- Força excepcional: Molybdenum is inherently strong, and the powder form allows it to be incorporated into composite materials, further enhancing their structural integrity. This makes it ideal for applications like gears, bearings, and armor components.
- Alto ponto de fusão: Molybdenum’s incredibly high melting point makes it suitable for high-temperature environments. It can withstand extreme heat without melting or losing its structural integrity, a crucial property for components in furnaces, jet engines, and rocket engines.
- Excelente resistência à corrosão: Molybdenum exhibits remarkable resistance to corrosion, making it a valuable material for applications exposed to harsh chemicals or saltwater environments. This property is particularly beneficial for marine components, chemical processing equipment, and heat sinks.
- Good Electrical Conductivity: While not as conductive as copper or silver, molybdenum powder possesses good electrical conductivity. This makes it a suitable material for electrical contacts and electrodes in various applications.
These combined strengths make molybdenum metal powder a versatile material for a wide range of demanding applications.
the Limitations of Molybdenum Metal Powder
Despite its impressive properties, molybdenum metal powder does have some limitations to consider:
- Inflamabilidade: In powder form, molybdenum can be flammable, especially in fine particle sizes. Proper handling and storage procedures are crucial to mitigate this risk.
- Reatividade: Molybdenum can react with certain elements like oxygen and nitrogen at high temperatures. This can affect the powder’s properties and needs to be considered during processing.
- Custo: High-purity molybdenum powder can be expensive compared to some alternative materials. A cost-benefit analysis is essential to determine if molybdenum is the most economical choice for a particular application.
the Applications of Molybdenum Metal Powder
Molybdenum metal powder isn’t a niche material confined to a laboratory shelf. Its unique properties translate into a surprisingly wide range of applications across various industries. Here, we’ll explore some of the prominent domains where molybdenum metal powder shines:
Metalurgia do Pó: This is arguably the most significant application of molybdenum metal powder. The powder is compacted and shaped using specialized techniques like pressing and sintering. This process allows the creation of complex and high-performance components with properties tailored to specific needs. Some examples include:
- Gears and Bearings: Molybdenum-containing alloys produced via powder metallurgy offer exceptional strength, wear resistance, and dimensional stability, making them ideal for gears and bearings in automotive, aerospace, and industrial machinery applications.
- Ferramentas de corte: Molybdenum-based tool steels formulated with powder metallurgy techniques boast superior hardness and hot hardness, allowing them to handle demanding cutting operations efficiently. These tools are used in machining, metalworking, and woodworking industries.
- Dissipadores de calor: Molybdenum’s excellent thermal conductivity makes it a valuable material for heat sinks, which dissipate heat away from electronic components. Powder metallurgy allows for the creation of intricate heat sink designs with high surface area for efficient heat transfer.
Eletrônicos: Molybdenum metal powder plays a crucial role in various electronic components due to its good electrical conductivity and high melting point. Here are some specific applications:
- Electrical Contacts: Molybdenum’s ability to conduct electricity while resisting corrosion and wear makes it suitable for electrical contacts in switches, relays, and circuit breakers.
- Sputtering Targets: Molybdenum can be used as a target material in a sputtering process to deposit thin films of molybdenum onto various substrates. These thin films find application in transistors, capacitors, and other electronic devices.
- High-Temperature Electronics: Molybdenum’s high melting point makes it a potential candidate for electronic components used in high-temperature environments, such as those found in jet engines or spacecraft.
Aeroespacial: The relentless pursuit of performance and efficiency in the aerospace industry makes molybdenum metal powder a valuable asset. Here’s how it finds use:
- Turbine Blades: Molybdenum alloys offer a compelling combination of strength, high-temperature performance, and creep resistance, making them suitable for turbine blades in jet engines. These blades operate under extreme temperatures and pressures, and molybdenum helps them withstand these demanding conditions.
- Rocket Engine Components: Similar to turbine blades, molybdenum’s ability to handle high temperatures makes it a candidate for rocket engine components that experience extreme heat during operation.
- Heat Shields: Molybdenum’s ability to withstand heat makes it a potential material for heat shields on spacecraft, protecting them from the scorching temperatures encountered during re-entry into the Earth’s atmosphere.
Outros aplicativos: Beyond these prominent domains, molybdenum metal powder finds use in various other applications:
- Lubrication: Molybdenum disulfide (MoS2), a compound derived from molybdenum powder, is a well-known solid lubricant with excellent friction-reducing properties. It’s used in various lubricants for extreme pressure and high-temperature applications.
- Pigmentos: Molybdenum compounds can be used to produce pigments with a vibrant blue or yellow color. These pigments find application in paints, inks, and plastics.
- Catalisadores: Molybdenum-based catalysts are used in various chemical reactions, promoting the efficiency and selectivity of these processes.
This list merely scratches the surface of the diverse applications for molybdenum metal powder. As research and development continue, we can expect to see even more innovative uses for this versatile material emerge in the future.
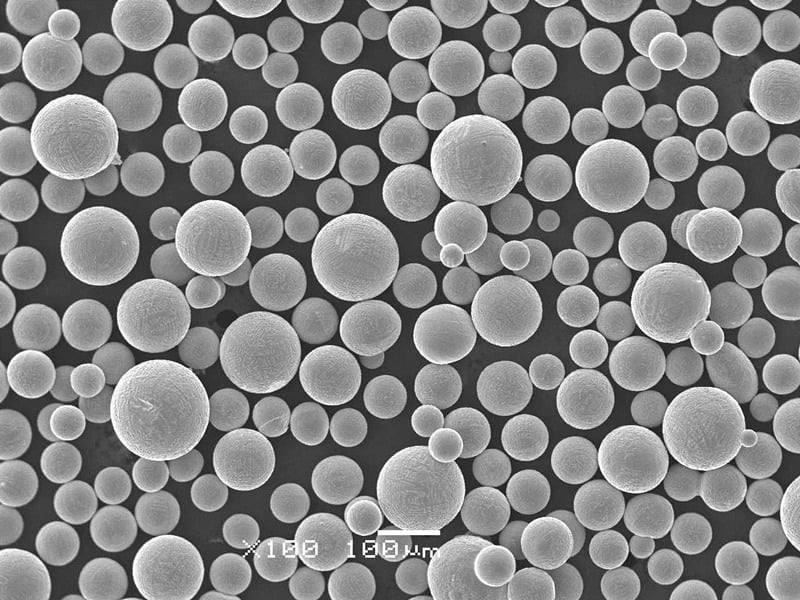
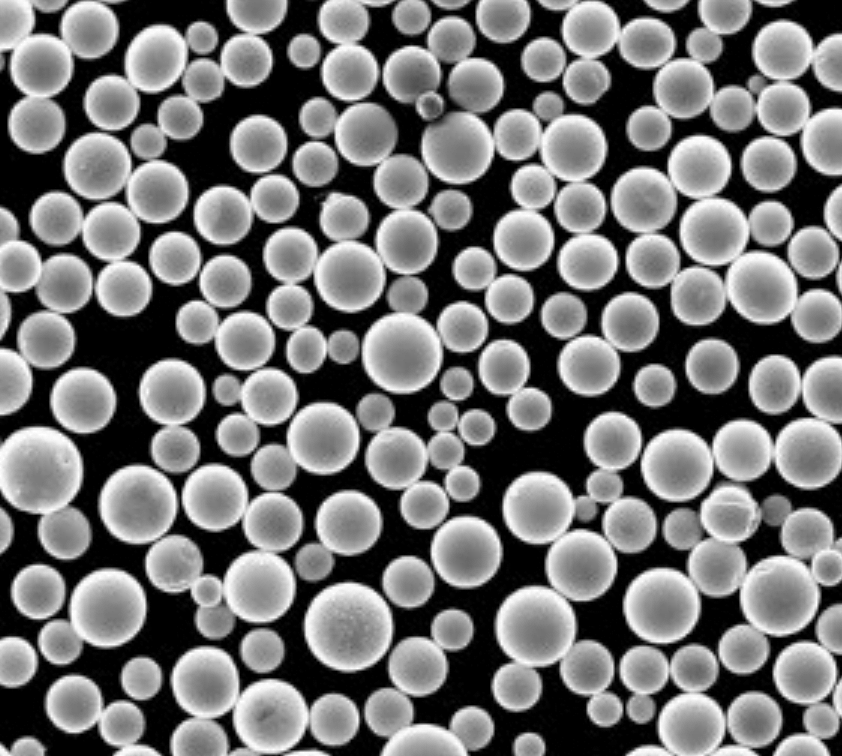
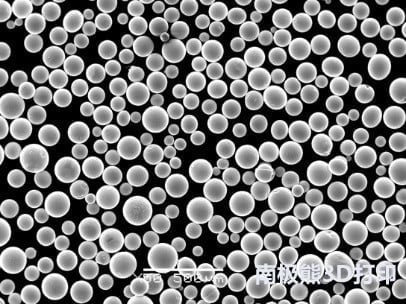
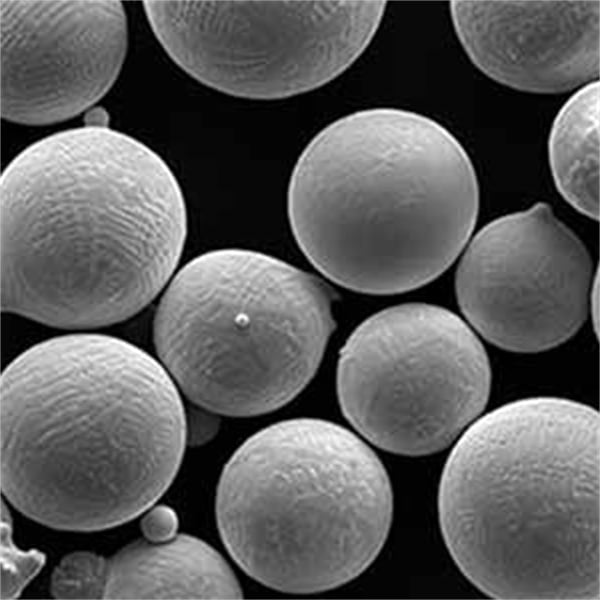
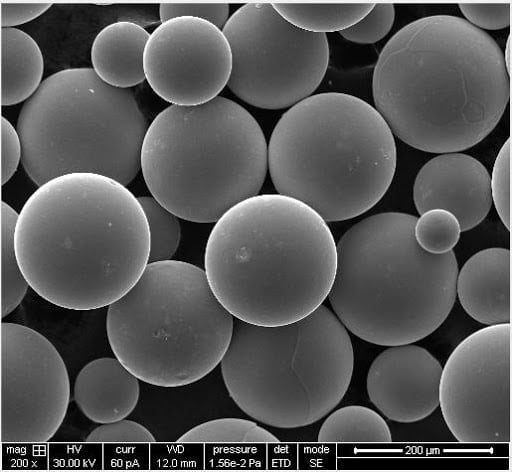
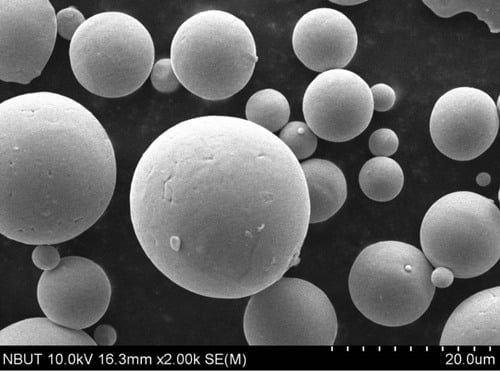
Molybdenum Metal Powder Grades and Standards
Molybdenum metal powder isn’t a one-size-fits-all solution. Different applications demand specific properties, and manufacturers offer a variety of grades and standards to cater to these needs. Here’s a breakdown of some key factors to consider:
Fator | Descrição | Impacto nos aplicativos |
---|---|---|
Pureza | The percentage of molybdenum (Mo) in the powder. | Higher purity grades offer better performance but come at a higher cost. |
Tamanho das partículas | The size and distribution of molybdenum particles in the powder. | Finer powders offer a larger surface area, while coarser powders might be easier to handle. |
Densidade Aparente | The bulk density of the powder. | Affects how much powder can be packed into a mold during powder metallurgy processes. |
Fluidez | A facilidade com que o pó flui. | Crucial for efficient processing in powder metallurgy applications. |
Conteúdo de oxigênio | The amount of oxygen present in the powder, typically as oxides. | Can affect the powder’s sintering behavior and final properties. |
Carbon Content | The amount of carbon present in the powder. | Can improve strength and hardenability but can lead to brittleness at high levels. |
Teor de Nitrogênio | The amount of nitrogen present in the powder. | May enhance high-temperature properties but can also promote nitride formation. |
Padrões | The industry standards or specifications to which the powder conforms. | Ensure consistent quality and meet specific application requirements. Common standards include ASTM International (ASTM) and American National Standards Institute (ANSI) |
Examples of Molybdenum Metal Powder Grades and Standards:
Here are some illustrative examples of molybdenum metal powder grades and standards:
- ASTM B163-20 (Standard Specification for Molybdenum Powder): This is a widely used standard for molybdenum powder used in powder metallurgy applications. It specifies different grades based on purity, particle size, and apparent density.
- HP Mo Powder (High Purity Molybdenum Powder): This is a commercially available grade with a minimum molybdenum content of 99.95%. It’s suitable for applications demanding exceptional purity, like electronic components and crucibles for high-temperature melting.
- AmAtom AM-MP-100: This is an example of a commercially available molybdenum powder with a specific particle size distribution (e.g., 100 microns) tailored for specific applications.
Selecting the Right Grade
Choosing the optimal molybdenum metal powder grade hinges on the specific application. Here are some crucial factors to consider:
- Propriedades desejadas: What are the key properties required for the final product (e.g., strength, high-temperature performance, electrical conductivity)?
- Processing Method: The powder metallurgy technique used (e.g., pressing, sintering) might influence the preferred particle size and flowability characteristics.
- Considerações sobre custos: Higher purity grades or finer particle sizes often come at a premium cost. Balancing cost with desired performance is crucial.
Consulting with a reputable molybdenum powder supplier can be invaluable in navigating the various grades and standards and selecting the most suitable option for your specific needs.
Molybdenum Metal Powder vs. Alternative Materials
Molybdenum metal powder isn’t the only player in the game. Several alternative materials offer similar properties and compete for applications in various industries. Here, we’ll take a closer look at two prominent contenders:
- Pó de tungstênio: Tungsten shares many similarities with molybdenum, including high melting point, excellent strength, and good corrosion resistance. However, tungsten is typically denser and more expensive than molybdenum. When weight is a critical factor, molybdenum might be the preferred choice.
Advantages of Molybdenum Metal Powder:
- Lower Cost: Compared to tungsten, molybdenum is generally more affordable.
- Good Formability: Molybdenum powder exhibits good formability, making it easier to shape into complex components during powder metallurgy processes.
- Alta relação entre resistência e peso: Molybdenum offers a favorable balance between strength and weight, making it suitable for applications where weight reduction is crucial.
Disadvantages of Molybdenum Metal Powder:
- Lower Melting Point: While still very high, molybdenum’s melting point is slightly lower than tungsten’s, which might limit its use in some extremely high-temperature applications.
- Oxidation Susceptibility: Molybdenum can oxidize at high temperatures, potentially affecting its properties. Careful processing techniques are needed to mitigate this issue.
- Ferro em pó: Iron powder is a widely used and cost-effective alternative for applications where exceptional strength or high-temperature performance aren’t paramount.
Advantages of Iron Powder:
- Low Cost: Iron powder is significantly cheaper than molybdenum powder, making it an attractive option for cost-sensitive applications.
- Wide Availability: Iron is a more abundant element compared to molybdenum, making iron powder readily available.
Disadvantages of Iron Powder:
- Lower Strength: Iron powder generally offers lower strength compared to molybdenum powder.
- Poor Corrosion Resistance: Iron is susceptible to corrosion, limiting its use in harsh environments.
The choice between molybdenum metal powder and its alternatives depends on the specific application requirements. Carefully consider factors like cost, desired properties, and environmental conditions to make an informed decision.
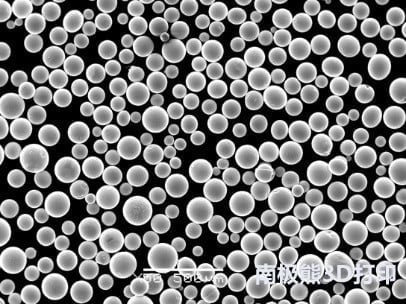
FAQ
Q: Is molybdenum metal powder safe to handle?
A: Molybdenum metal powder is generally considered safe to handle under normal conditions. However, fine molybdenum powder can be flammable and should be handled with care. Proper personal protective equipment (PPE) like gloves, safety glasses, and a respirator might be necessary depending on the specific handling procedures.
Q: How is molybdenum metal powder recycled?
A: Molybdenum scrap and leftover powder from manufacturing processes can be recycled back into usable molybdenum metal powder. There are two main methods for molybdenum powder recycling:
- Hydrometallurgical recycling: This process involves dissolving molybdenum scrap in a chemical solution, followed by purification and conversion back into molybdenum powder.
- Pyrometallurgical recycling: This method involves melting molybdenum scrap in a furnace, removing impurities, and then converting the molten molybdenum into a powder form.
Recycling molybdenum metal powder helps conserve resources, reduce environmental impact, and promotes sustainability in the manufacturing process.
Q: What are the future prospects for molybdenum metal powder?
A: The future of molybdenum metal powder appears promising. Here are some trends suggesting continued growth and innovation:
- Advancements in powder metallurgy: As powder metallurgy techniques become more sophisticated, molybdenum powder will likely play a role in developing even stronger, lighter, and more complex components.
- Emerging applications: Research and development efforts might lead to new applications for molybdenum powder in sectors like additive manufacturing (3D printing) and energy storage technologies.
- Foco na sustentabilidade: The ability to recycle molybdenum powder effectively aligns with the growing focus on sustainability in manufacturing, making it an attractive material choice for environmentally conscious industries.
Sobre o 3DP mETAL
Categoria do produto
ENTRE EM CONTATO
Alguma dúvida? Envie-nos uma mensagem agora! Após receber sua mensagem, processaremos sua solicitação com toda equipe.