Imagine a 3D printer that isn’t confined to a single material, but instead functions like a painter’s palette, wielding a rainbow of materials to construct objects with remarkable detail and functionality. This isn’t science fiction; it’s the magic of Jateamento com vários materiais (MMJ), an additive manufacturing (AM) process that’s revolutionizing the way we prototype and produce complex parts.
What is Multi-Material Jetting?
At its core, MMJ borrows inspiration from the familiar inkjet printer. But instead of ink cartridges, MMJ printers house a multitude of material jets that precisely deposit photopolymer droplets onto a build platform. Layer by layer, these droplets solidify under UV light, meticulously building the desired 3D object.
The real magic lies in the “multi” aspect. Unlike its single-material counterparts, MMJ printers can juggle a variety of materials within a single build. This opens a door to a world of possibilities: Imagine a prototype with rigid and flexible components, a model with different colors and textures, or even a medical implant that combines biocompatible and hard-wearing materials.
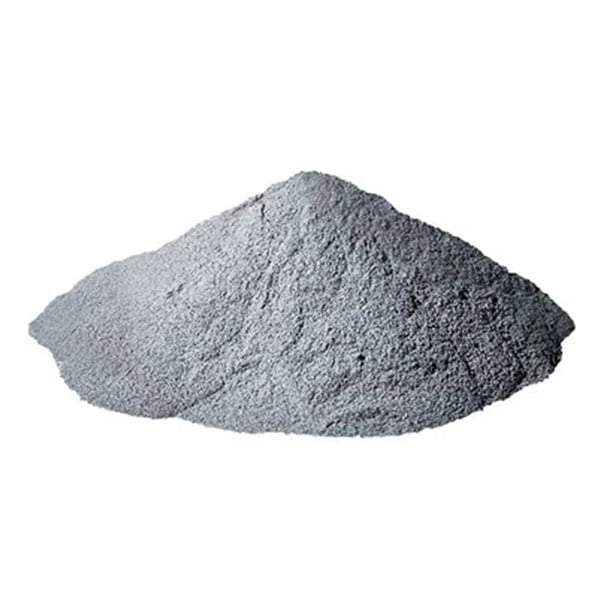
Aplicativos de Jateamento com vários materiais
The versatility of MMJ makes it a highly sought-after technology across various industries. Here are some captivating applications:
- Prototipagem: MMJ excels at creating realistic prototypes with intricate details and multiple functionalities. This allows designers and engineers to thoroughly test form, fit, and function before committing to large-scale production.
- Manufacturing: MMJ can be used to produce end-use parts, particularly for low-volume applications. The ability to combine materials within a single build streamlines production and eliminates the need for assembly of separate components.
- Assistência médica: MMJ is making waves in the medical field. It can be used to create customized prosthetics with varying degrees of flexibility and rigidity, or even intricate anatomical models for surgical planning.
- Arte e design: With its ability to render high-fidelity details and vibrant colors, MMJ is a boon for artists and designers. They can create unique and functional pieces with complex textures and multi-material compositions.
Advantages of Multi-Material Jetting
MMJ boasts several advantages that make it a compelling choice for various applications:
- Funcionalidade aprimorada: The ability to combine different materials within a single build unlocks a new level of functionality in printed parts. Imagine a drone wing with a rigid core for strength and a flexible leading edge for maneuverability – all printed in one go!
- Prototipagem realista: MMJ prototypes closely resemble the final product in terms of material properties and aesthetics. This allows for more comprehensive testing and design iterations before production.
- Streamlined Production: MMJ eliminates the need for assembly in many cases, as different material properties can be integrated within the same build. This translates to faster production times and reduced costs.
- Alta resolução e precisão: MMJ printers produce parts with exceptional detail and dimensional accuracy, making them ideal for applications demanding intricate features.
- Wide Material Range: MMJ offers compatibility with a vast array of materials, including rigid thermoplastics, flexible elastomers, biocompatible resins, and even opaque and transparent materials.
Desvantagens de Jateamento com vários materiais
While MMJ offers a plethora of benefits, it’s not without its limitations:
- Custo: MMJ printers and materials tend to be on the higher end of the 3D printing spectrum. This can be a barrier for entry for hobbyists or low-volume applications.
- Limited Material Strength: Compared to some traditional manufacturing techniques, MMJ-produced parts may not boast the same level of strength, especially for load-bearing applications.
- Pós-Processamento: MMJ parts often require post-processing steps like support removal and surface finishing, which can add time and complexity to the workflow.
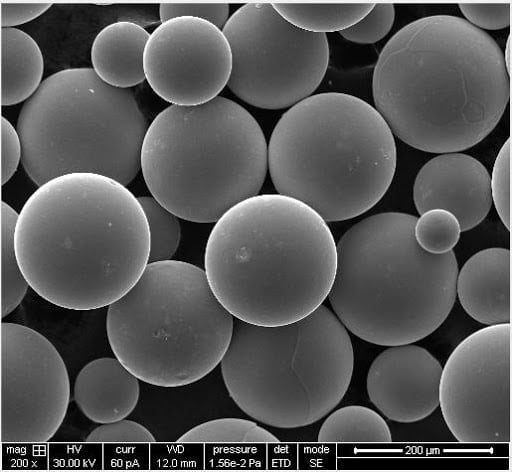
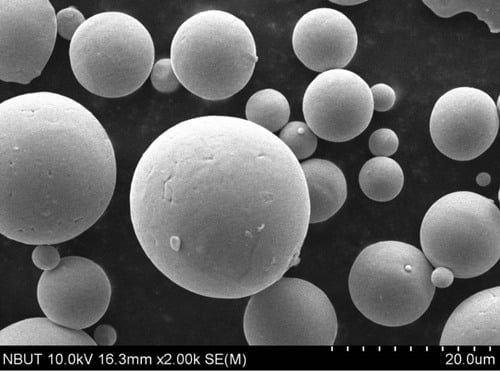
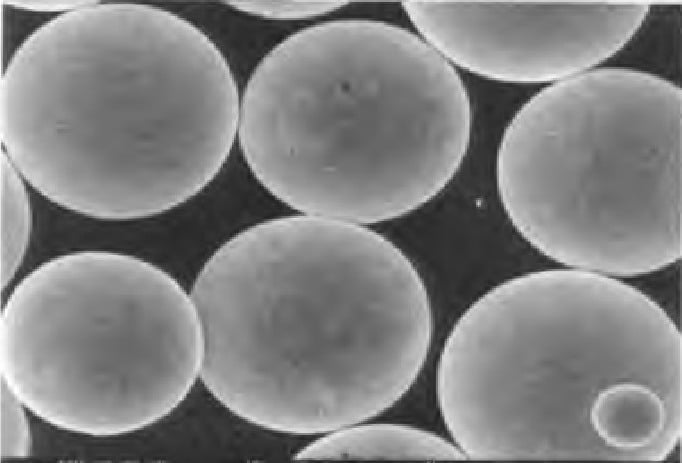
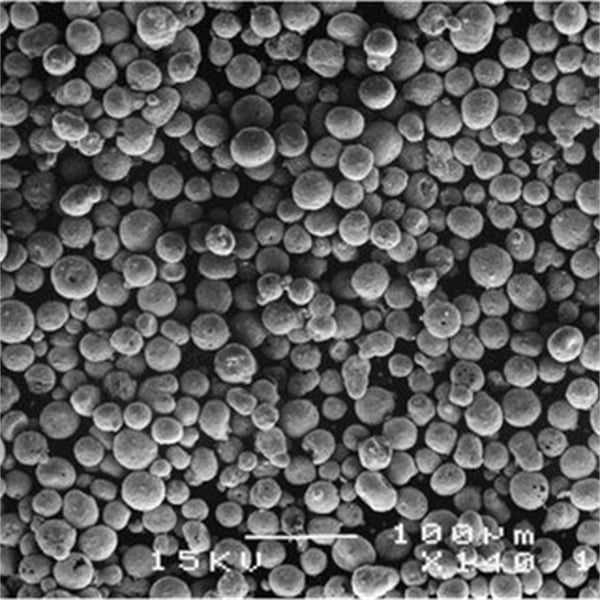
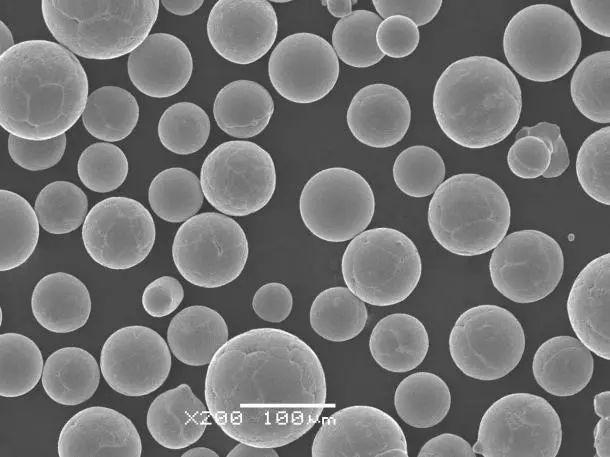
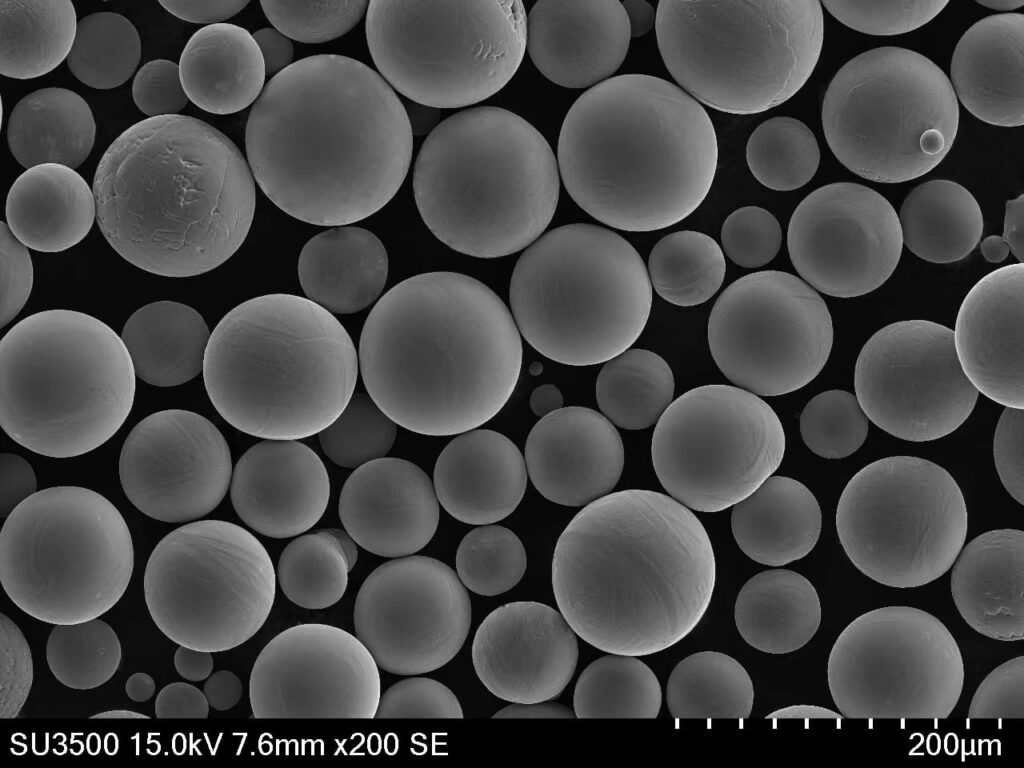
Factors to Consider When Choosing Multi-Material Jetting
Whether MMJ is the right fit for your project depends on several factors:
- Complexity of Design: If your design demands intricate details and multiple functionalities, MMJ could be a perfect choice.
- Requisitos de material: Consider the specific material properties needed for your project. MMJ offers a wide range, but it may not encompass everything.
- Volume de produção: For high-volume production runs, traditional manufacturing techniques might be more cost-effective.
- Orçamento: MMJ printers and materials come at a premium. Ensure your project budget can accommodate the technology.
The Future of Multi-Material Jetting
MMJ is a rapidly evolving technology. Here are some exciting trends to watch for:
- Materiais avançados: The development of new materials with enhanced strength, flexibility, and biocompatibility will further expand the applications of MMJ.
- Multi-Jet Integration: Printers with even more jet heads will enable even more.
- Material Jetting Resolution: Measured in microns (μm), resolution refers to the minimum size of a material droplet that the print head can deposit. Higher resolution translates to finer details and smoother surface finishes. Typical MMJ resolutions range from 16 to 32 microns.
Parâmetro | Descrição |
---|---|
Material Jetting Resolution | Minimum size of a material droplet |
Volume de construção | Maximum dimensions of a printable object |
Compatibilidade de materiais | Range of materials the printer can handle |
Espessura da camada | Thickness of each layer deposited during printing |
Velocidade de impressão | Rate at which the printer builds the object |
Material Compatibility in Multi-Material Jetting
As mentioned earlier, a significant advantage of MMJ is its compatibility with a diverse range of materials. Here’s a glimpse into the material palette an MMJ printer might offer:
- Rigid Thermoplastics: These materials, like ABS and Polycarbonate (PC), provide excellent strength and stiffness, making them suitable for structural components and functional prototypes.
- Flexible Elastomers: Think rubber-like materials like TangoPlus. These offer flexibility and shock absorption, ideal for applications requiring grip, seals, or living hinges.
- Biocompatible Resins: MMJ opens doors in medical applications with materials like biocompatible resins that can be used for customized prosthetics or surgical models.
- Supportive Materials: These temporary structures are used to support overhanging features during printing and are later removed.
Additionally, some MMJ systems allow for the incorporation of specialty materials like:
- Opaque and Transparent Materials: Imagine creating a model with clear windows or a housing with both opaque and transparent sections – all in a single print.
- Digital Metal Materials: These composite materials mimic the look and feel of metal, offering a cost-effective way to prototype metallic parts.
Jateamento com vários materiais vs Other 3D Printing Processes
When choosing a 3D printing process, understanding the strengths and weaknesses of MMJ compared to other options is crucial. Here’s a quick comparison:
- Fused Deposition Modeling (FDM): FDM, a popular 3D printing process, uses filament to create objects layer by layer. While it’s generally more affordable than MMJ, FDM is limited to single-material printing and offers lower resolution and detail compared to MMJ.
Recurso | Multi-Material Jetting (MMJ) | Modelagem por deposição fundida (FDM) |
---|---|---|
Compatibilidade de materiais | Multiple materials | Single material |
Resolution and Accuracy | Alto | Moderado |
Acabamento da superfície | Smooth | Layered texture |
Custo por peça | Maior | Mais baixo |
Velocidade | Moderado | Moderado |
- Estereolitografia (SLA): SLA utilizes a laser to cure liquid resin layer by layer. It offers exceptional resolution and detail, comparable to MMJ. However, SLA generally has a smaller build volume and limited material compatibility compared to MMJ.
Recurso | Multi-Material Jetting (MMJ) | Estereolitografia (SLA) |
---|---|---|
Compatibilidade de materiais | Multiple materials | Limited materials |
Resolution and Accuracy | Alto | Alto |
Acabamento da superfície | Smooth | Smooth |
Volume de construção | Larger | Smaller |
Custo por peça | Moderado | Moderado a alto |
When to Choose Jateamento com vários materiais
Given its unique capabilities and considerations, MMJ shines in specific scenarios:
- Prototyping complex, multi-functional parts: If your design demands intricate details, varying textures, or integration of different functionalities, MMJ allows you to create highly realistic prototypes that closely resemble the final product.
- Creating models for medical applications: The ability to combine biocompatible and rigid materials makes MMJ ideal for creating customized prosthetics, anatomical models, or surgical guides.
- Producing small batches of customized parts: MMJ excels at producing low-volume runs of parts with varying material properties. This eliminates the need for assembly and allows for rapid design iterations.
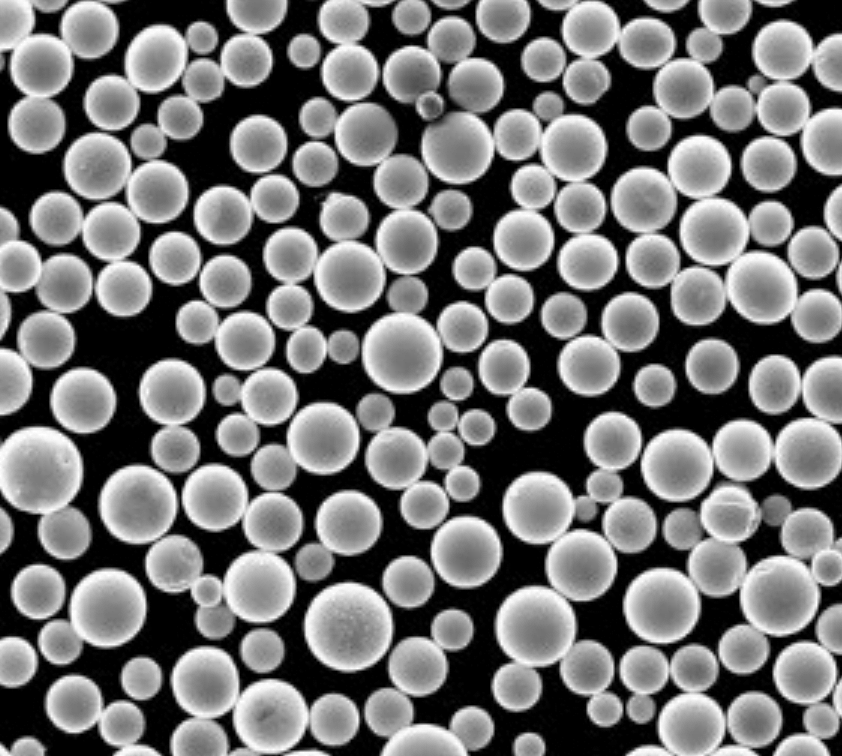
FAQ
What is the difference between Multi-Material Jetting and PolyJet?
While the terms are often used interchangeably, there is a subtle distinction:
- Multi-Material Jetting (MMJ): This refers to the broader 3D printing process itself. It utilizes multiple material jets to deposit droplets of photopolymer resin onto a build platform, building objects layer by layer.
- PolyJet: PolyJet is a specific brand name for MMJ technology developed by Stratasys, a leading manufacturer of 3D printers. So, any time you hear “PolyJet,” it essentially refers to MMJ printers made by Stratasys.
Is Multi-Material Jetting safe?
The safety of MMJ depends on the materials being used. Some materials, particularly certain resins, might emit mild fumes during printing. To ensure a safe printing environment:
- Always consult the Material Safety Data Sheet (MSDS): This document provides crucial information on the specific material’s properties, potential hazards, and recommended handling procedures.
- Ventilação adequada: If the MSDS recommends it, ensure adequate ventilation in your printing area to disperse any potential fumes.
- Follow Safety Protocols: Wear recommended personal protective equipment (PPE) like gloves and safety glasses, especially when handling uncured resins.
Can Multi-Material Jetting print in full color?
Yes, but with a caveat! While not all MMJ systems offer full-color capabilities, some advanced printers can jet photopolymer resins with a wide range of colors. These printers essentially function like high-tech inkjet printers, allowing for the creation of highly realistic prototypes and functional parts with intricate color details.
What are the limitations of Multi-Material Jetting?
MMJ offers a powerful toolset, but it’s not without limitations:
- Custo: MMJ printers and materials tend to be on the pricier side compared to other 3D printing technologies. This can be a barrier for hobbyists or low-volume applications.
- Força: While MMJ parts can be quite strong, they may not match the strength of parts produced through traditional manufacturing techniques, especially for highly load-bearing applications.
- Pós-Processamento: MMJ parts often require post-processing steps like support removal and surface finishing. This can add time and complexity to the workflow compared to some other 3D printing methods.
What’s the future outlook for Multi-Material Jetting?
The future of MMJ is brimming with exciting possibilities:
- Materiais avançados: The development of new materials with enhanced properties like superior strength, increased flexibility, and improved biocompatibility will significantly expand the applications of MMJ.
- Multi-Jet Integration: Printers with even more jet heads are on the horizon. This will enable the creation of even more intricate combinations of materials within a single build, leading to even more functional and complex parts.
- Avanços no software: Improvements in 3D modeling software specifically designed for MMJ will streamline the design and printing process, making it more accessible and user-friendly for a wider range of users.
By overcoming limitations and embracing advancements, Multi-Material Jetting is poised to play a transformative role in shaping the future of design and manufacturing.
Sobre o 3DP mETAL
Categoria do produto
ENTRE EM CONTATO
Alguma dúvida? Envie-nos uma mensagem agora! Após receber sua mensagem, processaremos sua solicitação com toda equipe.