Imagine a world where crafting intricate metal parts is as simple as shaping playdough. Well, with the advent of Pós preparados PREP, that world is inching closer to reality. PREP, or Plasma Rotating Electrode Process, is a revolutionary metal powder manufacturing technique that’s taking the additive manufacturing (3D printing) industry by storm. But what exactly are PREP-prepared powders, and how do they stack up against traditional options? Buckle up, because we’re about to delve into the fascinating world of these next-generation metal marvels.
What are PREP-Prepared Powders?
Unlike conventional metal powders produced through processes like gas or water atomization, PREP takes a unique approach. It utilizes a rotating electrode that’s partially submerged in molten metal within a plasma chamber. Imagine a metal bar spinning like a merry-go-round, half-dipped in a fiery vat. As the electrode rotates, the intense heat from the plasma melts its surface. Molten metal droplets are then flung outwards due to centrifugal force, rapidly solidifying into fine, spherical powder particles as they cool in the surrounding inert gas environment.
This innovative approach yields metal powders with several advantages over traditional methods. Here’s a table summarizing the key characteristics:
Recurso | PREP-Prepared Powders (pós preparados) | Traditional Methods (Gas/Water Atomization) |
---|---|---|
Formas das Partículas | Esférico | irregular |
Morfologia da superfície | Smooth | Rougher |
Pureza | Alto | Can contain impurities |
Fluidez | Excelente | Lower flowability |
Satellite Formation | Mínimo | More satellite particles (smaller, undesirable particles) |
The spherical shape of PREP powders is a game-changer. These near-perfect spheres pack together more efficiently, leading to superior flowability within the 3D printer. This translates to smoother layer formation during printing, ultimately resulting in denser, higher-quality metal parts.
Furthermore, the smooth surface morphology of PREP powders minimizes surface area, reducing the risk of oxidation and contamination. This translates to purer powders, essential for applications demanding high performance and tight tolerances.
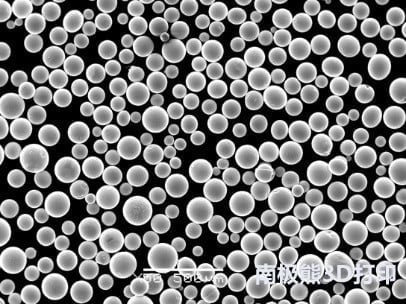
Unveiling the Power of PREP
Now that we understand the core concept, let’s explore some specific PREP-prepared metal powders available in the market. Here’s a breakdown of ten popular options, highlighting their properties and applications:
1. 316L Stainless Steel
- Descrição: An austenitic stainless steel known for its excellent corrosion resistance, making it ideal for applications exposed to harsh environments like chemical processing plants and marine components.
- Aplicativos: Aerospace components, medical implants, chemical processing equipment, jewelry.
2. 17-4 PH Stainless Steel
- Descrição: A precipitation-hardening stainless steel offering high strength and good corrosion resistance. It’s particularly valuable for parts requiring a balance of strength and ductility.
- Aplicativos: Aerospace components, automotive parts, gears, shafts.
3. Inconel 625
- Descrição: A nickel-chromium superalloy renowned for its exceptional high-temperature strength and oxidation resistance. It’s the go-to choice for parts operating under extreme heat, such as jet engine components.
- Aplicativos: Gas turbine blades, heat exchangers, rocket engine components.
4. Inconel 718
- Descrição: Another high-performance nickel-chromium superalloy offering a potent combination of strength, corrosion resistance, and good weldability. It’s widely used in demanding aerospace and power generation applications.
- Aplicativos: Turbine discs, rocket engine components, fasteners, pressure vessels.
5. Titanium 6Al-4V
- Descrição: A workhorse titanium alloy prized for its low weight, high strength, and excellent corrosion resistance. It’s extensively used in aerospace and biomedical applications.
- Aplicativos: Aircraft parts, medical implants, dental implants, sporting goods.
6. Aluminum Si7Mg0.6
- Descrição: A high-strength cast aluminum alloy offering good castability and machinability. It’s a popular choice for lightweight components requiring a balance of strength and weight savings.
- Aplicativos: Automotive parts, electronic enclosures, architectural components.
7. Copper
- Descrição: Pure copper powder known for its exceptional thermal and electrical conductivity. It’s opening doors for 3D printing of heat sinks, electrical components, and electrodes.
- Aplicativos: Heat exchangers, electrical busbars, waveguides, electrodes for additive manufacturing.
8. Nickel
- Descrição: High-purity nickel powder valued for its excellent corrosion resistance, ductility, and good weldability. It finds applications in various sectors, including electronics and chemical processing.
- Aplicativos: Electrical components, chemical processing equipment, battery electrodes, electroplating.
9. Cobalt Chrome (CoCr)
- Descrição: A biocompatible cobalt-chromium alloy known for its high strength, wear resistance, and excellent corrosion resistance in the human body. It’s a mainstay material for orthopedic implants.
- Aplicativos: Hip and knee replacements, dental implants, surgical instruments.
10. Hastelloy C-22
- Descrição: A nickel-chromium-molybdenum superalloy renowned for its exceptional corrosion resistance in a wide range of aggressive environments, including strong acids and chlorides. It’s ideal for parts exposed to harsh chemicals in the oil and gas industry and chemical processing plants.
- Aplicativos: Chemical processing equipment, heat exchangers, pulp and paper processing equipment, waste treatment facilities.
This list just scratches the surface of the vast potential of PREP-prepared metal powders. As research and development continue, we can expect an even wider range of materials becoming available, pushing the boundaries of what’s achievable with 3D printing.
Aplicativos de PREP-Prepared Powders (pós preparados)
The exceptional properties of PREP powders unlock a treasure trove of possibilities for 3D printing applications. Here’s a glimpse into some key areas where they’re making a significant impact:
Área de aplicação | Advantages of PREP Powders | Exemplos |
---|---|---|
Aeroespacial: | Lighter, stronger components for improved fuel efficiency and performance. | Turbine blades, aircraft structures, rocket engine components. |
Implantes médicos: | Biocompatible materials for customized implants with improved osseointegration (bone bonding). | Hip and knee replacements, dental implants, cranial implants. |
Automotivo: | Lightweight, high-strength components for weight reduction and improved fuel economy. | Engine components, body panels, heat exchangers. |
Bens de consumo: | Complex, high-quality metal parts for innovative product designs. | Jewelry, sporting goods, electronics enclosures. |
Tooling and Prototyping: | Rapid creation of functional metal prototypes and tooling with superior strength and dimensional accuracy. | Jigs and fixtures, casting molds, rapid tooling for low-volume production. |
This table highlights just a few examples. The versatility of PREP powders makes them applicable across various industries, with the potential to revolutionize how we design, manufacture, and use metal components.
Advantages and Limitations of PREP-Prepared Powders: A Balanced Perspective
While PREP powders offer a compelling set of advantages, it’s important to acknowledge their limitations for a well-rounded understanding.
Vantagens:
- Superior Flowability: The spherical shape of PREP powders enhances flowability within the 3D printer, leading to smoother layer formation and ultimately, denser, higher-quality metal parts.
- Enhanced Surface Quality: The smooth surface morphology minimizes surface area, reducing the risk of oxidation and contamination. This translates to purer powders, crucial for high-performance applications.
- Improved Powder Reuse: The spherical shape and consistent size distribution of PREP powders minimize satellite formation (smaller, undesirable particles) during printing. This allows for better powder recyclability, reducing waste and production costs.
- Wider Range of Materials: The PREP process is adaptable to various metals and alloys, opening doors for 3D printing with previously challenging materials.
Limitações:
- Custo mais alto: Currently, PREP powders tend to be more expensive than traditionally produced powders due to the relatively new technology and potentially lower production volumes. However, as demand increases and production scales up, the cost is expected to decrease.
- Disponibilidade limitada: While the range of PREP powders is expanding, it might not encompass all the metal varieties readily available in conventional methods. This could limit the immediate applicability of PREP in certain niche applications.
- Otimização de processos: The PREP process requires ongoing research and development to optimize parameters for specific materials and desired properties. Fine-tuning these parameters is crucial for achieving consistent and predictable printing results.
Despite these limitations, the advantages of PREP powders are undeniable. As technology advances and production costs go down, we can expect them to become a mainstream choice for a vast array of 3D printing applications.
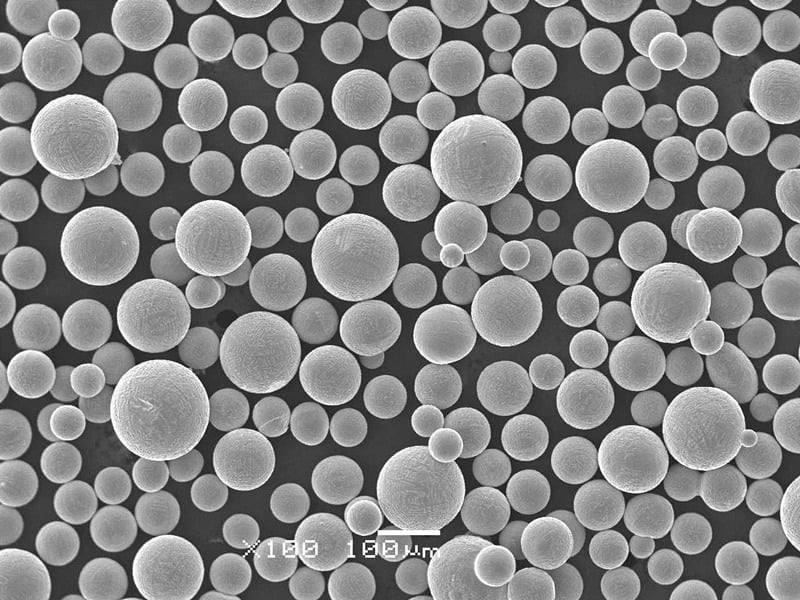
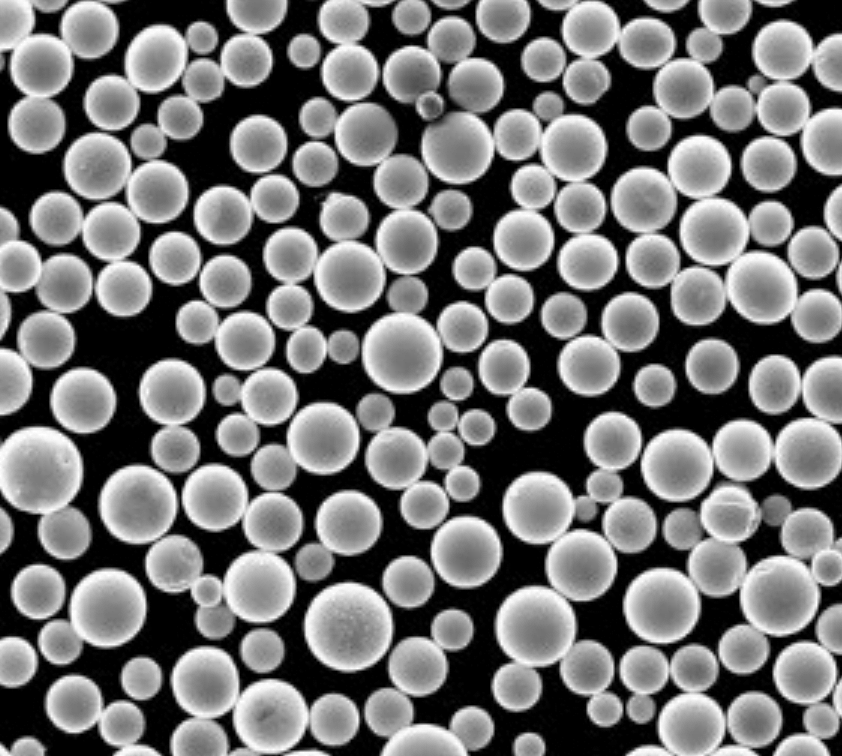
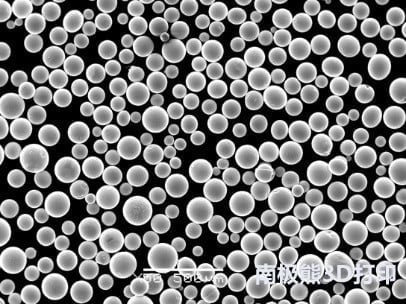
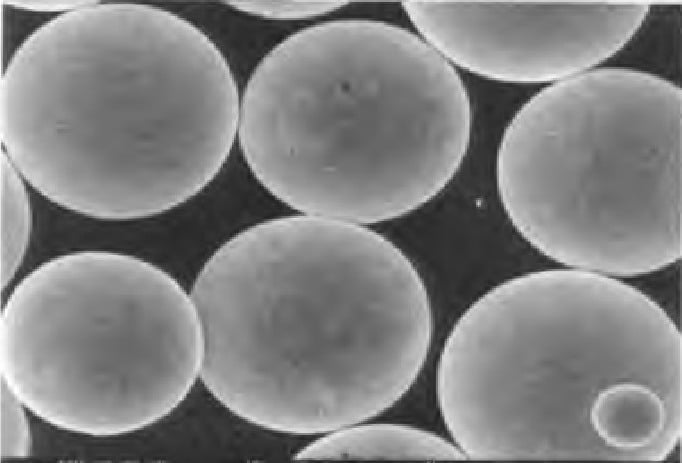
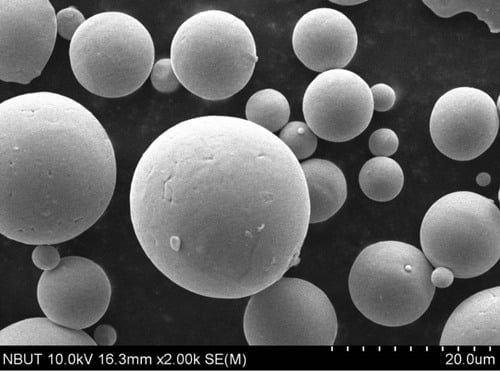
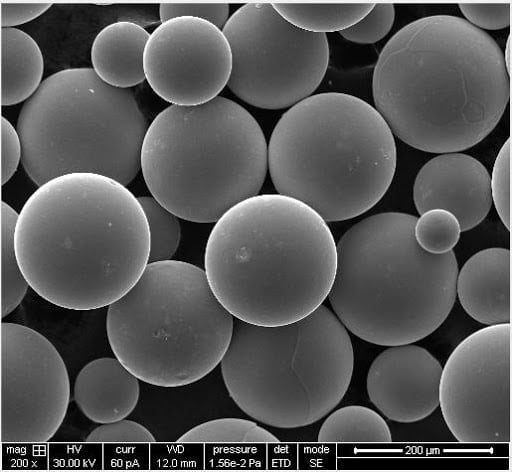
Specifications, Sizes, Grades, and Standards: Demystifying PREP Powders
Here’s a breakdown of key specifications, sizes, grades, and standards associated with Pós preparados PREP:
Especificações:
- Distribuição do tamanho das partículas: PREP powders typically fall within a specific size range, often expressed in micrometers (µm). A tighter size distribution ensures consistent flow and layer formation during printing. Common size ranges for metal powders can vary from 15-45 µm to 45-150 µm, depending on the desired application and printing technology.
- Esfericidade: As mentioned earlier, spherical particles are a hallmark of PREP powders. This parameter reflects how closely the particles resemble perfect spheres. A higher sphericity value (closer to 1) translates to better flowability and packing density.
- Fluidez: Measured by various techniques like the Hall Flowmeter method, flowability indicates how easily the powder moves and fills the printing chamber. Excellent flowability is crucial for smooth printing and consistent part quality.
- Densidade Aparente: This refers to the bulk density of the powder, measured in grams per cubic centimeter (g/cm³). It reflects how tightly the particles are packed together in their natural state.
- Densidade de batida: This density is measured after tapping the powder container to achieve a more compact packing. The difference between apparent and tap density indicates the powder’s flowability.
Tamanhos:
As discussed earlier, PREP powders come in various sizes depending on the application and printing technology. Here’s a general breakdown:
- Fine Powders (15-45 µm): Often used for high-resolution printing of intricate parts or with laser-based 3D printing technologies requiring finer powders.
- Pós médios (45-100 µm): A versatile size range suitable for various applications and printing methods like Selective Laser Melting (SLM) or Electron Beam Melting (EBM).
- Coarse Powders (100-150 µm): Typically used for applications where high strength and dimensional accuracy are prioritized, often with binder jetting or cold spray printing methods.
Notas:
PREP powders can be categorized into different grades based on their chemical composition and intended use. Here are some examples:
- Commercial Grade: Suitable for general-purpose applications where high performance is not the primary concern.
- High-Purity Grade: Contains minimal impurities, ideal for applications demanding tight tolerances and superior mechanical properties.
- Biocompatible Grade: Specifically formulated for medical implants, adhering to stringent biocompatibility standards to ensure safety within the human body.
- Additive-Mixed Grade: Incorporated with specific additives to enhance properties like flowability, printability, or sintering characteristics.
Padrões:
Several industry standards govern the production and quality control of metal powders for additive manufacturing, including PREP powders. Here are some key standards:
- ASTM International (ASTM): Provides various standards for metal powders, including particle size distribution, chemical composition, and flowability.
- American Society for Testing and Materials (ASME): Develops standards for materials used in specific industries like aerospace and medical implants. These standards often reference ASTM standards for powder properties.
- Organização Internacional de Padronização (ISO): Sets international standards for metal powders used in additive manufacturing, focusing on aspects like particle size, morphology, and chemical composition.
Fornecedores e preços
The availability and pricing of PREP powders can vary depending on the specific material, grade, and quantity purchased. Here’s a general overview:
- Suppliers: Several companies are emerging as leading suppliers of PREP powders, including AMPA Metallpulver GmbH (Germany), Höganäs AB (Sweden), LPW Technology Ltd. (UK), and GE Additive (USA).
- Preço: The cost of PREP powders can be higher than traditionally produced powders due to the newer technology. However, prices are expected to decrease as production volumes increase. Expect pricing to vary based on the material, grade, and quantity, ranging from tens of dollars per kilogram for common materials like stainless steel to hundreds of dollars per kilogram for high-performance alloys.
It’s important to note that the information provided above is for general reference only. Specific specifications, sizes, grades, standards, suppliers, and pricing details can vary depending on the chosen material and supplier.
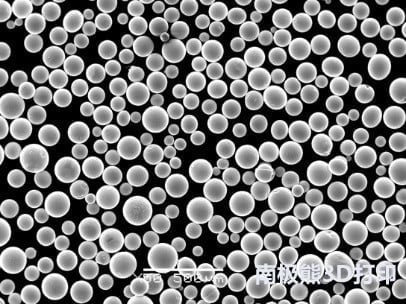
FAQ
A: The safety of PREP powders depends on the specific material. Some metal powders can pose health risks if inhaled or ingested. Always follow the recommended safety precautions provided by the material safety data sheet (MSDS) for the specific powder you’re using. This may include wearing personal protective equipment (PPE) like gloves, respirators, and safety glasses when handling the powder.
Q: What are the advantages of PREP powders compared to traditionally produced powders?
A: PREP powders offer several advantages over traditional methods like gas or water atomization:
- Superior flowability: The spherical shape of PREP powders enhances flow within the 3D printer, leading to smoother layer formation and ultimately denser, higher-quality metal parts.
- Enhanced surface quality: The smooth surface morphology minimizes surface area, reducing the risk of oxidation and contamination. This translates to purer powders, crucial for high-performance applications.
- Improved powder reuse: The spherical shape and consistent size distribution of PREP powders minimize satellite formation (smaller, undesirable particles) during printing. This allows for better powder recyclability, reducing waste and production costs.
- Wider range of materials: The PREP process is adaptable to various metals and alloys, opening doors for 3D printing with previously challenging materials.
Q: What are the limitations of PREP powders?
A: While PREP powders offer compelling advantages, some limitations exist:
- Higher cost: Currently, PREP powders tend to be more expensive than traditionally produced powders due to the relatively new technology and potentially lower production volumes. However, as demand increases and production scales up, the cost is expected to decrease.
- Disponibilidade limitada: While the range of PREP powders is expanding, it might not encompass all the metal varieties readily available in conventional methods. This could limit the immediate applicability of PREP in certain niche applications.
- Otimização de processos: The PREP process requires ongoing research and development to optimize parameters for specific materials and desired properties. Fine-tuning these parameters is crucial for achieving consistent and predictable printing results.
Q: How do I choose the right PREP powder for my 3D printing project?
A: Choosing the right PREP powder depends on several factors:
- Aplicativo: Consider the final use of the 3D printed part. Does it require high strength, good corrosion resistance, biocompatibility, or other specific properties?
- Printing technology: Different 3D printing methods may have varying requirements for powder size, flowability, and other characteristics.
- Propriedades do material: Research the desired mechanical properties like strength, ductility, and corrosion resistance offered by different PREP powder options.
- Cost and availability: Consider the budget for your project and the ease of acquiring the specific PREP powder you need.
Consulting with a material supplier or a 3D printing expert can be beneficial to determine the most suitable PREP powder for your specific requirements.
Q: What’s the future outlook for PREP-prepared powders?
A: The future of PREP powders appears bright. As research and development continue, we can expect advancements in:
- Otimização de processos: Leading to more efficient and cost-effective production of PREP powders.
- Material development: Expanding the range of materials available in PREP form, including exotic alloys and composites.
- Improved powder properties: Further refinement of powder characteristics like flowability, particle size distribution, and surface quality.
These advancements will likely lead to a wider adoption of PREP powders across various 3D printing applications, revolutionizing how we design, manufacture, and utilize metal components.
Sobre o 3DP mETAL
Categoria do produto
ENTRE EM CONTATO
Alguma dúvida? Envie-nos uma mensagem agora! Após receber sua mensagem, processaremos sua solicitação com toda equipe.