Metal powders are revolutionizing various industries, offering versatility, efficiency, and precision in manufacturing processes. From aerospace to automotive, and from medical implants to consumer electronics, metal powders play a crucial role. In this comprehensive guide, we’ll delve deep into the world of quality metal powders, exploring their types, compositions, properties, applications, specifications, suppliers, and more.
Overview of Quality Metal Powder
Quality metal powders are finely ground metals used in various manufacturing and production processes. Their applications span across several industries due to their unique properties, such as high surface area, excellent flow characteristics, and the ability to create intricate shapes with high precision.
Key Details
- Definition: Metal powders are finely divided metals produced through various processes.
- Applications: Widely used in additive manufacturing, metallurgy, electronics, automotive, aerospace, and medical industries.
- Properties: High purity, excellent flowability, controlled particle size distribution, high surface area.
Types and Models of Quality Metal Powder
There are several types of metal powders, each with unique properties and applications. Here, we’ll explore ten specific models, providing detailed descriptions for each.
1. Aluminum Powder
Aluminum powder is known for its lightweight and high corrosion resistance. It’s used extensively in aerospace and automotive industries.
2. Titanium Powder
Titanium powder is prized for its high strength-to-weight ratio and biocompatibility, making it ideal for aerospace components and medical implants.
3. Stainless Steel Powder
Stainless steel powder offers excellent corrosion resistance and strength, commonly used in additive manufacturing for complex parts.
4. Copper Powder
Copper powder is highly conductive and is widely used in electronics and electrical applications.
5. Nickel Powder
Nickel powder provides high resistance to corrosion and oxidation, suitable for superalloys and high-temperature applications.
6. Iron Powder
Iron powder is cost-effective and versatile, used in various industries for components, magnetic materials, and chemical applications.
7. Cobalt-Chromium Powder
Cobalt-chromium powder is known for its wear resistance and strength at high temperatures, used in dental and orthopedic implants.
8. Tungsten Powder
Tungsten powder is extremely dense and has a high melting point, ideal for applications requiring high temperature and wear resistance.
9. Magnesium Powder
Magnesium powder is lightweight with good strength, commonly used in automotive and aerospace applications.
10. Bronze Powder
Bronze powder, an alloy of copper and tin, is used for its excellent wear resistance and friction properties in bearings and bushings.
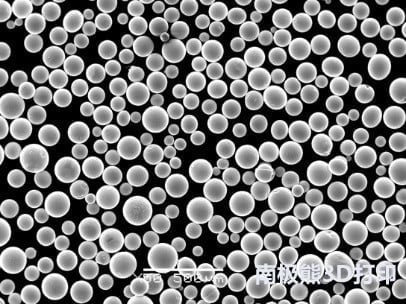
Composition of Quality Metal Powder
Understanding the composition of metal powders is crucial for selecting the right type for specific applications. Here, we’ll look at the primary components and their effects on the powder’s properties.
Metal Powder | Composition | Properties |
---|---|---|
Aluminum | Aluminum (Al), trace elements | Lightweight, corrosion-resistant |
Titanium | Titanium (Ti), trace elements | High strength, biocompatible |
Stainless Steel | Iron (Fe), Chromium (Cr), Nickel (Ni), Molybdenum (Mo) | Corrosion-resistant, strong |
Copper | Copper (Cu), trace elements | High conductivity |
Nickel | Nickel (Ni), trace elements | Corrosion and oxidation-resistant |
Iron | Iron (Fe), Carbon (C), trace elements | Versatile, magnetic properties |
Cobalt-Chromium | Cobalt (Co), Chromium (Cr), Molybdenum (Mo) | Wear-resistant, high-temperature strength |
Tungsten | Tungsten (W), trace elements | High density, high melting point |
Magnesium | Magnesium (Mg), trace elements | Lightweight, strong |
Bronze | Copper (Cu), Tin (Sn) | Wear-resistant, good friction properties |
Characteristics of Quality Metal Powder
Metal powders possess unique characteristics that determine their suitability for various applications. Here are some of the essential characteristics to consider:
- Particle Size Distribution: Affects flowability and packing density.
- Shape: Spherical particles offer better flowability, while irregular shapes may provide higher surface area.
- Purity: Higher purity powders ensure better performance and fewer defects.
- Flowability: Crucial for processes like additive manufacturing and powder metallurgy.
- Surface Area: Higher surface area can enhance reactivity and sintering.
Applications of Quality Metal Powder
Metal powders are used in a wide range of applications. Below is a table showcasing some of the primary uses of different metal powders.
Metal Powder | Applications |
---|---|
Aluminum | Aerospace components, automotive parts, pyrotechnics |
Titanium | Aerospace parts, medical implants, sports equipment |
Stainless Steel | Additive manufacturing, automotive parts, kitchenware |
Copper | Electrical components, heat exchangers, electronics |
Nickel | Superalloys, batteries, catalysts |
Iron | Magnetic materials, automotive parts, construction |
Cobalt-Chromium | Dental implants, orthopedic implants, turbine blades |
Tungsten | High-temperature applications, electrical contacts |
Magnesium | Automotive parts, aerospace components, fireworks |
Bronze | Bearings, bushings, decorative items |
Specifications, Sizes, Grades, and Standards
Metal powders come in various specifications, sizes, and grades, adhering to industry standards to ensure quality and performance.
Metal Powder | Size Range | Grades | Standards |
---|---|---|---|
Aluminum | 10-100 microns | 1100, 6061 | ASTM B928, ISO 209 |
Titanium | 15-150 microns | Grade 1, Grade 5 | ASTM B348, ISO 5832 |
Stainless Steel | 20-200 microns | 316L, 304 | ASTM A276, ISO 5832 |
Copper | 10-80 microns | ETP, OFHC | ASTM B170, ISO 431 |
Nickel | 15-100 microns | Ni 200, Ni 201 | ASTM B160, ISO 5755 |
Iron | 20-150 microns | 1000C, 1000B | ASTM B243, ISO 11124 |
Cobalt-Chromium | 15-150 microns | CoCrMo, CoCrW | ASTM F1537, ISO 5832 |
Tungsten | 10-100 microns | W1, W2 | ASTM B760, ISO 3878 |
Magnesium | 20-150 microns | AZ31B, AZ91D | ASTM B93, ISO 16220 |
Bronze | 15-80 microns | C93200, C95400 | ASTM B505, ISO 431 |
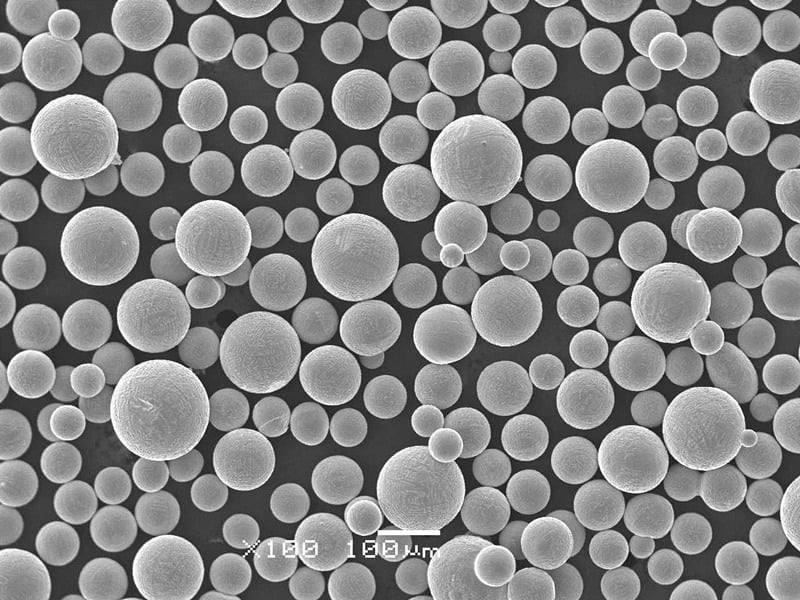
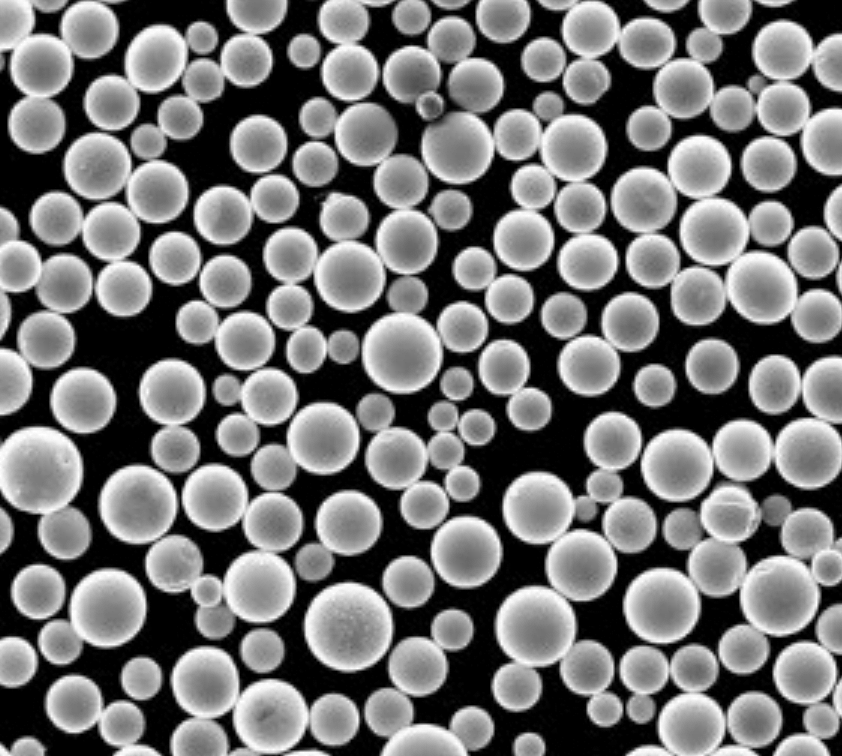
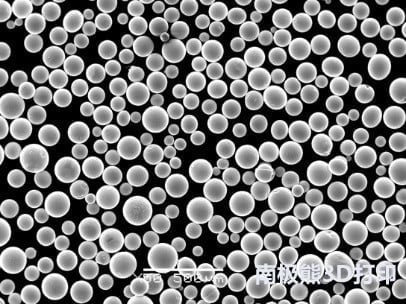
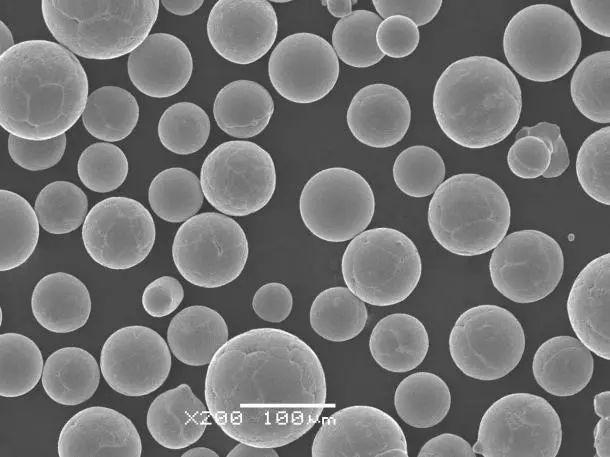
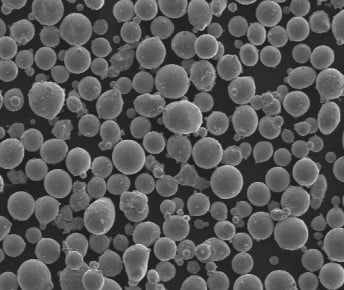
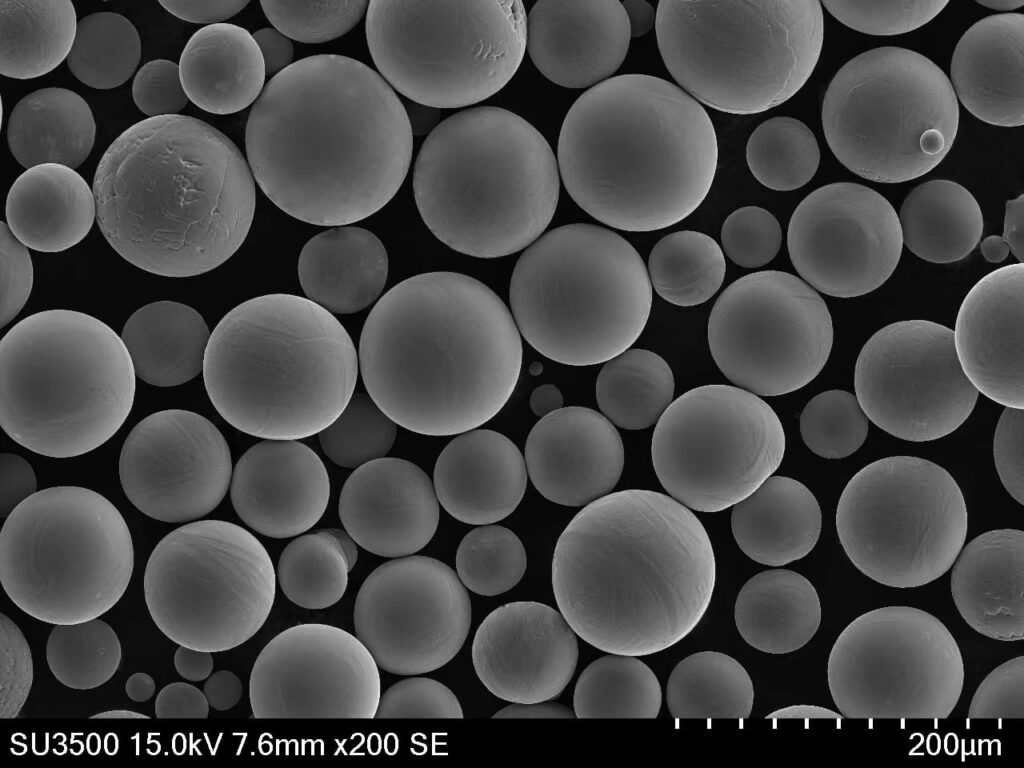
Suppliers and Pricing Details
Finding reliable suppliers and understanding pricing is essential for sourcing quality metal powders. Below is a table with some prominent suppliers and indicative pricing.
Supplier | Metal Powders | Pricing (per kg) | Region |
---|---|---|---|
Höganäs | Iron, Stainless Steel, Copper | $15 – $50 | Global |
Sandvik | Titanium, Nickel, Cobalt-Chromium | $50 – $200 | Global |
GKN Powder Metallurgy | Aluminum, Magnesium | $20 – $100 | Global |
Carpenter Technology | Stainless Steel, Titanium | $30 – $150 | Global |
American Elements | Tungsten, Nickel, Copper | $40 – $250 | North America |
Metal Powder Products | Iron, Bronze, Aluminum | $10 – $60 | North America |
LPW Technology | Titanium, Nickel, Stainless Steel | $60 – $300 | Europe, North America |
Praxair Surface Technologies | Nickel, Cobalt-Chromium | $70 – $250 | Global |
Advanced Powder Products | Stainless Steel, Bronze | $20 – $80 | North America |
Atomising Systems | Aluminum, Copper, Bronze | $15 – $90 | Europe |
Pros and Cons of Different Metal Powders
When choosing metal powders for specific applications, it’s essential to weigh the pros and cons. Here’s a comparative table highlighting the advantages and limitations of various metal powders.
Metal Powder | Advantages | Limitations |
---|---|---|
Aluminum | Lightweight, corrosion-resistant | Lower strength compared to other metals |
Titanium | High strength-to-weight ratio,biocompatible | Expensive, challenging to process |
Stainless Steel | Corrosion-resistant, strong | Heavier than other metal powders |
Copper | Highly conductive, excellent thermal properties | Prone to oxidation, expensive |
Nickel | Corrosion and oxidation-resistant | High cost, challenging to process |
Iron | Cost-effective, versatile | Prone to rust, lower corrosion resistance |
Cobalt-Chromium | Wear-resistant, high-temperature strength | Expensive, limited suppliers |
Tungsten | High density, high melting point | Very heavy, difficult to work with |
Magnesium | Lightweight, good strength | Highly reactive, flammable |
Bronze | Wear-resistant, good friction properties | Prone to tarnishing, less strong than pure metals |
Comparing Different Metal Powders
When selecting metal powders for specific applications, making explicit comparisons between different types is crucial. Here’s a look at how some common metal powders stack up against each other.
Aluminum vs. Titanium
Aluminum is lightweight and corrosion-resistant, making it ideal for applications where weight is a concern. Titanium, however, offers a higher strength-to-weight ratio and biocompatibility, making it better suited for high-performance aerospace and medical applications.
Stainless Steel vs. Copper
Stainless steel is strong and corrosion-resistant, suitable for structural applications. Copper, on the other hand, excels in electrical and thermal conductivity, making it the go-to choice for electronics and heat exchangers.
Nickel vs. Cobalt-Chromium
Nickel is known for its corrosion and oxidation resistance, perfect for superalloys and battery applications. Cobalt-chromium, with its wear resistance and high-temperature strength, is preferred for medical implants and turbine blades.
Tungsten vs. Magnesium
Tungsten’s high density and melting point make it ideal for high-temperature and high-wear applications. Magnesium, being lightweight with good strength, is more suitable for automotive and aerospace applications where weight reduction is crucial.
Expert Opinions and Studies
Several studies and expert opinions have highlighted the benefits and applications of metal powders. For instance, research on additive manufacturing has shown that metal powders like titanium and stainless steel enable the production of complex geometries with high precision, significantly reducing waste and production time.
According to a report by MarketsandMarkets, the metal powder market is expected to grow significantly, driven by the increasing adoption of additive manufacturing across various industries. Experts also point out that advancements in powder production technologies are leading to higher quality and more affordable metal powders, expanding their applications even further.
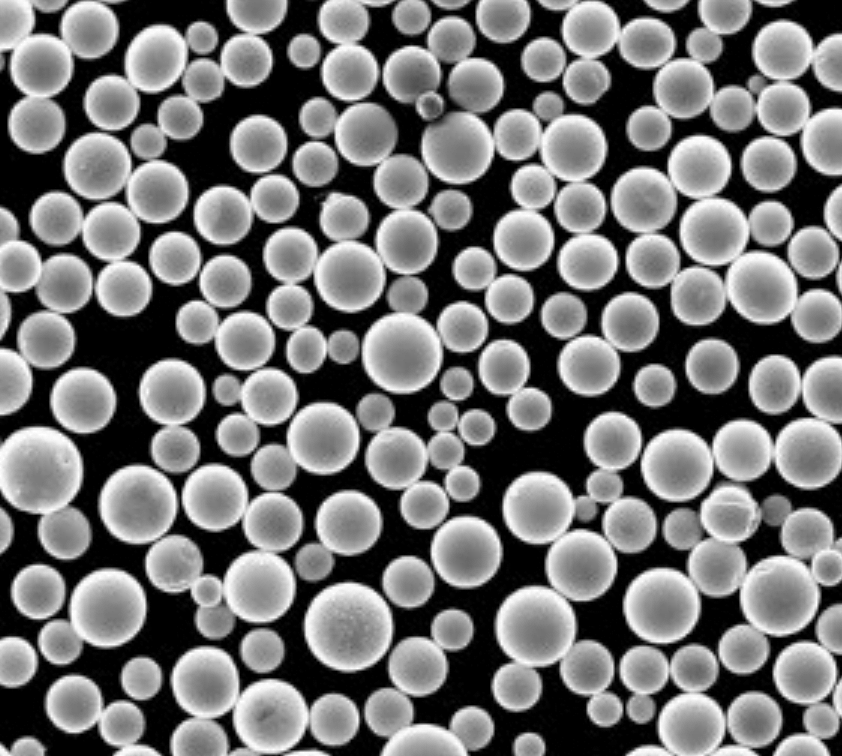
FAQs
Question | Answer |
---|---|
What are metal powders used for? | Metal powders are used in additive manufacturing, powder metallurgy, electronics, automotive, aerospace, and medical industries. |
How are metal powders produced? | Metal powders are produced through various methods such as atomization, reduction, electrolysis, and mechanical alloying. |
What are the benefits of using metal powders? | Metal powders offer high precision, efficiency, and the ability to create complex shapes with minimal waste. |
How do I choose the right metal powder? | Consider factors such as application, required properties, cost, and availability when choosing a metal powder. |
Are metal powders safe to use? | Yes, but it is essential to follow safety guidelines to prevent inhalation or exposure to fine particles. |
Conclusion
Quality metal powders are a cornerstone of modern manufacturing, enabling innovation and efficiency across various industries. By understanding the types, compositions, properties, applications, and suppliers, you can make informed decisions to leverage the full potential of metal powders in your projects.
In summary, whether you’re involved in aerospace engineering, medical device manufacturing, or electronics, metal powders offer unparalleled versatility and precision. With the right knowledge and resources, you can harness the power of these materials to push the boundaries of what’s possible in your field.
About 3DP mETAL
Product Category
CONTACT US
Any questions? Send us a message now! After receiving your message, we will process your request with a whole team.