Overview
Refractory powder materials are indispensable in various industrial applications due to their ability to withstand extreme temperatures, corrosion, and wear. These materials are vital in sectors such as metallurgy, aerospace, and ceramics. This article delves deep into the world of refractory powder materials, exploring their types, compositions, properties, applications, specifications, and much more. We’ll also examine specific metal powder models, their advantages, and limitations, providing a comprehensive guide for anyone interested in this fascinating field.
Types of Refractory Powder Materials
Refractory powder materials come in various forms, each tailored for specific industrial needs. Below is a table summarizing the key types, their compositions, and properties.
Type | Composition | Properties |
---|---|---|
Alumina | Al₂O₃ | High melting point, excellent thermal stability, good electrical insulation |
Magnesia | MgO | High melting point, good chemical stability, resistance to basic slags |
Silicon Carbide | SiC | High thermal conductivity, high hardness, good oxidation resistance |
Zirconia | ZrO₂ | High melting point, excellent thermal shock resistance, low thermal conductivity |
Chromium Oxide | Cr₂O₃ | High melting point, good wear resistance, excellent corrosion resistance |
Silicon Nitride | Si₃N₄ | High strength, thermal shock resistance, good oxidation and wear resistance |
Boron Carbide | B₄C | Extremely hard, high thermal conductivity, low density |
Hafnium Carbide | HfC | Very high melting point, good thermal and electrical conductivity, high hardness |
Titanium Diboride | TiB₂ | High hardness, high melting point, good electrical conductivity |
Tantalum Carbide | TaC | Extremely high melting point, good thermal and electrical conductivity, high hardness |
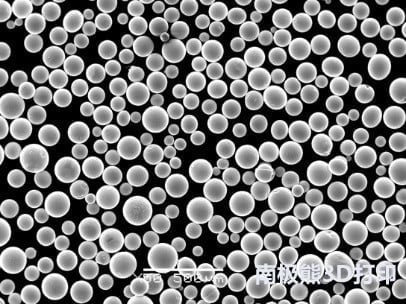
Applications of Refractory Powder Materials
Refractory powder materials are crucial in numerous high-temperature applications. Here’s a detailed table highlighting their uses across various industries.
Application | Industry | Material Used | Description |
---|---|---|---|
Furnace Linings | Metallurgy | Alumina, Magnesia, Zirconia | Provide thermal insulation and protection against corrosive environments |
Cutting Tools | Manufacturing | Silicon Carbide, Boron Carbide | Used for their hardness and wear resistance |
Thermal Insulation | Aerospace | Silicon Nitride, Hafnium Carbide | Protect components from extreme temperatures |
Protective Coatings | Industrial Equipment | Chromium Oxide, Titanium Diboride | Enhance durability and resistance to wear and corrosion |
Structural Components | Ceramics | Zirconia, Silicon Nitride | Provide strength and stability under high temperatures |
Semiconductor Fabrication | Electronics | Silicon Nitride, Alumina | Used in the production of electronic devices |
Nuclear Reactors | Energy | Boron Carbide, Zirconia | Provide radiation shielding and structural integrity |
Heat Exchangers | Chemical Processing | Silicon Carbide, Tantalum Carbide | Used for their thermal conductivity and corrosion resistance |
Abrasives | Surface Finishing | Boron Carbide, Silicon Carbide | Used in grinding, polishing, and cutting applications |
Catalytic Converters | Automotive | Alumina, Zirconia | Support the conversion of exhaust gases to less harmful emissions |
Specifications, Sizes, Grades, Standards
To ensure the right fit for various applications, refractory powder materials come in different specifications, sizes, grades, and standards. Here’s a detailed breakdown.
Material | Specifications | Sizes | Grades | Standards |
---|---|---|---|---|
Alumina | Purity: 99.5% | 1-100 microns | Industrial, Electronic | ASTM B1017, ISO 8656-1 |
Magnesia | Purity: 96-99% | 1-200 microns | Industrial, Refractory | ASTM C1446, ISO 10081-1 |
Silicon Carbide | Purity: 98-99% | 1-120 microns | Black, Green | ASTM F2263, ISO 9286 |
Zirconia | Purity: 95-99% | 1-150 microns | Industrial, Medical | ASTM C795, ISO 13356 |
Chromium Oxide | Purity: 99% | 1-80 microns | Industrial, Coating | ASTM C673, ISO 13765 |
Silicon Nitride | Purity: 98-99% | 1-50 microns | Industrial, Electronic | ASTM F2094, ISO 6474 |
Boron Carbide | Purity: 96-99% | 1-60 microns | Industrial, Nuclear | ASTM C750, ISO 9001 |
Hafnium Carbide | Purity: 99% | 1-100 microns | Industrial, Aerospace | ASTM E112, ISO 15924 |
Titanium Diboride | Purity: 98-99% | 1-90 microns | Industrial, Electronic | ASTM B376, ISO 19095 |
Tantalum Carbide | Purity: 99% | 1-120 microns | Industrial, Aerospace | ASTM E539, ISO 16372 |
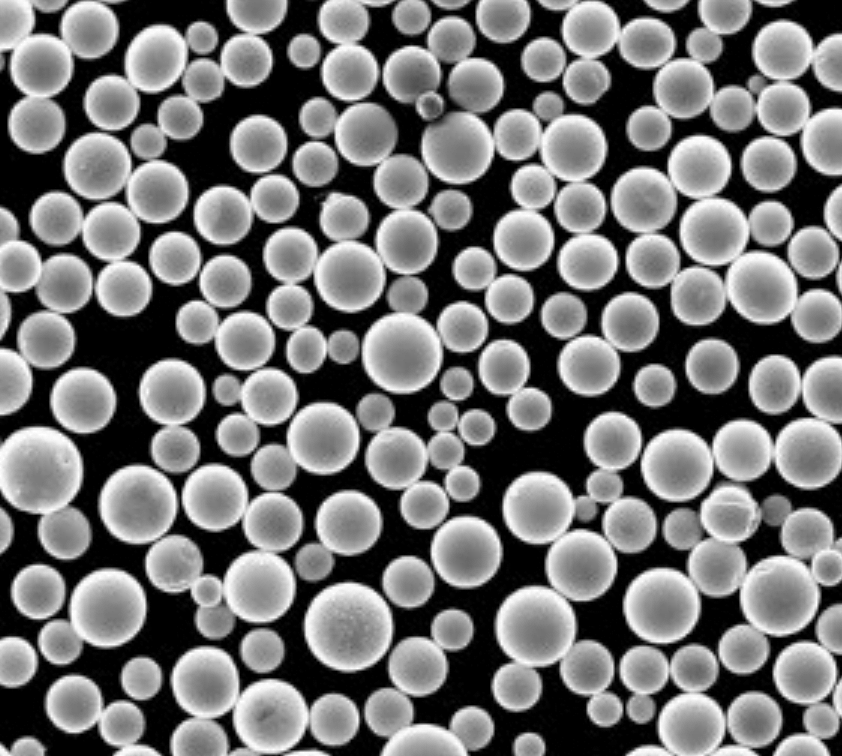
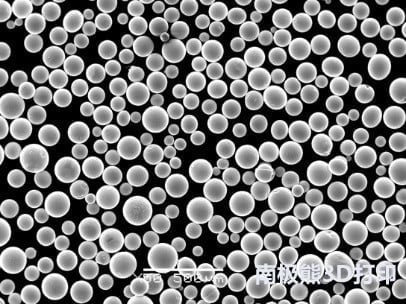
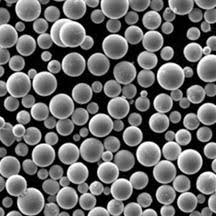
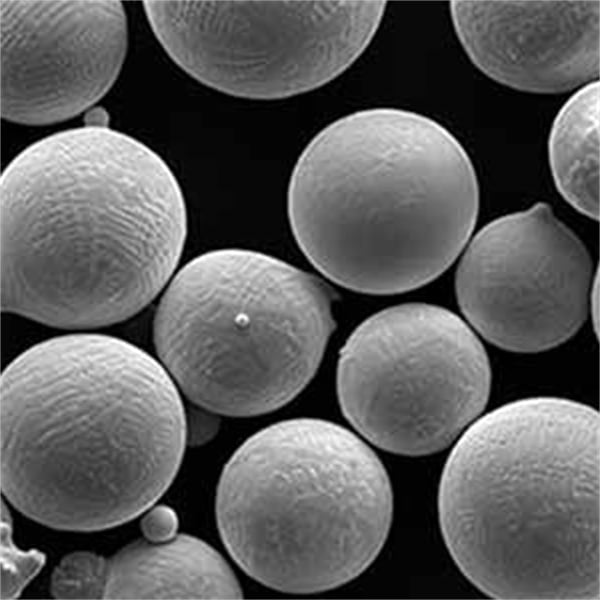
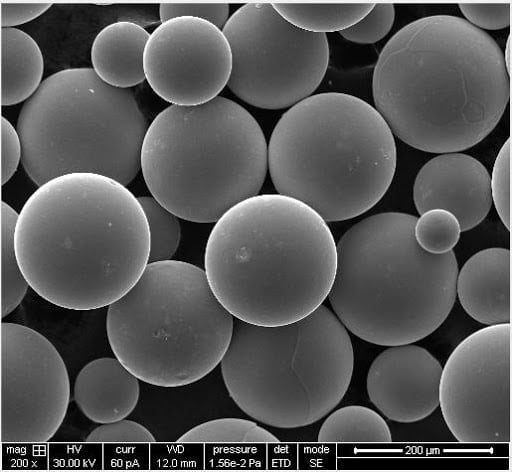
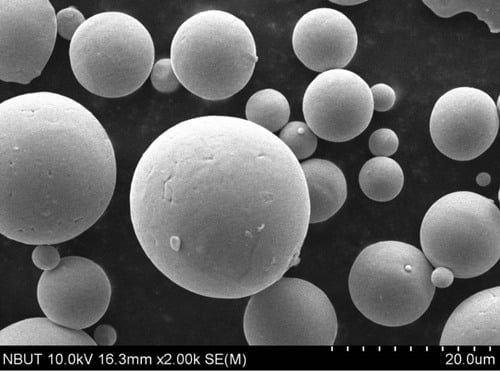
Suppliers and Pricing Details
Selecting the right supplier is crucial for quality and cost-effectiveness. Below is a table with notable suppliers and their pricing details.
Supplier | Location | Material | Price Range (per kg) | Contact |
---|---|---|---|---|
Advanced Materials Inc. | USA | Alumina, Silicon Carbide | $100 – $300 | [email protected] |
Refractory Experts Ltd. | UK | Zirconia, Chromium Oxide | $200 – $500 | [email protected] |
TechPowder Industries | Germany | Boron Carbide, Titanium Diboride | $300 – $600 | [email protected] |
NanoTech Materials | Japan | Hafnium Carbide, Tantalum Carbide | $400 – $700 | [email protected] |
HighTemp Solutions | China | Magnesia, Silicon Nitride | $150 – $350 | [email protected] |
Ceramic Materials Co. | USA | Alumina, Zirconia | $120 – $320 | [email protected] |
Global Refractory Supply | India | Silicon Carbide, Chromium Oxide | $180 – $450 | [email protected] |
Aerospace Alloys Inc. | France | Hafnium Carbide, Boron Carbide | $350 – $650 | [email protected] |
ThermalTech | South Korea | Tantalum Carbide, Silicon Nitride | $220 – $520 | [email protected] |
RefracMetals | Canada | Titanium Diboride, Magnesia | $250 – $550 | [email protected] |
Comparing Advantages and Limitations
Understanding the pros and cons of each refractory powder material is essential for making informed decisions. Here’s a comparison table highlighting these aspects.
Material | Advantages | Limitations |
---|---|---|
Alumina | High melting point, good electrical insulation, corrosion-resistant | Brittle, can be expensive |
Magnesia | Excellent thermal stability, resistance to basic slags | Reacts with water, limited availability |
Silicon Carbide | High thermal conductivity, high hardness, wear-resistant | Can be expensive, limited oxidation resistance |
Zirconia | High thermal shock resistance, low thermal conductivity | Expensive, limited to specific applications |
Chromium Oxide | Excellent wear and corrosion resistance, high melting point | Difficult to process, expensive |
Silicon Nitride | High strength, good oxidation and wear resistance, thermal shock resistance | High cost, complex processing |
Boron Carbide | Extremely hard, high thermal conductivity, low density | Expensive, can be difficult to process |
Hafnium Carbide | Very high melting point, good thermal and electrical conductivity | Extremely expensive, limited availability |
Titanium Diboride | High hardness, good electrical conductivity, high melting point | Difficult to process, high cost |
Tantalum Carbide | Extremely high melting point, good thermal and electrical conductivity | Extremely expensive, limited availability |
Specific Metal Powder Models
Let’s delve into specific metal powder models, each with unique properties and applications.
1. Alumina Powder (Al₂O₃)
Alumina powder is renowned for its high melting point and excellent electrical insulation properties. It’s commonly used in electrical insulators, refractory linings, and cutting tools. Its high corrosion resistance makes it ideal for use in aggressive environments.
2. Magnesia Powder (MgO)
Magnesia powder is prized for its high thermal stability and resistance to basic slags, making it a staple in the steel industry for furnace linings. It’s also used in refractory cements and as a raw material for producing magnesium metal.
3. Silicon Carbide Powder (SiC)
Silicon carbide powder is known for its high hardness and thermal conductivity. It is extensively used in abrasives, cutting tools, and as a refractory material in high-temperature applications. Its wear resistance makes it ideal for mechanical seals and bearings.
4. Zirconia Powder (ZrO₂)
Zirconia powder offers excellent thermal shock resistance and is used in thermal barrier coatings, structural ceramics, and dental ceramics. Its ability to withstand extreme temperatures makes it suitable for use in jet engines and gas turbines.
5. Chromium Oxide Powder (Cr₂O₃)
Chromium oxide powder is valued for its high melting point and excellent wear and corrosion resistance. It is commonly used in protective coatings, pigments, and as a refractory material in high-temperature applications.
6. Silicon Nitride Powder (Si₃N₄)
Silicon nitride powder is known for its high strength and thermal shock resistance. It’s widely used in automotive engines, bearings, and as a material for cutting tools due to its ability to withstand high temperatures and mechanical stress.
7. Boron Carbide Powder (B₄C)
Boron carbide powder is one of the hardest materials known and has high thermal conductivity. It’s used in armor plating, cutting tools, and as a neutron absorber in nuclear reactors due to its ability to withstand extreme conditions.
8. Hafnium Carbide Powder (HfC)
Hafnium carbide powder has an extremely high melting point and good thermal and electrical conductivity. It is used in high-temperature applications such as rocket nozzles, nuclear reactors, and as a hard coating material.
9. Titanium Diboride Powder (TiB₂)
Titanium diboride powder is highly valued for its hardness and electrical conductivity. It is used in conductive ceramics, cutting tools, and wear-resistant coatings due to its ability to maintain stability at high temperatures.
10. Tantalum Carbide Powder (TaC)
Tantalum carbide powder boasts an extremely high melting point and good thermal and electrical conductivity. It’s used in cutting tools, high-temperature structural materials, and as a carbide in cemented carbide tools.
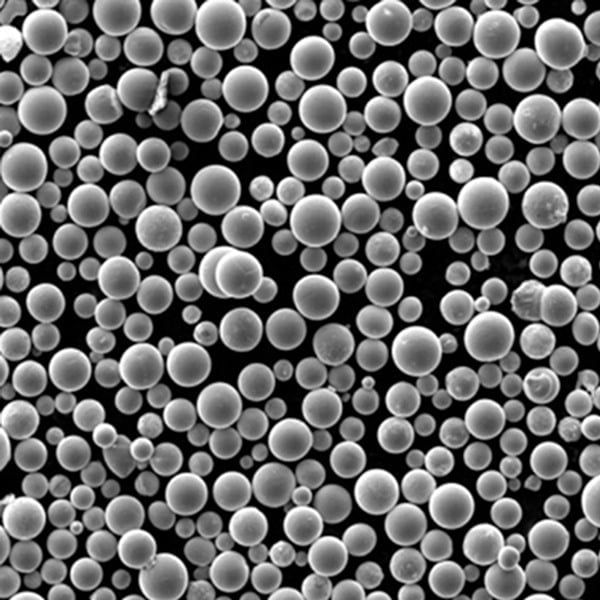
Advantages of Refractory Powder Materials
Refractory powder materials offer numerous advantages across different industries. Here are some key benefits:
High Temperature Resistance
Refractory powder materials are designed to withstand extremely high temperatures, making them ideal for use in furnaces, kilns, and reactors where conventional materials would fail.
Wear and Corrosion Resistance
Many refractory powders, such as chromium oxide and silicon carbide, are highly resistant to wear and corrosion. This makes them suitable for use in harsh environments where they can maintain their integrity over prolonged periods.
Thermal Stability
Materials like zirconia and magnesia exhibit excellent thermal stability, allowing them to maintain their properties and performance even under fluctuating temperatures. This is critical in applications like aerospace and high-temperature industrial processes.
Electrical Insulation
Some refractory powders, such as alumina, offer excellent electrical insulation properties. This makes them ideal for use in electronic components and insulators.
Versatility in Applications
From protective coatings to structural components and cutting tools, refractory powder materials can be tailored to suit a wide range of applications. Their versatility is a significant advantage in various industries.
Disadvantages of Refractory Powder Materials
Despite their numerous benefits, refractory powder materials have certain limitations:
Cost
Many refractory powder materials, such as hafnium carbide and tantalum carbide, are expensive. Their high cost can limit their use to critical applications where their unique properties justify the expense.
Brittleness
Materials like alumina and zirconia can be brittle, making them prone to cracking under mechanical stress. This limitation can restrict their use in applications requiring high impact resistance.
Complex Processing
Some refractory powders, such as silicon nitride and titanium diboride, require complex processing techniques. This can increase production costs and complicate manufacturing processes.
Availability
Certain refractory powders, such as hafnium carbide, are not widely available. Limited availability can lead to supply chain issues and increased costs.
Reactivity
Some materials, like magnesia, can react with water or other substances, limiting their use in certain environments. This reactivity must be carefully managed to ensure long-term performance.
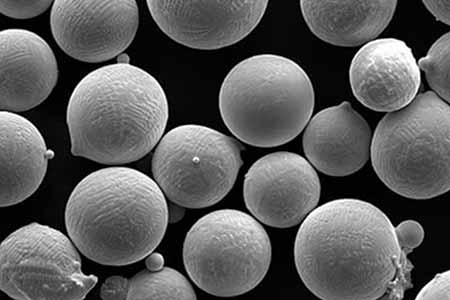
FAQs
Q: What are refractory powder materials?
A: Refractory powder materials are specialized substances designed to withstand extreme temperatures, corrosion, and wear. They are used in various industrial applications, including furnace linings, cutting tools, and protective coatings.
Q: Why are refractory powder materials important?
A: These materials are crucial for high-temperature applications where conventional materials would fail. They offer exceptional thermal stability, wear resistance, and corrosion resistance, making them essential in industries like metallurgy, aerospace, and ceramics.
Q: What are some common types of refractory powder materials?
A: Common types include alumina, magnesia, silicon carbide, zirconia, chromium oxide, silicon nitride, boron carbide, hafnium carbide, titanium diboride, and tantalum carbide.
Q: How are refractory powder materials used?
A: They are used in various applications such as furnace linings, cutting tools, thermal insulation, protective coatings, structural components, and more. Each material is selected based on its unique properties and suitability for the specific application.
Q: What are the advantages of using refractory powder materials?
A: Advantages include high temperature resistance, wear and corrosion resistance, thermal stability, electrical insulation properties, and versatility in applications.
Q: What are the limitations of refractory powder materials?
A: Limitations include high cost, brittleness, complex processing requirements, limited availability, and potential reactivity with certain substances.
Q: Where can I buy refractory powder materials?
A: Refractory powder materials can be purchased from specialized suppliers such as Advanced Materials Inc., Refractory Experts Ltd., TechPowder Industries, NanoTech Materials, and others. Prices vary depending on the material and supplier.
Q: Are there any safety concerns with using refractory powder materials?
A: Yes, handling refractory powder materials can pose health risks if proper safety measures are not followed. It is important to use appropriate personal protective equipment (PPE) and follow safety guidelines to avoid inhalation, skin contact, and other potential hazards.
Conclusion
Refractory powder materials are vital components in many high-temperature and high-stress applications across various industries. From their unique properties and advantages to their specific applications and potential limitations, understanding these materials is crucial for making informed decisions in industrial processes. By exploring the different types of refractory powder materials, their uses, and the specifics of each, we can appreciate their importance and optimize their application to enhance performance and efficiency in demanding environments.
About 3DP mETAL
Product Category
CONTACT US
Any questions? Send us a message now! After receiving your message, we will process your request with a whole team.