Imagine a world where metal isn’t just forged into hulking beams or sculpted into intricate statues. Imagine a world where metal can be broken down into microscopic particles, each one a tiny treasure trove of potential. This is the realm of Atomize Metal, a revolutionary process that’s fundamentally changing how we interact with and utilize metals in countless industries.
Преимущества Atomize Metal
But why go through the trouble of breaking down perfectly good metal? The answer lies in the unique properties that atomize metal possesses. Unlike their bulkier counterparts, atomize metal particles boast:
- Unmatched Versatility: Imagine having a metal that can be tailored to fit almost any application. With atomization, the size, shape, and even composition of the metal powder can be precisely controlled. This allows for the creation of powders specifically suited for different purposes, from delicate 3D printing projects to ultra-strong metal coatings.
- Superior Flow Characteristics: Ever tried pouring sand? It doesn’t exactly flow smoothly, does it? atomize metal powders, on the other hand, exhibit excellent flow properties. This makes them ideal for processes like metal injection molding (MIM) and additive manufacturing, where precise control over material placement is crucial.
- Enhanced Densification: Think of a snowball – loosely packed and full of air pockets. Now imagine a snowball that’s been compacted into a solid ice ball. That’s the difference between traditional metal and atomized metal. The fine particles of atomize metal pack together more tightly, leading to denser and stronger final products.
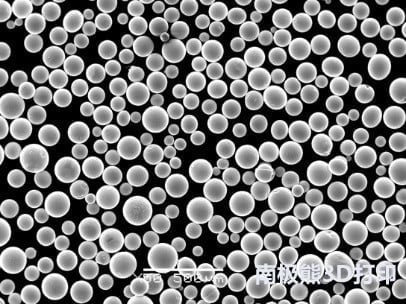
Applications of atomize metal
The applications of atomize metal are as diverse as the metals themselves. Here are just a few examples:
- Аддитивное производство (3D-печать): The world of 3D printing is booming, and atomize metal powders are a key player. These powders are used to create complex metal parts layer by layer, opening doors for innovation in everything from aerospace components to medical implants.
- Литье металлов под давлением (MIM): This intricate process utilizes atomize metal powders to create near-net-shape metal parts. Imagine creating complex shapes with the precision of plastic injection molding, but with the strength and durability of metal – that’s the power of MIM.
- Термические напыленные покрытия: Ever wondered how those bridges withstand years of harsh weather? Thermal spray coatings, often made from atomize metal powders, play a crucial role. These coatings protect surfaces from corrosion, wear, and extreme temperatures.
The Method of Atomizing Metals
So, how exactly do we transform molten metal into these microscopic marvels? The process, though complex, can be broken down into two key steps:
- Melting: The first step involves melting the desired metal feedstock in a furnace. This can be achieved using various methods, such as induction heating or electric arc furnaces.
- Распыление: Here’s where the magic happens. The molten metal stream is broken up into fine droplets using a high-velocity gas or liquid jet. Imagine a garden hose spraying water – only instead of water, we’re using a high-pressure stream to break up the metal.
The Production Process of atomize metal
While the basic concept of atomization is straightforward, the actual production process involves several intricate steps. Let’s delve deeper and explore the journey of molten metal to metal powder:
- Pre-processing: Before melting, the metal feedstock goes through a rigorous cleaning process to remove impurities. Think of it like preparing your canvas before painting – a clean surface ensures the final product is of the highest quality.
- Atomization Chamber: This is where the molten metal meets its high-pressure nemesis. The design of the chamber and the type of atomizing gas (inert gases like argon or nitrogen are commonly used) play a crucial role in determining the final characteristics of the metal powder. Just like different paint brushes create different artistic effects, the atomization chamber and gas influence the size, shape, and flow of the metal powder.
- Powder Collection and Classification: The rapidly solidified metal droplets fall into a collection system, where they are separated, cooled, and classified according to their size and morphology. Imagine sifting flour – the classification process ensures we have a consistent powder with the desired properties for specific applications.
- Постобработка: Finally, the metal powder may undergo additional treatments like de-gassing or surface modification to further enhance its properties for specific end-use applications.
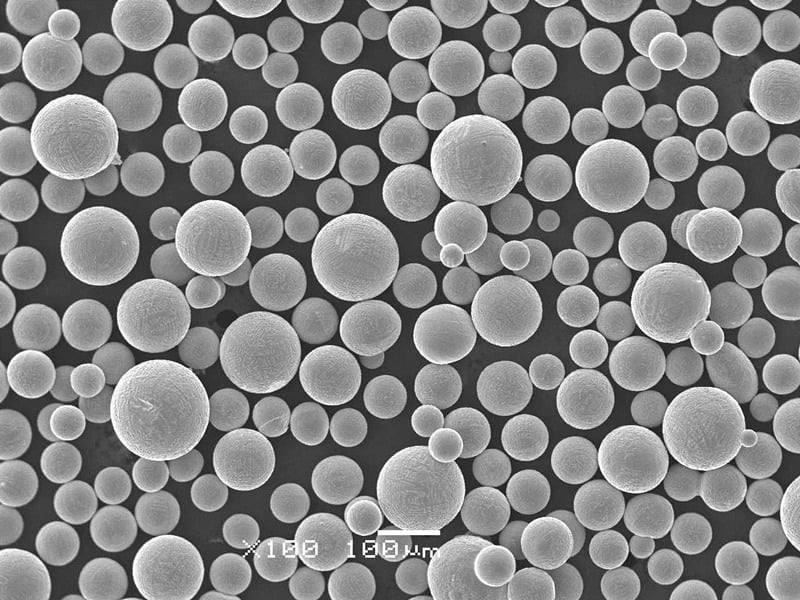
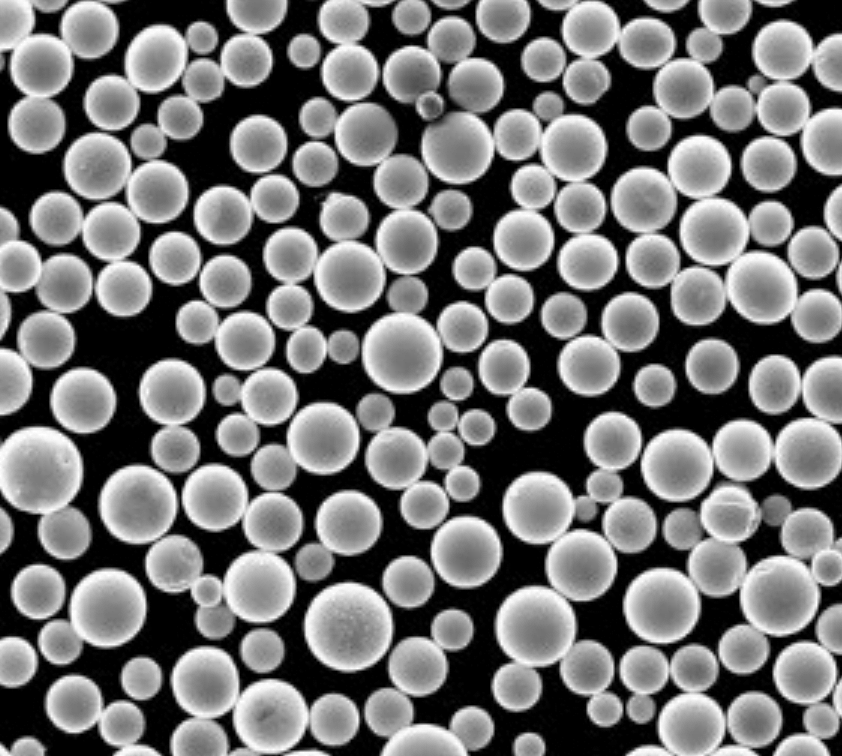
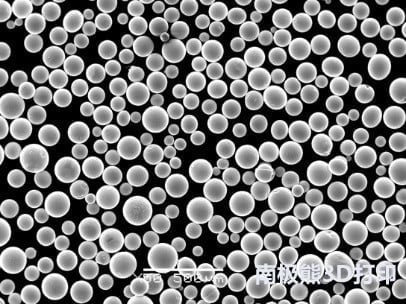
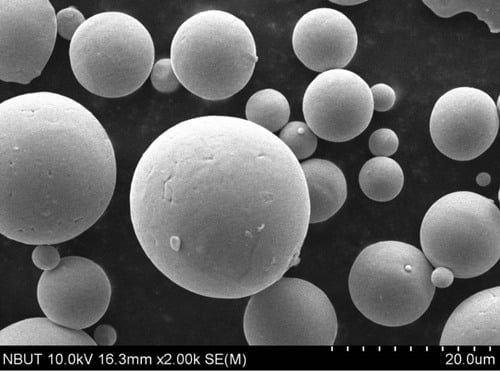
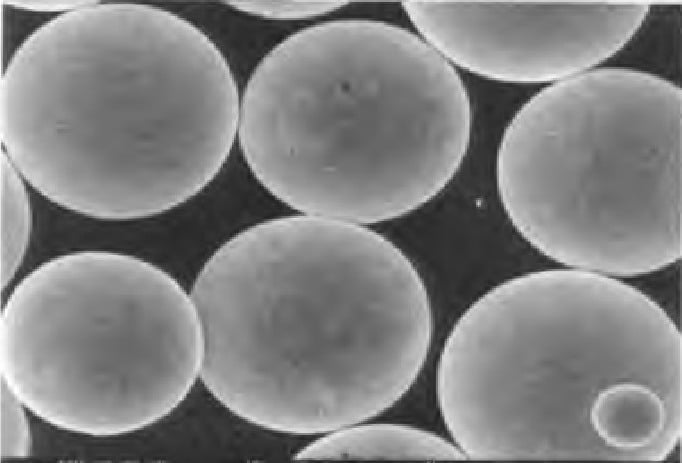
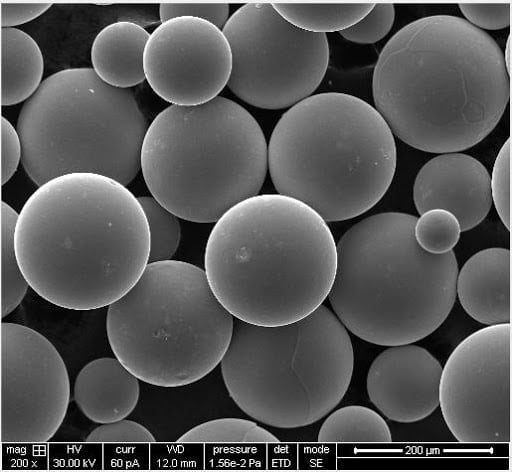
Equipment for Atomizing Metals
Характеристика | Газовая атомизация | Распыл воды |
---|---|---|
Production Rates | Высок | Низкий |
Характеристики порошка | Wide range of sizes and shapes | Excellent sphericity and smooth surface finish |
Oxidation Risk | Potential for oxidation | Minimized risk of oxidation |
Applicability | Широкий спектр металлов | Limited to some metals (not suitable for highly reactive metals) |
Environmental Considerations | Less complex wastewater treatment | Requires proper wastewater treatment to manage metal contamination |
Quality Control of atomize metal
Just like any other manufactured product, maintaining consistent quality is paramount in atomize metal production. Here are some key aspects of quality control:
- Химический состав: The chemical composition of the metal powder is rigorously analyzed to ensure it meets the desired specifications. Think of it like checking the ingredients on a food label – we need to make sure the powder has the right mix of elements for its intended purpose.
- Размер и распределение частиц: The size and distribution of the metal particles are crucial for its flowability and packing density. Different applications require powders with specific size ranges. Just like grains of sand come in various sizes, so too do atomize metal particles, and we need the right size distribution for optimal performance.
- Морфология: The shape and surface characteristics of the metal particles are also closely monitored. As mentioned earlier, some applications require highly spherical particles, while others might benefit from a more irregular shape.
- Сыпучесть: The ability of the metal powder to flow freely is essential for proper processing in techniques like MIM or 3D printing. Imagine trying to bake a cake with clumpy flour – a good flow ensures consistent and predictable behavior during the manufacturing process.
- Кажущаяся плотность: This refers to the bulk density of the metal powder. A higher apparent density indicates that the particles are packed together more tightly, leading to stronger and more durable final products.
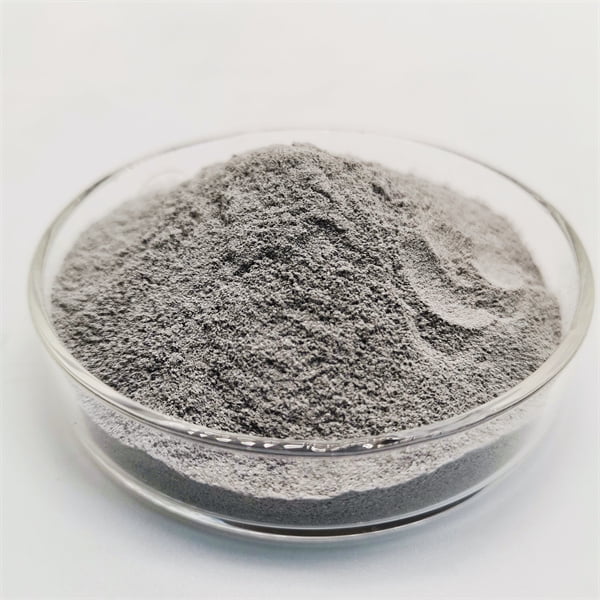
Будущее atomize metal
Мир atomize metal is constantly evolving. Researchers are exploring new techniques to produce even finer powders, control their morphology with greater precision, and develop powders from exotic or hard-to-machine metals. As the technology continues to advance, we can expect to see even more innovative applications emerge in various industries, pushing the boundaries of what’s possible with metal.
Часто задаваемые вопросы
Here are some frequently asked questions about atomize metal, answered in a clear and concise format:
Вопрос | Ответить |
---|---|
What are the benefits of using atomized metal? | Atomized metal offers superior versatility, flow characteristics, and allows for enhanced densification in final products. |
What are some applications of atomized metal? | Additive manufacturing (3D printing), metal injection molding (MIM), and thermal spray coatings are some prominent applications. |
How is metal atomized? | The process involves melting the metal and then breaking it up into fine droplets using a high-velocity gas or liquid jet. |
What are the different types of atomization? | Gas atomization and water atomization are the two main types, each with its own advantages and limitations. |
How is the quality of atomized metal controlled? | The chemical composition, particle size distribution, morphology, flowability, and apparent density are all closely monitored to ensure consistent quality. |
О компании 3DP mETAL
Категория продукта
СВЯЖИТЕСЬ С НАМИ
Есть вопросы? Отправьте нам сообщение прямо сейчас! После получения вашего сообщения мы обработаем ваш запрос всей командой.