Have you ever wondered how those intricate parts in your smartphone or the lightweight components in modern airplanes are made? The answer might lie in a fascinating technology called metal atomization. Imagine turning a scorching hot liquid metal into a cloud of ultra-fine metallic particles. That’s precisely what metal atomization equipment does, paving the way for innovative applications across various industries.
This article delves deep into the world of metal atomization equipment, exploring its different types, functionalities, and the magic behind transforming molten metal into a powdery paradise. So, buckle up and get ready to explore the fascinating realm of metal atomization!
Classification of Metal Atomization Equipment based on Atomization Methods
The heart of any metal atomization equipment lies in the atomization method it employs. Here’s a breakdown of the two primary methods used:
- Газовая атомизация: This method utilizes high-velocity inert gas jets, typically nitrogen or argon, to break down the molten metal stream into tiny droplets. These droplets rapidly solidify in the cool surrounding air, resulting in spherical-shaped metal powders. Gas atomization offers several advantages, including the production of high-purity powders with low oxygen content and excellent flowability, making them ideal for Additive Manufacturing (AM) techniques like 3D printing.
- Распыление воды: In this method, a high-pressure water jet disintegrates the molten metal stream. Compared to gas atomization, water atomization offers higher production rates but often yields powders with a slightly higher oxygen content and irregular shapes. However, water atomization is a more cost-effective approach for applications where powder morphology is less critical, such as metal injection molding (MIM).
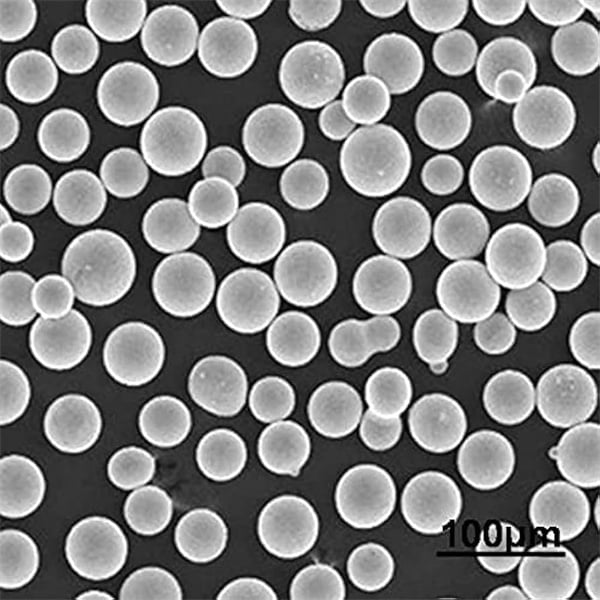
The Great Debate: Gas vs. Water Atomization
Choosing between gas and water atomization depends on your specific needs. Here’s a quick comparison to help you decide:
Характеристика | Газовая атомизация | Распыл воды |
---|---|---|
Production Rate | Низкий | Выше |
Чистота порошка | Higher (lower oxygen) | Lower (higher oxygen) |
Морфология порошка | Сферический | Неправильный |
Цена | Выше | Низкий |
Beyond the Binary: Other Atomization Methods
While gas and water atomization reign supreme, there are some niche players in the field:
- Центробежное распыление: This method employs a rotating disc or mold at high speed to atomize the molten metal. It offers good control over powder size and morphology but has limitations in terms of production rate.
- Ультразвуковое распыление: This emerging technology utilizes high-frequency sound waves to break down molten metal. It’s particularly well-suited for producing very fine powders but is still under development for large-scale production.
Классификация Оборудование для распыления металлов based on Atomization Environment
Metal atomization can occur in either a closed or an open environment, influencing the properties of the resulting powder.
- Closed-Loop Atomization: In this method, the entire atomization process takes place within a controlled atmosphere, typically an inert gas environment. This minimizes contamination and oxidation, leading to high-purity powders. Closed-loop systems are often used for gas atomization of reactive metals like titanium and aluminum.
- Open-Loop Atomization: Here, the atomization process is exposed to the ambient environment. While this method is simpler and more cost-effective, it can lead to higher oxygen pick-up in the powder. Open-loop atomization is commonly used for water atomization of less reactive metals like steel.
Closed vs. Open Loop: A Balancing Act
The choice between closed-loop and open-loop atomization hinges on the desired powder properties and cost considerations. Here’s a quick comparison:
Характеристика | Closed-Loop Atomization | Open-Loop Atomization |
---|---|---|
Чистота порошка | Higher (lower oxygen) | Lower (higher oxygen) |
Production Cost | Выше | Низкий |
Сложность | More complex | Simpler |
Technical Characteristics of Metal Atomization Equipment
Metal atomization equipment is a complex beast, but here’s a breakdown of some key technical characteristics:
- Melting Furnace: This is the heart of the system, responsible for melting the metal feedstock to a high temperature. Different furnace types are used depending on the material being processed, such as induction furnaces for reactive metals and resistance furnaces for less reactive ones.
- Atomization Chamber: This chamber houses the atomization nozzle and the environment (closed or open loop) where the metal stream is broken down into droplets.
- Cooling System: Rapid solidification is crucial for obtaining high-quality powder. Metal atomization equipment employs efficient cooling systems, often utilizing water or inert gas, to quench the molten metal droplets as they solidify into powder particles.
- Powder Collection System: The atomized powder needs to be efficiently collected and separated from the atomization medium (gas or water). This typically involves cyclones or filters to capture the powder while allowing the gas or water to be recycled or disposed of safely.
- Control System: The entire atomization process is a delicate dance, requiring precise control over parameters like metal feedstock temperature, atomization gas pressure, and cooling rate. Modern metal atomization equipment utilizes sophisticated control systems to ensure consistent and high-quality powder production.
Beyond the Basics: Advanced Features
While the core components remain the same, some advanced metal atomization equipment boasts additional features:
- Inert Gas Recycling Systems: These systems capture and re-purify the inert gas used in the closed-loop atomization process, minimizing gas consumption and operational costs.
- Powder Classification Systems: These systems allow for sorting the atomized powder into different size fractions based on their particle size distribution. This is crucial for many AM applications where precise powder size control is essential.
- Vacuum Atomization Systems: A specialized technique for producing ultra-high purity powders by performing the entire atomization process in a vacuum environment. This eliminates any chance of contamination from atmospheric gases.
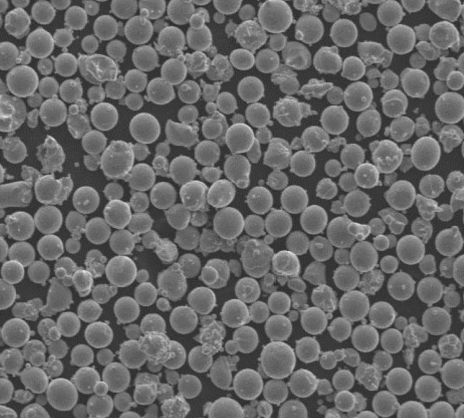
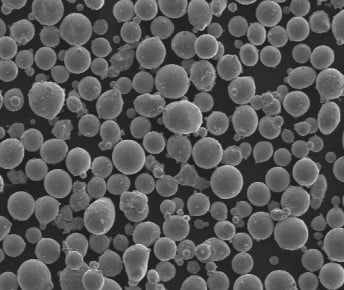
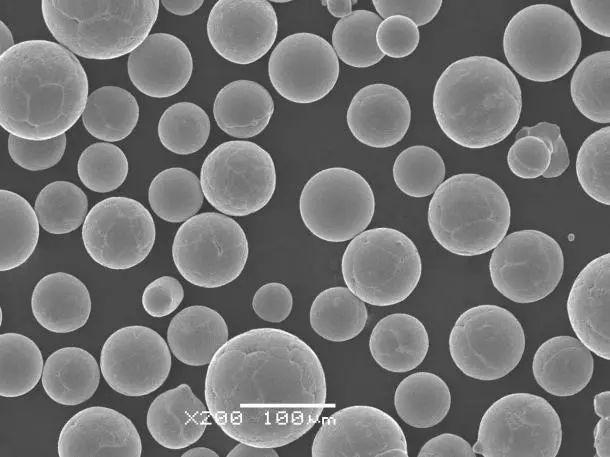
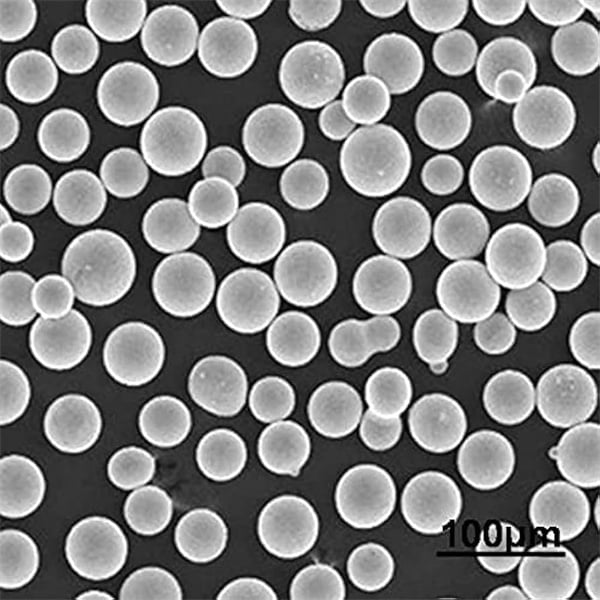
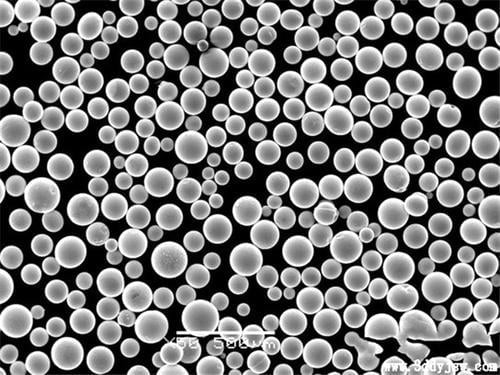
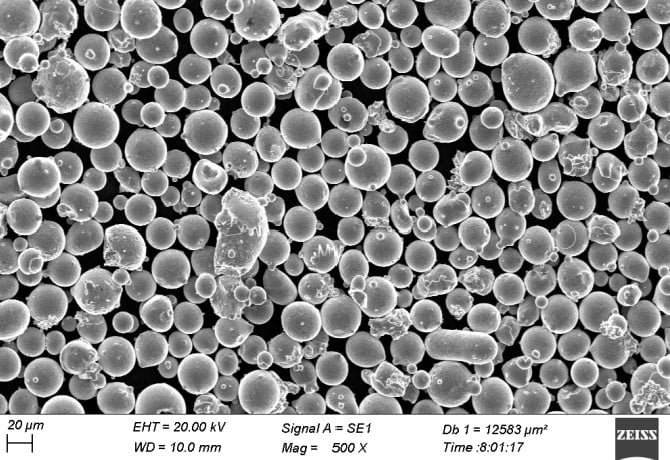
The Application of Metal Additive Manufacturing Equipment
Metal atomization equipment plays a pivotal role in the exciting world of Additive Manufacturing (AM), also known as 3D printing. The metal powders produced by these systems serve as the building blocks for creating complex 3D objects layer by layer. Here’s a glimpse into the diverse applications of metal atomization in AM:
- Аэрокосмическая промышленность: Lightweight and high-strength metal powders are used to create intricate components for aircraft, satellites, and spacecraft. This allows for design optimization, weight reduction, and improved fuel efficiency.
- Медицинские имплантаты: Biocompatible metal powders like titanium and cobalt-chrome are utilized to manufacture custom-designed implants for hip replacements, knee joints, and dental applications. This promotes better bone ingrowth and long-term implant performance.
- Автомобильная промышленность: Metal atomization enables the production of complex and lightweight components for cars, such as gears, engine parts, and heat sinks. This contributes to improved fuel economy and overall vehicle performance.
- Потребительская электроника: From intricate housings for mobile phones to innovative cooling solutions for laptops, metal atomization is making its way into the consumer electronics domain. This allows for the creation of complex geometries and improved heat dissipation.
The Future of Metal Atomization: A World of Possibilities
The field of metal atomization is constantly evolving, with research and development efforts focused on:
- Expanding the range of atomizable materials: New techniques are being developed to enable the atomization of challenging materials like high-alloy steels and refractory metals, opening doors for even more advanced applications.
- Finer powder production: The ability to produce even finer metal powders is crucial for pushing the boundaries of AM resolution and creating intricate micro-components.
- Sustainable atomization processes: Developing eco-friendly methods for metal atomization, such as utilizing recycled materials and minimizing energy consumption, is a key focus area for a sustainable future.
As metal atomization technology continues to mature, we can expect to see even more innovative applications emerge across various industries. From revolutionizing medical implants to creating lightweight and fuel-efficient vehicles, metal atomization holds immense potential to shape the future of manufacturing.
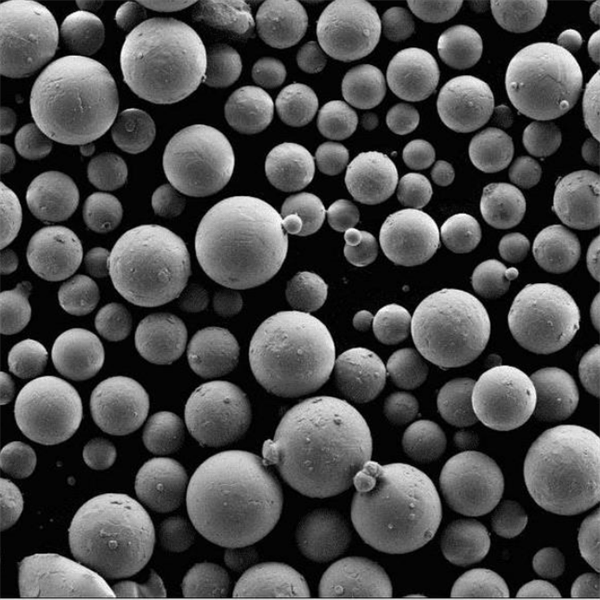
Часто задаваемые вопросы
What are the benefits of using metal atomization equipment?
Metal atomization equipment offers several advantages, including:
- Production of high-quality metal powders: These powders are essential for various applications, particularly in Additive Manufacturing.
- Material versatility: A wide range of metals and alloys can be atomized using different techniques.
- Control over powder properties: Desired characteristics like particle size and morphology can be tailored through process parameters.
What factors influence the choice of metal atomization equipment?
Several factors influence the selection of metal atomization equipment, including:
- The type of metal being processed: Different metals might require specific atomization methods or furnace configurations.
- Desired powder properties: Factors like powder purity, size distribution, and morphology play a crucial role.
- Production volume requirements: The chosen equipment should be able to handle the desired production rate.
- Budgetary considerations: Metal atomization equipment can range from basic to highly sophisticated, with varying costs.
What is the difference between metal atomization and metallization?
Metal atomization involves breaking down molten metal into fine particles. In contrast, metallization refers to the process of depositing a layer of metal onto a surface. Metallization can be achieved through various techniques like electroplating, thermal spraying, and sputtering.
Where can I learn more about metal atomization equipment?
Several resources offer valuable information on metal atomization equipment, including:
- Отраслевые ассоциации: Organizations like the Additive Manufacturing Users Group (AMUG) and the Metal Powder Industries Federation (MPIF) provide resources and educational materials on metal atomization.
- Equipment manufacturers: Leading manufacturers of metal atomization equipment often have detailed information on their websites and technical literature.
- Scientific publications: Research papers and articles published in technical journals delve deeper into the science and technology behind metal atomization.
Заключение
Metal atomization equipment is a powerful tool that unlocks a world of possibilities in metal Additive Manufacturing and beyond. By understanding the different types, functionalities, and technical aspects of this equipment, we can appreciate its role in shaping the future of manufacturing. As the technology continues to evolve, we can expect even more innovative applications to emerge, pushing the boundaries of what’s possible with metal.
О компании 3DP mETAL
Категория продукта
СВЯЖИТЕСЬ С НАМИ
Есть вопросы? Отправьте нам сообщение прямо сейчас! После получения вашего сообщения мы обработаем ваш запрос всей командой.