Imagine taking a solid block of steel and transforming it into a cloud of dust, only instead of dust, you have a collection of perfectly round, ultra-fine metal particles. That’s the magic of metal atomization technology. It’s a game-changer in various industries, allowing us to create new materials and applications with incredible properties.
This article dives deep into the fascinating world of metal atomization. We’ll explore the different methods used to break down bulk metal, the unique characteristics of metal powders, and the exciting ways they’re revolutionizing manufacturing.
Why Metal Atomization Technology Matters
Have you ever wondered how intricate parts for jet engines or customized implants for surgery are made? Often, the answer lies in metal powders produced through atomization. Traditional metalworking relies on casting, forging, or machining solid metal blocks. While effective, these methods have limitations.
- Сложность: Creating intricate shapes with traditional methods can be challenging and wasteful.
- Ограничения по материалу: Some high-performance metals are difficult or impossible to work with using conventional techniques.
- Strength and weight: Traditional methods might not achieve the ideal balance of strength and lightweight properties needed for advanced applications.
Metal atomization overcomes these limitations by creating a versatile starting material: metal powder. These fine particles, typically ranging from 5 to 150 microns (micrometers) in size, offer several advantages:
- Unmatched design freedom: Metal powders are perfect for additive manufacturing (3D printing) processes, allowing for the creation of complex and intricate shapes with minimal material waste.
- Unlocking new materials: Atomization makes it possible to work with even the most challenging metals, including reactive and high-melting-point materials like titanium and tantalum.
- Superior properties: Metal powders can be engineered to have specific properties like high strength, low weight, and improved resistance to corrosion or heat.
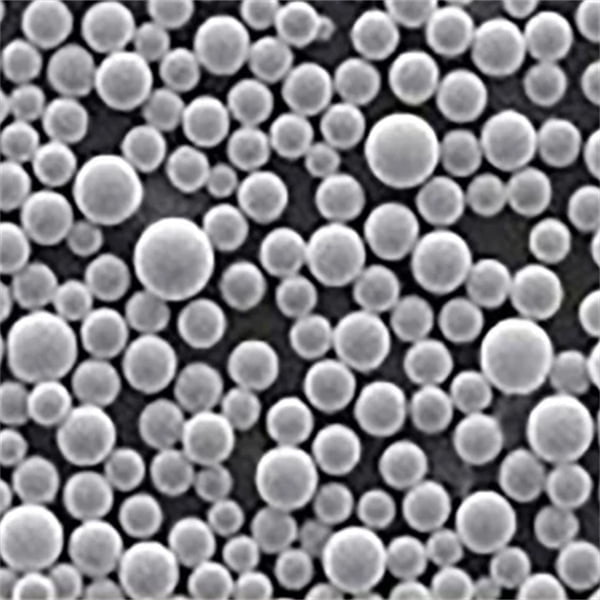
Different Metal Atomization Methods
Metal atomization isn’t a one-size-fits-all process. Different methods are employed depending on the desired powder characteristics and the type of metal being processed. Here’s a closer look at the three main methods:
- Распыление воды: This method uses a high-pressure water jet to break down a stream of molten metal into tiny droplets. It’s a mature and cost-effective technique, particularly suitable for less reactive metals like aluminum and copper. However, the resulting powders tend to be less spherical and have a broader size distribution compared to other methods.
- Газовая атомизация: Similar to water atomization, this method employs a high-velocity gas stream, typically inert gases like nitrogen or argon, to fragment the molten metal. Gas atomization offers greater control over particle size and shape, resulting in more spherical powders with a narrower size distribution. This method is particularly well-suited for a wider range of metals, including reactive materials like titanium and nickel.
- Плазменное распыление: This high-tech method utilizes an ionized gas stream (plasma) at extremely high temperatures to melt and atomize the metal. Plasma atomization is ideal for creating high-purity, spherical powders of reactive and refractory metals like titanium, tantalum, and tungsten. The high temperatures achieved in this process allow for excellent control over powder characteristics but come at a higher cost compared to other methods.
Выбор правильного метода: The selection of the atomization method depends on several factors, including:
- The desired properties of the final powder: Factors like particle size, shape, and purity will influence the choice of method.
- The type of metal being processed: Different metals have varying melting points and reactivity, requiring specific atomization techniques for optimal results.
- Cost considerations: Water atomization is generally the most cost-effective option, while plasma atomization is the most expensive.
Applications of Metal Atomization
Metal powders created through atomization have opened doors to exciting new possibilities across various industries. Here are some of the most prominent applications:
- Аддитивное производство (3D-печать): Metal powders are the primary material used in metal 3D printing technologies. This allows for the creation of complex, lightweight components for aerospace, automotive, and medical applications.
- Thermal Spray Coating: Metal powders are used to create protective and functional coatings on various surfaces. These coatings can improve wear resistance, corrosion resistance, and thermal properties. Applications include jet engine components, turbine blades, and biomedical implants.
- Литье металлов под давлением (MIM): This process combines the benefits of metalworking and plastic injection molding. Metal powders are mixed with a binder to create a feedstock that can be molded into complex shapes. The binder is then removed, leaving behind a high-density metal part. MIM is used for small, intricate components
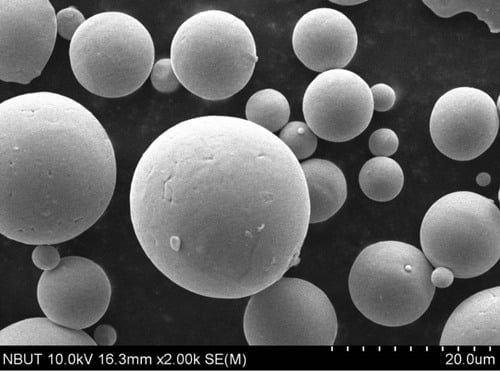
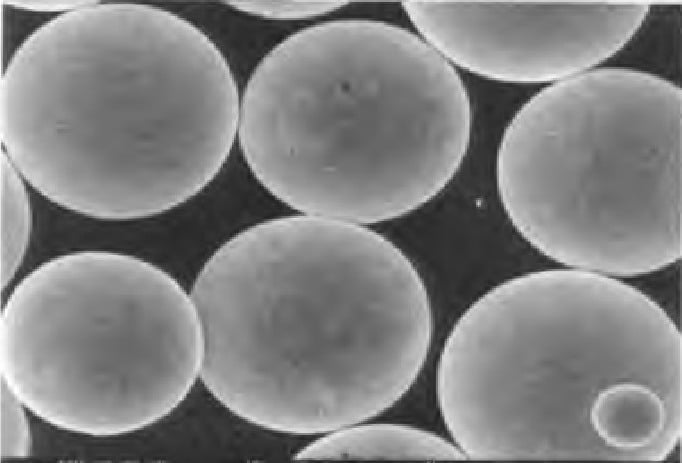
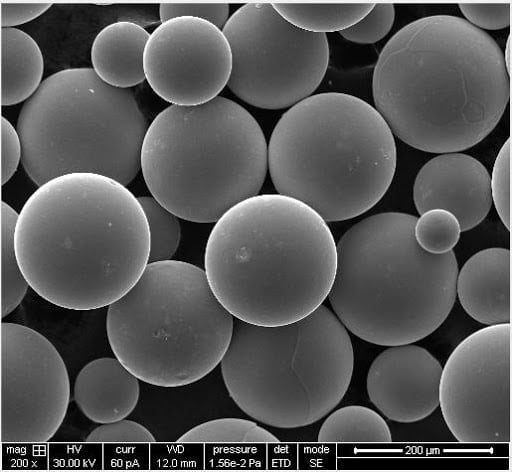
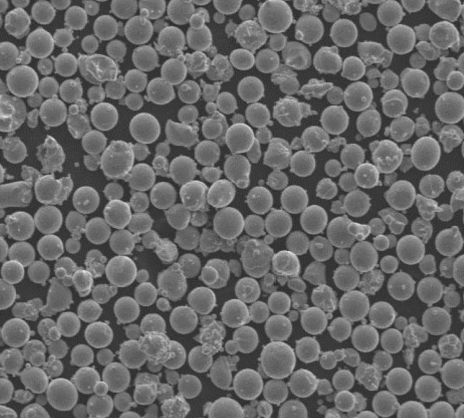
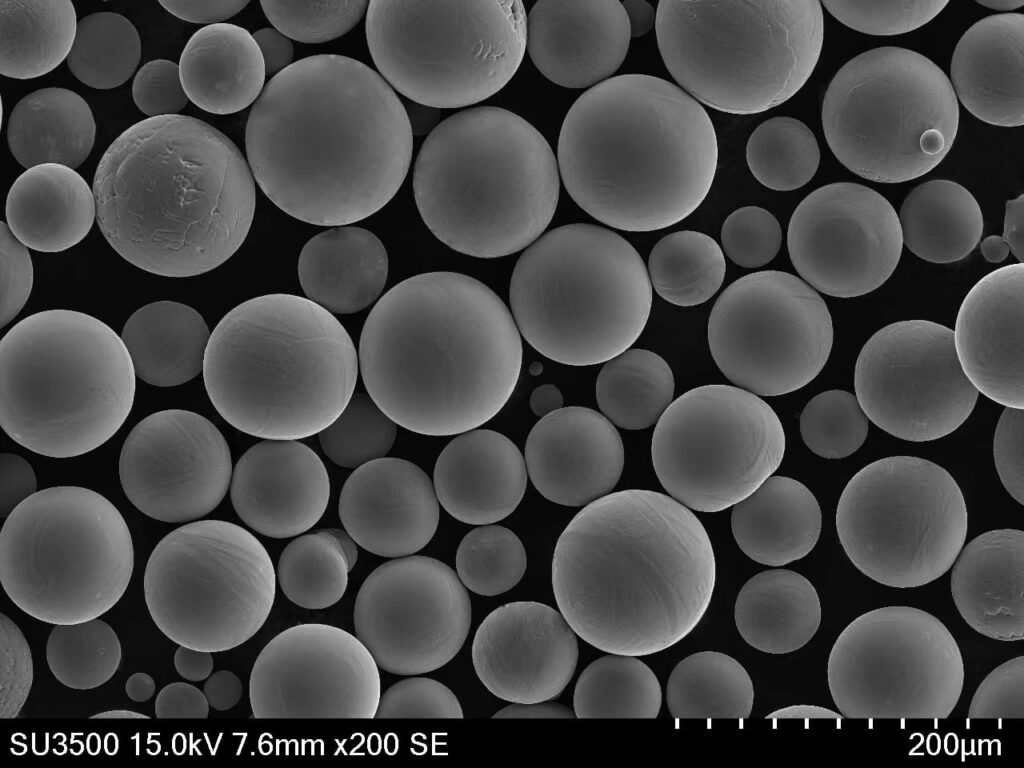
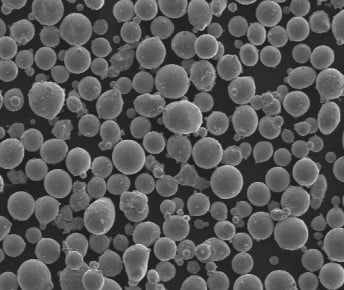
Characteristics of Metal Powders and their Impact
Metal powders may seem like tiny specks, but their characteristics play a crucial role in determining the final product’s performance. Here’s a breakdown of some key properties and how they influence applications:
- Размер и распределение частиц: The size and distribution of metal powder particles significantly impact the flowability, packing density, and surface finish of the final product. For instance, finer powders with a narrow size distribution are ideal for creating intricate features in 3D printing but might be challenging to handle due to reduced flowability. Conversely, coarser powders with a broader size distribution offer better flow characteristics but might limit the resolution achievable in 3D printing.
- Particle Shape: Ideally, metal powders should be spherical for optimal packing density and flowability. Spherical particles offer minimal inter-particle friction, leading to smoother surfaces and better material performance in applications like thermal spray coatings. However, some atomization methods might produce slightly irregular-shaped particles, which can be acceptable for certain applications.
- Porosity: Metal powders can have varying levels of porosity, referring to the presence of air pockets within the particles. In some cases, controlled porosity can be beneficial. For example, in filtration applications, some level of porosity allows the passage of fluids while retaining desired particles. However, excessive porosity can negatively impact the strength and density of the final product.
- Химия поверхности: The surface chemistry of metal powders refers to the presence of oxides, nitrides, or other chemical compounds on the particle surface. These can influence factors like powder flowability, reactivity during sintering (bonding process), and the final properties of the product. Surface treatments can be applied to modify the surface chemistry and enhance powder performance.
Understanding these characteristics and how they interact allows manufacturers to select the optimal metal powder for their specific application. For instance, in 3D printing a lightweight aerospace component, a fine metal powder with a narrow size distribution and spherical shape might be chosen to achieve high resolution and strength. Conversely, for a thermal spray coating application focused on wear resistance, a coarser powder with a slightly irregular shape might be suitable due to its improved flowability and adherence properties.
Advantages and Considerations of Metal Atomization
Metal atomization technology offers a multitude of advantages over traditional metalworking methods. Here are some key benefits:
- Unmatched Versatility: Metal atomization allows for the processing of a wide range of metals, including those difficult or impossible to work with using conventional techniques. This opens doors to the development of new materials with superior properties.
- Enhanced Control: The atomization process allows for precise control over the size, shape, and distribution of metal particles. This level of control translates to superior product quality and consistency in various applications.
- Сокращение отходов: Compared to traditional methods that involve machining solid metal blocks, metal atomization generates minimal waste. This translates to cost savings and a more environmentally friendly manufacturing process.
- Эффективность материала: Metal powders can be precisely deposited where needed in additive manufacturing processes, minimizing material waste and allowing for the creation of lightweight yet strong structures.
However, metal atomization also comes with some considerations:
- Стоимость: The cost of metal powders can vary depending on the atomization method, the type of metal, and the desired powder characteristics. Plasma atomization, for instance, produces high-purity powders but comes at a higher cost compared to water atomization.
- Обработка порошка: Metal powders can be susceptible to oxidation and moisture absorption, necessitating careful handling and storage procedures to maintain their quality and prevent degradation.
- Safety Measures: Fine metal powders can pose a safety risk if inhaled. Proper ventilation and handling procedures are crucial to ensure a safe working environment.
Despite these considerations, the advantages of metal atomization significantly outweigh the drawbacks, making it a transformative technology for various industries.
Exploring the Exciting Landscape of Metal Atomization
The future of metal atomization is bright, with continuous advancements in technology leading to even more possibilities. Here are some exciting trends to watch:
- Nanoparticle Atomization: The development of techniques for producing metal nanoparticles through atomization could open doors to entirely new applications in areas like electronics, catalysts, and bioprinting.
- Multi-Material Powders: Research is ongoing in developing processes for creating metal powders with blended compositions or even composite structures. This could lead to the creation of materials with entirely new combinations of properties.
- Sustainable Atomization: There’s a growing focus on developing more environmentally friendly atomization technologies. This could involve exploring alternative atomization media or using recycled materials in the process.
As metal atomization continues to evolve, we can expect to see even more innovative materials and applications emerge. From lightweight and fuel-efficient aircraft components to customized medical implants with enhanced biocompatibility, the possibilities are truly boundless.
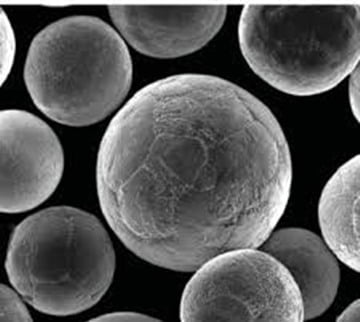
Часто задаваемые вопросы
Q: What are the typical sizes of metal powder particles?
A: Metal powder particles produced through atomization typically range from 5 to 150 microns (micrometers) in size. However, this range can vary depending on the specific atomization method and the desired application. For instance, finer powders below 10 microns might be used in specialized 3D printing applications requiring high resolution, while coarser powders exceeding 100 microns might be suitable for thermal spraying where a focus lies on deposition efficiency and wear resistance.
Q: How does metal atomization compare to other metal powder production methods?
A: There are alternative methods for producing metal powders, such as mechanical grinding or crushing. However, these methods generally result in powders with irregular shapes, broad size distributions, and potential contamination. Metal atomization offers a more controlled and consistent approach, producing spherical powders with a narrower size distribution and minimal contamination. This translates to superior powder flowability, packing density, and ultimately, the quality of the final product.
Q: Can metal powders produced through atomization be recycled?
A: Yes, in many cases, metal powders can be recycled. The recyclability depends on the specific type of metal and any contaminants present. In additive manufacturing processes, for instance, unutilized metal powder can often be collected and reused after sieving to remove any impurities. Recycling metal powders not only reduces waste but also promotes a more sustainable manufacturing process.
Q: What safety precautions are necessary when handling metal powders?
A: Metal powders, especially fine powders, can pose a health risk if inhaled. Here are some crucial safety precautions to consider:
- Proper ventilation: Ensure adequate ventilation in the workspace to prevent the accumulation of airborne metal particles.
- Respiratory protection: Wear appropriate respiratory protection, such as a respirator with a high-efficiency particulate air (HEPA) filter, when handling metal powders.
- Skin protection: Wear gloves and protective clothing to minimize skin contact with metal powders.
- Proper storage: Store metal powders in sealed containers in a dry and cool environment to prevent oxidation and moisture absorption.
By following these safety protocols, workers can minimize the risks associated with metal powder handling.
Q: What are the future applications of metal atomization technology?
A: As discussed earlier, the future of metal atomization is brimming with potential. Here are some exciting possibilities to explore:
- Аэронавтика и космонавтика: Metal atomization will likely play a crucial role in developing lighter, stronger, and more heat-resistant components for future aircraft and spacecraft.
- Biomedical implants: The ability to create metal powders with tailored properties could lead to the development of next-generation biomedical implants with improved biocompatibility and osseointegration (bone integration).
- Электроника: Nanoparticle metal powders produced through atomization could revolutionize the electronics industry, enabling the creation of miniaturized and high-performance electronic components.
О компании 3DP mETAL
Категория продукта
СВЯЖИТЕСЬ С НАМИ
Есть вопросы? Отправьте нам сообщение прямо сейчас! После получения вашего сообщения мы обработаем ваш запрос всей командой.