Imagine turning a steaming vat of molten metal into a cloud of ultra-fine powder, each particle a million times smaller than a marble. That’s the magic of оборудование для распыления металлического порошка, a technological marvel that’s revolutionizing countless industries.
In this comprehensive guide, we’ll delve into the fascinating world of metal powder atomization. We’ll explore the different types of equipment, uncover their diverse applications, and shed light on the advantages that make this technology so groundbreaking. So, buckle up and get ready to explore the intricate dance between molten metal and microscopic marvels!
Different Types of Metal Powder Atomization Equipment
Metal powder atomization equipment comes in two main flavors: water atomization и распыление газа. Each technique boasts its own strengths and caters to specific needs. Let’s take a closer look:
- Распыление воды: Picture a high-pressure stream of water colliding with a molten metal stream, shattering it into tiny droplets that solidify in mid-air. This rapid cooling process creates a fine, spherical powder. Water atomization is a cost-effective option, well-suited for high-volume production из common metals like aluminum and copper. However, it may introduce oxygen contamination and limit the production of reactive metals like titanium.
- Газовая атомизация: In this method, an inert gas like argon is used to break down the molten metal. The gas stream can be a jet, a de Laval nozzle, or a rotary atomizer. Gas atomization offers several advantages. It produces purer powders with a narrower size distribution compared to water atomization. This makes it ideal for reactive metals и high-performance applications like aerospace and medical implants. However, gas atomization equipment tends to be more expensive and have a lower production rate compared to its water-based counterpart.
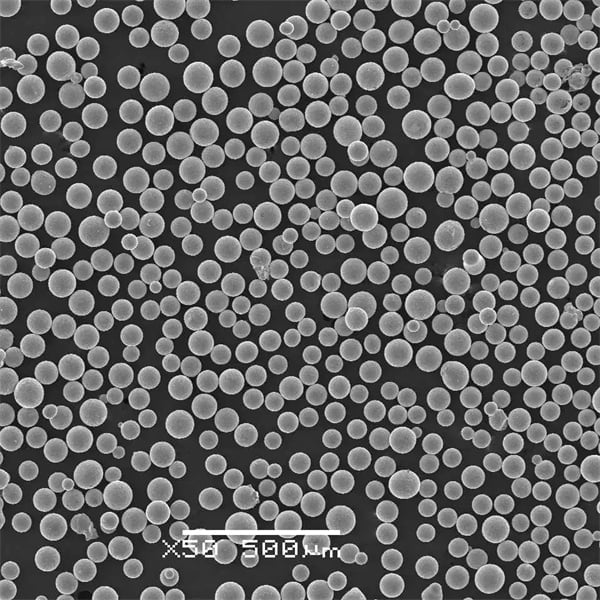
Choosing the Right Equipment:
The choice between water and gas atomization depends on several factors:
- Metal type: Water atomization works well for non-reactive metals, while gas atomization is preferred for reactive ones.
- Powder quality requirements: Gas atomization offers superior purity and size control.
- Объем производства: Water atomization excels in high-volume production.
- Бюджет: Water atomization is generally more cost-effective.
Beyond the Basics: Advanced Techniques
The world of metal atomization doesn’t stop there. Innovative techniques like vacuum atomization и electrolytic atomization are pushing the boundaries even further. Vacuum atomization creates ultra-clean powders in a controlled atmosphere, perfect for demanding applications like jet engine components. Electrolytic atomization utilizes an electric current to break down the metal, offering precise control over particle size and morphology.
Various Applications of Metal Powder Additive Manufacturing Takes Center Stage
Metal powder atomization is the backbone of a rapidly growing field: additive manufacturing (AM), also known as 3D printing. Here, metal powder is used to build complex objects layer by layer, opening doors to revolutionary advancements in various industries:
- Аэронавтика и космонавтика: Metal AM allows for the creation of lightweight, high-strength components for airplanes and spacecraft, leading to increased fuel efficiency and performance.
- Автомобильный: Complex car parts with intricate designs can be produced using metal AM, enabling weight reduction and improved fuel economy.
- Медицинский: The ability to create custom-made prosthetics and implants with biocompatible metal powders is revolutionizing patient care.
- Потребительские товары: From customized jewelry to lightweight sporting equipment, metal AM is making its way into everyday products.
Beyond AM: A Universe of Possibilities
Metal powder atomization extends far beyond the realm of 3D printing. Here are some other exciting applications:
- Литье металлов под давлением (MIM): Metal powders are mixed with a binder, molded into complex shapes, and then debindered and sintered to create high-precision metal parts.
- Термическое напыление: Metal powders are melted and sprayed onto surfaces to create wear-resistant coatings or build up worn-out parts.
- Brazing and Welding: Metal powders can be used as filler materials for joining metal components, offering superior strength and control.
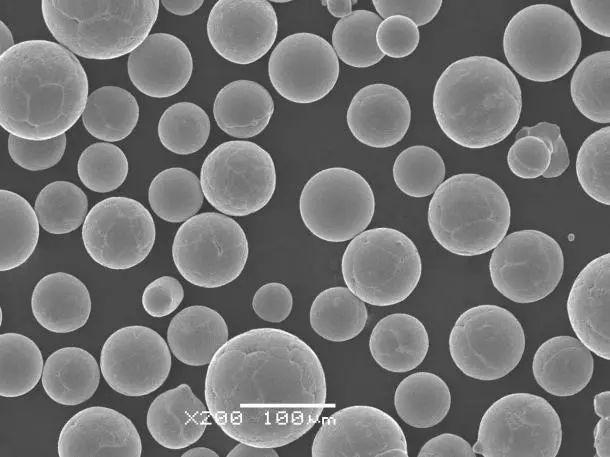
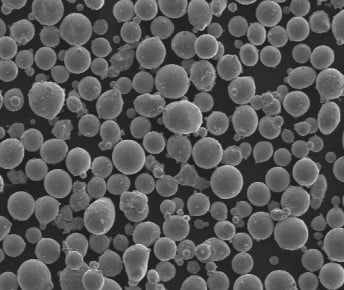
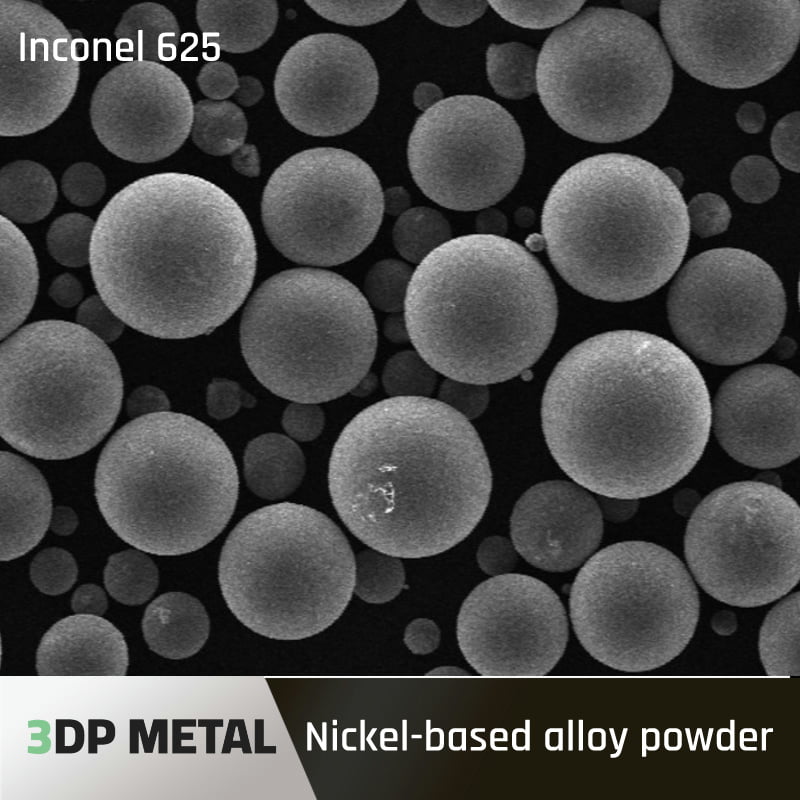
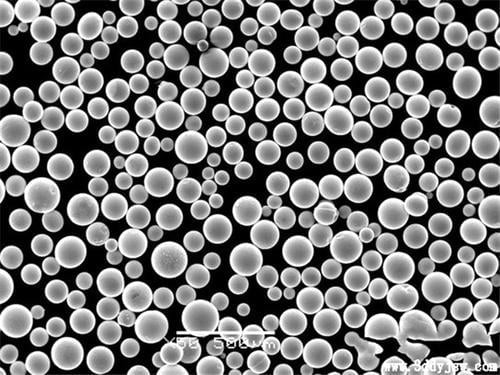
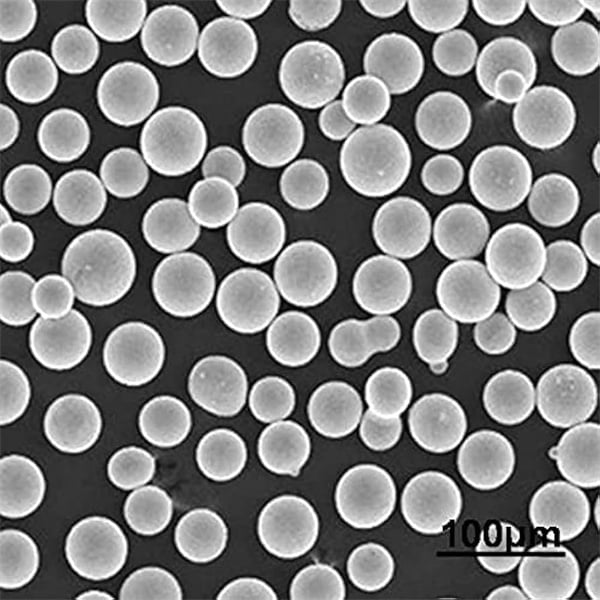
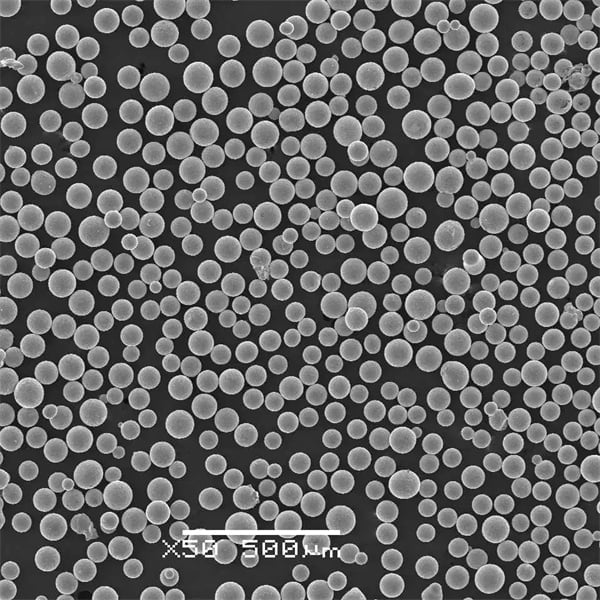
Преимущества Metal Powder Atomization Equipment
Metal powder atomization equipment offers a multitude of advantages that are transforming manufacturing processes:
- Свобода дизайна: Unlike traditional subtractive manufacturing techniques, metal AM allows for the creation of complex geometries with internal channels and lattices, previously impossible to achieve.
- Облегчение: Metal powders can be used to create lightweight, high-strength components, leading to increased fuel efficiency and performance in applications like aerospace and automotive.
- Material Efficiency : Metal AM minimizes waste by using only the necessary material to build the desired object. This is a stark contrast to traditional subtractive methods that generate significant scrap.
- Быстрое прототипирование: The ability to quickly create prototypes using metal AM allows for faster design iteration and product development cycles.
- Массовая кастомизация: Metal AM enables the production of customized parts in small batches, making it ideal for personalized products and niche applications.
- Улучшенная производительность: Metal powders can be engineered with unique properties, leading to components with superior strength, wear resistance, and heat tolerance.
Экологические преимущества: Metal powder atomization can contribute to a greener manufacturing landscape. Here’s how:
- Сокращение отходов материалов: As mentioned earlier, metal AM minimizes waste by using only the necessary material. This translates to less material ending up in landfills.
- Облегчение: The ability to create lightweight components using metal powders leads to reduced energy consumption during transportation in industries like automotive and aerospace.
- Производство по требованию: Metal AM allows for localized production, reducing the need for long-distance transportation and associated emissions.
Проблемы и соображения
While metal powder atomization offers a plethora of advantages, it’s important to acknowledge some challenges and considerations:
- High Equipment Cost: Metal atomization equipment, particularly gas atomization systems, can be expensive to purchase and maintain.
- Powder Quality Control: Maintaining consistent powder quality is crucial for successful applications like AM. Factors like particle size distribution and morphology need to be tightly controlled.
- Опасения по поводу безопасности: Metal powders can be flammable and pose health risks if inhaled. Proper handling and safety protocols are essential.
- Ограниченный выбор материалов: Not all metals are readily available in atomized powder form. Research and development are ongoing to expand the range of available materials.
- Постобработка: Metal powder-based parts often require post-processing steps like heat treatment or hot isostatic pressing (HIP) to achieve their final properties.
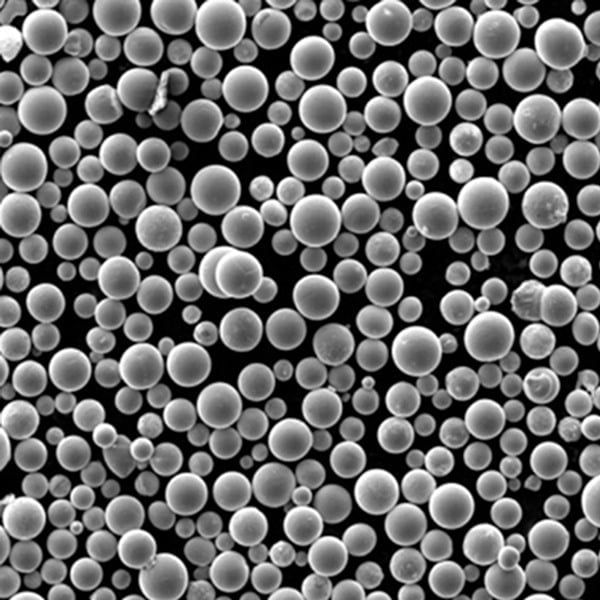
Часто задаваемые вопросы
Here’s a breakdown of some frequently asked questions regarding metal powder atomization equipment:
Вопрос | Ответить |
---|---|
What are the key factors to consider when choosing between water and gas atomization? | The primary factors include the type of metal being processed, desired powder quality, production volume, and budget. |
What are some emerging trends in metal powder atomization? | There’s a growing focus on developing finer and more uniform powders, exploring new atomization techniques like electrolytic atomization, and utilizing recycled metal feedstock for sustainable production. |
How is the metal powder atomization industry impacting the environment? | While there are challenges, metal AM, enabled by metal powder atomization, can contribute to a greener future by minimizing waste and enabling lightweighting. |
What are the safety precautions to take when handling metal powders? | Proper ventilation, personal protective equipment like respirators, and safe handling procedures are crucial to prevent inhalation and fire hazards. |
What is the future of metal powder atomization equipment? | As the demand for AM and other applications grows, advancements in atomization technology can be expected, leading to more efficient, cost-effective, and versatile equipment. |
Заключение
Metal powder atomization equipment is not just a piece of machinery; it’s a gateway to a world of possibilities. From the intricate structures of 3D-printed implants to the lightweight components of tomorrow’s airplanes, this technology is shaping the future of manufacturing. As research and development continue, we can expect even more innovative applications and advancements in metal powder atomization, pushing the boundaries of what’s possible and revolutionizing countless industries for years to come.
О компании 3DP mETAL
Категория продукта
СВЯЖИТЕСЬ С НАМИ
Есть вопросы? Отправьте нам сообщение прямо сейчас! После получения вашего сообщения мы обработаем ваш запрос всей командой.