Surface coating materials are the unsung heroes of our everyday lives. They shield our cars from rust, our bridges from corrosion, and our toys from chipping. But these coatings are far more than just protective layers; they can add a dazzling pop of color, enhance electrical conductivity, or even impart self-healing properties. In this comprehensive guide, we’ll delve into the fascinating world of surface coatings, exploring their types, properties, applications, and the remarkable metal powders that play a crucial role in their composition.
An Overview of Surface Coating Materials
Imagine your favorite pair of headphones. The sleek, vibrant finish isn’t just for aesthetics; it’s likely a coating that protects the underlying plastic from scratches and enhances its durability. This is just one example of the countless applications of surface coatings. But what exactly are they?
Surface coatings are essentially thin layers applied to the surface of a material to modify its properties. They can be organic (like paints and varnishes) or inorganic (like metal coatings) and come in a wide variety of formulations to achieve specific goals. Think of them as a versatile toolbox, offering a range of benefits:
- Protection: Coatings act as a barrier against environmental elements like moisture, UV radiation, and corrosion, extending the lifespan of the underlying material.
- Эстетика: From the gleaming chrome on a motorcycle to the vibrant hues on a children’s swing set, coatings enhance the visual appeal of objects.
- Functionality: Certain coatings can improve electrical conductivity, thermal insulation, or even impart self-cleaning abilities.
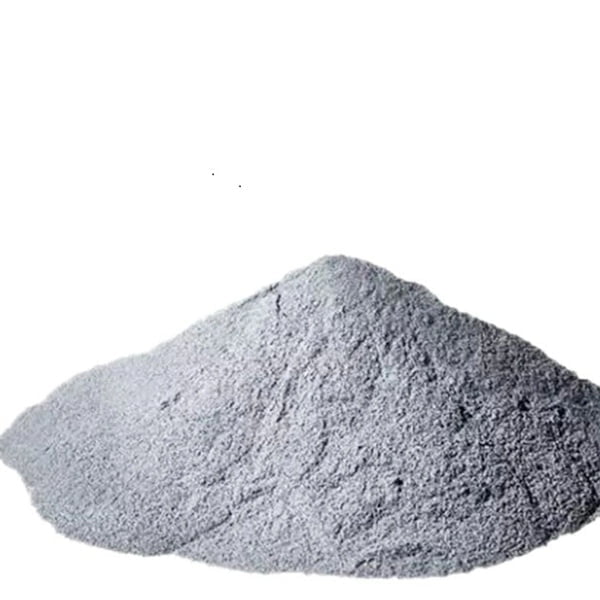
Composition and Properties of Surface Coatings
Surface coatings are typically a complex blend of several key components:
- Папки: These act as the glue, holding the coating together and adhering it to the substrate (the underlying material). Common binders include resins, epoxies, and polyurethanes.
- Пигменты: These provide color and opacity to the coating. Imagine a can of red paint – the red pigment is what gives it its vibrant hue.
- Solvents: These thin the coating for easier application and then evaporate as the coating dries. Water can be a solvent, but many coatings use organic solvents as well.
- Добавки: These specialized ingredients can enhance specific properties like UV resistance, fire retardancy, or even anti-microbial properties.
The specific composition of a coating determines its key properties:
- Adhesion: How well the coating sticks to the substrate. A poorly adhering coating will peel or flake off easily.
- Долговечность: How well the coating withstands wear and tear, harsh environments, and the test of time.
- Гибкость: How well the coating bends without cracking or breaking. This is crucial for materials that undergo movement.
- Chemical Resistance: How well the coating stands up to exposure to chemicals, solvents, or other aggressive substances.
- Твердость: This determines the coating’s resistance to scratches and abrasions. Imagine the difference between a soft, decorative paint and a hard, scratch-resistant coating on a tool.
Types of Surface Coatings
The world of surface coatings is vast, offering a variety of options to suit different needs. Here’s a glimpse into some of the most common types:
- Liquid Coatings: These are the most familiar type, applied in a liquid form (like paint) and then drying to form a solid film. They come in solvent-based, water-based, and high-solids varieties, each with its own advantages and limitations.
- Powder Coatings: These are dry, free-flowing powders that are electrostatically applied to a substrate and then cured with heat. They offer excellent durability, environmental benefits, and a wide range of color options.
- Electroplated Coatings: This method uses an electrical current to deposit a thin layer of metal onto a conductive substrate. It’s commonly used for applications like chrome plating on car parts or gold plating on jewelry.
- Vapor Deposition Coatings: These involve depositing a thin film of material onto a substrate in a vacuum chamber. This method can create highly specialized coatings with unique properties, like improved wear resistance or electrical conductivity.
the World of Metal Powders in Surface Coatings
Metal powders play a crucial role in many surface coatings, particularly powder coatings. These tiny metallic particles offer a multitude of benefits:
- Долговечность: Metal powders can significantly enhance the hardness, scratch resistance, and corrosion resistance of a coating. Imagine a playground slide – a metal powder coating can withstand the constant wear and tear from children’s play.
- Электропроводность: Certain metal powders, like copper or silver, can improve the electrical conductivity of a coating. This is vital for components used in electronics and electrical applications.
- Эстетика: Metal powders can create stunning visual effects. For example, aluminum powder can create a shimmering, metallic finish, while bronze powder can impart a warm, antique look.
But with great power comes great responsibility (or rather, a need for careful selection). Here are some key factors to consider when choosing metal powders for your coating:
- Размер и распределение частиц: The size and distribution of the metal particles significantly impact the properties of the coating. Finer particles generally create smoother finishes, while larger particles can enhance texture and provide improved wear resistance.
- Metal type: Different metals offer unique properties. For instance, stainless steel powder provides excellent corrosion resistance, while zinc powder is known for its superior sacrificial protection against rust.
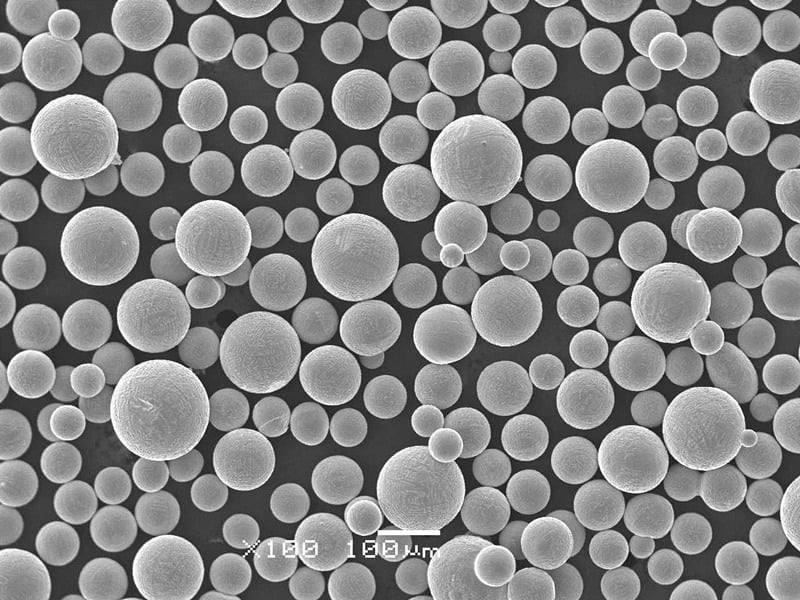
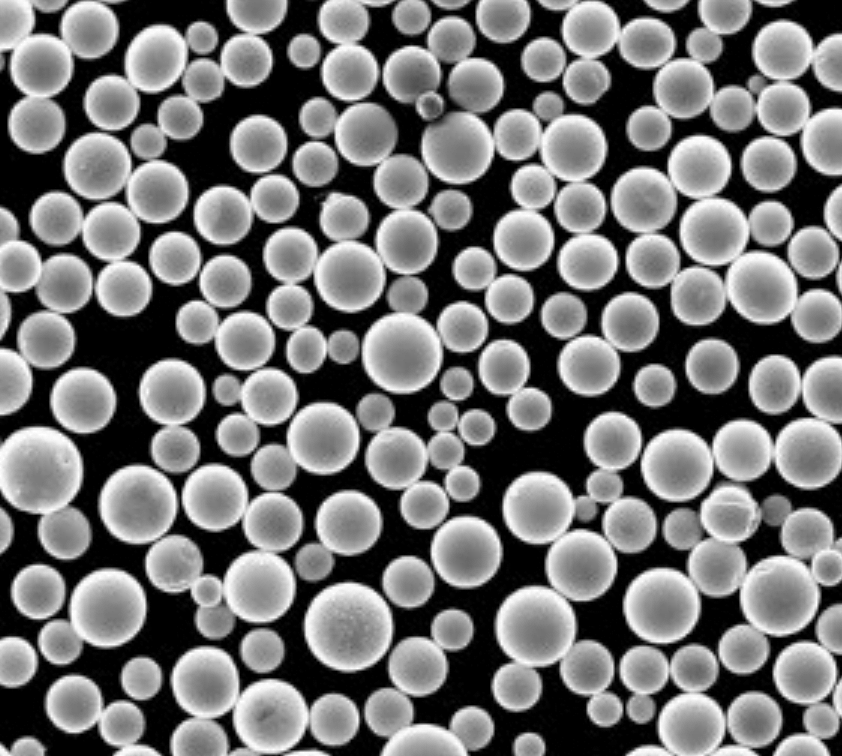
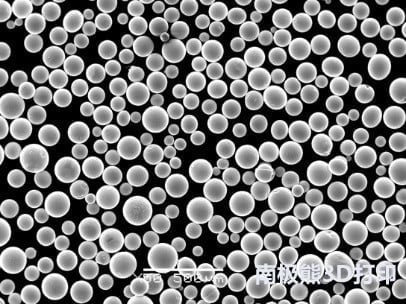
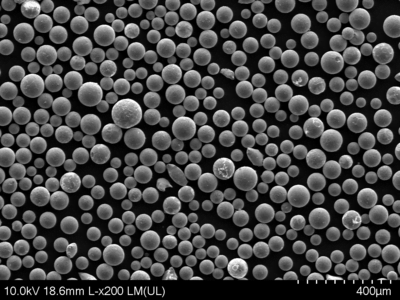
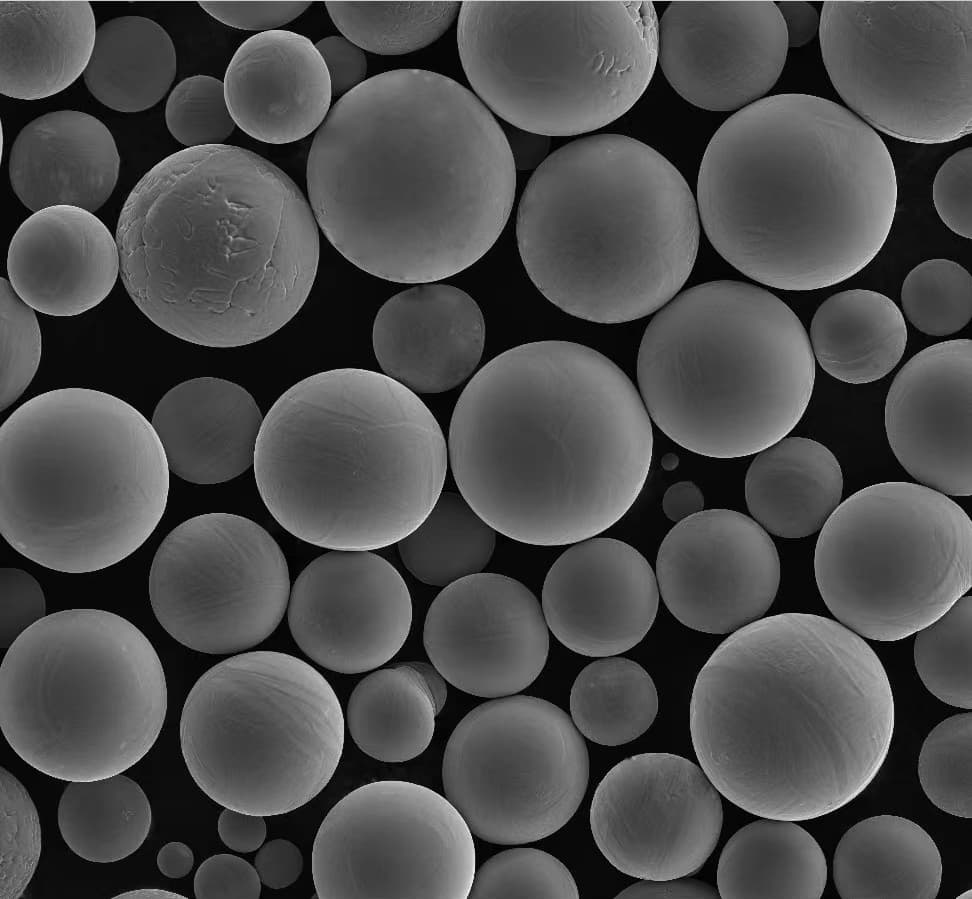
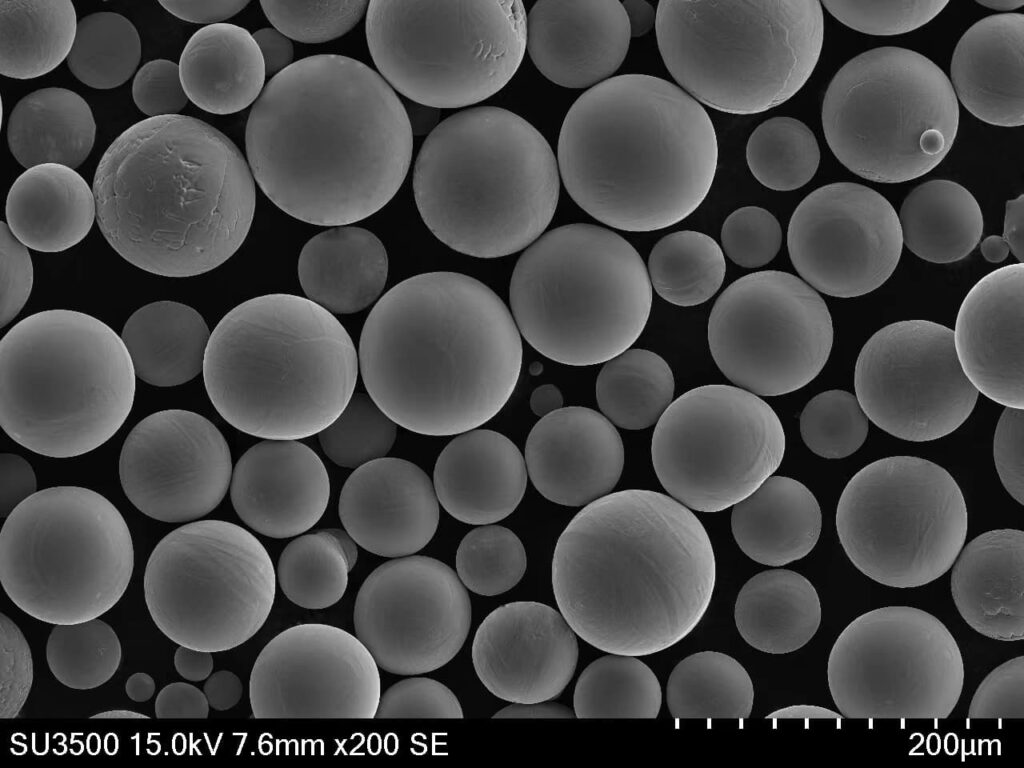
Here’s a closer look at some of the most popular metal powders used in surface coatings, along with their key characteristics and applications:
Металлический порошок | Описание | Основные характеристики | ПРИМЕНЕНИЯ |
---|---|---|---|
Алюминиевая пудра | Fine, silvery particles | Excellent reflectivity, lightweight, good corrosion resistance | Automotive parts, appliances, heat sinks, decorative finishes |
Бронзовый порошок | Flaky particles with a warm, golden hue | Distinctive aesthetic appeal, good corrosion resistance | Architectural elements, furniture hardware, artistic finishes |
Медный порошок | Spherical particles with a reddish-brown color | High electrical conductivity, good heat dissipation | Electrical components, heat sinks, EMI shielding |
Никелевый порошок | Irregular-shaped particles with a silvery-white color | Magnetic properties, good hardness, corrosion resistance | Electromagnetic components, wear-resistant coatings, hard disk drives |
Порошок из нержавеющей стали | Spherical particles with a silvery-gray color | Excellent corrosion resistance, high strength, good heat resistance | Medical equipment, food processing equipment, marine hardware |
Цинковый порошок | Irregular-shaped particles with a grayish-white color | Sacrificial corrosion protection, good electrical conductivity | Galvanized coatings, electrical grounding applications, anti-corrosion primers |
Железный порошок | Irregular-shaped particles with a dark gray color | Magnetic properties, high density, good hardness | Electromagnetic components, heavy-duty coatings, weight balancing applications |
Silicon Carbide Powder | Sharp, angular particles with a black color | Exceptional hardness, wear resistance, good thermal conductivity | Abrasive blasting media, cutting tools, wear-resistant coatings |
Титановый порошок | Spherical particles with a silvery-white color | Высокое соотношение прочности и веса, отличная коррозионная стойкость | Аэрокосмические компоненты, медицинские имплантаты, высокопроизводительные спортивные товары |
Beyond the Basics: A Deeper Dive into Metal Powder Selection
Choosing the right metal powder isn’t just about aesthetics; it’s about optimizing the coating for its specific application. Here are some additional considerations:
- Chemical compatibility: Ensure the chosen metal powder is compatible with the other coating components and the substrate material. A reactive metal powder could potentially cause unwanted chemical reactions.
- Application method: Different application methods (like electrostatic spray or fluidized bed) may favor specific particle sizes and shapes.
- Environmental regulations: Some metal powders may have environmental restrictions depending on their composition. It’s crucial to comply with relevant regulations.
By carefully considering these factors and the unique properties of each metal powder, you can select the ideal material to create a high-performance, long-lasting surface coating.
Применение Surface Coating Materials
Surface coatings have a vast array of applications across different industries. Here’s a glimpse into their diverse uses:
Промышленность | ПРИМЕНЕНИЯ | Преимущества |
---|---|---|
Строительство | Protecting bridges, buildings, and other structures from corrosion, weather elements, and fire | Extends lifespan, enhances aesthetics, improves safety |
Автомобильный | Coating car bodies, wheels, and engine components | Protects against rust, scratches, and wear, enhances appearance |
Аэрокосмическая отрасль | Creating lightweight, high-performance coatings for aircraft components | Reduces weight for fuel efficiency, enhances durability under extreme conditions |
Товары народного потребления | Coating appliances, electronics, furniture, and toys | Protects against wear and tear, enhances aesthetics, provides scratch resistance |
Морская пехота | Protecting ships, boats, and offshore structures from harsh saltwater environments | Prevents corrosion, biofouling (marine organism growth), improves underwater visibility |
Медицинские приборы | Coating implants and surgical instruments | Enhances biocompatibility, reduces risk of infection, improves wear resistance |
Pros and Cons of Surface Coating Materials
Преимущества
- Enhanced Aesthetics: From vibrant colors to metallic finishes, coatings can elevate the visual appeal of objects, making them more attractive and marketable.
- Functional Benefits: Certain coatings can offer specific functionalities like improved electrical conductivity, thermal insulation, self-cleaning properties, or even fire resistance.
- Универсальность: With a wide range of types and formulations available, surface coatings can be tailored to meet the specific needs of a vast array of applications.
Недостатки
- Воздействие на окружающую среду: Some coating materials and application processes can generate volatile organic compounds (VOCs) that contribute to air pollution. However, advancements in technology are leading to the development of more eco-friendly coatings.
- Application Challenges: Certain coating methods require specialized equipment and expertise, potentially increasing costs and complexity.
- Improper Application: If not applied correctly, coatings may not adhere properly or achieve their desired performance, leading to premature failure.
Making Informed Choices: Weighing the Pros and Cons
The decision to use a surface coating requires careful consideration of both the benefits and drawbacks. Here are some key questions to ask yourself:
- What is the primary purpose of the coating? Is it for protection, aesthetics, functionality, or a combination of factors?
- What is the substrate material? Different materials require compatible coatings to ensure proper adhesion and performance.
- What is the intended lifespan of the coated object? High-performance coatings may be necessary for applications requiring long-term durability.
- What are the environmental regulations in your area? Ensure the chosen coating and application method comply with relevant regulations.
- What is your budget? Consider the cost of the coating material, application equipment, and labor.
By carefully evaluating these factors, you can select the most suitable surface coating material for your project, maximizing the benefits while minimizing the drawbacks.
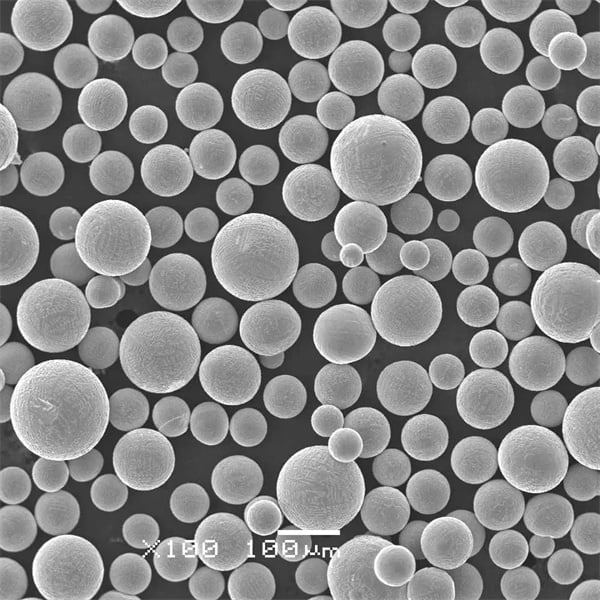
Часто задаваемые вопросы
Here are some frequently asked questions (FAQs) about surface coatings to shed light on any lingering curiosities:
Q: How long do surface coatings typically last?
A: The lifespan of a surface coating depends on several factors, including the type of coating, the substrate material, the application process, and the environmental conditions. High-quality coatings applied correctly can last for many years, while lower-quality coatings or those exposed to harsh environments may require more frequent reapplication.
Q: Are surface coatings safe?
A: The safety of surface coatings depends on the specific materials used. Some older coatings may contain harmful chemicals like lead or chromates. However, modern formulations prioritize safety and often comply with strict regulations. Always ensure proper ventilation during application and consult the manufacturer’s safety data sheet (SDS) for specific handling instructions.
Q: Can surface coatings be repaired?
A: Yes, in many cases, surface coatings can be repaired. The repair method depends on the extent of the damage and the type of coating. Minor scratches or chips may be touched up with a compatible paint, while more extensive damage may require complete removal and reapplication of the coating.
Q: What are some of the latest advancements in surface coating technology?
A: The surface coating industry is constantly evolving. Some exciting advancements include:
- Self-healing coatings that can repair minor scratches upon exposure to light or heat.
- Antibacterial coatings that can help prevent the spread of germs on surfaces.
- Superhydrophobic coatings that repel water and other liquids, making surfaces self-cleaning and easier to maintain.
By understanding the vast potential of материалы для покрытия поверхности, their diverse applications, and the considerations for selection, you can harness their power to protect, enhance, and extend the lifespan of the objects in your world. So, the next time you admire the gleaming finish on your car or the vibrant colors on your child’s swing set, remember – it’s the magic of surface coatings at work!
О компании 3DP mETAL
Категория продукта
СВЯЖИТЕСЬ С НАМИ
Есть вопросы? Отправьте нам сообщение прямо сейчас! После получения вашего сообщения мы обработаем ваш запрос всей командой.