Overview of the Sinter Equipment Industry
The sinter equipment industry is a fascinating and highly technical sector that plays a crucial role in materials science and manufacturing. It revolves around the process of sintering, a method used to create solid materials from powder by heating them without liquefying them completely. This process is essential for producing a wide range of products, from everyday household items to advanced aerospace components. But what exactly is sintering? And how does it tie into the broader landscape of metalworking and powder metallurgy?
In simple terms, sintering is like baking a cake. You start with a mixture of ingredients—in this case, powdered metals or ceramics—and apply heat to bond the particles together. The result is a solid piece with specific properties tailored to its intended use. This method is highly efficient, reduces waste, and is perfect for creating complex shapes and high-strength materials.
Composition of Sinter Equipment Industry
To truly understand the sinter equipment industry, it’s essential to dive into the types of metal powders used, their compositions, and how they affect the final product’s properties. Each powder is unique, bringing specific characteristics to the table.
Metal Powder Model | Composition | Properties | Applications | Notable Characteristics |
---|---|---|---|---|
Iron Powder (Fe) | 99% Fe | High strength, magnetic | Automotive components, gears | Excellent compressibility, good sinterability |
Stainless Steel Powder (316L) | 18% Cr, 8% Ni, 74% Fe | Corrosion resistance, high toughness | Medical implants, aerospace parts | Superior corrosion resistance, good mechanical properties |
Copper Powder (Cu) | 99% Cu | High electrical conductivity | Electrical contacts, heat sinks | Excellent electrical conductivity, good thermal properties |
Aluminum Powder (Al) | 99% Al | Lightweight, good thermal conductivity | Lightweight structures, electronics | Low density, good corrosion resistance |
Tungsten Carbide Powder (WC) | 94% W, 6% C | High hardness, wear resistance | Cutting tools, mining equipment | Extremely hard, good wear resistance |
Cobalt-Chromium Powder (Co-Cr) | 60% Co, 30% Cr | High strength, biocompatibility | Dental implants, orthopedic devices | Biocompatible, excellent corrosion resistance |
Titanium Powder (Ti6Al4V) | 90% Ti, 6% Al, 4% V | High strength-to-weight ratio, biocompatibility | Aerospace, medical implants | Lightweight, high strength, excellent biocompatibility |
Nickel Powder (Ni) | 99% Ni | High corrosion resistance, good mechanical properties | Superalloys, batteries | Good resistance to oxidation, excellent durability |
Magnesium Powder (Mg) | 99% Mg | Lightweight, good machinability | Automotive, aerospace | Extremely lightweight, high specific strength |
Zinc Powder (Zn) | 99% Zn | Corrosion resistance, galvanization | Coatings, batteries | Excellent corrosion resistance, used in galvanization |
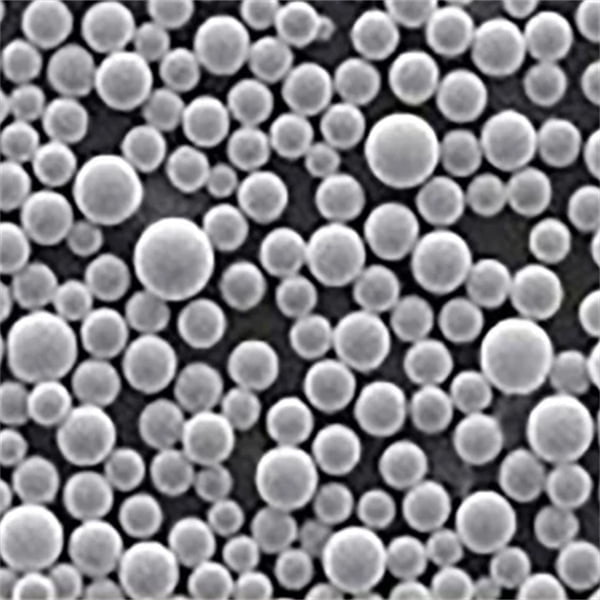
Characteristics of Sinter Equipment Industry
The sinter equipment industry is characterized by a wide range of factors that influence the final products’ quality, cost, and applicability. These factors include the types of equipment used, the specific processes involved, and the unique challenges and benefits associated with sintering.
Key Characteristics:
- Precision and Control: Sintering requires precise control over temperature, pressure, and time to ensure consistent product quality.
- Material Efficiency: Sintering is highly efficient in terms of material usage, reducing waste and improving cost-effectiveness.
- Complex Geometries: The sintering process allows for the creation of complex shapes that would be difficult or impossible to achieve with traditional manufacturing methods.
- Diverse Applications: From automotive to medical devices, the products of sintering are used across various industries.
- Environmental Impact: The sintering process can be more environmentally friendly compared to other manufacturing techniques, especially when using recycled materials.
Advantages of the Sinter Equipment Industry
Why is sintering so popular? Let’s break down some of the key advantages that make this process a go-to for many manufacturers.
- Cost-Effective Production: Sintering allows for high-volume production at a relatively low cost, especially when compared to traditional casting or machining.
- Material Versatility: The range of materials that can be sintered is vast, from metals and alloys to ceramics and composites, making it a versatile manufacturing technique.
- Energy Efficiency: Because sintering typically occurs at lower temperatures than melting, it can be more energy-efficient, reducing overall production costs.
- High Precision and Quality: Sintering offers excellent dimensional accuracy and can produce parts with tight tolerances, reducing the need for additional machining or finishing processes.
- Environmental Benefits: The ability to recycle and reuse metal powders in the sintering process minimizes waste, contributing to more sustainable manufacturing practices.
Applications of Sinter Equipment Industry
The applications of sintered products are as diverse as the industries that use them. Here’s a look at how sintered materials are utilized across different sectors.
Industry | Application | Benefits |
---|---|---|
Automotive | Engine components, gears, bushings | High strength, wear resistance |
Aerospace | Turbine blades, structural components | Lightweight, high-temperature resistance |
Medical | Implants, surgical instruments | Biocompatibility, corrosion resistance |
Electronics | Connectors, heat sinks, inductors | High electrical and thermal conductivity |
Tooling | Cutting tools, dies, punches | Extreme hardness, wear resistance |
Energy | Fuel cells, batteries | High energy density, durability |
Construction | Fasteners, structural components | High strength, corrosion resistance |
Consumer Goods | Watches, jewelry, kitchenware | Aesthetic appeal, durability |
Defense | Armor, projectiles | High strength, impact resistance |
Mining | Drilling bits, wear parts | High wear resistance, toughness |
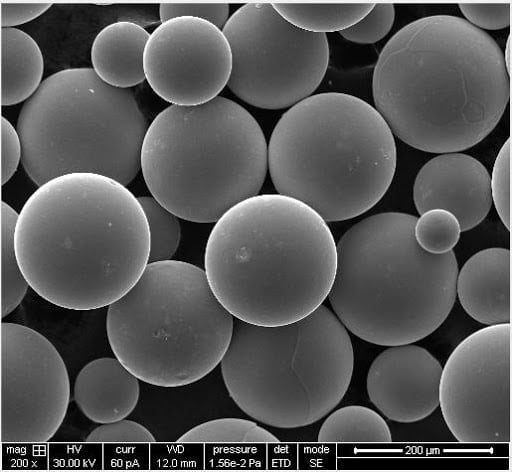
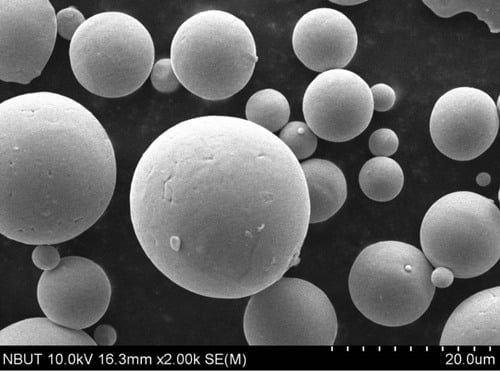
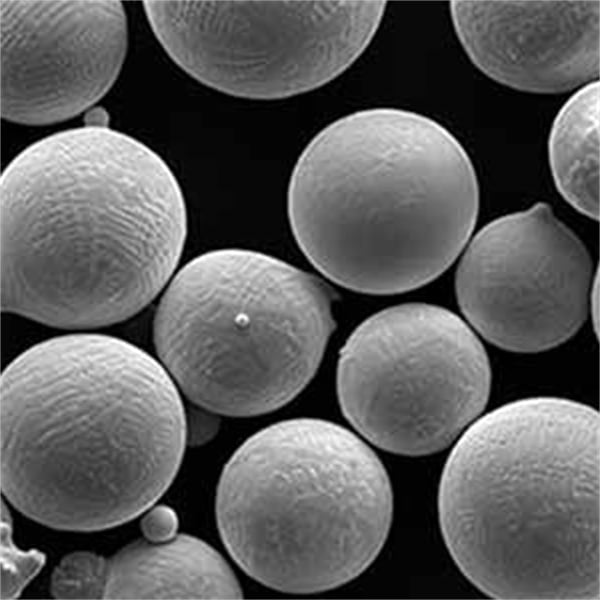
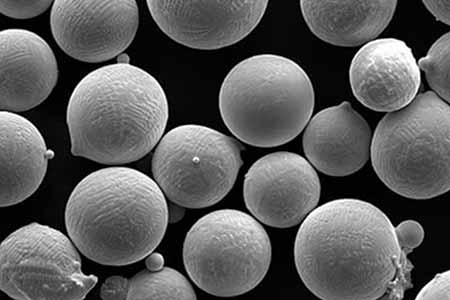
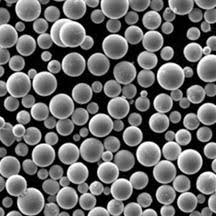
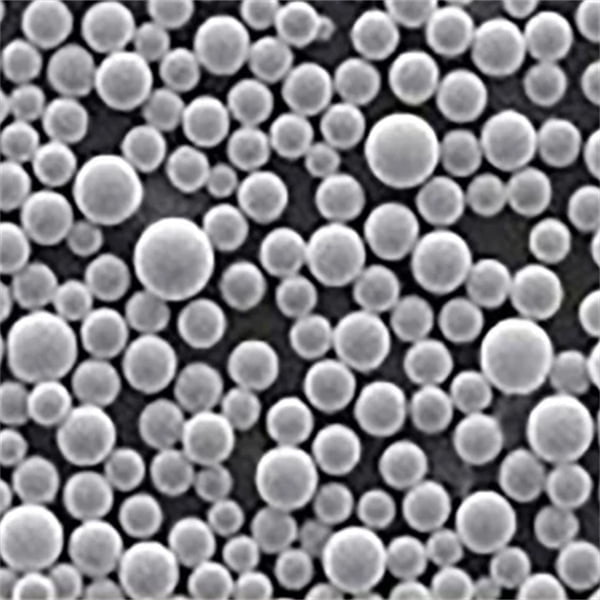
Specifications, Sizes, Grades, and Standards
In the sintering industry, specifications, sizes, grades, and standards are critical to ensuring the final product meets the required performance criteria. The following table outlines some common standards and specifications for various sintering materials.
Material | Grade | Size (µm) | Standard | Description |
---|---|---|---|---|
Iron Powder | A1000C | 45-150 | ASTM B214 | High compressibility for automotive components |
Stainless Steel | 316L | 25-75 | ASTM F138 | Corrosion-resistant for medical implants |
Copper Powder | C-123 | 20-45 | ASTM B170 | High conductivity for electrical applications |
Aluminum Powder | 6061-T6 | 10-60 | ASTM B928 | Lightweight for aerospace structures |
Tungsten Carbide | WC-Co 6% | 0.5-10 | ISO 9001 | Extremely hard for cutting tools |
Cobalt-Chromium | Co-Cr-Mo | 20-80 | ASTM F75 | Biocompatible for orthopedic devices |
Titanium Alloy | Ti6Al4V | 15-45 | ASTM F136 | High strength-to-weight ratio for aerospace |
Nickel Powder | Ni201 | 10-50 | ASTM B335 | Oxidation-resistant for superalloys |
Magnesium Powder | Mg99.9 | 5-25 | ASTM B90 | Lightweight for automotive applications |
Zinc Powder | Zn99.5 | 10-45 | ASTM B201 | Galvanization for corrosion protection |
Suppliers and Pricing Details
The availability and cost of sintering materials can vary depending on the supplier, material, and quantity ordered. Here’s a glimpse into some suppliers and pricing ranges for sintering materials.
Supplier | Material | Price (per kg) | Minimum Order | Location |
---|---|---|---|---|
Höganäs AB | Iron Powder (Fe) | $8 – $12 | 500 kg | Sweden |
Sandvik | Stainless Steel (316L) | $30 – $50 | 100 kg | USA |
Kymera International | Copper Powder (Cu) | $20 – $35 | 200 kg | USA |
Alcoa | Aluminum Powder (Al) | $15 – $25 | 300 kg | USA |
Kennametal | Tungsten Carbide (WC) | $50 – $100 | 50 kg | USA |
Carpenter Technology | Cobalt-Chromium (Co-Cr) | $60 – $80 | 100 kg | USA |
ATI Metals | Titanium Powder (Ti6Al4V) | $150 – $200 | 20 kg | USA |
Vale | Nickel Powder (Ni) | $25 – $40 | 150 kg | Canada |
Rima Group | Magnesium Powder (Mg) | $12 – $18 | 500 kg | Brazil |
Zochem | Zinc Powder (Zn) | $10 – $15 | 250 kg | Canada |
Pros and Cons of Sinter Equipment Industry
When evaluating the sintering process and equipment, it’s essential to consider the advantages and limitations. Here’s a comparison that highlights the key points.
Aspect | Advantages | Limitations |
---|---|---|
Cost | Lower production costs for high volumes | High initial setup cost for equipment |
Material Efficiency | Minimal waste, high material utilization | Limited to specific material types |
Product Quality | High precision, consistent quality | Potential for porosity, which may affect strength |
Design Flexibility | Complex shapes achievable | Limited post-processing options |
Environmental Impact | Lower energy consumption compared to melting | Requires specific environmental controls |
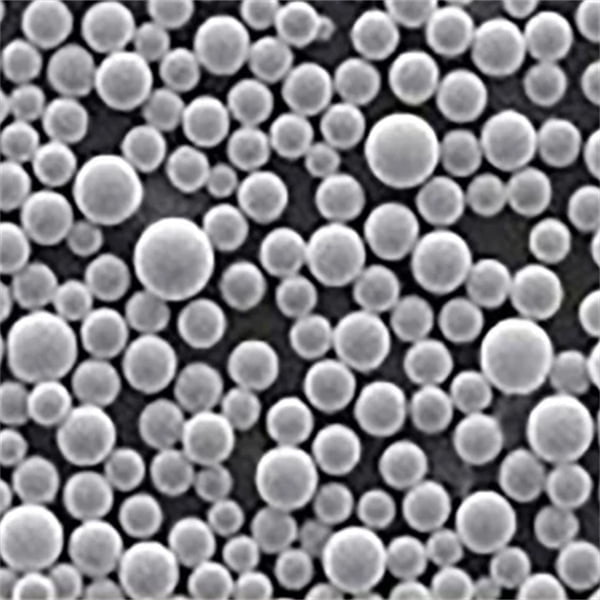
FAQ
Q: What is the sintering process?
A: Sintering is a manufacturing process where powdered materials are heated below their melting point to bond particles together into a solid mass. It’s commonly used in the production of metal parts with complex shapes and high strength.
Q: Which industries use sintered products?
A: Sintered products are used across various industries, including automotive, aerospace, medical, electronics, tooling, and more. Each industry values sintering for its ability to produce high-quality, precision components efficiently.
Q: What are the main advantages of sintering?
A: The main advantages of sintering include cost-effective production, material versatility, energy efficiency, high precision, and environmental benefits. It’s particularly favored for its ability to create complex geometries with minimal waste.
Q: Are there any limitations to the sintering process?
A: Yes, sintering has some limitations, such as high initial setup costs for equipment, potential porosity in the final product, and restrictions on the types of materials that can be used.
Q: How does the sintering process compare to traditional manufacturing methods?
A: Compared to traditional methods like casting or machining, sintering offers better material efficiency, lower production costs for high volumes, and the ability to produce complex shapes with high precision. However, it may require more specialized equipment and can have limitations in material choices.
Q: Can sintering be used with all types of metals?
A: Sintering is most effective with metals that have good powder characteristics, such as iron, copper, aluminum, tungsten carbide, and titanium alloys. However, not all metals are suitable for sintering due to their specific thermal and chemical properties.
Conclusion
The sinter equipment industry is a dynamic and essential part of modern manufacturing, providing the tools and processes needed to create high-quality, precision components. From automotive to aerospace, the versatility, efficiency, and precision of sintering make it a go-to method for producing complex parts with specific material properties.
Whether you’re a manufacturer looking to optimize production or a buyer searching for the best sintered products, understanding the sinter equipment industry is crucial. With its diverse applications, advanced technology, and sustainable practices, this industry is set to continue playing a vital role in the future of manufacturing.
About 3DP mETAL
Product Category
CONTACT US
Any questions? Send us a message now! After receiving your message, we will process your request with a whole team.