Sinter-hardening alloy powder is a groundbreaking material in the realm of metallurgy and manufacturing. It offers unique properties that enhance the strength, durability, and performance of metal parts. In this comprehensive guide, we’ll delve into everything you need to know about sinter-hardening alloy powder, from its composition and characteristics to its applications and advantages.
Overview of Sinter-Hardening Alloy Powder
Sinter-hardening alloy powder is used primarily in powder metallurgy to produce high-strength components. The sintering process involves compacting and heating metal powders below their melting point to form a solid mass. The addition of alloying elements allows these powders to harden during cooling, eliminating the need for secondary heat treatment.
Key Details
- Composition: Varies with the type of alloy, but common elements include iron, nickel, copper, molybdenum, and carbon.
- Properties: High strength, wear resistance, and dimensional stability.
- Applications: Automotive parts, machinery components, gears, and bearings.
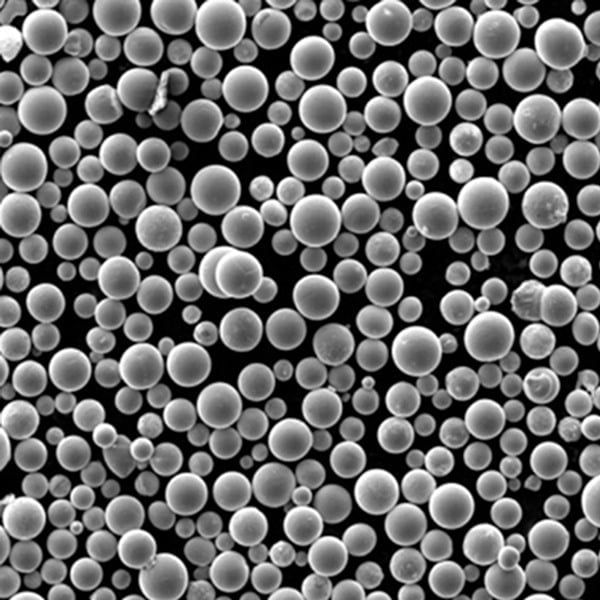
Types and Composition of Sinter-Hardening Alloy Powder
Different types of sinter-hardening alloy powders have distinct compositions, which influence their properties and applications. Here, we list some specific models and their characteristics.
Model | Composition | Properties | Applications |
---|---|---|---|
SH-100 | Iron, 4% Nickel, 2% Copper, 1% Molybdenum | High tensile strength, moderate hardness | Automotive gears, cams |
SH-200 | Iron, 2% Nickel, 1.5% Copper, 1% Carbon | Excellent wear resistance, high hardness | Bearing components, pump gears |
SH-300 | Iron, 1% Molybdenum, 0.8% Carbon | High impact strength, good machinability | Structural parts, machine fittings |
SH-400 | Iron, 1.5% Copper, 1% Carbon | Superior dimensional stability, high strength | Precision gears, sprockets |
SH-500 | Iron, 2% Nickel, 1% Copper, 1.2% Carbon | High hardness, excellent fatigue resistance | Engine parts, heavy-duty machinery |
SH-600 | Iron, 0.5% Molybdenum, 0.8% Carbon | Good ductility, high strength | Mechanical seals, valve seats |
SH-700 | Iron, 1% Nickel, 1.5% Copper | Moderate hardness, good wear resistance | Gearboxes, differential gears |
SH-800 | Iron, 3% Nickel, 1% Copper, 0.8% Carbon | Very high tensile strength, good ductility | Crankshafts, connecting rods |
SH-900 | Iron, 0.8% Molybdenum, 1% Carbon | Excellent toughness, high wear resistance | Cutting tools, wear plates |
SH-1000 | Iron, 1% Nickel, 1% Copper, 1% Carbon | Balanced hardness and strength | Automotive parts, industrial gears |
Characteristics of Sinter-Hardening Alloy Powder
Physical Properties
Sinter-hardening alloy powders are renowned for their high strength and hardness, which are achieved through the alloying process and the subsequent sintering. They exhibit excellent wear resistance and maintain dimensional stability under stress, making them ideal for high-precision applications.
Mechanical Properties
These powders offer superior mechanical properties, such as tensile strength, impact resistance, and fatigue resistance. The alloying elements like nickel, copper, and molybdenum enhance these properties by forming hard phases within the metal matrix.
Thermal Properties
The thermal stability of sinter-hardening alloy powders allows them to maintain their mechanical properties at elevated temperatures. This makes them suitable for use in engine components and other high-temperature applications.
Chemical Properties
The alloy powders are resistant to oxidation and corrosion due to the presence of elements like nickel and molybdenum. This enhances their longevity and reliability in harsh environments.
Applications of Sinter-Hardening Alloy Powder
Sinter-hardening alloy powders find applications across various industries due to their versatile properties. Here are some common uses:
Application | Description |
---|---|
Automotive Industry | Used in gears, cams, crankshafts, and engine components due to high strength and wear resistance. |
Machinery Components | Ideal for producing bearings, bushings, and structural parts that require durability and precision. |
Aerospace Industry | Utilized in components that need to withstand high stress and thermal conditions. |
Industrial Equipment | Employed in heavy-duty machinery parts, such as gears and sprockets, for enhanced performance. |
Tooling | Suitable for cutting tools and wear plates, thanks to their toughness and wear resistance. |
Energy Sector | Used in mechanical seals and valve seats, where high strength and corrosion resistance are crucial. |
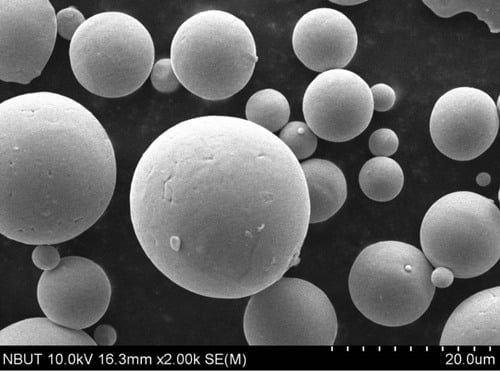
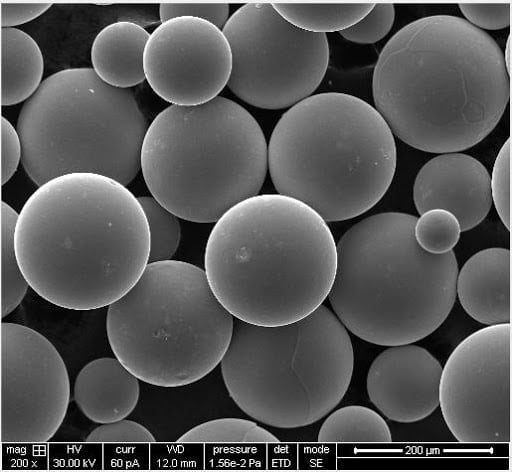
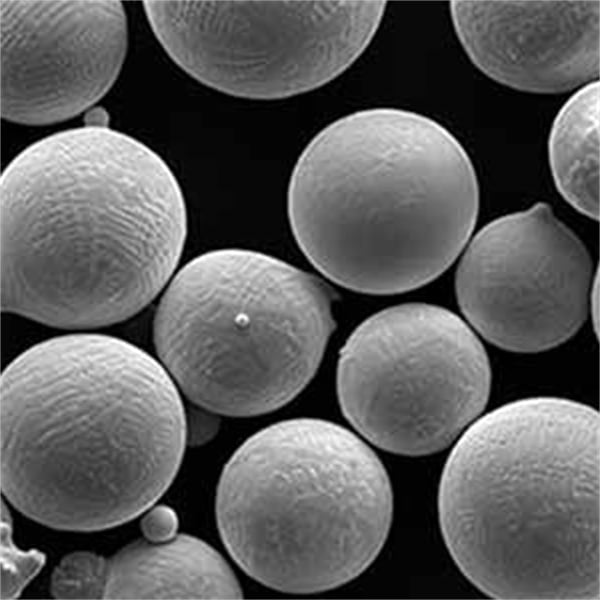
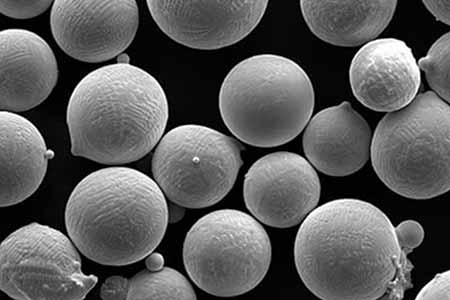
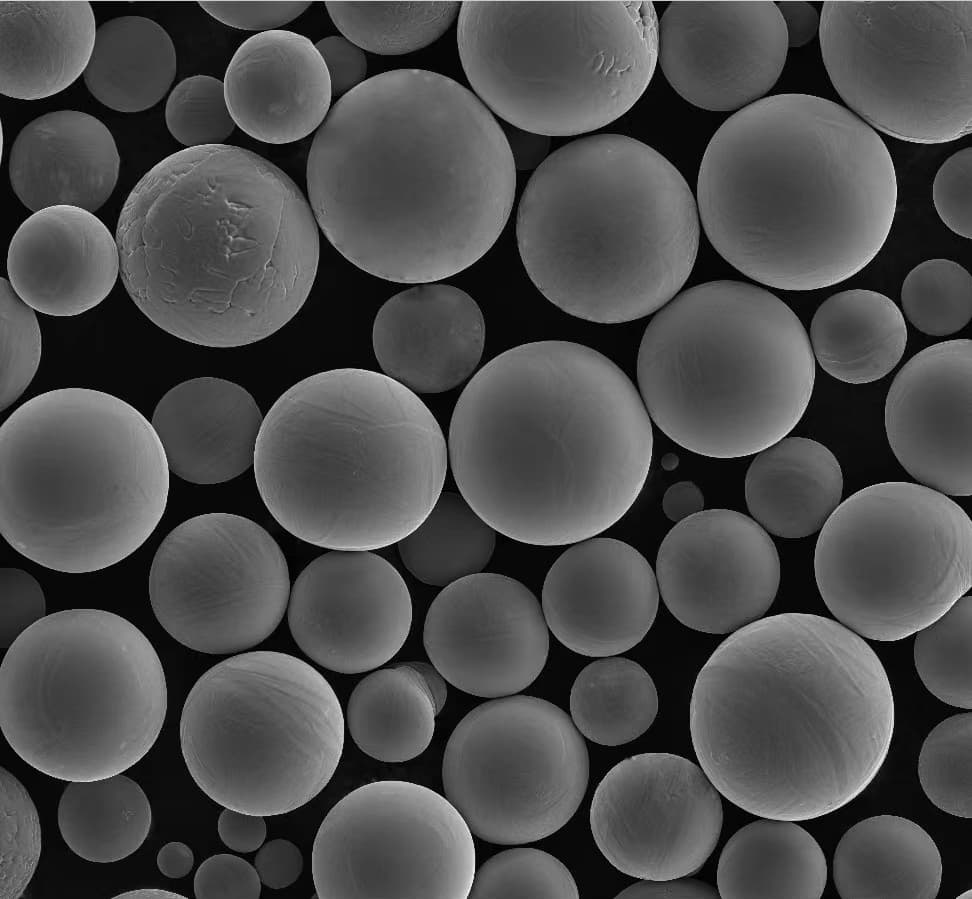
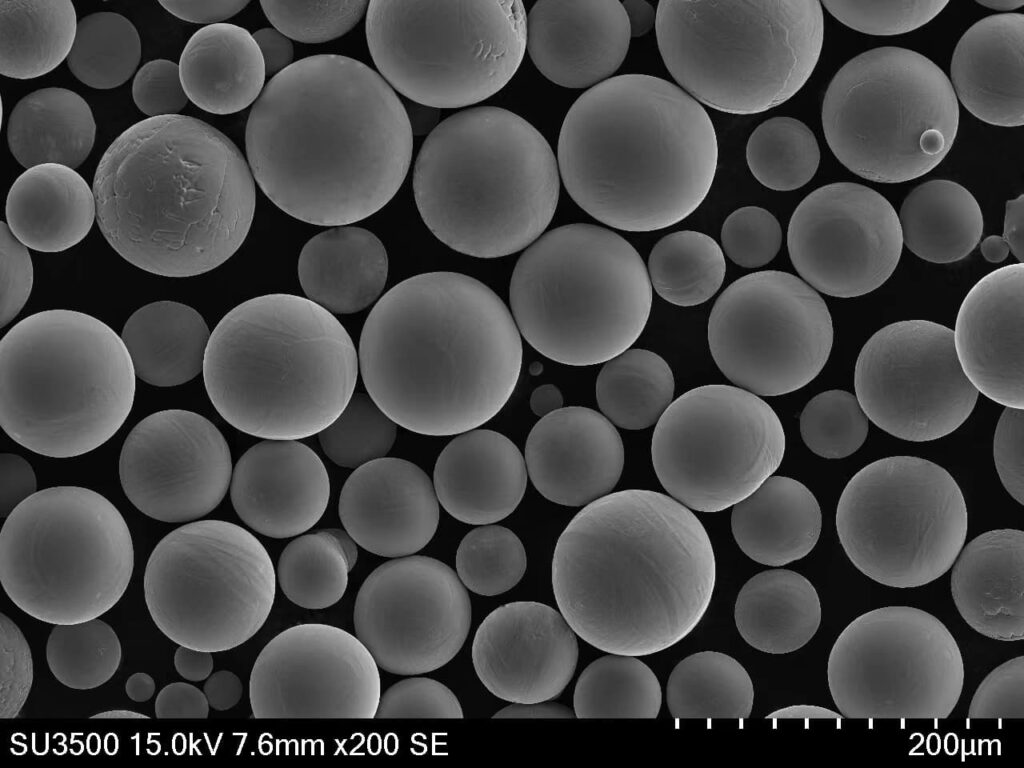
Specifications, Sizes, Grades, and Standards
Different sinter-hardening alloy powders come with various specifications to suit specific applications. Here’s a detailed look at the typical specifications:
Specification | Details |
---|---|
Particle Size | Ranges from 10 to 100 micrometers, depending on the application. |
Density | Typically between 6.8 to 7.4 g/cm³ after sintering. |
Grade | Defined by the alloy composition and intended use (e.g., SH-100, SH-200). |
Standards | Comply with international standards such as ASTM B783, MPIF 35. |
Suppliers and Pricing Details
Pricing for sinter-hardening alloy powders varies based on composition, quantity, and supplier. Here are some key suppliers and their pricing details:
Supplier | Model | Price per kg | Minimum Order Quantity |
---|---|---|---|
Supplier A | SH-100 | $15 | 100 kg |
Supplier B | SH-200 | $20 | 50 kg |
Supplier C | SH-300 | $18 | 75 kg |
Supplier D | SH-400 | $22 | 100 kg |
Supplier E | SH-500 | $25 | 50 kg |
Supplier F | SH-600 | $19 | 80 kg |
Supplier G | SH-700 | $21 | 100 kg |
Supplier H | SH-800 | $23 | 50 kg |
Supplier I | SH-900 | $24 | 60 kg |
Supplier J | SH-1000 | $26 | 100 kg |
Advantages and Limitations of Sinter-Hardening Alloy Powder
Advantages
- High Strength and Hardness: Achieved through alloying and sintering processes, providing durable and reliable components.
- Wear Resistance: Excellent for applications requiring high durability.
- Dimensional Stability: Maintains shape and size under stress, ideal for precision parts.
- Thermal Stability: Suitable for high-temperature applications.
- Corrosion Resistance: Longevity in harsh environments due to alloying elements.
Limitations
- Cost: Higher compared to traditional metal powders due to complex alloying and sintering processes.
- Processing Complexity: Requires precise control during manufacturing to achieve desired properties.
- Limited Suppliers: Fewer manufacturers produce these specialized powders, impacting availability and lead times.
Comparison of Sinter-Hardening Alloy Powder Models
Let’s compare different models of sinter-hardening alloy powders to help you choose the right one for your application.
Model | Strength | Hardness | Wear Resistance | Thermal Stability | Applications |
---|---|---|---|---|---|
SH-100 | High | Moderate | Good | Good | Automotive gears, cams |
SH-200 | Moderate | High | Excellent | Moderate | Bearing components, pump gears |
SH-300 | High | Moderate | Good | Excellent | Structural parts, fittings |
SH-400 | High | High | Good | Moderate | Precision gears, sprockets |
SH-500 | Very High | High | Excellent | High | Engine parts, machinery |
SH-600 | Moderate | High | Good | Excellent | Mechanical seals, valve seats |
SH-700 | High | Moderate | Good | Good | Gearboxes, differential gears |
SH-800 | Very High | High | Excellent | High | Crankshafts, connecting rods |
SH-900 | High | High | Excellent | Moderate | Cutting tools, wear plates |
SH-1000 | High | High | Good | High | Automotive parts, gears |
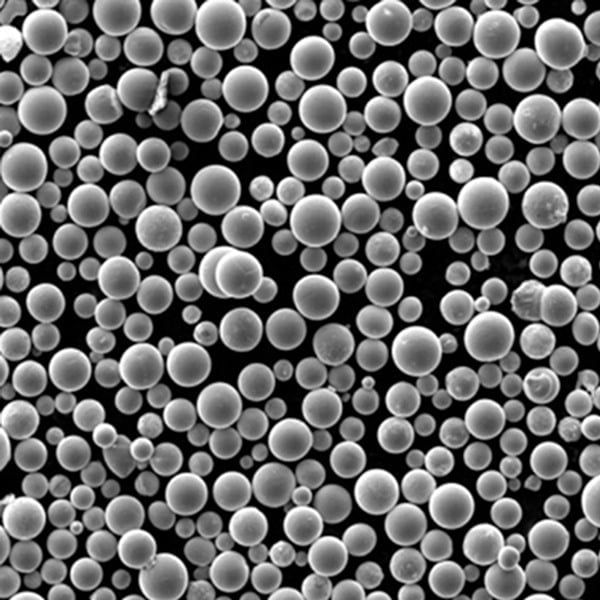
FAQ
Question | Answer |
---|---|
What is sinter-hardening alloy powder? | It is a type of metal powder that hardens during the sintering process, eliminating the need for secondary heat treatment. |
What are the main benefits of using sinter-hardening alloy powder? | High strength, wear resistance, and dimensional stability, making it ideal for high-performance applications. |
How does the composition affect the properties of the powder? | Different alloying elements like nickel, copper, and molybdenum enhance various properties such as strength, hardness, and corrosion resistance. |
What are common applications of sinter-hardening alloy powders? | Automotive parts, machinery components, gears, bearings, and high-temperature applications. |
Are there any limitations to using sinter-hardening alloy powders? | Higher cost and processing complexity compared to traditional metal powders, along with limited suppliers. |
How do I choose the right sinter-hardening alloy powder for my application? | Consider the specific properties required for your application, such as strength, hardness, and thermal stability, and compare different models accordingly. |
Conclusion
Sinter-hardening alloy powder represents a significant advancement in materials science, offering superior mechanical properties and performance. Whether you’re in the automotive industry, machinery manufacturing, or any other field that demands high-strength, wear-resistant components, understanding the various types, compositions, and applications of these powders is crucial. This guide provides a comprehensive overview, helping you make informed decisions for your specific needs. With the right choice of sinter-hardening alloy powder, you can enhance the quality and durability of your products, ensuring they meet the highest standards of performance and reliability.
About 3DP mETAL
Product Category
CONTACT US
Any questions? Send us a message now! After receiving your message, we will process your request with a whole team.