Overview of Specialty Metal Powders
Specialty metal powders are integral in a variety of high-tech industries, including aerospace, automotive, medical, and electronics. These finely divided metals have unique properties that make them suitable for applications requiring high precision, strength, and durability. In this comprehensive guide, we will explore the intricacies of specialty metal powders, their types, compositions, properties, applications, and much more.
What Are Specialty Metal Powders?
Specialty metal powders are finely ground metal particles used in numerous industrial processes. These powders are produced through various methods such as atomization, reduction, electrolysis, and mechanical comminution. The resultant powders possess unique characteristics such as specific particle sizes, shapes, and surface areas, which are tailored for specific applications.
Importance of Specialty Metal Powders
These powders play a crucial role in manufacturing advanced materials and components. Their importance lies in their ability to:
- Enhance material properties like strength, conductivity, and corrosion resistance.
- Enable the production of complex geometries and fine features.
- Improve manufacturing efficiency and material utilization.
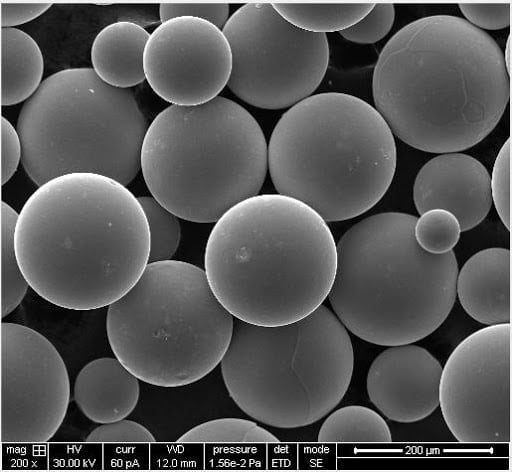
Types of Specialty Metal Powders
Common Specialty Metal Powders
There are numerous specialty metal powders, each with its unique properties and applications. Here’s a detailed look at some of the most commonly used types:
Metal Powder | Composition | Properties | Applications |
---|---|---|---|
Aluminum (Al) | Pure Al or Al alloys | Lightweight, high conductivity | Automotive, aerospace, 3D printing |
Titanium (Ti) | Pure Ti or Ti alloys | High strength-to-weight ratio, biocompatible | Medical implants, aerospace, sports equipment |
Copper (Cu) | Pure Cu or Cu alloys | Excellent electrical and thermal conductivity | Electrical components, heat sinks, electronics |
Nickel (Ni) | Pure Ni or Ni alloys | Corrosion resistance, high melting point | Batteries, aerospace, chemical processing |
Stainless Steel | Fe-Cr alloys | Corrosion resistance, strength | Medical devices, automotive, construction |
Cobalt (Co) | Pure Co or Co alloys | Magnetic properties, wear resistance | Hard metals, magnetic materials, dental alloys |
Tungsten (W) | Pure W or W alloys | High density, high melting point | Electronics, aerospace, medical devices |
Iron (Fe) | Pure Fe or Fe alloys | Abundant, versatile, magnetic properties | Automotive, construction, electronics |
Zinc (Zn) | Pure Zn or Zn alloys | Corrosion resistance, low melting point | Galvanizing, batteries, die-casting |
Molybdenum (Mo) | Pure Mo or Mo alloys | High melting point, strength at high temperatures | Aerospace, electronics, high-temperature applications |
Properties and Characteristics of Specialty Metal Powders
Understanding the properties of specialty metal powders is crucial for selecting the right material for specific applications. Here are some key properties and characteristics to consider:
Property | Description |
---|---|
Particle Size | Determines the powder’s flowability, packing density, and surface area. |
Shape | Influences the powder’s behavior during processing and the final product’s properties. |
Surface Area | Affects reactivity, sintering behavior, and coating characteristics. |
Purity | Higher purity usually means better performance in critical applications. |
Density | Impacts the weight and strength of the final product. |
Melting Point | Determines the powder’s suitability for high-temperature applications. |
Electrical Conductivity | Important for electronic and electrical applications. |
Thermal Conductivity | Crucial for heat management in various applications. |
Magnetic Properties | Relevant for applications in electronics and magnetic devices. |
Applications of Specialty Metal Powders
Specialty metal powders find applications across a wide range of industries. Here’s a detailed look at some of the primary uses:
Industry | Applications |
---|---|
Aerospace | Turbine blades, structural components, fuel systems |
Automotive | Engine components, brake systems, lightweight structural parts |
Medical | Implants, surgical instruments, dental devices |
Electronics | Conductive inks, heat sinks, magnetic materials |
Construction | Structural reinforcements, corrosion-resistant coatings |
Energy | Batteries, fuel cells, solar panels |
3D Printing | Prototyping, complex geometries, custom components |
Chemical Processing | Catalysts, filters, reaction vessels |
Consumer Goods | High-performance sports equipment, jewelry, electronic gadgets |
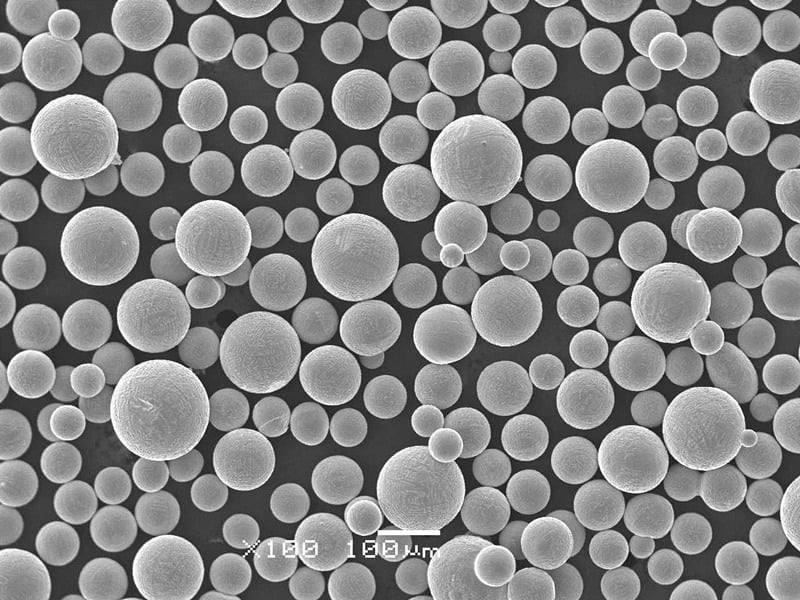
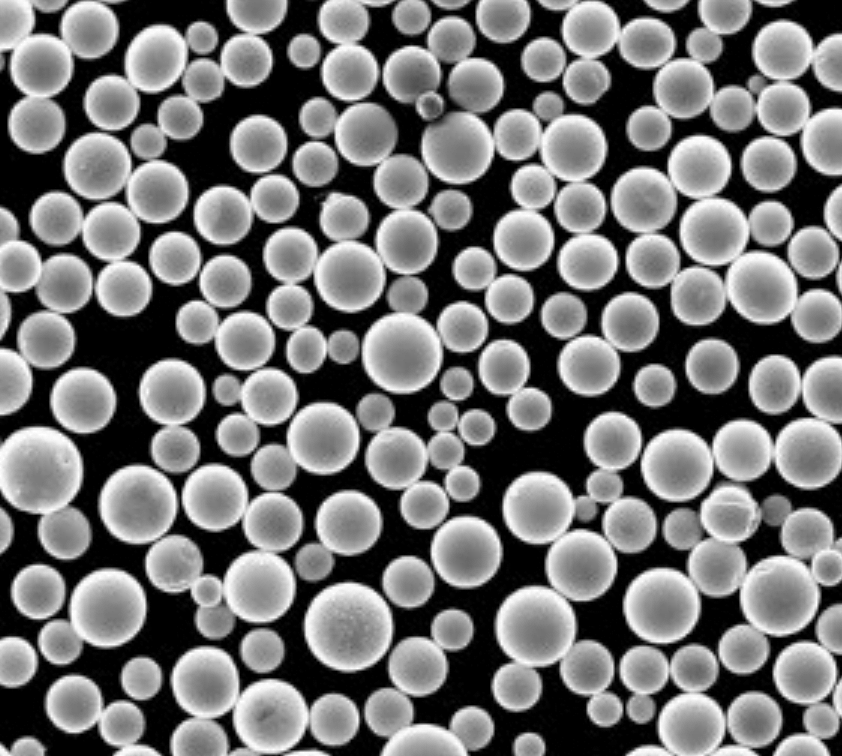
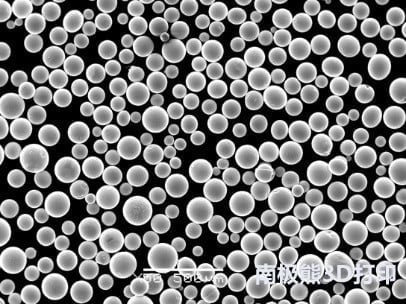
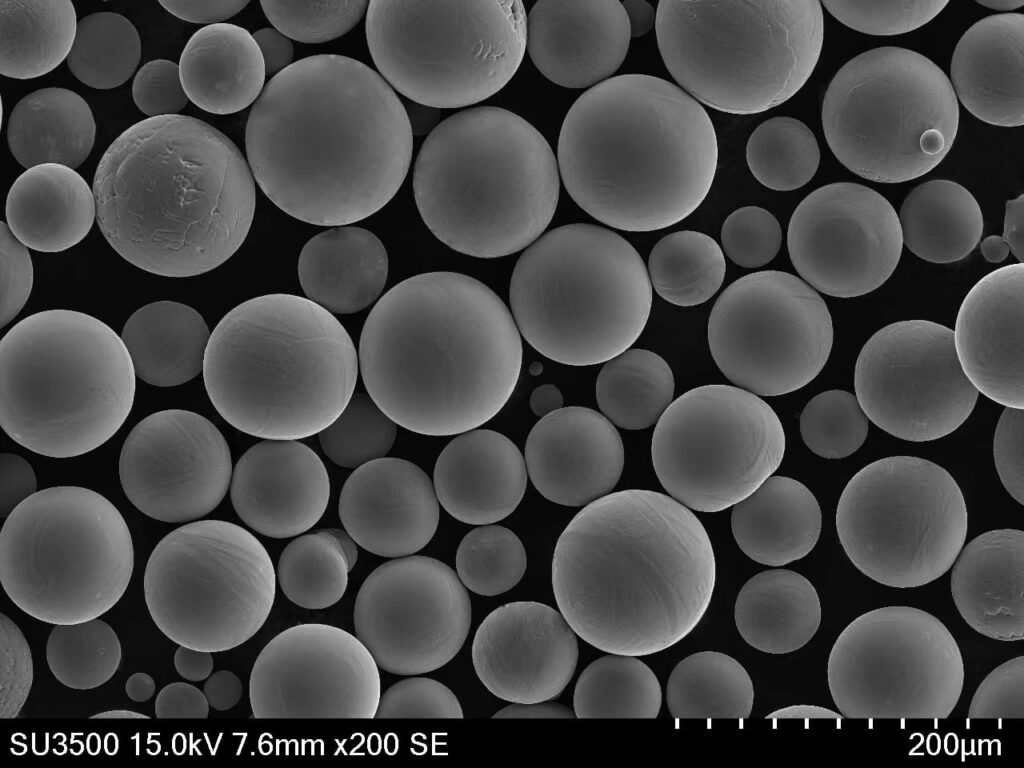
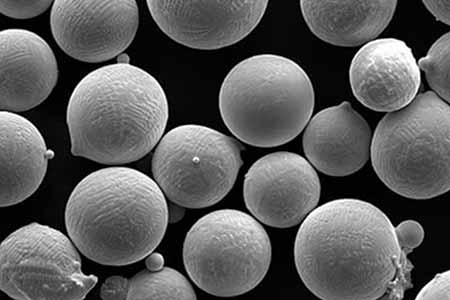
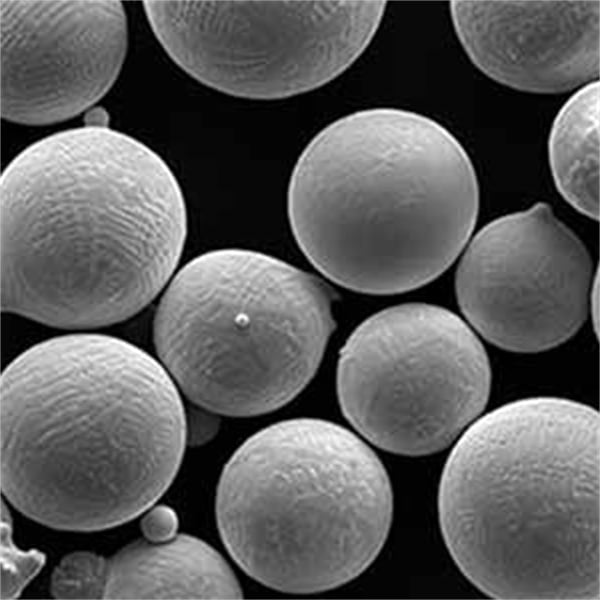
Specifications, Sizes, Grades, and Standards
When selecting specialty metal powders, it’s essential to consider the specific grades, sizes, and standards required for your application. Here are some examples:
Metal Powder | Grades | Particle Sizes | Standards |
---|---|---|---|
Aluminum (Al) | 1100, 2024, 6061, 7075 | 10-100 microns | ASTM B-85, ISO 209-1 |
Titanium (Ti) | Grade 1-5, 7, 9, 23 | 15-45 microns, 45-105 microns | ASTM F67, ASTM F136 |
Copper (Cu) | C11000, C10100, C10200 | 10-50 microns | ASTM B-170, JIS H3250 |
Nickel (Ni) | Ni 200, Ni 201, Ni 205 | 20-80 microns | ASTM B-330, ISO 4289 |
Stainless Steel | 304, 316, 410, 420 | 15-150 microns | ASTM A-276, ISO 683/13 |
Cobalt (Co) | F75, F90, F105 | 20-60 microns | ASTM F-1537, ISO 5832-4 |
Tungsten (W) | W1, W2, W4 | 5-45 microns | ASTM B-777, ISO 4186 |
Iron (Fe) | Fe2, Fe3 | 20-200 microns | ASTM E-108, ISO 683/10 |
Zinc (Zn) | Zamak 2, Zamak 3 | 10-60 microns | ASTM B-240, ISO 301 |
Molybdenum (Mo) | Mo 1, Mo 2, TZM | 5-45 microns | ASTM B-386, ISO 4289 |
Suppliers and Pricing Details
Choosing the right supplier is crucial for obtaining high-quality specialty metal powders. Here are some notable suppliers and an overview of their pricing:
Supplier | Metal Powders Offered | Pricing (per kg) | Additional Services |
---|---|---|---|
Höganäs AB | Iron, Stainless Steel, Copper, Nickel | $50 – $200 | Custom powder development, technical support |
Sandvik | Titanium, Stainless Steel, Nickel-based alloys | $150 – $600 | R&D collaboration, application support |
GKN Powder Metallurgy | Iron, Stainless Steel, Aluminum, Copper | $40 – $180 | Design and prototyping, testing services |
LPW Technology | Titanium, Aluminum, Nickel, Cobalt | $200 – $800 | Powder lifecycle management, recycling |
Carpenter Technology | Titanium, Stainless Steel, Nickel | $250 – $900 | Custom alloy development, supply chain management |
ATI Metals | Nickel, Titanium, Cobalt, Stainless Steel | $100 – $700 | Powder production optimization, analytical services |
Arcam EBM | Titanium, Cobalt-Chrome | $300 – $1000 | Electron beam melting technology, design services |
Praxair Surface Technologies | Aluminum, Nickel, Cobalt | $80 – $500 | Coating solutions, thermal spray powders |
PyroGenesis | Titanium, Aluminum, Stainless Steel | $220 – $850 | Plasma atomization, additive manufacturing powders |
Tekna Plasma Systems | Titanium, Aluminum, Nickel, Copper | $150 – $700 | Spheroidization services, powder analysis |
Comparing Advantages and Limitations of Specialty Metal Powders
Each type of metal powder has its pros and cons. Let’s compare them:
Metal Powder | Advantages | Limitations |
---|---|---|
Aluminum | Lightweight, high conductivity, corrosion resistance | Lower strength compared to other metals |
Titanium | High strength-to-weight ratio, corrosion resistance, biocompatible | High cost, challenging to process |
Copper | Excellent electrical and thermal conductivity | High density, can oxidize |
Nickel | Corrosion resistance, high melting point | Expensive, can cause allergic reactions |
Stainless Steel | Corrosion resistance, strength, durability | Heavier than aluminum and titanium |
Cobalt | Wear resistance, magnetic properties | Expensive, limited availability |
Tungsten | High density, high melting point | Brittle, challenging to work with |
Iron | Abundant, versatile, magnetic properties | Corrosion-prone, lower conductivity |
Zinc | Corrosion resistance, low melting point | Lower strength, can be brittle |
Molybdenum | High melting point, strength at high temperatures | Expensive, difficult to process |
Application-Specific Insights
Aerospace Industry
In aerospace, the need for materials that offer high strength-to-weight ratios and excellent fatigue resistance is paramount. Specialty metal powders such as titanium and nickel-based alloys are ideal for manufacturing turbine blades, structural components, and fuel systems. Their ability to withstand extreme temperatures and corrosive environments makes them indispensable in this sector.
Automotive Industry
The automotive industry utilizes specialty metal powders to create lighter and stronger components, improving fuel efficiency and performance. Aluminum and stainless steel powders are commonly used for engine parts, brake systems, and lightweight structural components. The use of these powders allows for intricate designs and complex geometries that are difficult to achieve with traditional manufacturing methods.
Medical Industry
Medical applications demand materials that are biocompatible and resistant to wear and corrosion. Titanium and cobalt-chrome powders are frequently used to produce implants, surgical instruments, and dental devices. These materials not only meet the stringent regulatory standards but also provide the necessary strength and durability required for medical applications.
Electronics Industry
In electronics, the demand for materials with high electrical and thermal conductivity is critical. Copper and silver powders are widely used in the production of conductive inks, heat sinks, and magnetic materials. These powders enable the miniaturization of electronic components while ensuring efficient heat dissipation and electrical performance.
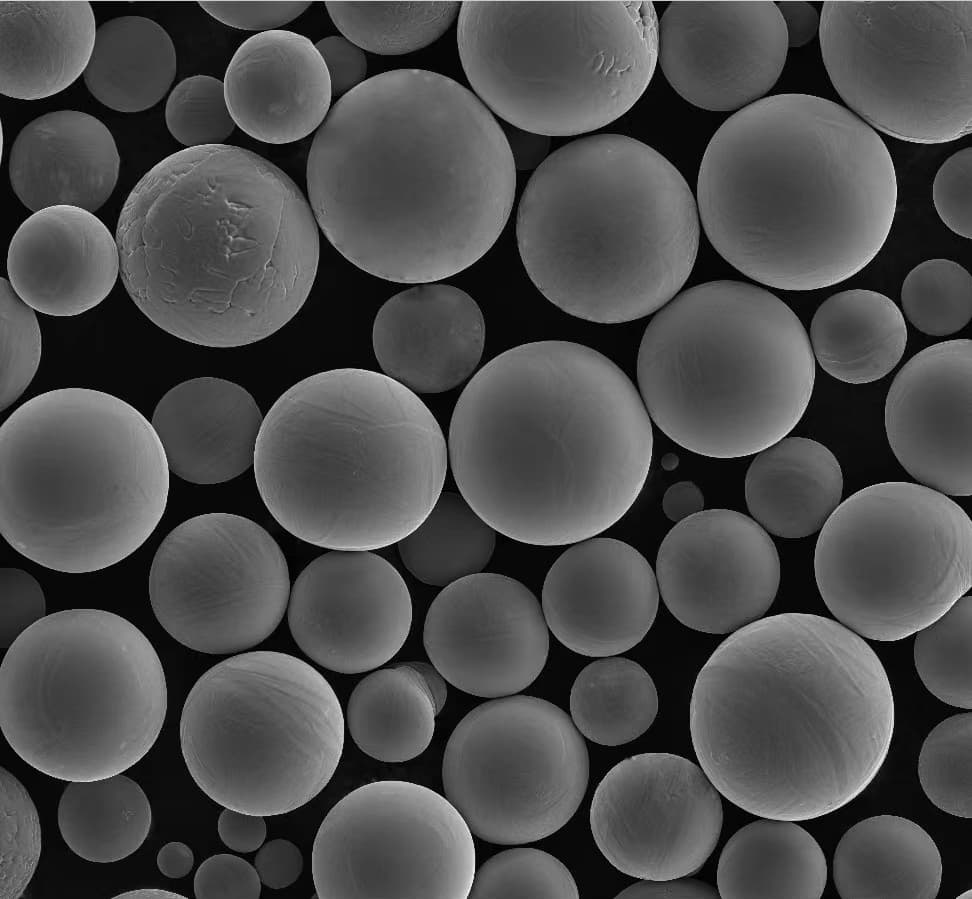
FAQ
What are the key benefits of using specialty metal powders in manufacturing?
Specialty metal powders offer several benefits, including the ability to create complex geometries, improve material properties (such as strength and conductivity), and enhance manufacturing efficiency by reducing waste and enabling precise material utilization.
How are specialty metal powders produced?
Specialty metal powders are produced through various methods, including atomization (gas or water), reduction, electrolysis, and mechanical comminution. Each method offers different advantages in terms of particle size, shape, and purity.
What factors should be considered when selecting a specialty metal powder?
When selecting a specialty metal powder, consider factors such as particle size, shape, surface area, purity, density, melting point, and specific properties like electrical and thermal conductivity or magnetic characteristics.
What are the common applications of titanium powder?
Titanium powder is commonly used in aerospace for turbine blades and structural components, in medical applications for implants and surgical instruments, and in sports equipment for its high strength-to-weight ratio and biocompatibility.
Are specialty metal powders expensive?
The cost of specialty metal powders varies depending on the type of metal, purity, particle size, and the production method. Generally, powders such as titanium and cobalt are more expensive due to their properties and production complexity.
Can specialty metal powders be recycled?
Yes, specialty metal powders can be recycled. Many suppliers offer powder lifecycle management services, including recycling and reconditioning to ensure sustainable use and cost efficiency.
How do the properties of metal powders affect their performance in 3D printing?
The properties of metal powders, such as particle size, shape, and purity, significantly affect their performance in 3D printing. These properties influence the powder’s flowability, packing density, and the final product’s mechanical properties and surface finish.
What is the difference between pure metal powders and alloy powders?
Pure metal powders consist of a single metal element, offering properties inherent to that metal. Alloy powders are composed of a mixture of metals, providing enhanced properties such as increased strength, corrosion resistance, or specific electrical or magnetic characteristics.
How do you ensure the quality of specialty metal powders?
Quality is ensured through rigorous testing and adherence to industry standards. This includes analyzing particle size distribution, chemical composition, purity, and physical properties. Reputable suppliers also provide certifications and traceability for their products.
What advancements are being made in the field of specialty metal powders?
Advancements include the development of new alloys with enhanced properties, improved production methods for higher purity and consistency, and innovations in powder recycling and reconditioning techniques. These advancements aim to meet the evolving demands of various high-tech industries.
About 3DP mETAL
Product Category
CONTACT US
Any questions? Send us a message now! After receiving your message, we will process your request with a whole team.