Spherical aluminum powder is a fascinating and versatile material with a wide range of applications, from metallurgy to electronics. In this comprehensive guide, we’ll dive deep into the world of spherical aluminum powder, exploring its properties, uses, types, and much more. Whether you’re an engineer, a manufacturer, or just curious about this remarkable substance, you’ll find everything you need to know right here.
Overview of Spherical Aluminum Powder
Spherical aluminum powder is a finely divided form of aluminum that has been processed to have a spherical shape. This unique shape gives the powder distinct properties that make it ideal for various industrial applications. But what exactly makes spherical aluminum powder so special? Let’s break it down.
Key Properties
- Shape: Spherical
- Composition: Pure aluminum or aluminum alloys
- Particle Size: Typically ranges from 1 to 100 micrometers
- Density: 2.70 g/cm³
- Melting Point: 660.3°C
Why Spherical Shape?
The spherical shape of aluminum powder provides several advantages:
- Flowability: Spherical particles flow more easily compared to irregularly shaped particles, making them ideal for processes like additive manufacturing.
- Packing Density: They have a higher packing density, which is beneficial in applications requiring compact, dense materials.
- Uniformity: Spherical powders ensure uniform distribution in mixtures, leading to consistent performance in end products.
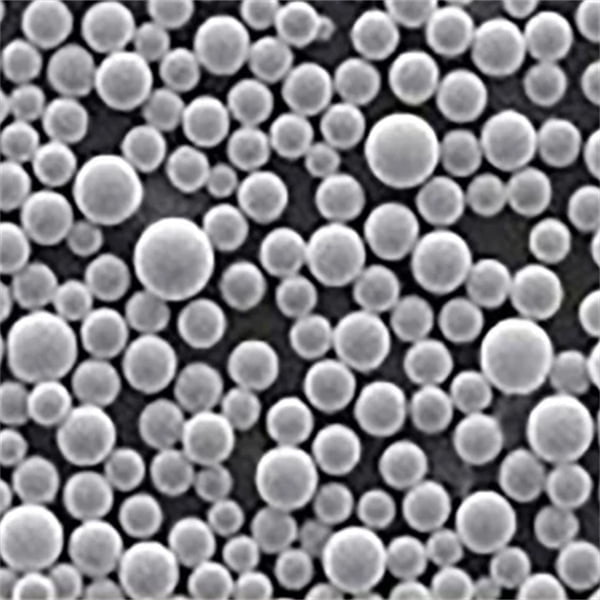
Types of Spherical Aluminum Powder
There are various types of spherical aluminum powder, each tailored for specific applications. Here, we’ll list and describe ten common models.
1. Spherical Aluminum 100
- Description: High-purity aluminum powder with a particle size of 100 micrometers.
- Applications: Used in metallurgy and alloy production.
2. Spherical Aluminum 50
- Description: Medium-sized particles around 50 micrometers.
- Applications: Ideal for additive manufacturing and 3D printing.
3. Spherical Aluminum 20
- Description: Fine powder with a particle size of 20 micrometers.
- Applications: Used in electronic components and conductive inks.
4. Spherical Aluminum 10
- Description: Ultra-fine powder with a particle size of 10 micrometers.
- Applications: Suitable for high-performance coatings and paints.
5. Alloyed Spherical Aluminum 7075
- Description: An alloyed powder containing zinc, magnesium, and copper.
- Applications: Aerospace and automotive industries for lightweight components.
6. Spherical Aluminum 5N
- Description: High-purity (99.999%) aluminum powder.
- Applications: Research and development, specialized electronic applications.
7. Spherical Aluminum 6061
- Description: An aluminum-magnesium-silicon alloy powder.
- Applications: Structural components in various industries.
8. Spherical Aluminum Nitride Coated
- Description: Aluminum powder coated with aluminum nitride.
- Applications: Enhanced thermal conductivity for electronic applications.
9. Spherical Aluminum Hydroxide
- Description: Powder with a hydroxide coating.
- Applications: Fire retardant materials and fillers.
10. Spherical Aluminum Silicon
- Description: Aluminum powder with silicon alloy.
- Applications: Improved castability for manufacturing complex shapes.
Properties and Characteristics of Spherical Aluminum Powder
To fully understand the potential of spherical aluminum powder, it’s important to delve into its properties and characteristics. Below is a detailed breakdown of its composition, properties, and other key features.
Type | Composition | Properties | Characteristics |
---|---|---|---|
Spherical Aluminum 100 | Pure aluminum | High flowability, moderate density | Suitable for metallurgy |
Spherical Aluminum 50 | Pure aluminum | Good flowability, higher density | Ideal for 3D printing |
Spherical Aluminum 20 | Pure aluminum | Excellent flowability, high density | Used in electronics |
Spherical Aluminum 10 | Pure aluminum | Superior flowability, very high density | Great for coatings |
Alloyed Spherical Aluminum 7075 | Aluminum-zinc-magnesium-copper | High strength, lightweight | Aerospace components |
Spherical Aluminum 5N | 99.999% pure aluminum | Extremely high purity | Specialized applications |
Spherical Aluminum 6061 | Aluminum-magnesium-silicon | Versatile, strong | Structural uses |
Spherical Aluminum Nitride Coated | Aluminum with nitride coating | Enhanced thermal conductivity | Electronics cooling |
Spherical Aluminum Hydroxide | Aluminum with hydroxide | Fire retardant properties | Safety materials |
Spherical Aluminum Silicon | Aluminum-silicon alloy | Improved castability | Complex manufacturing |
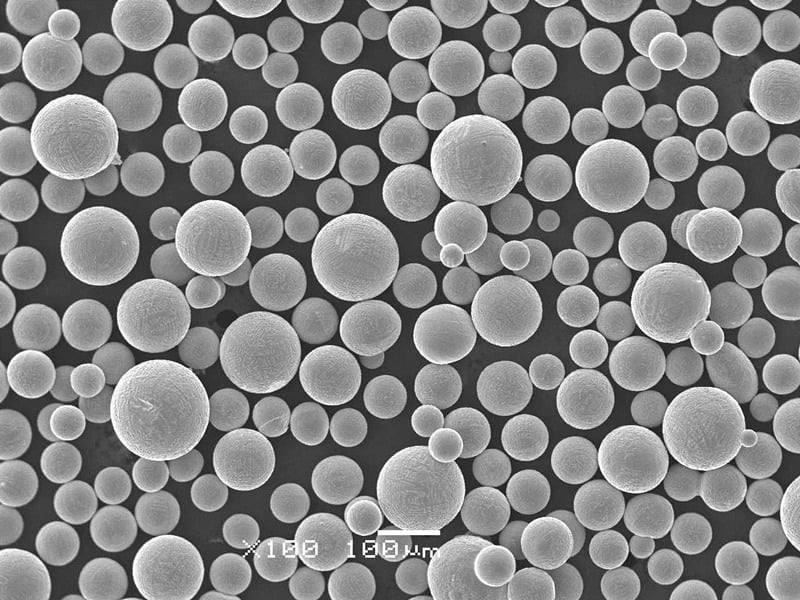
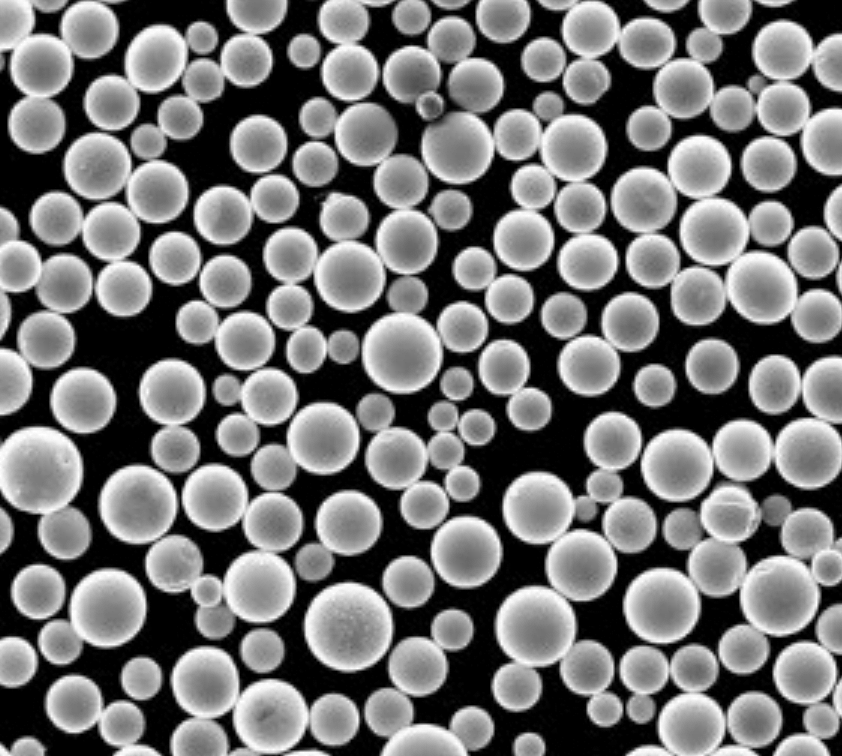
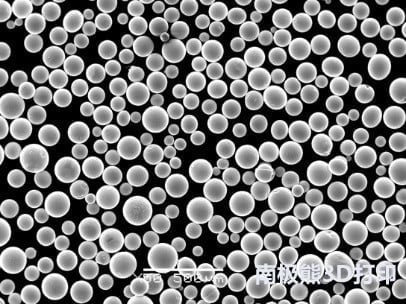
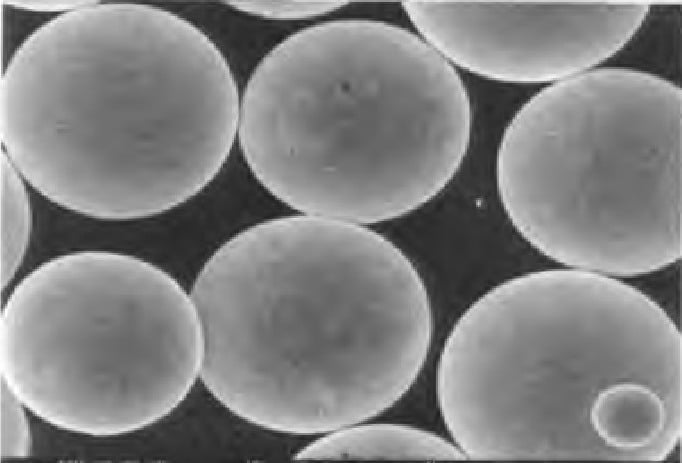
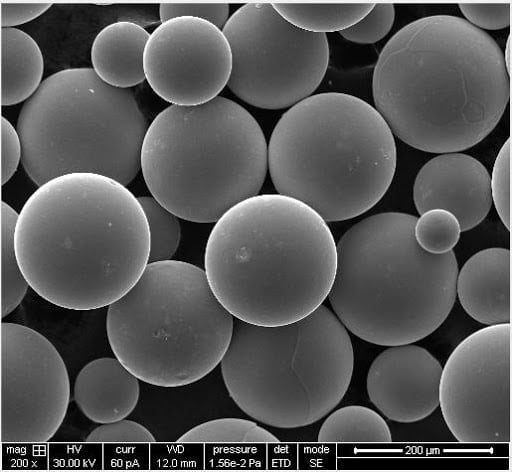
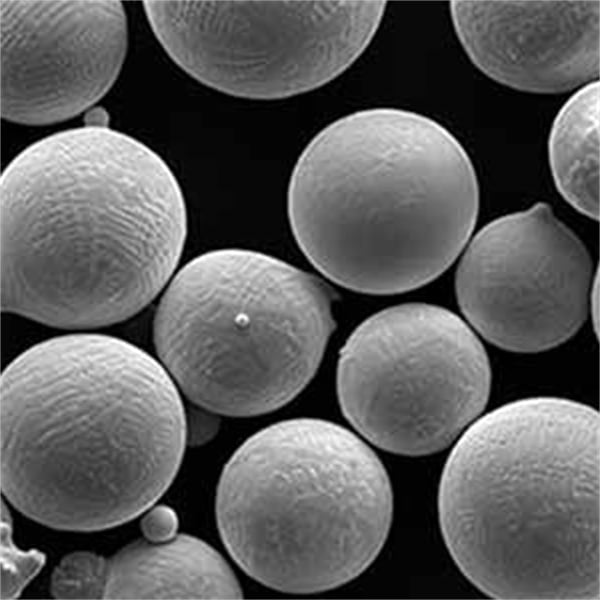
Applications of Spherical Aluminum Powder
The versatility of spherical aluminum powder means it has a wide range of applications. Here’s a detailed look at some of the most common uses.
Application | Description |
---|---|
Additive Manufacturing | Used in 3D printing for producing complex shapes with high precision. |
Metallurgy | Helps in alloy production and enhancing the properties of metals. |
Electronics | Used in conductive inks, thermal pastes, and components. |
Coatings and Paints | Provides high-performance coatings with excellent durability. |
Aerospace | Utilized in lightweight, high-strength components for aircraft. |
Automotive | Essential in producing lightweight and strong automotive parts. |
Research and Development | High-purity powders are used in scientific studies and material development. |
Safety Materials | Used in fire retardant materials to enhance safety. |
Thermal Management | Improved thermal conductivity for cooling electronic devices. |
Casting and Molding | Enhances castability for manufacturing complex shapes in various industries. |
Specifications, Sizes, Grades, and Standards
Understanding the specifications, sizes, grades, and standards is crucial for selecting the right spherical aluminum powder for your needs.
Specification | Details |
---|---|
Particle Size | Ranges from 1 to 100 micrometers. |
Purity Levels | From 99% to 99.999%, depending on the application. |
Grades | Different grades based on alloy content and purity (e.g., 7075, 6061, 5N). |
Standards | Adheres to various industry standards like ASTM, ISO, and AMS. |
Coatings | Available with various coatings like aluminum nitride and aluminum hydroxide for specific uses. |
Packaging | Supplied in different packaging options from small containers to bulk bags. |
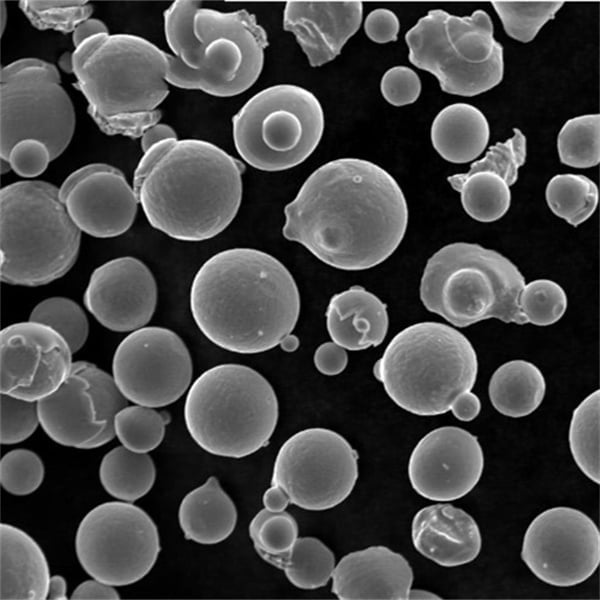
Suppliers and Pricing Details
Here’s a look at some of the major suppliers and typical pricing for spherical aluminum powder.
Supplier | Product Range | Pricing (per kg) |
---|---|---|
Supplier A | Full range of aluminum powders | $50 – $150 |
Supplier B | Specialized in high-purity powders | $200 – $500 |
Supplier C | Alloyed aluminum powders | $100 – $300 |
Supplier D | Customizable particle sizes and coatings | $150 – $400 |
Supplier E | Bulk supplier for industrial applications | $30 – $100 |
Comparing Pros and Cons
It’s important to weigh the advantages and limitations of using spherical aluminum powder.
Aspect | Advantages | Limitations |
---|---|---|
Flowability | Excellent flow properties make it suitable for precision applications. | May require special handling to avoid aggregation. |
Density | High packing density for more efficient material use. | Higher cost compared to irregular powders. |
Uniformity | Ensures consistent performance in end products. | Limited availability for some specialized grades. |
Thermal Conductivity | Enhanced thermal management properties. | Coatings can add to cost and complexity. |
Strength | High-strength alloys available for demanding applications. | Potentially higher costs for high-purity or alloyed versions. |
Versatility | Wide range of applications from electronics to aerospace. | Requires careful selection to match specific application needs. |
Advantages of Spherical Aluminum Powder
Spherical aluminum powder offers numerous benefits across various applications.
1. Improved Flowability
The spherical shape ensures that the powder flows smoothly, making it ideal for processes that require precise material handling, such as additive manufacturing and 3D printing. This flowability also reduces the risk of clogging and ensures consistent performance.
2. Higher Packing Density
Spherical particles pack more densely than irregular particles. This higher packing density is beneficial in applications where space is a premium, such as in electronic components and thermal management systems.
3. Consistent Quality
The uniform shape and size distribution of spherical aluminum powder result in consistent quality in the final product. This consistency is crucial for applications requiring high precision and reliability.
4. Enhanced Thermal Conductivity
Certain coated versions of spherical aluminum powder, like aluminum nitride-coated powders, offer improved thermal conductivity. This property is especially important in electronics, where efficient heat dissipation is critical.
5. Versatility
With various types, sizes, and grades available, spherical aluminum powder can be tailored to suit a wide range of applications. From high-purity powders for research to alloyed powders for industrial manufacturing, there’s a spherical aluminum powder for almost every need.
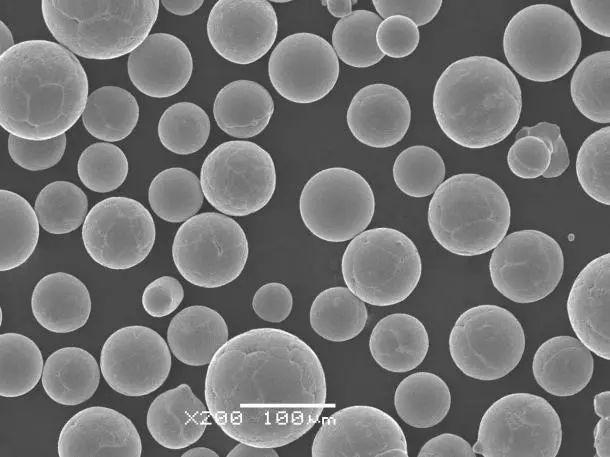
Disadvantages of Spherical Aluminum Powder
Despite its many advantages, spherical aluminum powder also has some drawbacks.
1. Cost
Spherical aluminum powders, particularly high-purity and alloyed versions, can be more expensive than their irregular counterparts. This higher cost can be a limiting factor for some applications, especially those with tight budget constraints.
2. Handling Complexity
While the flowability of spherical powders is generally an advantage, it can also pose challenges. Fine powders, in particular, require careful handling to prevent aggregation and ensure even distribution.
3. Availability
Certain specialized grades and coated versions of spherical aluminum powder may have limited availability. This limitation can lead to longer lead times and higher costs for specific applications.
4. Specific Application Requirements
Not all applications benefit from the properties of spherical aluminum powder. For instance, in some manufacturing processes, the benefits of spherical shape may not justify the additional cost compared to irregular powders.
Technical Comparisons
When choosing between different types of spherical aluminum powders, it’s important to consider their specific properties and how they align with your needs.
Spherical Aluminum 100 vs. Spherical Aluminum 50
- Flowability: Both offer excellent flow properties, but Spherical Aluminum 50 has a higher packing density due to its smaller particle size.
- Applications: Spherical Aluminum 100 is better suited for metallurgy, while Spherical Aluminum 50 excels in 3D printing.
Alloyed Spherical Aluminum 7075 vs. Spherical Aluminum 6061
- Strength: Alloyed Spherical Aluminum 7075 offers higher strength, making it ideal for aerospace applications.
- Versatility: Spherical Aluminum 6061 is more versatile and can be used in a wider range of structural applications.
Spherical Aluminum 5N vs. Spherical Aluminum Nitride Coated
- Purity: Spherical Aluminum 5N has extremely high purity, making it suitable for specialized electronic applications.
- Thermal Conductivity: Spherical Aluminum Nitride Coated offers enhanced thermal conductivity, which is beneficial for thermal management in electronics.
Real-World Applications and Case Studies
To bring the technical details to life, let’s explore some real-world applications and case studies involving spherical aluminum powder.
Additive Manufacturing in Aerospace
A leading aerospace company needed to produce lightweight, high-strength components for a new aircraft model. They chose Alloyed Spherical Aluminum 7075 for its superior strength-to-weight ratio. The powder’s excellent flowability and high packing density allowed for precise 3D printing of complex parts, reducing weight without compromising strength.
Thermal Management in Electronics
A manufacturer of high-performance electronics required a solution for efficient heat dissipation in their devices. They opted for Spherical Aluminum Nitride Coated powder. The enhanced thermal conductivity of the coated powder significantly improved the thermal management of their products, leading to better performance and longevity.
Fire Retardant Materials
A construction materials company aimed to develop fire-retardant panels for buildings. They incorporated Spherical Aluminum Hydroxide powder into their products. The fire retardant properties of the powder helped them create safer building materials that met stringent safety standards.
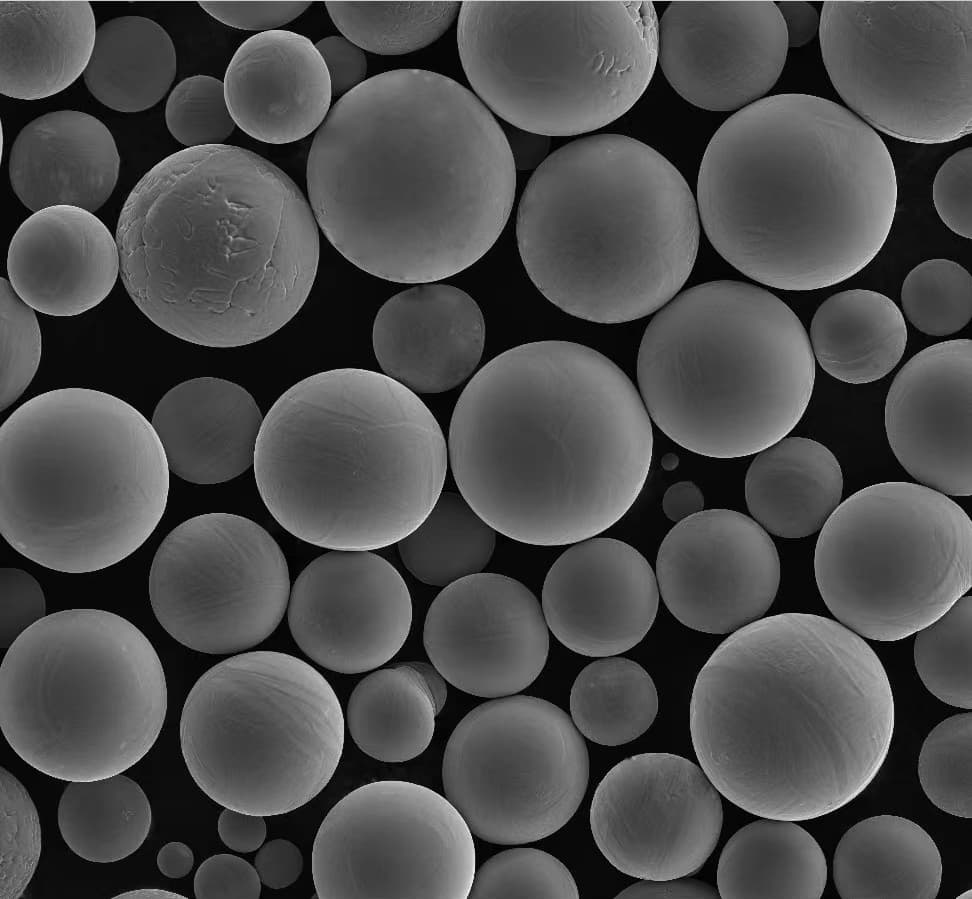
FAQ
Q1: What is spherical aluminum powder used for?
A1: Spherical aluminum powder is used in a variety of applications, including additive manufacturing, metallurgy, electronics, coatings, aerospace, automotive, and more. Its unique properties, such as excellent flowability and high packing density, make it ideal for precision applications.
Q2: How is spherical aluminum powder made?
A2: Spherical aluminum powder is typically produced using atomization processes, where molten aluminum is dispersed into small droplets and solidified into spherical shapes. Various methods, such as gas or plasma atomization, can be used to achieve the desired particle size and shape.
Q3: What are the benefits of using spherical aluminum powder in 3D printing?
A3: The benefits include improved flowability, higher packing density, and uniform particle distribution, which result in better print quality, precision, and material efficiency.
Q4: Are there any safety concerns with handling spherical aluminum powder?
A4: Yes, fine aluminum powders can be hazardous due to their flammability and potential for dust explosions. Proper safety measures, including adequate ventilation, dust collection systems, and personal protective equipment, are essential when handling these materials.
Q5: Can spherical aluminum powder be customized for specific applications?
A5: Absolutely. Spherical aluminum powder can be produced in various sizes, purities, and alloy compositions to meet specific application requirements. Additionally, coatings can be applied to enhance certain properties, such as thermal conductivity.
About 3DP mETAL
Product Category
CONTACT US
Any questions? Send us a message now! After receiving your message, we will process your request with a whole team.