Hot Isostatic Pressing (HIP) is a post-processing technique that utilizes high pressure and temperature to eliminate internal voids and enhance the mechanical properties of manufactured components. Metal powders, like AlSi10(4045) power for HIP, play a crucial role in this process, offering several advantages over conventional fabrication methods. This article delves deep into the world of AlSi10(4045) powder for HIP applications, exploring its properties, benefits, limitations, and various available models.
Tổng quan
AlSi10(4045) power for HIP is a well-established material specifically designed for Hot Isostatic Pressing. It belongs to the Aluminum-Silicon (AlSi) alloy family, recognized for its exceptional castability, weldability, and good mechanical strength. The “10” in AlSi10(4045) denotes the nominal silicon content of 10%, which significantly improves castability and fluidity compared to pure aluminum. The “(4045)” designation refers to the specific Aluminum Association standard that governs the composition and properties of this alloy.
During HIP, AlSi10(4045) powder particles are consolidated under an inert gas atmosphere at elevated temperatures (typically between 400°C and 600°C) and high isotropic pressure (ranging from 70 to 100 MPa). This intense pressure forces the powder particles together, eliminating voids, cracks, and other internal defects that might be present. The elevated temperature facilitates diffusion bonding between the particles, resulting in a near-net-shaped, high-density component with superior mechanical properties.
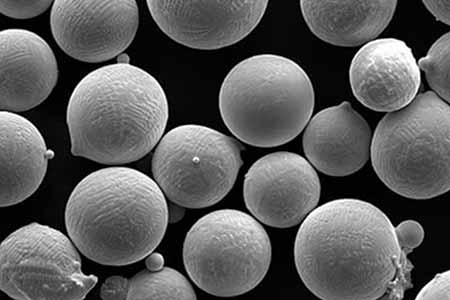
Metal Powder Models for AlSi10(4045) power for HIP
A diverse range of AlSi10(4045) powder models are available from various manufacturers, each catering to specific application requirements. Here’s a closer look at ten prominent models:
- AMpact AM300 (SLM Solutions): This gas-atomized powder boasts excellent flowability and packing density, making it ideal for complex geometries and intricate lattice structures. Its spherical morphology promotes efficient powder spreading in additive manufacturing processes before HIP.
- Höganäs Grafoil AM (Höganäs AB): This water-atomized powder offers a cost-effective solution for HIP applications. Its irregular particle shape enhances mechanical interlocking during compaction, leading to improved strength after HIP.
- APEX ADiM 316L (APEX Powder Company): While not strictly AlSi10(4045), this Aluminum-Silicon-Magnesium alloy powder is worth mentioning due to its similar properties and excellent performance in HIP. The addition of magnesium enhances strength and corrosion resistance compared to standard AlSi10(4045).
- LPW AlSi10Mg (LPW Technology): This gas-atomized powder incorporates magnesium, similar to APEX ADiM 316L. The magnesium content refines the grain structure and improves both strength and ductility after HIP.
- DLP AlSi10Si (DLP Laser GmbH): This silicon-rich variant of AlSi10(4045) offers enhanced wear resistance due to the presence of hard silicon particles. It’s particularly well-suited for components subjected to high wear and tear.
- SLM Solutions AlSi10Mn (SLM Solutions): This manganese-alloyed variant exhibits improved strength and hot cracking resistance compared to standard AlSi10(4045). The manganese addition refines the grain structure and enhances high-temperature performance.
- EOS Aluminium AlSi10Mg (EOS GmbH): Similar to LPW AlSi10Mg and APEX ADiM 316L, this magnesium-containing powder delivers superior strength and corrosion resistance after HIP. It’s a popular choice for applications demanding a combination of these properties.
- Proto Labs AlSi10Mg 2.0 (Proto Labs): This gas-atomized powder boasts exceptional flowability and packing density, making it suitable for intricate geometries in additive manufacturing before HIP. The magnesium content refines the grain structure and enhances mechanical properties.
- Lehmann Voss AlSi10Si (Lehmann Voss GmbH): This silicon-alloyed variant mirrors DLP AlSi10Si, offering improved wear resistance due to the presence of hard silicon particles. It caters to applications requiring high wear resistance alongside the benefits of HIP processing.
- Customizable Alloy Powders: Several manufacturers offer the ability to tailor AlSi10(4045) powder compositions to specific needs. This allows for fine-tuning properties like strength, corrosion resistance, and wear behavior to match the demands of the application.
how to Choosing an AlSi10(4045) power for HIP Model
While the selection above highlights some popular choices, choosing the ideal AlSi10(4045) powder model for your HIP application requires careful consideration of several factors:
- Application Requirements: The primary function of the final component heavily influences powder selection. Components requiring high strength and ductility might benefit from magnesium-alloyed variants like LPW AlSi10Mg or EOS Aluminium AlSi10Mg. Conversely, applications demanding superior wear resistance might favor silicon-rich options like DLP AlSi10Si or Lehmann Voss AlSi10Si.
- Particle Morphology: The shape and size of the powder particles significantly impact flowability, packing density, and final component properties. Spherical morphologies, like those found in AMpact AM300, generally offer better flowability and are suitable for intricate geometries. Conversely, irregular shapes, like those in Höganäs Grafoil AM, can enhance mechanical interlocking during compaction, leading to improved strength. Particle size distribution also plays a role, with finer powders typically achieving higher densities after HIP but potentially exhibiting reduced flowability.
- Manufacturing Process: The intended fabrication method, such as additive manufacturing or conventional powder metallurgy, can influence powder selection. Powders specifically designed for additive manufacturing, like AMpact AM300 and Proto Labs AlSi10Mg 2.0, often prioritize flowability for efficient spreading in laser or electron beam melting processes.
- Cost Considerations: Production costs can vary depending on the powder model. Gas-atomized powders, like AMpact AM300 and LPW AlSi10Mg, generally command a premium due to the involved production process. Water-atomized variants, like Höganäs Grafoil AM, might be more cost-effective but might require adjustments in processing parameters to achieve desired properties.
- Supplier Reputation: Selecting a reputable supplier with a proven track record in metal powder production is crucial. Look for suppliers who offer consistent quality control measures, detailed technical data sheets, and application support to ensure successful HIP processing.
Additional Considerations:
- Environmental Impact: The production process and material composition of the powder can influence its environmental footprint. Consider suppliers committed to sustainable practices and powders with minimal environmental impact.
- Safety Precautions: Always follow recommended safety protocols when handling metal powders. This includes using appropriate personal protective equipment (PPE) and adhering to safe handling procedures to minimize inhalation risks and potential fire hazards.
By carefully evaluating these factors and consulting with your chosen supplier, you can select the optimal AlSi10(4045) powder model to achieve the desired properties and performance in your HIP application.
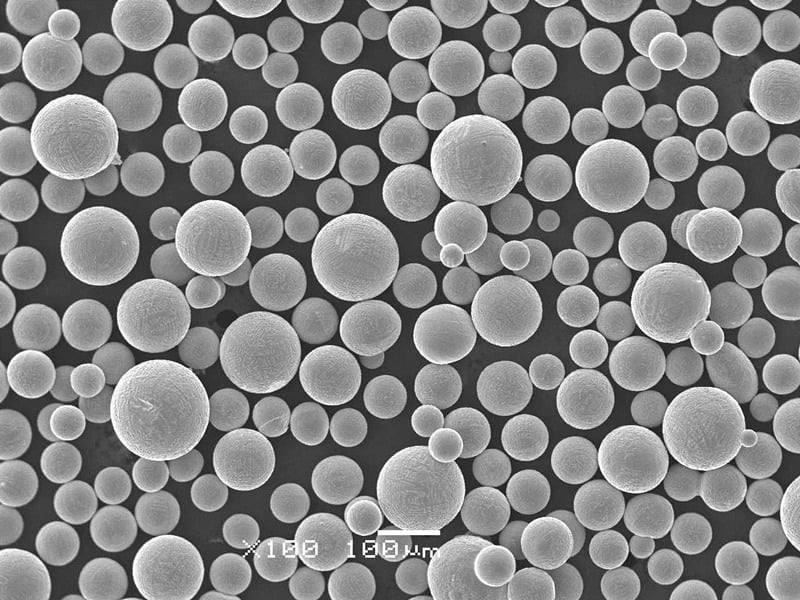
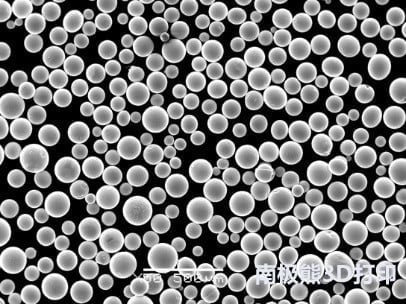
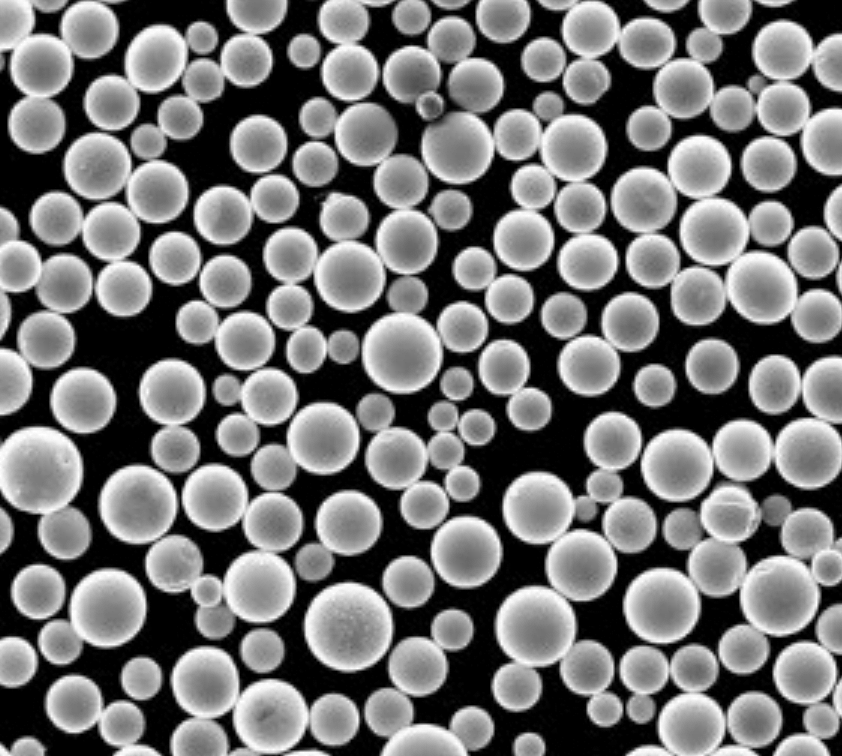
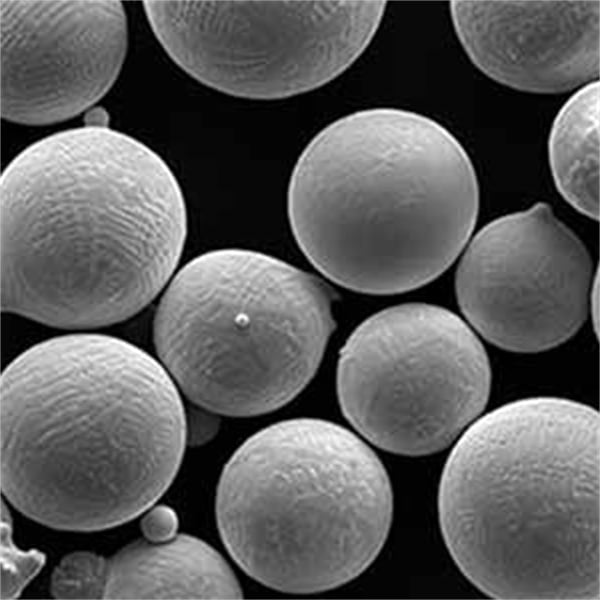
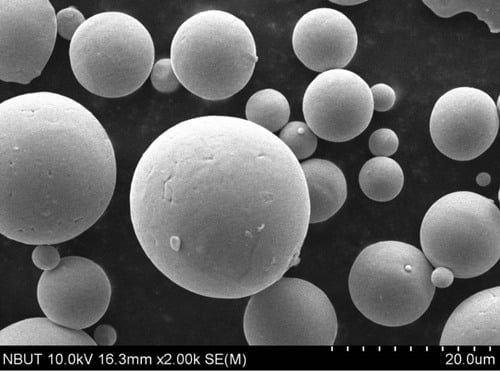
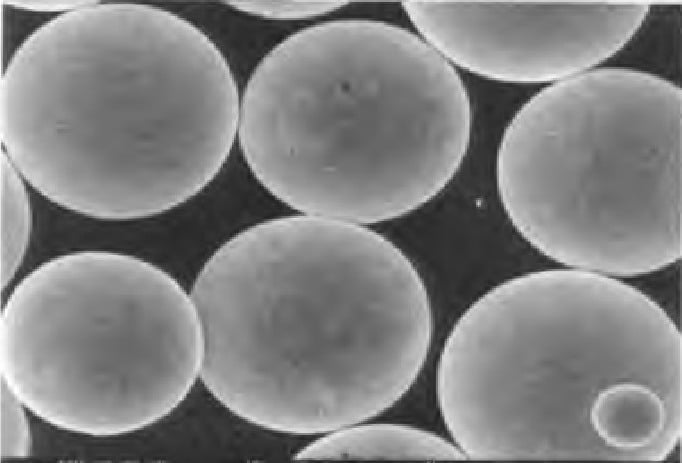
Properties of AlSi10(4045) power for HIP
The properties of AlSi10(4045) powder play a vital role in determining the final characteristics of the HIPed component. Here’s a table summarizing some key properties:
Bất động sản | Miêu tả |
---|---|
Chemical Composition | ~10% Silicon (Si), balance Aluminum (Al) |
Mật độ | ~2.65 g/cm³ (depending on powder processing method) |
Khả năng chảy | Varies depending on particle morphology and size distribution |
Mật độ biểu kiến | ~60-70% of theoretical density (increases after HIP) |
Điểm Nóng Chảy | ~577°C |
Hệ số giãn nở nhiệt | ~23 x 10^-6 /K |
After HIPing, AlSi10(4045) components typically exhibit:
- High Density: HIP eliminates voids, achieving near-net-shape components with densities exceeding 99% of theoretical.
- Improved Mechanical Strength: The elimination of defects and enhanced inter-particle bonding lead to significant increases in tensile strength, yield strength, and fatigue resistance.
- Enhanced Ductility: HIP can improve ductility compared to cast components, offering better resistance to deformation under stress.
- Dimensional Accuracy: HIP minimizes shrinkage and distortion, resulting in components with exceptional dimensional accuracy.
It’s important to remember that the specific properties of the final HIPed component can be influenced by several factors, including:
- Powder model selection (as discussed earlier)
- HIP processing parameters (temperature, pressure, and hold time)
- Cooling profile after HIP
Applications of AlSi10(4045) Powder for HIP
AlSi10(4045) powder finds application in a diverse range of industries due to its versatility and the exceptional properties achievable through HIP processing. Here are some prominent examples:
Ngành | Ví dụ ứng dụng |
---|---|
Hiệp công | Lightweight structural components, heat exchangers, engine parts requiring high strength-to-weight ratio |
Ô tô | Complex engine components, brake calipers, wheels (especially for electric vehicles) |
Y học | Biocompatible implants, prosthetics, custom surgical instruments |
Quốc phòng | Armor components, weapon parts demanding high strength and fatigue resistance |
Consumer Electronics | Heat sinks for high-performance electronics, intricate housings for mobile devices |
Dầu & Khí đốt | Downhole components requiring exceptional wear resistance and corrosion protection |
Beyond these specific examples, AlSi10(4045) powder for HIP holds promise in various emerging applications, including:
- Additive Manufacturing (AM): AlSi10(4045) powder is a popular choice for AM processes like Selective Laser Melting (SLM) due to its good flowability and laser compatibility. HIPing post-processed AM components in AlSi10(4045) significantly improves their mechanical properties, making them suitable for demanding applications.
- Lightweighting: The high strength-to-weight ratio of AlSi10(4045) after HIP makes it ideal for weight-critical applications across industries like aerospace and automotive. Components can be designed with intricate lattice structures to further reduce weight while maintaining structural integrity.
- Multi-Material Parts: HIP allows for the consolidation of AlSi10(4045) powder with other materials, enabling the creation of components with tailored properties in different regions. This opens doors for innovative designs with functional gradients.
Advantages and Limitations of AlSi10(4045) Powder for HIP
Advantages:
- Excellent Castability and Weldability: The high silicon content in AlSi10(4045) powder enhances its castability and weldability, making it suitable for complex geometries.
- High Strength and Ductility: After HIP, AlSi10(4045) components achieve superior mechanical properties, offering a good balance between strength and ductility.
- Dimensional Accuracy: HIP minimizes shrinkage and distortion, resulting in components with exceptional dimensional precision.
- Lightweight: AlSi10(4045) offers a good strength-to-weight ratio, making it ideal for weight-critical applications.
- Versatility: AlSi10(4045) powder finds application in diverse industries due to its tailorable properties and compatibility with various post-processing techniques like HIP.
Limitations:
- Cost: The production process for metal powders can be expensive, and HIP adds an additional step to the manufacturing chain, potentially increasing overall costs.
- Residual Stresses: HIPing can introduce residual stresses in the component, which require careful consideration during design and potentially additional post-processing steps for stress relief.
- Surface Finish: The surface finish of HIPed components might not be as smooth as those achieved with traditional machining techniques. Additional finishing processes might be necessary depending on the application requirements.
- Environmental Impact: Production of metal powders can have an environmental footprint. Selecting suppliers committed to sustainable practices and minimizing material waste during processing are crucial considerations.
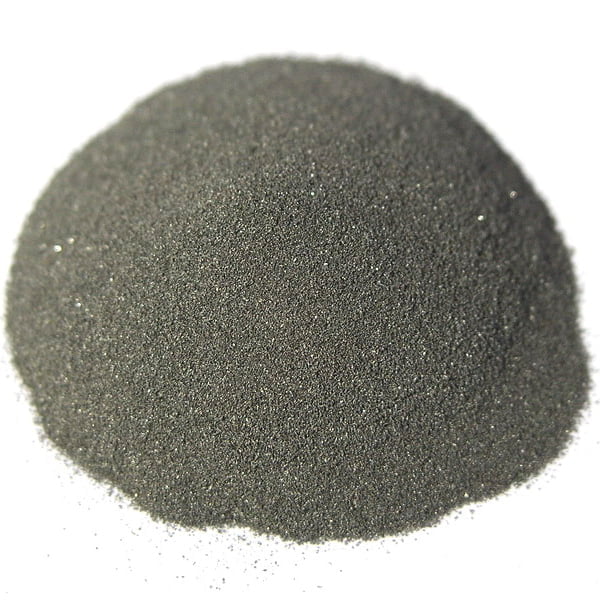
Specifications, Sizes, and Grades of AlSi10(4045) Powder for HIP
AlSi10(4045) powder typically adheres to the specifications outlined in the Aluminum Association standard AMS 4045. This standard defines the chemical composition, mechanical properties, and other relevant characteristics of the powder. However, some manufacturers might offer proprietary variants with slight modifications to cater to specific application needs.
Here’s a table summarizing the typical specifications, sizes, and grades of AlSi10(4045) powder for HIP:
Bất động sản | Miêu tả |
---|---|
Tiêu chuẩn | AMS 4045 (Aluminum Association) |
Chemical Composition | ~10% Silicon (Si), balance Aluminum (Al) |
Phân phối kích thước hạt | Varies depending on the manufacturer and application (typically between 10 µm and 100 µm) |
Mật độ biểu kiến | ~60-70% of theoretical density |
Khả năng chảy | Varies depending on particle morphology and size distribution |
Grades | Typically unalloyed, although some manufacturers might offer variants with minor alloying elements for specific properties. |
It’s important to consult with your chosen powder supplier for detailed information on the specific specifications, sizes, and grades available for their AlSi10(4045) powder product.
Suppliers and Pricing of AlSi10(4045) Powder for HIP
Several reputable suppliers offer AlSi10(4045) powder for HIP applications. Here are some prominent examples, but this list is not exhaustive:
- SLM Solutions: A leading provider of metal additive manufacturing technologies, SLM Solutions also offers a range of metal powders, including gas-atomized AlSi10(4045) optimized for their SLM machines and compatible with HIP post-processing.
- Höganäs AB: Renowned for their water-atomized metal powders, Höganäs AB offers a cost-effective AlSi10(4045) variant suitable for HIP applications. Their focus on sustainability practices might be a deciding factor for environmentally conscious manufacturers.
- APEX Powder Company: This supplier offers a broader range of aluminum alloy powders, including APEX ADiM 316L, an Aluminum-Silicon-Magnesium alloy similar to AlSi10(4045) but with enhanced strength and corrosion resistance. It’s a valuable option for applications demanding these properties alongside the benefits of HIP.
- LPW Technology: A major player in the metal additive manufacturing space, LPW Technology provides gas-atomized AlSi10Mg powder containing magnesium. This addition refines the grain structure and improves both strength and ductility after HIP, making it suitable for components requiring these characteristics.
- DLP Laser GmbH: This company offers DLP AlSi10Si, a silicon-rich variant of the standard AlSi10(4045) powder. The increased silicon content enhances wear resistance, making it ideal for components subjected to high wear and tear and requiring the benefits of HIP processing.
- SLM Solutions GmbH: Not to be confused with SLM Solutions mentioned earlier, this supplier offers EOS Aluminium AlSi10Mg, similar to LPW AlSi10Mg and APEX ADiM 316L. The presence of magnesium improves strength and corrosion resistance after HIP, making it a popular choice for demanding applications.
- Proto Labs: A specialist in rapid prototyping and on-demand manufacturing, Proto Labs offers Proto Labs AlSi10Mg 2.0 powder. This gas-atomized variant boasts excellent flowability for intricate geometries in additive manufacturing before HIP. The magnesium content refines the grain structure and enhances mechanical properties.
- Lehmann Voss GmbH: This supplier provides Lehmann Voss AlSi10Si, mirroring DLP AlSi10Si with its focus on enhanced wear resistance due to the presence of hard silicon particles. It caters to applications requiring high wear resistance alongside the benefits of HIP.
Pricing for AlSi10(4045) powder can vary depending on several factors, including:
- Manufacturer: Brand recognition and production processes can influence pricing.
- Powder quantity: Bulk purchases often command lower prices per kilogram compared to smaller quantities.
- Particle size distribution: Finer powders might be more expensive due to the increased processing involved.
- Alloying elements: Variants with additional elements like magnesium might incur a premium.
It’s recommended to contact potential suppliers directly for up-to-date pricing information and to discuss your specific application requirements. Many suppliers offer quotation tools on their websites or are readily available to answer technical questions and provide tailored quotes.
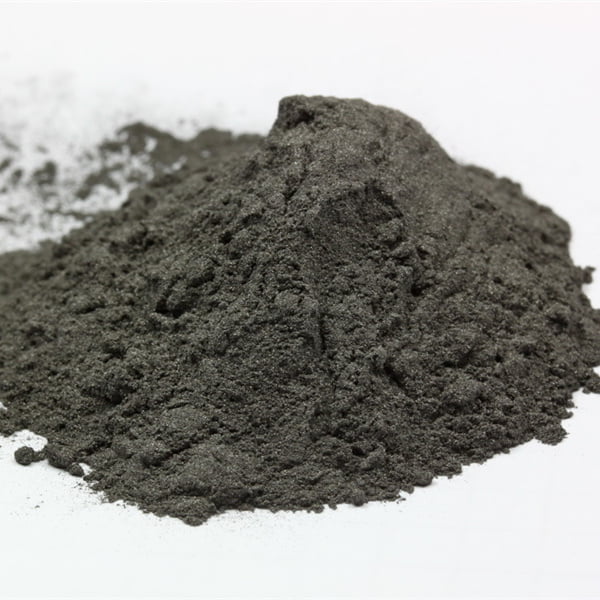
Câu hỏi thường gặp
Q: What are the advantages of using AlSi10(4045) powder for HIP compared to traditional casting methods?
A: HIPing AlSi10(4045) powder offers several advantages over traditional casting. Here are some key points:
- Elimination of voids and porosity: HIP creates near-net-shaped components with superior density, leading to improved mechanical properties and reduced risk of failure.
- Enhanced strength and ductility: The elimination of defects and improved inter-particle bonding significantly increase tensile strength, yield strength, and fatigue resistance compared to castings.
- Dimensional accuracy: HIP minimizes shrinkage and distortion, resulting in components with exceptional dimensional precision, reducing the need for post-machining.
- Design flexibility: Powder-based additive manufacturing techniques, often used before HIP with AlSi10(4045), enable the creation of complex geometries not achievable with conventional casting.
Q: Are there any alternatives to AlSi10(4045) powder for HIP applications?
A: Yes, several alternative metal powders are suitable for HIP. Here are a few examples:
- Aluminum-Magnesium alloys: These offer similar benefits to AlSi10(4045) with potentially enhanced strength and corrosion resistance due to the presence of magnesium.
- Nickel-based superalloys: These alloys boast exceptional high-temperature strength and creep resistance, making them ideal for components operating in extreme environments like jet engines and gas turbines. However, they are generally more expensive than AlSi10(4045).
- Titanium alloys: Offering a unique blend of high strength, low weight, and excellent corrosion resistance, titanium alloys are popular choices for aerospace and biomedical applications. However, they can be significantly more challenging to process compared to AlSi10(4045) and require specialized HIP equipment.
The best choice for your application depends on the specific requirements, including: desired properties, operating environment, cost constraints, and processing capabilities. Consulting with a qualified materials engineer and potential powder suppliers can help you determine the optimal material selection for your HIP application.
Q: What are some safety precautions to consider when handling AlSi10(4045) powder?
A: AlSi10(4045) powder, like most metal powders, can pose certain health risks if not handled appropriately. Here are some crucial safety precautions to follow:
- Personal Protective Equipment (PPE): Always wear appropriate PPE like safety glasses, gloves, and a respirator with a P-100 filter when handling AlSi10(4045) powder. This minimizes the risk of inhalation and potential skin irritation.
- Proper Ventilation: Ensure adequate ventilation in your workspace to prevent airborne powder accumulation. Fume hoods or well-ventilated workstations are recommended.
- Safe Handling Practices: Avoid creating dust clouds and minimize direct contact with the powder. Use designated tools and scoops for handling, and clean up spills promptly following established procedures.
- Proper Disposal: Do not dispose of AlSi10(4045) powder in regular waste bins. Consult with your local regulations for proper disposal procedures to minimize environmental impact.
Safety data sheets (SDS) from the powder supplier will provide detailed information on specific handling and disposal guidelines for AlSi10(4045) powder. Following these guidelines is essential to ensure a safe working environment.
Q: What is the future outlook for AlSi10(4045) powder for HIP applications?
A: The future of AlSi10(4045) powder for HIP appears bright due to several factors:
- Advancements in additive manufacturing: The growing adoption of additive manufacturing techniques like Selective Laser Melting (SLM) creates a strong demand for high-quality metal powders like AlSi10(4045) suitable for both AM and subsequent HIP processing.
- Lightweighting trend: The ongoing push for weight reduction in various industries, particularly aerospace and automotive, makes AlSi10(4045) with its high strength-to-weight ratio an attractive material choice, especially when combined with the benefits of HIP.
- Development of new alloys: Continuous research and development efforts might lead to the creation of new aluminum alloy powders with even better properties tailored for specific applications when used in conjunction with HIP.
- Focus on sustainability: As environmental concerns gain prominence, manufacturers are increasingly seeking sustainable practices. Suppliers committed to eco-friendly powder production methods using recycled materials might gain a competitive edge.
About 3DP mETAL
Product Category
LIÊN HỆ
Bạn có thắc mắc không? Hãy gửi tin nhắn ngay cho chúng tôi! Sau khi nhận được tin nhắn của bạn, chúng tôi sẽ xử lý yêu cầu của bạn với cả một đội ngũ.