Metal injection molding (MIM) has revolutionized the manufacturing landscape for complex, near-net-shape metal components. But the magic behind MIM lies not just in the intricate molding process, but also in the very foundation – the metal powder itself. In this realm, AlSi12(4047) power for MIM stands out as a champion, offering a unique blend of properties that empower engineers to push the boundaries of design and functionality.
Understanding AlSi12(4047) power for MIM
At its core, AlSi12(4047) powder is a marvel of material science. It’s a silicon-aluminum alloy powder, specifically formulated for exceptional performance in MIM applications. The key player in this alloy is, unsurprisingly, aluminum (Al), constituting the majority of the composition (typically around 85-88%). Aluminum brings its well-known advantages to the table – lightweight, excellent corrosion resistance, and good thermal and electrical conductivity.
But it’s the addition of silicon (Si), typically around 11-13%, that truly elevates AlSi12(4047) to new heights. Silicon acts as an alloying element, introducing a multitude of benefits:
- Enhanced Strength and Hardness: Silicon promotes the formation of harder intermetallic phases within the aluminum matrix, significantly improving the material’s tensile strength, yield strength, and hardness compared to pure aluminum. This translates to components that can withstand greater loads and resist deformation under pressure.
- Improved Castability: Silicon refines the grain structure of the aluminum, leading to smoother flow during the MIM process. This translates to better dimensional accuracy and reduced surface roughness in the final parts.
- Wear Resistance: The presence of hard silicon phases on the surface enhances the wear resistance of AlSi12(4047) components, making them ideal for applications that experience friction and abrasion.
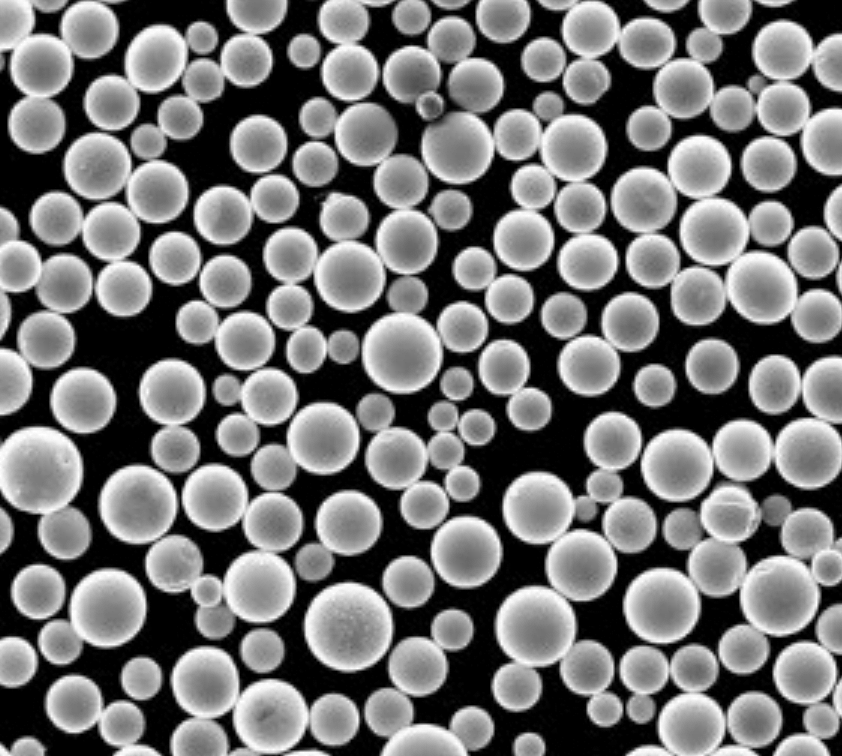
Choosing the Right Fit for Your Needs
The beauty of MIM lies in its versatility. But to truly unlock its potential, selecting the appropriate metal powder is crucial. While AlSi12(4047) shines in many applications, there are a variety of other metal powders available, each with its own strengths and characteristics. Here’s a glimpse into some of the most popular options:
Common Metal Powders for MIM Applications
Metal Powder | Miêu tả | Key Properties | ỨNG DỤNG |
---|---|---|---|
AlSi10Mg (319) | A widely used silicon-aluminum alloy powder with lower silicon content compared to AlSi12(4047). | Offers a good balance of strength, ductility, and castability. | Automotive parts, gears, housings, electronic components |
17-4PH Stainless Steel | A precipitation-hardenable stainless steel powder known for its high strength and corrosion resistance. | Offers excellent mechanical properties, good wear resistance, and biocompatibility. | Medical devices, aerospace components, fasteners, pump parts |
316L Stainless Steel | A versatile austenitic stainless steel powder known for its excellent corrosion resistance. | Offers good formability, weldability, and biocompatibility. | Medical devices, chemical processing equipment, food contact parts |
Nickel Alloy 625 | A high-performance nickel-chromium-molybdenum alloy powder known for its exceptional strength and high-temperature capabilities. | Offers outstanding strength at elevated temperatures, good corrosion resistance, and oxidation resistance. | Aerospace components, turbine blades, heat exchangers |
Inconel 625 | Similar to Nickel Alloy 625, but with a slightly different composition offering improved high-temperature performance. | Offers exceptional strength and creep resistance at very high temperatures. | Gas turbine components, heat exchangers, rocket engine parts |
Titanium Grade 2 | A commercially pure titanium powder known for its biocompatibility, good strength, and low weight. | Offers excellent biocompatibility, good corrosion resistance, and high strength-to-weight ratio. | Medical implants, aerospace components, sporting goods |
Đồng | A pure copper powder known for its excellent electrical conductivity and thermal conductivity. | Offers superior conductivity for electrical applications and good heat dissipation. | Electrical connectors, heat sinks, brazing materials |
Carbon Steel | A family of iron-carbon alloy powders offering a wide range of properties depending on the specific composition. | Offers good strength, affordability, and machinability. | Gears, levers, structural components, low-stress applications |
AlSi12(4047) in Action: Unleashing Potential Across Industries
The unique properties of AlSi12(4047) powder make it a highly sought-after material for a diverse range of applications. Here, we delve into some of the key industries that leverage its strengths:
Automotive Industry: AlSi12(4047) excels in the automotive industry due to its combination of strength, lightweight properties, and good castability. Here are some specific examples:
- Engine Components: Components like pistons, cylinder heads, and transmission housings benefit from AlSi12(4047)’s ability to handle high loads and operate at elevated temperatures.
- Body Parts: AlSi12(4047) can be used for intricate structural components like brackets and levers, offering a balance of strength and weight reduction for improved fuel efficiency.
Consumer Electronics: The electronics industry thrives on miniaturization and complex geometries. AlSi12(4047) plays a vital role in this arena:
- Heat Sinks: Due to its good thermal conductivity, AlSi12(4047) is ideal for heat sinks that dissipate heat away from sensitive electronic components.
- EMI/RFI Shielding: The conductivity of AlSi12(4047) makes it suitable for creating enclosures that shield electronic devices from electromagnetic interference.
- Structural Components: MIM parts made from AlSi12(4047) can be intricate and lightweight, perfect for supporting various electronic components within devices.
Aerospace and Defense: The stringent demands of the aerospace and defense sectors necessitate high-performance materials. AlSi12(4047) steps up to the challenge in several ways:
- Lightweight Structures: In aerospace applications, weight reduction is paramount. AlSi12(4047) offers a good strength-to-weight ratio, allowing for the creation of lightweight yet robust components for aircraft and spacecraft.
- Corrosion Resistance: AlSi12(4047) exhibits good corrosion resistance, essential for parts exposed to harsh environments like those encountered in aerospace applications.
Medical Devices: The medical device industry requires materials that are biocompatible and can withstand the rigors of medical procedures. AlSi12(4047) demonstrates its versatility here as well:
- Surgical Instruments: The intricate geometries achievable with MIM, combined with the strength of AlSi12(4047), make it suitable for the creation of various surgical instruments.
- Prosthetic Components: AlSi12(4047) can be used for certain prosthetic components due to its balance of strength and weight, offering improved comfort and functionality for patients.
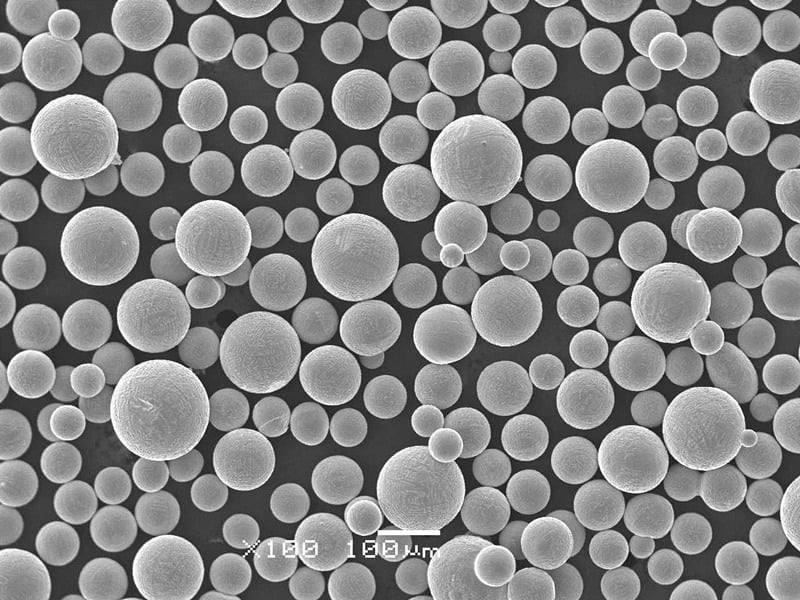
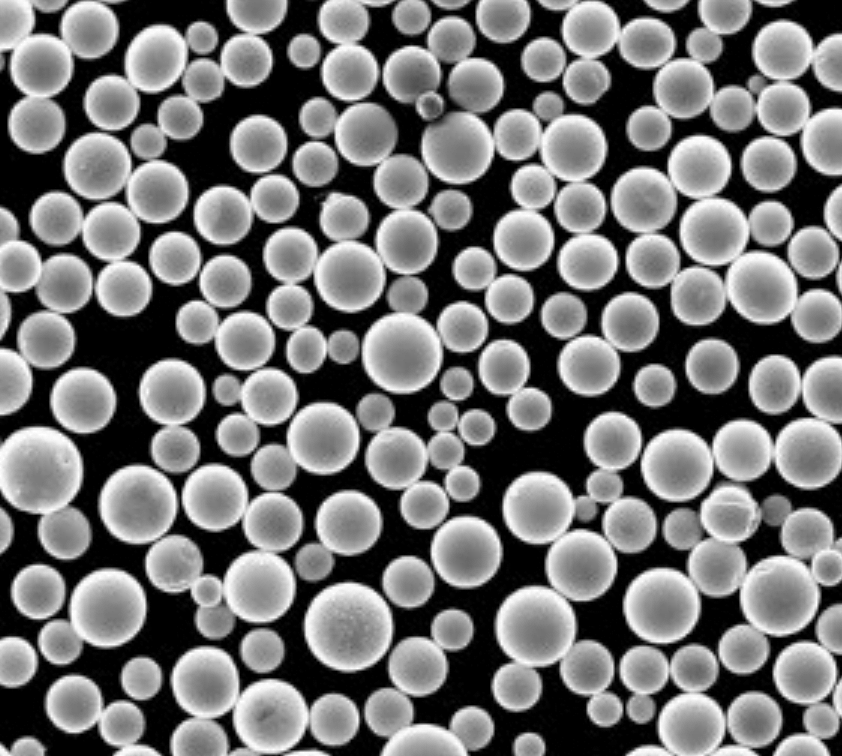
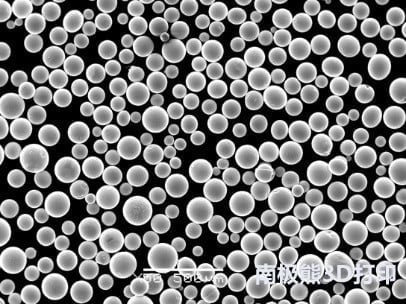
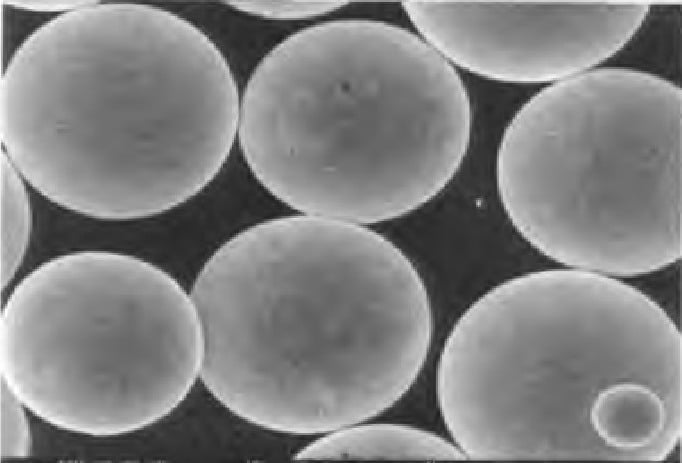
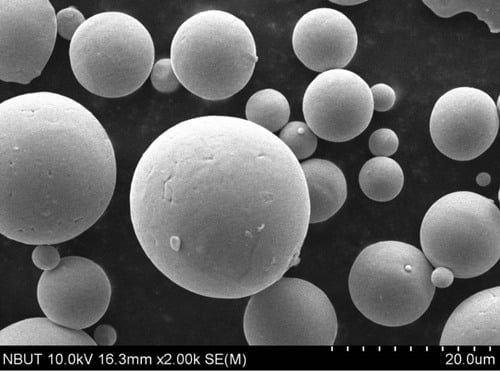
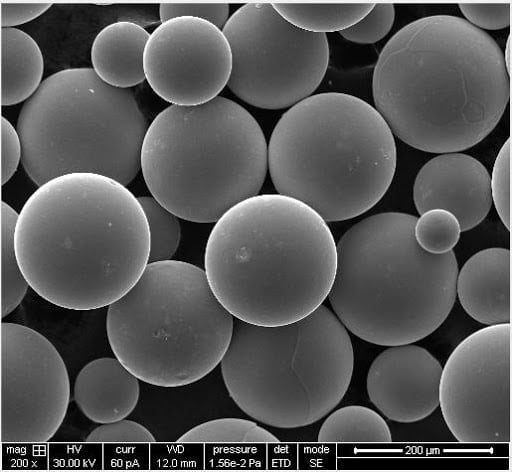
Advantages of AlSi12(4047) power for MIM
When compared to other metal powders for MIM, AlSi12(4047) boasts several key advantages:
- Superior Mechanical Properties: The combination of aluminum and silicon in AlSi12(4047) delivers superior strength, hardness, and wear resistance compared to pure aluminum powders. This translates to MIM parts that can withstand greater loads and perform under demanding conditions.
- Excellent Castability: The presence of silicon refines the grain structure of AlSi12(4047), enhancing its flow characteristics during the MIM process. This results in better dimensional accuracy, smoother surface finishes, and reduced part rejection rates.
- Cost-Effectiveness: Aluminum is a relatively abundant and affordable material compared to some specialty alloys used in MIM. This translates to cost-competitive pricing for AlSi12(4047) powder, making it an attractive option for various applications.
- Wide Range of Applications: The versatility of AlSi12(4047) allows it to be used across a diverse range of industries, from automotive and consumer electronics to aerospace and medical devices.
Disadvantages of AlSi12(4047) Powder for MIM
While AlSi12(4047) offers numerous advantages, it’s essential to consider some limitations:
- Lower Strength Compared to Some Alloys: While stronger than pure aluminum, AlSi12(4047) might not be suitable for applications requiring the absolute highest strength. In such cases, high-performance alloys like 17-4PH stainless steel or Inconel 625 might be better choices.
- Higher Brittleness Compared to Pure Aluminum: The addition of silicon can slightly increase the brittleness of AlSi12(4047) compared to pure aluminum. This needs to be taken into account for applications requiring high ductility or impact resistance.
Selecting the Right Metal Powder for Your MIM Needs
Choosing the optimal metal powder for your MIM application hinges on understanding the specific requirements of your project. Here are some key factors to consider when comparing AlSi12(4047) to other options:
- Mechanical Properties: Evaluate the required strength, hardness, wear resistance, and ductility for your application. AlSi12(4047) offers a good balance, but high-performance alloys might be necessary for exceptional strength demands.
- Corrosion Resistance: Consider the environment your MIM parts will operate in. AlSi12(4047) exhibits good corrosion resistance, but for harsher environments, stainless steel powders might be a better choice.
- Thermal Properties: If thermal conductivity or heat dissipation is crucial, consider copper or aluminum-based powders like AlSi12(4047). For high-temperature applications, nickel alloys might be more suitable.
- Biocompatibility: For medical device applications, biocompatibility is paramount. AlSi12(4047) might be suitable for certain applications, but for others, titanium or specific biocompatible stainless steel powders might be necessary.
- Weight Considerations: In applications where weight reduction is critical, aluminum-based powders like AlSi12(4047) excel. However, for parts requiring high density, materials like steel or copper powders might be a better fit.
- Cost: AlSi12(4047) offers a cost-effective option compared to some specialty alloys. However, consider the overall project budget and the cost-performance trade-off when making your selection.
MIM Powder Specifications and Considerations
Beyond the base material selection (e.g., AlSi12(4047) versus another alloy), several factors influence the performance of MIM powders:
- Particle Size and Distribution: The size and distribution of powder particles significantly impact flowability, packing density, and final part properties. Powders with a well-controlled particle size distribution are preferred for optimal MIM processing.
- Powder Flowability: Good flowability ensures efficient powder movement during the MIM process, leading to consistent part quality. Powders with the appropriate particle size and morphology exhibit better flow characteristics.
- Mật độ biểu kiến: The apparent density of the powder influences the amount of material required to fill the mold cavity and the final density of the MIM part. Powders with higher apparent density can result in denser parts with improved mechanical properties.
- Powder Purity: The presence of impurities in the powder can negatively affect the performance of the MIM part. High purity powders are essential for achieving consistent and reliable results.
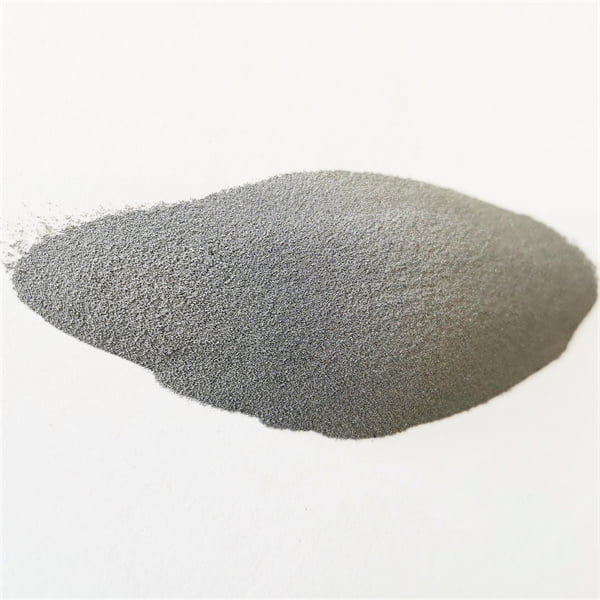
Suppliers and Pricing of AlSi12(4047) Powder
AlSi12(4047) powder is readily available from a variety of reputable metal powder suppliers. Pricing can vary depending on factors like:
- Order Quantity: Larger quantities typically command lower per-unit prices.
- Powder Specifications: Powders with tighter particle size control or higher purity might come at a premium.
- Supplier Lead Times: Expedited shipping or specific requirements might affect the cost.
It’s recommended to obtain quotes from multiple suppliers to compare pricing and ensure you’re getting the best value for your project needs.
Câu hỏi thường gặp
Q: How strong is AlSi12(4047) powder compared to pure aluminum?
A: AlSi12(4047) offers significantly higher strength and hardness compared to pure aluminum. The addition of silicon promotes the formation of harder intermetallic phases, enhancing the material’s mechanical properties.
Q: Is AlSi12(4047) powder corrosion resistant?
A: AlSi12(4047) exhibits good corrosion resistance due to the presence of aluminum in its composition. However, for environments with harsher corrosive elements, stainless steel powders might be a better choice.
Q: What are some applications where AlSi12(4047) powder wouldn’t be ideal?
A: While versatile, AlSi12(4047) might not be the best fit for applications requiring the absolute highest strength or extreme ductility. In such cases, high-performance alloys or pure aluminum might be better suited.
Q: How does AlSi12(4047) powder compare to other metal powders for MIM in terms of cost?
A: AlSi12(4047) is a relatively cost-effective option compared to some specialty alloys used in MIM. This makes it an attractive choice for various applications where cost is a consideration.
About 3DP mETAL
Product Category
LIÊN HỆ
Bạn có thắc mắc không? Hãy gửi tin nhắn ngay cho chúng tôi! Sau khi nhận được tin nhắn của bạn, chúng tôi sẽ xử lý yêu cầu của bạn với cả một đội ngũ.