Imagine a material that combines the lightweight sturdiness of aluminum, the robust strength of iron, and the exceptional corrosion resistance of zirconium. That’s the magic of aluminium-iron-zirconium powders, a unique blend offering a treasure trove of properties for various industrial applications. Buckle up, because we’re about to embark on a journey to explore these remarkable metallic marvels!
Understanding the Synergy: A Compositional Breakdown
Aluminium-iron-zirconium powders, as the name suggests, are engineered metallic mixtures where the three elements come together in varying ratios to achieve specific functionalities. Here’s a closer look at the key players in this metallic alliance:
- Aluminum (Al): The lightweight champion, aluminum brings remarkable weight savings without compromising on strength. It also boasts excellent thermal and electrical conductivity.
- Iron (Fe): The iron fist in this metallic glove, iron provides superior strength, toughness, and wear resistance – crucial qualities for demanding applications.
- Zirconium (Zr): The unsung hero, zirconium shines with its exceptional resistance to corrosion, even in harsh environments. It also enhances the material’s high-temperature performance.
By combining these elements in different proportions, manufacturers can tailor the properties of the powder to suit specific needs.
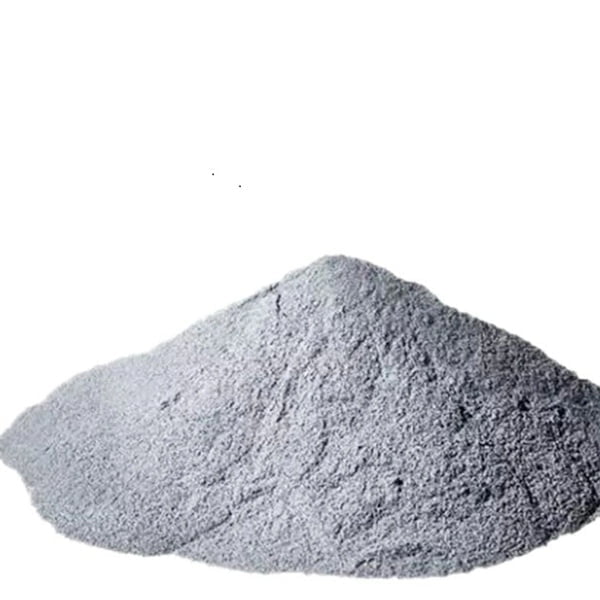
Common Aluminium-Iron-Zirconium Powder Model Variations
Here’s a glimpse into some of the most popular aluminium-iron-zirconium powder models, along with their characteristic compositions and applications:
Model Name | Composition (wt%) | Key Properties | ỨNG DỤNG |
---|---|---|---|
Al-10Fe-1Zr | Al-90%, Fe-10%, Zr-1% | High strength-to-weight ratio, good corrosion resistance | Automotive components, aerospace parts, sporting goods |
Al-5Fe-2Zr | Al-93%, Fe-5%, Zr-2% | Excellent machinability, enhanced wear resistance | Gears, pistons, bearings |
Fe-Al-20Zr | Fe-70%, Al-10%, Zr-20% | Superior high-temperature strength, exceptional corrosion resistance | Heat exchangers, furnace components, chemical processing equipment |
Al-30Fe-5Zr | Al-65%, Fe-30%, Zr-5% | High strength, good wear resistance, moderate weight savings | Construction materials, tools, wear plates |
Zr-20Fe-10Al | Zr-70%, Fe-20%, Al-10% | Unmatched corrosion resistance, good high-temperature performance | Marine components, chemical processing equipment, nuclear reactors (limited applications due to radioactivity of Zr) |
Additional Considerations:
These are just a few examples, and the specific composition can be further customized based on the desired properties. Factors like particle size, morphology, and surface treatments can also significantly influence the powder’s behavior.
Applications of Aluminium-Iron-Zirconium Powders
The unique blend of properties offered by aluminium-iron-zirconium powders opens doors to a wide range of applications across various industries. Let’s delve into some of the most prominent areas where these metallic marvels leave their mark:
- Automotive and Aerospace: The lightweight strength and corrosion resistance make these powders ideal for manufacturing car parts (wheels, engine components), aircraft components (fuselage panels, landing gear), and even spacecraft parts (heat shields, rocket nozzles). Every gram saved translates to improved fuel efficiency and payload capacity.
- Construction and Infrastructure: Their robust strength and durability make them suitable for building materials (cladding panels, reinforcement bars), tools (hammers, drills), and wear plates for heavy machinery.
- Chemical Processing and Energy Production: The exceptional corrosion resistance of these powders makes them perfect for equipment used in harsh environments, such as chemical reactors, heat exchangers, and components for nuclear power plants (limited applications due to radioactivity of Zr).
- Sporting Goods and Consumer Electronics: The combination of strength, machinability, and lightweight properties makes them well-suited for high-performance sporting goods (bicycle frames, baseball bats) and even some electronic components (heat sinks).
Beyond the Obvious:
The potential applications of these powders are constantly being explored. Researchers are investigating their use in:
- Biomedical implants: Due to their biocompatibility (depending on specific composition) and corrosion resistance, these powders could be used for implants requiring long-term functionality.
- Additive manufacturing (3D printing): Their flowability and good sintering behavior make them suitable for creating complex 3D printed parts with tailored properties.
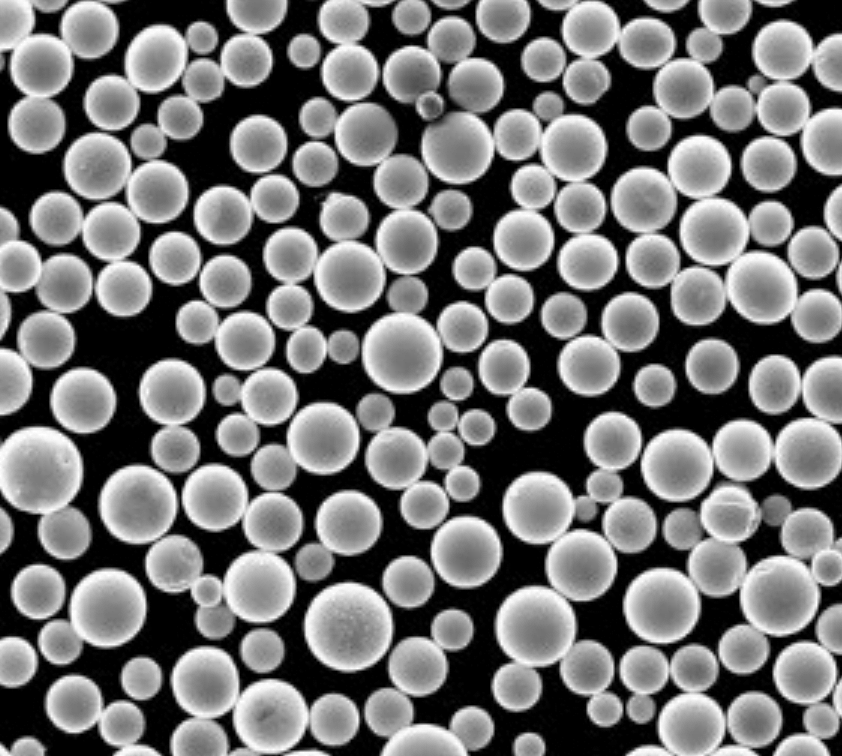
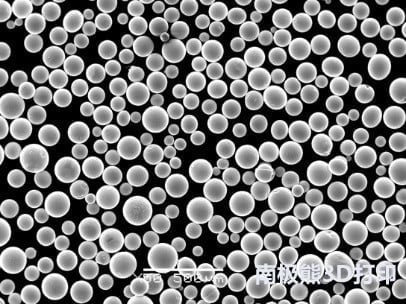
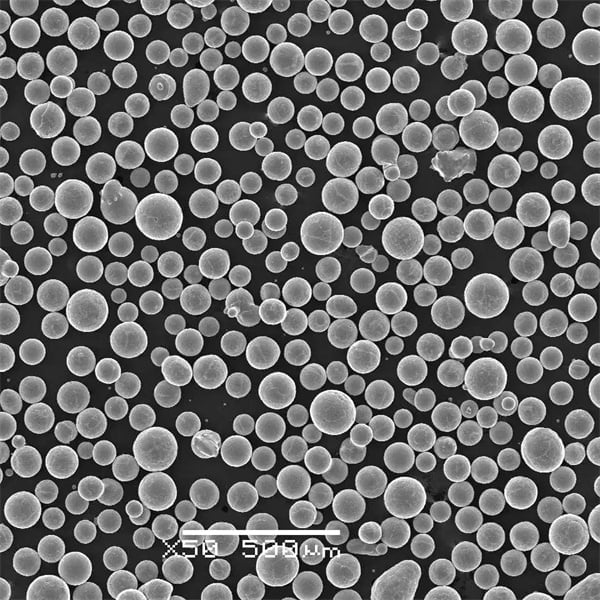
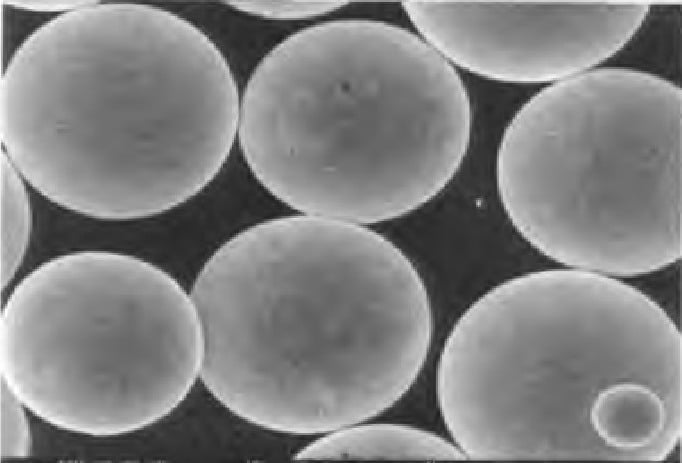
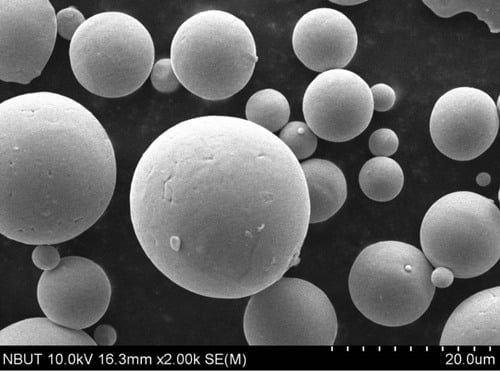
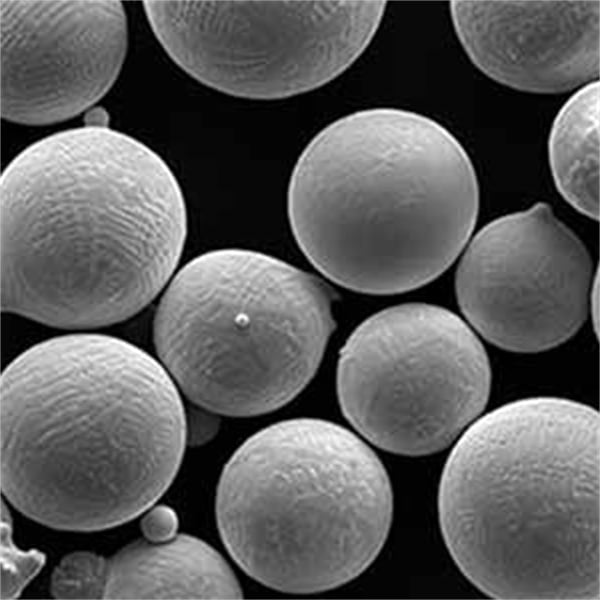
Specifications and Considerations: Choosing the Right Powder
When selecting the right aluminium-iron-zirconium powder for your application, several factors need to be considered:
- Sáng tác: As discussed earlier, the specific ratio of aluminum, iron, and zirconium will significantly impact the powder’s properties. Consider the trade-off between factors like strength, weight, corrosion resistance, and machinability based on your application’s needs.
- Particle Size and Morphology: The size and shape of the powder particles influence aspects like flowability, packing density, and final product properties. Finer powders offer better surface area contact for enhanced bonding but may be more challenging to handle due to increased caking tendency. Conversely, larger particles offer better flowability but may result in a less homogenous final product.
- Surface Treatments: Powders can undergo various surface treatments like oxidation, nitriding, or silanization. These treatments can improve bonding characteristics, corrosion resistance, or flowability depending on the chosen method.
Standardization and Availability
Several international standards govern the specifications of metallic powders, including aluminium-iron-zirconium blends. Some common standards include:
- ASTM International (ASTM): Sets standards for various aspects of materials, including powders (e.g., ASTM B243 for aluminum powders).
- American Society of Mechanical Engineers (ASME): Provides standards for mechanical engineering applications, including powder metallurgy (e.g., ASME B 92.2 for metallic powders used in sintered parts).
- International Organization for Standardization (ISO): Develops international standards for a wide range of products and processes, including metallic powders (e.g., ISO 3091 for non-agglomerated metal powders).
Knowing the relevant standards can help ensure the powder you choose meets the necessary quality and performance requirements.
Sourcing and Pricing:
The availability and pricing of aluminium-iron-zirconium powders can vary depending on factors like:
- Sáng tác: Powders with higher zirconium content tend to be more expensive due to the element’s relative rarity.
- Particle size and morphology: Finer powders or those with specific morphologies may command a premium price.
- Surface treatments: Powders with specialized surface treatments may incur additional costs.
- Quantity: Larger purchases often benefit from bulk discounts.
Several reputable suppliers offer aluminium-iron-zirconium powders. Conducting thorough research and comparing pricing from various vendors is crucial for securing the best value for your project.
General Pricing Trends:
While specific pricing can fluctuate, here’s a ballpark range for aluminium-iron-zirconium powders (per kilogram):
- Standard grade powders: $10- $50
- Finer powders or powders with specific morphologies: $50- $100
- Powders with specialized surface treatments: $100+
Remember: These are just general estimates, and actual pricing can vary significantly depending on the factors mentioned above.
Advantages and Limitations of Aluminium-Iron-Zirconium Powders
Advantages:
- Tailored Properties: By adjusting the composition, these powders offer a remarkable degree of customization in terms of strength, weight, corrosion resistance, and machinability.
- Lightweight Strength: The combination of aluminum and iron allows for achieving high strength-to-weight ratios, crucial for applications where weight reduction is essential (e.g., aerospace, automotive).
- Superior Corrosion Resistance: The presence of zirconium significantly enhances the material’s resistance to corrosion, making it ideal for harsh environments (e.g., chemical processing, marine applications).
- Good Machinability: Depending on the specific composition and particle size, these powders can offer good machinability, allowing for efficient shaping and fabrication of components.
Limitations:
- Cost: Compared to some common engineering materials (e.g., mild steel), aluminium-iron-zirconium powders can be more expensive, especially for compositions with higher zirconium content.
- Processing Challenges: Depending on the powder characteristics, specialized techniques like hot isostatic pressing (HIP) may be required for achieving optimal densification and performance in the final product.
- Limited Availability: While gaining popularity, aluminium-iron-zirconium powders may not be as readily available as some more common metallic powders.
The Takeaway:
Aluminium-iron-zirconium powders offer a unique combination of properties that make them valuable for diverse applications. However, it’s crucial to weigh the advantages against the limitations and consider factors like cost and processing requirements before incorporating them into your project.
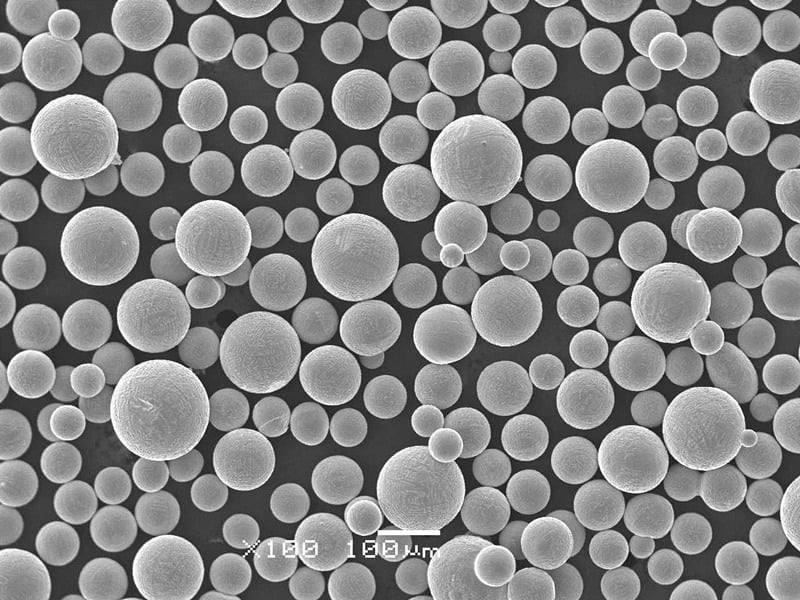
Câu hỏi thường gặp
Q: Are aluminium-iron-zirconium powders safe to handle?
A: The safety profile of these powders depends on the specific composition. Aluminium and iron are generally considered safe for handling with proper precautions (e.g., wearing gloves, dust masks). Zirconium can pose some health risks, particularly in its dust form. Always consult the safety data sheet (SDS) provided by the manufacturer for specific handling recommendations and any potential hazards associated with the particular aluminium-iron-zirconium powder blend.
Q: How do aluminium-iron-zirconium powders compare to other metal powders?
A: Here’s a comparison of aluminium-iron-zirconium powders with some commonly used metal powders:
Feature | Aluminium-Iron-Zirconium Powders | Steel Powders | Aluminum Powders |
---|---|---|---|
Sức mạnh | High (depending on iron content) | Cao nhất | Vừa đủ |
Weight | Nhẹ | Heaviest | Lightest |
Khả năng chống ăn mòn | Excellent (due to zirconium) | Vừa đủ | Yếu |
Khả năng gia công | Good (depending on composition) | Tốt | Xuất sắc |
Chi phí | Moderate to High (depending on zirconium content) | Thấp | Thấp |
As you can see, aluminium-iron-zirconium powders offer a good balance of strength, weight, and corrosion resistance, making them a suitable choice for applications where these combined properties are crucial. However, they may be more expensive than steel or aluminum powders alone.
Q: What are the future prospects for aluminium-iron-zirconium powders?
A: The future of aluminium-iron-zirconium powders looks promising. Here are some potential areas of growth:
- Advancements in powder metallurgy: As powder metallurgy techniques continue to evolve, these powders could become even more cost-effective and widely used for producing complex, high-performance parts.
- Development of new compositions: Research is ongoing to explore new compositions and processing methods to further optimize the properties of these powders for specific applications.
- Additive manufacturing (3D printing): The growing adoption of 3D printing technologies could open up new avenues for utilizing aluminium-iron-zirconium powders in creating complex, custom-designed components.
The overall outlook suggests that aluminium-iron-zirconium powders are poised to play an increasingly significant role in various industrial sectors as their unique properties and processing capabilities are further explored and exploited.
Kết luận
Aluminium-iron-zirconium powders offer a compelling proposition for engineers and designers seeking a material that blends strength, weight savings, and exceptional corrosion resistance. By understanding the interplay between composition, processing methods, and final properties, you can unlock the true potential of these versatile metallic marvels in your next project. Remember, careful consideration of the advantages and limitations alongside a thorough evaluation of your specific needs will guide you towards selecting the most suitable aluminium-iron-zirconium powder for your application. As research and development efforts continue, we can expect even more exciting possibilities to emerge from this powerful metallic trio.
About 3DP mETAL
Product Category
LIÊN HỆ
Bạn có thắc mắc không? Hãy gửi tin nhắn ngay cho chúng tôi! Sau khi nhận được tin nhắn của bạn, chúng tôi sẽ xử lý yêu cầu của bạn với cả một đội ngũ.