Overview of Atomized Powders
Atomized powders are finely powdered metals created through atomization, a process where molten metal is dispersed into fine droplets and solidified rapidly. These powders are integral in various industries, from aerospace to biomedical applications, due to their precise particle size distribution and unique properties. Let’s delve into the fascinating world of atomized powders, exploring their types, compositions, properties, applications, and more.
What Are Atomized Powders?
Atomized powders are produced by atomizing molten metal into tiny droplets using gas, water, or centrifugal forces. The resulting particles are rapidly solidified, creating powders with specific characteristics suitable for diverse industrial applications.
Key Benefits of Atomized Powders
- Uniform Particle Size Distribution: Ensures consistent quality and performance in applications.
- High Purity Levels: Essential for applications demanding stringent material standards.
- Enhanced Sintering Properties: Ideal for additive manufacturing and powder metallurgy.
- Versatile Applications: Used in various sectors, including aerospace, automotive, and medical industries.
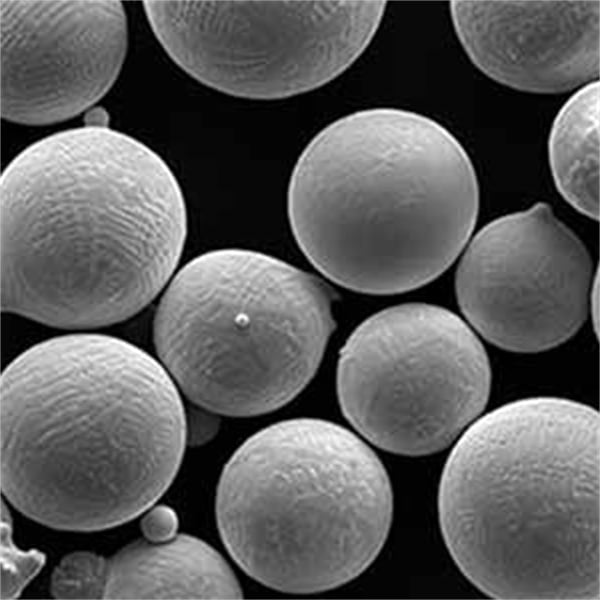
Types of Atomized Powders
Type | Sáng tác | thuộc tính |
---|---|---|
Iron Powder | Sắt | High compressibility, magnetic properties |
Aluminum Powder | Al | Lightweight, high thermal conductivity |
Copper Powder | Đồng | Excellent electrical conductivity |
Stainless Steel Powder | Fe, Cr, Ni | Corrosion resistance, high strength |
Nickel Powder | Đúng | High temperature resistance, corrosion resistance |
Titanium Powder | Ti | High strength-to-weight ratio, biocompatibility |
Cobalt Powder | Co | Wear resistance, magnetic properties |
Bronze Powder | Cu, Sn | Low friction, good conductivity |
Zinc Powder | Zn | Anti-corrosive properties, galvanizing |
Magnesium Powder | Mg | Lightweight, high strength |
Applications of Atomized Powders
Atomized powders serve a plethora of applications due to their versatile properties. Here’s an overview:
Ứng dụng | Loại bột | Lợi ích |
---|---|---|
sản xuất bồi đắp | Titanium, Stainless Steel | Precise part fabrication, reduced waste |
Luân kim thuật bột | Iron, Bronze | Enhanced mechanical properties, cost-effective |
Điện tử | Copper, Silver | Superior electrical conductivity, miniaturization |
Hiệp công | Nickel, Titanium | Lightweight, high performance in extreme conditions |
Ô tô | Aluminum, Magnesium | Weight reduction, fuel efficiency |
Biomedical Implants | Titanium, Cobalt-Chrome | Biocompatibility, durability |
Coatings | Zinc, Aluminum | Corrosion resistance, aesthetic finishes |
Catalysts | Platinum, Palladium | High catalytic activity, efficiency in reactions |
Magnetic Applications | Iron, Cobalt | Magnetic properties, used in motors and sensors |
Energy Storage | Lithium, Silicon | High energy density, long cycle life |
Detailed Descriptions of Specific Metal Powder Models
- Iron Powder (Fe)
- Description: Commonly used in automotive parts and magnetic materials due to its excellent compressibility and magnetic properties.
- Applications: Powder metallurgy, magnetic applications, automotive parts.
- Properties: High purity, good compressibility, magnetic.
- Aluminum Powder (Al)
- Description: Known for its lightweight and high thermal conductivity, making it ideal for aerospace and automotive industries.
- Applications: Lightweight structures, thermal management, additive manufacturing.
- Properties: Lightweight, high thermal conductivity, corrosion-resistant.
- Copper Powder (Cu)
- Description: Offers excellent electrical and thermal conductivity, widely used in electronics and conductive inks.
- Applications: Electrical contacts, heat sinks, conductive inks.
- Properties: High electrical conductivity, good thermal properties, malleable.
- Stainless Steel Powder (Fe, Cr, Ni)
- Description: A blend of iron, chromium, and nickel, offering high strength and corrosion resistance, suitable for diverse applications.
- Applications: Additive manufacturing, biomedical implants, aerospace components.
- Properties: Corrosion-resistant, high strength, durable.
- Nickel Powder (Ni)
- Description: Essential for high-temperature and corrosion-resistant applications, often used in aerospace and chemical industries.
- Applications: Superalloys, catalysts, batteries.
- Properties: High temperature resistance, corrosion-resistant, good mechanical properties.
- Titanium Powder (Ti)
- Description: Known for its high strength-to-weight ratio and biocompatibility, critical for aerospace and medical applications.
- Applications: Aerospace parts, biomedical implants, high-performance sports equipment.
- Properties: High strength, lightweight, biocompatible.
- Cobalt Powder (Co)
- Description: Offers wear resistance and magnetic properties, commonly used in cutting tools and magnetic applications.
- Applications: Hard metals, magnetic materials, batteries.
- Properties: Wear-resistant, magnetic, high strength.
- Bronze Powder (Cu, Sn)
- Description: A mixture of copper and tin, valued for its low friction and good conductivity, ideal for bearings and bushings.
- Applications: Bearings, electrical contacts, decorative items.
- Properties: Low friction, good conductivity, corrosion-resistant.
- Zinc Powder (Zn)
- Description: Primarily used for galvanizing to prevent corrosion and in batteries, providing anti-corrosive properties.
- Applications: Galvanizing, batteries, paints and coatings.
- Properties: Anti-corrosive, good electrochemical properties, reactive.
- Magnesium Powder (Mg)
- Description: Extremely lightweight with high strength, used extensively in the automotive and aerospace industries for weight reduction.
- Applications: Lightweight structures, aerospace components, pyrotechnics.
- Properties: Lightweight, high strength, reactive.
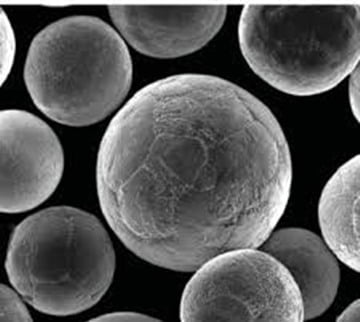
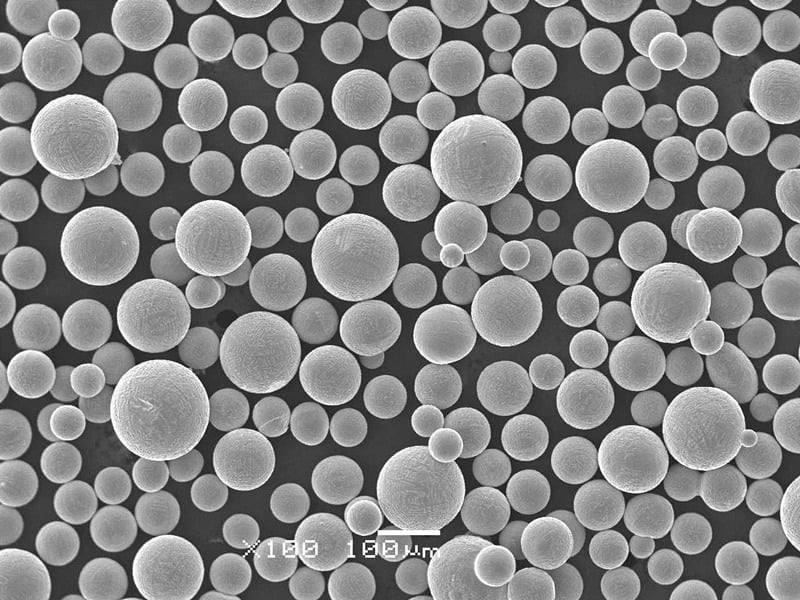
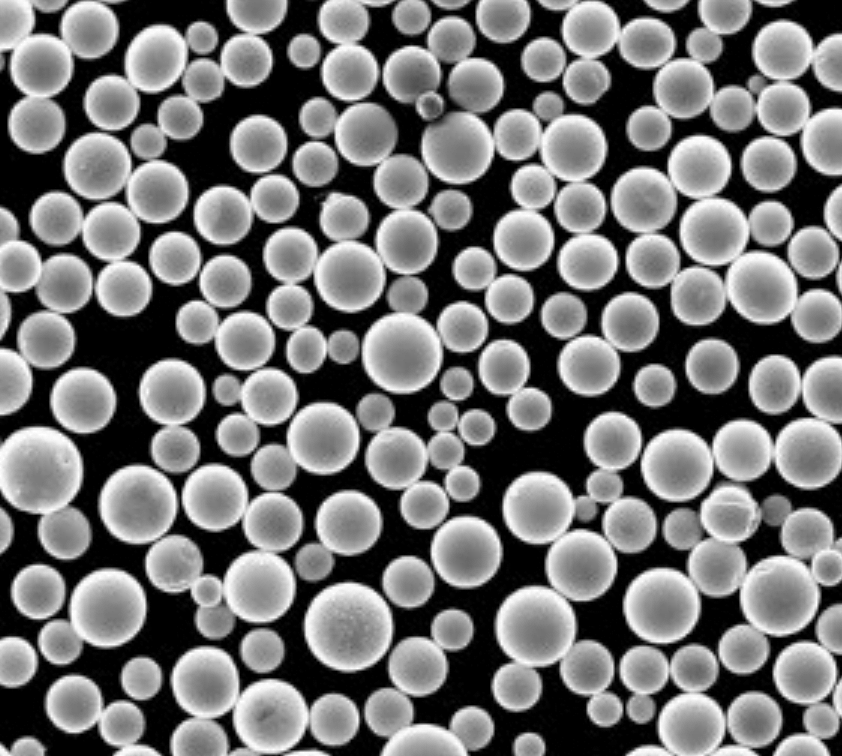
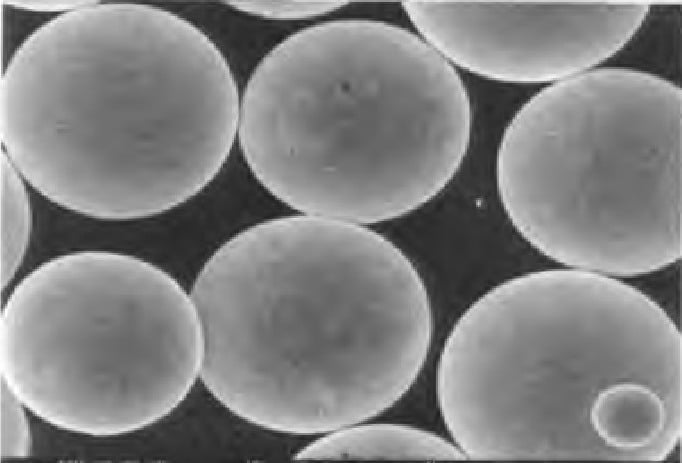
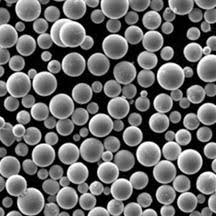
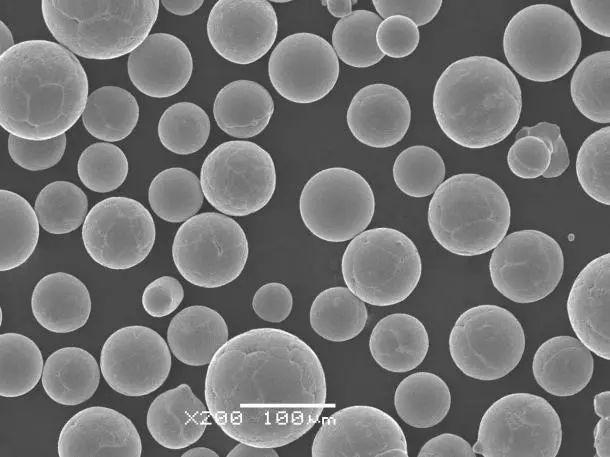
Properties and Characteristics of Atomized Powders
Bất động sản | Miêu tả |
---|---|
Phân phối kích thước hạt | Determines flowability and packing density, crucial for additive manufacturing. |
Sạch sẽ | High purity levels ensure minimal contamination, critical for electronic and biomedical applications. |
Khả năng chảy | Influences how powders behave in manufacturing processes like 3D printing and powder metallurgy. |
Mật độ | Affects the final product’s mechanical properties, such as strength and durability. |
Cấu trúc từ | Shape and surface texture impact how powders are processed and their end-use performance. |
Specifications, Sizes, and Standards
Đặc điểm kỹ thuật | Iron Powder | Aluminum Powder | Copper Powder | Stainless Steel Powder | Nickel Powder | Titanium Powder | Cobalt Powder | Bronze Powder | Zinc Powder | Magnesium Powder |
---|---|---|---|---|---|---|---|---|---|---|
Particle Size (µm) | 10-100 | 15-50 | 5-45 | 10-75 | 15-45 | 20-60 | 10-50 | 5-45 | 10-70 | 20-150 |
Purity (%) | 99.5 | 99.8 | 99.9 | 99.7 | 99.9 | 99.5 | 99.8 | 99.5 | 99.7 | 99.8 |
Tiêu chuẩn | ASTM B243 | ASTM B209 | ASTM B212 | ASTM A276 | ASTM B330 | ASTM F67 | ASTM B837 | ASTM B427 | ASTM B329 | ASTM B403 |
Suppliers and Pricing Details
Nhà cung cấp | Loại bột | Price (per kg) | Địa điểm |
---|---|---|---|
Höganäs AB | Iron, Stainless Steel, Bronze | $10 – $50 | Thụy Điển |
GKN Hoeganaes | Aluminum, Copper, Zinc | $15 – $60 | Hoa Kỳ |
Vật liệu bột và lớp phủ cải tiến | Nickel, Titanium, Cobalt | $20 – $80 | Canada |
Sandvik | Stainless Steel, Titanium | $25 – $100 | Thụy Điển |
Carpenter Technology | Iron, Nickel, Cobalt | $30 – $90 | Hoa Kỳ |
Arcam AB | Titanium, Aluminum | $35 – $120 | Thụy Điển |
Advantages and Limitations of Atomized Powders
Lợi ích | Hạn chế |
---|---|
High purity and consistency | Can be expensive |
Excellent mechanical properties | Limited availability of some metals |
Versatile applications | Handling and safety considerations |
Enhanced sintering and bonding | Potential environmental impact of production |
Customizable particle sizes | Specialized equipment required for production |
Comparison of Atomized Powders
Iron vs. Aluminum:
- Sắt offers high compressibility and magnetic properties, making it suitable for automotive and magnetic applications.
- Nhôm is lightweight with high thermal conductivity, perfect for aerospace and automotive sectors where weight reduction is crucial.
Copper vs. Stainless Steel:
- Đồng excels in electrical and thermal conductivity, ideal for electronics and conductive inks.
- Thép không gỉ provides corrosion resistance and high strength, making it suitable for additive manufacturing and biomedical implants.
Nickel vs. Titanium:
- Niken is favored for high-temperature and corrosion-resistant applications, crucial in aerospace and chemical industries.
- Titan stands out with its high strength-to-weight ratio and biocompatibility, essential for aerospace and medical applications.
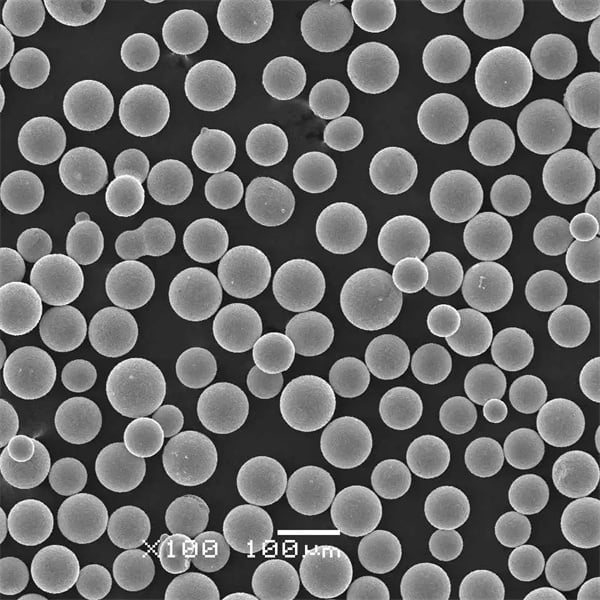
Câu hỏi thường gặp
Question | Answer |
---|---|
What is atomization in metal powders? | Atomization is a process where molten metal is dispersed into fine droplets and rapidly solidified to create metal powders with specific properties. |
What are the benefits of using atomized powders? | Benefits include uniform particle size distribution, high purity levels, enhanced sintering properties, and versatility in applications. |
Which industries use atomized powders? | Industries such as aerospace, automotive, electronics, biomedical, and additive manufacturing extensively use atomized powders. |
How are atomized powders produced? | They are produced by atomizing molten metal using gas, water, or centrifugal forces, resulting in fine, rapidly solidified droplets. |
What are some common types of atomized powders? | Common types include iron, aluminum, copper, stainless steel, nickel, titanium, cobalt, bronze, zinc, and magnesium powders. |
Why are particle size and purity important? | Particle size affects flowability and packing density, while purity ensures minimal contamination, both critical for high-performance applications. |
Can atomized powders be customized? | Yes, they can be tailored in terms of particle size, morphology, and composition to meet specific application requirements. |
What are the limitations of atomized powders? | Limitations include cost, limited availability of certain metals, handling and safety concerns, and potential environmental impact. |
Kết luận
Atomized powders represent a significant advancement in material science, offering unparalleled precision and performance for a multitude of applications. From the lightweight structures in aerospace to the biocompatible implants in medical fields, these powders are revolutionizing industries. By understanding their properties, applications, and specific models, we can better appreciate their role in today’s technological advancements.
About 3DP mETAL
Product Category
LIÊN HỆ
Bạn có thắc mắc không? Hãy gửi tin nhắn ngay cho chúng tôi! Sau khi nhận được tin nhắn của bạn, chúng tôi sẽ xử lý yêu cầu của bạn với cả một đội ngũ.