Depowdering systems are a critical component in additive manufacturing, especially in processes involving metal powders. These systems ensure that excess powder is efficiently removed from printed parts, improving both the quality and consistency of the final product. In this comprehensive guide, we will delve into the various aspects of depowdering systems, including their types, composition, characteristics, applications, and more. Whether you’re new to the concept or looking to deepen your understanding, this article will provide you with the insights you need.
Overview of Depowdering Systems
Depowdering systems play a vital role in the post-processing of 3D printed parts. They ensure that any residual powder left on the parts after printing is removed, which is crucial for both the functionality and appearance of the final product. These systems are particularly important in industries like aerospace, medical, and automotive, where precision and cleanliness are paramount.
Key Details
- Function: Removal of excess powder from 3D printed parts
- Importance: Enhances quality, consistency, and performance of printed parts
- Industries: Aerospace, medical, automotive, and more
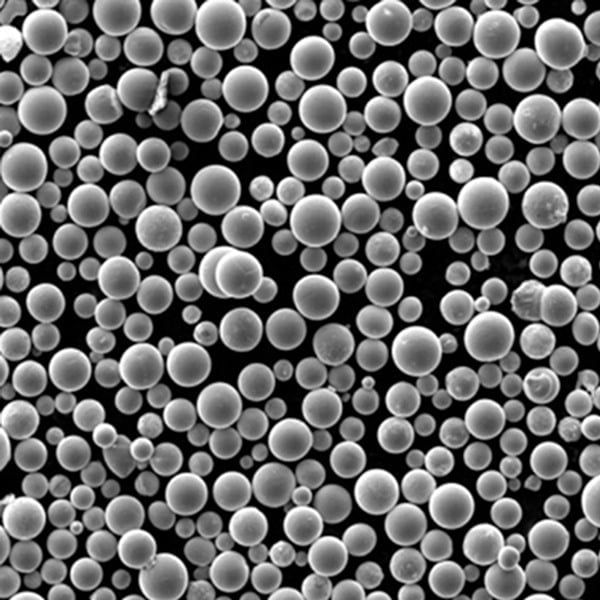
Types and Composition of Depowdering Systems
Depowdering systems can be categorized based on their method of operation and the type of powder they handle. Here, we will explore different models and their specific compositions.
Type | Mô hình | Sáng tác | Miêu tả |
---|---|---|---|
Vibratory Systems | XYZ-100 | Stainless steel, elastomers | Uses vibrations to shake off excess powder. Suitable for larger parts and coarse powders. |
Air Blast Systems | AB-200 | Aluminum, nylon nozzles | Utilizes compressed air to blow off powder. Ideal for fine powders and complex geometries. |
Ultrasonic Systems | US-300 | Titanium, ceramic transducers | Employs ultrasonic waves to dislodge powder. Effective for intricate and delicate parts. |
Fluidized Bed | FB-400 | Polypropylene, air pumps | Involves a fluidized bed of air and powder that gently removes excess material. Great for uniform depowdering of small to medium-sized parts. |
Manual Systems | MS-500 | Mixed materials | Requires manual brushing or air blasting. Best for small-scale operations or delicate parts requiring a personal touch. |
Robotic Systems | RS-600 | Robotics, sensors | Automated robotic arms perform the depowdering process. Highly efficient for large-scale production. |
Vacuum Systems | VS-700 | High-power vacuums | Uses vacuum suction to remove powder. Suitable for both fine and coarse powders, and versatile for various part sizes. |
Wet Cleaning | WC-800 | Stainless steel, water jets | Combines water jets and solvents to clean parts. Effective for removing stubborn powders and residues. |
Magnetic Systems | MAG-900 | Rare-earth magnets, steel | Employs magnetic fields to attract and remove ferromagnetic powders. Useful in specific applications requiring such properties. |
Hybrid Systems | HYB-1000 | Combination of above methods | Integrates multiple depowdering techniques into one system. Offers flexibility and efficiency in handling different types of powders and part complexities. |
Characteristics of Depowdering Systems
Depowdering systems vary widely in their characteristics, which influence their suitability for different applications. Here are some key characteristics to consider.
Đặc điểm | Miêu tả |
---|---|
Efficiency | How quickly and thoroughly the system removes powder. |
Part Compatibility | The range of part sizes and geometries the system can handle. |
Loại bột | Compatibility with different powder types (e.g., fine, coarse, ferromagnetic). |
Automation Level | Degree of automation, from manual to fully robotic systems. |
Chi phí | Initial investment and operational costs associated with the system. |
Maintenance | Ease of maintenance and frequency of required upkeep. |
Safety Features | Measures in place to protect operators and ensure safe operation, especially with hazardous powders. |
Environmental Impact | Considerations regarding the system’s energy consumption and waste management. |
Applications of Depowdering Systems
Depowdering systems find applications across various industries. Let’s explore some of the common uses and the benefits they bring.
Ngành | Ứng dụng | Lợi ích |
---|---|---|
Hiệp công | Component manufacturing, prototyping | Ensures high precision and cleanliness of critical parts. |
Y học | Implants, surgical tools | Guarantees sterility and functionality of medical devices. |
Ô tô | Engine components, custom parts | Enhances performance and aesthetic quality of automotive parts. |
Hàng hóa tiêu dùng | Electronics, fashion accessories | Improves product appearance and tactile quality. |
Công nghiệp | Tooling, machinery parts | Increases durability and operational efficiency of industrial tools. |
Năng lượng | Turbines, solar panel components | Boosts performance and reliability of energy devices. |
Quốc phòng | Weapon components, tactical gear | Ensures reliability and safety of defense equipment. |
Education & R&D | Prototyping, experimental setups | Facilitates innovation and accurate testing. |
Art & Design | Sculptures, intricate designs | Allows for high-detail finishing and creativity. |
Custom Manufacturing | Bespoke parts for various industries | Provides flexibility and precision for custom manufacturing. |
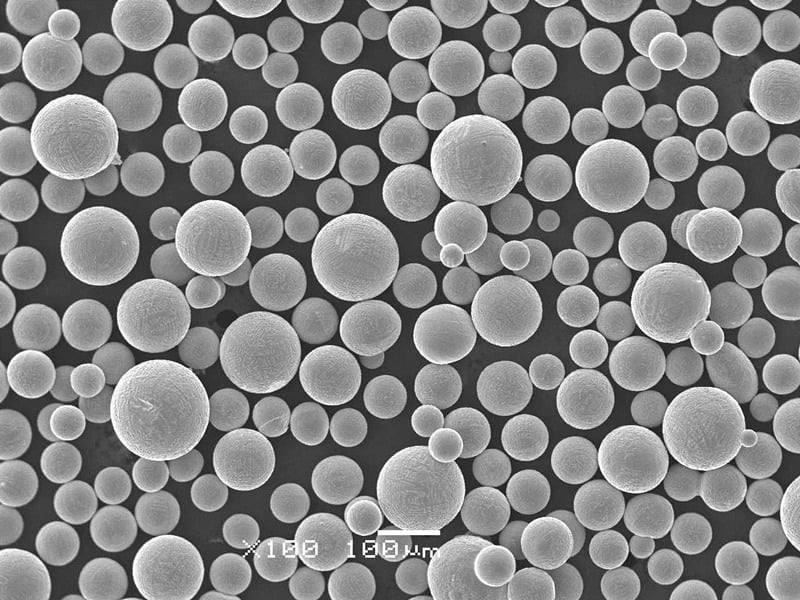
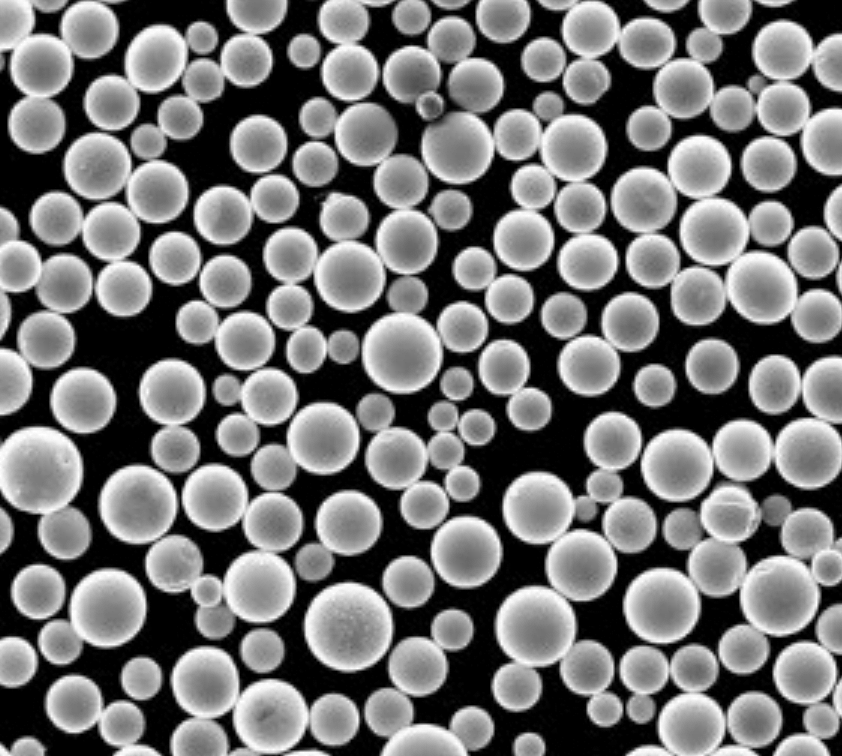
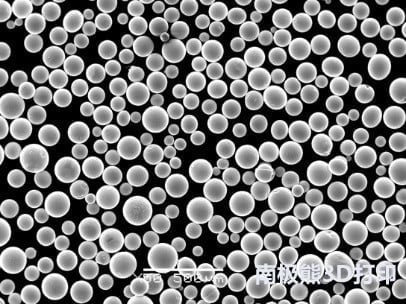
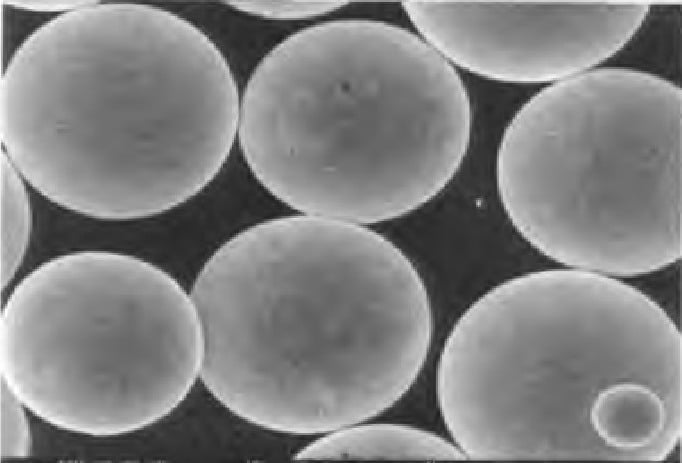
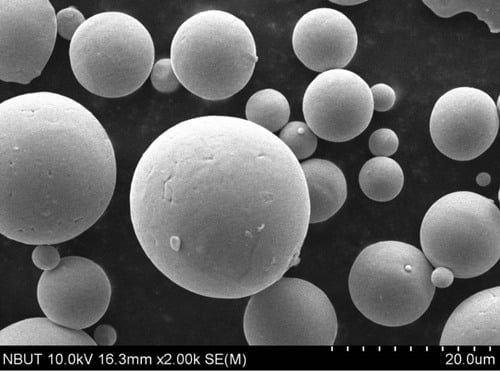
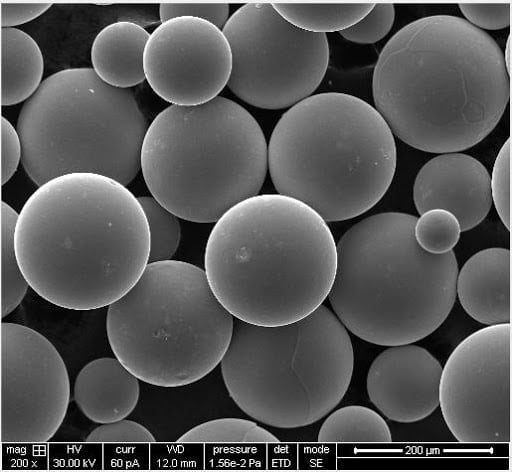
Specifications, Sizes, Grades, and Standards
When selecting a depowdering system, it’s important to consider the specific requirements for your application. Here are some key specifications, sizes, grades, and standards to keep in mind.
Đặc điểm kỹ thuật | Detail |
---|---|
Phạm vi kích thước | Systems can handle parts from a few millimeters to several meters in size. |
Lớp | Industrial, commercial, medical, aerospace grades available, depending on the system and application. |
Tiêu chuẩn | Compliance with industry standards like ISO, ASTM, and specific regulatory requirements. |
Power Requirements | Varies from low-power manual systems to high-power automated systems. |
Material Compatibility | Capable of handling different materials including metals, polymers, and composites. |
Operational Environment | Suitable for clean rooms, industrial settings, and specialized environments. |
Suppliers and Pricing Details
Choosing the right supplier is crucial for obtaining a reliable depowdering system. Here are some top suppliers and an overview of their pricing.
Nhà cung cấp | Mô hình | Mức giá | Contact Details |
---|---|---|---|
Supplier A | XYZ-100 | $10,000 – $20,000 | [email protected] |
Supplier B | AB-200 | $15,000 – $25,000 | [email protected] |
Supplier C | US-300 | $20,000 – $30,000 | [email protected] |
Supplier D | FB-400 | $12,000 – $22,000 | [email protected] |
Supplier E | MS-500 | $8,000 – $18,000 | [email protected] |
Supplier F | RS-600 | $25,000 – $40,000 | [email protected] |
Supplier G | VS-700 | $10,000 – $20,000 | [email protected] |
Supplier H | WC-800 | $15,000 – $25,000 | [email protected] |
Supplier I | MAG-900 | $10,000 – $20,000 | [email protected] |
Supplier J | HYB-1000 | $30,000 – $50,000 | [email protected] |
Pros and Cons of Different Depowdering Systems
Each type of depowdering system has its own advantages and limitations. Understanding these can help you choose the best system for your needs.
Type | Lợi ích | Hạn chế |
---|---|---|
Vibratory Systems | Effective for large parts, relatively simple setup | May not be suitable for fine powders, can cause part damage if not carefully controlled |
Air Blast Systems | Excellent for fine powders and complex geometries | Requires high-power air supply, can be noisy |
Ultrasonic Systems | Gentle on delicate parts, effective for intricate designs | Can be expensive, may require special fluids or cleaning solutions |
Fluidized Bed | Uniform cleaning, gentle process | Limited to certain part sizes, setup can be complex |
Manual Systems | Low cost, flexible for small operations | Labor-intensive, not suitable for large-scale production |
Robotic Systems | High efficiency, consistent results | High initial cost, requires technical expertise for setup and maintenance |
Vacuum Systems | Versatile for different powders and part sizes | Can be less effective on very fine powders, requires regular maintenance |
Wet Cleaning | Effective for stubborn residues, thorough cleaning | Requires drying process, potential for water contamination |
Magnetic Systems | Excellent for ferromagnetic powders, non-contact process | Limited to specific powder types, may not be versatile for other materials |
Hybrid Systems | Combines benefits of multiple methods, highly flexible | Complex setup and maintenance, higher cost |
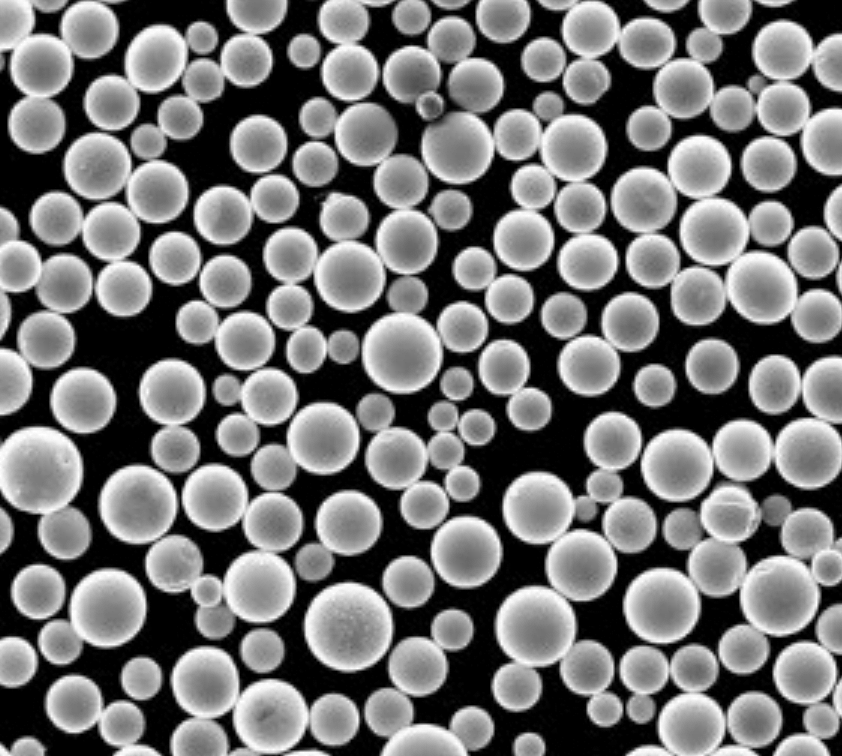
Câu hỏi thường gặp
Here are some frequently asked questions about depowdering systems to help you understand more about these essential tools.
Question | Answer |
---|---|
What is a depowdering system? | A machine or process that removes excess powder from 3D printed parts. |
Why is depowdering important? | It ensures the quality, functionality, and appearance of the final product. |
What types of depowdering systems are there? | Various types include vibratory, air blast, ultrasonic, fluidized bed, manual, robotic, vacuum, and more. |
Which industries use depowdering systems? | Aerospace, medical, automotive, consumer goods, industrial, energy, defense, and more. |
How do I choose the right depowdering system? | Consider factors like part size, powder type, automation level, cost, and specific application needs. |
Are depowdering systems expensive? | Prices vary widely based on the type and complexity, ranging from $8,000 to $50,000 or more. |
Can depowdering systems handle all powder types? | Some systems are specialized for certain powder types; hybrid systems can handle multiple types. |
What are the maintenance requirements? | Varies by system; some require regular cleaning and part replacement, while others need minimal maintenance. |
Are there any safety concerns? | Yes, systems should have safety features to protect operators, especially when handling hazardous powders. |
Where can I buy a depowdering system? | From specialized suppliers, manufacturers, and online industrial equipment vendors. |
Depowdering systems are an essential part of the additive manufacturing process, ensuring that printed parts are free from excess powder and meet the necessary quality standards. By understanding the various types, characteristics, applications, and suppliers, you can make an informed decision on the best depowdering system for your needs. With the right system in place, you can achieve superior results in your 3D printing projects, enhancing both the functionality and aesthetics of your products.
About 3DP mETAL
Product Category
LIÊN HỆ
Bạn có thắc mắc không? Hãy gửi tin nhắn ngay cho chúng tôi! Sau khi nhận được tin nhắn của bạn, chúng tôi sẽ xử lý yêu cầu của bạn với cả một đội ngũ.