Dual-phase alloy powders are revolutionizing the material science industry with their unique properties and diverse applications. This guide provides an in-depth look at what makes these powders special, their compositions, characteristics, uses, and much more. Whether you’re an engineer, a researcher, or just curious about advanced materials, this guide has something for you.
Overview of Dual-Phase Alloy Powder
Dual-phase alloy powders consist of two distinct phases within their microstructure, typically combining a soft phase with a hard phase to create a material that benefits from the strengths of both. These powders are engineered to provide exceptional mechanical properties, including high strength, ductility, and toughness. They are used in various industries, from aerospace to automotive, due to their versatile applications.
Key Points:
- Sáng tác: Typically a combination of two metal phases.
- thuộc tính: High strength, good ductility, wear resistance.
- ỨNG DỤNG: Aerospace, automotive, industrial tooling, and more.
- Lợi ích: Combines the best properties of different metals.
- Những thách thức: Complex manufacturing process, higher cost.
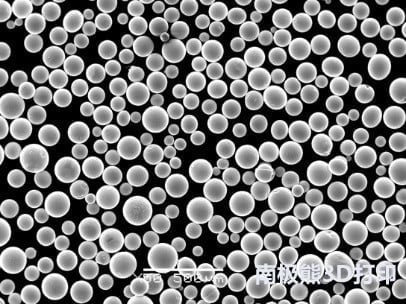
Types of Dual-Phase Alloy Powder
Type | Sáng tác | thuộc tính | ỨNG DỤNG | Suppliers |
---|---|---|---|---|
DP-Steel Powder | Iron, Carbon, Manganese, Silicon | High strength, good ductility | Automotive components, structural parts | Höganäs, GKN Powder |
Aluminum-Silicon Powder | Aluminum, Silicon | Lightweight, corrosion resistance | Hàng không, Ô tô | ECKA Granules, Valimet |
Copper-Nickel Powder | Copper, Nickel | Good electrical conductivity | Electrical contacts, marine applications | American Elements, Vale |
Titanium-Aluminum Powder | Titanium, Aluminum | Tỷ lệ độ bền/trọng lượng cao | Aerospace, medical implants | AP&C, TLS Technik |
Nickel-Titanium Powder | Nickel, Titanium | Shape memory, superelasticity | Medical devices, actuators | Fort Wayne Metals, SAES |
Cobalt-Chromium Powder | Cobalt, Chromium | Wear resistance, biocompatibility | Dental implants, cutting tools | ATI Powder Metals, Kennametal |
Tungsten-Carbide Powder | Tungsten, Carbon | Extreme hardness, wear resistance | Cutting tools, mining equipment | H.C. Starck, Sandvik |
Iron-Nickel Powder | Iron, Nickel | Magnetic properties, strength | Electronics, aerospace | Carpenter Technology, CRS Holdings |
Stainless Steel Powder | Iron, Chromium, Nickel | Corrosion resistance, strength | Medical devices, automotive components | Sandvik, Carpenter Technology |
Magnesium-Aluminum Powder | Magnesium, Aluminum | Lightweight, high strength | Aerospace, automotive, sports equipment | ECKA Granules, Tekna |
Composition of Dual-Phase Alloy Powder
The composition of dual-phase alloy powders is critical to their performance. Each metal in the alloy contributes specific properties that enhance the overall material. Understanding these compositions can help in selecting the right powder for your application.
Key Compositions:
- DP-Steel Powder: Composed of iron with carbon, manganese, and silicon to enhance strength and ductility.
- Aluminum-Silicon Powder: Combines lightweight aluminum with silicon to improve corrosion resistance.
- Copper-Nickel Powder: Utilizes the electrical conductivity of copper and the strength of nickel.
- Titanium-Aluminum Powder: Provides a high strength-to-weight ratio, ideal for aerospace applications.
- Nickel-Titanium Powder: Known for its shape memory and superelastic properties, used in medical devices.
Composition Table:
Type | Primary Elements | Additional Elements | Phase Distribution |
---|---|---|---|
DP-Steel Powder | Fe, C | Mn, Si | Martensite in a ferrite matrix |
Aluminum-Silicon Powder | Al | Có | Silicon dispersed in aluminum matrix |
Copper-Nickel Powder | Đồng | Đúng | Homogeneous mixture |
Titanium-Aluminum Powder | Ti | Al | Intermetallic phases |
Nickel-Titanium Powder | Đúng | Ti | Austenite and martensite phases |
Cobalt-Chromium Powder | Co | Cr | Solid solution |
Tungsten-Carbide Powder | W | I can help with that! However, the text "C" doesn't provide enough context for an accurate translation. Could you please provide more information or context so that I can assist you better? | Carbide particles in a metal matrix |
Iron-Nickel Powder | Sắt | Đúng | Ferrite with nickel-rich precipitates |
Stainless Steel Powder | Fe, Cr | Ni, Mo | Austenitic or martensitic structure |
Magnesium-Aluminum Powder | Mg | Al | Magnesium matrix with Al particles |
Characteristics of Dual-Phase Alloy Powder
Understanding the characteristics of dual-phase alloy powders is essential for their effective application. These powders exhibit a combination of properties that make them unique compared to single-phase alloys.
Key Characteristics:
- Sức mạnh: High tensile and compressive strength due to the combination of hard and soft phases.
- Độ dẻo dai: Enhanced ductility allowing for better formability and machining.
- Khả năng chống mài mòn: Improved wear resistance, making them suitable for high-stress applications.
- Khả năng chống ăn mòn: Certain compositions offer excellent corrosion resistance, ideal for harsh environments.
- Tính ổn định nhiệt: Good thermal stability, maintaining properties at high temperatures.
Characteristics Table:
Type | Strength (MPa) | Ductility (%) | Khả năng chống mài mòn | Khả năng chống ăn mòn | Thermal Stability (°C) |
---|---|---|---|---|---|
DP-Steel Powder | 600-1200 | 10-20 | Vừa đủ | Thấp | 250-350 |
Aluminum-Silicon Powder | 300-500 | 10-15 | Thấp | Cao | 400-600 |
Copper-Nickel Powder | 200-400 | 20-30 | Thấp | Vừa đủ | 300-500 |
Titanium-Aluminum Powder | 800-1100 | 5-10 | Vừa đủ | Cao | 600-800 |
Nickel-Titanium Powder | 500-800 | 8-12 | Vừa đủ | Cao | 300-500 |
Cobalt-Chromium Powder | 700-1000 | 5-15 | Cao | Cao | 600-900 |
Tungsten-Carbide Powder | 1500-2000 | 1-5 | Rất cao | Thấp | 900-1200 |
Iron-Nickel Powder | 600-800 | 15-25 | Thấp | Vừa đủ | 200-400 |
Stainless Steel Powder | 500-900 | 20-30 | Cao | Rất cao | 500-700 |
Magnesium-Aluminum Powder | 200-400 | 10-20 | Thấp | Vừa đủ | 300-500 |
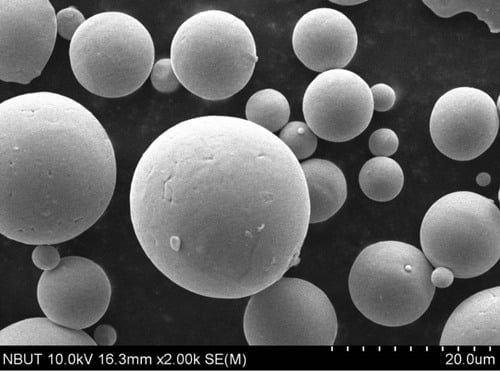
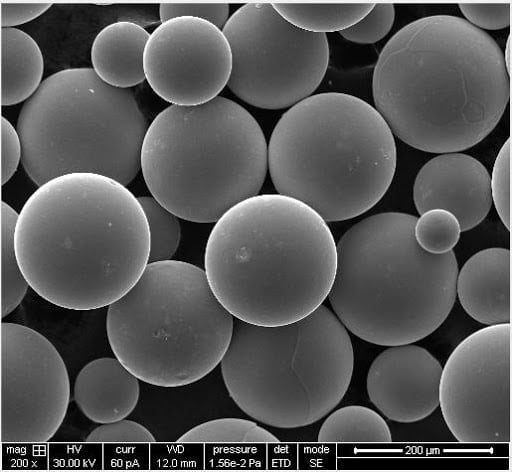
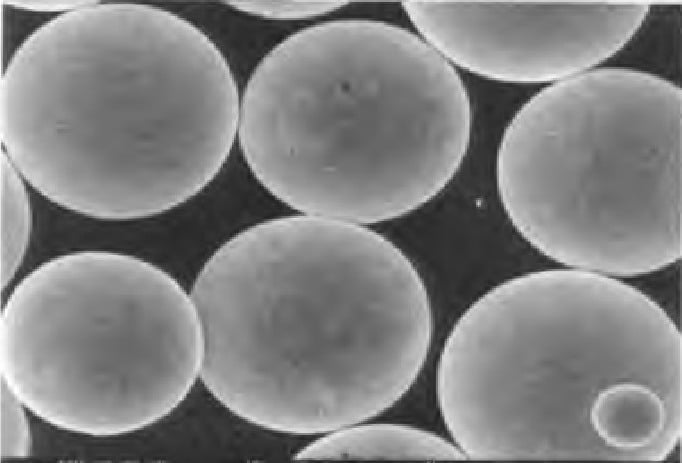
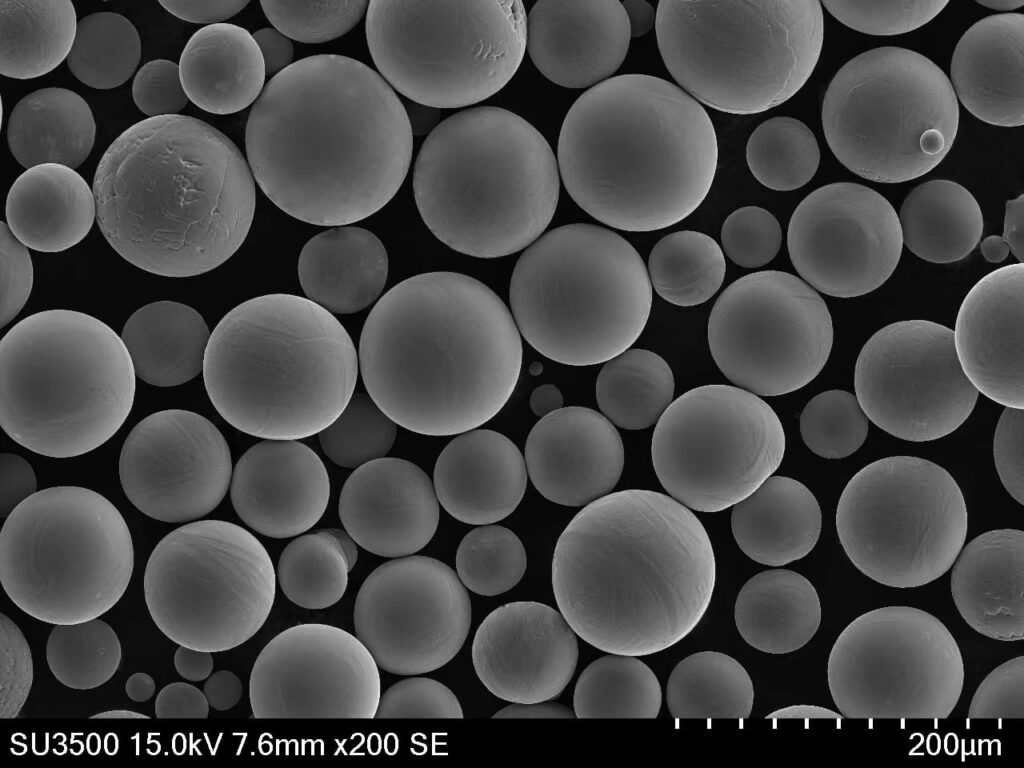
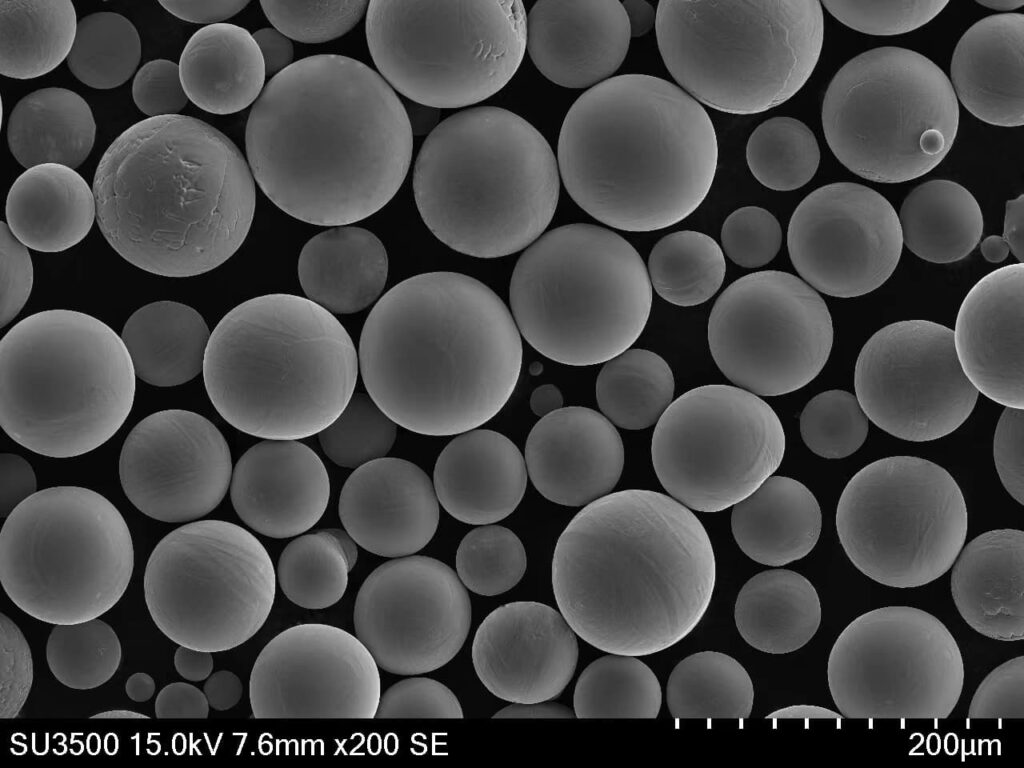
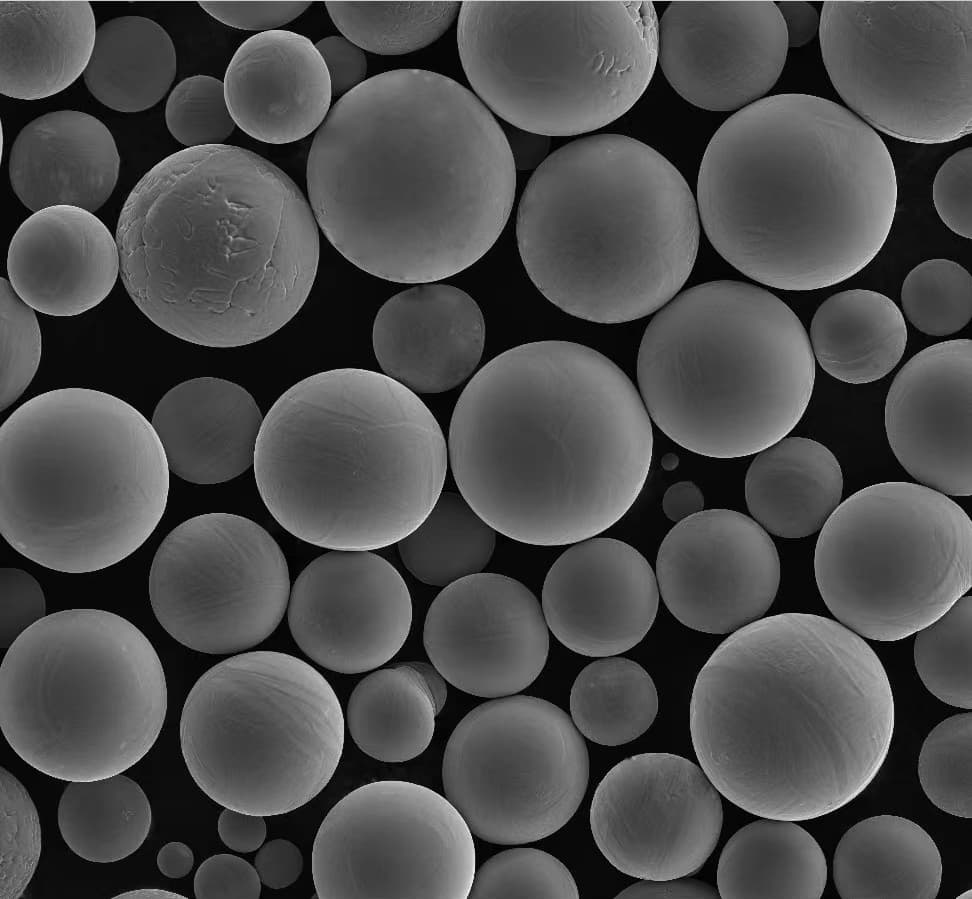
Applications of Dual-Phase Alloy Powder
Dual-phase alloy powders find applications across various industries due to their versatile properties. From automotive to aerospace, these materials are indispensable in modern manufacturing.
Application Table:
Ngành | ỨNG DỤNG | Lợi ích |
---|---|---|
Ô tô | Engine components, structural parts | High strength, good ductility |
Hiệp công | Aircraft parts, turbine blades | Lightweight, high strength-to-weight ratio |
Y học | Implants, surgical instruments | Biocompatibility, corrosion resistance |
Industrial Tooling | Công cụ cắt, khuôn, khuôn đúc | Wear resistance, hardness |
Điện tử | Connectors, magnetic components | Electrical conductivity, magnetic properties |
Thủy quân lục chiến | Shipbuilding, offshore structures | Corrosion resistance, durability |
Sports Equipment | Bicycle frames, golf clubs | Lightweight, high strength |
Năng lượng | Power plant components, wind turbine parts | Thermal stability, corrosion resistance |
Xây dựng | Reinforcement bars, fasteners | Strength, durability |
Hàng hóa tiêu dùng | Watches, jewelry, eyeglass frames | Aesthetics, corrosion resistance |
Specifications, Sizes, Grades, and Standards
When selecting dual-phase alloy powders, it’s essential to consider the specifications, sizes, grades, and standards to ensure the material meets your application requirements.
Specifications Table:
Type | Sizes (µm) | Grades | Tiêu chuẩn |
---|---|---|---|
DP-Steel Powder | 10-100 | AISI 1010, 1020 | ASTM A108, ISO 683-17 |
Aluminum-Silicon Powder | 5-50 | 4047, 6061 | ASTM B209, ISO 6361 |
Copper-Nickel Powder | 20-100 | C70600, C71500 | ASTM B122, ISO 6283 |
Titanium-Aluminum Powder | 10-70 | Ti-6Al-4V, Ti-6Al-2Sn-4Zr-6Mo | ASTM B348, ISO 5832-3 |
Nickel-Titanium Powder | 15-90 | Nitinol 55, Nitinol 60 | ASTM F2063, ISO 5832-7 |
Cobalt-Chromium Powder | 10-80 | CoCrMo, CoCrW | ASTM F75, ISO 5832-4 |
Tungsten-Carbide Powder | 1-10 | WC-Co, WC-Ni | ASTM B777, ISO 4489 |
Iron-Nickel Powder | 20-150 | Invar 36, FeNi42 | ASTM F1684, ISO 8320 |
Stainless Steel Powder | 10-100 | 304L, 316L | ASTM A276, ISO 683-13 |
Magnesium-Aluminum Powder | 5-50 | AZ91D, AM60 | ASTM B93, ISO 16220 |
Suppliers and Pricing Details
Choosing the right supplier is crucial for obtaining high-quality dual-phase alloy powders. Pricing can vary based on the type of alloy, quantity, and supplier.
Suppliers and Pricing Table:
Nhà cung cấp | Type | Price (per kg) | Địa điểm | Notes |
---|---|---|---|---|
Höganäs | DP-Steel Powder | $10-20 | Thụy Điển | Large volume discounts |
Viên nén ECKA | Aluminum-Silicon Powder | $15-25 | Đức | High purity grades available |
American Elements | Copper-Nickel Powder | $30-40 | Hoa Kỳ | Custom compositions offered |
AP&C | Titanium-Aluminum Powder | $200-300 | Canada | Aerospace-grade powders |
Fort Wayne Metals | Nickel-Titanium Powder | $400-600 | Hoa Kỳ | Medical-grade standards |
ATI Powder Metals | Cobalt-Chromium Powder | $50-70 | Hoa Kỳ | High wear resistance |
H.C. Starck | Tungsten-Carbide Powder | $100-150 | Đức | Extreme hardness |
Carpenter Technology | Iron-Nickel Powder | $20-30 | Hoa Kỳ | Magnetic properties |
Sandvik | Stainless Steel Powder | $30-50 | Thụy Điển | Various stainless steel grades |
Tekna | Magnesium-Aluminum Powder | $25-35 | Canada | Lightweight applications |
Advantages and Limitations of Dual-Phase Alloy Powder
Every material has its pros and cons. Understanding the advantages and limitations of dual-phase alloy powders helps in making informed decisions for specific applications.
Advantages:
- High Strength and Ductility: Combining hard and soft phases results in materials with high tensile strength and good ductility.
- Khả năng chống mài mòn: Enhanced wear resistance due to the hard phase.
- Khả năng chống ăn mòn: Certain compositions provide excellent corrosion resistance.
- Tính ổn định nhiệt: Maintains properties at high temperatures.
- Versatility: Can be tailored for specific applications by adjusting composition.
Limitations:
- Chi phí: More expensive than single-phase alloys due to complex manufacturing processes.
- Manufacturing Challenges: Requires precise control over composition and processing conditions.
- Tính sẵn có: Limited availability for some specialized compositions.
- Compatibility Issues: May not be compatible with all manufacturing processes or environments.
- Complexity: More complex to work with, requiring specialized knowledge and equipment.
Advantages and Limitations Table:
Type | Lợi ích | Hạn chế |
---|---|---|
DP-Steel Powder | High strength, good ductility | Moderate corrosion resistance |
Aluminum-Silicon Powder | Lightweight, corrosion resistance | Lower strength compared to some alloys |
Copper-Nickel Powder | Good electrical conductivity | Higher cost, lower wear resistance |
Titanium-Aluminum Powder | Tỷ lệ độ bền/trọng lượng cao | Expensive, difficult to machine |
Nickel-Titanium Powder | Shape memory, superelasticity | Very expensive, limited availability |
Cobalt-Chromium Powder | Wear resistance, biocompatibility | High cost, difficult to process |
Tungsten-Carbide Powder | Extreme hardness, wear resistance | Very high cost, brittleness |
Iron-Nickel Powder | Magnetic properties, strength | Moderate corrosion resistance |
Stainless Steel Powder | Corrosion resistance, strength | Higher cost than regular steel |
Magnesium-Aluminum Powder | Lightweight, high strength | Lower wear resistance, more expensive than pure Mg |
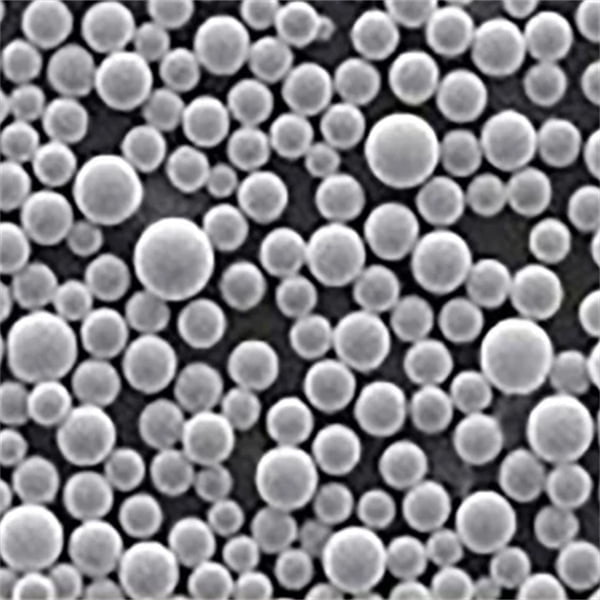
Detailed Analysis of Specific Metal Powder Models
Let’s dive deeper into specific metal powder models, their unique properties, and their applications.
1. DP-Steel Powder
DP-steel powder, also known as dual-phase steel, typically contains iron, carbon, manganese, and silicon. The microstructure consists of martensite dispersed in a ferrite matrix, providing a balance of high strength and good ductility. It’s widely used in the automotive industry for components like structural parts and engine components due to its excellent mechanical properties.
2. Aluminum-Silicon Powder
Aluminum-silicon powders combine the lightweight nature of aluminum with the enhanced corrosion resistance provided by silicon. These powders are ideal for applications in the aerospace and automotive industries where weight reduction is critical. The addition of silicon improves the casting properties and mechanical strength of the alloy.
3. Copper-Nickel Powder
Copper-nickel powders are known for their excellent electrical conductivity and strength. These powders are commonly used in electrical and marine applications due to their resistance to corrosion, particularly in seawater environments. They are also used in coinage and various industrial applications.
4. Titanium-Aluminum Powder
Titanium-aluminum powders, such as Ti-6Al-4V, offer a high strength-to-weight ratio, making them ideal for aerospace and biomedical applications. These powders are used in the production of aircraft parts, turbine blades, and medical implants. The alloy’s ability to withstand high temperatures and its biocompatibility make it highly valuable in these industries.
5. Nickel-Titanium Powder
Nickel-titanium powders, commonly known as Nitinol, exhibit unique properties such as shape memory and superelasticity. These characteristics make them ideal for medical devices, such as stents and guidewires, as well as actuators and sensors. The alloy can return to its original shape after deformation when exposed to heat.
6. Cobalt-Chromium Powder
Cobalt-chromium powders are known for their excellent wear resistance and biocompatibility. They are commonly used in dental and orthopedic implants, as well as in the production of cutting tools. The alloy’s ability to maintain hardness at high temperatures makes it suitable for demanding industrial applications.
7. Tungsten-Carbide Powder
Tungsten-carbide powders are among the hardest materials available, offering exceptional wear resistance. These powders are used in cutting tools, mining equipment, and wear-resistant coatings. The high hardness and strength make tungsten-carbide ideal for applications requiring extreme durability.
8. Iron-Nickel Powder
Iron-nickel powders, such as Invar 36, are known for their low coefficient of thermal expansion and good mechanical properties. They are used in applications requiring dimensional stability, such as precision instruments, aerospace components, and electronics.
9. Stainless Steel Powder
Stainless steel powders, including grades like 304L and 316L, offer excellent corrosion resistance and strength. These powders are used in a wide range of applications, from medical devices and automotive components to consumer goods like watches and eyeglass frames.
10. Magnesium-Aluminum Powder
Magnesium-aluminum powders combine the lightweight properties of magnesium with the strength of aluminum. These powders are used in aerospace, automotive, and sports equipment applications where weight reduction is crucial. The alloy offers a good balance of strength and ductility.
Câu hỏi thường gặp
What are dual-phase alloy powders?
Dual-phase alloy powders are materials composed of two distinct metal phases, typically combining a soft phase with a hard phase to create a material with enhanced mechanical properties, such as high strength and ductility.
What are the advantages of using dual-phase alloy powders?
Dual-phase alloy powders offer several advantages, including high strength, good ductility, wear resistance, corrosion resistance, and thermal stability. They can be tailored for specific applications by adjusting their composition.
Where are dual-phase alloy powders commonly used?
These powders are used in various industries, including automotive, aerospace, medical, industrial tooling, electronics, marine, sports equipment, energy, construction, and consumer goods.
How are dual-phase alloy powders manufactured?
The manufacturing process for dual-phase alloy powders involves precise control over the composition and processing conditions. Techniques such as atomization, mechanical alloying, and thermal spraying are commonly used.
What are some common types of dual-phase alloy powders?
Some common types include DP-steel powder, aluminum-silicon powder, copper-nickel powder, titanium-aluminum powder, nickel-titanium powder, cobalt-chromium powder, tungsten-carbide powder, iron-nickel powder, stainless steel powder, and magnesium-aluminum.
About 3DP mETAL
Product Category
LIÊN HỆ
Bạn có thắc mắc không? Hãy gửi tin nhắn ngay cho chúng tôi! Sau khi nhận được tin nhắn của bạn, chúng tôi sẽ xử lý yêu cầu của bạn với cả một đội ngũ.