Overview of Electrode Inert Gas Atomisers
Electrode inert gas atomisers are a critical component in the world of metal powder production, playing a pivotal role in industries ranging from aerospace to additive manufacturing. These sophisticated devices enable the creation of fine metal powders with high precision and consistency, making them indispensable in modern material science and manufacturing processes.
But what exactly are electrode inert gas atomisers, and why are they so important? To answer that, we need to delve into the technology behind them, their applications, and the various types of metal powders they produce. This article will provide an in-depth exploration of electrode inert gas atomisers, from their basic principles to their role in cutting-edge industries, and everything in between.
Understanding Electrode Inert Gas Atomisers
What Are Electrode Inert Gas Atomisers?
Electrode inert gas atomisers are advanced systems designed to produce metal powders through a process known as gas atomisation. The term “inert gas” refers to the use of gases such as argon or nitrogen, which do not react with the metal during the atomisation process. This ensures that the resulting metal powder is free from unwanted chemical reactions, maintaining its purity and consistency.
The core of an electrode inert gas atomiser consists of a metal electrode, which is heated to a molten state. Once the metal reaches the desired temperature, it is subjected to a high-pressure stream of inert gas. This stream breaks the molten metal into fine droplets, which solidify into powder as they cool.
This technology is widely used for producing metal powders with precise particle size distributions and high purity levels. These powders are essential in various industries, including aerospace, automotive, and electronics, where material quality is paramount.
How Do Electrode Inert Gas Atomisers Work?
The operation of an electrode inert gas atomiser can be broken down into several key steps:
- Melting the Metal: The process begins with heating the metal electrode until it becomes molten. The choice of metal and the temperature are crucial factors that influence the quality of the final powder.
- Atomisation: Once the metal is molten, it is subjected to a high-velocity stream of inert gas. This gas stream breaks the molten metal into fine droplets. The size of these droplets can be controlled by adjusting the gas pressure and the flow rate.
- Solidification: As the droplets are dispersed in the gas stream, they quickly solidify into fine metal powders. The inert gas ensures that the metal does not react with the environment, preserving its purity.
- Collection: The solidified metal powder is then collected in a chamber, where it is further processed and classified based on particle size and other properties.
The entire process is highly controlled, allowing manufacturers to produce metal powders with specific characteristics, such as particle size distribution, flowability, and density.
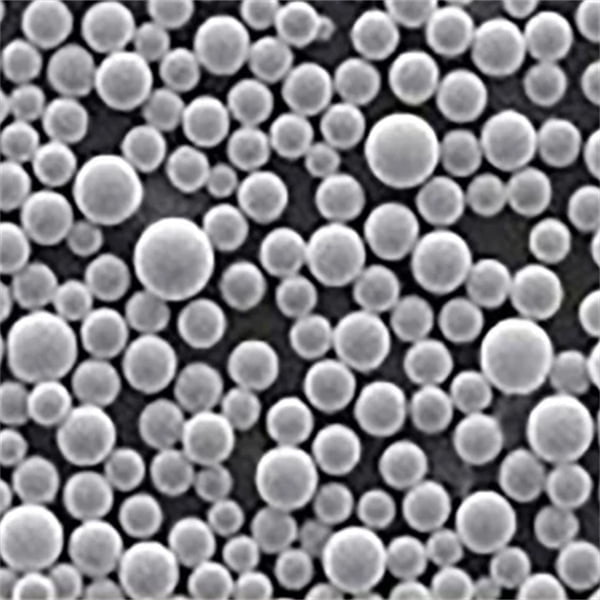
Composition of Electrode Inert Gas Atomisers
Materials Used in Construction
The construction of electrode inert gas atomisers involves the use of various high-performance materials. These materials are selected based on their ability to withstand extreme temperatures, resist corrosion, and maintain structural integrity under high-stress conditions.
- Stainless Steel: Commonly used for the body and internal components of the atomiser due to its excellent corrosion resistance and high strength.
- Copper Alloys: Often used for electrodes because of their superior electrical conductivity and resistance to thermal fatigue.
- Ceramics: Employed in certain parts of the atomiser that are exposed to very high temperatures, providing insulation and durability.
Electrode Composition
The electrode is a critical component of the atomiser, as it directly influences the quality of the metal powder produced. The choice of electrode material depends on the type of metal being atomised and the desired properties of the final powder.
- Tungsten Electrodes: Used for atomising high-melting-point metals like titanium and tungsten. Tungsten electrodes offer excellent thermal stability and resistance to melting.
- Graphite Electrodes: Suitable for atomising non-ferrous metals like aluminium and copper. Graphite electrodes are favored for their ability to withstand thermal shock and their non-reactivity with most metals.
Characteristics of Electrode Inert Gas Atomisers
Physical and Chemical Properties
Electrode inert gas atomisers are designed to operate under extreme conditions, and their physical and chemical properties are critical to their performance:
- Temperature Resistance: The materials used in the atomiser must withstand the high temperatures required to melt metals like titanium and stainless steel.
- Corrosion Resistance: The atomiser’s components must resist corrosion from the molten metal and the inert gas, ensuring longevity and consistent performance.
- Electrical Conductivity: The electrodes must have high electrical conductivity to efficiently heat the metal and maintain a stable melting process.
Performance Characteristics
The performance of an electrode inert gas atomiser is measured by several key factors:
- Efficiency in Powder Production: The atomiser must produce metal powders with minimal waste and maximum yield.
- Particle Size Distribution: The ability to control the particle size distribution is crucial for producing powders that meet specific industrial requirements.
- Consistency: The atomiser must produce metal powders with consistent properties, batch after batch, ensuring reliability in downstream applications.
Types of Metal Powders Produced by Electrode Inert Gas Atomisers
Specific Metal Powder Models
Electrode inert gas atomisers are capable of producing a wide range of metal powders, each with unique properties and applications. Below are ten specific metal powder models commonly produced by this technology:
- Stainless Steel Powder (316L)
- Description: A highly corrosion-resistant powder used in marine and chemical environments. It offers excellent mechanical properties and is suitable for 3D printing and sintering applications.
- Applications: Aerospace components, medical devices, chemical processing equipment.
- Titanium Powder (Ti-6Al-4V)
- Description: A lightweight, high-strength powder known for its biocompatibility. It is widely used in the medical and aerospace industries.
- Applications: Medical implants, aerospace parts, high-performance sporting goods.
- Aluminium Powder (AlSi10Mg)
- Description: A powder with good strength-to-weight ratio and excellent thermal conductivity. It is commonly used in lightweight structures and heat exchangers.
- Applications: Automotive parts, heat sinks, lightweight structural components.
- Copper Powder (Cu)
- Description: A highly conductive powder used in electrical and thermal applications. It offers excellent corrosion resistance and malleability.
- Applications: Electrical components, heat exchangers, conductive inks.
- Nickel-Based Powder (Inconel 718)
- Description: A high-strength, corrosion-resistant powder suitable for extreme environments. It retains its properties at high temperatures, making it ideal for aerospace and energy applications.
- Applications: Turbine blades, exhaust systems, high-temperature fasteners.
- Cobalt-Based Powder (CoCrMo)
- Description: Known for its wear resistance and biocompatibility, this powder is often used in medical implants and aerospace applications.
- Applications: Dental implants, orthopedic implants, turbine blades.
- Iron-Based Powder (Fe-Ni Alloy)
- Description: A powder with good mechanical properties and magnetic characteristics. It is used in various structural and magnetic applications.
- Applications: Structural components, magnetic cores, tooling.
- Superalloy Powder (Hastelloy X)
- Description: A powder designed for high-temperature and corrosive environments. It offers excellent oxidation resistance and strength.
- Applications: Gas turbine engines, chemical processing, nuclear reactors.
- Tungsten Powder (W)
- Description: A dense, high-melting-point powder used in high-temperature and radiation-shielding applications. It offers exceptional hardness and thermal stability.
- Applications: Radiation shielding, cutting tools, high-temperature furnace components.
- Magnesium Powder (AZ91D)
- Description: A lightweight, corrosion-resistant powder used in automotive and aerospace applications. It is known for its good castability and strength.
- Applications: Automotive components, aerospace structures, electronics housings.
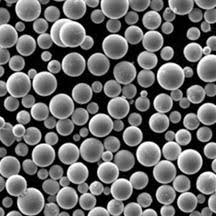
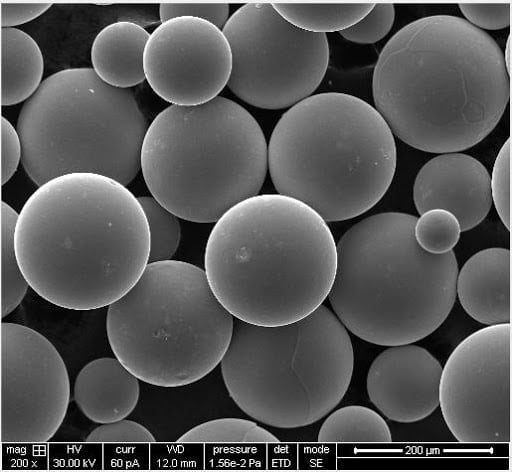
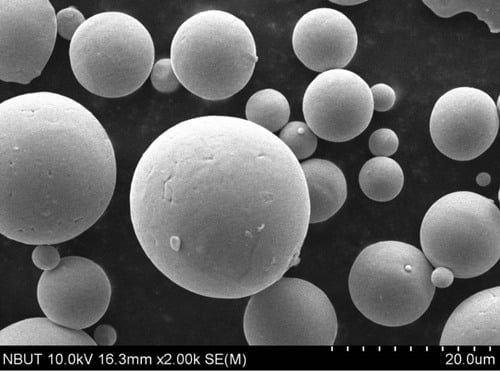
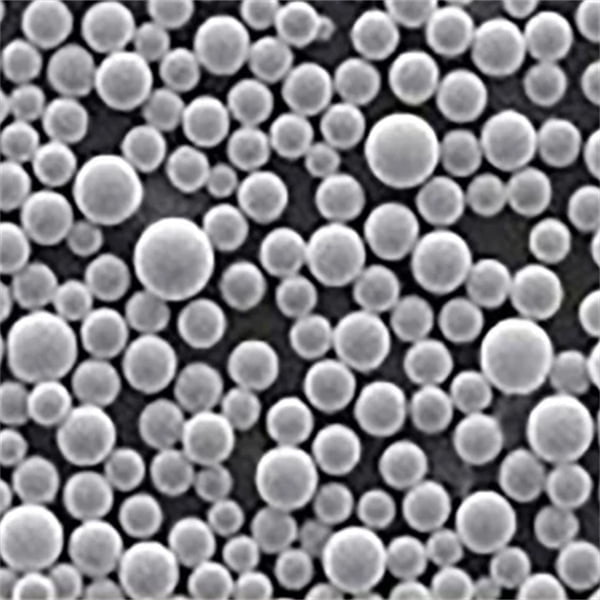
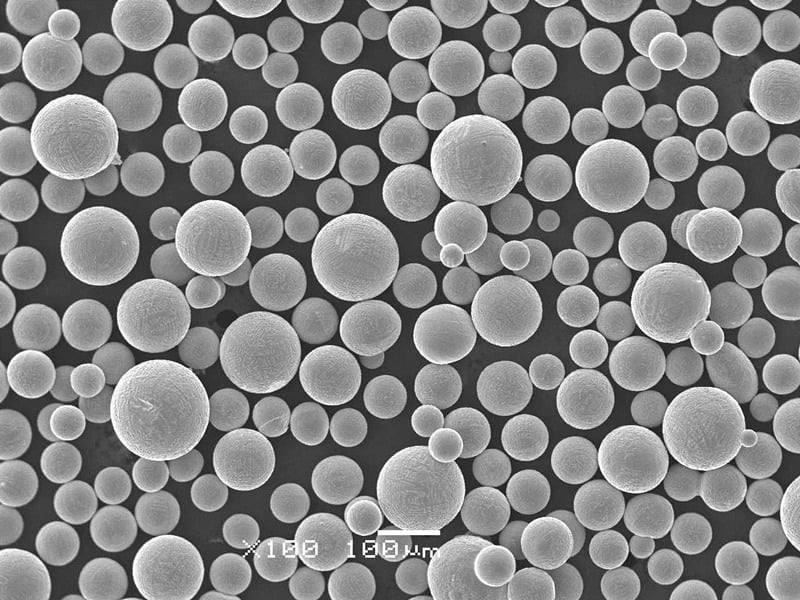
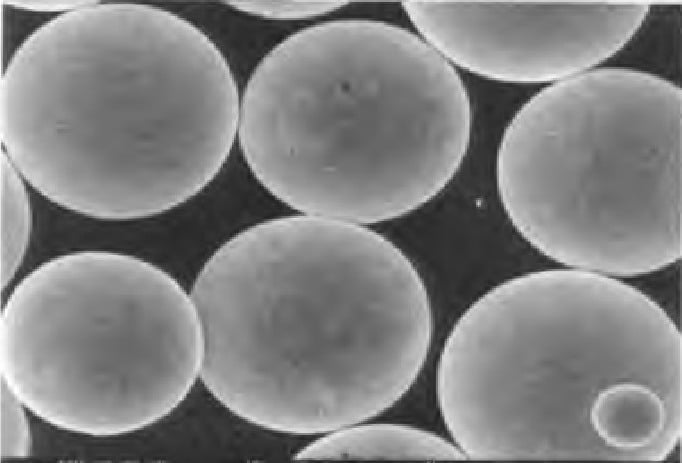
Applications of Metal Powders from Electrode Inert Gas Atomisers
Industries and Sectors
The metal powders produced by electrode inert gas atomisers are used across various industries, each benefiting from the unique properties of these powders. Here’s a look at the primary industries and the specific applications within them:
- Ngành công nghiệp Hàng không Vũ trụ
- Applications: Turbine blades, structural components, engine parts.
- Lợi ích: High strength-to-weight ratio, corrosion resistance, ability to withstand extreme temperatures.
- Medical Implants
- Applications: Orthopedic implants, dental implants, prosthetics.
- Lợi ích: Biocompatibility, precision in shape and size, excellent mechanical properties.
- Cụm chi tiết ô tô
- Applications: Engine components, transmission parts, lightweight structural elements.
- Lợi ích: Reduced weight, improved fuel efficiency, enhanced durability.
- Electronics Manufacturing
- Applications: Conductive inks, heat sinks, electromagnetic shielding.
- Lợi ích: High electrical and thermal conductivity, miniaturization of components.
- 3D Printing (Additive Manufacturing)
- Applications: Prototyping, complex geometries, custom components.
- Lợi ích: Design flexibility, material efficiency, rapid production cycles.
- Energy and Power Generation
- Applications: Turbine blades, fuel cells, heat exchangers.
- Lợi ích: High-temperature performance, corrosion resistance, durability.
- Tooling and Die Making
- Applications: Molds, cutting tools, dies.
- Lợi ích: Wear resistance, precision, longevity.
Technical Specifications and Standards
Specifications of Electrode Inert Gas Atomisers
When selecting an electrode inert gas atomiser, it’s important to consider various specifications to ensure that the system meets the required performance standards. Here are some key specifications:
Đặc điểm kỹ thuật | Miêu tả |
---|---|
Kích thước | Available in various sizes to accommodate different production scales. |
Operating Temperature | Ranges from 1,500°C to 3,000°C depending on the metal being atomised. |
Inert Gas Pressure | Typically between 10 to 50 bar, adjustable based on desired particle size. |
Electrode Material | Options include tungsten, graphite, and copper alloys. |
Particle Size Range | Can produce powders with particle sizes ranging from 10 to 150 microns. |
năng lực sản xuất | Varies from small-scale lab units to large industrial systems capable of producing several tons per day. |
Cooling Method | Options include water cooling and air cooling systems. |
Specifications of Metal Powders
The metal powders produced by electrode inert gas atomisers must meet specific standards to be suitable for their intended applications. Key specifications include:
Đặc điểm kỹ thuật | Miêu tả |
---|---|
Kích thước hạt | Typically ranges from 10 to 100 microns, depending on the application. |
Purity Level | High purity levels, often exceeding 99.9%, depending on the metal. |
Khả năng chảy | Measured to ensure smooth handling in manufacturing processes. |
Mật độ | Varies by material, with powders designed to achieve specific packing densities. |
Shape Consistency | Spherical particles are preferred for uniformity and performance in applications like 3D printing. |
Suppliers and Pricing Details
Leading Suppliers of Electrode Inert Gas Atomisers
Several companies specialize in manufacturing electrode inert gas atomisers, each offering unique features and benefits. Here’s a comparison of some leading suppliers:
Nhà cung cấp | Key Features | Địa điểm | Product Range |
---|---|---|---|
ALD Vacuum Technologies | Advanced design, high efficiency, customizable systems | Đức | Lab to industrial-scale atomisers |
Praxair Surface Technologies | Extensive experience, comprehensive support, wide range of systems | United States | Gas atomisers, plasma atomisers |
AP&C (Advanced Powders & Coatings) | High purity powders, advanced atomisation technology | Canada | Titanium and nickel alloy powders |
Atomising Systems Ltd. | Specialized in small to medium-scale production systems | United Kingdom | Custom-designed atomisers |
Công ty dịch vụ sản xuất phụ gia Carpenter | Integrated solutions, from atomisation to powder delivery | United States | Stainless steel, nickel, cobalt powders |
Pricing Information
Pricing for electrode inert gas atomisers and the metal powders they produce can vary widely based on several factors, including material type, production scale, and customization requirements. Here’s a general overview of pricing:
Sản phẩm | Mức giá | Factors Affecting Price |
---|---|---|
Electrode Inert Gas Atomiser | $200,000 – $2,000,000 | Size, production capacity, materials used, customization. |
Stainless Steel Powder (316L) | $20 – $50 per kg | Purity, particle size, production scale. |
Titanium Powder (Ti-6Al-4V) | $150 – $300 per kg | Alloy composition, particle size, supplier. |
Aluminium Powder (AlSi10Mg) | $30 – $70 per kg | Alloy composition, particle size, regional pricing variations. |
Nickel-Based Powder (Inconel 718) | $60 – $150 per kg | Alloy composition, particle size, production method. |
Copper Powder (Cu) | $15 – $40 per kg | Purity, particle size, supplier. |
Advantages and Disadvantages of Electrode Inert Gas Atomisers
Lợi ích
Electrode inert gas atomisers offer several distinct advantages, making them a preferred choice in various industries:
- Precision in Powder Production: The ability to control particle size and distribution with high accuracy is a key advantage, ensuring that the metal powders meet specific industrial requirements.
- Versatility Across Different Metals: These atomisers can handle a wide range of metals, including those with high melting points, making them suitable for diverse applications.
- High-Quality Output: The use of inert gas prevents oxidation and contamination, resulting in powders with high purity and consistent properties.
- Scalability: Electrode inert gas atomisers are available in various sizes, from small laboratory units to large industrial systems, allowing manufacturers to scale production as needed.
Nhược điểm
Despite their many advantages, electrode inert gas atomisers also have some drawbacks:
- High Operational Costs: The cost of the equipment, energy consumption, and inert gas can make the process expensive, especially for large-scale production.
- Complex Maintenance Requirements: These systems require regular maintenance and skilled operators to ensure optimal performance. The high-tech components and precise calibration need consistent oversight to prevent issues and maintain efficiency.
- Energy-Intensive Process: The process of melting metals and maintaining high temperatures consumes significant amounts of energy, which can impact operational costs and environmental footprint.
Comparison of Electrode Inert Gas Atomisers with Other Atomisation Technologies
When evaluating different atomisation technologies, it’s essential to understand how electrode inert gas atomisers stack up against other methods. Each atomisation technique has its unique advantages and drawbacks, making them suitable for specific applications.
Electrode Inert Gas Atomisation vs. Plasma Atomisation
Electrode Inert Gas Atomisation:
- Pros:
- High purity powders due to the use of inert gases.
- Good control over particle size distribution.
- Versatile, able to handle a wide range of metals.
- Cons:
- Higher operational costs due to energy consumption and inert gas usage.
- Complex and expensive maintenance.
Plasma Atomisation:
- Pros:
- Capable of producing very fine powders with narrow size distributions.
- Suitable for high-temperature and reactive metals.
- Cons:
- Higher capital investment compared to some other methods.
- More complex setup and operational procedures.
Comparison:
Plasma atomisation can produce even finer powders than electrode inert gas atomisation, but it often comes with higher equipment costs and complexity. Electrode inert gas atomisers, on the other hand, are more versatile and suitable for a broader range of metals but may incur higher operational costs.
Electrode Inert Gas Atomisation vs. Water Atomisation
Electrode Inert Gas Atomisation:
- Pros:
- Produces powders with a high level of purity.
- Allows for precise control over the powder characteristics.
- Cons:
- More expensive due to inert gas requirements and energy consumption.
- Complex to maintain.
Water Atomisation:
- Pros:
- Generally lower operational costs compared to inert gas atomisation.
- Simpler technology and maintenance.
- Cons:
- Water can react with some metals, leading to contamination.
- Produces powders with less control over particle size distribution.
Comparison:
Water atomisation is less costly and simpler but can introduce impurities and offer less control over powder characteristics compared to electrode inert gas atomisation. The choice between these methods depends on the required purity and precision of the powder.
Electrode Inert Gas Atomisation vs. Centrifugal Atomisation
Electrode Inert Gas Atomisation:
- Pros:
- Produces spherical powders with consistent properties.
- Suitable for a wide range of metals.
- Cons:
- Higher energy and inert gas costs.
- Complex maintenance needs.
Centrifugal Atomisation:
- Pros:
- Can produce high-quality powders with controlled particle size.
- Often used for metals with high melting points.
- Cons:
- Typically used for smaller-scale production.
- Can be less efficient for producing very fine powders.
Comparison:
Centrifugal atomisation is effective for high-melting-point metals but may not achieve the same level of precision in particle size distribution as electrode inert gas atomisation. Electrode inert gas atomisers offer more versatility and can produce larger quantities of high-purity powders.
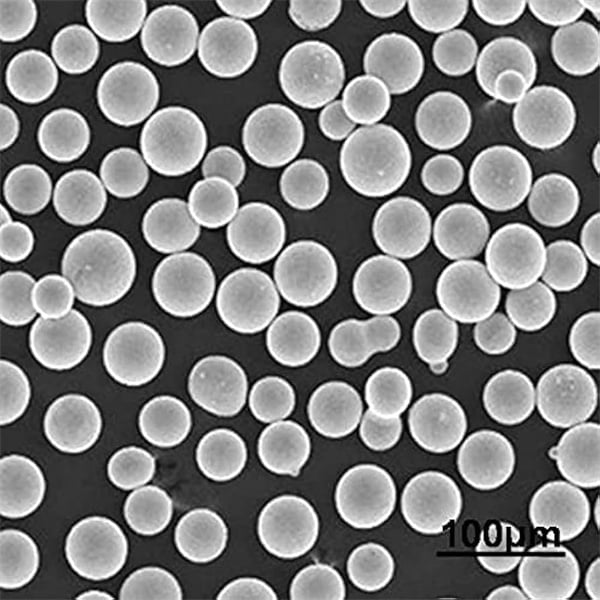
Future Trends and Innovations
Technological Advancements
The field of electrode inert gas atomisation is continuously evolving, with several technological advancements on the horizon:
- Enhanced Materials and Alloys: Researchers are developing new materials and alloys that can be processed more efficiently and with improved properties. This includes high-performance alloys for extreme conditions and lightweight materials for aerospace applications.
- Improved Atomiser Designs: Innovations in atomiser design aim to enhance efficiency, reduce energy consumption, and improve the control of particle size distribution. This includes the development of more precise gas flow control systems and advanced electrode materials.
- Automation and Smart Technology: Integration of automation and smart technology is streamlining the operation and monitoring of atomisers, leading to increased precision, reduced downtime, and enhanced data collection for process optimization.
Market Trends
- Growing Demand in 3D Printing: The rise of additive manufacturing (3D printing) is driving demand for high-quality metal powders. Electrode inert gas atomisers are well-positioned to meet this demand with their ability to produce powders with precise characteristics.
- Expansion into New Industries: Electrode inert gas atomisers are finding applications in emerging industries such as renewable energy, advanced electronics, and biotechnology. This expansion is driven by the need for high-performance materials in these rapidly growing sectors.
Sustainability and Environmental Impact
- Energy-Efficient Designs: Manufacturers are focusing on developing more energy-efficient atomiser designs to reduce operational costs and environmental impact. This includes optimizing heating processes and improving inert gas usage.
- Waste Reduction Strategies: Efforts are being made to minimize waste and enhance recycling of metal powders and by-products. This includes advancements in powder recovery and reprocessing technologies.
Câu hỏi thường gặp
Question | Answer |
---|---|
What is the purpose of using inert gas in atomisation? | Inert gas is used to prevent chemical reactions between the molten metal and the environment, ensuring high purity and consistency of the powder. |
How do electrode inert gas atomisers compare to other atomisation methods? | Electrode inert gas atomisers offer high purity and precise control over particle size but come with higher costs and maintenance compared to methods like water or centrifugal atomisation. |
What types of metal powders are best suited for 3D printing? | Metal powders such as stainless steel, titanium, and aluminium are commonly used in 3D printing due to their favorable properties and ability to produce high-quality parts. |
How does the choice of electrode material affect atomiser performance? | The electrode material affects the efficiency and quality of the atomisation process. For example, tungsten is used for high-melting-point metals due to its high thermal stability. |
What are the key factors to consider when selecting an atomiser for industrial use? | Factors include the type of metal to be atomised, the desired powder properties, production scale, operational costs, and maintenance requirements. |
Kết luận
Electrode inert gas atomisers play a crucial role in producing high-quality metal powders for various industrial applications. Their ability to deliver precision, consistency, and high purity makes them indispensable in fields ranging from aerospace to 3D printing. As technology advances, these atomisers continue to evolve, offering new possibilities for material science and manufacturing.
By understanding the intricacies of electrode inert gas atomisers, their advantages and limitations, and how they compare to other atomisation methods, you can make informed decisions about their use in your applications. Whether you’re exploring new materials for additive manufacturing or optimizing production processes, this comprehensive guide provides the insights you need to navigate the world of electrode inert gas atomisation.
know more 3D printing processes
[WORDPRESS_PDF]
About 3DP mETAL
Product Category
LIÊN HỆ
Bạn có thắc mắc không? Hãy gửi tin nhắn ngay cho chúng tôi! Sau khi nhận được tin nhắn của bạn, chúng tôi sẽ xử lý yêu cầu của bạn với cả một đội ngũ.