Imagine a world where complex metal parts, once limited by traditional manufacturing methods, can be conjured from thin air, layer by layer, with unparalleled precision and detail. This, my friend, is the reality of Electron Beam Melting Technology technology, a revolutionary 3D printing process that’s transforming the way we design and produce metal components. Buckle up, because we’re about to delve into the fascinating world of Electron Beam Melting Technology, exploring its inner workings, uncovering its advantages, and witnessing its applications across various industries.
The Working Principle of Electron Beam Melting Technology
EBM operates in a realm of high vacuum and intense energy. Here’s a breakdown of the magic behind this technology:
- The Stage is Set: The process begins within a tightly sealed chamber pumped to a near-vacuum state. This eliminates the presence of oxygen and other contaminants that could hinder the melting process or compromise the final product’s quality.
- Powder Power: A bed of fine metal powder, specifically chosen for the desired final part properties, is meticulously spread across the build platform. Think of this powder as the building blocks for your metallic masterpiece.
- Electron Beam: The Conductor: A high-powered electron beam, generated by an electron gun, takes center stage. Imagine this beam as a super-focused stream of electrons, acting like a tiny, supercharged paintbrush.
- Melting on Demand: The electron beam is meticulously scanned across the powder bed, precisely melting the designated areas according to a pre-programmed digital blueprint. This targeted melting fuses the powder particles together, creating a single, solid layer.
- Building Block by Building Block: The platform lowers slightly, and a fresh layer of powder is deposited on top of the previously melted layer. The electron beam then dances across this new canvas, meticulously melting the designated pattern, effectively building the part one layer at a time. This process continues layer by serendipitous layer until the entire 3D structure is complete.
- The Grand Unveiling: Once the build is finished, the chamber is brought back to atmospheric pressure, and the completed part is separated from the surrounding unmelted powder. With some post-processing steps like support removal and surface finishing, your complex metal masterpiece is ready to shine!
Think of EBM like a sophisticated inkjet printer, but instead of ink cartridges, it uses a high-powered electron beam and metal powder to create intricate 3D objects.
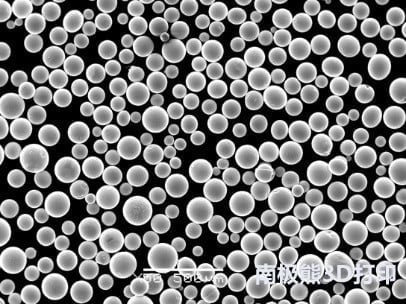
Advantages of Electron Beam Melting Technology
EBM boasts several advantages that make it a compelling choice for various metal additive manufacturing applications. Here’s a closer look at some of its key benefits:
- Unparalleled Design Freedom: EBM allows for the creation of complex geometries with intricate internal features and lattice structures, which would be near-impossible or incredibly expensive to achieve with traditional manufacturing techniques. Imagine designing a lightweight aircraft component with internal channels for improved heat management – EBM makes it possible!
- Superior Material Properties: The high-vacuum environment and precise melting process in EBM lead to parts with excellent mechanical properties, including high strength, good ductility, and exceptional fatigue resistance. These characteristics make EBM ideal for applications demanding high performance under harsh conditions.
- Minimal Residual Stress: The controlled melting process in EBM minimizes residual stress within the finished part. This translates to reduced warping and distortion, leading to parts with exceptional dimensional accuracy and stability. Say goodbye to post-processing headaches associated with stress relief!
- Broad Material Compatibility: EBM offers compatibility with a wide range of metal powders, including reactive materials like titanium and tantalum, which are notoriously challenging to work with using traditional methods. This opens doors to a vast array of potential applications across different industries.
- High Production Rate: Compared to some other metal additive manufacturing processes, EBM offers a relatively high production rate, making it suitable for producing medium to large batches of complex metal parts.
EBM technology empowers designers and engineers to push the boundaries of what’s possible, creating high-performance, intricate metal parts that were once relegated to the realm of science fiction.
Applications of Electron Beam Melting Technology
The unique capabilities of EBM make it a valuable tool across various industries. Here are some prominent examples of where EBM shines:
- Ngành hàng không vũ trụ: The weight-saving potential and excellent mechanical properties of EBM-produced parts make them ideal for aerospace applications. Components like lightweight, high-strength engine brackets and heat exchangers can be manufactured using EBM, contributing to improved fuel efficiency and overall aircraft performance.
- Medical Implants: EBM’s biocompatibility with certain metal alloys makes it perfect for creating custom-designed medical implants like prosthetic joints and spinal cages. The high-resolution printing capabilities of EBM allow for the creation of implants with porous structures that encourage bone ingrowth, promoting better osseointegration (fusion between bone and implant). This can significantly improve the long-term success rate of these implants and patient outcomes.
- Ô tô: EBM is increasingly used in the automotive industry to produce lightweight, high-performance components for race cars and high-end vehicles. Think of intricate components like complex gear parts or customized pistons that can withstand the extreme stresses of racing environments.
- Tooling and Molds: EBM offers a fast and efficient way to create complex tooling and molds with intricate cooling channels. These molds can be used for various applications, including injection molding of plastic parts and casting of metal components. The high strength and thermal stability of EBM-produced molds make them ideal for high-volume production runs.
- Defense and Security: EBM’s ability to create intricate parts with exceptional strength-to-weight ratios makes it valuable for the defense and security sector. Components like lightweight firearms components and customized armor plates can be manufactured using EBM, offering superior performance advantages.
It’s important to remember that EBM technology is still evolving, but its potential applications are vast and ever-expanding. As the technology matures and costs become more competitive, we can expect to see EBM playing an even more significant role in shaping the future of metal manufacturing across various industries.
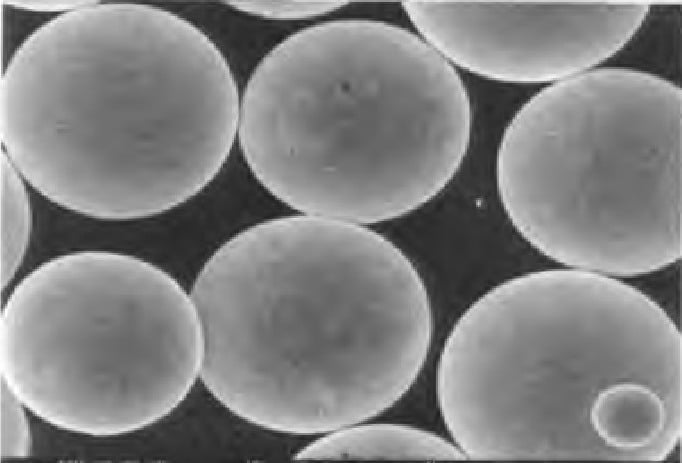
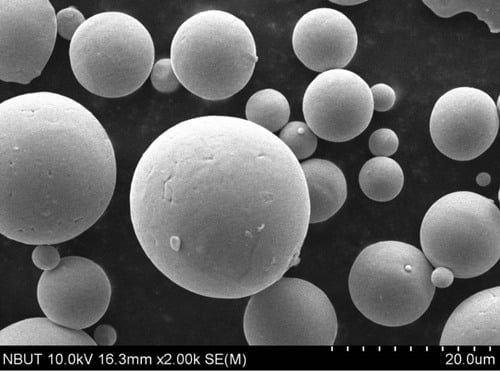
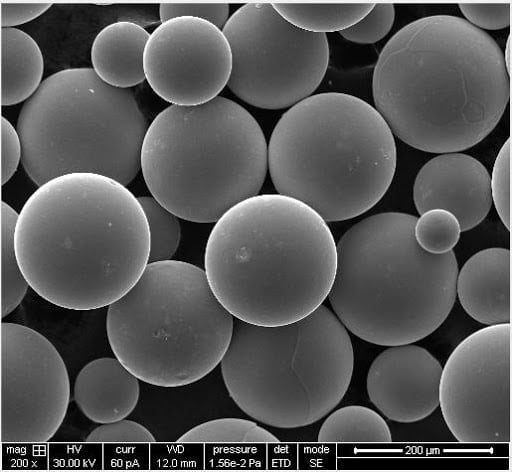
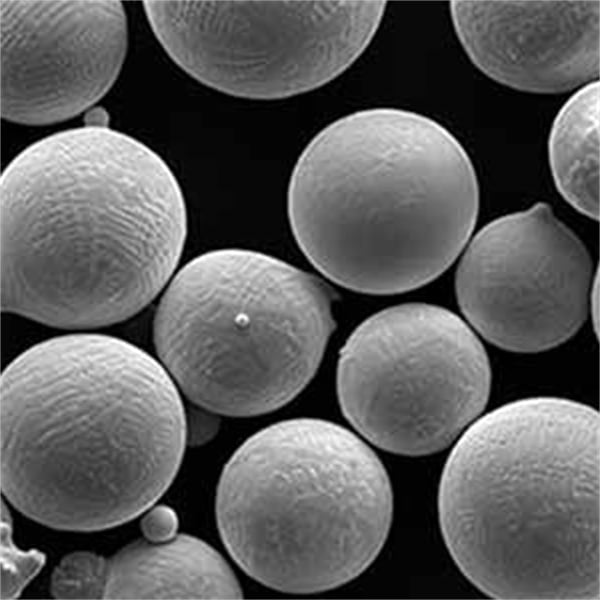
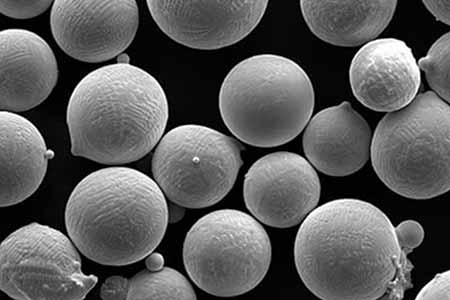
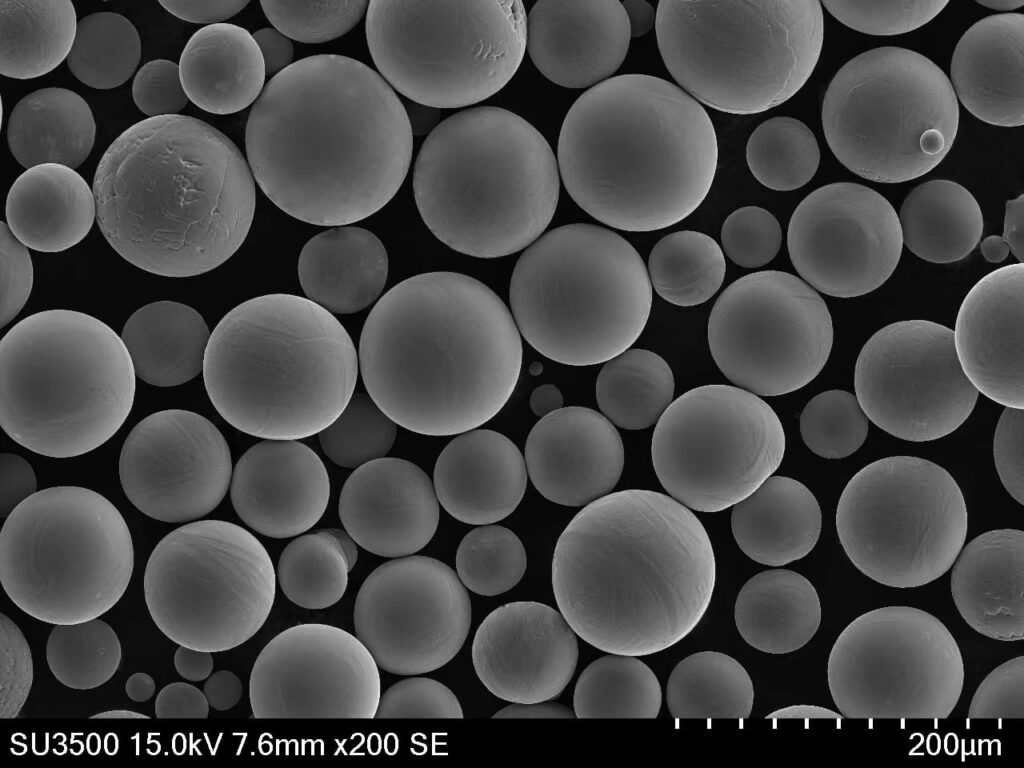
Limitations and Considerations for Electron Beam Melting Technology
While EBM boasts impressive advantages, it’s essential to acknowledge some limitations and considerations before diving headfirst into this technology.
- Cost: EBM systems are generally more expensive compared to some other metal additive manufacturing technologies. The high cost of the equipment, combined with the relatively high cost of metal powders, can translate to higher overall part costs.
- Surface Roughness: Parts produced using EBM can exhibit a slightly rougher surface finish compared to some other metal additive manufacturing techniques. While post-processing techniques can improve surface finish, it’s a factor to consider when designing parts for specific applications.
- Support Structures: Similar to other 3D printing processes, EBM often requires the use of support structures to build overhanging features. These supports need to be removed after the build is complete, which can add to post-processing time and potentially leave minor marks on the final part.
- Limited Build Size: While build sizes for EBM machines are increasing, they are generally smaller compared to some other additive manufacturing technologies. This can limit the size of parts that can be produced using EBM.
Despite these limitations, EBM technology continues to advance, with ongoing research and development efforts focused on reducing costs, improving surface finishes, and expanding build sizes. As these advancements unfold, EBM’s limitations will shrink, further solidifying its position as a powerful tool for metal additive manufacturing.
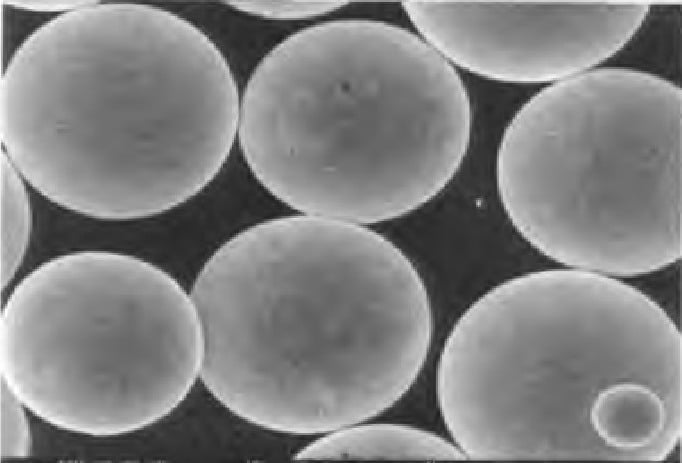
Câu hỏi thường gặp
Here’s a breakdown of some frequently asked questions about Electron Beam Melting technology, presented in a clear and concise table format for easy reference:
Question | Answer |
---|---|
What types of metal powders can be used with EBM? | A wide range of metal powders can be used with EBM, including titanium alloys, nickel alloys, cobalt-chrome alloys, stainless steels, and even some refractory metals like tantalum and tungsten. |
How strong are parts made with EBM? | Parts made with EBM can exhibit excellent mechanical properties, including high tensile strength, fatigue resistance, and good ductility. The specific properties will depend on the chosen metal powder and the build parameters used. |
How does EBM compare to other metal additive manufacturing technologies? | Compared to other metal additive manufacturing processes like Selective Laser Melting (SLM), EBM generally offers a higher build rate but might have a slightly rougher surface finish. EBM also boasts superior compatibility with reactive metals like titanium. |
Is EBM environmentally friendly? | EBM offers some environmental advantages compared to traditional manufacturing techniques. The high-vacuum environment minimizes waste and emissions, and the ability to create near-net-shape parts reduces material scrap. |
What is the future of EBM technology? | The future of EBM looks bright! With ongoing advancements in technology, we can expect to see reduced costs, improved surface finishes, larger build sizes, and the development of new metal powders specifically designed for EBM applications. |
About 3DP mETAL
Product Category
LIÊN HỆ
Bạn có thắc mắc không? Hãy gửi tin nhắn ngay cho chúng tôi! Sau khi nhận được tin nhắn của bạn, chúng tôi sẽ xử lý yêu cầu của bạn với cả một đội ngũ.