Introduction
When it comes to producing high-quality metal powders, gas atomizer equipment is at the forefront of modern technology. Whether you’re in aerospace, automotive, or additive manufacturing, the quality of the metal powder you use can make or break your project. But what exactly is gas atomizer equipment, and why is it so crucial? In this comprehensive guide, we’ll dive deep into the world of gas atomizers, exploring everything from how they work to the specific types of metal powders they produce. By the end, you’ll have a thorough understanding of why gas atomizers are indispensable in today’s manufacturing landscape.
Overview of Gas Atomizer Equipment
What is Gas Atomization?
Gas atomization is a process used to create metal powders by breaking down molten metal into fine droplets, which then solidify into powder particles. This technique is widely employed in industries that require precise and uniform powder particles, such as 3D printing, metal injection molding, and coating processes.
History and Development
The origins of gas atomization can be traced back to the mid-20th century, when the demand for uniform metal powders began to rise. Initially, the process was rudimentary, with limited control over particle size and distribution. However, advances in technology and materials have transformed gas atomization into a sophisticated method capable of producing high-quality powders for a variety of applications.
Importance in Modern Manufacturing
In today’s manufacturing environment, the demand for fine, consistent metal powders is higher than ever. Gas atomizer equipment plays a critical role in meeting this demand, offering unparalleled control over particle size, distribution, and composition. This precision is vital in industries such as aerospace, where even the smallest deviation can lead to significant consequences.
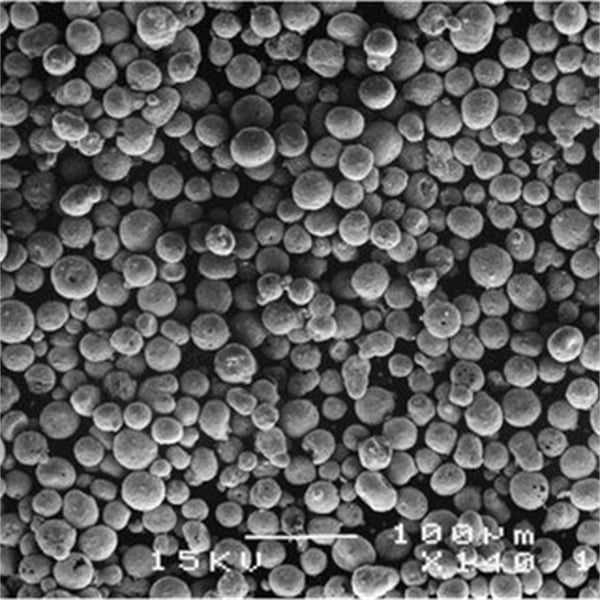
How Gas Atomizer Equipment Works
Basic Principles of Gas Atomization
At its core, gas atomization involves the rapid cooling of molten metal through the use of high-pressure gas jets. As the molten metal is forced through a nozzle, the gas jets break it into tiny droplets. These droplets then solidify into fine powder particles as they cool.
Key Components of Gas Atomizer Equipment
- Crucible: The vessel where the metal is melted before atomization.
- Nozzle: The critical component where the molten metal is forced out and atomized by the gas jets.
- Gas Supply System: Provides the necessary pressure and flow of gas to break up the molten metal.
- Powder Collection Chamber: Where the solidified metal powder is collected after atomization.
- Control Systems: Advanced electronics that regulate the temperature, gas flow, and other parameters to ensure consistent powder quality.
Process Flow: From Metal to Powder
- Melting: The metal is melted in the crucible at a controlled temperature.
- Atomization in Vietnamese can be translated as "phân tử hóa.": The molten metal is forced through the nozzle, where it’s broken into fine droplets by high-pressure gas jets.
- Solidification: The droplets rapidly cool and solidify into powder particles.
- Collection: The powder is collected in a chamber, ready for further processing or packaging.
Types of Metal Powders Produced by Gas Atomization
Gas atomization is versatile, producing a wide range of metal powders. Here’s a list of 10+ specific metal powders along with their descriptions:
- Stainless Steel Powder
Used in automotive and aerospace industries for its corrosion resistance and strength. - Titanium Powder
Essential in medical implants and aerospace for its biocompatibility and high strength-to-weight ratio. - Aluminum Alloy Powder
Popular in additive manufacturing due to its lightweight nature and good mechanical properties. - Nickel Alloy Powder
Widely used in high-temperature applications like gas turbines and jet engines. - Cobalt-Chrome Powder
Known for its wear resistance, making it ideal for dental implants and orthopedic devices. - Copper Powder
Common in electrical applications due to its excellent conductivity. - Bronze Powder
Used in sintering and coating applications for its aesthetic appeal and corrosion resistance. - Inconel Powder
A superalloy used in extreme environments, such as nuclear reactors and space vehicles. - Tool Steel Powder
Used in the manufacturing of cutting tools and dies, known for its hardness and durability. - Iron Powder
Essential in magnetic materials and certain sintering applications.
Comparison of Metal Powders
Metal Powder | Primary Use | Key Properties | Industries |
---|---|---|---|
Thép không gỉ | Automotive, Aerospace | Corrosion resistance, strength | Automotive, Aerospace |
Titan | Medical Implants, Aerospace | Biocompatibility, high strength | Medical, Aerospace |
Aluminum Alloy | sản xuất bồi đắp | Lightweight, mechanical properties | Sản xuất |
Nickel Alloy | High-Temperature Applications | Chịu nhiệt | Hiệp công |
Cobalt-Chrome | Dental Implants, Orthopedics | Khả năng chống mài mòn | Y học |
Đồng | Electrical Applications | Độ dẫn điện | ĐIỆN |
Đồng | Sintering, Coating | Aesthetic, corrosion resistance | Sản xuất |
Inconel | Extreme Environments | Superalloy properties | Aerospace, Energy |
Tool Steel | Cutting Tools, Dies | Hardness, durability | Sản xuất |
Sắt | Magnetic Materials, Sintering | Magnetic properties | Sản xuất |
Composition of Gas Atomizer Equipment
Material Selection for Construction
The construction materials of gas atomizer equipment are crucial for ensuring durability, resistance to corrosion, and thermal stability. Typically, high-grade stainless steel, ceramics, and alloys are used in various components of the equipment.
Impact of Materials on Performance
The choice of materials affects the efficiency and longevity of the equipment. For instance, using a high-quality steel for the crucible ensures it can withstand repeated heating and cooling cycles without degradation. Similarly, ceramic nozzles are preferred for their ability to handle extreme temperatures without deforming.
Materials Used in Gas Atomizer Equipment
Thành phần | Material Type | Reason for Selection |
---|---|---|
Crucible | High-Grade Stainless Steel | Durability, corrosion resistance |
Nozzle | Ceramic | Heat resistance, stability |
Gas Supply System | Alloy Steel | Strength, ability to handle pressure |
Powder Collection Chamber | Stainless Steel, Alloys | Corrosion resistance, durability |
Control Systems | Electronics with Heat-Resistant Casings | Reliability under high temperatures |
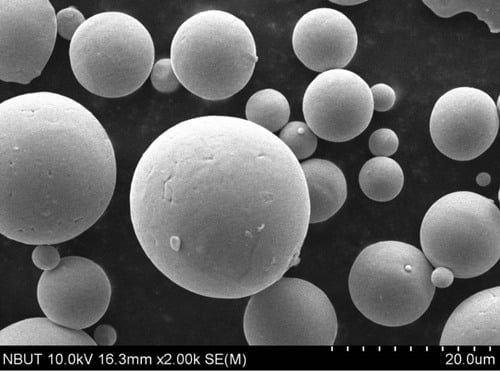
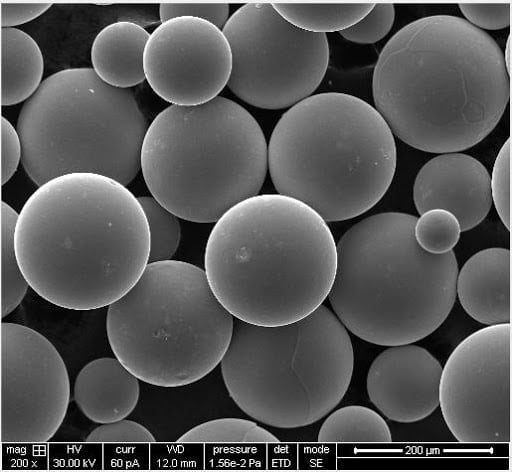
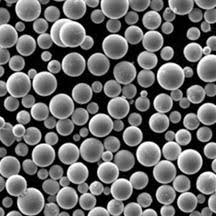
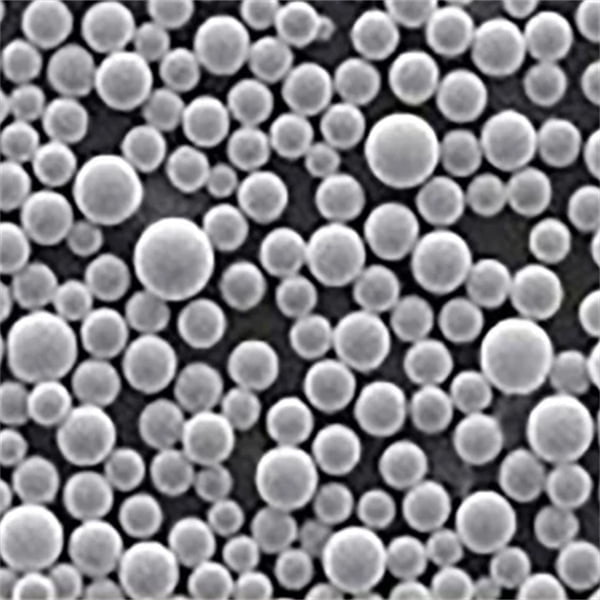
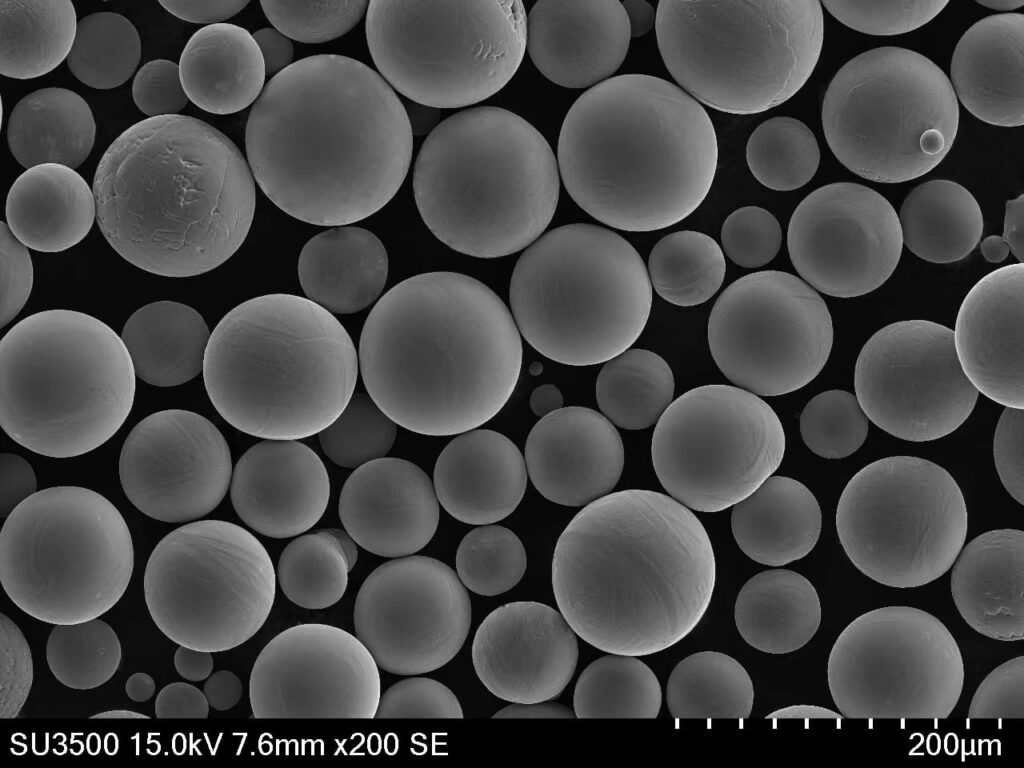
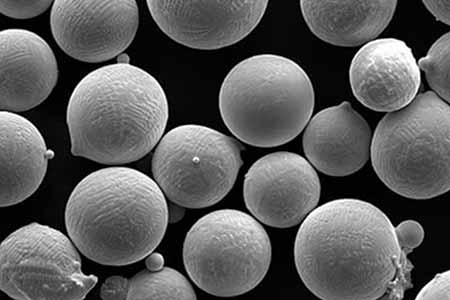
Characteristics of Gas Atomizer Equipment
Efficiency and Throughput
Efficiency in gas atomization is measured by the yield of usable powder produced per unit of raw material. Modern equipment boasts high efficiency, minimizing waste and optimizing throughput.
Particle Size and Distribution
One of the most critical characteristics is the ability to control particle size and distribution. This is essential for applications requiring uniform powders, such as additive manufacturing. Advanced gas atomizers allow for precise control over these parameters, resulting in consistent powder quality.
Performance Characteristics of Gas Atomizer Equipment
Đặc điểm | Importance | Typical Values/Range |
---|---|---|
Efficiency | Maximizes usable powder production | 80-95% efficiency |
Kích thước hạt | Key for specific applications | 10-100 microns |
Particle Distribution | Affects final product quality | Narrow size distribution |
Gas Pressure | Influences atomization efficiency | 10-50 bar |
Cooling Rate | Affects microstructure of powders | Rapid cooling for fine powders |
Advantages of Gas Atomizer Equipment
High Precision in Powder Production
Gas atomizers excel in producing metal powders with highly controlled particle sizes and distributions. This precision is essential in industries like aerospace and medical devices, where the consistency of materials can affect the safety and performance of the final product.
Versatility in Powder Types
Another significant advantage is the versatility of gas atomizers. They can produce powders from a wide range of metals and alloys, making them indispensable in industries that require specialized materials.
Pros of Gas Atomization
Advantage | Miêu tả | Impact on Applications |
---|---|---|
Precision | Tight control over particle size | Higher quality final products |
Versatility | Capable of producing various powders | Supports diverse industries |
High Efficiency | Minimal waste in production | Cost-effective operations |
Khả năng mở rộng | Suitable for both small and large-scale production | Adaptable to industry needs |
Consistency | Uniform powder quality | Reliability in manufacturing |
Disadvantages of Gas Atomizer Equipment
High Initial Investment
One of the primary drawbacks of gas atomization equipment is the high upfront cost. The sophisticated technology and materials used in construction make these machines expensive to purchase and install.
Energy Consumption
Gas atomizers require significant amounts of energy to melt metals and maintain the high-pressure gas flow needed for atomization. This can lead to higher operational costs, especially for large-scale production.
Cons of Gas Atomization
Disadvantage | Miêu tả | Impact on Applications |
---|---|---|
High Cost | Expensive initial investment | May limit accessibility for small businesses |
Energy Intensive | Requires significant energy | Increases operational costs |
Maintenance Requirements | Complex machinery needs regular upkeep | Potential downtime if not maintained |
Complexity | Requires skilled operators | May require specialized training |
Limited Material Compatibility | Not all metals are suitable for gas atomization | Limits material selection |
Applications of Gas Atomized Powders
Gas atomized powders are used across a variety of industries, each with unique requirements. The precision and uniformity of these powders make them ideal for high-tech applications.
Industries and Sectors Using These Powders
- Hiệp công: Lightweight and strong powders like titanium and aluminum alloys are essential for aircraft components.
- Y học: Biocompatible powders such as titanium are used in implants and prosthetics.
- Ô tô: Stainless steel and aluminum powders are used in the manufacturing of engine components and lightweight structures.
- sản xuất bồi đắp: A broad range of metal powders is used in 3D printing to create intricate designs with high precision.
- Năng lượng: Nickel and cobalt powders are used in high-temperature environments, such as gas turbines and nuclear reactors.
Applications of Metal Powders
Ngành | Metal Powder Used | Application Example |
---|---|---|
Hiệp công | Titanium, Aluminum Alloy | Aircraft components |
Y học | Titanium, Cobalt-Chrome | Implants, Prosthetics |
Ô tô | Stainless Steel, Aluminum Alloy | Engine components, lightweight structures |
sản xuất bồi đắp | Various (e.g., Inconel, Steel) | 3D printed parts |
Năng lượng | Nickel, Cobalt-Chrome | Turbines, nuclear reactor components |
Specifications of Gas Atomizer Equipment
When selecting gas atomizer equipment, it’s crucial to consider key specifications that will affect performance and suitability for specific applications.
Key Specifications to Consider
- năng lực sản xuất: Determines how much powder can be produced per hour or day.
- Particle Size Range: Indicates the range of powder particle sizes that the equipment can produce.
- Gas Type and Pressure: Different gases (e.g., argon, nitrogen) can be used, with varying effects on the final powder quality.
- Temperature Control: Critical for ensuring consistent melting and atomization.
- Automation Level: Determines how much of the process is controlled by software versus manual operation.
Common Sizes, Grades, and Standards
Đặc điểm kỹ thuật | Miêu tả | Typical Values/Standards |
---|---|---|
năng lực sản xuất | Output of powder per unit time | 10-100 kg/hour |
Particle Size Range | Range of particle sizes produced | 10-100 microns |
Gas Pressure | Pressure of atomizing gas | 10-50 bar |
Operating Temperature | Temperature range for melting metal | 1200-1600°C |
Automation Level | Degree of process automation | Manual to Fully Automated |
Comparison of Gas Atomizer Equipment Models
Here, we compare some of the top models available in the market, focusing on their features, capabilities, and costs.
Top Models Compared: Features, Capabilities, Costs
Mô hình | Features | Capabilities | Cost Range |
---|---|---|---|
Atomizer X100 | High precision, fully automated | 50 kg/hour, 10-50 micron size range | $$$$ |
Atomizer Pro 500 | Versatile, suitable for multiple metals | 70 kg/hour, wide size range | $$$ |
UltraAtom 3000 | Energy-efficient, compact design | 30 kg/hour, 15-60 micron size range | $$ |
Precision Atomizer 850 | Superior temperature control | 80 kg/hour, 10-40 micron size range | $$$$ |
Econo Atomizer 200 | Cost-effective, basic features | 20 kg/hour, 20-100 micron size range | $ |
Nhà cung cấp và Giá
Identifying the right supplier is crucial for acquiring high-quality gas atomizer equipment at a competitive price. Here, we list some top suppliers and provide an overview of pricing trends.
Top Manufacturers and Suppliers
- PowderTech Inc.: Known for high-end, customizable gas atomizers.
- AtomizeCo: Offers a range of models for different scales of production.
- MetalMelt: Specializes in energy-efficient designs.
- GasAtom Machines: Provides affordable, entry-level equipment.
Market Pricing and Cost Trends
The pricing of gas atomizer equipment varies widely based on features, production capacity, and automation level. High-end models can cost upwards of $500,000, while more basic, smaller-scale machines may start around $50,000. The trend in recent years has seen a gradual decrease in prices due to technological advancements and increased competition among manufacturers.
Suppliers and Pricing Details
Nhà cung cấp | Model Available | Mức giá | Special Features |
---|---|---|---|
PowderTech Inc. | Precision Atomizer 850 | $$$$ | Superior temperature control |
AtomizeCo | UltraAtom 3000 | $$ | Energy-efficient, compact |
MetalMelt | Atomizer Pro 500 | $$$ | Versatile, multiple metals |
GasAtom Machines | Econo Atomizer 200 | $ | Cost-effective, basic features |
Advantages and Limitations of Gas Atomizer Equipment
When choosing gas atomizer equipment, it’s important to weigh the advantages against the limitations to ensure it fits your specific needs.
Strengths and Best Use Cases
Gas atomizers are best suited for applications requiring high precision and consistency in powder production. Their ability to handle a wide range of materials and produce uniform particles makes them ideal for industries like aerospace, medical, and additive manufacturing.
Challenges and Limitations
However, the high cost, energy consumption, and complexity of operation can be significant barriers for smaller businesses or those new to the technology.
Advantages vs. Limitations
Advantage | Limitation |
---|---|
High precision | High initial investment |
Versatility | Energy intensive |
Khả năng mở rộng | Requires skilled operators |
Consistency | Complex maintenance |
Reliable quality | Limited material compatibility |
Future Trends in Gas Atomization Technology
The future of gas atomization technology looks promising, with several emerging trends likely to shape the industry in the coming years.
Emerging Technologies and Innovations
- Advanced Automation: The incorporation of AI and machine learning to optimize the atomization process in real-time.
- Eco-Friendly Designs: Development of more energy-efficient machines and processes to reduce environmental impact.
- Enhanced Material Compatibility: Research into new materials that can be atomized, broadening the range of applications.
Future Market Trends and Predictions
As the demand for high-quality metal powders
continues to grow, especially in additive manufacturing and aerospace, the market for gas atomizer equipment is expected to expand. Prices may become more competitive as more players enter the market, and advancements in technology may lower operational costs, making gas atomization accessible to a wider range of industries.
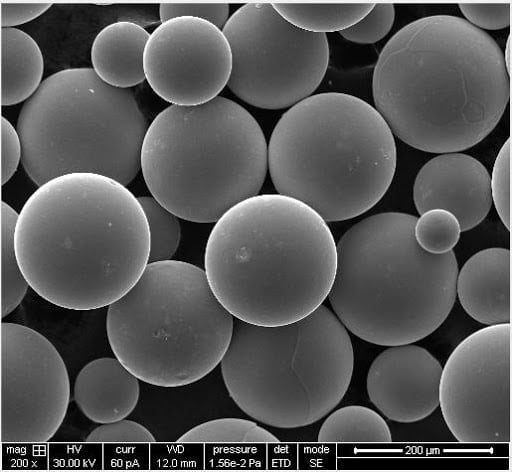
Câu hỏi thường gặp
Question | Answer |
---|---|
What is the primary advantage of gas atomization? | High precision and uniformity in powder production. |
What metals can be processed using gas atomizers? | A wide range, including stainless steel, titanium, aluminum, nickel, and cobalt. |
How much does a typical gas atomizer cost? | Prices range from $50,000 to over $500,000, depending on features and capacity. |
Is gas atomization suitable for small-scale production? | While possible, the high costs and complexity make it more suited for medium to large-scale production. |
What industries benefit the most from gas atomization? | Aerospace, medical, automotive, and additive manufacturing are the primary beneficiaries. |
Kết luận
Gas atomizer equipment represents a cornerstone of modern manufacturing, offering unparalleled precision and versatility in the production of metal powders. While the initial investment and operational complexity can be high, the benefits in terms of product quality and consistency are significant. Whether you’re involved in aerospace, medical, automotive, or additive manufacturing, understanding the intricacies of gas atomization can help you make informed decisions about the equipment and processes you choose. As technology continues to advance, the future of gas atomization looks bright, with new innovations poised to make the process even more efficient and accessible.
About 3DP mETAL
Product Category
LIÊN HỆ
Bạn có thắc mắc không? Hãy gửi tin nhắn ngay cho chúng tôi! Sau khi nhận được tin nhắn của bạn, chúng tôi sẽ xử lý yêu cầu của bạn với cả một đội ngũ.