Hastelloy X powder is a revolutionary material taking the world of manufacturing by storm. Imagine crafting intricate parts boasting exceptional resistance to heat, corrosion, and wear – that’s the magic of Hastelloy X powder. But what exactly is it, and why is it causing such a stir? Buckle up, because we’re diving deep into the fascinating world of this super material.
Introduction to Hastelloy X Powder
Hastelloy X powder is a specialized form of the high-performance alloy, Hastelloy X. This nickel-chromium-iron-molybdenum alloy has long been prized for its ability to withstand harsh environments. Now, in powder form, Hastelloy X unlocks a whole new level of design freedom and intricate part creation.
Think of it this way: Imagine building intricate Lego structures, but instead of colorful plastic bricks, you’re using a super-strong, heat-resistant metal. That’s the potential of Hastelloy X powder – complex geometries with the incredible properties of the original Hastelloy X alloy.
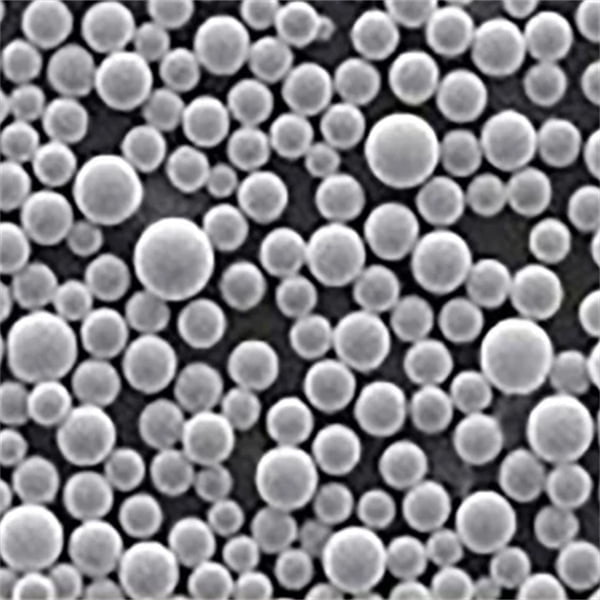
Characteristics of Hastelloy X Powder
So, what makes Hastelloy X powder so special? Let’s break down its key characteristics:
- Superior Strength and High-Temperature Performance: Hastelloy X powder retains the exceptional high-temperature strength of its bulk counterpart. It can withstand scorching temperatures exceeding 1200°F (650°C) without losing its structural integrity. This makes it ideal for applications in aerospace, power generation, and chemical processing plants.
- Outstanding Corrosion Resistance: Hastelloy X powder boasts phenomenal resistance to a wide range of corrosive environments. Whether it’s harsh chemicals, oxidizing agents, or saltwater, this powder shrugs them off with ease. This characteristic makes it perfect for components used in marine environments, pollution control equipment, and chemical processing vessels.
- Excellent Weldability and Fabricability: Unlike some other high-performance powders, Hastelloy X powder is surprisingly weldable and fabricable. This means manufacturers can easily join components made with this powder, creating complex assemblies without compromising the material’s properties.
Applications of Hastelloy X Powder
With its unique blend of properties, Hastelloy X powder finds application in a diverse range of industries:
- Ngành hàng không vũ trụ: In the high-flying world of aerospace, weight reduction is paramount. Hastelloy X powder allows for the creation of lightweight yet incredibly strong components for jet engines, rocket parts, and airframes. Its high-temperature resistance makes it perfect for withstanding the intense heat generated by jet engines.
- Xử lý hóa học: Chemical processing plants are battlegrounds for harsh chemicals and corrosive environments. Hastelloy X powder steps up to the challenge, offering exceptional resistance to these conditions. It can be used to manufacture pipes, valves, and reaction vessels that can handle even the most aggressive chemicals.
- Oil and Gas: The unforgiving world of oil and gas exploration demands materials that can handle extreme pressures and temperatures. Hastelloy X powder is a game-changer, allowing for the creation of downhole tools, wellhead components, and pipelines that resist corrosion and maintain their strength in these demanding environments.
- Sản xuất năng lượng: From traditional fossil fuel power plants to cutting-edge nuclear reactors, Hastelloy X powder plays a vital role. It can be used to manufacture turbine blades, heat exchangers, and reactor components that can withstand the intense heat and pressure associated with power generation.
Beyond these core applications, Hastelloy X powder holds promise for various other industries:
- Medical Devices: The biocompatible nature of Hastelloy X powder makes it a potential candidate for the creation of medical implants and surgical tools that offer superior strength and corrosion resistance.
- Ô tô: The ever-evolving automotive industry is constantly seeking ways to improve performance and efficiency. Hastelloy X powder could be used to create lightweight, high-strength components for exhaust systems and turbochargers.
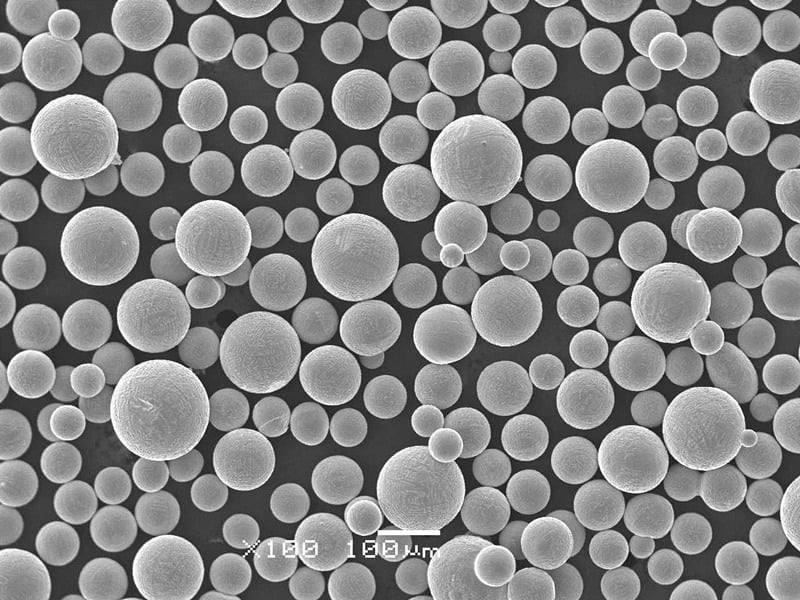
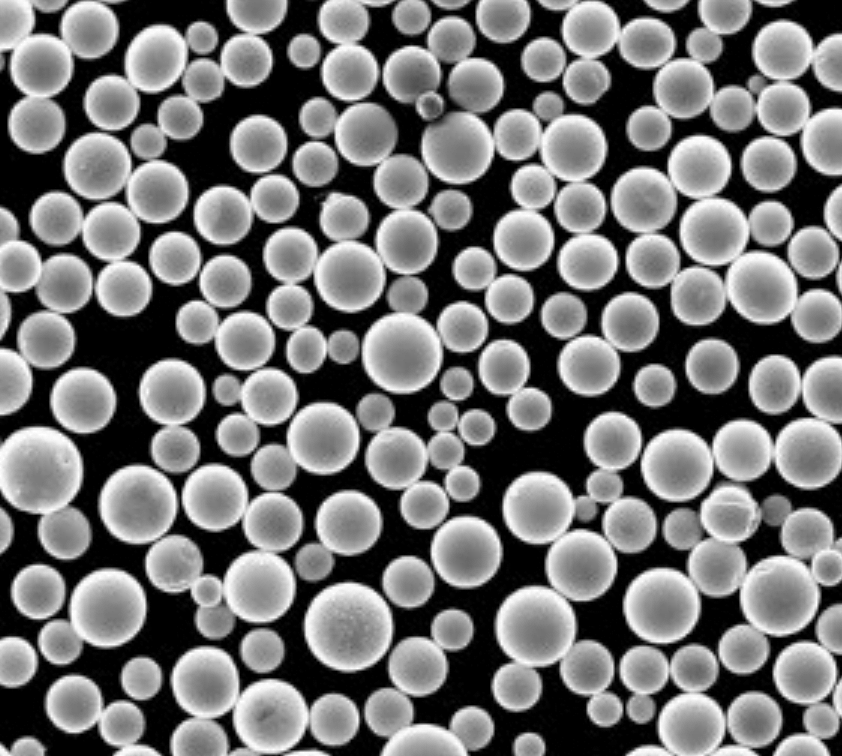
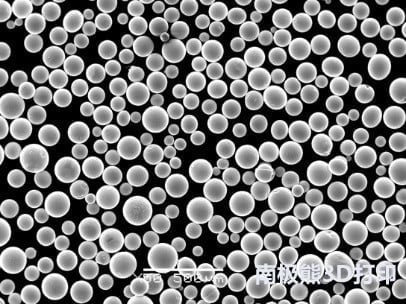
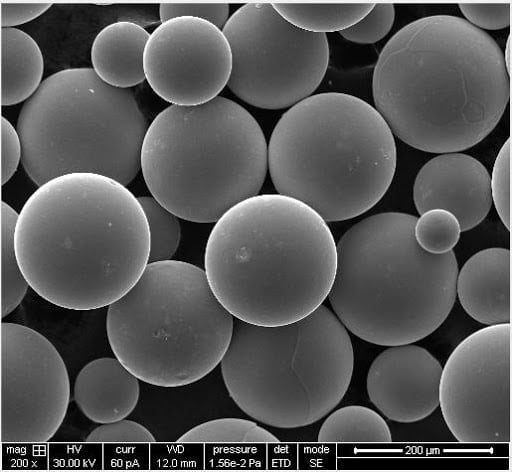
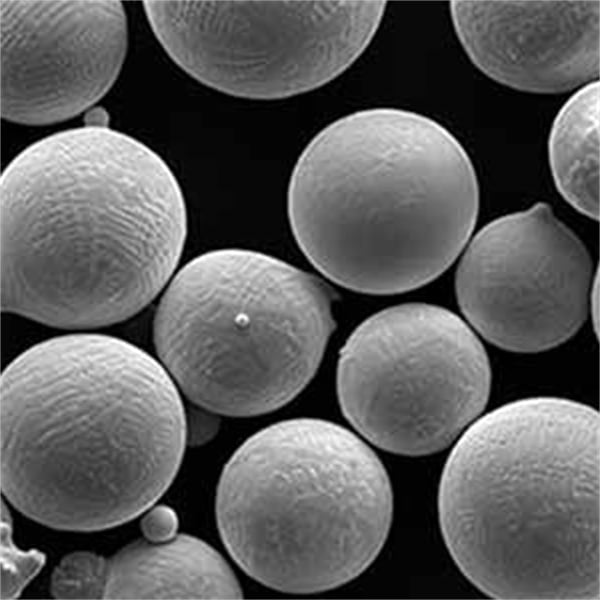
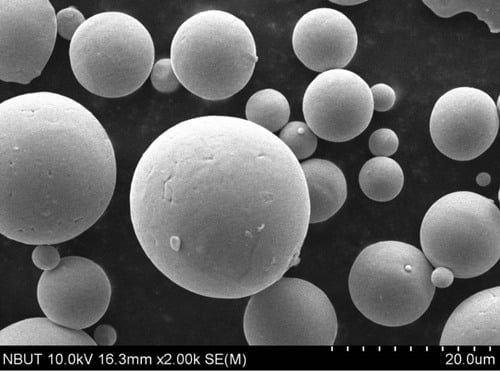
Advantages and Considerations of Hastelloy X Powder
While Hastelloy X powder boasts a remarkable set of properties, it’s essential to consider some factors:
- Cost: Compared to traditional manufacturing methods, creating parts with Hastelloy X powder can be more expensive. The specialized equipment and processes involved contribute to the higher cost.
- Limited Availability: As a relatively new technology, Hastelloy X powder might not be readily available from all manufacturers. However, as its adoption grows, availability is expected to improve.
- Post-processing: Parts created with Hastelloy X powder might require specialized post-processing techniques to achieve the desired final properties.
However, the advantages of Hastelloy X powder often outweigh these considerations:
- Design Freedom: This powder allows for the creation of complex geometries that would be impossible with traditional manufacturing methods. This opens doors for innovative designs that optimize performance and weight reduction.
- Reduced Waste: Additive manufacturing with Hastelloy X powder often minimizes material waste compared to traditional subtractive techniques like machining. This translates to cost savings and environmental benefits.
- Improved Performance: The ability to create intricate internal structures with Hastelloy X powder can lead to components with improved heat transfer, fluid flow, and overall performance.
Making an informed decision about Hastelloy X powder requires careful consideration of both its advantages and limitations. For applications where high performance, intricate designs, and long-term durability are paramount, the benefits of Hastelloy X powder can outweigh the initial cost considerations.
Manufacturing Techniques for Hastelloy X Powder
Hastelloy X powder comes alive through specialized additive manufacturing (AM) techniques. Here are some of the most common methods:
- Selective Laser Melting (SLM): This technique uses a high-powered laser to selectively melt Hastelloy X powder layer by layer, building the desired 3D object. SLM offers high precision and detail, making it ideal for complex geometries.
- Electron Beam Melting (EBM): Similar to SLM, EBM uses a focused electron beam to melt the powder. This technique can handle larger powder particles and is often used for applications requiring high strength and fatigue resistance.
- Binder Jetting: This method uses a liquid binder to selectively glue Hastelloy X powder particles together. The resulting part is then heat-treated to achieve its final properties. Binder jetting offers a faster and more affordable option compared to SLM and EBM, but the final product might have slightly lower mechanical properties.
The choice of AM technique depends on factors like the desired part complexity, dimensional accuracy, mechanical properties, and production cost.
Future Outlook for Hastelloy X Powder
The future of Hastelloy X powder is bright. As additive manufacturing technology continues to evolve, we can expect to see:
- Reduced Costs: Advancements in AM equipment and powder production are expected to bring down the cost of using Hastelloy X powder, making it more accessible to a wider range of applications.
- Improved Powder Characteristics: Manufacturers are constantly developing new methods to produce Hastelloy X powder with tighter particle size distribution and improved flowability. This will lead to better printability and potentially even higher performance of finished parts.
- Expansion into New Markets: As the benefits of Hastelloy X powder become more widely recognized, we can expect to see its adoption in new and exciting markets like biomedical devices, electronics, and even consumer goods.
Overall, Hastelloy X powder is poised to revolutionize manufacturing for demanding applications. Its unique combination of properties and the ever-evolving world of additive manufacturing paint a promising picture for the future.
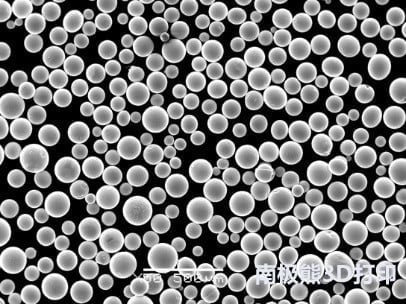
Câu hỏi thường gặp
Q: What are the typical particle sizes of Hastelloy X powder?
A: Hastelloy X powder is typically available in a range of particle sizes, from 15 to 150 micrometers. The specific size chosen depends on the desired application and the AM technique being used.
Q: Can Hastelloy X powder be recycled?
A: Yes, Hastelloy X powder can be recycled to a certain extent. Unused powder can be collected and reused in subsequent printing processes. However, there might be some limitations on the number of recycling cycles due to potential changes in powder properties.
Q: How strong is Hastelloy X powder compared to bulk Hastelloy X?
A: When properly manufactured using optimized AM techniques, Hastelloy X powder can achieve mechanical properties very close to those of bulk Hastelloy X. However, factors like porosity and post-processing techniques can influence the final strength of the printed part.
Q: What are some of the challenges associated with using Hastelloy X powder?
A: Some of the challenges include the high cost of the powder itself, the need for specialized AM equipment and expertise, and the potential for part defects due to factors like powder flowability and laser parameters.
Q: Where can I find more information about Hastelloy X powder?
A: Several manufacturers of Hastelloy X powder and AM equipment providers offer detailed information and resources on their websites. Additionally, industry publications and research papers can provide deeper insights into the technical aspects of using Hastelloy X powder.
About 3DP mETAL
Product Category
LIÊN HỆ
Bạn có thắc mắc không? Hãy gửi tin nhắn ngay cho chúng tôi! Sau khi nhận được tin nhắn của bạn, chúng tôi sẽ xử lý yêu cầu của bạn với cả một đội ngũ.