When it comes to engineering, especially in areas like aerospace, automotive, and heavy machinery, high-stress engine applications play a crucial role. These applications demand materials and components that can withstand extreme conditions, such as high temperatures, intense pressures, and constant wear and tear. One key element in these high-stress environments is the use of advanced metal powders. In this article, we will dive deep into high-stress engine applications, explore various metal powder models, and provide you with a thorough understanding of their characteristics, uses, and advantages.
Overview of High-Stress Engine Applications
High-stress engine applications refer to any engineering scenario where the engine components must endure extreme conditions. This includes everything from jet engines and rocket propulsion systems to racing car engines and industrial turbines. The materials used in these engines must not only survive but thrive under these conditions, ensuring reliability and performance.
Key Points:
- Extremes of Temperature and Pressure: These engines operate at high temperatures and pressures.
- Material Durability: The materials need to resist wear, corrosion, and deformation.
- Performance Reliability: Consistent performance under stress is critical.
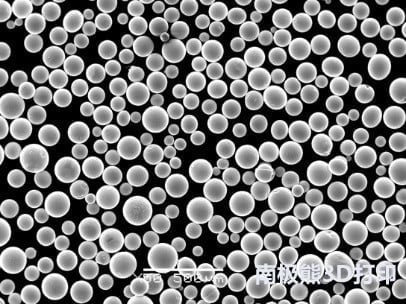
Importance of Metal Powders in High-Stress Applications
Metal powders are a cornerstone in the development and manufacturing of components for high-stress engine applications. Their ability to be tailored at a microscopic level allows for enhanced properties that are critical in these demanding environments.
Metal Powder Model | Sáng tác | thuộc tính | Đặc điểm |
---|---|---|---|
Inconel 718 | Nickel-Chromium | High strength, corrosion-resistant, heat-resistant | Excellent fatigue and creep resistance |
Hastelloy X | Nickel-Chromium-Iron-Molybdenum | Exceptional oxidation resistance, high temperature strength | Great weldability and formability |
Ti-6Al-4V | Titanium-Aluminum-Vanadium | High strength-to-weight ratio, corrosion-resistant | Biocompatible, excellent for aerospace applications |
MAR-M247 | Nickel-Based Superalloy | High temperature stability, corrosion-resistant | Used in turbine blades, nozzles |
CoCrMo | Cobalt-Chromium-Molybdenum | Wear and corrosion-resistant | Common in biomedical applications and gas turbines |
Nimonic 80A | Nickel-Chromium | High strength, heat-resistant | Ideal for gas turbine components |
MP35N | Nickel-Cobalt-Chromium-Molybdenum | High strength, corrosion-resistant | Excellent for marine and aerospace applications |
Haynes 230 | Nickel-Chromium-Tungsten-Molybdenum | Oxidation resistant, high temperature strength | Used in industrial furnace applications |
CMSX-4 | Nickel-Based Single Crystal Superalloy | Exceptional creep and oxidation resistance | Utilized in jet engine turbine blades |
Rene 41 | Nickel-Chromium-Molybdenum | High strength, heat-resistant | Suitable for high-temperature bolting applications |
Applications of Metal Powders in High-Stress Engine Environments
Ứng dụng | Metal Powder Model | Why It’s Used |
---|---|---|
Jet Engines | Inconel 718, CMSX-4 | High temperature and stress resistance, durability |
Rocket Engines | MAR-M247, Hastelloy X | Exceptional high-temperature performance and oxidation resistance |
Automotive Racing | Ti-6Al-4V, MP35N | High strength-to-weight ratio, durability under stress |
Industrial Turbines | Nimonic 80A, Haynes 230 | Heat resistance, corrosion resistance |
Biomedical Implants | CoCrMo, Ti-6Al-4V | Biocompatibility, wear resistance |
Ứng dụng biển | MP35N, Rene 41 | Corrosion resistance, high strength |
Specifications and Standards for Metal Powders
Metal Powder Model | Specifications | Sizes (microns) | Grades | Tiêu chuẩn |
---|---|---|---|---|
Inconel 718 | AMS 5662, ASTM B637 | 15-53, 45-106 | Aerospace, Industrial | AMS 5662, ASTM B637 |
Hastelloy X | AMS 5536, ASTM B572 | 15-45, 45-90 | Industrial, Chemical | AMS 5536, ASTM B572 |
Ti-6Al-4V | AMS 4911, ASTM F136 | 25-45, 45-90 | Biomedical, Aerospace | AMS 4911, ASTM F136 |
MAR-M247 | AMS 5771, PWA 1477 | 15-53, 45-106 | Turbine, Aerospace | AMS 5771, PWA 1477 |
CoCrMo | ASTM F1537 | 10-45, 45-90 | Biomedical, Industrial | ASTM F1537 |
Nimonic 80A | BS HR 1, ASTM B637 | 15-53, 45-106 | Turbine, Industrial | BS HR 1, ASTM B637 |
MP35N | AMS 5844, ASTM F562 | 15-45, 45-106 | Aerospace, Marine | AMS 5844, ASTM F562 |
Haynes 230 | AMS 5878, ASTM B572 | 15-53, 45-106 | Industrial, Turbine | AMS 5878, ASTM B572 |
CMSX-4 | PWA 1484, AMS 5884 | 10-45, 45-90 | Aerospace, Turbine | PWA 1484, AMS 5884 |
Rene 41 | AMS 5712, ASTM B172 | 15-53, 45-106 | Aerospace, Industrial | AMS 5712, ASTM B172 |
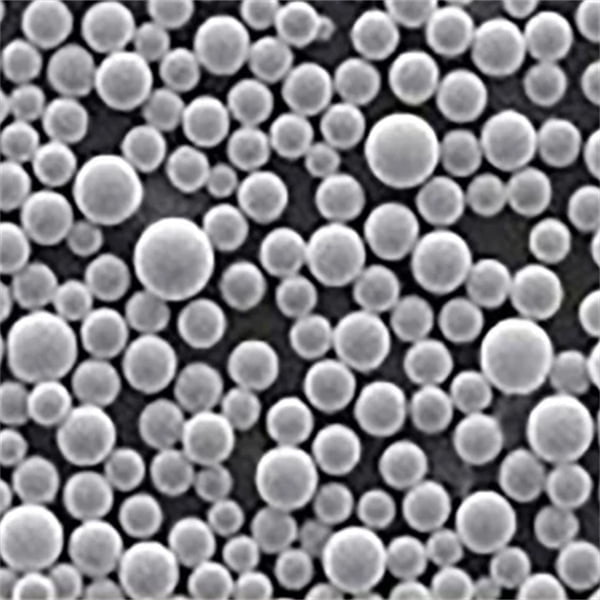
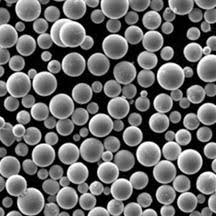
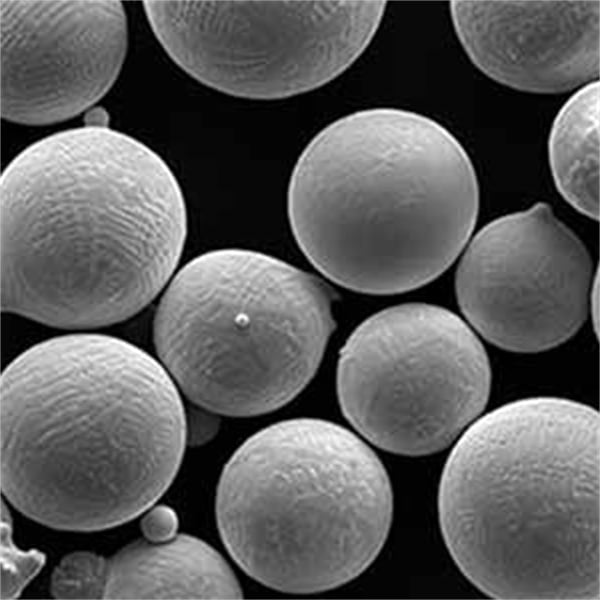
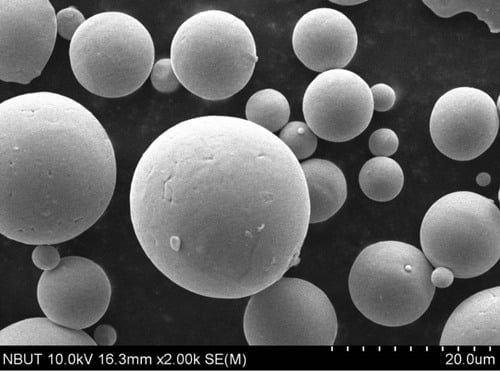
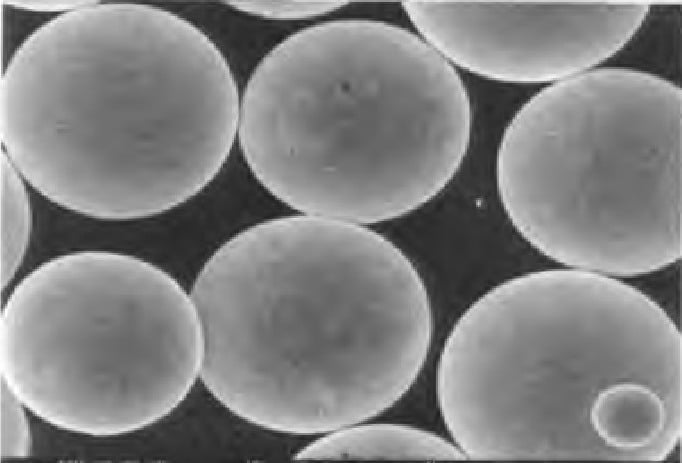
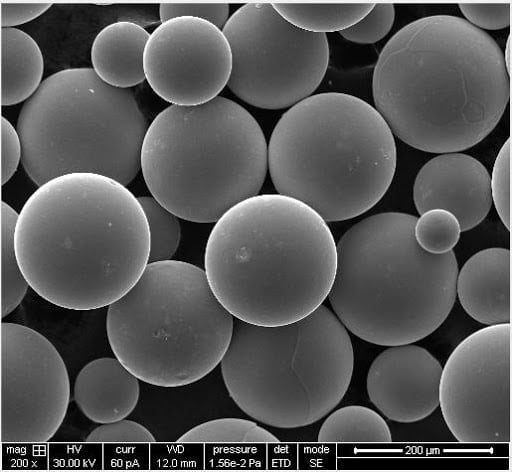
Suppliers and Pricing Details
Nhà cung cấp | Metal Powder Model | Giá theo 1kg | Bulk Discounts | Lead Time |
---|---|---|---|---|
Carpenter Technology | Inconel 718, Ti-6Al-4V | $150 – $300 | Yes | 4-6 weeks |
ATI Metals | Hastelloy X, Rene 41 | $200 – $350 | Yes | 6-8 weeks |
Sandvik Materials | CoCrMo, MP35N | $180 – $320 | Yes | 5-7 weeks |
Höganäs AB | Nimonic 80A, Haynes 230 | $160 – $290 | Yes | 4-6 weeks |
HC Starck | CMSX-4, MAR-M247 | $220 – $400 | Yes | 6-8 weeks |
Comparing Metal Powders for High-Stress Applications
Metal Powder Model | Lợi ích | Nhược điểm |
---|---|---|
Inconel 718 | High strength, corrosion-resistant | Expensive, difficult to machine |
Hastelloy X | Excellent high-temperature strength | Costly, limited availability |
Ti-6Al-4V | Lightweight, strong, biocompatible | Expensive, can be difficult to work with |
MAR-M247 | High temperature stability, strong | Expensive, difficult to manufacture |
CoCrMo | Wear and corrosion-resistant | Expensive, heavy |
Nimonic 80A | Heat-resistant, strong | Limited applications, expensive |
MP35N | High strength, corrosion-resistant | Very expensive, limited suppliers |
Haynes 230 | Oxidation resistant, durable | Expensive, limited high-temperature usage |
CMSX-4 | Exceptional creep and oxidation resistance | Very expensive, difficult to produce |
Rene 41 | High strength, heat-resistant | Costly, challenging to machine |
Detailed Examination of Metal Powder Models
Inconel 718
Inconel 718 is a nickel-chromium alloy known for its excellent strength and corrosion resistance at high temperatures. It’s commonly used in jet engines and gas turbines due to its remarkable performance under stress. This alloy is also prized for its resistance to oxidation and its ability to maintain its mechanical properties over a wide temperature range.
Hastelloy X
Hastelloy X is another high-performance nickel-chromium alloy, but with added
iron and molybdenum. This composition grants it exceptional oxidation resistance and high-temperature strength. It’s a popular choice for applications in gas turbine engines and chemical processing due to its robustness and ability to withstand extreme conditions.
Ti-6Al-4V
This titanium alloy is renowned for its high strength-to-weight ratio and corrosion resistance, making it ideal for aerospace applications. Ti-6Al-4V is also biocompatible, which has led to its use in medical implants. Its versatility and excellent mechanical properties under stress make it a standout material for high-stress engine components.
MAR-M247
MAR-M247 is a nickel-based superalloy known for its high temperature stability and corrosion resistance. It’s extensively used in turbine blades and nozzles, where it can handle the severe conditions present in jet engines and other high-stress environments.
CoCrMo
Cobalt-chromium-molybdenum alloys are known for their wear and corrosion resistance, making them suitable for both industrial and biomedical applications. CoCrMo alloys are commonly found in gas turbines and medical implants, thanks to their excellent performance in harsh conditions.
Nimonic 80A
Nimonic 80A is a nickel-chromium alloy that offers high strength and heat resistance. It’s frequently used in gas turbines and other high-temperature applications where durability and reliability are critical.
MP35N
This nickel-cobalt-chromium-molybdenum alloy is highly resistant to corrosion and boasts high strength, making it suitable for aerospace and marine applications. MP35N’s exceptional properties come with a high price tag, but its performance justifies the cost in demanding environments.
Haynes 230
Haynes 230 is a nickel-chromium-tungsten-molybdenum alloy with excellent oxidation resistance and high-temperature strength. It’s often used in industrial furnace applications and other high-stress environments where durability under heat is essential.
CMSX-4
CMSX-4 is a single crystal superalloy designed for high-temperature performance. Its exceptional creep and oxidation resistance make it ideal for jet engine turbine blades, where it can withstand the extreme conditions found in modern aerospace engineering.
Rene 41
Rene 41 is a nickel-chromium-molybdenum alloy known for its high strength and heat resistance. It’s particularly suited for high-temperature bolting applications and other scenarios where maintaining mechanical properties at elevated temperatures is crucial.
Advantages of High-Stress Engine Applications
High-stress engine applications come with several advantages, particularly when using advanced metal powders:
- Enhanced Performance: These materials offer superior performance under extreme conditions, ensuring engines operate efficiently.
- Durability: The alloys are designed to resist wear, corrosion, and high temperatures, leading to longer-lasting components.
- Safety: High-stress engine applications require materials that can withstand stress without failing, ensuring the safety of operations in critical industries like aerospace and automotive.
Disadvantages of High-Stress Engine Applications
However, there are also some disadvantages to consider:
- Cost: High-performance alloys are expensive, both in terms of material costs and manufacturing processes.
- Manufacturing Challenges: These materials can be difficult to machine and form, requiring specialized equipment and techniques.
- Limited Availability: Some advanced alloys may have limited availability, leading to longer lead times and higher costs.
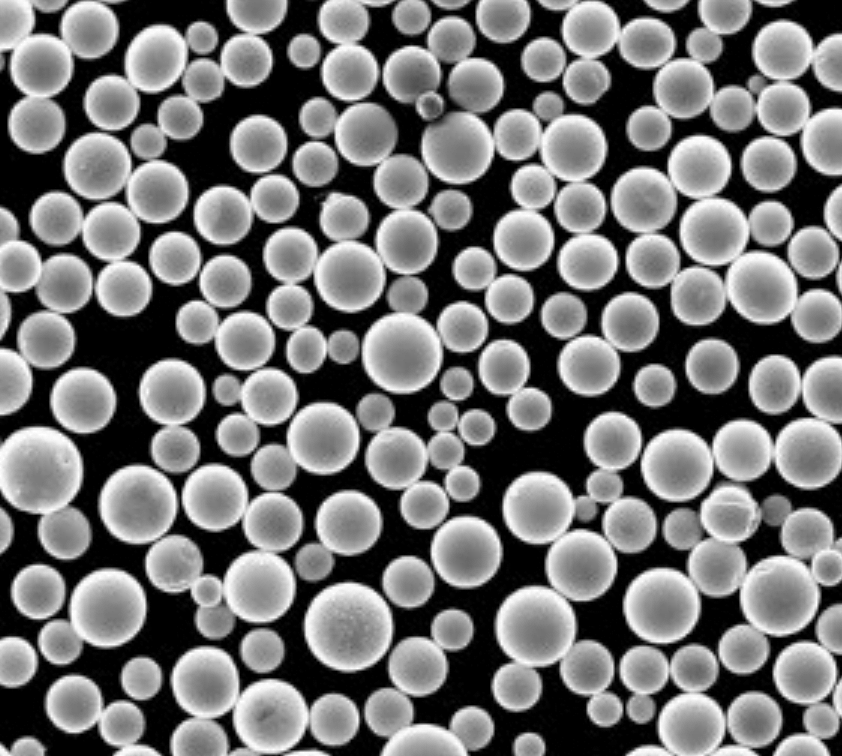
Câu hỏi thường gặp
What are high-stress engine applications?
High-stress engine applications refer to scenarios where engine components must endure extreme conditions, such as high temperatures, pressures, and constant wear. These applications are common in aerospace, automotive racing, and industrial turbines.
Why are metal powders important in high-stress applications?
Metal powders are crucial because they can be engineered to possess specific properties, such as high strength, corrosion resistance, and durability under extreme conditions. This makes them ideal for manufacturing components used in high-stress environments.
What is the difference between Inconel 718 and Hastelloy X?
Inconel 718 is known for its excellent strength and corrosion resistance at high temperatures, making it suitable for jet engines and gas turbines. Hastelloy X, on the other hand, offers exceptional oxidation resistance and high-temperature strength, making it ideal for gas turbine engines and chemical processing.
How is Ti-6Al-4V used in high-stress applications?
Ti-6Al-4V is used in high-stress applications due to its high strength-to-weight ratio, corrosion resistance, and biocompatibility. It’s commonly found in aerospace components and medical implants.
What are the advantages of using MAR-M247 in turbine blades?
MAR-M247 offers high temperature stability and corrosion resistance, making it ideal for turbine blades and nozzles. It can withstand the severe conditions present in jet engines and other high-stress environments.
Which metal powder is best for biomedical implants?
CoCrMo and Ti-6Al-4V are both excellent choices for biomedical implants. CoCrMo is known for its wear and corrosion resistance, while Ti-6Al-4V offers biocompatibility and high strength-to-weight ratio.
Are there any disadvantages to using high-performance metal powders?
Yes, high-performance metal powders can be expensive and challenging to manufacture. They may also have limited availability, leading to longer lead times and higher costs.
What are the key factors to consider when selecting a metal powder for high-stress applications?
When selecting a metal powder for high-stress applications, consider factors such as temperature resistance, corrosion resistance, strength, durability, and cost. It’s also important to evaluate the specific requirements of the application and the performance characteristics of the alloy.
Can high-stress engine materials be recycled?
Yes, many high-stress engine materials can be recycled. However, the recycling process can be complex and costly, requiring specialized equipment and techniques to reclaim and repurpose the materials effectively.
Where can I purchase metal powders for high-stress applications?
Metal powders for high-stress applications can be purchased from specialized suppliers such as Carpenter Technology, ATI Metals, Sandvik Materials, Höganäs AB, and HC Starck. Prices and availability may vary, so it’s important to research and contact suppliers for specific details.
How do metal powders enhance the performance of high-stress engines?
Metal powders enhance the performance of high-stress engines by providing materials that are specifically engineered for extreme conditions. This includes high strength, corrosion resistance, and durability under stress, ensuring reliable and efficient engine operation.
Kết luận
High-stress engine applications demand the use of advanced materials that can withstand extreme conditions. Metal powders such as Inconel 718, Hastelloy X, and Ti-6Al-4V offer the necessary properties to ensure durability, performance, and safety in these demanding environments. While these materials come with challenges such as cost and manufacturing complexity, their benefits in critical applications like aerospace, automotive racing, and industrial turbines make them indispensable. By understanding the characteristics, applications, and advantages of these metal powders, engineers and manufacturers can make informed decisions to optimize the performance and reliability of high-stress engines.
About 3DP mETAL
Product Category
LIÊN HỆ
Bạn có thắc mắc không? Hãy gửi tin nhắn ngay cho chúng tôi! Sau khi nhận được tin nhắn của bạn, chúng tôi sẽ xử lý yêu cầu của bạn với cả một đội ngũ.