Tổng quan
When it comes to metal powders, their shape, size, and purity are crucial factors that can significantly impact their performance in various applications. Among these, highly spherical powder stands out due to its unique properties and versatility. This guide will delve into everything you need to know about highly spherical powder, from its composition and characteristics to its applications and specifications.
What is Highly Spherical Powder?
Highly spherical powder is a type of metal powder that has been engineered to have a uniform, round shape. This shape is achieved through various manufacturing processes, and it provides numerous benefits in terms of flowability, packing density, and overall performance in industrial applications.
Composition of Highly Spherical Powder
The composition of highly spherical powder varies depending on the metal used. Here are some common metals used in the production of highly spherical powder along with their descriptions:
Metal Powder Model | Sáng tác | Miêu tả |
---|---|---|
Aluminum (AlSi10Mg) | Aluminum, Silicon, Magnesium | Lightweight, high strength, excellent corrosion resistance |
Titanium (Ti64) | Titanium, Aluminum, Vanadium | High strength-to-weight ratio, biocompatible, corrosion resistant |
Stainless Steel (316L) | Iron, Chromium, Nickel, Molybdenum | High corrosion resistance, good mechanical properties |
Đồng (Cu) | Đồng nguyên chất | Dẫn nhiệt và dẫn điện tuyệt vời |
Nickel (Ni625) | Nickel, Chromium, Molybdenum | High strength, oxidation, and corrosion resistance |
Cobalt-Chrome (CoCr) | Cobalt, Chromium | High wear and corrosion resistance, used in medical implants |
Iron (Fe) | Pure Iron | Good magnetic properties, used in electronics |
Kẽm (Zn) | Pure Zinc | Good corrosion resistance, used in galvanizing |
Magie (Mg) | Pure Magnesium | Lightweight, good strength-to-weight ratio |
Vonfram (W) | Pure Tungsten | High melting point, very dense, used in heavy-duty applications |
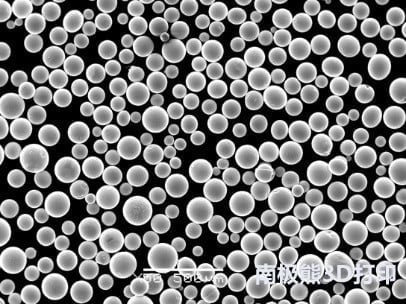
Characteristics of Highly Spherical Powder
Highly spherical powder offers several key characteristics that make it desirable for various industrial applications. Let’s explore these characteristics in detail:
Đặc điểm | Miêu tả |
---|---|
Khả năng chảy | Spherical powders have excellent flow properties, making them ideal for additive manufacturing and other powder metallurgy processes. |
Packing Density | Due to their uniform shape, spherical powders can achieve high packing densities, leading to stronger and denser final products. |
Diện tích bề mặt | Spherical powders have a lower surface area compared to irregularly shaped powders, which can affect sintering and melting behavior. |
Reactivity | The reduced surface area also leads to lower reactivity, making spherical powders more stable and easier to handle. |
Consistency | Highly spherical powders offer consistent performance due to their uniform shape and size distribution. |
Advantages of Highly Spherical Powder
Highly spherical powder offers several advantages over traditional, irregularly shaped powders. Here are some of the key benefits:
Advantage | Miêu tả |
---|---|
Better Flowability | The uniform shape allows for smoother flow in manufacturing processes, reducing clogs and improving efficiency. |
Higher Packing Density | Spherical powders can pack more closely together, leading to denser and stronger final products. |
Improved Surface Finish | Parts made from spherical powders often have a smoother surface finish, reducing the need for post-processing. |
Reduced Waste | The uniformity of spherical powders leads to more predictable results, minimizing waste and material costs. |
Cải thiện các tính chất cơ học | Components made from spherical powders typically exhibit superior mechanical properties due to the even distribution of particles. |
Applications of Highly Spherical Powder
Highly spherical powders are used in a wide range of applications across various industries. Here are some common uses:
Ứng dụng | Miêu tả |
---|---|
Additive Manufacturing (3D Printing) | Spherical powders are ideal for 3D printing due to their excellent flowability and packing density, resulting in high-quality prints. |
Luân kim thuật bột | Used in the production of complex metal parts through techniques such as pressing and sintering. |
"Phun nhiệt" | Spherical powders are used in thermal spraying to create coatings for corrosion and wear resistance. |
Điện tử | Used in the production of electronic components, such as conductive inks and pastes. |
Medical Implants | Biocompatible metals like titanium and cobalt-chrome are used to create medical implants with excellent mechanical properties. |
Hiệp công | Lightweight and high-strength spherical powders are used in the production of aerospace components. |
Ô tô | Used in the manufacturing of high-performance automotive parts, such as engine components and gears. |
Năng lượng | Utilized in the production of fuel cells, batteries, and other energy storage devices. |
Trang sức | Precious metal powders are used in jewelry making for intricate designs and smooth finishes. |
Catalysts | Spherical powders are used in catalytic converters and other chemical processes due to their high surface area and reactivity. |
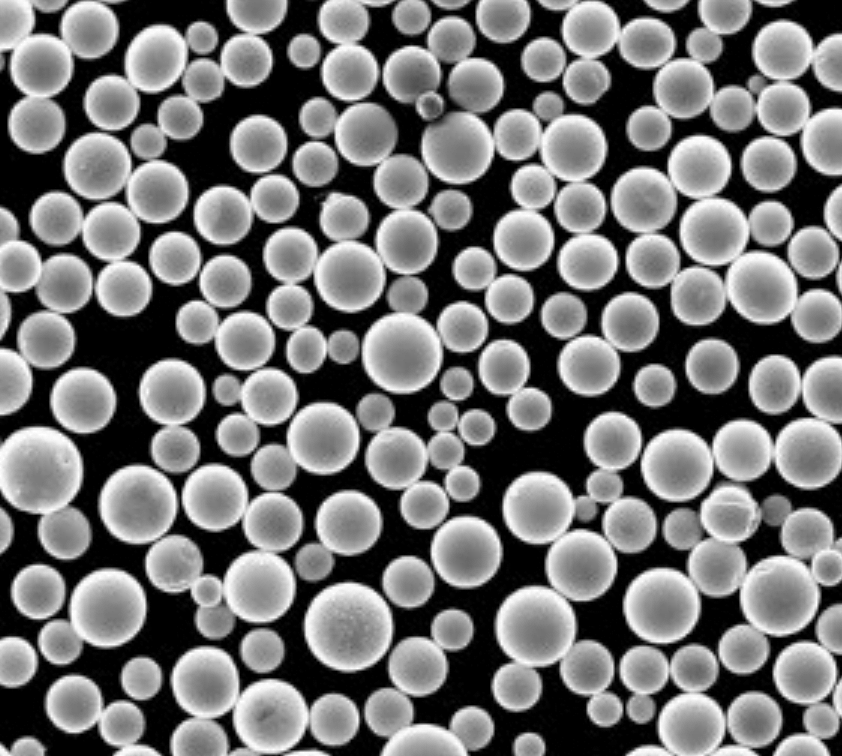
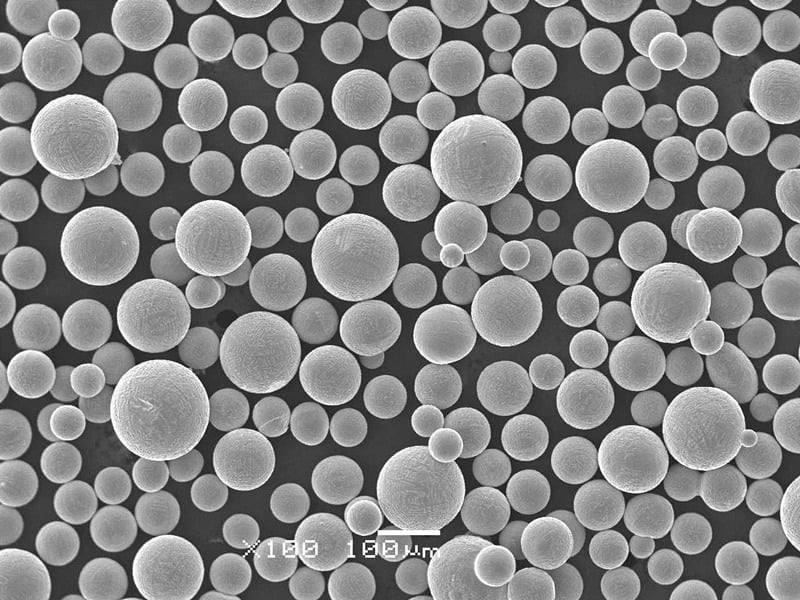
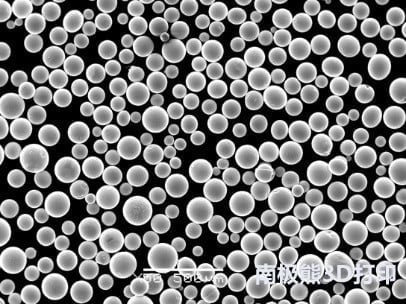
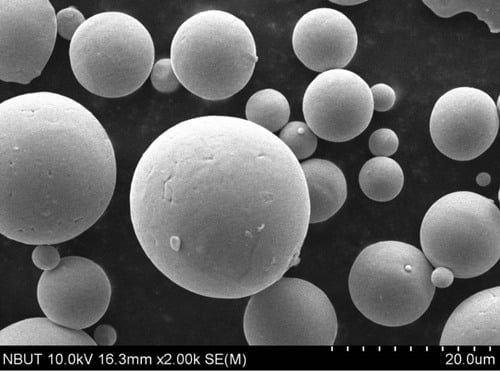
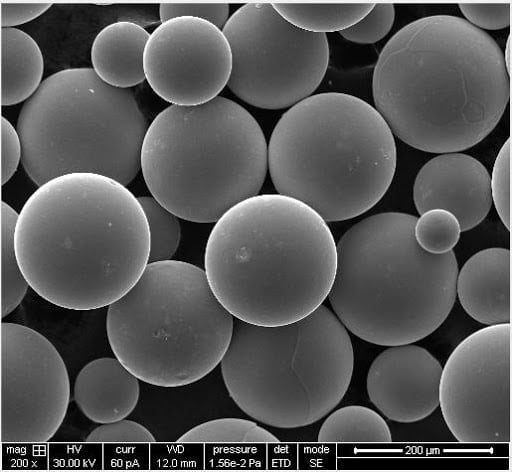
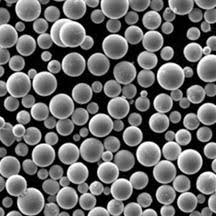
Specifications, Sizes, and Standards for Highly Spherical Powder
Understanding the specifications, sizes, and standards for highly spherical powders is crucial for selecting the right material for your application. Here is a detailed breakdown:
Đặc điểm kỹ thuật | Miêu tả |
---|---|
Kích thước hạt | Typically ranges from a few micrometers to several hundred micrometers, depending on the application. |
Sạch sẽ | High purity levels are essential to ensure the performance and reliability of the powder in various applications. |
Sphericity | Sphericity is a measure of how closely the shape of the particles approximates a perfect sphere. High sphericity is desirable for better flowability and packing density. |
Mật độ | The density of the powder can vary based on the metal used. Higher density powders are used in applications requiring more robust and durable components. |
Tiêu chuẩn | Various standards, such as ASTM and ISO, govern the quality and specifications of highly spherical powders. Adhering to these standards ensures consistency and reliability. |
Suppliers and Pricing of Highly Spherical Powder
The market for highly spherical powder is competitive, with various suppliers offering different grades and types of powders. Here is a comparison of some leading suppliers and their pricing:
Nhà cung cấp | Metal Powder | Price (per kg) | Additional Notes |
---|---|---|---|
Höganäs | Iron, Stainless Steel, Copper | $50 – $200 | Leading supplier with a wide range of metal powders. |
Công ty dịch vụ sản xuất phụ gia Carpenter | Titanium, Nickel, Cobalt-Chrome | $200 – $500 | High-quality powders for aerospace and medical applications. |
Sandvik Osprey | Aluminum, Titanium, Stainless Steel | $100 – $300 | Known for their precision and consistency. |
Vật liệu bột và lớp phủ cải tiến | Nickel, Cobalt-Chrome | $150 – $400 | Specializes in powders for thermal spraying and additive manufacturing. |
Công nghệ LPW | Titanium, Stainless Steel | $250 – $600 | Focuses on additive manufacturing with high-purity powders. |
Epson Atmix | Iron, Stainless Steel, Copper | $75 – $250 | Offers a wide range of powders with excellent flow properties. |
Tekna | Aluminum, Titanium, Nickel | $100 – $350 | High-performance powders for various industrial applications. |
PyroGenesis | Titanium, Nickel, Cobalt-Chrome | $200 – $450 | Known for their advanced plasma atomization process. |
Makin Metal Powders | Copper, Zinc, Aluminum | $50 – $150 | Provides cost-effective solutions for various industries. |
Valimet | Aluminum, Titanium, Stainless Steel | $80 – $300 | Offers a wide range of spherical powders for different applications. |
Comparing Highly Spherical Powder with Irregular Powders
When it comes to choosing between highly spherical powder and irregularly shaped powders, several factors come into play. Let’s compare these two types of powders:
Yếu tố | Highly Spherical Powder | Irregular Powder |
---|---|---|
Khả năng chảy | Excellent flow properties due to uniform shape | Poor flow properties due to irregular shapes |
Packing Density | High packing density, leading to denser final products | Lower packing density, resulting in less dense products |
Diện tích bề mặt | Lower surface area, affecting reactivity and sintering behavior | Higher surface area, which can increase reactivity and sintering rate |
Consistency | Consistent performance with predictable results | Variable performance due to inconsistent shapes and sizes |
Chi phí | Typically more expensive due to advanced manufacturing processes | Generally less expensive due to simpler production methods |
ỨNG DỤNG | Ideal for high-precision and high-performance applications such as aerospace, medical implants, and additive manufacturing. | More suited for applications where precision is less critical, such as basic metal processing and less demanding manufacturing processes. |
Pros and Cons of Highly Spherical Powder
To make an informed decision, it’s crucial to weigh the pros and cons of highly spherical powder compared to other types. Here’s a detailed breakdown:
Ưu điểm | Nhược điểm |
---|---|
Uniform Flowability | Higher Cost |
Spherical powders have excellent flow properties, reducing clogs and improving processing efficiency. | The advanced manufacturing process for spherical powders often results in higher costs compared to irregular powders. |
High Packing Density | Complex Manufacturing |
The uniform shape allows for better packing, leading to stronger and denser products. | Producing spherical powders requires sophisticated equipment and techniques. |
Smooth Surface Finish | Limited Availability |
Components made from spherical powders generally have a smoother finish, reducing the need for post-processing. | Some specialized spherical powders might not be widely available in all markets. |
Predictable Performance | Specific Application Needs |
Consistent shape and size lead to reliable performance and fewer defects. | Not all applications require the precision and performance benefits of spherical powders. |
Reduced Waste | Potential Over-specification |
The efficiency of spherical powders minimizes waste and material costs. | Using highly spherical powders for simple applications may be seen as over-specification. |
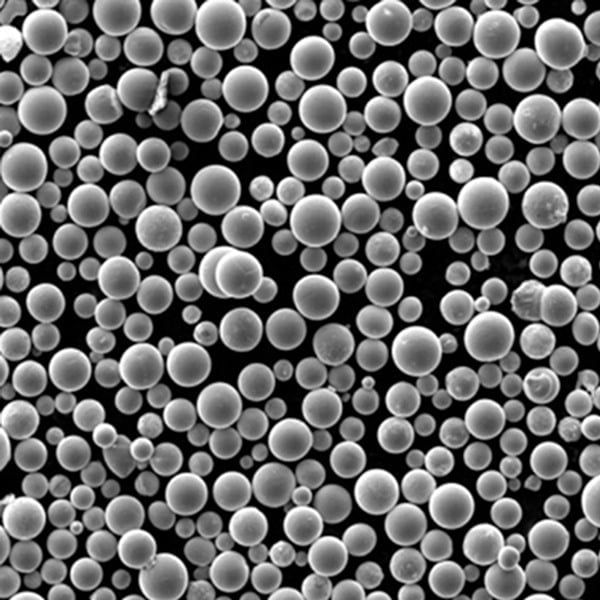
Câu hỏi thường gặp
Here are some common questions about highly spherical powder and their answers:
Question | Answer |
---|---|
What makes highly spherical powder different from other types of metal powders? | Highly spherical powder has a uniform round shape, which provides better flowability and packing density compared to irregularly shaped powders. |
What are the main benefits of using spherical powder in additive manufacturing? | Spherical powders improve the quality of 3D-printed parts by ensuring smooth flow and consistent layering, which leads to better surface finishes and stronger final products. |
Can spherical powder be used in all types of powder metallurgy processes? | While spherical powders are excellent for many applications, they are particularly beneficial for processes that require precise control over powder flow and packing, such as additive manufacturing and high-density sintering. |
How does the cost of spherical powder compare to irregular powders? | Spherical powders tend to be more expensive due to the advanced manufacturing processes required to produce them. However, their benefits often justify the higher cost in high-performance applications. |
What industries most commonly use highly spherical powders? | Highly spherical powders are widely used in industries such as aerospace, medical devices, electronics, automotive, and energy due to their superior performance characteristics. |
Are there any specific standards for highly spherical powders? | Yes, various standards such as ASTM and ISO define the quality and specifications for spherical powders, ensuring consistency and reliability in their applications. |
How can I choose the right type of spherical powder for my application? | Consider factors such as particle size, metal composition, flowability, and specific performance requirements of your application. Consulting with suppliers and reviewing technical data can also help in making the right choice. |
Kết luận
Highly spherical powder represents a significant advancement in metal powder technology, offering numerous benefits in terms of flowability, packing density, and overall performance. Whether you’re involved in additive manufacturing, powder metallurgy, or any other high-precision application, understanding the properties, advantages, and applications of spherical powders can help you make informed decisions and optimize your processes.
By carefully considering the specifications, costs, and potential applications, you can leverage the unique benefits of highly spherical powder to achieve superior results in your projects.
About 3DP mETAL
Product Category
LIÊN HỆ
Bạn có thắc mắc không? Hãy gửi tin nhắn ngay cho chúng tôi! Sau khi nhận được tin nhắn của bạn, chúng tôi sẽ xử lý yêu cầu của bạn với cả một đội ngũ.