Imagine a world where tiny air bubbles trapped inside a crucial engine component can be squeezed out, leaving behind a super-strong, ultra-dense material. That’s the magic of Ép đẳng tĩnh nhiệt (HIP), a game-changing technology that takes metal parts, ceramics, and even some polymers to a whole new level.
In this comprehensive guide, we’ll delve into the fascinating world of HIP, exploring its core principles, the intricate dance of heat and pressure, and the impressive benefits it unlocks for various industries. Buckle up and get ready to discover how this technology is transforming the way we manufacture critical components.
The Principle of Hot Isostatic Pressing
At its core, HIP is a bit like a high-tech pressure cooker for industrial materials. Here’s the basic idea:
- The Chamber: The object to be treated is placed inside a high-pressure vessel made from a super-strong material that can withstand intense heat.
- Heating Up: The vessel is then heated to extremely high temperatures, often reaching thousands of degrees Celsius (depending on the material being treated). This mimics the conditions the material might experience during its actual use.
- The Squeeze Play: While the material is nice and hot and its internal structure is more flexible, an inert gas (usually argon) is introduced into the chamber. This gas applies immense isotropic pressure (meaning equal pressure from all directions) on the object. Imagine millions of tiny invisible hands pushing in from every direction.
The Analogy: Think of a sponge soaked with water. When you squeeze it, the water gets pushed out, leaving behind a denser, more compact sponge. In HIP, the air pockets trapped within the material act like the water in the sponge, and the hot isostatic pressure acts like your squeezing hand, forcing out the air and densifying the material.
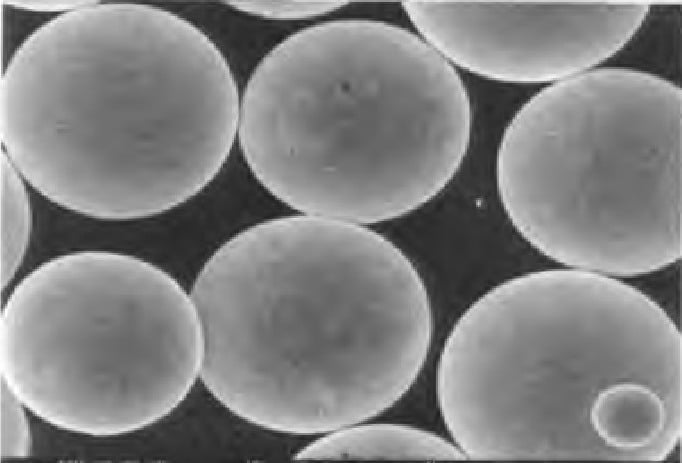
The Process Flow of Ép đẳng tĩnh nhiệt
Now that we understand the underlying principle, let’s take a closer look at the typical process flow of hot isostatic pressing:
- Preparation: The object to be treated undergoes a thorough cleaning process to remove any surface contaminants that could react with the high temperatures and pressure during HIP.
- Sealing (Optional): For certain materials or complex geometries, the object might be sealed in a special container to prevent any internal reactions or distortions during the process.
- Loading: The prepared object is carefully loaded into the high-pressure vessel.
- Heating and Pressurization: The vessel is evacuated to remove any air and then filled with the inert gas (usually argon) at the desired pressure. The temperature is then gradually increased according to a predetermined profile specific to the material being treated.
- Holding: Once the target temperature and pressure are reached, the system is held at these conditions for a specific duration to allow for complete densification and any desired metallurgical reactions to occur.
- Cooling and Depressurization: The temperature and pressure are slowly reduced in a controlled manner to minimize any residual stresses in the object.
- Unloading and Inspection: After cooling down, the vessel is depressurized, and the object is removed for final inspection.
The Importance of Time and Temperature: The specific time and temperature used in the HIP process are crucial factors that depend on the material being treated and the desired outcome. For instance, higher temperatures and longer holding times might be needed for materials that require extensive diffusion bonding or microstructural changes.
The Advantages of Ép đẳng tĩnh nhiệt
Hot Isostatic Pressing offers a unique set of advantages that make it a valuable tool across various industries. Here are some of the key benefits:
- Improved Mechanical Properties: By eliminating porosity (tiny air bubbles), HIP leads to denser, stronger materials with enhanced mechanical properties like tensile strength, fatigue resistance, and creep resistance. This translates to components that can withstand higher loads, last longer, and perform more reliably under demanding conditions.
- Enhanced Microstructure: The combination of heat and pressure can promote grain growth and improve the overall microstructure of the material. This can further enhance mechanical properties and even lead to improved electrical conductivity or corrosion resistance in certain materials.
- Closure of Internal Defects: Hot Isostatic Pressing can effectively close internal defects like cracks, voids, and shrinkage cavities that might be present in castings or components manufactured using other methods. This results in a more uniform and reliable material with improved performance and predictability.
- Improved Bonding: HIP is a powerful tool for diffusion bonding. By applying heat and pressure simultaneously, HIP can create a strong metallurgical bond between similar or dissimilar materials. This opens doors to the creation of composite structures with unique properties.
- Stress Relief: The controlled heating and cooling cycle in HIP can help relieve residual stresses that might be introduced during the manufacturing process. This can improve dimensional stability and reduce the risk of cracking or distortion during subsequent machining or service.
- Improved Machinability: Denser materials with a more uniform microstructure often exhibit better machinability. This translates to faster machining times, reduced tool wear, and improved surface finishes on the final component.
- Material Versatility: Hot Isostatic Pressing is not limited to metals. It can be effectively applied to a wide range of materials, including ceramics, some polymers, and even metal matrix composites. This versatility makes it a valuable tool for various industries with diverse material needs.
A Balancing Act: It’s important to note that the benefits of HIP need to be weighed against the processing costs. The high temperatures and pressures required can be energy-intensive, and the specialized equipment can be expensive. However, for critical applications where performance and reliability are paramount, the advantages of HIP often outweigh the costs.
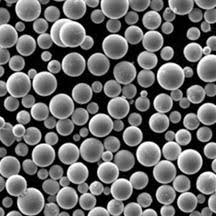
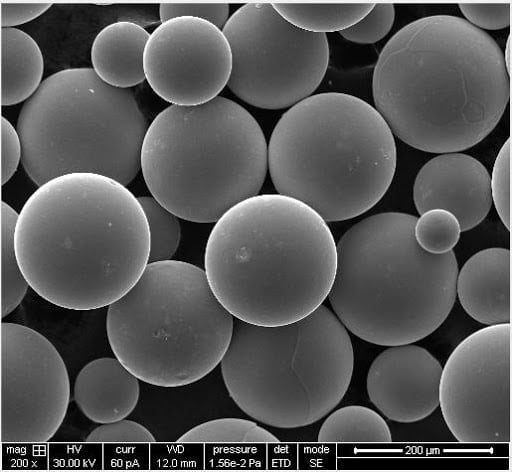
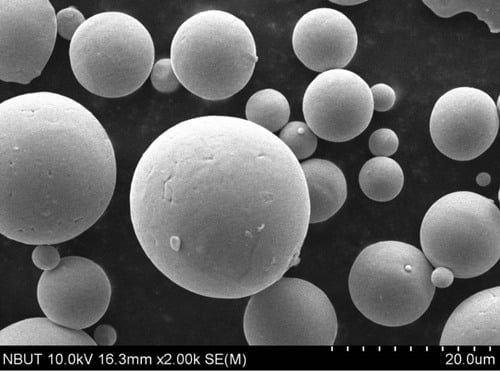
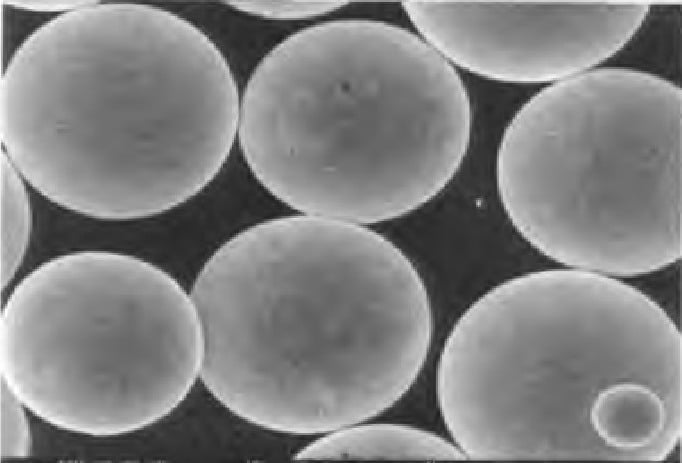
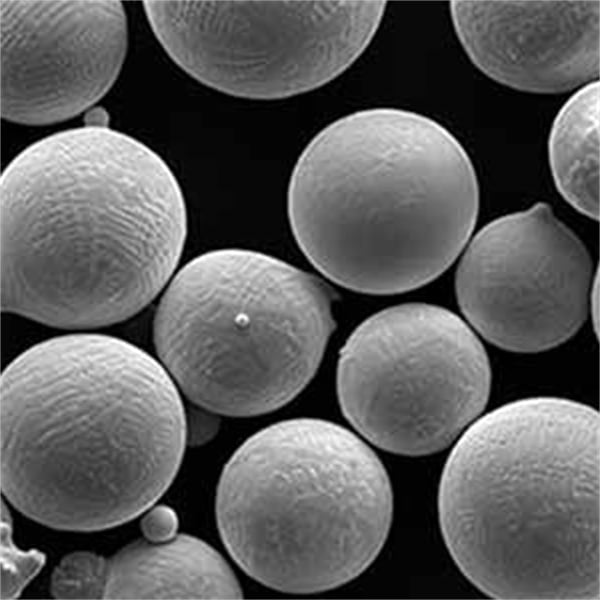
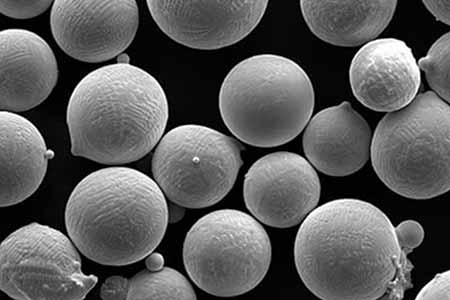
Applications of Hot Isostatic Pressing
Hot Isostatic Pressing finds applications in a wide range of industries due to its ability to enhance material properties and functionality. Here are some key examples:
- Ngành hàng không vũ trụ: HIP is critical in the aerospace industry for manufacturing high-performance components for jet engines, rocket engines, and airframes. Turbine blades, landing gear components, and structural elements all benefit from the improved strength, fatigue resistance, and dimensional stability achieved through HIP.
- Medical Devices: Medical implants like artificial joints, bone screws, and dental implants rely on HIP to achieve the density, biocompatibility, and fatigue resistance needed for safe and long-lasting performance inside the human body.
- Oil and Gas: Components used in oil and gas exploration and production, such as downhole tools and wellhead equipment, often require exceptional strength and resistance to harsh downhole environments. HIP ensures these components can withstand extreme pressures and temperatures.
- Tooling: High-performance cutting tools and dies used in metalworking and other industries benefit from HIP treatment. The process enhances their wear resistance and overall lifespan, leading to increased productivity and reduced downtime.
- Sản xuất bồi đắp: Hot Isostatic Pressing is increasingly used as a post-processing step for components manufactured using additive manufacturing techniques like 3D printing. HIP helps to eliminate internal porosity inherent to some 3D printing processes, resulting in denser, stronger, and more functional parts.
Beyond the Obvious: These are just a few prominent applications of Hot Isostatic Pressing. The potential uses of this technology continue to expand as researchers explore its capabilities for new materials and applications.
Considerations and Limitations of Ép đẳng tĩnh nhiệt
While Hot Isostatic Pressing offers a plethora of advantages, it’s essential to consider some limitations and factors to ensure successful implementation:
- Material Compatibility: Not all materials are suitable for Hot Isostatic Pressing. Some materials might react adversely to the high temperatures or pressures involved. Careful selection of materials and process parameters is crucial.
- Dimensional Changes: The high pressures and temperatures in HIP can cause slight dimensional changes in the treated object. This needs to be factored into the design and manufacturing process to ensure the final component meets the required specifications.
- Cost Considerations: As mentioned earlier, the cost of Hot Isostatic Pressing can be a factor. The size and complexity of the components, as well as the required processing parameters, all influence the overall cost.
Choosing the Right Tool for the Job: Hot Isostatic Pressing is a powerful tool, but it’s not a one-size-fits-all solution. Understanding the limitations and carefully considering the cost-benefit analysis are essential before deciding if HIP is the right choice for a particular application.
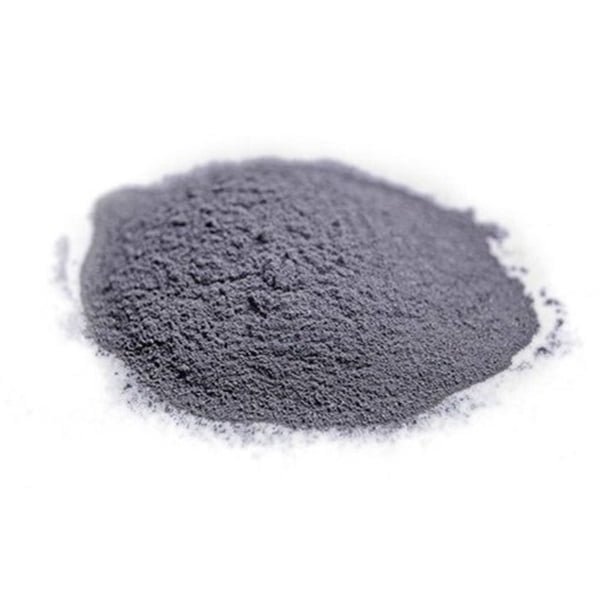
Câu hỏi thường gặp
Here are some frequently asked questions about Hot Isostatic Pressing, answered in a clear and concise format:
Question | Answer |
---|---|
What types of materials can be treated with Hot Isostatic Pressing? | Hot Isostatic Pressing is commonly used for metals, ceramics, some polymers, and metal matrix composites. |
What are the benefits of Hot Isostatic Pressing? | HIP offers numerous benefits, including improved mechanical properties, enhanced microstructure, closure of internal defects, improved bonding, stress relief, and better machinability. |
What are some limitations of Hot Isostatic Pressing? | Material compatibility, potential for dimensional changes, and processing costs are some limitations to consider. |
What are some applications of Hot Isostatic Pressing? | Hot Isostatic Pressing finds applications in aerospace, medical devices, oil and gas, tooling, and additive manufacturing. |
Is Hot Isostatic Pressing expensive? | The cost of HIP can vary depending on the size and complexity of the components, as well as the required processing parameters |
About 3DP mETAL
Product Category
LIÊN HỆ
Bạn có thắc mắc không? Hãy gửi tin nhắn ngay cho chúng tôi! Sau khi nhận được tin nhắn của bạn, chúng tôi sẽ xử lý yêu cầu của bạn với cả một đội ngũ.