Laser Metal Deposition (LMD) is a cutting-edge technology revolutionizing the manufacturing and repair industries. Imagine being able to build or repair metal parts with pinpoint precision, layer by layer, using a laser. Sounds futuristic, right? Well, it’s not just the future; it’s happening right now. Let’s dive deep into this fascinating technology.
Overview of Laser Metal Deposition (LMD)
Laser Metal Deposition (LMD), also known as Direct Metal Deposition (DMD), is an additive manufacturing process that uses a high-power laser to melt metal powder or wire as it is deposited onto a substrate. This technology is pivotal in creating complex geometries, repairing high-value components, and adding features to existing parts.
Key Details:
- Quy trình: A laser beam creates a melt pool on the substrate where metal powder or wire is fed, forming a layer as it solidifies.
- ỨNG DỤNG: Aerospace, automotive, medical implants, and tool and die industries.
- Nguyên liệu: Various metals including titanium, stainless steel, cobalt-chrome, and Inconel.
- Lợi ích: High precision, minimal waste, and the ability to repair expensive components.
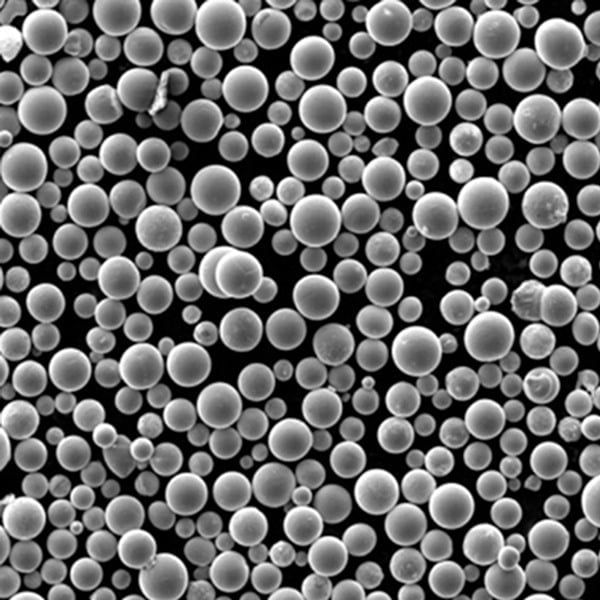
Types of Metal Powders for Laser Metal Deposition
Common Metal Powders Used in LMD
Metal Powder | Sáng tác | thuộc tính | Đặc điểm |
---|---|---|---|
Inconel 625 | Nickel-Chromium | High strength, corrosion, and oxidation resistance | Excellent weldability, used in harsh environments |
Titanium 6Al-4V | Titanium-Aluminum-Vanadium | High strength-to-weight ratio, corrosion resistance | Lightweight, biocompatible, used in aerospace |
Stainless Steel 316L | Iron-Chromium-Nickel | High corrosion resistance, good formability | Used in medical implants, marine applications |
Cobalt-Chrome | Cobalt-Chromium-Molybdenum | High wear and corrosion resistance | Used in dental and orthopedic implants |
Aluminum AlSi10Mg | Aluminum-Silicon-Magnesium | Lightweight, good thermal properties | Used in automotive, aerospace |
Đồng | Đồng nguyên chất | Dẫn nhiệt và dẫn điện tuyệt vời | Used in electrical components, heat exchangers |
Nickel 718 | Nickel-Chromium-Iron | High strength, excellent fatigue, and creep resistance | Used in gas turbines, aerospace |
Tool Steel H13 | Iron-Carbon-Chromium | High toughness, wear resistance | Used in tooling and die-making |
Maraging Steel | Iron-Nickel-Cobalt-Molybdenum | High strength, good toughness | Used in aerospace, tooling |
Bronze CuSn10 | Copper-Tin | Good wear resistance, corrosion resistance | Used in artistic applications, machinery bearings |
Detailed Descriptions
- Inconel 625: This nickel-chromium-based superalloy is known for its excellent fatigue and thermal-fatigue properties, oxidation, and corrosion resistance. It’s commonly used in aerospace and marine applications due to its robustness in extreme environments.
- Titanium 6Al-4V: With a composition of titanium, aluminum, and vanadium, this alloy offers a superior strength-to-weight ratio and corrosion resistance, making it a staple in the aerospace industry and medical implants.
- Stainless Steel 316L: This iron-chromium-nickel alloy is favored for its corrosion resistance and good formability, making it ideal for marine and medical applications where durability is crucial.
- Cobalt-Chrome: Known for its high wear and corrosion resistance, cobalt-chrome is extensively used in dental and orthopedic implants due to its biocompatibility and strength.
- Aluminum AlSi10Mg: This lightweight alloy offers good thermal properties and is used in the automotive and aerospace sectors where weight reduction without compromising strength is essential.
- Đồng: Pure copper is utilized in applications requiring excellent thermal and electrical conductivity, such as electrical components and heat exchangers.
- Nickel 718: With its exceptional strength and resistance to fatigue and creep, this nickel-chromium-iron alloy is commonly used in gas turbines and aerospace applications.
- Tool Steel H13: Renowned for its high toughness and wear resistance, H13 tool steel is a go-to material for tooling and die-making.
- Maraging Steel: This high-strength, tough alloy is used in the aerospace and tooling industries. Its composition includes iron, nickel, cobalt, and molybdenum.
- Bronze CuSn10: Known for its wear and corrosion resistance, this copper-tin alloy is used in artistic applications and machinery bearings.
Composition of Laser Metal Deposition (LMD)
The composition of the materials used in LMD is crucial for achieving the desired properties in the finished product. Here’s a detailed look:
Composition of Common LMD Metal Powders
Metal Powder | Primary Elements | Additional Elements | Typical Uses |
---|---|---|---|
Inconel 625 | Nickel, Chromium | Molybdenum, Niobium | Aerospace, marine, chemical processing |
Titanium 6Al-4V | Titanium, Aluminum | Vanadi | Aerospace, medical implants |
Stainless Steel 316L | Iron, Chromium | Nickel, Molybdenum | Medical devices, marine applications |
Cobalt-Chrome | Cobalt, Chromium | Molyben | Dental, orthopedic implants |
Aluminum AlSi10Mg | Aluminum, Silicon | Magie | Automotive, aerospace |
Đồng | Đồng | Oxy | Electrical components, heat exchangers |
Nickel 718 | Nickel, Chromium | Iron, Molybdenum, Niobium | Gas turbines, aerospace |
Tool Steel H13 | Iron, Carbon | Chromium, Molybdenum | Tooling, die-making |
Maraging Steel | Iron, Nickel | Cobalt, Molybdenum | Aerospace, tooling |
Bronze CuSn10 | Copper, Tin | Zinc | Artistic applications, machinery bearings |
Properties and Characteristics of Laser Metal Deposition (LMD)
Key Properties
- Precision: LMD allows for precise control over the deposition process, resulting in high accuracy in building or repairing parts.
- Material Efficiency: Minimal waste is generated as the process uses only the required amount of material.
- Versatility: A wide range of metals can be used, including superalloys and biocompatible materials.
- Mechanical Strength: Components produced using LMD often have mechanical properties that match or exceed those of traditionally manufactured parts.
Detailed Characteristics
Bất động sản | Miêu tả |
---|---|
Dimensional Accuracy | High precision in creating complex geometries |
Surface Finish | Can vary from smooth to rough depending on parameters and post-processing |
Cấu trúc vi mô | Typically fine-grained due to rapid solidification |
Mật độ | Near full density can be achieved with optimal parameters |
Độ rỗng | Low porosity is achievable, critical for mechanical properties |
Bond Strength | Strong metallurgical bonds between layers and the substrate |
Khả năng chống ăn mòn | Dependent on material; high for alloys like stainless steel and Inconel |
Tính chất nhiệt | Good thermal conductivity for metals like copper; essential for heat exchangers |
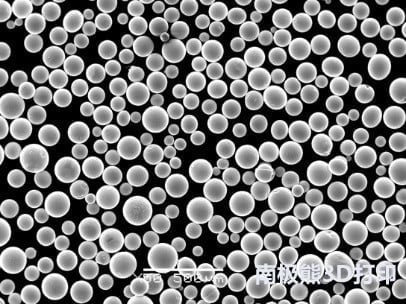
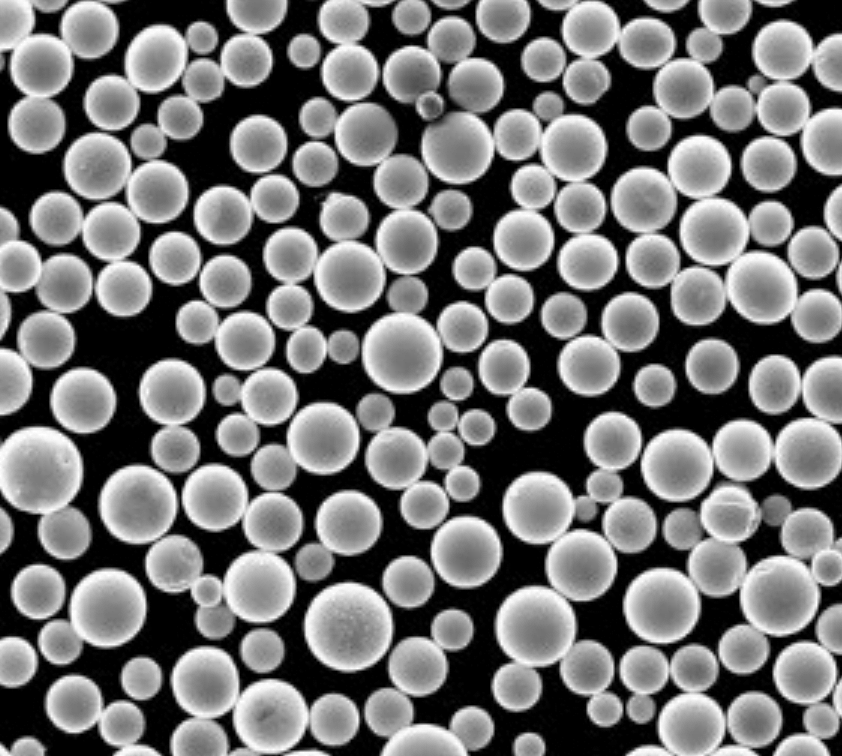
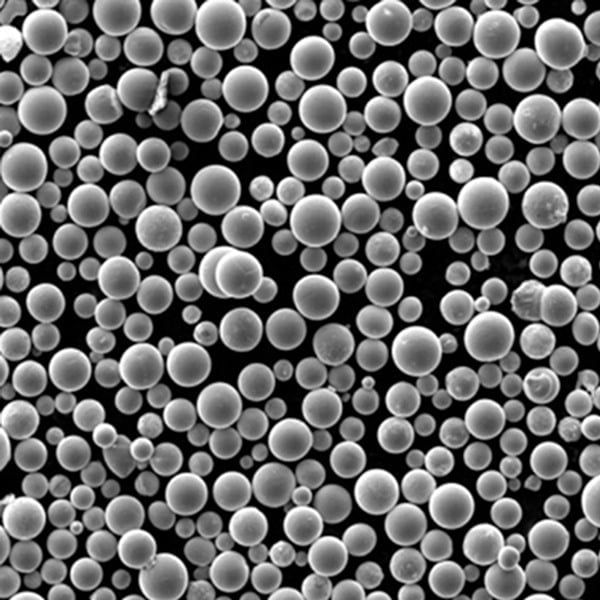
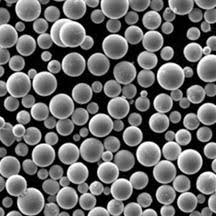
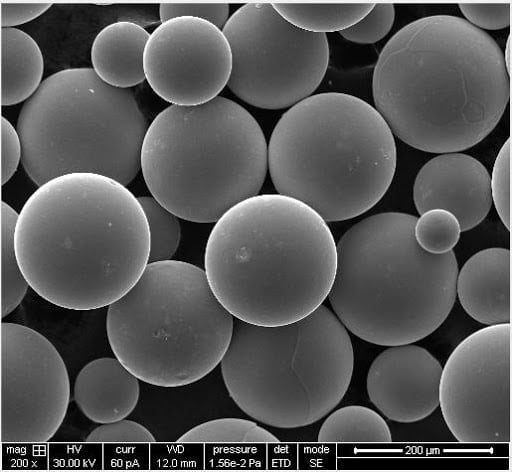
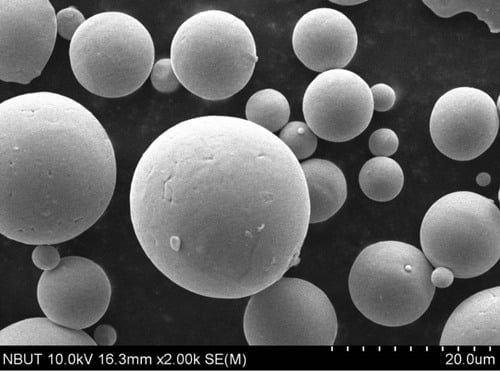
Applications of Laser Metal Deposition (LMD)
LMD technology is versatile and finds applications across various industries due to its ability to produce high-quality, complex parts and repair expensive components.
Industrial Applications
Ngành | ỨNG DỤNG |
---|---|
Hiệp công | Engine components, structural parts, repair of turbine blades |
Ô tô | Lightweight components, prototypes, tool repair |
Y học | Custom implants, dental restorations, orthopedic devices |
Tooling and Die | Mold and die repair, manufacturing of cutting tools |
Năng lượng | Turbine repair, heat exchangers, nuclear reactor components |
Quốc phòng | Weapon components, repair and maintenance of critical parts |
Use Cases
- Hiệp công: The ability to repair and manufacture complex engine components makes LMD invaluable. For instance, turbine blades, which operate under extreme conditions, can be repaired with minimal downtime.
- Ô tô: LMD is used to produce lightweight, high-strength components that improve fuel efficiency and performance. It’s also excellent for creating prototypes and repairing tools.
- Y học: Custom implants and dental restorations are crafted with precision, ensuring biocompatibility and patient-specific solutions.
- Tooling and Die: The repair of molds and dies using LMD extends their lifespan and reduces manufacturing costs. High-precision cutting tools are also manufactured using this technology.
Specifications, Sizes, Grades, and Standards
Specifications and Standards for LMD Metal Powders
Metal Powder | Specifications | Sizes (µm) | Grades | Tiêu chuẩn |
---|---|---|---|---|
Inconel 625 | ASTM B443, AMS 5599 | 15-45, 45-106 | UNS N06625 | ASTM, AMS, ISO |
Titanium 6Al-4V | ASTM F1472, AMS 4928 | 15-45, 45-106 | Lớp 5 | ASTM, AMS, ISO |
Stainless Steel 316L | ASTM A240, AMS 5507 | 15-45, 45-106 | UNS S31603 | ASTM, AMS, ISO |
Cobalt-Chrome | ASTM F75, ISO 5832-4 | 15-45, 45-106 | CoCrMo alloy | ASTM, ISO |
Aluminum AlSi10Mg | ASTM B209 | 15-45, 45-106 | AlSi10Mg | ASTM, ISO |
Đồng | ASTM B152 | 15-45, 45-106 | C11000 | ASTM, ISO |
Nickel 718 | ASTM B637, AMS 5663 | 15-45, 45-106 | UNS N07718 | ASTM, AMS, ISO |
Tool Steel H13 | ASTM A681, DIN 1.2344 | 15-45, 45-106 | H13 | ASTM, DIN |
Maraging Steel | ASTM A538 | 15-45, 45-106 | 18Ni(300) | ASTM, ISO |
Bronze CuSn10 | ASTM B505 | 15-45, 45-106 | UNS C90500 | ASTM, ISO |
Suppliers and Pricing Details
Nhà cung cấp | Metal Powders | Pricing (per kg) | Địa điểm | Contact |
---|---|---|---|---|
Höganäs | Inconel 625, Titanium 6Al-4V, Stainless Steel 316L | $200 – $400 | Thụy Điển | www.hoganas.com |
Công nghệ LPW | Inconel 625, Nickel 718, Maraging Steel | $250 – $450 | Vương quốc Anh | www.lpwtechnology.com |
Carpenter Technology | Tool Steel H13, Stainless Steel 316L | $220 – $380 | Hoa Kỳ | www.carpentertechnology.com |
EOS GmbH | Cobalt-Chrome, Aluminum AlSi10Mg | $300 – $500 | Đức | www.eos.info |
AP&C | Titanium 6Al-4V, Inconel 625 | $270 – $460 | Canada | www.advancedpowders.com |
Oerlikon Metco | Cobalt-Chrome, Nickel 718 | $280 – $470 | Switzerland | www.oerlikon.com/metco |
Sandvik | Stainless Steel 316L, Tool Steel H13 | $240 – $420 | Thụy Điển | www.materials.sandvik |
Renishaw | Maraging Steel, Aluminum AlSi10Mg | $260 – $440 | Vương quốc Anh | www.renishaw.com |
Arcam AB | Titanium 6Al-4V, Cobalt-Chrome | $280 – $460 | Thụy Điển | www.arcam.com |
GKN Hoeganaes | Inconel 625, Stainless Steel 316L | $230 – $410 | Hoa Kỳ | www.gknpm.com |
Comparison of Advantages and Limitations
Advantages and Limitations of LMD Metal Powders
Metal Powder | Lợi ích | Hạn chế |
---|---|---|
Inconel 625 | Excellent corrosion and oxidation resistance, high strength | Expensive, difficult to machine |
Titanium 6Al-4V | High strength-to-weight ratio, biocompatible | High cost, challenging to work with |
Stainless Steel 316L | High corrosion resistance, good formability | Lower strength compared to some other alloys |
Cobalt-Chrome | High wear and corrosion resistance, biocompatible | Brittle, expensive |
Aluminum AlSi10Mg | Lightweight, good thermal properties | Lower strength compared to steel alloys |
Đồng | Dẫn nhiệt và dẫn điện tuyệt vời | High cost, prone to oxidation |
Nickel 718 | High strength, excellent fatigue and creep resistance | Expensive, difficult to machine |
Tool Steel H13 | High toughness and wear resistance | Requires heat treatment, expensive |
Maraging Steel | High strength, good toughness | Expensive, requires aging treatment |
Bronze CuSn10 | Good wear resistance, corrosion resistance | Lower strength compared to steel, prone to de-zincification |
Parameters and Thresholds
Tham số | Threshold/Range | Miêu tả |
---|---|---|
Công suất laser | 200 – 1000 W | Determines the energy input for melting the powder |
Tốc độ quét | 200 – 1000 mm/s | Affects the deposition rate and layer quality |
Powder Feed Rate | 1 – 10 g/min | Controls the amount of powder delivered to the melt pool |
Độ dày lớp phủ | 20 – 100 µm | Affects the resolution and surface finish of the part |
Shielding Gas | Argon, Nitrogen | Protects the melt pool from oxidation |
Substrate Temperature | Room temperature to 200°C | Can influence the bonding quality and residual stresses |
Khoảng cách giữa các ô lưới | 0.1 – 0.5 mm | Distance between adjacent laser tracks |
Overlap Percentage | 50 – 90% | Ensures complete coverage and bonding between layers |
Cooling Rate | 10^2 – 10^6 °C/s | Affects the microstructure and mechanical properties |
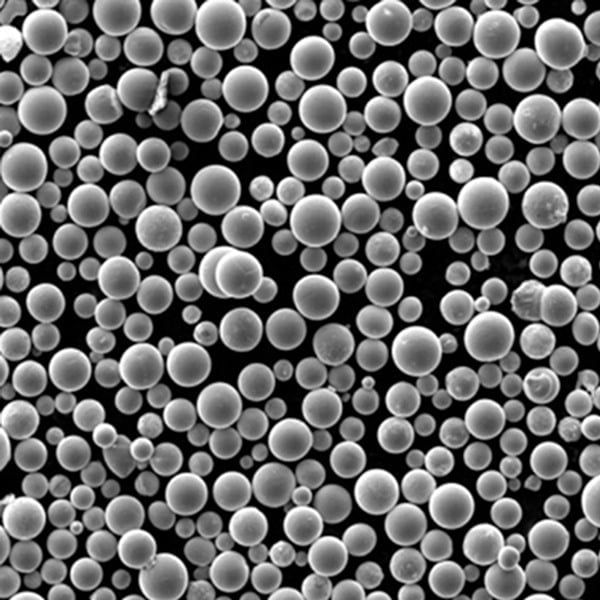
Câu hỏi thường gặp
Question | Answer |
---|---|
What is Laser Metal Deposition (LMD)? | LMD is an additive manufacturing process that uses a laser to melt metal powder or wire as it is deposited onto a substrate. |
What materials can be used in LMD? | Various metals including Inconel, titanium alloys, stainless steel, cobalt-chrome, aluminum, copper, and more. |
What industries use LMD? | Aerospace, automotive, medical, tooling and die, energy, and defense industries. |
What are the advantages of LMD? | High precision, minimal waste, ability to repair expensive components, and versatility in materials. |
How does LMD compare to traditional manufacturing? | LMD offers higher precision, reduced waste, and the ability to create complex geometries compared to traditional methods. |
What are the limitations of LMD? | High initial cost, slower build rates compared to some traditional methods, and limited by the size of the build area. |
What is the typical layer thickness in LMD? | The typical layer thickness ranges from 20 to 100 micrometers. |
Can LMD be used for repairing parts? | Yes, LMD is highly effective for repairing high-value components, extending their life and reducing costs. |
What are the key parameters in the LMD process? | Key parameters include laser power, scan speed, powder feed rate, layer thickness, and shielding gas. |
How is the quality of LMD parts ensured? | Quality is ensured through precise control of process parameters, proper material selection, and post-processing techniques. |
About 3DP mETAL
Product Category
LIÊN HỆ
Bạn có thắc mắc không? Hãy gửi tin nhắn ngay cho chúng tôi! Sau khi nhận được tin nhắn của bạn, chúng tôi sẽ xử lý yêu cầu của bạn với cả một đội ngũ.