Introduction to Laser Powder Bed Fusion
Imagine crafting intricate metal objects from a bed of fine powder, layer by layer, using the focused energy of a laser. This isn’t science fiction; it’s laser powder bed fusion (LPBF), a groundbreaking additive manufacturing process that’s revolutionizing industries.
LPBF, also known as powder bed fusion, is a family of techniques that employ a laser beam to melt and fuse metal powder into a desired three-dimensional shape. It’s like baking a metal cake, one thin layer at a time, with the laser as your precise oven.
How Does Laser Powder Bed Fusion Work?
At its core, LPBF is a relatively simple concept. A thin layer of metal powder is spread evenly across a build platform. A high-powered laser beam scans over the powder, melting the particles in the desired pattern. As the laser moves, the melted metal cools and solidifies, bonding with the previously fused layers. This process is repeated until the entire part is built.
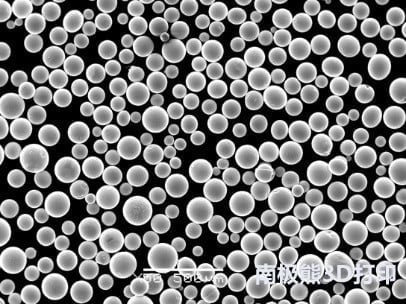
Types of Laser Powder Bed Fusion
While the fundamental principle remains the same, there are several variations of LPBF, each with its own nuances:
- Direct Metal Laser Sintering (DMLS): A widely used method where the laser partially melts the metal powder, creating strong bonds between particles.
- Selective Laser Melting (SLM): This technique fully melts the metal powder, resulting in denser and more refined parts.
- Electron Beam Melting (EBM): Instead of a laser, an electron beam is used to melt the powder. EBM is often used for materials that are challenging to process with lasers.
Metal Powders Used in Laser Powder Bed Fusion
The choice of metal powder is crucial for the success of an LPBF project. Different powders offer varying properties, influencing the final product’s characteristics. Here’s a look at some common metal powders used in LPBF:
Metal Powder | Miêu tả |
---|---|
Stainless Steel Powder | Offers excellent corrosion resistance, strength, and durability. Widely used in various industries. |
Titanium Powder | Known for its high strength-to-weight ratio, biocompatibility, and excellent corrosion resistance. Ideal for aerospace and medical applications. |
Aluminum Powder | Lightweight with good thermal conductivity and corrosion resistance. Commonly used in automotive and aerospace industries. |
Cobalt-Chromium Powder | Offers high strength, hardness, and wear resistance. Widely used in dental and medical implants. |
Nickel Alloy Powder | Known for its high-temperature resistance, corrosion resistance, and strength. Used in aerospace and energy applications. |
Copper Powder | Excellent thermal and electrical conductivity. Used in electronics and heat exchange applications. |
Inconel Powder | Offers exceptional corrosion resistance, high-temperature strength, and oxidation resistance. Used in harsh environments. |
Maraging Steel Powder | Known for its high strength and toughness. Used in aerospace and defense applications. |
Tool Steel Powder | Offers excellent hardness, wear resistance, and toughness. Used in tooling and manufacturing applications. |
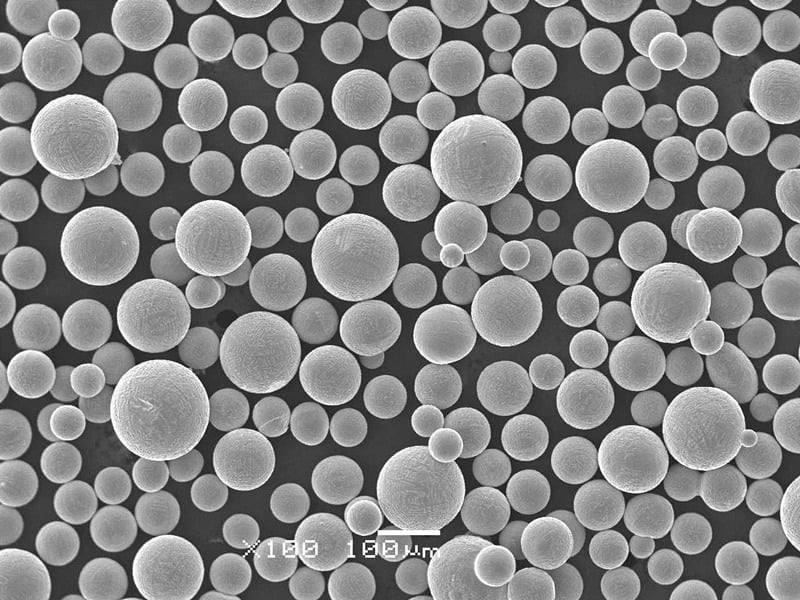
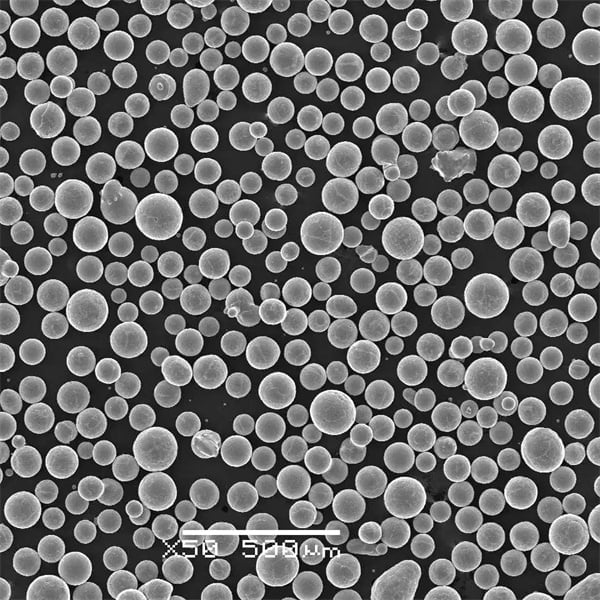
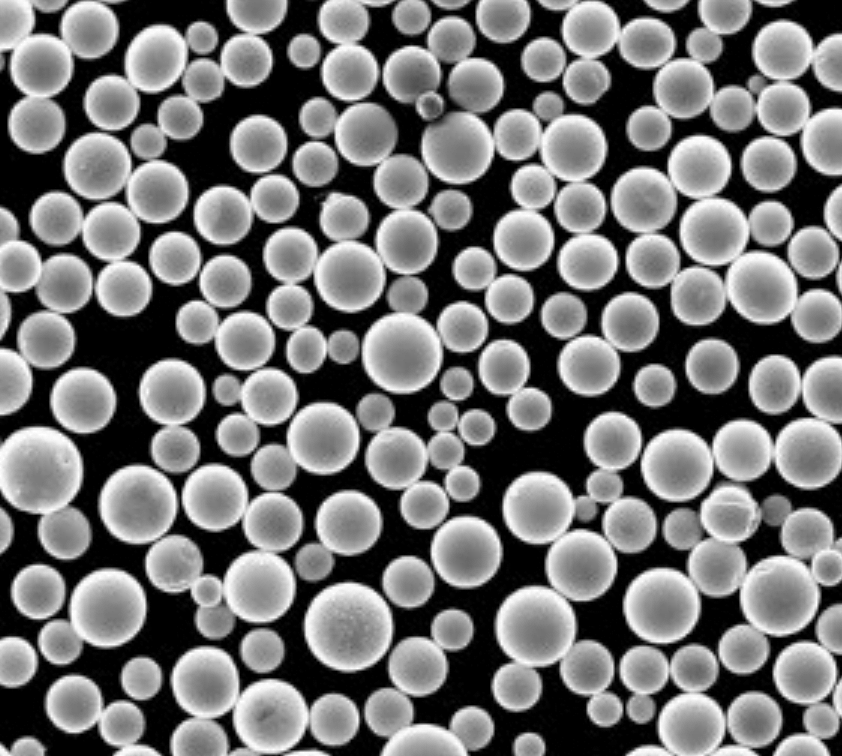
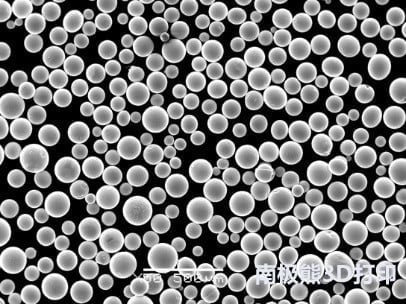
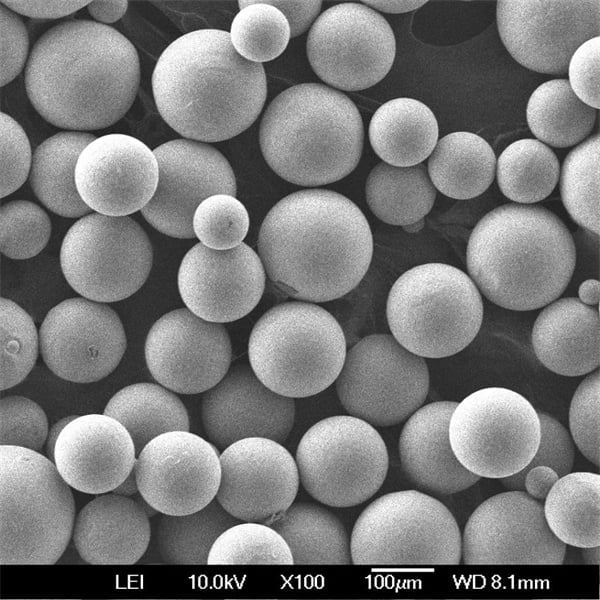
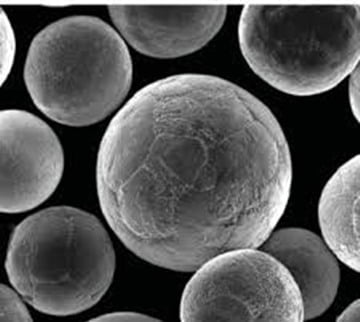
Applications of Laser Powder Bed Fusion
The versatility of LPBF has opened up a world of possibilities across various industries. Here are some key application areas:
Ngành | ỨNG DỤNG |
---|---|
Hiệp công | Aircraft components, engine parts, satellite components |
Ô tô | Prototyping, tooling, production parts, lightweight components |
Y học | Implants, dental prosthetics, surgical instruments |
Năng lượng | Turbine blades, heat exchangers, fuel nozzles |
Dầu mỏ và khí đốt | Downhole tools, pump components, valve bodies |
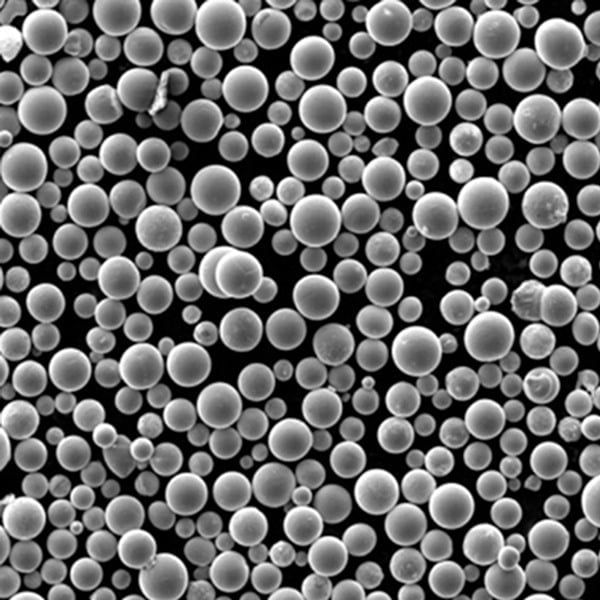
Advantages and Disadvantages of Laser Powder Bed Fusion
Like any technology, LPBF has its strengths and weaknesses.
Advantages:
- Design freedom: Create complex geometries impossible with traditional manufacturing methods.
- Material efficiency: Minimal material waste compared to subtractive manufacturing processes.
- Production flexibility: Quickly produce small batches or single parts.
- Strong and durable parts: High mechanical properties due to the dense microstructure.
Disadvantages:
- High equipment cost: LPBF machines can be expensive.
- Powder handling challenges: Metal powders can be hazardous if not handled properly.
- Build time: Producing large parts can be time-consuming.
- Surface finish: May require post-processing for optimal surface quality.
Laser Powder Bed Fusion: The Future is Bright
LPBF is still a relatively young technology, but its potential is immense. As research and development continue, we can expect to see even more innovative applications emerge. From personalized medicine to sustainable energy solutions, LPBF has the power to shape our future.
About 3DP mETAL
Product Category
LIÊN HỆ
Bạn có thắc mắc không? Hãy gửi tin nhắn ngay cho chúng tôi! Sau khi nhận được tin nhắn của bạn, chúng tôi sẽ xử lý yêu cầu của bạn với cả một đội ngũ.