Imagine building intricate structures, powerful machines, and even life-saving medical implants, all from a fine, metallic dust. That’s the magic of low alloy powders, a revolutionary material transforming the landscape of manufacturing. But what exactly are these powders, and how do they work their wonders? Buckle up, because we’re diving deep into the world of these tiny titans!
At their core, low alloy powders are iron-based fellows, just like their solid steel counterparts. However, the secret sauce lies in the addition of small amounts (typically less than 10%) of other elements, like:
- Chromium (Cr): Enhances corrosion resistance and hardenability. Think of it as a knight’s armor, shielding the steel from environmental attacks.
- Manganese (Mn): Improves strength and workability. Imagine it as the blacksmith’s hammer, making the steel more robust and easier to shape.
- Molybdenum (Mo): Boosts high-temperature strength. Picture it as a firefighter’s suit, protecting the steel from the heat of intense processes.
- Nickel (Ni): Enhances toughness and ductility. Think of it as a gymnast’s flexibility, allowing the steel to bend without breaking.
- Silicon (Si): Improves deoxidization and castability. Imagine it as a sculptor’s chisel, removing impurities for a cleaner final product.
A Tailored Approach:
The specific combination and percentage of these alloying elements vary depending on the desired properties of the final product. It’s like a recipe – adjust the ingredients to create the perfect steel for the job, be it a lightweight car part or a heavy-duty industrial gear.
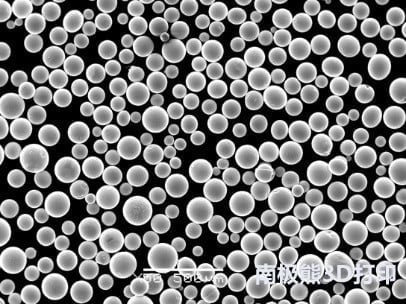
Properties and Characteristics of Low Alloy Powders
Superior Strength:
Low alloy powders boast impressive strength compared to traditional steels. The addition of alloying elements creates a denser microstructure, making them more resistant to deformation under pressure. Imagine them as miniature weightlifters, capable of handling heavy loads without breaking a sweat (or a particle).
Enhanced Workability:
Despite their strength, low alloy powders retain a good degree of workability. This allows them to be readily shaped using various manufacturing techniques, like additive manufacturing (3D printing) and metal injection molding (MIM). Think of them as Play-Doh for adults – strong yet moldable to create complex shapes.
Tailored Performance:
By adjusting the alloying elements, manufacturers can fine-tune the properties of low alloy powders. Need exceptional wear resistance? Up the chromium content. Desire outstanding weldability? Reduce the carbon content. It’s like having a toolbox filled with different alloys, each offering unique benefits for specific applications.
Lightweight Potential:
Compared to some traditional steels, low alloy powders can offer weight reduction. This is particularly attractive in industries like aerospace and automotive, where every gram saved translates to better fuel efficiency and performance. Think of them as feathers compared to lead weights, offering strength without the bulk.
Applications of Low Alloy Powders
The Manufacturing Revolution:
Low alloy powders are revolutionizing the way we manufacture complex parts. Here are some key applications:
- Ngành hàng không vũ trụ: Low alloy powders are used to create lightweight, high-strength components for aircraft, reducing fuel consumption and increasing flight range. Imagine them as the building blocks for a new generation of super-efficient airplanes.
- Ô tô: From gears and engine components to lightweight car bodies, low alloy powders are making vehicles stronger, lighter, and more fuel-efficient. Think of them as the future of car manufacturing, creating vehicles that are both powerful and eco-friendly.
- Medical Implants: The biocompatible nature of certain low alloy powders allows for the creation of customized implants like hip replacements and knee joints. Imagine them as tiny lifesavers, restoring mobility and improving patients’ lives.
- Tools and Dies: Low alloy powders can be used to create wear-resistant tools and dies for various industries. Think of them as the workhorses of manufacturing, ensuring precise and long-lasting performance.
- Consumer Goods: From complex bicycle components to intricate jewelry pieces, low alloy powders are opening doors for innovative and customized consumer products. Imagine them as the building blocks for the next generation of gadgets and everyday items.
The Potential is Limitless:
As research and development continue, the applications of low alloy powders are expected to expand even further. They hold immense potential for industries like energy, construction, and even electronics.
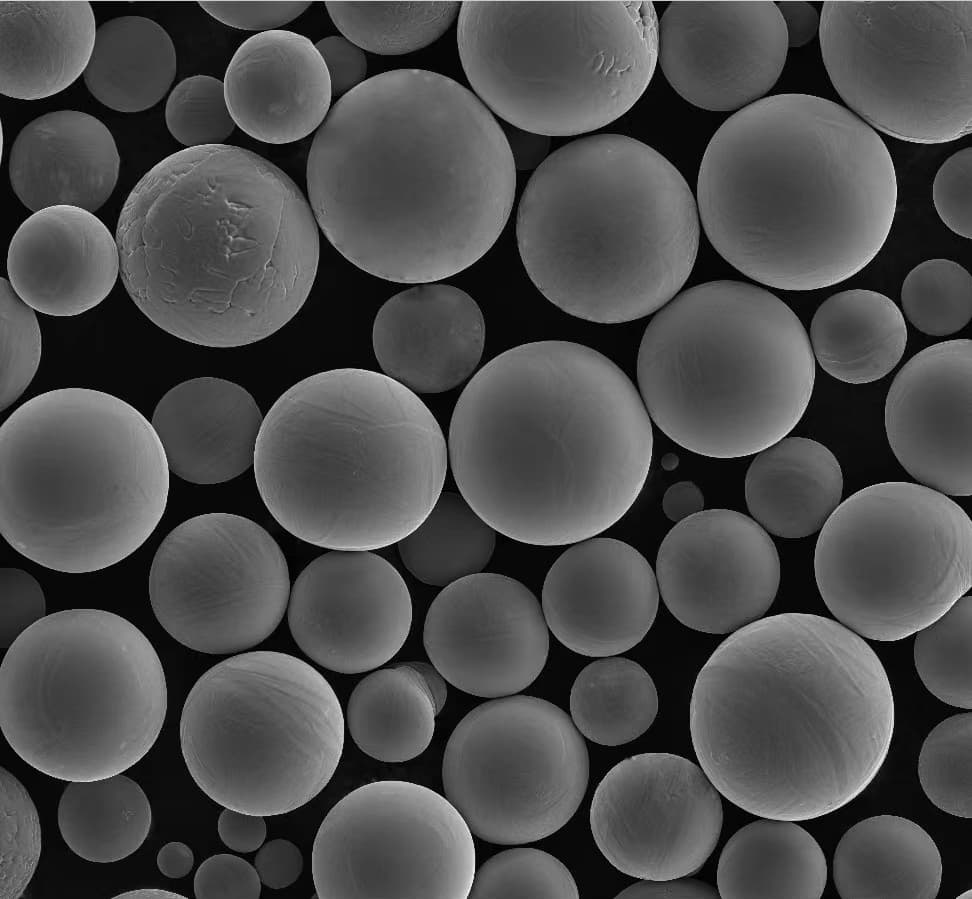
Specifications, Sizes, Grades, and Standards
Tailored for Perfection:
Low alloy powders come in a variety of specifications, sizes, grades, and standards to cater to diverse manufacturing needs.
Specification Breakdown:
- Particle Size Distribution: This refers to the range of particle sizes present in the powder. Finer powders offer better surface finish but can be more challenging to flow freely. Coarser powders flow more easily but may result in a rougher surface finish. The ideal particle size depends on the chosen manufacturing technique and desired final product properties.
- Chemical Composition: The specific percentages of iron and alloying elements are precisely controlled to achieve the targeted properties. Manufacturers adhere to strict industry standards like ASTM International (ASTM) or the Society of Automotive Engineers (SAE) for chemical composition.
- Mật độ biểu kiến: This refers to the weight of powder per unit volume, considering both the solid particles and the air spaces between them. A higher apparent density translates to less powder needed to produce a part, which can be more cost-effective.
- Khả năng chảy trôi: This describes how easily the powder flows, impacting its suitability for specific manufacturing processes. Powders with good flowability are essential for techniques like additive manufacturing and MIM.
Size Matters:
Low alloy powders are available in a wide range of sizes, typically ranging from 10 to 150 micrometers (µm). Here’s a glimpse into the impact of size:
- Finer Powders (10-45 µm): Offer exceptional surface finish and are ideal for creating intricate details in parts. However, they may require special handling due to their flow characteristics.
- Medium Powders (45-100 µm): Balance good surface finish with flowability, making them suitable for a wider range of applications.
- Coarser Powders (100-150 µm): Flow freely but may result in a slightly rougher surface finish. They are often used for applications where dimensional accuracy is less critical.
Grade Expectations:
Low alloy powders come in various grades, each offering a specific set of properties. Common grades include:
- Distributing: General-purpose powders with balanced properties for a wide range of applications.
- Carburizing: Contain lower carbon content, making them ideal for parts that will undergo subsequent carburizing processes for enhanced wear resistance.
- Nitriding: Contain specific alloying elements that promote nitriding, a surface hardening treatment.
- High-Strength: Boast increased levels of alloying elements for exceptional strength in critical applications.
Standards for Confidence:
To ensure consistent quality and performance, low alloy powder manufacturers adhere to various national and international standards. Some key standards include:
- ASTM International (ASTM): Sets standards for various aspects of metal powders, including chemical composition, particle size distribution, and flowability.
- Society of Automotive Engineers (SAE): Develops specifications for low alloy steel powders used in the automotive industry.
- International Organization for Standardization (ISO): Provides international standards for metal powders, including testing methods and quality control procedures.
By following these standards, manufacturers ensure that low alloy powders meet the specific requirements of different industries and applications.
Pros and Cons of Low Alloy Powders
The Power and the Price:
Like any material, low alloy powders come with their own set of advantages and limitations. Let’s weigh the pros and cons:
Advantages:
- Superior Strength: Low alloy powders offer exceptional strength compared to traditional steels, making them ideal for demanding applications.
- Enhanced Workability: Despite their strength, they retain good workability, allowing for versatile manufacturing processes.
- Tailored Performance: The ability to adjust the alloying elements allows for customized properties to meet specific needs.
- Lightweight Potential: Low alloy powders can contribute to weight reduction in some applications, improving efficiency and performance.
- Design Freedom: Additive manufacturing techniques using low alloy powders enable the creation of complex geometries previously impossible with traditional methods.
- Reduced Waste: Powder-based manufacturing techniques minimize material waste compared to traditional subtractive processes.
Disadvantages:
- Higher Cost: Low alloy powders can be more expensive than conventional steels due to the production process and quality control measures.
- Surface Finish: Depending on the chosen particle size, the surface finish of parts made with low alloy powders may require additional post-processing.
- Process Complexity: Additive manufacturing and other techniques using low alloy powders can involve complex setup and expertise.
- Limited Availability: Compared to traditional steels, the variety of low alloy powder compositions readily available may be smaller.
Making the Right Choice:
Understanding the advantages and limitations of low alloy powders is crucial for making informed decisions in the design and manufacturing process. Weighing the benefits against potential drawbacks ensures you choose the right material for your specific application.
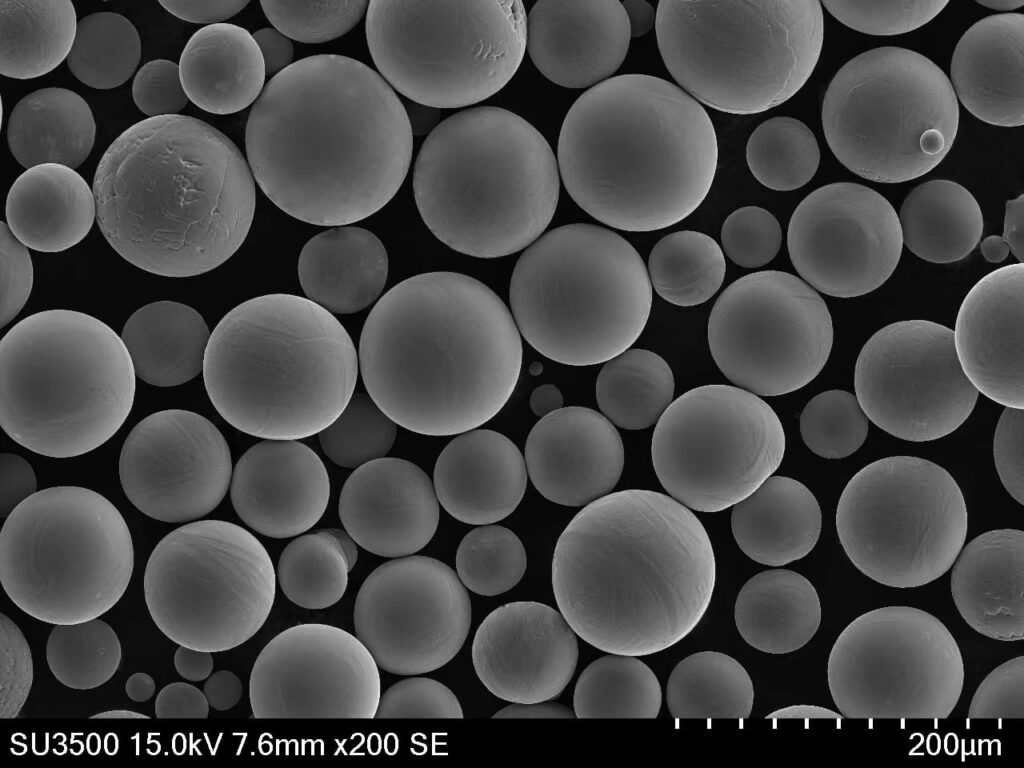
Câu hỏi thường gặp
Q: What are the advantages of using low alloy powders compared to traditional steels?
A: Low alloy powders offer several advantages, including superior strength, enhanced workability, tailored performance, lightweight potential, and design freedom with additive manufacturing.
Q: Are there any disadvantages to using low alloy powders?
A: Some potential drawbacks include higher cost compared to traditional steels, surface finish considerations depending on particle size, process complexity for some manufacturing techniques, and limited availability of certain compositions compared to standard steels.
Q: How do I choose the right low alloy powder for my application?
A: Consider factors like desired properties (strength, ductility, corrosion resistance, etc.), application requirements (e.g., weight limitations, environmental exposure), and budget constraints. Researching different models and consulting with metal powder suppliers can help you make the best choice.
Q: What are some common applications of low alloy powders?
A: Low alloy powders are used in various industries, including aerospace, automotive, medical implants, tools and dies, and consumer goods. They are revolutionizing manufacturing by enabling the creation of complex, high-performance parts.
Q: Where can I find suppliers of low alloy powders?
A: Several reputable manufacturers and distributors specialize in low alloy powders. Researching online or attending industry trade shows can help you connect with potential suppliers.
About 3DP mETAL
Product Category
LIÊN HỆ
Bạn có thắc mắc không? Hãy gửi tin nhắn ngay cho chúng tôi! Sau khi nhận được tin nhắn của bạn, chúng tôi sẽ xử lý yêu cầu của bạn với cả một đội ngũ.