Metal alloy powders are revolutionizing the manufacturing landscape, offering a unique blend of properties and possibilities. Imagine metallic components crafted layer by layer, with intricate details and exceptional strength – that’s the magic of metal alloy powders. But these aren’t your kid’s finger paints; they’re sophisticated engineered materials with a vast array of applications. Buckle up, because we’re diving deep into the world of metal alloy powders!
What are Metal Alloy Powders?
Think of metal alloy powders as tiny, granular versions of your favorite metals – like iron, aluminum, or titanium – but with a twist. These metal grains are meticulously crafted through various processes like atomization, resulting in a fine powder with specific characteristics. By combining different metals, we create alloys, unlocking a whole new spectrum of properties.
Think of it like this: You wouldn’t use the same paintbrush for a delicate watercolor and a bold street mural, right? Similarly, metal alloy powders cater to diverse manufacturing needs.
Here’s a table summarizing the key details of metal alloy powders:
Key Details | Miêu tả |
---|---|
Sáng tác | Made from various metals and their alloys, often blended for specific properties. |
Kích thước hạt | Ranging from micrometers to hundreds of micrometers, depending on the application. |
Phương pháp sản xuất | Atomization (gas or water), mechanical grinding, or other specialized techniques. |
ỨNG DỤNG | Additive Manufacturing (3D Printing), Thermal Spraying, Metal Injection Molding (MIM), and more. |
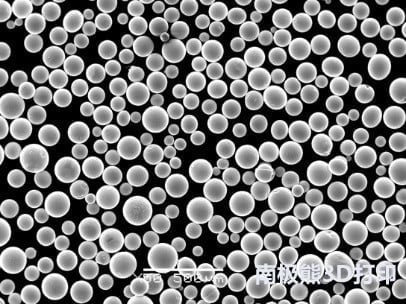
A Universe of Metal Alloy Powders
With a plethora of metal alloy powders available, choosing the right one can feel overwhelming. Here’s a glimpse into ten popular models, each with its own story to tell:
- Stainless Steel 316L: Renowned for its exceptional corrosion resistance, this powder is a champion in harsh environments like marine applications or chemical processing plants. Imagine building a durable boat component that withstands salty sea air – that’s the power of 316L!
- Inconel 625: This high-performance nickel-chromium alloy powder boasts superior resistance to high temperatures and oxidation. Think jet engine parts or components exposed to extreme heat – Inconel 625 can handle it with ease.
- Aluminum 6061: A versatile and lightweight option, 6061 aluminum powder excels in applications demanding good strength-to-weight ratios. Imagine crafting a sleek, sturdy bicycle frame – 6061 aluminum powder is a perfect choice.
- Titanium Grade 2: Offering a beautiful balance of strength, low weight, and excellent biocompatibility, this powder shines in aerospace, medical implants, and sporting goods. Picture a lightweight yet robust prosthetic leg – that’s the potential of Titanium Grade 2 powder.
- Cobalt Chrome (CoCr): A popular choice in the medical field, particularly for dental implants, CoCr powder delivers exceptional biocompatibility and wear resistance. Imagine a dental implant that seamlessly integrates with your body and lasts for years – that’s the promise of CoCr powder.
- Nickel Superalloys: This broad category encompasses various nickel-based alloys, each formulated for unique needs. They offer exceptional strength at high temperatures, making them ideal for gas turbine components or rocket engine parts. Imagine parts that can withstand the scorching heat of a jet engine – that’s the power of nickel superalloy powders.
- Tool Steel Powders: These workhorses boast exceptional hardness and wear resistance, perfect for creating durable tools and dies. Imagine crafting a punch that can effortlessly stamp out intricate shapes for years – that’s the benefit of tool steel powders.
- Copper Alloys: Combining the excellent thermal and electrical conductivity of copper with the enhanced strength of alloying elements, these powders are ideal for heat sinks, electrical components, and more. Imagine a heat sink that efficiently dissipates heat in your high-performance computer – that’s the potential of copper alloy powders.
- Refractory Metal Powders: Tungsten, Molybdenum, and Tantalum powders fall into this category, offering exceptional high-temperature capabilities. Imagine furnace parts that can withstand the blistering heat – that’s the strength of refractory metal powders.
- Biocompatible Alloys: Designed specifically for medical applications, these powders prioritize biocompatibility and corrosion resistance. Imagine creating bone implants that seamlessly integrate with the human body – that’s the promise of biocompatible alloy powders.
This list merely scratches the surface of the vast metal alloy powder universe. With ongoing advancements, new and innovative options are constantly emerging.
Applications of Metal Alloy Powders
Metal alloy powders are not just fancy dust; they’re the building blocks for a revolution in manufacturing. Here’s a glimpse into the diverse applications that leverage their unique properties:
Additive Manufacturing (3D Printing): This transformative technology allows for the creation of complex, three-dimensional objects layer by layer. Metal alloy powders are a perfect fit, enabling the printing of intricate components with exceptional strength and detail. Imagine printing a lightweight yet robust rocket engine part – that’s the power of metal alloy powders in 3D printing!
Thermal Spraying: This process involves melting metal alloy powders and propelling them at high velocity towards a target surface. This creates a coating that enhances properties like wear resistance, corrosion resistance, and thermal conductivity. Picture giving your turbine blades a new lease on life with a wear-resistant thermal spray coating – that’s the benefit of metal alloy powders in thermal spraying.
Metal Injection Molding (MIM): This technique combines the precision of injection molding with the strength of metal. Metal alloy powders are mixed with a binder, molded into the desired shape, and then debindered and sintered to create a final metallic component. Imagine crafting intricate gears with complex geometries – that’s the potential of metal alloy powders in MIM.
Beyond these core applications, metal alloy powders are making waves in various industries:
- Ngành hàng không vũ trụ: Lightweight and high-strength components for aircraft and spacecraft.
- Ô tô: Customizable parts for engines, transmissions, and lightweight body panels.
- Y tế: Biocompatible implants, surgical instruments, and dental prosthetics.
- Consumer Goods: Durable and lightweight components for bicycles, sporting equipment, and electronics.
- Energy: Components for turbines, heat exchangers, and other power generation equipment.
The possibilities are truly endless, with new applications constantly emerging. Metal alloy powders are pushing the boundaries of what’s possible in manufacturing, opening doors to lighter, stronger, and more complex components across various industries.
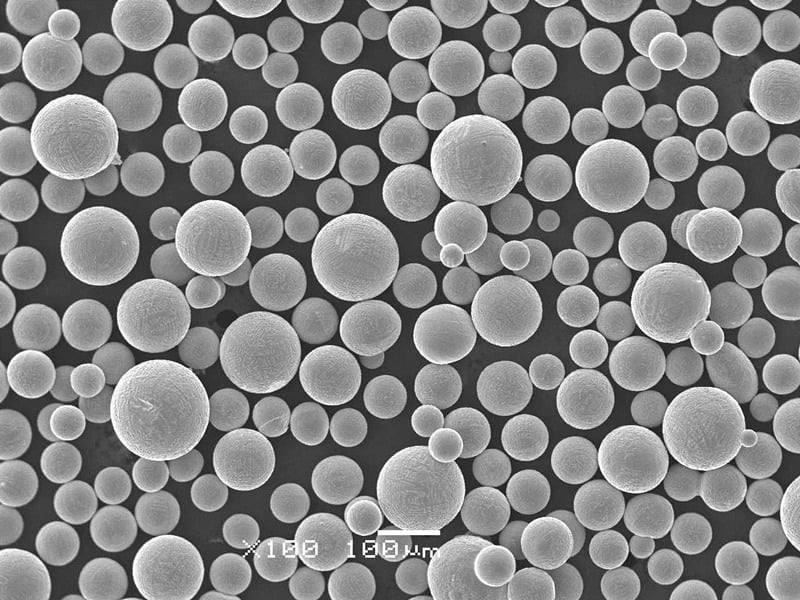
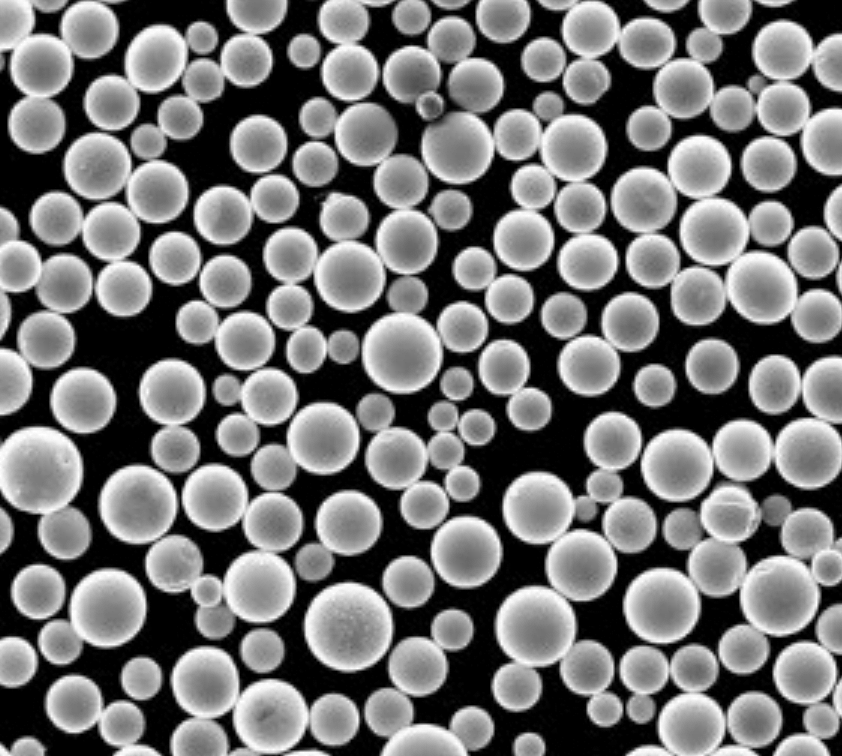
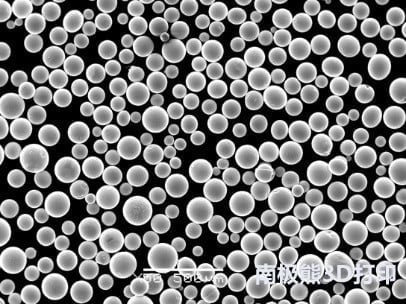
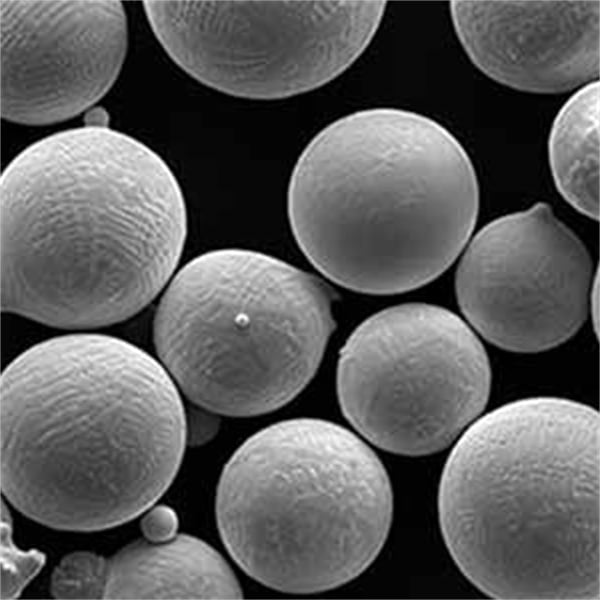
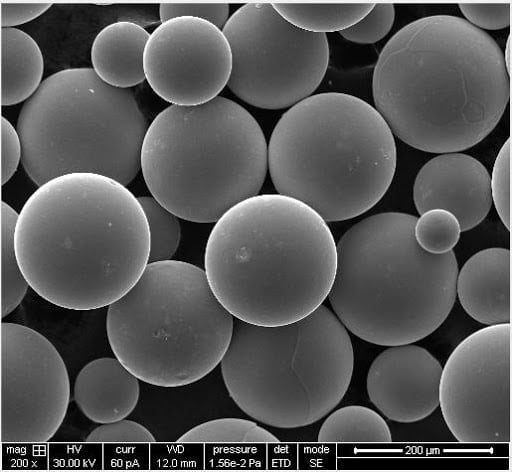
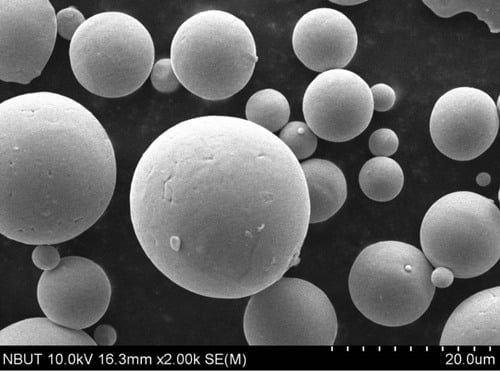
Advantages and Limitations of Metal Alloy Powders
Like any technology, metal alloy powders come with their own set of advantages and limitations. Let’s delve into both sides of the coin:
Advantages:
- Design Freedom: Additive manufacturing allows for the creation of complex geometries that would be impossible with traditional techniques. Imagine crafting a lattice structure for optimal strength-to-weight ratio – that’s the design freedom offered by metal alloy powders.
- Lightweighting: Many metal alloy powders boast high strength-to-weight ratios, enabling the creation of lighter components for improved efficiency. Picture a fuel-efficient car with lightweight metal alloy components – that’s a benefit of this technology.
- Material Efficiency: Metal alloy powders minimize waste compared to traditional subtractive manufacturing techniques. Imagine using only the necessary material to create a component – that’s the advantage of powder-based manufacturing.
- Customization: The ability to tailor the composition and properties of metal alloy powders opens doors for specialized applications. Imagine creating a medical implant perfectly suited to a patient’s specific needs – that’s the power of customization.
Limitations:
- Cost: Metal alloy powder production and processing can be expensive, especially for high-performance alloys. Imagine the initial investment required for a new metal 3D printing setup – that’s a cost consideration with this technology.
- Surface Finish: While advancements are being made, achieving a smooth surface finish with metal alloy powders can be challenging compared to traditional techniques. Imagine a rough surface on a medical implant – that’s a potential limitation of this technology.
- Production Speed: Additive manufacturing with metal alloy powders can be slower than traditional techniques, especially for larger components. Imagine the time it takes to 3D print a complex engine part compared to traditional casting – that’s a speed limitation to consider.
- Limited Material Selection: While the range of available metal alloy powders is expanding, it may not yet encompass all the options readily available in wrought or cast forms. Imagine needing a specific type of steel that isn’t yet available as a powder – that’s a current limitation.
The key takeaway? Metal alloy powders offer a powerful toolkit for manufacturers, but it’s crucial to weigh the advantages and limitations against the specific application. As technology advances, costs decrease, and production speeds improve, metal alloy powders are poised to become an even more dominant force in the manufacturing landscape.
Specifications, Sizes, Grades & Standards
Choosing the right metal alloy powder requires a deep dive into its technical specifications. Here’s a breakdown of key factors to consider:
Yếu tố | Miêu tả | Example |
---|---|---|
Chemical Composition | The specific elements and their weight percentages in the alloy. | 316L Stainless Steel powder typically contains 16-18% chromium, 10-14% nickel, and 2-3% molybdenum. |
Phân phối kích thước hạt | The range of particle sizes within the powder, impacting flowability, packing density, and final component properties. | A powder might have a particle size distribution ranging from 15 to 45 micrometers. |
Mật độ biểu kiến | The weight of powder per unit volume in its loose, uncompacted state. | A titanium powder might have an apparent density of 4.2 g/cm³. |
Mật độ chịu nén | The density of the powder after a standardized tapping procedure, influencing packing behavior. | The tap density of the same titanium powder might be 4.4 g/cm³. |
Khả năng chảy | How easily the powder flows, affecting its suitability for various manufacturing processes. | Powders with good flowability are easier to handle and process in techniques like 3D printing. |
Sintering Behavior | The ability of the powder particles to bond together during the sintering process, impacting the final component’s strength and porosity. | Metal powders with good sintering behavior create strong, dense components. |
Lớp | The designation indicating the specific properties and performance of the powder within an alloy type. | 316L stainless steel powder can come in various grades with slight variations in composition for optimized corrosion resistance or machinability. |
Tiêu chuẩn | Industry-established specifications for metal alloy powders, ensuring consistent quality and performance. | ASTM International (ASTM) and the International Organization for Standardization (ISO) set relevant standards for metal alloy powders. |
Understanding these specifications empowers you to make informed decisions when selecting metal alloy powders for your specific application. Don’t hesitate to consult with material suppliers and experts to ensure you’re getting the perfect powder for the job.
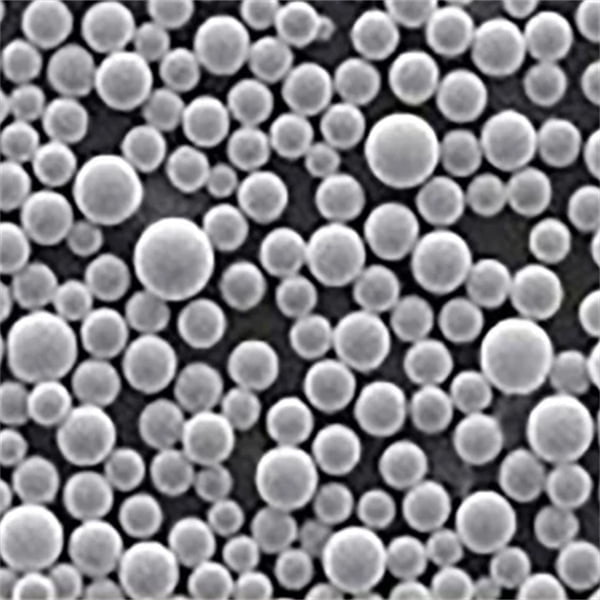
Suppliers and Pricing: Finding the Right Fit
The world of metal alloy powder suppliers is vast and ever-evolving. Here’s a glimpse into finding the right partner for your needs:
- Reputable Manufacturers: Look for established companies with a proven track record of producing high-quality metal alloy powders. Research their certifications, quality control procedures, and customer reviews.
- Material Diversity: Consider suppliers offering a diverse range of metal alloy powders to cater to your specific needs. This allows for greater flexibility and exploration of different options.
- Technical Expertise: Partner with a supplier that possesses in-depth technical knowledge about metal alloy powders. They can provide valuable guidance on material selection, processing parameters, and troubleshooting challenges.
- Pricing Transparency: Metal alloy powder pricing can vary depending on the material, grade, quantity, and market conditions. Seek transparent pricing structures from potential suppliers and compare quotes carefully.
Here’s a table (without specific pricing details due to constant fluctuation) to provide a general sense of pricing considerations:
Yếu tố | Impact on Pricing |
---|---|
Metal Type | Exotic or high-performance alloys generally cost more than common metals. |
Powder Purity | Higher purity powders typically command a premium price. |
Kích thước hạt | Powders with tighter particle size distributions might be more expensive. |
Số lượng | Bulk purchases often negotiate lower per-unit costs. |
Remember, the cheapest option isn’t always the best. Focus on finding a supplier that offers a good balance of quality, price, technical expertise, and reliable service.
Metal Alloy Powders: A Comparison of Pros and Cons
We’ve explored the advantages and limitations of metal alloy powders, but a direct comparison can solidify your understanding. Here’s a breakdown of key pros and cons:
Ưu điểm | Nhược điểm |
---|---|
Design Freedom | Complex geometries achievable compared to traditional techniques. |
Lightweighting | Enables creation of lighter components for improved efficiency. |
Material Efficiency | Minimizes waste compared to subtractive manufacturing. |
Customization | Tailoring composition and properties for specialized applications. |
High Strength-to-Weight Ratio | Ideal for components requiring both strength and lightness. |
Broad Range of Applications | Diverse industries can leverage the benefits of metal alloy powders. |
Potential for Near-Net-Shape Manufacturing | Reduces the need for extensive post-processing. |
Chi phí | Production and processing can be expensive, especially for high-performance alloys. |
Surface Finish | Achieving a smooth surface finish can be challenging compared to traditional techniques, though advancements are being made. |
Production Speed | Additive manufacturing with metal alloy powders can be slower than traditional techniques, especially for larger components. |
Limited Material Selection | While the range of available metal alloy powders is expanding, it may not yet encompass all the options readily available in wrought or cast forms. |
Process Complexity | Metal powder processing techniques can require specialized equipment and expertise. |
The Verdict: Metal alloy powders offer a powerful and versatile toolset for modern manufacturing. By carefully considering the advantages, limitations, and specific application requirements, you can unlock the true potential of this technology.
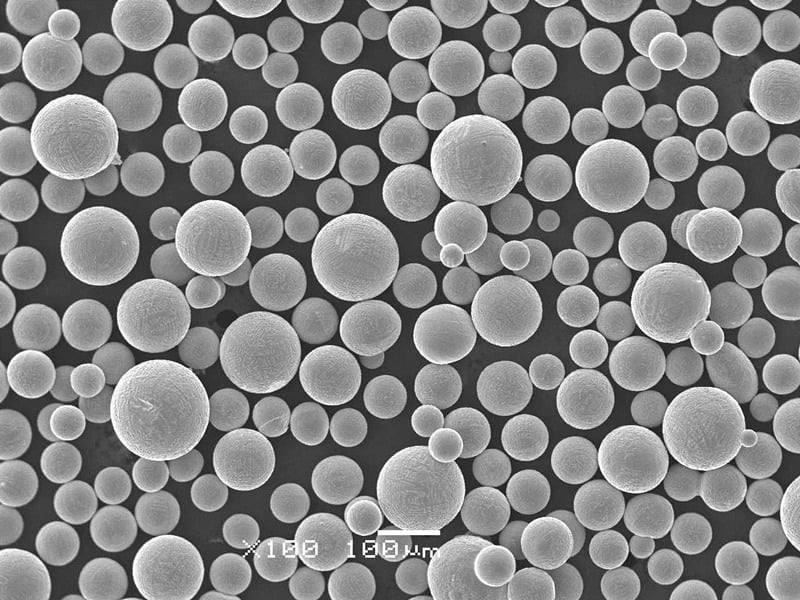
Câu hỏi thường gặp
Here are some commonly asked questions regarding metal alloy powders, presented in a clear and concise table format:
Question | Answer |
---|---|
What are the advantages of using metal alloy powders over traditional manufacturing techniques? | Metal alloy powders offer design freedom for complex geometries, enable lightweighting, minimize material waste, and allow for customization of properties. |
What are some limitations of metal alloy powders? | Cost of production and processing can be high, achieving smooth surface finishes can be challenging, production speeds might be slower, and material selection may be limited compared to traditional methods. |
What are some typical applications of metal alloy powders? | Additive manufacturing (3D printing), thermal spraying, metal injection molding (MIM), and various applications across industries like aerospace, automotive, medical, and energy. |
How are metal alloy powders priced? | Pricing varies based on the metal type, powder purity, particle size, and quantity. Generally, exotic alloys, higher purity, tighter particle size distributions, and smaller quantities command a higher price. |
What are some factors to consider when choosing a metal alloy powder supplier? | Look for reputable manufacturers with a diverse product range, technical expertise, transparent pricing, and reliable service. |
About 3DP mETAL
Product Category
LIÊN HỆ
Bạn có thắc mắc không? Hãy gửi tin nhắn ngay cho chúng tôi! Sau khi nhận được tin nhắn của bạn, chúng tôi sẽ xử lý yêu cầu của bạn với cả một đội ngũ.