Metal molding machines have been the backbone of metal manufacturing for centuries, crafting everything from intricate medical devices to the powerful engines that propel our cars. But the landscape of metal molding is rapidly evolving, with new technologies and materials pushing the boundaries of what’s possible. In this comprehensive guide, we’ll delve into the fascinating world of metal molding machines, exploring their types, applications, benefits, and considerations.
An Overview of Metal Molding Machines
Imagine a sculptor meticulously shaping clay into a masterpiece. Metal molding machines operate on a similar principle, but instead of clay, they manipulate molten metal or metal powders into complex and precise shapes. These machines come in various forms, each with its strengths and ideal applications. Some popular types include:
- Die Casting Machines: These workhorses of the industry inject molten metal under high pressure into a reusable mold (die). They excel at producing high-volume, intricate parts with excellent dimensional accuracy.
- Investment Casting Machines: This intricate process involves creating a wax pattern of the desired part, investing it in a ceramic mold, and then burning away the wax. Molten metal is then poured into the ceramic shell, creating a near-net-shape casting with exceptional detail.
- Sand Casting Machines: The most traditional method, sand casting utilizes a mold carved from sand. Molten metal is poured into the cavity, and after solidification, the sand is broken away to reveal the finished product. Sand casting is known for its versatility and affordability, but dimensional accuracy can be less precise compared to other methods.
- Metal Injection Molding (MIM) Machines: This innovative technology combines aspects of plastic injection molding with powder metallurgy. Metal powder mixed with a binder is injected into a mold, and then the binder is removed through a debinding process. Finally, the part is sintered to achieve its final strength and properties. MIM is ideal for complex, near-net-shape parts with good dimensional accuracy and material properties close to wrought metals.
This is just a glimpse into the diverse world of metal molding machines. Each type offers unique advantages and caters to specific needs.
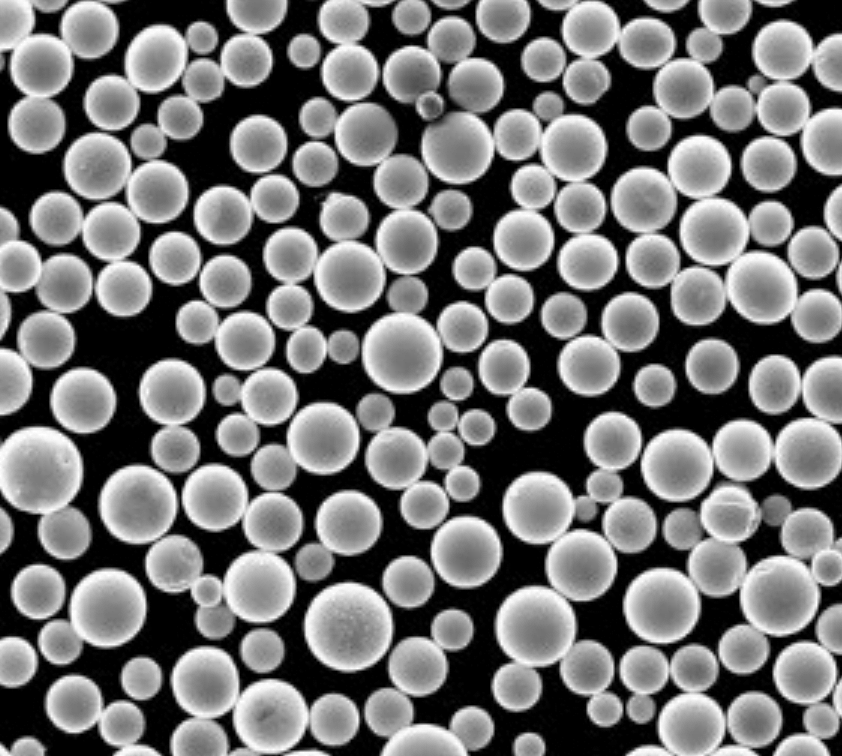
Metal Powders for Molding: A Material Menagerie
Metal molding isn’t just about the machines; the choice of metal powder significantly impacts the final product’s properties and applications. Here’s a look at some commonly used metal powders for molding:
1. Stainless Steel Powders: Offering excellent corrosion resistance and good mechanical properties, stainless steel powders are widely used in applications like medical devices, pump components, and automotive parts.
2. Tool Steel Powders: Renowned for their high wear resistance and hardness, tool steel powders are ideal for creating cutting tools, dies, and molds themselves.
3. Aluminum Powders: Lightweight and offering good conductivity, aluminum powders are popular for applications in aerospace, electronics, and automotive sectors due to their weight-saving properties.
4. Nickel-based Powders: Exhibiting exceptional high-temperature strength and corrosion resistance, nickel-based powders are in high demand for components in jet engines, turbines, and oil & gas exploration.
5. Titanium Powders: Famed for their exceptional strength-to-weight ratio and biocompatibility, titanium powders are used in aerospace components, medical implants, and high-performance sporting goods.
6. Copper Powders: Highly conductive and malleable, copper powders are used in electrical components, heat sinks, and applications requiring excellent thermal management.
7. Iron Powders: The workhorse material of metal powders, iron powders offer good mechanical properties and affordability. They are widely used in automotive components, gears, and structural parts.
8. Cobalt-Chrome Powders: Offering a combination of high strength, corrosion resistance, and biocompatibility, cobalt-chrome powders are used in medical implants, dental prosthetics, and wear-resistant components.
9. Kovar Powders: With a thermal expansion coefficient that closely matches glass, Kovar powders are ideal for applications requiring a hermetic seal between metal and glass, such as in electronic packages.
10. Inconel Powders: A family of nickel-chromium superalloys known for their exceptional high-temperature strength and oxidation resistance, Inconel powders are used in applications like jet engine components, heat exchangers, and chemical processing equipment.
This is just a selection of the vast array of metal powders available for molding. Each material offers unique benefits and considerations, making the selection process a crucial step in metal molding.
the properties and applications of some common metal powders
Metal Powder | thuộc tính | ỨNG DỤNG |
---|---|---|
Thép không gỉ | Corrosion resistant, good mechanical properties | Medical devices, pump components, automotive parts |
Tool Steel | High wear resistance, hardness | Công cụ cắt, khuôn, khuôn đúc |
Nickel-based | Exceptional high-temperature strength, corrosion resistance | Jet engine components, turbines, oil & gas exploration |
Titan | Exceptional strength-to-weight ratio, biocompatibility | Aerospace components, medical implants, high-performance sporting goods |
Đồng | Highly conductive, malleable | Electrical components, heat sinks, applications requiring excellent thermal management |
Sắt | Good mechanical properties, affordability | Automotive components, gears, structural parts |
Cobalt-Chrome | High strength, corrosion resistance, biocompatibility | Medical implants, dental prosthetics, wear-resistant components |
Kovar | Thermal expansion coefficient matches glass | Applications requiring hermetic seal between metal and glass (electronic packages) |
Inconel | Exceptional high-temperature strength, oxidation resistance | Jet engine components, heat exchangers, chemical processing equipment |
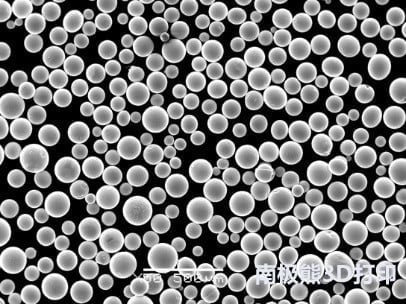
Beyond the Basics: A Deeper Dive into Metal Powders
While the table above provides a starting point, the world of metal powders is brimming with complexity. Here are some additional factors to consider when choosing a metal powder for molding:
- Particle size and distribution: The size and distribution of the metal powder particles significantly impact the final product’s properties. Finer powders generally produce parts with smoother surfaces and better dimensional accuracy, but they can also be more challenging to flow and may require special molding techniques. Conversely, coarser powders offer better flow characteristics but can result in a rougher surface finish and potentially affect dimensional tolerances.
- Powder purity: The presence of impurities in the metal powder can negatively impact the final product’s mechanical properties, corrosion resistance, and overall performance. Choosing high-purity powders ensures consistent and reliable results.
- Sintering behavior: The sintering process involves heating the metal powder to a specific temperature below its melting point, allowing the particles to bond together and form a solid part. Different metal powders exhibit varying sintering behaviors, requiring adjustments in time, temperature, and atmosphere during the sintering process to achieve optimal results.
- Surface treatments: Some metal powders can be pre-treated with lubricants or other surface modifiers to improve flowability, reduce friction during molding, and enhance the final product’s properties.
The Importance of Powder Selection: A Balancing Act
Selecting the right metal powder for your molding project requires careful consideration of the desired properties, application requirements, and cost factors. It’s often a balancing act, weighing the advantages and limitations of different materials. Working closely with a reputable metal powder supplier and a qualified metal molding expert can ensure you select the optimal material for your specific needs.
Applications of Metal Molding Machines
Metal molding machines are the versatile workhorses of the manufacturing industry, shaping metal into a vast array of products across diverse sectors. Here’s a glimpse into the applications that leverage the power of metal molding:
- Ô tô: From intricate engine components like pistons and cylinder heads to lightweight body parts and structural elements, metal molding plays a crucial role in modern vehicles. The ability to produce complex shapes with high precision and repeatability makes metal molding ideal for the automotive industry’s demanding requirements.
- Ngành hàng không vũ trụ: The quest for lightweight yet high-strength materials in aerospace applications finds a perfect partner in metal molding. From jet engine components like turbine blades and combustors to airframe structures, metal molding technologies like titanium and aluminum powder bed fusion (PBF) are pushing the boundaries of what’s possible in aircraft design.
- Medical Devices: The need for biocompatible and high-precision components in medical devices is perfectly addressed by metal molding. From orthopedic implants like hip replacements and knee joints to surgical instruments and dental prosthetics, metal molding technologies like investment casting and MIM are used to create life-saving and life-enhancing devices.
- Consumer Electronics: The ubiquitous presence of electronics in our daily lives relies heavily on metal molding for intricate and reliable components. From the tiny connectors within smartphones to the heat sinks that dissipate heat in laptops, metal molding ensures the smooth functioning of our electronic devices.
- Industrial Machinery: Durability and high-performance are hallmarks of industrial machinery, and metal molding delivers on these requirements. Gears, bearings, and other critical components for industrial equipment are often produced using metal molding techniques like sand casting and die casting, ensuring robust and reliable operation.
These are just a few examples, and the potential applications of metal molding machines extend far beyond. From the intricate workings of a mechanical watch to the powerful turbines that generate electricity, metal molding shapes the world around us in countless ways.
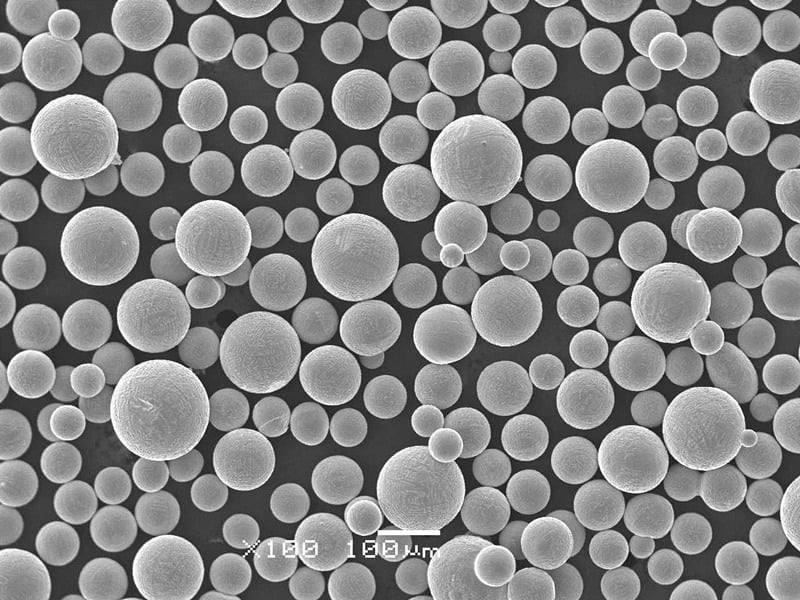
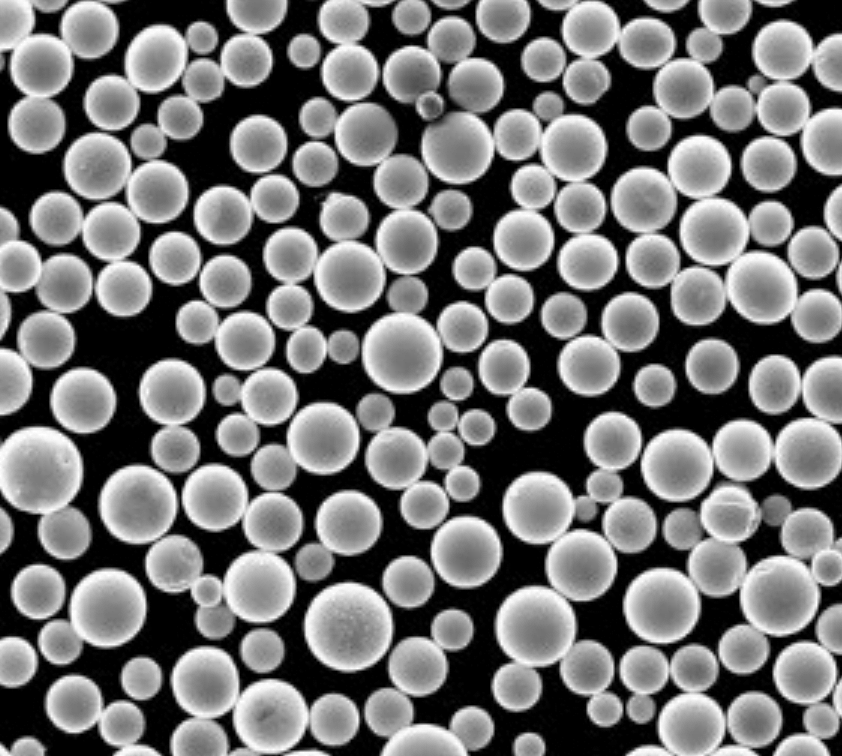
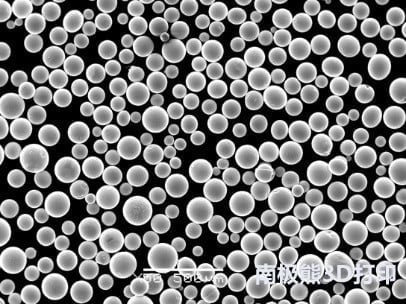
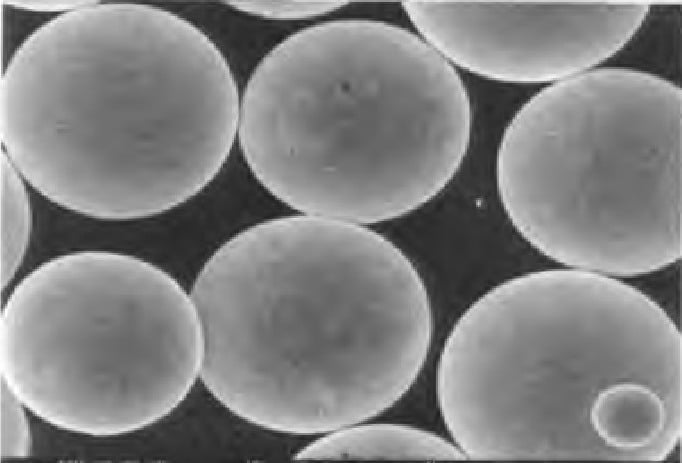
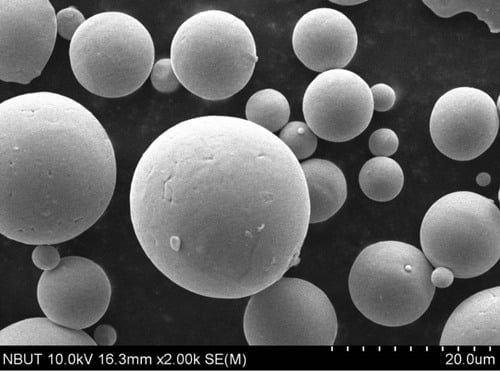
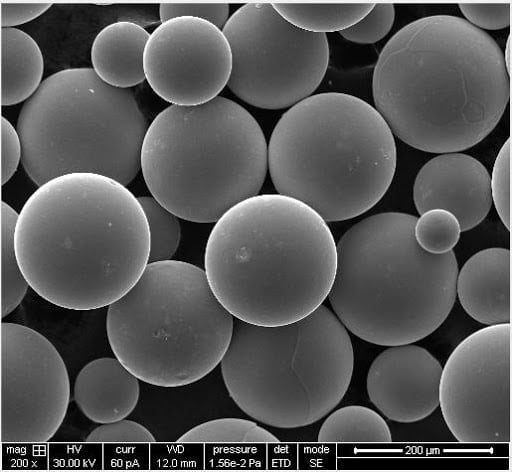
Advantages of Metal Molding Machines: A Winning Combination
Metal molding machines offer a compelling combination of advantages that have made them a cornerstone of the metal manufacturing industry. Here are some of the key benefits that make them such a winning choice:
- Design Flexibility: Unlike traditional subtractive manufacturing techniques like machining, metal molding allows for the creation of complex geometries and intricate shapes. This design freedom empowers engineers to push the boundaries of functionality and create innovative products.
- High Precision and Repeatability: Metal molding machines can produce parts with exceptional dimensional accuracy and a high degree of consistency. This is particularly advantageous for applications requiring precise tolerances and interchangeable parts.
- Mass Production Capability: Certain metal molding techniques, like die casting, excel at high-volume production. This makes them ideal for manufacturing large quantities of parts efficiently and cost-effectively.
- Material Versatility: Metal molding machines can handle a wide range of metal powders, from common materials like aluminum and steel to more exotic options like titanium and nickel alloys. This versatility allows manufacturers to tailor the material selection to the specific needs of the application.
- Near-Net-Shape Manufacturing: Some metal molding techniques, like MIM, can produce parts very close to their final shape. This minimizes the need for extensive post-processing steps, reducing manufacturing time and costs.
- Reduced Material Waste: Compared to subtractive manufacturing techniques that generate significant scrap material, metal molding offers a more efficient use of materials. This translates to cost savings and reduced environmental impact.
Beyond the Obvious: Additional Advantages to Consider
While the core advantages listed above are well-established, there are additional benefits to consider when evaluating metal molding machines:
- Improved Surface Finishes: Certain metal molding techniques can produce parts with excellent surface finishes, reducing or eliminating the need for additional finishing processes.
- Enhanced Mechanical Properties: Metal molding processes like powder bed fusion (PBF) can create parts with unique microstructures, leading to improved mechanical properties like strength and fatigue resistance.
- Lightweighting Potential: The ability to produce complex shapes with metal molding allows for the design of lightweight components, which is crucial in sectors like aerospace and automotive where weight reduction is a primary goal.
- Automation Potential: Many metal molding machines are highly automated, reducing reliance on manual labor and improving production efficiency and consistency.
It’s important to remember that no single manufacturing technology is a perfect fit for every application. Metal molding machines also have limitations to consider, which we’ll explore in the next section.
Disadvantages of Metal Molding Machines
While metal molding machines offer a plethora of advantages, they also come with certain limitations that need to be considered:
- High Initial Investment: Metal molding machines, particularly advanced technologies like PBF, can involve significant upfront costs. This can be a barrier for smaller companies or those with limited budgets.
- Tooling Costs: Depending on the specific metal molding technique, tooling costs can be substantial. This includes the cost of dies, molds, and other specialized equipment needed for the process.
- Minimum Order Quantities: Some metal molding techniques, like die casting, are most efficient for high-volume production. This can be a disadvantage for projects requiring smaller quantities of parts.
- Process Complexity: Operating metal molding machines, especially newer technologies like PBF, can require a high level of technical expertise and process control. This can necessitate specialized training for personnel.
- Material Limitations: While metal molding offers material versatility, there may be limitations on the types of powders that can be effectively processed with certain techniques.
- Post-Processing Requirements: While some metal molding techniques offer near-net-shape parts, some level of post-processing, such as heat treatment or machining, may still be necessary depending on the application requirements.
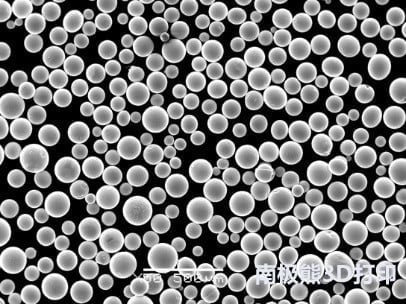
Câu hỏi thường gặp
In this section, we’ll address some frequently asked questions (FAQs) regarding metal molding machines:
Q: What is the difference between metal casting and metal molding?
A: The terms “metal casting” and “metal molding” are often used interchangeably. However, a subtle distinction can be made. Metal casting typically refers to processes that utilize molten metal poured into a mold cavity. Metal molding can encompass a broader range of techniques, including those that use metal powders instead of molten metal.
Q: What are the different types of metal molding machines?
A: There are various types of metal molding machines, each with its strengths and applications. Some common examples include:
- Die Casting Machines: These workhorses inject molten metal under high pressure into a reusable mold (die) for high-volume, intricate parts.
- Investment Casting Machines: This process creates a wax pattern, invests it in a ceramic mold, burns away the wax, and pours molten metal for near-net-shape castings with exceptional detail.
- Sand Casting Machines: The most traditional method, sand casting utilizes a carved sand mold for versatility and affordability, but with less dimensional accuracy.
- Metal Injection Molding (MIM) Machines: MIM combines plastic injection molding with powder metallurgy for complex, near-net-shape parts with good dimensional accuracy and material properties close to wrought metals.
Q: How do I choose the right metal molding machine for my project?
A: Selecting the right metal molding machine involves considering several factors:
- Part complexity: For intricate shapes, die casting or MIM might be suitable. Sand casting offers more flexibility for simpler geometries.
- Production volume: Die casting excels in high volume, while investment casting caters to smaller batches.
- Material requirements: Consider the desired properties and the compatibility with different metal powders.
- Cost constraints: Balance upfront costs (machine, tooling) with production costs (per-part) and post-processing needs.
Consulting with a metal molding expert can provide valuable guidance in selecting the optimal machine for your specific project requirements.
Q: What are the future trends in metal molding machines?
A: The future of metal molding machines is bright, with advancements in several areas:
- Additive Manufacturing (AM): AM techniques like Powder Bed Fusion (PBF) are revolutionizing metal molding by enabling the creation of complex geometries previously impossible with traditional methods.
- Advanced Materials: The development of new metal powders with superior properties like high strength-to-weight ratios and improved corrosion resistance will expand the capabilities of metal molding.
- Automation and Integration: Increased automation and integration of robots and other technologies will enhance efficiency, consistency, and safety in metal molding processes.
These advancements promise to push the boundaries of what’s possible with metal molding, creating exciting opportunities for future innovations.
About 3DP mETAL
Product Category
LIÊN HỆ
Bạn có thắc mắc không? Hãy gửi tin nhắn ngay cho chúng tôi! Sau khi nhận được tin nhắn của bạn, chúng tôi sẽ xử lý yêu cầu của bạn với cả một đội ngũ.