Overview of Phân phối kích thước hạt
Particle size distribution (PSD) is a crucial concept in materials science and engineering, especially when dealing with powders and granular materials. It refers to the distribution of different sizes of particles within a given sample and significantly impacts the material’s physical and chemical properties. Understanding PSD is essential for optimizing product performance and ensuring quality in various applications, including pharmaceuticals, metallurgy, and additive manufacturing.
This comprehensive guide delves into the specifics of PSD, covering its types, measurement techniques, significance, and applications. We’ll also look at specific metal powder models and provide detailed comparisons to help you make informed decisions. By the end of this article, you’ll have a thorough understanding of particle size distribution and its importance in your field.
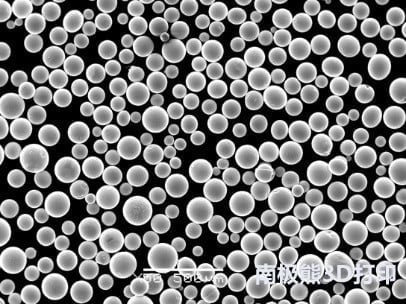
Types and Measurement of Particle Size Distribution
Understanding Particle Size Distribution Types
Particle size distribution can be classified based on the nature and size of the particles. Here are the main types:
- Monomodal Distribution: A single peak representing most particles within a specific size range.
- Bimodal Distribution: Two distinct peaks indicating two predominant particle sizes.
- Multimodal Distribution: Multiple peaks showing a range of dominant particle sizes.
- Cumulative Distribution: The cumulative percentage of particles below a particular size.
Measurement Techniques for Phân phối kích thước hạt
Several methods are used to measure particle size distribution, each suitable for different types of materials and size ranges:
- Laser Diffraction: Uses laser light scattering to measure particle sizes ranging from nanometers to millimeters.
- Dynamic Light Scattering (DLS): Ideal for submicron particles, it measures Brownian motion to determine particle size.
- Rây: A simple, traditional method for larger particles using a series of sieves with different mesh sizes.
- Sedimentation: Measures the rate at which particles settle in a fluid to determine size.
- Image Analysis: Uses microscopes and cameras to capture and analyze particle images.
Comparative Table of Measurement Techniques
Technique | Phạm vi kích thước | Lợi ích | Hạn chế |
---|---|---|---|
Laser Diffraction | Nanometers to mm | Wide size range, fast, accurate | Expensive equipment |
Dynamic Light Scattering | Nanometers to microns | High resolution for small particles, non-destructive | Limited to small particles, sensitive to contaminants |
Rây | Microns to mm | Simple, low cost, suitable for large particles | Limited precision, labor-intensive |
Sedimentation | Microns to mm | Effective for larger particles, cost-effective | Time-consuming, affected by fluid properties |
Image Analysis | Nanometers to mm | Detailed particle shape and size information | Requires high-quality imaging equipment |
Significance of Particle Size Distribution
Particle size distribution significantly affects the material’s behavior and performance in various applications. Here’s why PSD is important:
- Khả năng chảy: Smaller particles may lead to poor flow properties, impacting processes like powder coating and additive manufacturing.
- Diện tích bề mặt: Finer particles increase surface area, enhancing reactivity and dissolution rates in pharmaceuticals.
- Packing Density: PSD influences how particles pack together, affecting material strength and porosity.
- Stability: Uniform particle size can improve suspension stability in liquids.
Applications of Particle Size Distribution
PSD plays a crucial role across numerous industries. Here are some notable applications:
Ngành | Ứng dụng | PSD Significance |
---|---|---|
Pharmaceuticals | Drug formulation, bioavailability | Controls dissolution rates and bioavailability |
Metallurgy | Powder metallurgy, additive manufacturing | Affects mechanical properties and sintering behavior |
Ceramics | Ceramic tile production, glaze formulations | Influences strength and finish quality |
Agriculture | Fertilizers, pesticides | Determines application efficacy and dispersion |
Food | Powdered foods, ingredients | Impacts texture, stability, and taste |
Specific Metal Powder Models and Their PSD
Let’s explore some specific metal powder models, each with unique particle size distributions tailored for various applications:
- 316L Stainless Steel Powder
- Miêu tả: Used in additive manufacturing and powder metallurgy.
- PSD: Monomodal distribution with a mean particle size of 15-45 microns.
- thuộc tính: High corrosion resistance, excellent mechanical properties.
- Ti-6Al-4V Titanium Alloy Powder
- Miêu tả: Popular in aerospace and medical implants.
- PSD: Bimodal distribution with peaks at 20 and 40 microns.
- thuộc tính: High strength-to-weight ratio, biocompatibility.
- AlSi10Mg Aluminum Alloy Powder
- Miêu tả: Ideal for lightweight structural components.
- PSD: Monomodal distribution, 10-50 microns.
- thuộc tính: Good thermal properties, lightweight.
- Inconel 718 Nickel Alloy Powder
- Miêu tả: Used in high-temperature applications like turbines.
- PSD: Monomodal distribution, 15-53 microns.
- thuộc tính: Excellent heat and corrosion resistance.
- Cobalt-Chrome Alloy Powder
- Miêu tả: Utilized in dental and orthopedic implants.
- PSD: Monomodal distribution, 10-45 microns.
- thuộc tính: High wear resistance, biocompatible.
- Copper Powder
- Miêu tả: Used in conductive and thermal management applications.
- PSD: Multimodal distribution, 5-50 microns.
- thuộc tính: Excellent electrical and thermal conductivity.
- Tool Steel Powder
- Miêu tả: Essential for making high-strength tools and molds.
- PSD: Bimodal distribution, 10 and 50 microns.
- thuộc tính: High hardness and wear resistance.
- Tungsten Carbide Powder
- Miêu tả: Used for cutting tools and wear-resistant coatings.
- PSD: Monomodal distribution, 1-10 microns.
- thuộc tính: Extremely hard, high melting point.
- NiTi Shape Memory Alloy Powder
- Miêu tả: Utilized in medical devices and actuators.
- PSD: Monomodal distribution, 10-45 microns.
- thuộc tính: Shape memory effect, superelasticity.
- Zirconium Powder
- Miêu tả: Applied in nuclear reactors and chemical processing.
- PSD: Multimodal distribution, 5-40 microns.
- thuộc tính: High corrosion resistance, good thermal properties.
Table: Properties and Applications of Metal Powder Models
Metal Powder | Mean Particle Size (Microns) | thuộc tính | ỨNG DỤNG |
---|---|---|---|
316L Stainless Steel | 15-45 | Corrosion resistance, mechanical strength | Additive manufacturing, powder metallurgy |
Ti-6Al-4V Titanium Alloy | 20, 40 | High strength, biocompatibility | Aerospace, medical implants |
AlSi10Mg Aluminum Alloy | 10-50 | Lightweight, thermal properties | Cấu phần cấu trúc |
Inconel 718 Nickel Alloy | 15-53 | Heat and corrosion resistance | Turbines, high-temperature applications |
Cobalt-Chrome Alloy | 10-45 | Wear resistance, biocompatibility | Dental, orthopedic implants |
Đồng | 5-50 | Electrical, thermal conductivity | Conductive, thermal management |
Tool Steel | 10, 50 | Hardness, wear resistance | Tools, molds |
Tungsten Carbide | 1-10 | Hardness, high melting point | Cutting tools, coatings |
NiTi Shape Memory Alloy | 10-45 | Shape memory, superelasticity | Medical devices, actuators |
Zirconium | 5-40 | Corrosion resistance, thermal properties | Nuclear reactors, chemical processing |
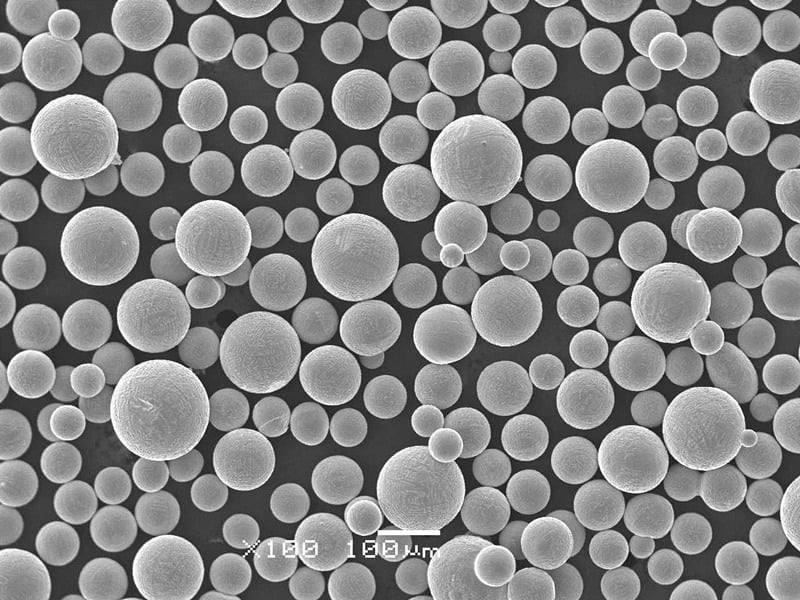
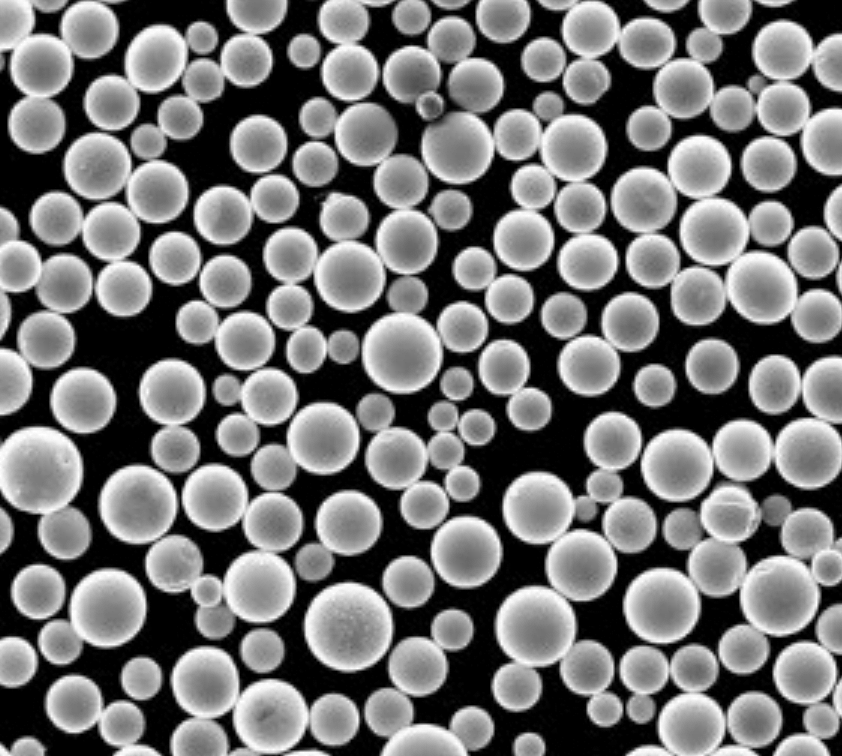
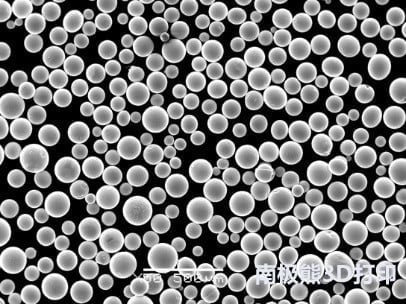
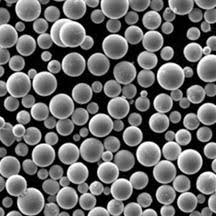
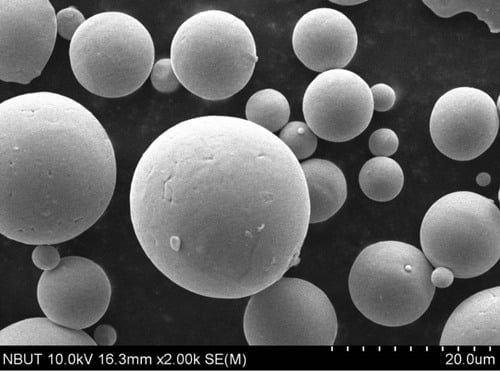
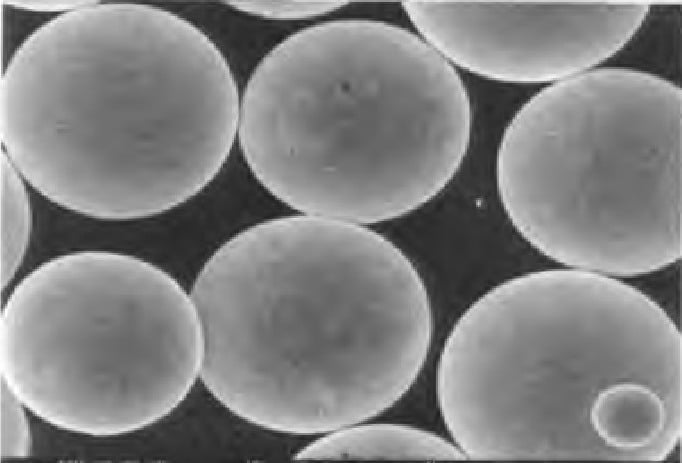
Comparing Particle Size Distribution Methods
Laser Diffraction vs. Dynamic Light Scattering
When choosing between laser diffraction and dynamic light scattering, consider the particle size range and the nature of the material. Laser diffraction is versatile and can handle a wide range of sizes, making it suitable for many industrial applications. Dynamic light scattering, on the other hand, is best for small particles, providing high-resolution data for nanoparticles.
Sieving vs. Sedimentation
Sieving is straightforward and ideal for larger particles, making it a go-to method for industries dealing with coarse materials. Sedimentation, however, offers more precision for particles that can settle in a fluid, although it is more time-consuming.
Pros and Cons Table: Measurement Techniques
Technique | Ưu điểm | Nhược điểm |
---|---|---|
Laser Diffraction | Wide size range, fast, accurate | Expensive equipment |
Dynamic Light Scattering | High resolution for small particles, non-destructive | Limited to small particles, sensitive to contaminants |
Rây | Simple, low cost, suitable for large particles | Limited precision, labor-intensive |
Sedimentation | Effective for larger particles, cost-effective | Time-consuming, affected by fluid properties |
Image Analysis | Detailed particle shape and size information | Requires high-quality imaging equipment |
Suppliers and Pricing of Metal Powders
Metal Powder | Nhà cung cấp | Price (per kg) | Lớp |
---|---|---|---|
316L Stainless Steel | Carpenter Technology | $80 | ASTM A240 |
Ti-6Al-4V Titanium Alloy | Praxair Surface Technologies | $150 | AMS 4998 |
AlSi10Mg Aluminum Alloy | ECKART America | $50 | ISO 9001 |
Inconel 718 Nickel Alloy | VDM Metals | $200 | AMS 5662 |
Cobalt-Chrome Alloy | EOS GmbH | $180 | ISO 5832-4 |
Đồng | American Elements | $25 | ASTM B170 |
Tool Steel | Höganäs AB | $70 | AISI P20 |
Tungsten Carbide | Kennametal | $300 | ISO 9001 |
NiTi Shape Memory Alloy | Fort Wayne Metals | $400 | ASTM F2063 |
Zirconium | ATI Metals | $350 | ASTM B551 |
Advantages and Limitations of Different Metal Powders
Metal Powder | Lợi ích | Hạn chế |
---|---|---|
316L Stainless Steel | Corrosion resistance, mechanical strength | Higher cost compared to carbon steel |
Ti-6Al-4V Titanium Alloy | High strength-to-weight ratio, biocompatibility | Expensive, challenging to machine |
AlSi10Mg Aluminum Alloy | Lightweight, good thermal properties | Lower strength compared to other alloys |
Inconel 718 Nickel Alloy | Heat and corrosion resistance | High cost |
Cobalt-Chrome Alloy | Wear resistance, biocompatibility | Expensive, difficult to process |
Đồng | Độ dẫn điện và dẫn nhiệt tuyệt vời | Susceptible to oxidation |
Tool Steel | High hardness and wear resistance | Requires heat treatment |
Tungsten Carbide | Extremely hard, high melting point | Brittle, high cost |
NiTi Shape Memory Alloy | Shape memory effect, superelasticity | Expensive, complex processing |
Zirconium | High corrosion resistance, good thermal properties | Expensive, limited availability |
Specifications, Sizes, and Standards
Metal Powder | Đặc điểm kỹ thuật | Size Range (Microns) | Tiêu chuẩn |
---|---|---|---|
316L Stainless Steel | Spherical, gas atomized | 15-45 | ASTM A240 |
Ti-6Al-4V Titanium Alloy | Spherical, plasma atomized | 20-40 | AMS 4998 |
AlSi10Mg Aluminum Alloy | Spherical, gas atomized | 10-50 | ISO 9001 |
Inconel 718 Nickel Alloy | Spherical, gas atomized | 15-53 | AMS 5662 |
Cobalt-Chrome Alloy | Spherical, gas atomized | 10-45 | ISO 5832-4 |
Đồng | Spherical, electrolytic | 5-50 | ASTM B170 |
Tool Steel | Irregular, water atomized | 10-50 | AISI P20 |
Tungsten Carbide | Spherical, sintered | 1-10 | ISO 9001 |
NiTi Shape Memory Alloy | Spherical, plasma atomized | 10-45 | ASTM F2063 |
Zirconium | Spherical, gas atomized | 5-40 | ASTM B551 |
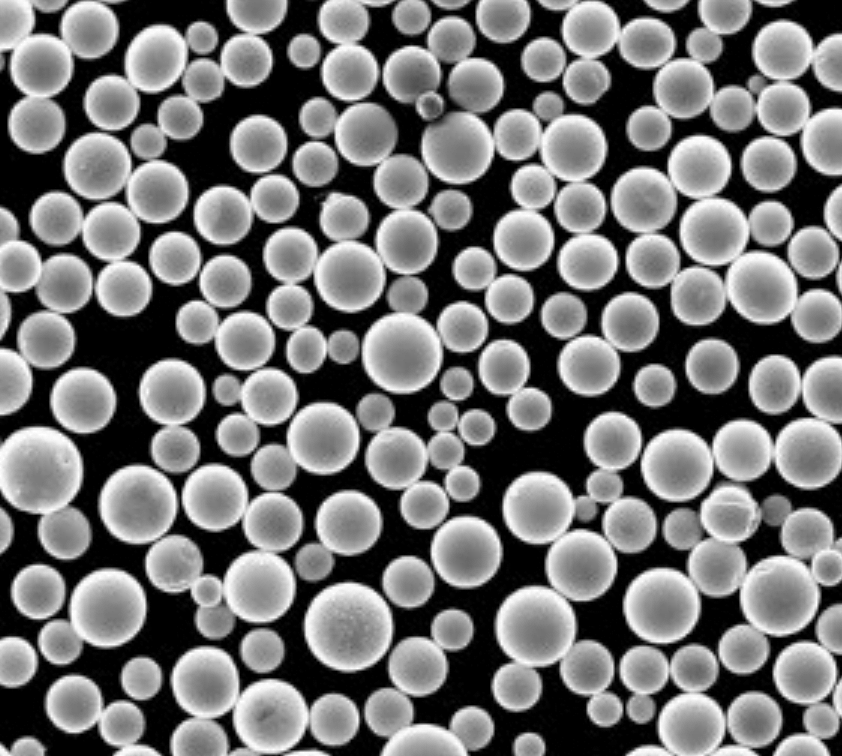
Câu hỏi thường gặp
Question | Answer |
---|---|
What is particle size distribution (PSD)? | PSD is the distribution of particle sizes in a given sample, affecting material properties and behavior. |
Why is PSD important? | It influences flowability, surface area, packing density, and stability, impacting various applications. |
What are the common methods for measuring PSD? | Laser diffraction, dynamic light scattering, sieving, sedimentation, and image analysis are commonly used. |
How does PSD affect pharmaceuticals? | PSD controls drug dissolution rates and bioavailability, crucial for effective drug delivery. |
Which industries rely heavily on PSD? | Pharmaceuticals, metallurgy, ceramics, agriculture, and food industries all rely on PSD for quality control. |
What is a monomodal distribution? | A single peak in the PSD graph, indicating most particles are within a specific size range. |
What is a bimodal distribution? | Two distinct peaks in the PSD graph, indicating two predominant particle sizes. |
Can PSD be tailored for specific applications? | Yes, by controlling the production process, PSD can be optimized for specific performance requirements. |
What is the role of PSD in additive manufacturing? | PSD affects powder flowability, packing density, and final product properties in additive manufacturing. |
How do suppliers ensure consistent PSD in metal powders? | Through rigorous quality control and standardized production processes. |
Kết luận
Understanding particle size distribution is vital for optimizing material properties and ensuring high performance in various applications. Whether you’re working in pharmaceuticals, metallurgy, or additive manufacturing, a thorough grasp of PSD can significantly enhance your processes and product quality. By leveraging the right measurement techniques and selecting appropriate metal powder models, you can achieve desired outcomes in your projects.
Exploring the intricacies of PSD, from measurement methods to applications, helps in making informed decisions that impact both efficiency and quality. As technology advances, the precision and applicability of PSD measurement will continue to evolve, offering even greater control and insight into material behavior.
About 3DP mETAL
Product Category
LIÊN HỆ
Bạn có thắc mắc không? Hãy gửi tin nhắn ngay cho chúng tôi! Sau khi nhận được tin nhắn của bạn, chúng tôi sẽ xử lý yêu cầu của bạn với cả một đội ngũ.