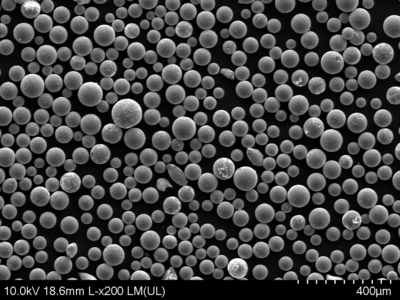
Best IN939 Powder for 3D Printing in 2023
Overview of IN939 Powder for 3D Printing IN939 is a high-performance nickel-based superalloy powder designed for additive manufacturing of critical components needing exceptional mechanical properties at high temperatures. This article provides a comprehensive guide to IN939 powder for 3D printing applications across aerospace, automotive, energy and industrial sectors. Key aspects covered include IN939 composition, properties,…
MOQ nhỏ
Tìm nguồn cung ứng linh hoạt cho hàng trăm sản phẩm
Hỗ trợ tùy chỉnh
Bột tùy chỉnh theo ngành
Giao hàng nhanh chóng
Bằng DHL Express, an toàn và nhanh chóng trực tiếp đến tay bạn
Overview of IN939 Powder for 3D Printing
IN939 is a high-performance nickel-based superalloy powder designed for additive manufacturing of critical components needing exceptional mechanical properties at high temperatures. This article provides a comprehensive guide to IN939 powder for 3D printing applications across aerospace, automotive, energy and industrial sectors.
Key aspects covered include IN939 composition, properties, print parameters, applications, specifications, suppliers, handling, inspection, comparisons to alternatives, advantages and limitations, and frequently asked questions. Quantitative data is presented in easy-to-reference tables.
Composition of IN939 Powder
IN939 has a complex precipitation hardening alloy composition:
Nguyên tố | Tỉ trọng | Mục đích |
---|---|---|
Niken | Sự cân bằng | Principal matrix element |
Chrome | 15 – 18 | Khả năng chống ôxi hóa |
Nhôm | 3.8 – 4.8 | Phân cứng kết tủa |
Titan | 0.9 – 1.4 | Phân cứng kết tủa |
Cô ban | 12 – 15 | Solid solution strengthening |
Tantal | 3.8 – 4.8 | Carbide former |
Carbon | 0.05 – 0.15 | Carbide former |
Boron | 0.006 – 0.012 | Grain boundary strengthener |
Trace quantities of zirconium, magnesium and sulphur are also added for enhanced properties.
Properties of IN939 Powder
IN939 possesses an exceptional combination of properties:
Bất động sản | Miêu tả |
---|---|
độ bền cao | Excellent tensile and creep rupture strength up to 1050¡«C |
Tính ổn định nhiệt | Strength maintained up to 1000¡«C |
Creep resistance | High stress-rupture life at high temperatures |
Khả năng chống ôxi hóa | Forms protective Cr2O3 oxide scale |
Thermal fatigue resistance | Resists cracking during thermal cycling |
Phase stability | Microstructure stable after prolonged exposures |
Khả năng chống ăn mòn | Resistant to hot corrosion, oxidation, sulfidation |
The properties enable use under extreme thermal and mechanical loads.
3D Printing Parameters for IN939 Powder
Typical AM processing parameters for IN939 include:
Tham số | Typical value | Mục đích |
---|---|---|
Layer thickness | 20-50 õm | Resolution vs build speed |
Laser power | 250-500 W | Sufficient melting without evaporation |
Scan speed | 800-1200 mm/s | Density vs production rate |
Hatch spacing | 100-200 Ã×m | Mechanical properties |
Support structure | Minimal | Easy removal |
Hot isostatic pressing | 1160¡«C, 100 MPa, 3h | Eliminate porosity |
Parameters are optimized for attributes like density, microstructure, build rate, and post-processing requirements.
Applications of 3D Printed IN939 Parts
Additively manufactured IN939 components serve critical applications including:
Ngành | Thành phần |
---|---|
Hiệp công | Cánh tua-bin, cánh tĩnh, buồng đốt |
Phát điện | Hot gas path parts, heat exchangers |
Ô tô | Turbocharger wheels, valves |
Xử lý hóa chất | Pumps, valves, reaction vessels |
Benefits over conventionally processed IN939 include complex geometries and reduced lead time.
Specifications of IN939 Powder for 3D Printing
IN939 powder for AM must meet exacting specifications:
Tham số | Đặc điểm kỹ thuật |
---|---|
Kích thước hạt | 15-45 Ã×m typical |
Hình dạng hạt | Spherical morphology |
Mật độ biểu kiến | > 4 g/cc |
Mật độ chịu nén | > 6 g/cc |
Lưu lượng phòng | > 23 sec for 50 g |
Sạch sẽ | >99.9% |
Hàm lượng oxy | <100 ppm |
Tighter tolerances, custom size distributions, and controlled impurity levels available.
Suppliers of IN939 Powder
Reputable suppliers of IN939 powder include:
Nhà cung cấp | Địa điểm |
---|---|
Sandvik Osprey | Vương quốc Anh |
Công ty dịch vụ sản xuất phụ gia Carpenter | Hoa Kỳ |
Praxair | Hoa Kỳ |
AP&C | Canada |
Erasteel | Thụy Điển |
AMETEK | Hoa Kỳ |
Pricing for IN939 powder ranges from $110/kg to over $220/kg based on quality and order volume.
Handling and Storage of IN939 Powder
As a reactive powder, careful handling of IN939 is needed:
- Store sealed containers in a cool, inert atmosphere
- Prevent contact with moisture, oxygen, acids
- Use properly grounded equipment
- Avoid dust accumulation to minimize explosion risk
- Local exhaust ventilation recommended
- Wear appropriate PPE while handling
Proper techniques and controls prevent IN939 powder oxidation or contamination.
Inspection and Testing of IN939 Powder
IN939 powder is validated using:
Phương pháp | Parameters Tested |
---|---|
Phân tích rây | Phân phối kích thước hạt |
Hình ảnh SEM | Particle morphology |
EDX | Chemistry and composition |
XRD | Phases present |
Pycnometry | Mật độ |
Lưu lượng phòng | Lưu lượng bột |
Testing per applicable ASTM standards ensures batch consistency.
Comparing IN939 to Alternative Alloy Powders
IN939 compares to other Ni-based superalloys as:
Hợp kim | Độ bền ở nhiệt độ cao | Chi phí | Printability | Độ dẻo dai |
---|---|---|---|---|
IN939 | Xuất sắc | Cao | Xuất sắc | Thấp |
IN738 | Tốt | Trung bình | Xuất sắc | Trung bình |
IN718 | Công bằng | Thấp | Tốt | Xuất sắc |
Hastelloy X | Xuất sắc | Cao | Công bằng | Trung bình |
For balanced properties and processability, IN939 supersedes alternatives like IN718 or Hastelloy X.
Pros and Cons of IN939 Powder for 3D Printing
Ưu điểm | Nhược điểm |
---|---|
Exceptional high temperature strength | Expensive compared to IN718 |
Excellent oxidation and creep resistance | Significant parameter optimization needed |
Complex geometries feasible | Limited room temperature ductility |
Faster processing than cast/wrought | Controlled storage and handling environment |
Comparable properties to cast alloy | Difficult to machine after printing |
IN939 enables high-performance printed parts but with higher costs and controlled processing needs.
Frequently Asked Questions about IN939 Powder for 3D Printing
Q: What particle size range works best for printing IN939?
A: A particle size range of 15-45 microns provides good flowability combined with high resolution and density. Finer particles below 10 microns can improve density and surface finish.
Q: Does IN939 require any post-processing after 3D printing?
A: Post processes like hot isostatic pressing, heat treatment, and machining are usually needed to eliminate porosity, relieve stresses, and achieve final tolerances and surface finish.
Q: What precision can be achieved with IN939 printed parts?
A: After post-processing, dimensional accuracy and surface finish comparable to CNC machined parts can be achieved with IN939 AM components.
Q: Are support structures necessary for printing IN939 powder?
A: Minimal supports are recommended for complex channels and overhangs to prevent deformation and facilitate easy removal. IN939 powder has good flowability.
Q: What alloy powder is the closest alternative to IN939 for AM?
A: IN738 is the closest alternative in terms of balanced properties and maturity for additive manufacturing. Other alloys like IN718 or Hastelloy X have some trade-offs.
Q: Is IN939 compatible with direct metal laser sintering (DMLS)?
A: Yes, IN939 is readily processable by major powder bed fusion techniques including DMLS along with selective laser melting (SLM) and electron beam melting (EBM).
Q: What density is achievable with 3D printed IN939 components?
A: With optimized parameters, densities over 99% are achievable, matching properties of traditionally processed IN939 products.
Q: How do the properties of printed IN939 compare to cast alloy?
A: Additively manufactured IN939 exhibits comparable or better mechanical properties and microstructure compared to conventional cast and wrought forms.
Q: What defects can occur when printing with IN939 powder?
A: Potential defects are cracking, distortion, porosity, surface roughness, incomplete fusion etc. Most can be prevented by proper parameter optimization and powder quality.
Q: Is hot isostatic pressing (HIP) mandatory for IN939 AM parts?
A: HIP eliminates internal voids and improves fatigue resistance. For less demanding applications, heat treatment alone may suffice instead of HIP.
Liên lạc với chúng tôi ngay
Vui lòng liên hệ với chúng tôi để biết báo giá sản phẩm gần đây và tình trạng còn hàng trong kho.