Titanium alloys, renowned for their exceptional strength-to-weight ratio, exceptional corrosion resistance, and biocompatibility, have revolutionized various industries. But what if we could harness these properties in a revolutionary new form? Enter titanium alloy powders – the game-changer in additive manufacturing and beyond.
What are Titanium Alloy Powders?
Imagine taking the incredible properties of titanium alloys and miniaturizing them into a fine, metallic powder. That’s the magic of titanium alloy powders. These tiny, granular particles, typically ranging from 10 to 150 microns in size, unlock a whole new world of possibilities for creating complex, high-performance components.
Types, Composition, and Properties of Titanium Alloy Powders
Just like their bulk counterparts, titanium alloy powders come in a variety of flavors, each with its unique set of properties tailored for specific applications. Here’s a closer look at some of the most popular models:
Mô hình | Sáng tác | Key Properties | ỨNG DỤNG |
---|---|---|---|
Ti-6Al-4V (Grade 23) | 90% Ti, 6% Aluminum (Al), 4% Vanadium (V) | High strength, excellent corrosion resistance, good biocompatibility | Aerospace components, biomedical implants, sporting goods |
CP Ti (Grade 1) | 99.4% Ti (minimum) | Excellent ductility, good corrosion resistance | Chemical processing equipment, filtration systems, biomedical devices |
CP Ti (Grade 2) | 99% Ti (minimum) | Higher strength than Grade 1, good corrosion resistance | Aerospace components, automotive parts, medical devices |
Ti-6Al-4V (ELI) | 90% Ti, 6% Aluminum (Al), 4% Vanadium (V), Lower Oxygen & Nitrogen content | High strength-to-weight ratio, excellent corrosion resistance, superior biocompatibility | Medical implants, aerospace components demanding high fatigue strength |
Ti-17CuNi | 73% Ti, 17% Copper (Cu), 10% Nickel (Ni) | High strength, good wear resistance, excellent biocompatibility | Biomedical implants, dental applications |
Ti-5Al-2.5Sn | 92.5% Ti, 5% Aluminum (Al), 2.5% Tin (Sn) | High strength, good ductility, superior workability | Aerospace components, golf clubs |
Beta Ti Alloy (Ti-29Nb-13Ta-4.6Zr) | 72.8% Ti, 29% Niobium (Nb), 13% Tantalum (Ta), 4.6% Zirconium (Zr) | High strength, excellent creep resistance at high temperatures | Jet engine components, heat exchangers |
Nickel Titanium (Nitinol) | Titanium & Nickel Alloy | Shape memory effect, superelasticity | Medical devices, eyeglass frames |
Ti-4Al-3Mo-1V | 87% Ti, 4% Aluminum (Al), 3% Molybdenum (Mo), 1% Vanadium (V) | High strength, good high-temperature performance | Aerospace components, missile components |
Ti-Mo | Titanium & Molybdenum Alloy | High creep resistance, excellent oxidation resistance | Gas turbine components, chemical processing equipment |
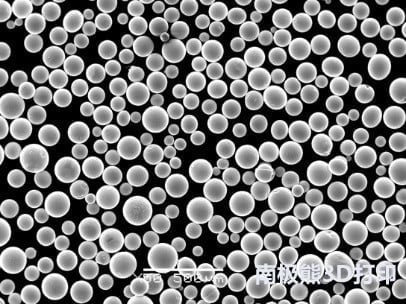
Applications of Titanium Alloy Powders
The possibilities with titanium alloy powders are truly boundless. Here are just a few of the industries benefiting from this revolutionary material:
Ngành | ỨNG DỤNG | Lợi ích |
---|---|---|
Hiệp công | Jet engine components, landing gear parts, airframe components | Lighter weight for increased fuel efficiency, exceptional strength-to-weight ratio |
Y sinh | Hip and knee replacements, dental implants, surgical instruments | Excellent biocompatibility, reduces risk of rejection, superior corrosion resistance |
Ô tô | High-performance engine components, lightweight suspension parts | Reduced weight improves fuel efficiency, high strength for demanding applications |
Hàng hóa tiêu dùng | Sports equipment (golf clubs, bicycle frames), jewelry, luxury watches | High strength-to-weight ratio for enhanced performance, unique aesthetics |
Xử lý hóa chất | Pumps, valves, reactors | Exceptional corrosion resistance for handling harsh chemicals |
Advantages and Considerations of Titanium Alloy Powders
Advantages:
- Unparalleled Strength-to-Weight Ratio: Imagine a material that’s incredibly strong yet surprisingly lightweight. That’s the magic of titanium alloy powders. Compared to traditional manufacturing techniques, additive manufacturing with titanium powders allows for the creation of complex, lightweight components that outperform heavier alternatives. In the ever-weight-conscious world of aerospace, this translates to increased fuel efficiency and longer flight ranges.
- Exceptional Corrosion Resistance: Titanium’s natural affinity for forming a protective oxide layer makes it highly resistant to corrosion. This property carries over to titanium alloy powders, making them ideal for applications exposed to harsh environments. Chemical processing equipment, marine components, and even biomedical implants benefit from the exceptional corrosion resistance of titanium alloy powders.
- Design Freedom and Complex Geometries: Unlike traditional manufacturing methods that can be limited by material properties and machining complexities, additive manufacturing with titanium powders opens doors to unparalleled design freedom. Think intricate lattice structures for weight reduction or internal channels for improved fluid flow – these complex geometries are easily achievable with titanium powder-based additive manufacturing.
- Biocompatible Bonanza: For those seeking materials that work harmoniously with the human body, titanium alloy powders are a dream come true. Their excellent biocompatibility makes them a perfect choice for medical implants, such as hip and knee replacements. The body readily accepts titanium implants, minimizing the risk of rejection and ensuring a long service life.
- Reduced Material Waste: Traditional manufacturing processes often generate significant amounts of scrap material. This is minimized with additive manufacturing using titanium powders. Only the necessary amount of powder is used to create the desired component, significantly reducing waste and lowering overall production costs.
Considerations:
- Powder Handling and Storage: Titanium alloy powders are susceptible to moisture and oxygen contamination, which can affect their flowability and printability. Proper handling and storage techniques, such as inert gas environments and desiccants, are crucial to maintain powder quality and ensure successful printing.
- Cost Factor: Titanium, by its very nature, is a relatively expensive material. This translates to higher costs for titanium alloy powders compared to some other metal powders. However, the exceptional properties and performance benefits often outweigh the initial cost, especially for high-value applications.
- Process Optimization: Additive manufacturing with titanium alloy powders is still a relatively new technology. As with any new process, there’s a learning curve involved. Optimizing printing parameters for different powder types and achieving consistent quality across production runs requires ongoing research and development.
- Surface Finish Considerations: Components printed with titanium alloy powders may have a rougher surface finish compared to traditionally machined parts. While post-processing techniques can improve surface smoothness, it’s an additional step to consider in the overall production process.
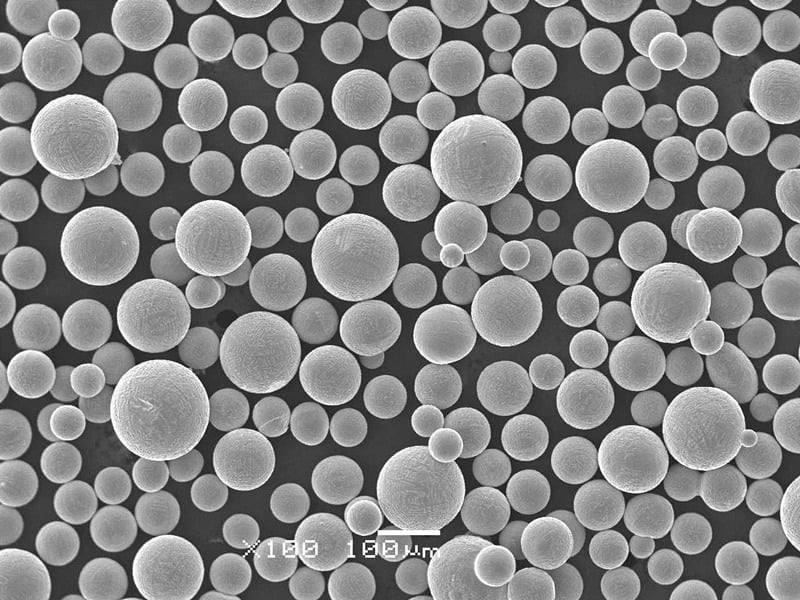
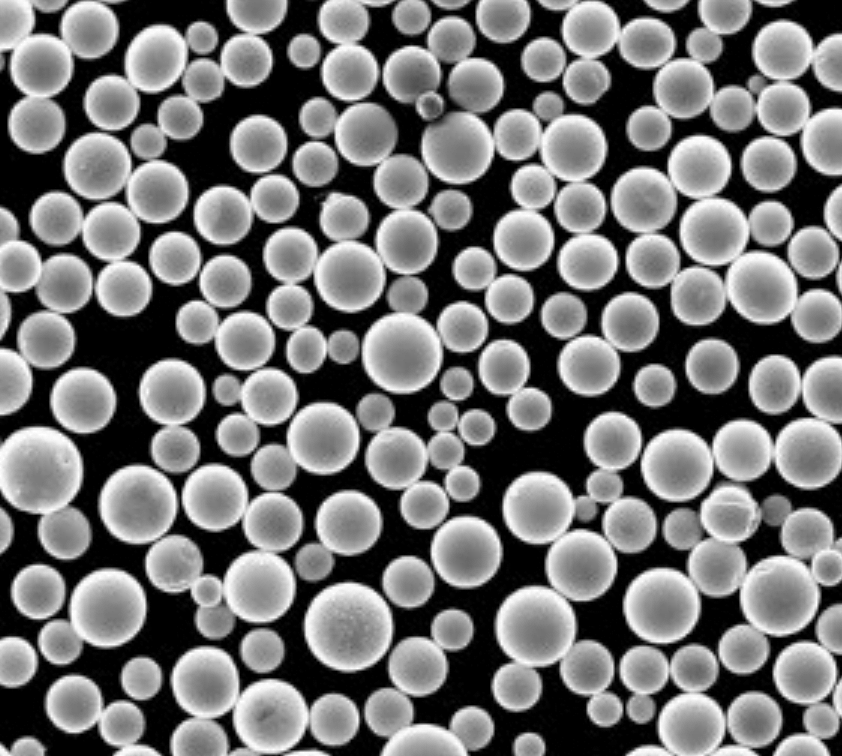
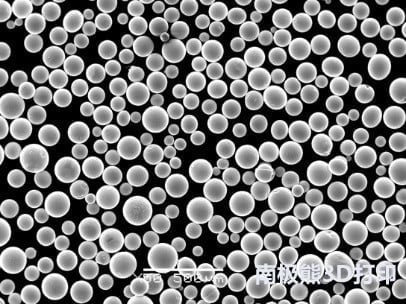
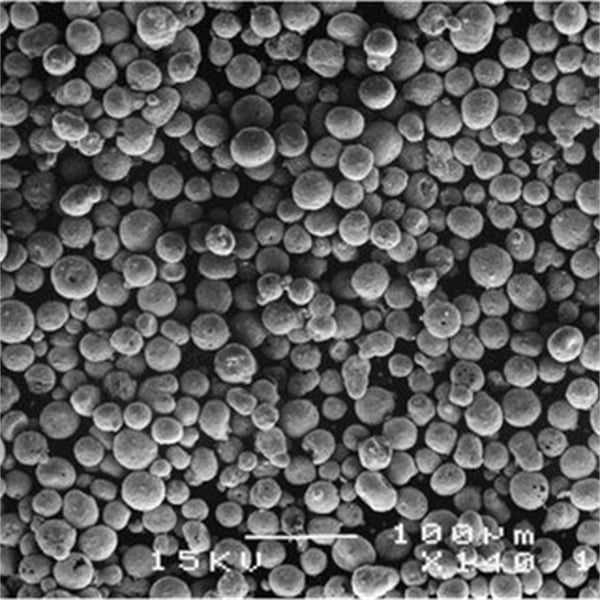
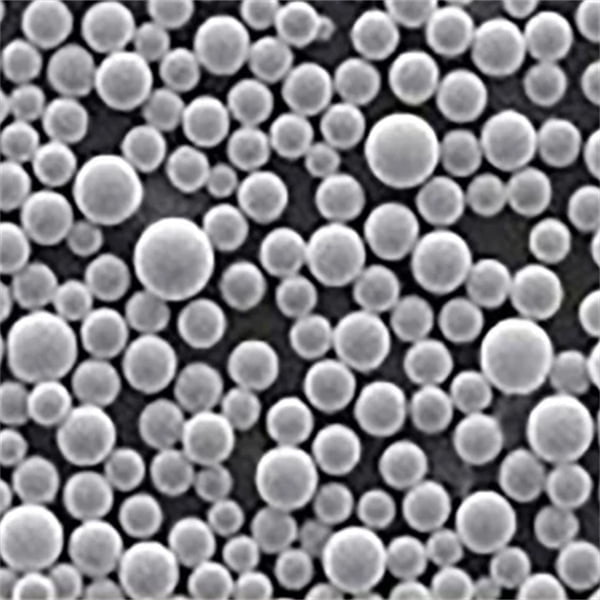
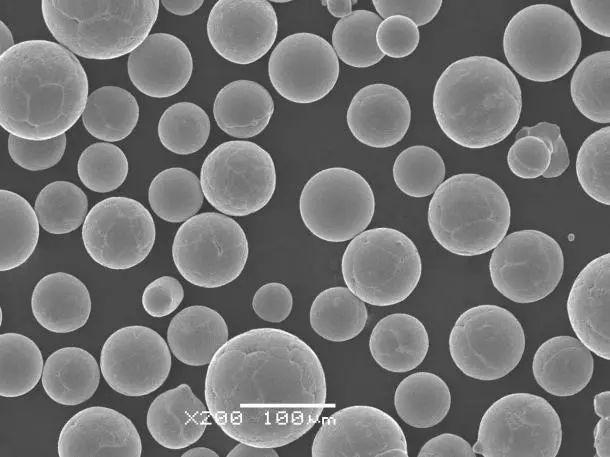
Specifications, Sizes, Grades, and Standards of Titanium Alloy Powders
When selecting titanium alloy powders for a particular application, several factors come into play. Here’s a breakdown of key specifications to consider:
Đặc điểm kỹ thuật | Miêu tả | Importance |
---|---|---|
Kích thước hạt | The diameter of individual powder particles, typically ranging from 10 to 150 microns | Affects flowability, printability, and final surface finish of the printed component. |
Phân phối kích thước hạt | The variation in size of the powder particles within a batch | A consistent distribution ensures optimal packing density and printability. |
Sphericity | The degree to which powder particles are spherical | Spherical particles flow better and pack more efficiently, leading to improved printability. |
Khả năng chảy | The ease with which powder flows | Critical for smooth and consistent feeding of powder during the additive manufacturing process. |
Phân loại chất bột | Refers to the chemical composition and mechanical properties of the powder | Matches the desired properties of the final printed component. |
Standards:
Several industry standards govern the production and quality control of titanium alloy powders. These standards ensure consistency and reliability for critical applications:
- ASTM International (ASTM): ASTM provides various standards for metal powders, including specifications for particle size distribution, chemical composition, and mechanical properties.
- Aerospace Material Specifications (AMS): Developed by SAE International, AMS standards are widely used in the aerospace industry for metallic materials, including titanium alloy powders.
- Medical Device Standards: Standards such as ISO 13485 and ASTM F67 set guidelines for the biocompatibility and safety of materials used in medical devices, including titanium alloy powders for implants.
Suppliers and Pricing of Titanium Alloy Powders
The global market for titanium alloy powders is experiencing significant growth, driven by the increasing adoption of additive manufacturing technologies. Several leading suppliers offer a wide range of titanium alloy powders catering to diverse applications.
Major Suppliers:
- AM powders (AM Powders Co., Ltd. – A subsidiary of Aluminum Corporation of China Limited) (China): A leading global supplier of metal powders for additive manufacturing, AM Powders offers a broad selection of titanium alloy powders in various grades and particle sizes.
- Arcam AB (Sweden): A pioneer in metal additive manufacturing, Arcam offers high-quality titanium alloy powders specifically optimized for their Electron Beam Melting (EBM) additive manufacturing systems.
- Carpenter Additive Manufacturing (USA): A trusted name in metal alloys, Carpenter Additive Manufacturing provides titanium alloy powders known for their consistency and excellent printability.
- Höganäs AB (Sweden): A world leader in metal powder manufacturing, Höganäs offers a comprehensive portfolio of titanium alloy powders for various additive manufacturing applications.
- LPW Technology Ltd (UK): A leading provider of powder-bed fusion additive manufacturing systems, LPW also offers a range of titanium alloy powders optimized for their specific machines.
- Merck KGaA, Darmstadt, Germany (Germany): A renowned chemical and pharmaceutical company, Merck also has a division dedicated to metal powders, including titanium alloy powders for additive manufacturing.
- OM Materials (UK): Specializing in high-performance materials, OM Materials offers titanium alloy powders catering to demanding applications in aerospace and other sectors.
- Plasma Atom (USA): A leading manufacturer of titanium and titanium alloy powders, Plasma Atom offers powders known for their purity and consistency.
- Sandvik Additive Manufacturing (Sweden): A subsidiary of the global engineering giant Sandvik, Sandvik Additive Manufacturing offers titanium alloy powders tailored for their additive manufacturing systems.
- TLS Technik GmbH & Co. KG (Germany): A specialist in metal powders for additive manufacturing, TLS Technik offers titanium alloy powders with specific properties for various applications.
Pricing Considerations:
The pricing of titanium alloy powders can vary depending on several factors, including:
- Powder type (alloy composition): More complex alloys with higher performance characteristics typically command a premium price.
- Particle size and distribution: Powders with tighter particle size control and a more consistent distribution may be priced higher.
- Powder purity: Higher purity levels, achieved through stricter manufacturing processes, can lead to a higher cost.
- Quantity: Bulk purchases often receive discounts compared to smaller quantities.
- Supplier and market dynamics: Pricing can vary depending on the supplier and current market conditions.
As a general estimate, titanium alloy powders can range from around $50 to $200 per kilogram, with some specialized powders reaching even higher prices. However, the cost of the powder needs to be weighed against the potential benefits of using titanium alloys in additive manufacturing, such as weight reduction, design freedom, and improved performance.
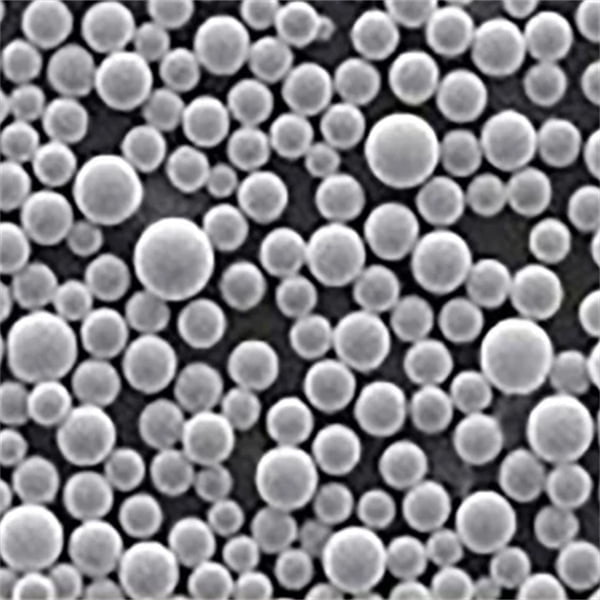
Câu hỏi thường gặp
Q: What are the advantages of using titanium alloy powders over wrought titanium products?
A: Additive manufacturing with titanium alloy powders offers several advantages over traditional machining of wrought titanium products. These include:
- Design freedom: Complex geometries and internal features are achievable with additive manufacturing, which can be challenging or even impossible with conventional machining.
- Reduced material waste: Additive manufacturing minimizes scrap material compared to subtractive machining techniques used for wrought titanium.
- Lightweight components: The ability to create intricate lattice structures with titanium alloy powders allows for significant weight reduction, crucial in applications like aerospace.
Q: Are titanium alloy powders safe to handle?
A: Titanium alloy powders, like most fine metal powders, can pose health risks if inhaled. Proper handling procedures, including the use of personal protective equipment like respirators and working in well-ventilated areas, are essential to minimize exposure.
Q: What are the future prospects for titanium alloy powders?
A: The future of titanium alloy powders looks bright. As additive manufacturing technology continues to evolve, the use of titanium alloy powders is expected to grow significantly across various industries. Advancements in powder production techniques and a decline in overall costs are likely to further accelerate this growth.
Q: Can titanium alloy powders be recycled?
A: Yes, titanium alloy powders can be recycled to a certain extent. Unused powder from the additive manufacturing process can often be collected and reused after proper sieving and quality control checks. However, there may be limitations on the number of recycling cycles due to potential contamination and changes in powder properties.
About 3DP mETAL
Product Category
LIÊN HỆ
Bạn có thắc mắc không? Hãy gửi tin nhắn ngay cho chúng tôi! Sau khi nhận được tin nhắn của bạn, chúng tôi sẽ xử lý yêu cầu của bạn với cả một đội ngũ.