Overview of Vacuum Induction Melting
Vacuum Induction Melting (VIM) is a sophisticated process used to produce high-quality metal alloys under a controlled vacuum environment. This method has become a cornerstone in industries where precision, purity, and uniformity of metal products are paramount. From aerospace components to medical implants, VIM enables the production of specialized metal powders that meet stringent industry standards.
But what exactly is Vacuum Induction Melting, and why is it such a game-changer? Imagine a process where you can melt metals in a vacuum, eliminating contaminants like oxygen and nitrogen that can compromise the material’s integrity. It’s like cooking your favorite dish in a pristine kitchen, free from any unwanted elements that could spoil the flavor.
The VIM process stands out for its ability to produce metals with exceptional purity, making it ideal for critical applications where even the slightest impurity could lead to catastrophic failures. In this guide, we’ll explore the ins and outs of VIM, breaking down its mechanics, advantages, limitations, and much more. Whether you’re an industry expert or just curious about how your stainless steel watch was made, you’re in the right place.
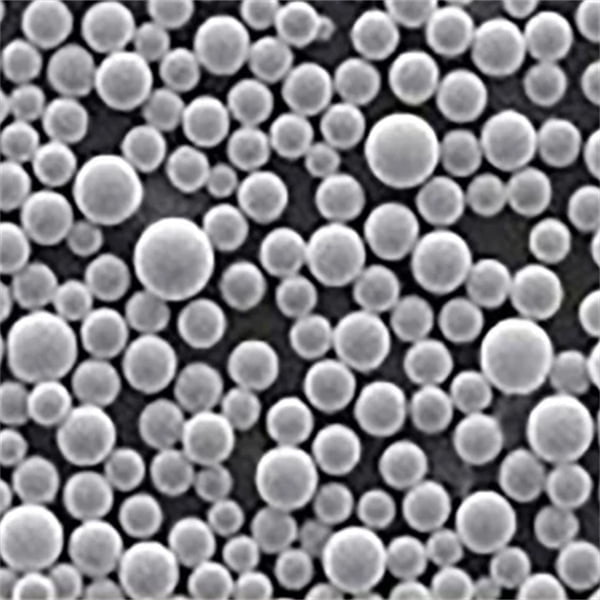
Understanding the Vacuum Induction Melting Process
What is Vacuum Induction Melting?
Vacuum Induction Melting is a process used to melt and refine metals in a vacuum environment. The vacuum ensures that the molten metal does not react with gases like oxygen, nitrogen, or hydrogen, which can lead to unwanted chemical reactions. Instead, the metal is heated using electromagnetic induction, which provides precise control over the melting process.
How Does VIM Work?
At the heart of VIM is the induction furnace, a device that uses alternating current to generate a magnetic field. This magnetic field induces eddy currents in the metal charge, heating it until it melts. The entire process takes place in a vacuum-sealed chamber, preventing contamination and ensuring the production of ultra-pure metal alloys.
- Step 1: Loading the Furnace
The process begins with loading the furnace with raw materials, which can include scrap metal, alloying elements, and other additives. These materials are carefully selected to meet the desired chemical composition of the final product. - Step 2: Melting Under Vacuum
Once the furnace is loaded, the chamber is evacuated to remove air and other gases. The induction coil is then energized, generating a magnetic field that heats the metal charge. As the temperature rises, the metal melts and forms a homogenous liquid. - Step 3: Refining and Degassing
The molten metal is kept under vacuum, which helps to remove impurities and dissolved gases. This step is crucial for producing metals with high purity and uniform properties. - Step 4: Pouring and Solidification
After refining, the molten metal is poured into molds or cast into ingots. The solidification process is carefully controlled to ensure that the final product has the desired microstructure and mechanical properties.
Why Vacuum Induction Melting?
The need for Vacuum Induction Melting arises from the limitations of conventional melting processes. In traditional furnaces, the presence of air can lead to oxidation and the formation of undesirable compounds in the metal. VIM eliminates these issues by operating in a vacuum, ensuring that the final product is free from contaminants.
Moreover, VIM allows for precise control over the chemical composition of the alloy. This is particularly important in industries like aerospace, where even minor deviations in material properties can have significant consequences. Whether you’re manufacturing turbine blades, medical implants, or high-strength fasteners, VIM provides the consistency and purity that these applications demand.
Composition of Metals Produced by Vacuum Induction Melting
The Role of Composition in Metal Alloys
The composition of a metal alloy determines its properties, such as strength, hardness, corrosion resistance, and ductility. VIM allows for precise control over the composition, enabling the production of alloys with tailored properties for specific applications.
Let’s take a look at some of the common metal powders produced using VIM, along with their specific compositions and characteristics.
Common Metal Powders Produced by VIM
Metal Powder Model | Sáng tác | thuộc tính | ỨNG DỤNG |
---|---|---|---|
Inconel 718 | Nickel (50-55%), Chromium (17-21%), Iron (Bal.), Niobium (4.75-5.5%), Molybdenum (2.8-3.3%) | High strength, excellent corrosion resistance, good weldability | Aerospace engines, gas turbines, nuclear reactors |
Hastelloy X | Nickel (47.0-52.5%), Chromium (20.5-23.0%), Iron (17.0-20.0%), Molybdenum (8.0-10.0%) | Excellent oxidation resistance, good high-temperature strength | Gas turbine engines, chemical processing, furnace components |
Titanium Grade 5 (Ti-6Al-4V) | Titanium (90%), Aluminum (6%), Vanadium (4%) | High strength-to-weight ratio, good fatigue resistance, biocompatibility | Medical implants, aerospace components, high-performance automotive parts |
Stellite 6 | Cobalt (Bal.), Chromium (28-32%), Tungsten (4.0-6.0%), Carbon (1.0-1.4%) | Excellent wear resistance, good corrosion resistance, high hardness | Valve seats, cutting tools, wear-resistant coatings |
Maraging Steel (C300) | Iron (Bal.), Nickel (18-19%), Cobalt (8.5-9.5%), Molybdenum (4.6-5.2%) | Ultra-high strength, good toughness, low carbon content | Aerospace landing gears, high-performance sporting equipment |
CP Titanium (Grade 2) | Titanium (99% min.), Iron (0.30% max.), Oxygen (0.25% max.) | Good strength, excellent corrosion resistance, biocompatibility | Medical implants, chemical processing, marine applications |
NiTi (Nitinol) | Nickel (55-56%), Titanium (44-45%) | Shape memory effect, superelasticity, biocompatibility | Medical devices, actuators, eyeglass frames |
Haynes 188 | Cobalt (Bal.), Nickel (20-24%), Chromium (20-24%), Tungsten (13-16%) | Excellent high-temperature strength, good oxidation resistance | Gas turbine engines, industrial furnaces, nuclear reactors |
Rene 41 | Nickel (Bal.), Chromium (18-20%), Cobalt (10-12%), Molybdenum (9-10%) | High-temperature strength, good oxidation resistance | Jet engines, gas turbines, space vehicles |
Aluminum 7075 | Aluminum (90.0-91.5%), Zinc (5.6-6.1%), Magnesium (2.1-2.5%), Copper (1.2-2.0%) | High strength, good fatigue resistance, low density | Aircraft structures, sports equipment, automotive parts |
These metal powders, produced via VIM, are designed to meet the specific demands of their respective applications. For instance, Inconel 718 is known for its excellent mechanical properties at high temperatures, making it ideal for use in jet engines and gas turbines. On the other hand, Titanium Grade 5 is highly valued in the medical field for its biocompatibility and high strength-to-weight ratio.
Characteristics of Vacuum Induction Melting
Key Characteristics of VIM Process
The VIM process is characterized by several key features that make it distinct from other metal production methods. These characteristics are crucial in ensuring the production of high-purity, high-performance metal alloys.
- Vacuum Environment: The use of a vacuum environment is the most defining characteristic of VIM. This eliminates the presence of oxygen, nitrogen, and hydrogen, which can lead to undesirable reactions and impurities in the metal.
- Induction Heating: VIM uses electromagnetic induction to heat and melt the metal. This allows for precise control over the temperature and ensures uniform melting of the metal charge.
- Refining Capability: The vacuum environment not only prevents contamination but also aids in the removal of impurities and dissolved gases from the molten metal. This refining capability is essential for producing metals with high purity and consistent properties.
- Alloying Flexibility: VIM allows for precise control over the composition of the alloy. This flexibility is crucial in industries where specific material properties are required, such as aerospace, medical, and automotive sectors.
- Khả năng mở rộng: The VIM process can be scaled up or down depending on the production requirements. This makes it suitable for both small-scale, specialized production runs and large-scale industrial manufacturing.
Advantages of Vacuum Induction Melting
- High Purity: The vacuum environment ensures that the metal is free from contaminants, resulting in a high-purity product.
- Precise Control: The use of induction heating and a controlled vacuum environment allows for precise control over the melting and alloying process.
- Uniform Properties: VIM produces metals with consistent and uniform properties, which is essential for critical applications.
- Reduced Gas Content: The vacuum environment helps in reducing the gas content in the metal, which can improve its mechanical properties and reduce the risk of defects.
- Versatility: VIM can be used to produce a wide range of metal alloys, making it a versatile process suitable for various industries.
Limitations of Vacuum Induction Melting
- High Cost: The equipment and operational costs associated with VIM are relatively high compared to conventional melting processes. This can make it less cost-effective for certain applications.
- Complex Operation: The VIM process requires specialized equipment and expertise, which can add to the complexity of the operation.
- Limited Production Volume: While VIM is scalable, the production volume is often limited compared to other mass-production methods. This can be a drawback for large-scale manufacturing.
- Energy Consumption: The induction heating process used in VIM can be energy-intensive, contributing to higher operational costs.
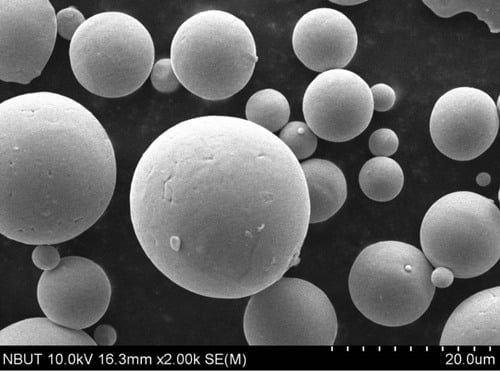
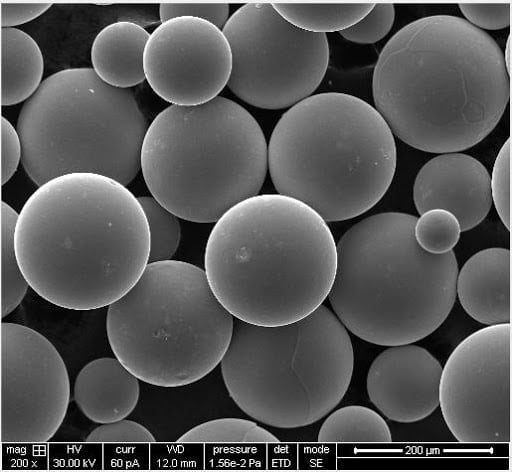
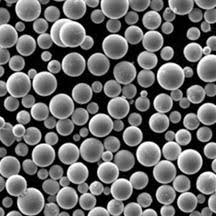
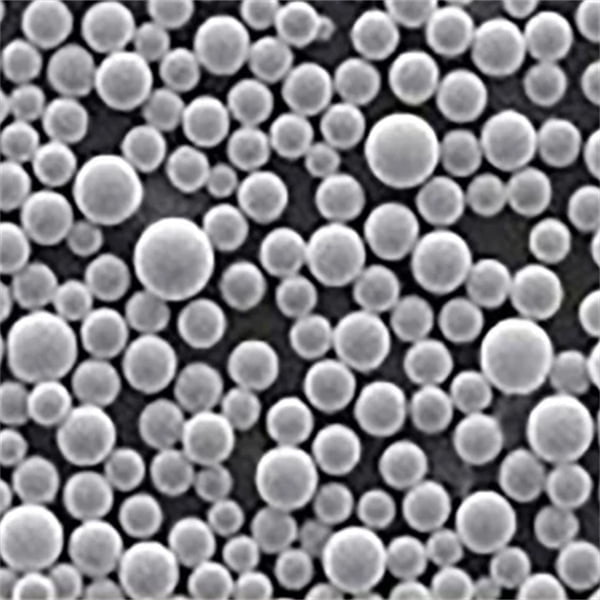
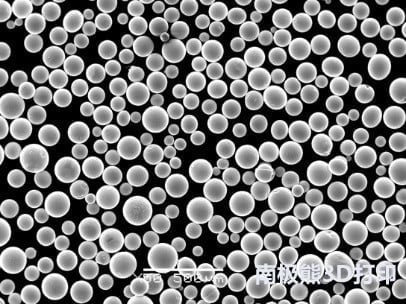
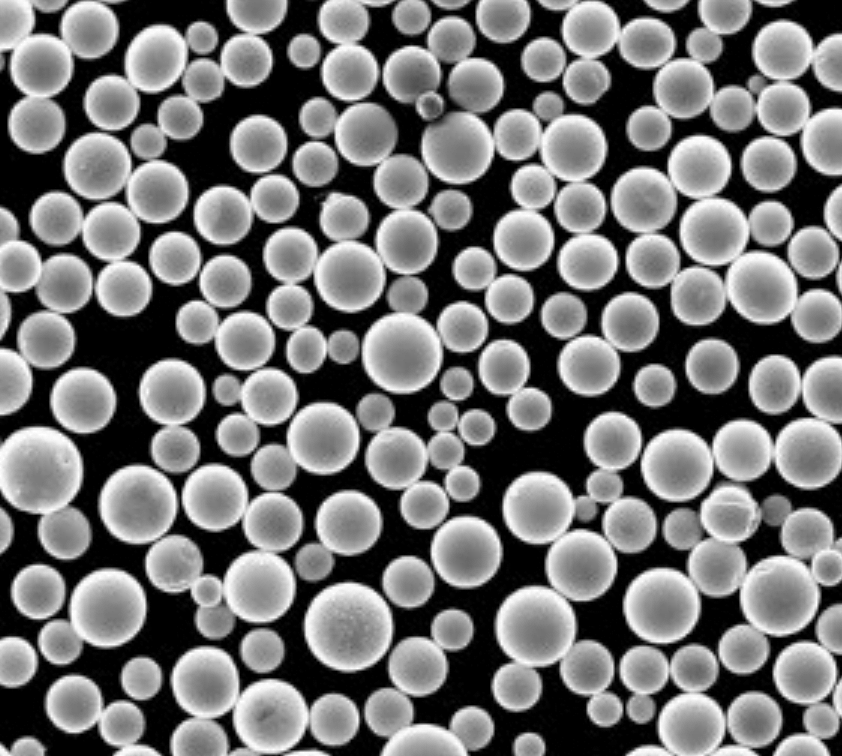
Applications of Vacuum Induction Melting
Where is VIM Used?
The applications of Vacuum Induction Melting are vast and varied, spanning across multiple industries. The ability to produce high-purity, high-performance metal alloys makes VIM a preferred choice for critical applications where material properties cannot be compromised.
Common Applications of VIM Products
Ngành | Ứng dụng | Miêu tả |
---|---|---|
Hiệp công | Jet Engine Components | VIM is used to produce superalloys like Inconel and Rene 41, which are essential for high-temperature, high-stress components in jet engines. |
Y học | Surgical Implants | Metals like Titanium Grade 5 and NiTi produced via VIM are used in medical implants due to their biocompatibility and mechanical properties. |
Ô tô | High-Performance Parts | VIM-produced metals like Maraging Steel and Aluminum 7075 are used in automotive parts that require high strength and lightweight properties. |
Năng lượng | Gas Turbine Blades | VIM is used to produce superalloys like Hastelloy and Haynes, which are essential for the high-temperature components in gas turbines. |
Hạt nhân | Reactor Components | VIM allows for the production of corrosion-resistant and radiation-resistant metals required in nuclear reactors. |
Công nghiệp | Wear-Resistant Coatings | Stellite and other cobalt-based alloys produced by VIM are used in industrial applications requiring wear resistance. |
Quốc phòng | Armor and Weapon Components | VIM is used to produce high-strength alloys for armor plating and other defense applications. |
Thủy quân lục chiến | Corrosion-Resistant Components | VIM-produced titanium and nickel alloys are used in marine applications due to their excellent corrosion resistance. |
Điện tử | High-Purity Contacts and Connectors | VIM is used to produce high-purity copper and gold alloys for electronic components requiring high conductivity and reliability. |
Xử lý hóa chất | Corrosion-Resistant Equipment | Hastelloy and other nickel-based alloys produced by VIM are used in chemical processing equipment due to their excellent corrosion resistance. |
As seen, VIM products find applications in industries that demand superior material properties, such as high temperature resistance, corrosion resistance, and mechanical strength. Whether it’s the aerospace industry, where materials must withstand extreme conditions, or the medical field, where biocompatibility is paramount, VIM delivers the quality and consistency needed.
Specifications, Sizes, Grades, and Standards of VIM Products
Understanding the Technical Specifications
When it comes to VIM products, there are several key specifications and standards that must be met to ensure the material performs as expected. These specifications can vary based on the alloy, application, and industry requirements.
Key Specifications and Standards for VIM Products
Đặc điểm kỹ thuật | Miêu tả | Typical Alloys | Tiêu chuẩn |
---|---|---|---|
Chemical Composition | Defines the precise elemental makeup of the alloy. | All alloys | ASTM, ISO, AMS |
Tính chất cơ học | Includes tensile strength, yield strength, hardness, and elongation. | Maraging Steel, Titanium, Inconel | ASTM, MIL-SPEC, DIN |
Grain Size | Refers to the size of the grains in the metal, affecting its mechanical properties. | Superalloys, Stainless Steels | ASTM E112 |
Sạch sẽ | The level of impurities in the alloy, crucial for high-performance applications. | All alloys | ASTM B117, AMS 2248 |
Cấu trúc vi mô | The arrangement of phases within the metal, impacting its mechanical and physical properties. | Superalloys, Titanium, Hastelloy | ASTM E407 |
Surface Finish | The quality of the surface after processing, important for certain applications. | Maraging Steel, Stainless Steels | ISO 4287, ASME B46.1 |
Dimensional Tolerances | The allowable variations in the dimensions of the final product. | All alloys | ISO 2768, ASME Y14.5 |
Xử lý Nhiệt | Specifies the heat treatment process to achieve desired mechanical properties. | Maraging Steel, Inconel, Hastelloy | AMS 2750, ISO 18203 |
Khả năng chống ăn mòn | The ability of the alloy to resist corrosion in specific environments. | Hastelloy, Titanium, Stainless Steels | ASTM G48, ISO 15156 |
Radiographic Quality | Ensures the alloy is free from internal defects like porosity and inclusions. | Aerospace Alloys, Nuclear Alloys | ASTM E1742, ISO 5579 |
Sizes and Grades Available
Hợp kim | Available Sizes | Available Grades |
---|---|---|
Inconel 718 | Bars: 10mm to 500mm diameter | AMS 5662, ASTM B637, DIN 2.4668 |
Hastelloy X | Sheets: 1mm to 50mm thickness | ASTM B435, AMS 5754, DIN 2.4665 |
Titanium Grade 5 | Plates: 1mm to 100mm thickness | AMS 4911, ASTM B265, DIN 3.7165 |
Stellite 6 | Castings: Custom sizes available | AMS 5387, ASTM F75 |
Maraging Steel C300 | Bars: 20mm to 300mm diameter | AMS 6514, ASTM A538 |
CP Titanium Grade 2 | Sheets: 0.5mm to 25mm thickness | ASTM B265, AMS 4902 |
NiTi (Nitinol) | Wires: 0.1mm to 5mm diameter | ASTM F2063, AMS 5382 |
Haynes 188 | Tubes: 10mm to 200mm OD | AMS 5608, ASTM B435 |
Rene 41 | Rods: 5mm to 100mm diameter | AMS 5544, ASTM B435 |
Aluminum 7075 | Extrusions: Custom profiles available | AMS 4045, ASTM B209 |
These specifications, sizes, and grades ensure that VIM products meet the stringent requirements of various industries. For instance, the aerospace industry requires alloys with specific mechanical properties and corrosion resistance, while the medical field demands biocompatibility and purity.
Suppliers and Pricing Details
Where to Source VIM Products?
When sourcing VIM products, it’s crucial to work with reputable suppliers who can provide certified materials that meet the required specifications. Below is a list of some of the leading suppliers of VIM products, along with an overview of their pricing.
Key Suppliers of VIM Products
Nhà cung cấp | Địa điểm | Product Range | Mức giá (USD) |
---|---|---|---|
ATI Specialty Materials | Hoa Kỳ | Superalloys, Titanium Alloys, Maraging Steel | $50 – $150 per kg |
Carpenter Technology | Hoa Kỳ | High-Performance Alloys, Stainless Steels | $30 – $120 per kg |
VSMPO-AVISMA | Russia | Titanium Alloys, Nickel Alloys | $40 – $130 per kg |
Precision Castparts Corp. | Hoa Kỳ | Aerospace Alloys, Industrial Alloys | $70 – $200 per kg |
Outokumpu | Finland | Stainless Steels, High-Performance Alloys | $20 – $100 per kg |
Allegheny Technologies | Hoa Kỳ | Superalloys, Titanium, Specialty Alloys | $50 – $160 per kg |
Haynes International | Hoa Kỳ | High-Temperature Alloys, Corrosion-Resistant Alloys | $60 – $170 per kg |
AMG Superalloys | Vương quốc Anh | Specialty Alloys, Superalloys | $50 – $140 per kg |
Special Metals Corporation | Hoa Kỳ | Nickel Alloys, Superalloys | $70 – $180 per kg |
Sandvik Materials Technology | Thụy Điển | Stainless Steels, High-Performance Alloys | $25 – $110 per kg |
The pricing of VIM products can vary significantly depending on the alloy, grade, and quantity ordered. For instance, superalloys used in aerospace applications tend to be more expensive due to the stringent requirements and high performance needed.
Comparing Pros and Cons of Vacuum Induction Melting Products
The Good and the Not-So-Good
While VIM offers numerous advantages, it’s essential to understand its limitations as well. Here’s a comparison of the pros and cons of VIM products.
Advantages of VIM Products
Advantage | Miêu tả |
---|---|
High Purity | VIM products are known for their exceptional purity, making them ideal for critical applications. |
Consistent Quality | The controlled environment ensures uniform properties across the entire batch. |
Precise Composition Control | VIM allows for exact alloying, enabling the production of metals with specific desired properties. |
Reduced Defects | The vacuum environment minimizes the risk of defects like porosity and inclusions. |
High Mechanical Properties | VIM products often exhibit superior mechanical properties, including strength and corrosion resistance. |
Limitations of VIM Products
Limitation | Miêu tả |
---|---|
Higher Cost | The VIM process is more expensive than traditional melting methods, which can lead to higher material costs. |
Energy-Intensive | The induction heating process used in VIM consumes a significant amount of energy. |
Complex Equipment | VIM requires specialized equipment and expertise, which can add to the complexity and cost of production. |
Limited Production Volume | VIM is often limited to smaller production runs, making it less suitable for mass production. |
Longer Lead Times | The complexity of the process can result in longer lead times for VIM products. |
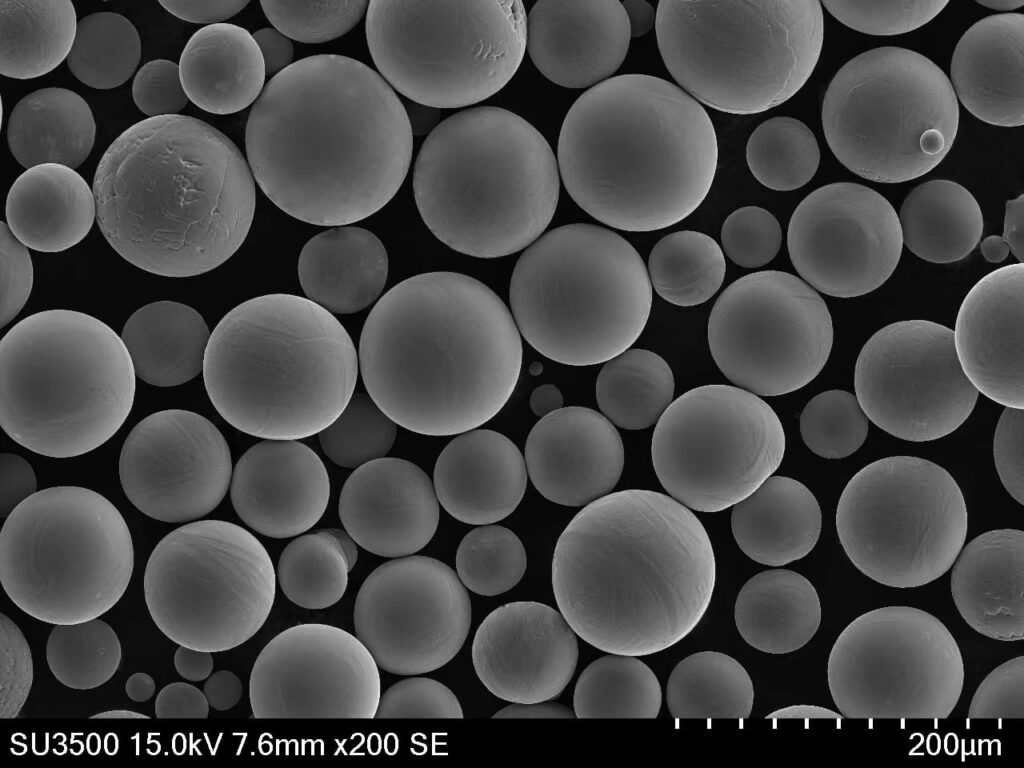
Câu hỏi thường gặp
Question | Answer |
---|---|
What is Vacuum Induction Melting? | Vacuum Induction Melting (VIM) is a process used to melt and refine metals in a vacuum environment. It ensures high purity by eliminating contaminants like oxygen and nitrogen. |
Why is VIM used in aerospace applications? | VIM is used in aerospace due to its ability to produce superalloys with high-temperature resistance, strength, and purity, which are critical for components like jet engines. |
How does VIM differ from conventional melting? | Unlike conventional melting, VIM takes place in a vacuum, preventing contamination and allowing for precise control over the alloy composition. |
What are the main alloys produced by VIM? | Common alloys produced by VIM include Inconel 718, Hastelloy X, Titanium Grade 5, and Maraging Steel C300. |
Is VIM suitable for mass production? | VIM is generally not ideal for mass production due to its higher costs and limited production volumes. It is better suited for specialized, high-performance applications. |
What industries benefit most from VIM? | Industries such as aerospace, medical, automotive, energy, and defense benefit most from the high purity and precise alloying offered by VIM. |
What are the environmental impacts of VIM? | VIM is energy-intensive, which can have a higher environmental impact compared to traditional methods. However, the high-quality output often justifies its use in critical applications. |
Can VIM be used for all types of metals? | VIM is particularly effective for producing high-performance alloys, but it may not be cost-effective for more common metals like basic carbon steels. |
How do I choose the right VIM product? | Choosing the right VIM product depends on your specific application requirements, including mechanical properties, corrosion resistance, and temperature resistance. Consulting with a supplier can help you make the right choice. |
What are the future trends in VIM technology? | Future trends in VIM include advancements in energy efficiency, automation, and the development of new alloys tailored for emerging industries like renewable energy and space exploration. |
Kết luận
Vacuum Induction Melting is a powerful tool in the production of high-performance metal alloys. Its ability to produce metals with exceptional purity and precise composition control makes it indispensable in industries where material quality cannot be compromised. However, the higher costs and complexity associated with VIM mean that it’s typically reserved for applications where these benefits outweigh the drawbacks.
As industries continue to demand materials with superior properties, the role of VIM in metal production is likely to grow. Whether you’re in aerospace, medical, automotive, or any other high-tech field, understanding the ins and outs of VIM can help you make informed decisions about your material needs.
This guide has provided a detailed overview of Vacuum Induction Melting, from its process and characteristics to its applications and limitations. If you have further questions or need specific advice, don’t hesitate to reach out to a VIM supplier or industry expert.
About 3DP mETAL
Product Category
LIÊN HỆ
Bạn có thắc mắc không? Hãy gửi tin nhắn ngay cho chúng tôi! Sau khi nhận được tin nhắn của bạn, chúng tôi sẽ xử lý yêu cầu của bạn với cả một đội ngũ.