Zinc powder, a fine, greyish-blue powder with a surprisingly high energy content, plays a vital role in the fascinating world of metallurgy. Imagine tiny soldiers made of zinc, infiltrating the ranks of other metals to enhance their properties, protect them from harm, and create entirely new functionalities. That’s the essence of what zinc powder brings to the metallurgical table.
But before we delve deeper, let’s establish a common ground. Have you ever encountered that pesky rust on your favorite bike? Or perhaps witnessed the tarnishing of cherished silver jewelry? These are instances of corrosion, the nemesis of metals. Zinc powder, with its inherent sacrificial nature, acts as a shield, taking the brunt of the attack and safeguarding the underlying metal from corrosion’s grasp.
Now, buckle up as we embark on a comprehensive exploration of zinc powder in metallurgy. We’ll dissect its various forms, delve into its applications, unveil its strengths and weaknesses, and answer burning questions you might have.
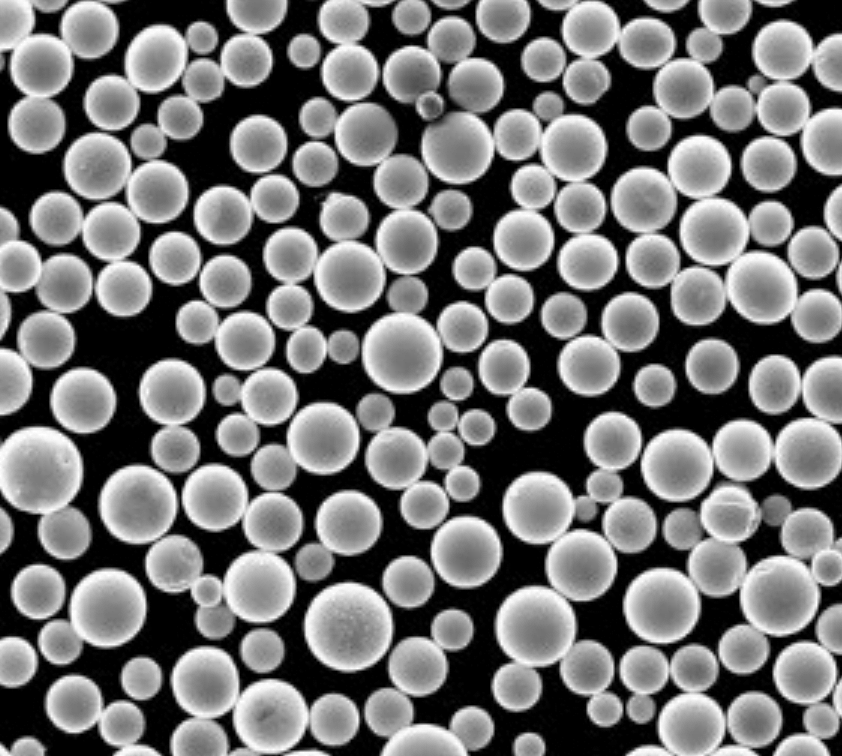
the Zinc Powder Arsenal: A Multifaceted Approach
Zinc powder isn’t a monolithic entity. It comes in a diverse range of forms, each with its own unique characteristics tailored for specific applications. Here’s a glimpse into ten prominent zinc powder models:
- Zinc Dust (Zn Dust): This finely divided, bluish-gray powder, often containing varying amounts of zinc oxide, boasts a high surface area. It excels in de-oxidation (removing oxygen from molten metals) and cementation (introducing a new element into the surface of a base metal).
- Zinc Granules: Imagine tiny, irregular-shaped pebbles of zinc. These granules, typically ranging from 0.15 to 1.6 millimeters, find favor in sherardizing, a diffusion process that coats steel with a zinc layer for superior corrosion resistance.
- Electrolytic Zinc Powder: As the name suggests, this type is produced through an electrolytic process, resulting in a high degree of purity (often exceeding 99.95% zinc). Its exceptional purity makes it ideal for applications demanding minimal contamination, such as powder metallurgy (creating objects from metal powders) and pyrotechnics (creation of fireworks).
- Atomized Zinc Powder: This powder is formed by rapidly solidifying molten zinc droplets using an inert gas stream. The resulting particles boast a spherical shape and a relatively narrow size distribution, making them perfect for spray deposition (coating a surface with molten metal droplets) and thermal spraying (creating a coating by melting and propelling metal powder particles).
- Flake Zinc Powder: Think of thin, plate-like zinc particles. These flakes offer a larger surface area compared to spherical powders, making them well-suited for chemical reactions where maximizing surface contact is crucial.
- Zinc Paste: This pre-mixed blend incorporates zinc powder with a binder, creating a paste-like consistency. Zinc paste finds application in galvanic protection (sacrificial protection of a metal from corrosion) and cold galvanizing (applying a zinc coating without using high temperatures).
- Zinc-Aluminum Powder Alloys: Imagine combining the strengths of zinc with aluminum. These alloys offer a synergistic effect, enhancing properties like corrosion resistance and strength. They shine in applications like thermal spraying and metal matrix composites (composites where a metal matrix reinforces a ceramic or polymer phase).
- Micronized Zinc Powder: Picture an ultra-fine zinc powder with particle sizes ranging from 4 to 10 microns. This microscopic marvel finds use in alkaline batteries and pyrotechnics, where its high reactivity is a valuable asset.
- Zinc-Rich Paint: This isn’t exactly a pure zinc powder model, but it deserves a mention. Here, zinc powder is incorporated into a paint formulation, creating a coating that provides exceptional galvanic protection to steel structures.
- Pigmentary Zinc Powder: Zinc powder isn’t just about muscle; it has a touch of artistry too. This type boasts specific particle sizes and surface treatments, making it a valuable pigment in corrosion-resistant paints and coatings.
Key Considerations When Choosing a Zinc Powder Model:
- Particle size and distribution: Finer powders offer a larger surface area for reactions, while coarser ones might be better suited for structural applications.
- Độ tinh khiết: Higher purity translates to less contamination, crucial for specific applications.
- Surface morphology: The shape and texture of the particles can influence factors like packing density and reactivity.
- Chemical composition: Alloys with other metals can introduce new properties to the mix.
Zinc Powder in Action: A Metallurgical Powerhouse
Here’s a closer look at some key applications of zinc powder in metallurgy:
- De-oxidation: Molten metals often pick up unwanted oxygen during processing. Zinc powder, with its high affinity for oxygen, acts as a deoxidizer. It reacts with the oxygen, forming stable zinc oxides that float to the surface and are skimmed off, leaving the purified metal behind. This ensures the final product possesses the desired mechanical properties and avoids brittleness caused by oxygen.
Imagine a pot of molten metal simmering away. Oxygen, like an unwelcome guest, tries to crash the party. Zinc powder, the ever-reliable bouncer, steps in, grabs the oxygen, and throws it out, keeping the metal pure.
- Cementization: This process involves introducing a new element onto the surface of a base metal. Zinc powder excels in this role. When packed around steel components and heated in a controlled atmosphere, the zinc diffuses into the steel surface, creating a zinc-iron alloy layer. This layer enhances the steel’s corrosion resistance and hardenability.
Think of a steel sword. While strong, it’s susceptible to rust. By surrounding it with zinc powder and heating it up, we create a zinc-iron alloy layer on the surface, acting like a knight’s armor, shielding the sword from corrosion’s wrath.
- Sherardizing: This diffusion process coats steel with a protective layer of zinc. Here, zinc powder plays a starring role. Steel parts are tumbled in a container with zinc granules and a reducing agent at elevated temperatures. The zinc vaporizes, reacts with the steel surface, and forms a tightly bonded zinc layer. This layer offers superior corrosion protection compared to traditional galvanizing, making it ideal for small parts and threaded components.
Imagine a bunch of screws and nuts, vital components but prone to rust. Sherardizing, with the help of zinc powder, coats them with a protective zinc layer, ensuring they stay strong and functional for years to come.
- Luyện kim bột: This fascinating technology builds objects by compacting and sintering metal powders. Zinc powder finds application here, particularly in the creation of porous metal components. By incorporating a specific amount of zinc powder into the mix, we can design components with a controlled pore size and distribution. These pores can be beneficial for applications like filtration, catalysis, và heat exchangers.
Imagine a filter made not from solid metal but from a network of tiny interconnected pores. Zinc powder, when used in powder metallurgy, helps create such structures, allowing fluids to pass through while capturing unwanted particles.
- Thermal Spraying and Spray Deposition: These processes involve melting metal powder and propelling the molten droplets onto a substrate to create a coating. Zinc powder is a popular choice due to its excellent corrosion resistance properties. Thermal spraying is used to protect steel structures like bridges and pipelines, while spray deposition finds application in automotive components and other areas requiring wear and corrosion resistance.
Imagine a bridge, constantly battling the elements. Thermal spraying with zinc powder creates a protective shield, safeguarding the bridge’s steel underbelly from corrosion’s relentless attack.
These are just a few examples of how zinc powder flexes its muscles in the metallurgical arena. Its versatility and unique properties make it a valuable asset for creating stronger, more durable, and corrosion-resistant metals.
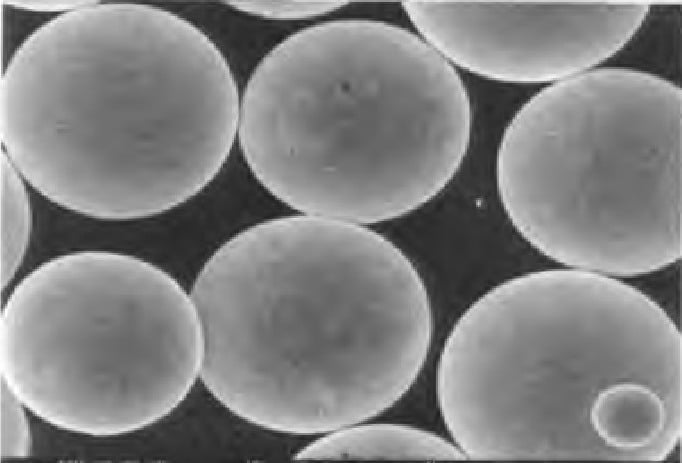
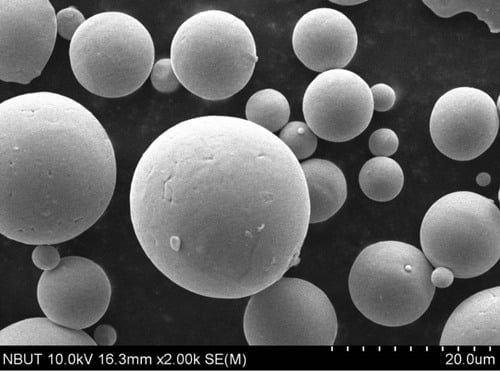
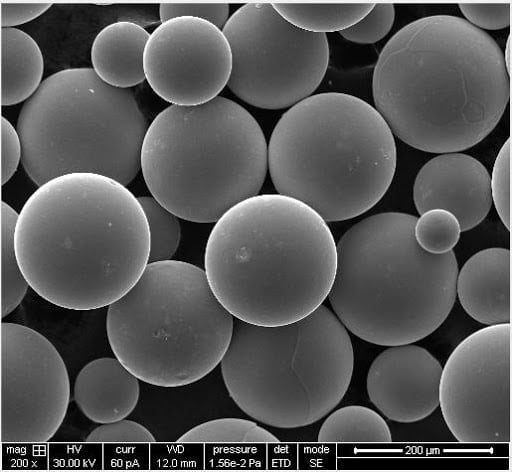
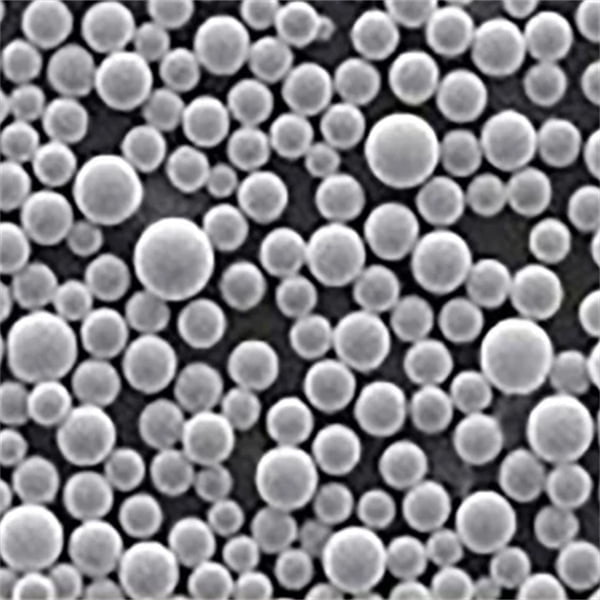
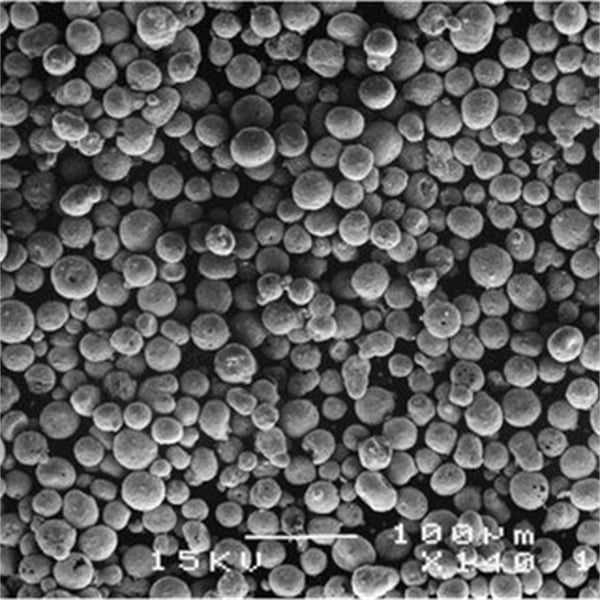
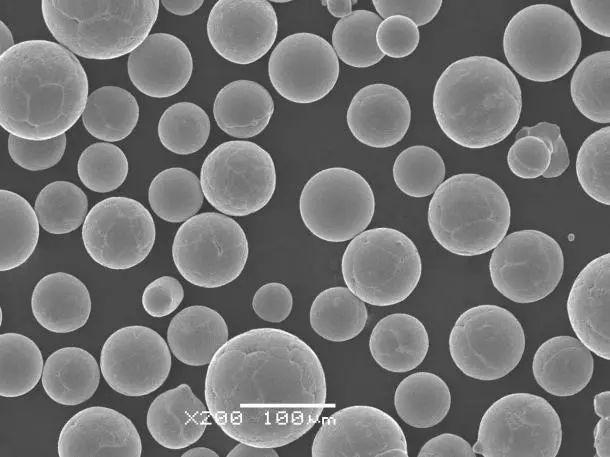
Advantages and Limitations of Zinc Powder in Metallurgy
Advantages:
- Enhanced Corrosion Resistance: Zinc powder’s sacrificial nature makes it a champion in the fight against corrosion. By creating a barrier between the base metal and the environment, it takes the brunt of the attack, protecting the underlying metal.
- Improved Formability: In some cases, incorporating zinc powder into metal mixtures can enhance the formability of the final product. This allows for the creation of complex shapes without compromising on strength.
- Strength and Hardenability: Certain applications of zinc powder, like cementation, can introduce elements that enhance the strength and hardenability of the base metal.
- Versatility: With various forms and compositions available, zinc powder caters to a diverse range of metallurgical needs.
- Cost-effective: Compared to some other corrosion protection methods, zinc powder can be a cost-effective solution.
Limitations:
- Reactivity: Zinc powder’s high reactivity can be a double-edged sword. While it aids in de-oxidation and other processes, it also necessitates careful handling and storage to avoid unintended reactions.
- Flammability: In certain forms, zinc powder can be flammable and requires proper safety precautions during use.
- Potential for Hydrogen Embrittlement: Under specific conditions, the use of zinc powder can introduce hydrogen into the base metal, leading to hydrogen embrittlement, a phenomenon that can cause the metal to become brittle and fracture.
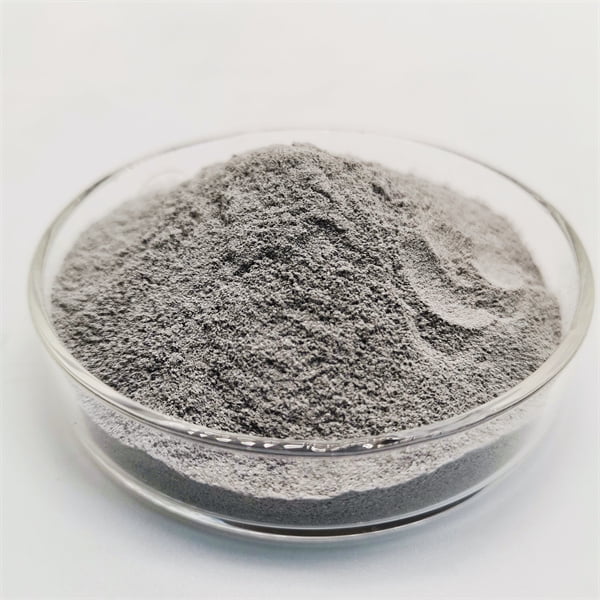
Câu hỏi thường gặp
Q: What are the different factors to consider when choosing a zinc powder for a specific metallurgical application?
A: Several factors influence zinc powder selection:
- Particle size and distribution: Finer powders offer a larger surface area, crucial for reactions like de-oxidation. Coarser particles might be better suited for applications like sherardizing, where packing density is important.
- Độ tinh khiết: Higher purity zinc powder minimizes contamination, essential for processes like powder metallurgy where even small impurities can affect the final product’s properties.
- Surface morphology: The shape and texture of the particles can influence factors like packing density, reactivity, and suitability for specific coating methods. Spherical particles might flow better for spraying applications, while flakes might offer a larger surface area for chemical reactions.
- Chemical composition: For applications like thermal spraying, zinc-aluminum alloy powders can introduce properties like enhanced strength and wear resistance.
Q: How is zinc powder typically stored and handled?
A: Due to its reactive nature, zinc powder requires proper storage and handling to ensure safety and prevent degradation. Here are some key points:
- Storage:
- Cool, dry location away from heat sources and direct sunlight.
- Moisture-proof containers to prevent oxidation and caking.
- Inert atmosphere storage for highly reactive powders.
- Handling:
- Proper grounding and ventilation to minimize the risk of dust explosions.
- Use of personal protective equipment like gloves, respirators, and eye protection to avoid inhalation or skin contact.
- Following safe handling practices as outlined by the material safety data sheet (MSDS) for the specific zinc powder type.
Q: Are there any environmental considerations associated with the use of zinc powder in metallurgy?
A: While zinc is a generally safe element, there are some environmental considerations:
- Dust control: During handling and processing, zinc powder dust can be generated. Implementing proper dust control measures like ventilation systems is crucial to minimize airborne emissions and protect worker health.
- Waste disposal: Spent zinc powder or residues from processes involving zinc powder might require proper disposal according to local environmental regulations.
Q: What are some emerging trends in the use of zinc powder in metallurgy?
A: The future of zinc powder in metallurgy is brimming with potential:
- Nanoparticles: Zinc nanoparticles offer a vast surface area and unique properties, opening doors for applications like creating advanced coatings with enhanced functionalities.
- Composite materials: Zinc powder combined with other materials like polymers or ceramics can lead to the development of novel composite materials with superior properties tailored for specific needs.
- Additive manufacturing: The growing field of additive manufacturing, also known as 3D printing, might see increased use of zinc powder in creating complex metal structures with customized properties.
Kết luận
Zinc powder, with its versatility and unique properties, has carved a significant niche in the realm of metallurgy. From shielding metals from corrosion’s grasp to enabling the creation of novel materials, zinc powder continues to play a vital role in crafting a stronger, more durable metallic future. As research and development delve deeper, we can expect even more innovative applications of this mighty metal powder to emerge in the years to come.
About 3DP mETAL
Product Category
LIÊN HỆ
Bạn có thắc mắc không? Hãy gửi tin nhắn ngay cho chúng tôi! Sau khi nhận được tin nhắn của bạn, chúng tôi sẽ xử lý yêu cầu của bạn với cả một đội ngũ.