Repairing a workpiece, especially in industrial contexts, requires precision, knowledge, and the right materials. Whether you are dealing with wear and tear or accidental damage, understanding how to repair a workpiece effectively can save time, reduce costs, and improve the longevity of your machinery. This comprehensive guide will delve into the nitty-gritty of workpiece repair, focusing on metal powders used in the process, their specific models, and various techniques involved. We’ll also provide detailed tables to help you compare different options, their applications, and the pros and cons. So, let’s get started!
Overview of Workpiece Repair
Repairing a workpiece involves restoring its original function and performance through various methods such as welding, brazing, soldering, or using metal powders. The primary goal is to fix the damage without compromising the integrity of the original material. Workpiece repair is crucial in industries like automotive, aerospace, manufacturing, and heavy machinery, where even minor defects can lead to significant issues.
Key Techniques in Workpiece Repair
- Welding: Joining two pieces of metal using heat and pressure.
- Brazing: A metal-joining process that uses a filler metal with a lower melting point.
- Soldering: Similar to brazing but typically used for smaller, more delicate tasks.
- Metal Powders: Used for precision repair, filling voids, and restoring worn surfaces.
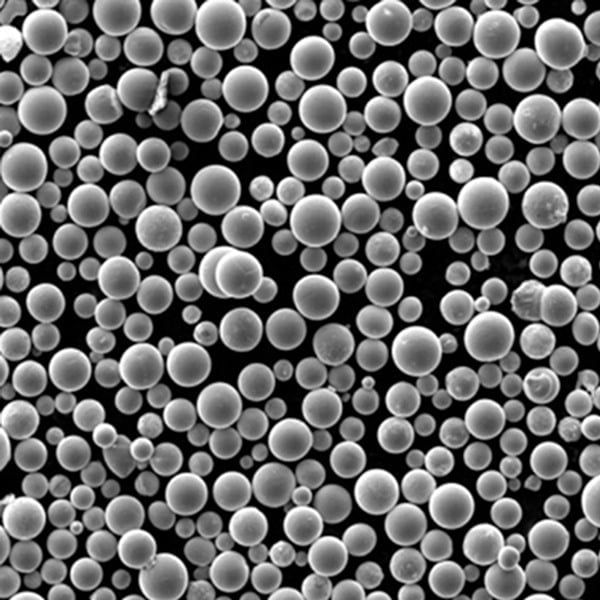
Types of Metal Powders for Workpiece Repair
Metal powders are essential in workpiece repair due to their versatility and effectiveness. Here’s a list of specific metal powder models, their compositions, properties, and characteristics:
Metal Powder Model | Composition | Properties | Characteristics |
---|---|---|---|
Inconel 625 | Nickel-Chromium-Molybdenum Alloy | High strength, oxidation resistance | Excellent for high-temperature applications |
Stellite 6 | Cobalt-Chromium Alloy | Hardness, wear resistance | Suitable for extreme wear conditions |
Tungsten Carbide | Tungsten and Carbon | Exceptional hardness | Ideal for abrasion-resistant applications |
316L Stainless Steel | Iron, Chromium, Nickel, Molybdenum | Corrosion resistance, good mechanical properties | Commonly used in marine environments |
Aluminum 6061 | Aluminum, Magnesium, Silicon | Lightweight, good corrosion resistance | Perfect for aerospace applications |
Copper-Nickel 90/10 | Copper, Nickel | Corrosion resistance, good weldability | Used in marine and offshore engineering |
Titanium Ti-6Al-4V | Titanium, Aluminum, Vanadium | High strength-to-weight ratio | Preferred in aerospace and medical applications |
Nickel 200 | Pure Nickel | Good electrical conductivity, corrosion resistance | Utilized in electrical and chemical industries |
Hastelloy C276 | Nickel-Molybdenum-Chromium Alloy | Excellent corrosion resistance | Suitable for chemical processing environments |
Molybdenum | Pure Molybdenum | High melting point, good thermal conductivity | Used in high-temperature applications |
Applications of Metal Powders in Workpiece Repair
Metal Powder Model | Applications |
---|---|
Inconel 625 | Turbine blades, exhaust systems, chemical processing equipment |
Stellite 6 | Valve seats, bearings, cutting tools |
Tungsten Carbide | Mining tools, wear plates, drilling equipment |
316L Stainless Steel | Boat fittings, medical devices, food processing equipment |
Aluminum 6061 | Aircraft components, automotive parts, construction materials |
Copper-Nickel 90/10 | Heat exchangers, condensers, desalination plants |
Titanium Ti-6Al-4V | Aerospace fasteners, orthopedic implants, sporting goods |
Nickel 200 | Battery components, electroplating, chemical plant equipment |
Hastelloy C276 | Flue gas desulfurization systems, pulp and paper processing |
Molybdenum | Furnace components, electrodes, nuclear power applications |
Specifications, Sizes, Grades, and Standards
Metal Powder Model | Specifications | Sizes | Grades | Standards |
---|---|---|---|---|
Inconel 625 | AMS 5666, ASTM B443 | -325 mesh | NiCr22Mo9Nb | UNS N06625 |
Stellite 6 | ASTM F75, AMS 5894 | -140 mesh | CoCrW | UNS R30006 |
Tungsten Carbide | ISO 9001 | -200 mesh | WC | ASTM B777 |
316L Stainless Steel | ASTM A240 | -325 mesh | FeCr18Ni12Mo3 | UNS S31603 |
Aluminum 6061 | ASTM B209 | -100 mesh | AlMg1SiCu | UNS A96061 |
Copper-Nickel 90/10 | ASTM B466 | -325 mesh | CuNi10Fe1Mn | UNS C70600 |
Titanium Ti-6Al-4V | AMS 4911 | -200 mesh | Ti6Al4V | UNS R56400 |
Nickel 200 | ASTM B160 | -325 mesh | Ni99.6 | UNS N02200 |
Hastelloy C276 | ASTM B575 | -325 mesh | NiMo16Cr15W | UNS N10276 |
Molybdenum | ASTM B387 | -325 mesh | Mo | UNS R03620 |
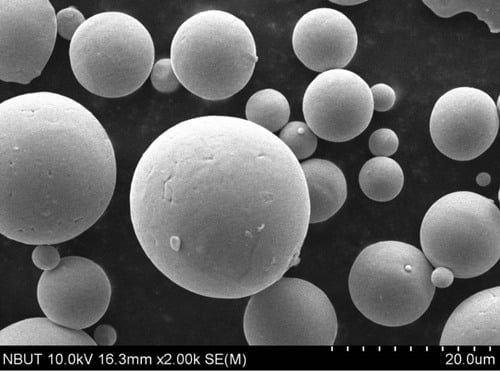
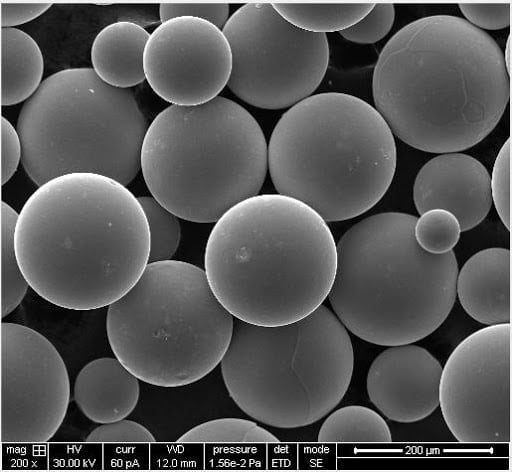
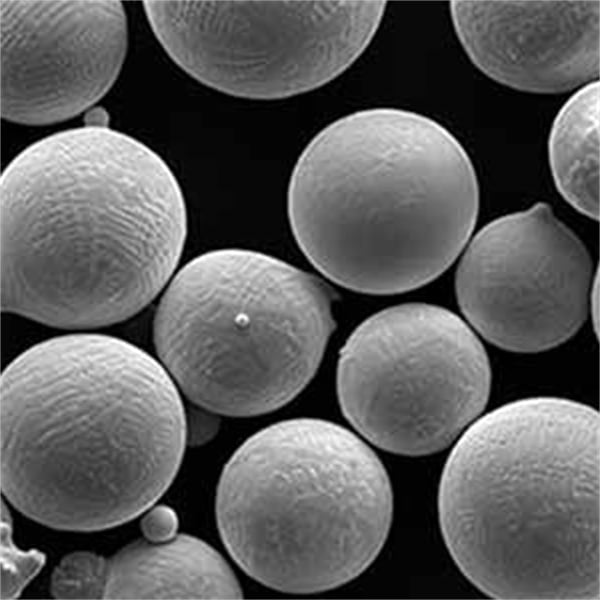
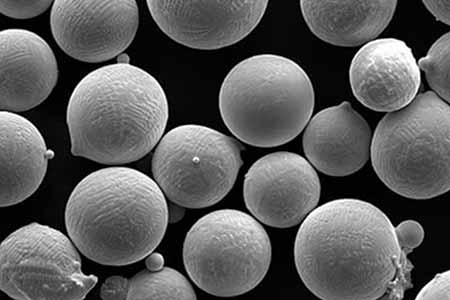
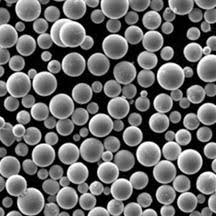
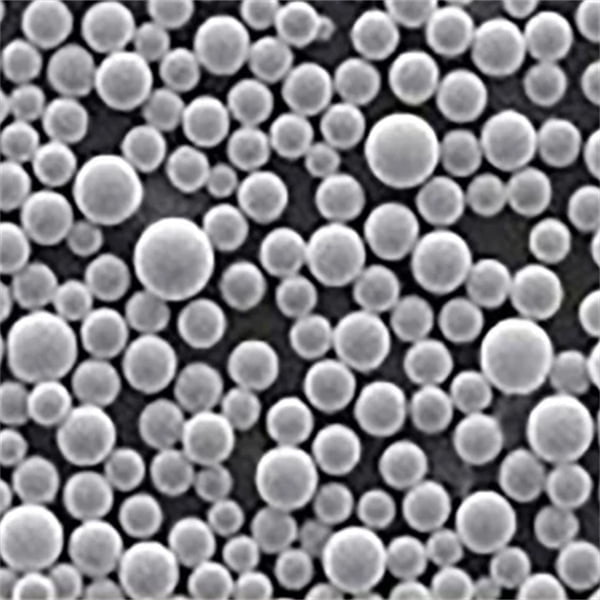
Suppliers and Pricing Details
Supplier | Metal Powder Models Available | Price Range |
---|---|---|
Global Metal Powders | Inconel 625, Stellite 6, Tungsten Carbide | $50 – $100 per kg |
American Elements | 316L Stainless Steel, Aluminum 6061, Copper-Nickel 90/10 | $30 – $70 per kg |
Carpenter Technology | Titanium Ti-6Al-4V, Nickel 200, Hastelloy C276 | $100 – $200 per kg |
H.C. Starck | Molybdenum, Tungsten Carbide, Stellite 6 | $80 – $150 per kg |
Advanced Metal Powders | 316L Stainless Steel, Inconel 625, Aluminum 6061 | $40 – $90 per kg |
Comparing Pros and Cons: Metal Powders for Workpiece Repair
Metal Powder Model | Pros | Cons |
---|---|---|
Inconel 625 | High strength, excellent corrosion resistance | Expensive, difficult to machine |
Stellite 6 | Exceptional wear resistance, hardness | Brittle, expensive |
Tungsten Carbide | Superior hardness, wear resistance | High cost, difficult to process |
316L Stainless Steel | Corrosion resistance, good mechanical properties | Lower strength compared to other alloys |
Aluminum 6061 | Lightweight, good corrosion resistance | Lower strength, not suitable for high-temperature applications |
Copper-Nickel 90/10 | Good weldability, corrosion resistance | Expensive, lower mechanical strength |
Titanium Ti-6Al-4V | High strength-to-weight ratio, corrosion resistance | Expensive, challenging to weld |
Nickel 200 | Good electrical conductivity, corrosion resistance | Limited high-temperature applications |
Hastelloy C276 | Excellent corrosion resistance, high strength | Very expensive, difficult to machine |
Molybdenum | High melting point, good thermal conductivity | Brittle, challenging to work with |
Detailed Techniques in Workpiece Repair
Welding
Welding is a process of joining two or more pieces of metal using heat and pressure. The welding process can vary significantly depending on the materials involved and the desired outcome. Common welding techniques include MIG (Metal Inert Gas), TIG (Tungsten Inert Gas), and stick welding. Each technique has its advantages and specific applications:
- MIG Welding: Ideal for thin to medium-thickness metals, offering high-speed welding with minimal clean-up.
- TIG Welding: Provides precise control over the weld, making it suitable for thin materials and intricate work.
- Stick Welding: Versatile and effective for thicker materials and outdoor applications.
Brazing
Brazing involves joining metals by melting a filler metal with a lower melting point than the workpieces. This technique is often used for its ability to create strong, leak-proof joints without melting the base metals. It is commonly applied in plumbing, HVAC systems, and automotive repair.
Soldering
Soldering is similar to brazing but generally used for smaller, more delicate tasks. It involves melting a filler metal (solder) to join workpieces. Soldering is widely used in electronics, jewelry making, and small metal repairs.
Metal Powders
Using metal powders for workpiece repair is a specialized technique involving the application of powdered metals to fill voids, build up worn surfaces, or create new parts. This method is particularly effective for precision repairs and applications requiring high strength and durability.
Applications and Use Cases
Automotive Industry
In the automotive industry, workpiece repair is essential for maintaining engine components, transmission parts, and bodywork. Metal powders like Inconel 625 and 316L Stainless Steel are often used to repair turbochargers, exhaust systems, and other high-stress components.
Aerospace Industry
Aerospace applications require materials that can withstand extreme conditions, such as high temperatures and pressures. Titanium Ti-6Al-4V and Hastelloy C276 are frequently used for repairing turbine blades, engine components, and structural parts.
Manufacturing and Heavy Machinery
Manufacturing and heavy machinery industries rely on robust and durable repairs to keep equipment running smoothly. Stellite 6 and Tungsten Carbide are ideal for repairing cutting tools, wear plates, and other heavily used components.
Marine and Offshore Engineering
In marine environments, corrosion resistance is paramount. Copper-Nickel 90/10 and 316L Stainless Steel are commonly used to repair heat exchangers, condensers, and other components exposed to seawater.
Medical and Dental Fields
The medical and dental fields require biocompatible and high-strength materials for repairing surgical instruments, implants, and prosthetics. Titanium Ti-6Al-4V and 316L Stainless Steel are popular choices for these applications.
Advantages of Workpiece Repair
Repairing a workpiece offers several advantages compared to replacing it entirely:
- Cost-Effective: Repairing is often significantly cheaper than replacing a part.
- Time-Saving: Repairs can be completed faster than manufacturing or sourcing a new part.
- Resource Efficiency: Repairing reduces waste and conserves materials.
- Extended Lifespan: Proper repairs can extend the life of machinery and components.
- Customization: Repairs can be tailored to specific needs and conditions.
Challenges and Limitations
Despite its advantages, workpiece repair also presents certain challenges and limitations:
- Skill Requirements: Effective repair requires skilled technicians and specialized knowledge.
- Material Compatibility: Not all materials are suitable for repair, and mismatched materials can cause failure.
- Quality Control: Ensuring the quality and integrity of repairs can be challenging.
- Equipment Needs: Advanced repair techniques may require specialized equipment.
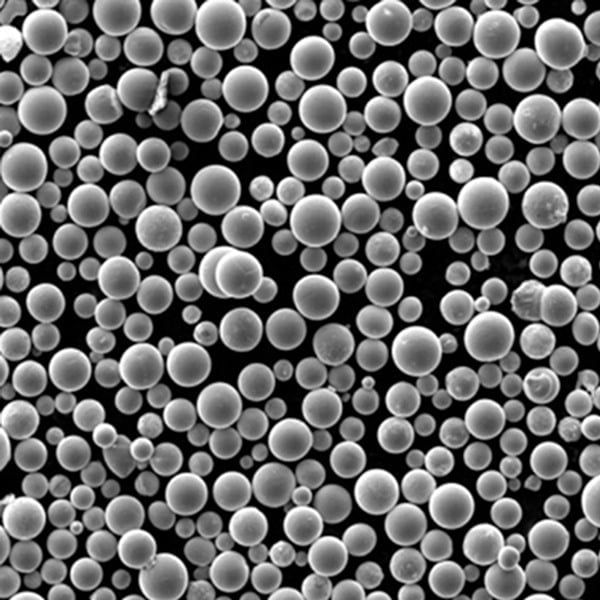
FAQ
Question | Answer |
---|---|
What is the best method for repairing a worn workpiece? | The best method depends on the material and application. Common methods include welding, brazing, soldering, and using metal powders. |
Can all metals be repaired using metal powders? | Not all metals are suitable for powder repair. It’s important to choose the appropriate powder for the specific material and application. |
How do I choose the right metal powder for repair? | Consider the composition, properties, and intended use of the powder. Refer to supplier specifications and consult with experts if needed. |
Is it cost-effective to repair workpieces instead of replacing them? | Yes, repairing workpieces is often more cost-effective than replacing them, especially for high-value components. |
What industries benefit most from workpiece repair? | Industries like automotive, aerospace, manufacturing, marine, and medical fields benefit significantly from workpiece repair. |
How do I ensure the quality of a repaired workpiece? | Use high-quality materials, employ skilled technicians, and follow strict quality control procedures to ensure the integrity of the repair. |
What are the common challenges in workpiece repair? | Common challenges include skill requirements, material compatibility, quality control, and the need for specialized equipment. |
Can workpiece repair extend the life of my machinery? | Yes, proper repairs can significantly extend the lifespan of machinery and components, reducing downtime and costs. |
Conclusion
Workpiece repair is an essential aspect of maintaining and extending the life of industrial machinery and components. By understanding the various techniques and materials available, particularly metal powders, you can make informed decisions that optimize performance, reduce costs, and ensure the longevity of your equipment. Whether you’re dealing with minor wear and tear or significant damage, the right approach to repair can make all the difference. Use this guide to navigate the complexities of workpiece repair and choose the best solutions for your specific needs.
About 3DP mETAL
Product Category
CONTACT US
Any questions? Send us a message now! After receiving your message, we will process your request with a whole team.