Imagine a world where medicine comes in a fine mist you inhale, paint coats a car with a single pass, and firefighters extinguish blazes with a targeted shower. This isn’t science fiction; it’s the reality of vernevelingstechnologie, a powerful tool that breaks down liquids and solids into tiny particles, unlocking a universe of possibilities.
Classification of Verstuivingstechnologie
Think of atomization like a culinary technique – but for all sorts of materials. Just like whisking an egg creates a fluffy foam, atomization uses various methods to transform substances into a fine dispersion. Here’s a breakdown of the main approaches:
- Pneumatische verstuiving: This method utilizes compressed air to break up a liquid stream into droplets. Picture a garden hose with a strong spray – that’s the basic idea. It’s a popular choice for tasks like spray painting and dust control.
- Hydraulische verstuiving: Here, the liquid itself is the driving force. As the liquid is forced through a narrow orifice at high pressure, it shears and breaks into droplets. Imagine squeezing a water balloon – the forceful expulsion creates a spray, similar to hydraulic atomization. This method is commonly used in agricultural sprayers and fuel injectors.
- Two-Fluid Atomization: This combines the power of both air and liquid. By injecting compressed air into the liquid stream, even finer droplets are achieved. It’s a bit like using a whisk with an air pump – the added force creates a more delicate and even dispersion. This method is ideal for applications like medical nebulizers and coating sensitive surfaces.
- Ultrasone verstuiving: This technology relies on high-frequency sound waves to vibrate and break up the material. Imagine using sound waves to shatter a glass – that’s the basic principle. It’s a gentle yet effective method for creating ultra-fine mists, often used in humidifiers and essential oil diffusers.
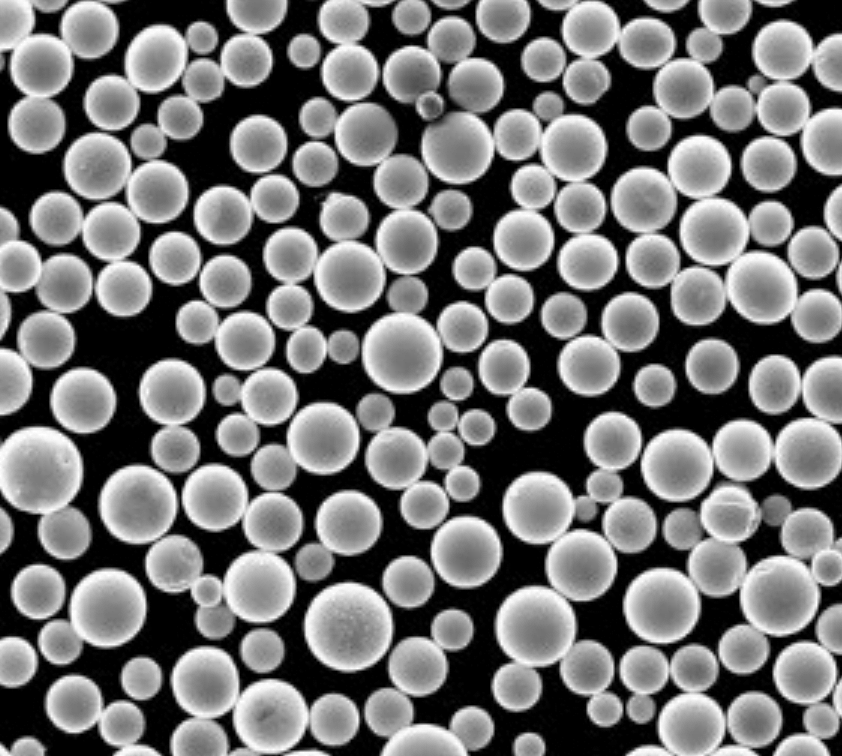
Characteristics of Atomization Technology
Beyond the classification, what makes atomization technology so special? Here are some key characteristics that set it apart:
- Controllable Particle Size: The beauty of atomization lies in its ability to tailor the droplet size. From coarse sprays for industrial applications to ultra-fine mists for medical use, the technology offers a wide range of control. Imagine adjusting the coarseness of your pepper grinder – atomization offers similar control over the “grind” of liquids and solids.
- Improved Efficiency: By breaking down materials into smaller particles, atomization allows for better utilization. Imagine trying to paint a wall with a thick glob of paint versus a fine mist – the mist will coat the surface more evenly and use less paint overall. This translates to efficiency gains in various applications.
- Verbeterde prestaties: The increased surface area created by tiny particles can significantly impact performance. For instance, a finer fuel mist in an engine leads to better combustion. Imagine a campfire with large logs versus kindling – the kindling ignites faster and burns more efficiently, similar to how a finer fuel mist enhances engine performance.
- Minder afval: Atomization can minimize waste by ensuring even distribution of materials. This is crucial in applications like agriculture, where precise application of pesticides and fertilizers reduces both environmental impact and wasted resources.
De toepassingen van Verstuivingstechnologie
The world of atomization stretches far and wide, impacting numerous aspects of our lives. Here are some intriguing examples:
Applicatie | Beschrijving | Voordelen | Overwegingen | Voorbeelden |
---|---|---|---|---|
Landbouw | Precise application of pesticides, herbicides, and fertilizers ensures targeted delivery and minimizes environmental impact. Atomization allows farmers to control droplet size and spray patterns, reducing drift and ensuring chemicals reach their intended targets. | Reduced waste of agricultural chemicals Enhanced crop yield Minimized environmental impact Improved farmer safety | Selection of appropriate nozzle type and droplet size for specific chemicals and targets. Weather conditions can affect spray drift. Maintenance of spray equipment is crucial to ensure optimal performance. | Spraying herbicides to control weeds without harming surrounding crops. Applying targeted fungicides to specific areas of a vineyard. Distributing liquid fertilizers for even nutrient delivery across a field. |
Fabricage | From coating delicate electronics to applying a smooth finish on cars, atomization offers precise control and efficient material use. Paint particles of uniform size ensure a flawless finish, while precise control over spray patterns minimizes waste. | Improved product quality Enhanced production efficiency Reduced material waste Consistent coating thickness | Selecting the right atomization method (e.g., pneumatic, electrostatic) based on material properties and desired finish. Optimizing spray parameters like pressure and flow rate for each application. Ensuring proper ventilation to remove overspray and protect workers. | Applying a thin layer of solder paste on circuit boards for electronics assembly. Painting car bodies with a uniform, high-quality finish. Coating furniture with a durable and aesthetically pleasing layer. |
Voedselverwerking | Atomization plays a crucial role in various food applications, from creating powdered milk for instant consumption to atomizing flavors for instant drinks. The process allows for efficient drying and preservation of food products. | Increased convenience and shelf life of food products Improved product consistency Reduced processing time Minimized food waste | Selecting the appropriate atomization technique based on the desired particle size and product characteristics. Controlling drying conditions (temperature, pressure) to ensure product quality. Maintaining a hygienic environment to prevent food contamination. | Transforming liquid milk into a shelf-stable powder for instant preparation. Atomizing coffee extract to create instant coffee granules. Drying fruit juices into a concentrated powder form for convenient use. |
Geneeskunde | Inhalation therapy relies on atomization technology to deliver medication directly to the lungs. Nebulizers and inhalers use atomization to create a fine mist of medication that can be easily inhaled, bypassing the digestive system for faster and more targeted treatment. | Efficient and targeted drug delivery Improved treatment outcomes for respiratory conditions Reduced side effects compared to oral medications Convenient and portable medication delivery systems | Selecting the right atomization method for specific medications and patient needs. Particle size of the medication mist is crucial for optimal lung deposition. Proper cleaning and maintenance of nebulizers and inhalers are essential. | Delivering bronchodilators to treat asthma symptoms. Administering antibiotics for respiratory infections. Providing pain relief through inhaled medications. |
Firefighting | Specialized fog cannons utilize atomization to create a dense mist that effectively extinguishes fires. The fine water droplets absorb heat and create an oxygen-depleted environment, suffocating the flames and minimizing water damage. | Faster and more efficient fire suppression Reduced water usage compared to traditional firefighting methods Lower risk of structural damage from water Improved firefighter safety | Selecting the appropriate atomization nozzle for the specific type of fire. Ensuring adequate water supply and pressure for effective operation. Following safety protocols for firefighting operations. | Extinguishing industrial fires involving flammable liquids. Controlling wildfires by creating firebreaks with atomized water mist. Suppressing kitchen fires by minimizing the spread of flames and grease. |
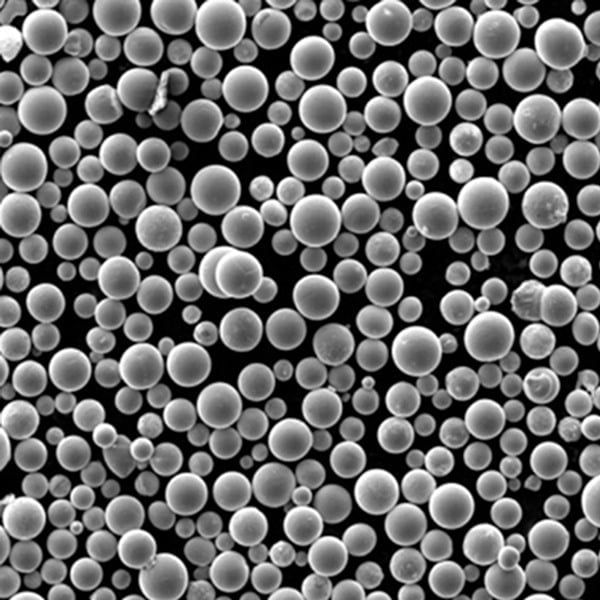
the Nuances of Verstuivingstechnologie
Aspect | Beschrijving | Impact |
---|---|---|
Degree of Atomization | This refers to the final size and distribution of the droplets or particles created. Technologies like ultrasonic nebulizers produce incredibly fine mists (in the micrometer range) ideal for drug delivery, while pressure nozzles used in agriculture might create larger droplets (millimeters) for efficient irrigation. | The degree of atomization significantly affects the application. Finer droplets have a larger surface area, promoting faster evaporation and better interaction with the target (e.g., medication in lungs). Conversely, larger droplets can deliver a higher volume of material at once. |
Fluid Properties | The viscosity, surface tension, and presence of solids in the liquid being atomized can influence the process. High viscosity liquids require more energy to break into droplets, while surface tension can cause them to clump together. Solids require specialized nozzles to prevent clogging. | Understanding the fluid properties is crucial for efficient atomization. Pre-heating viscous liquids can improve flow, while specific nozzle designs can counteract surface tension or handle solids. Choosing the wrong technology for the fluid can lead to uneven atomization, wasted energy, and equipment damage. |
Control over the Spray Pattern | The ability to direct and shape the atomized spray is essential in various applications. Fan nozzles create flat, wide sprays for coating surfaces, while hollow cone nozzles produce hollow, cone-shaped patterns for tasks like cooling towers. | Precise control over the spray pattern minimizes waste and optimizes application. In agriculture, targeted spraying reduces herbicide or pesticide use on non-target areas. Conversely, a poorly designed spray pattern in a paint booth can lead to uneven coverage and overspray. |
Energy Source | Atomization can be achieved through various methods, each with its own advantages and limitations. Compressed air offers simplicity but can be energy-intensive. Ultrasonic waves provide precise control but might not be suitable for high-volume applications. | The choice of energy source impacts efficiency, cost, and environmental footprint. Compressed air systems are relatively inexpensive but require significant energy input. Electrostatic atomization offers lower energy consumption but may have limitations on the types of fluids it can handle. |
Safety Considerations | Depending on the materials being atomized, there might be safety concerns regarding flammability, inhalation hazards, or potential for explosions. Specialized nozzles and enclosures may be necessary. | Safety is paramount. For flammable liquids, explosion-proof equipment is crucial. Inhaling certain atomized materials can be hazardous, requiring proper ventilation and operator protection. |
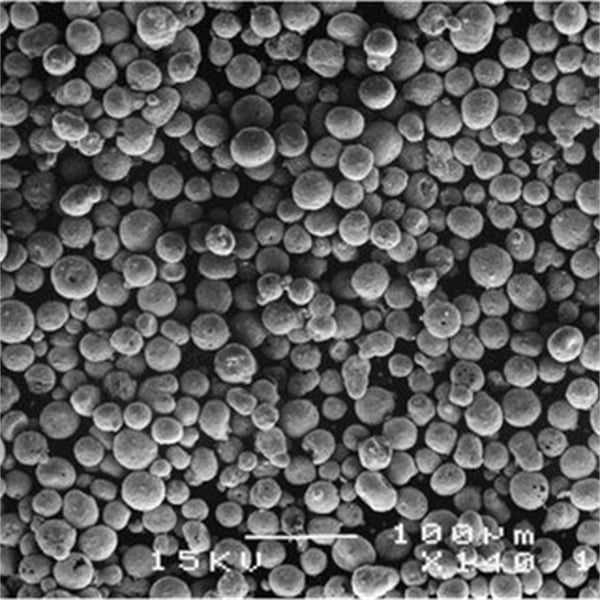
Optimizing for Specific Needs in Verstuivingstechnologie
Factor | Overwegingen | Optimization Strategies |
---|---|---|
Aanvraagvereisten | The primary function of the atomized spray dictates key choices. In spray drying, a narrow size distribution of uniform droplets is crucial for consistent product formation. Conversely, coating applications might prioritize a wider spray pattern for efficient material deposition. | Understanding the desired outcome of the atomization process is the first step. Achieving a specific particle size might necessitate a two-stage atomization process, while high deposition efficiency could require optimizing nozzle geometry and material flow rate. |
Materiaaleigenschappen | The physical and chemical characteristics of the liquid being atomized significantly influence the selection of technology. High viscosity liquids benefit from preheating or using pressure-fed nozzles. Sheer-sensitive materials might require gentler atomization techniques like ultrasonic nebulization. | Matching the atomization method to the fluid properties ensures efficient processing and minimizes potential damage. For instance, using a high-pressure nozzle with a shear-sensitive polymer solution could lead to product degradation. |
Production Scale and Throughput | The volume of material that needs to be atomized per unit time dictates the choice of technology. Ultrasonic nozzles, while precise, might not be suitable for large-scale industrial processes. Conversely, pressure nozzles excel at high throughput but might lack the control needed for delicate applications. | Balancing precision with efficiency is key. Pilot testing with different atomization techniques helps determine the optimal approach for achieving desired production volumes while maintaining product quality. |
Energie-efficiëntie | Minimizing energy consumption is a growing concern. Compressed air nozzles, while common, can be energy-intensive. Exploring alternative methods like electrostatic atomization or optimizing compressed air flow rates through computational modeling can lead to significant energy savings. | Several strategies can be employed to improve energy efficiency. Investing in energy-efficient equipment, optimizing operating parameters, and implementing process automation can all contribute to a more sustainable operation. |
Milieu-impact | The potential environmental impact of the atomization process should be considered. Overspray and solvent use can contribute to air and water pollution. Choosing closed-loop systems for solvent recovery and implementing targeted spray patterns can minimize environmental impact. | Sustainable practices are becoming increasingly important. Selecting atomization techniques with minimal overspray and exploring environmentally friendly solvents whenever possible contribute to a more responsible approach. |
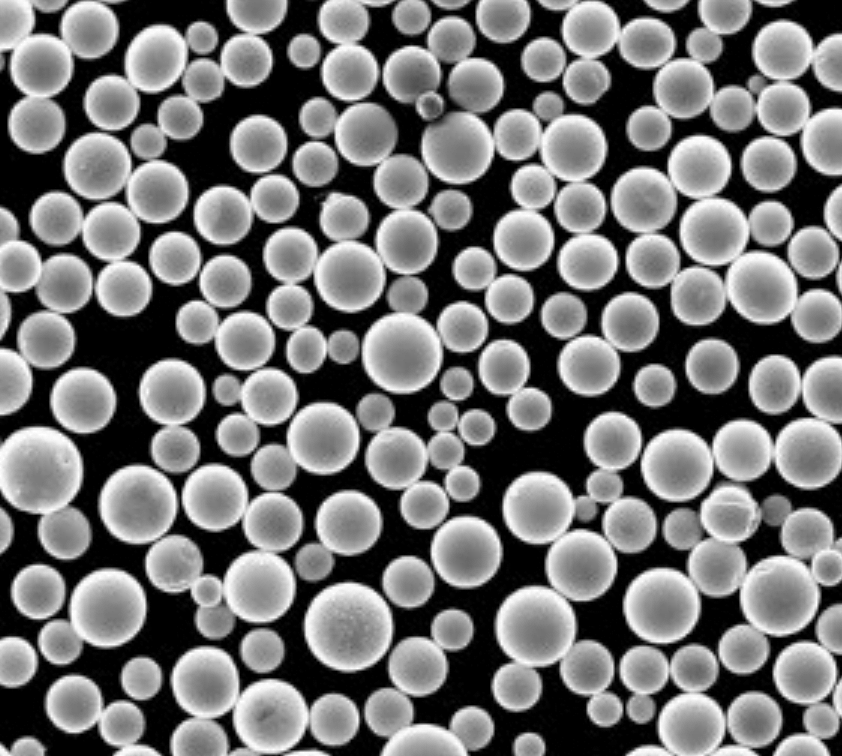
Pushing the Boundaries of Atomization
De wereld van vernevelingstechnologie is constantly evolving. Here are some exciting advancements on the horizon:
- Nanotechnology: Atomization techniques are being refined to create even finer particles in the nanometer range. These nanoparticles hold immense potential in medicine, materials science, and electronics.
- Geavanceerde materialen: New materials for nozzles and other components are being developed to handle more aggressive chemicals and extreme temperatures, expanding the application possibilities.
- Computational Modeling: Computer simulations are playing a growing role in optimizing atomization processes This allows for more precise control and prediction of droplet size and distribution.
FAQ
Q: What are the advantages of atomization technology?
A: Atomization offers several advantages, including:
- Controllable particle size: Tailoring droplets to specific needs.
- Improved efficiency: Better utilization of materials and reduced waste.
- Enhanced performance: Increased surface area for better performance in various applications.
- Minder afval: Precise application minimizes environmental impact.
Q: What are some limitations of atomization technology?
A: While powerful, atomization does have some limitations:
- Energieverbruik: Some methods, like pneumatic atomization, require compressed air, which can increase energy consumption.
- Clogging risk: Fine nozzles can be susceptible to clogging, requiring proper maintenance.
- Material limitations: Not all materials are easily atomized, especially those with high viscosity or that solidify quickly.
Q: What are some safety considerations with atomization technology?
A: Safety is paramount when working with atomization. Here are some key considerations:
- Respiratory hazards: Inhaling certain atomized materials can be harmful. Proper ventilation and personal protective equipment might be necessary.
- Fire hazards: Some atomized liquids can be flammable. Precautions should be taken to prevent ignition.
- Pressure hazards: High-pressure systems used in atomization require proper training and safety protocols.
In Conclusion
Atomization technology, though often unseen, plays a vital role in shaping our world. From the medicine we take to the food we eat, from the cars we drive to the fires we extinguish, the power of breaking things down to build a better future lies in the magic of tiny particles. As research continues to push the boundaries, the possibilities of atomization technology are truly limitless.
Over 3DP mETAL
Productcategorie
NEEM CONTACT OP
Vragen? Stuur ons nu een bericht! Na ontvangst van uw bericht gaan we met een heel team uw aanvraag verwerken.