Imagine building complex metal parts layer by layer, with the precision of a digital file and the strength of forged steel. This isn’t science fiction; it’s the reality of Electron Beam Additive Manufacturing (EBAM), a revolutionary technology that’s transforming the way we design and produce metal components.
What is Electron Beam Additive Manufacturing (EBAM)?
EBAM, also known as Electron Beam Melting (EBM), is a metal additive manufacturing process that utilizes a high-powered electron beam to melt metal wire feedstock, building a three-dimensional part layer by layer within a vacuum chamber. Think of it like a high-tech inkjet printer, but instead of ink cartridges, it uses spools of metal wire, and instead of paper, it builds on a platform that gradually lowers as the part takes shape.
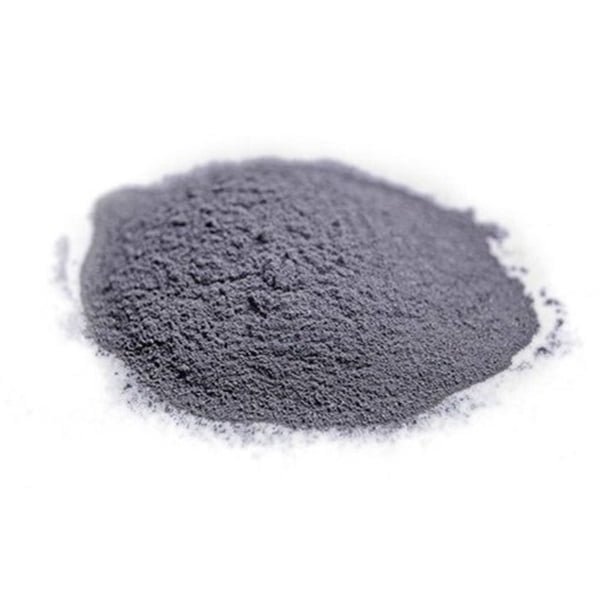
Operational Principle of Electron Beam Additive Manufacturing (EBAM)
The EBAM process can be broken down into several key steps:
- Digital Design: The first step, as with any 3D printing process, is creating a computer-aided design (CAD) model of the desired part. This digital blueprint will dictate the path of the electron beam and the deposition of the metal wire.
- Vacuum Chamber Preparation: The build platform and metal wire are loaded into a high-vacuum chamber. This eliminates the presence of oxygen and other contaminants that could hinder the melting process and compromise the final part’s properties.
- Elektronenbundelsmelten: An electron beam is generated by a high-voltage electron gun. This beam is focused and directed towards the metal wire feedstock, melting it upon contact.
- Layer-by-Layer Deposition: The electron beam is precisely controlled by computer software, following the pre-programmed path defined by the CAD model. As the molten metal cools and solidifies, it bonds with the previous layer, building the part one thin layer at a time.
- Part Removal and Post-Processing: Once the build process is complete, the vacuum chamber is depressurized, and the newly formed part is removed from the build platform. Depending on the application, the part may undergo additional finishing processes like heat treatment or machining.
Advantages of Electron Beam Additive Manufacturing (EBAM)
EBAM offers several advantages over traditional metal fabrication techniques like casting, forging, and machining:
- Ontwerpvrijheid: Unlike traditional methods, EBAM is not limited by complex geometries. With EBAM, you can design intricate internal features, channels, and lattice structures that would be impossible or prohibitively expensive to achieve with other methods. This opens up a world of possibilities for lightweight and high-performance parts.
- Large Build Volumes: EBAM systems can create parts significantly larger than those possible with other additive manufacturing processes like laser powder bed fusion (LPBF). This makes it ideal for applications in aerospace, defense, and heavy industry.
- Veelzijdigheid van materiaal: EBAM can work with a wide range of metal alloys, including refractory metals like titanium and tantalum, which are difficult or impossible to process with other methods. This allows for the creation of parts with exceptional strength, heat resistance, and corrosion resistance.
- High Deposition Rates: EBAM boasts significantly faster deposition rates compared to LPBF. This translates to quicker build times and higher production efficiency.
- Minimal Material Waste: Unlike traditional methods that generate significant scrap material, EBAM utilizes a near-net-shape approach, minimizing leftover material and promoting sustainability.
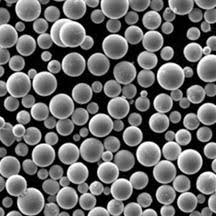
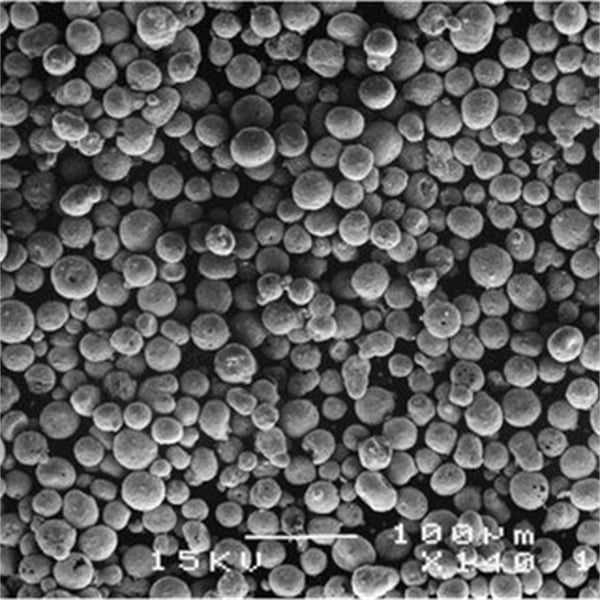
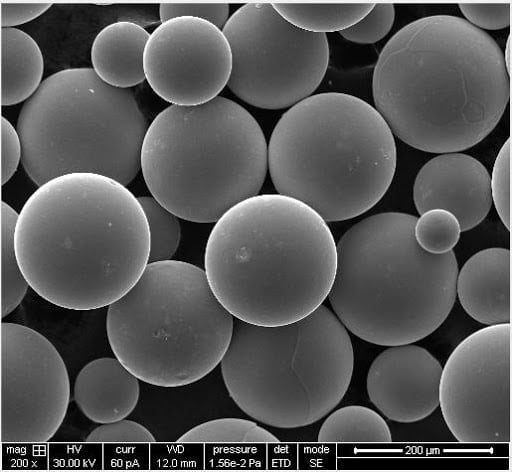
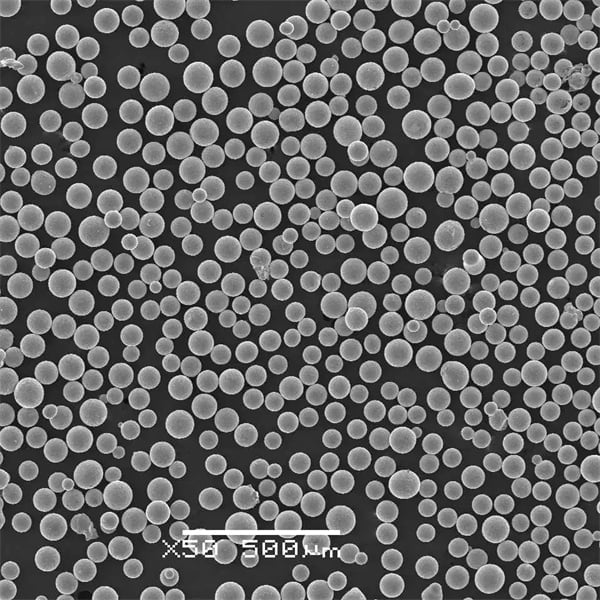
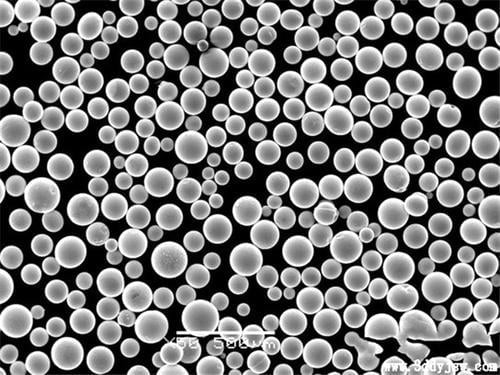
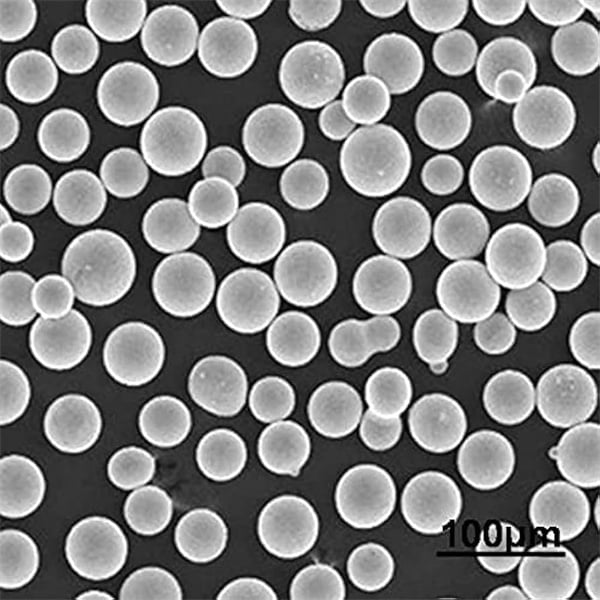
Applications of Electron Beam Additive Manufacturing (EBAM)
EBAM’s unique capabilities make it a prime candidate for a wide range of applications across various industries:
- Lucht- en ruimtevaart: The ability to create lightweight, high-strength components with complex internal structures makes EBAM ideal for aircraft parts, rocket engine components, and satellite structures.
- Verdediging: EBAM is used to produce complex weapon systems components, armored vehicles, and other mission-critical parts requiring exceptional strength and durability.
- Medisch: Custom orthopedic implants, prosthetics, and surgical instruments can be manufactured with EBAM, offering patients personalized solutions with improved biocompatibility.
- Olie en gas: EBAM is used to create high-pressure resistant components for downhole tools and equipment operating in harsh environments.
- Automobiel: High-performance engine components, lightweight chassis components, and intricate heat exchangers are potential applications for EBAM in the automotive industry.
Challenges and Considerations of Electron Beam Additive Manufacturing (EBAM)
While EBAM offers significant advantages, it’s essential to consider some limitations:
- Hoge kosten: EBAM systems are currently more expensive compared to other metal additive manufacturing technologies. This is a factor to consider, especially for low-volume production runs.
- Afwerking oppervlak: Due to the melting process, EBAM parts can have a rougher surface finish compared to those produced by other methods like machining. This may necessitate additional post-processing steps depending on the application requirements.
- Materiaaleigenschappen: The rapid melting and solidification process in EBAM can lead to slight variations in the final microstructure of the material compared to traditional methods. This can have subtle effects on mechanical properties and requires careful consideration during the design and build process.
- Beperkingen in onderdeelgrootte: While EBAM boasts large build volumes compared to other additive manufacturing processes, there are still limitations on the maximum part size achievable. However, these limitations are constantly being pushed as technology advances.
Future of Electron Beam Additive Manufacturing (EBAM)
Despite these challenges, EBAM is a rapidly evolving technology with immense potential. Here are some exciting trends shaping the future of EBAM:
- Lagere kosten: As technology matures and adoption rates increase, we can expect the cost of EBAM systems and materials to come down, making it more accessible to a wider range of manufacturers.
- Geavanceerde materialen: Research is ongoing to develop new metal alloys and composite materials specifically optimized for EBAM, further expanding the range of applications.
- Hybrid Manufacturing: The integration of EBAM with other manufacturing techniques, such as machining or subtractive processes, is gaining traction. This allows for the creation of complex parts with features that are difficult or impossible to achieve with EBAM alone.
- Automation and Software Advancements: Automation of the EBAM process and development of sophisticated software for design optimization and process control will further improve efficiency and part quality.
EBAM vs. Other Metal Additive Manufacturing Processes
When choosing a metal additive manufacturing process, it’s crucial to understand the strengths and weaknesses of each technology relative to your specific application. Here’s a brief comparison of EBAM with other popular methods:
- Electron Beam Powder Bed Fusion (EBPBF): This process uses an electron beam to melt metal powder laid down in a thin layer. Compared to EBAM, EBPBF offers finer resolution and smoother surface finishes but is limited in build volume and material selection.
- Laser Powder Bed Fusion (LPBF): This widely used method utilizes a laser beam to melt metal powder. While offering good resolution and detail, LPBF typically has slower deposition rates and higher material waste compared to EBAM.
- Directed Energy Deposition (DED): Similar to EBAM, DED uses a focused energy beam to melt metal wire or powder, but it’s typically used for repairing existing parts or creating features on top of a pre-manufactured substrate. DED offers higher deposition rates but is limited in design freedom compared to EBAM.
Factors to Consider When Choosing Between EBAM and Other Metal Additive Manufacturing Processes:
- Deel Complexiteit: For intricate geometries with internal features, EBAM excels.
- Onderdeelgrootte: If you require large-scale metal parts, EBAM is a clear choice.
- Materiaalkeuze: EBAM offers superior compatibility with challenging materials like titanium and tantalum.
- Surface Finish Requirements: If a smooth surface finish is critical, other methods like EBPBF may be preferable.
- Productievolume: For high-volume production runs, established methods like LPBF might be more cost-effective.
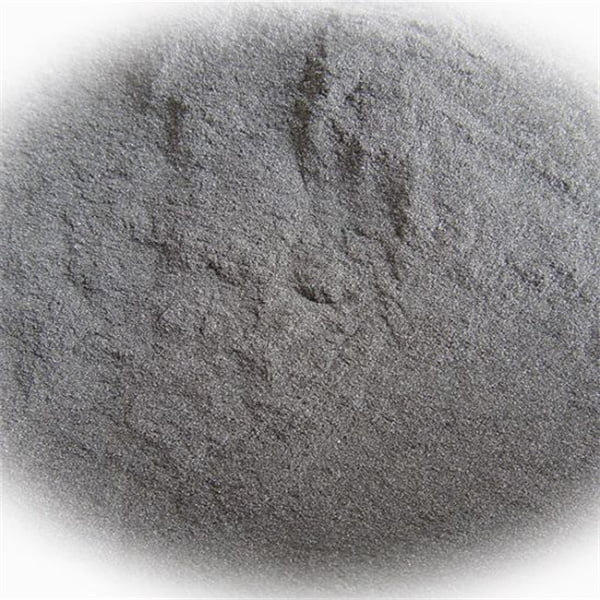
FAQ
Q: What are the benefits of EBAM over traditional metal fabrication methods?
A: EBAM offers design freedom, ability to create large parts, works with a wider range of materials, boasts faster build times, and minimizes material waste.
Q: What are some applications of EBAM?
A: EBAM is used in aerospace, defense, medical, oil & gas, and automotive industries for components requiring high strength, complex geometries, and compatibility with challenging materials.
Q: What are the limitations of EBAM?
A: Higher cost compared to other methods, potentially rougher surface finishes, variations in material properties, and limitations on part size.
Q: What’s the future outlook for EBAM?
A: Reduced costs, development of advanced materials, integration with other manufacturing techniques, and advancements in automation and software are promising trends for EBAM’s future.
Q: How does EBAM compare to other metal additive manufacturing processes?
A: Consider factors like part complexity, size, material selection, surface finish requirements, and production volume to choose the most suitable method for your needs.
Over 3DP mETAL
Productcategorie
NEEM CONTACT OP
Vragen? Stuur ons nu een bericht! Na ontvangst van uw bericht gaan we met een heel team uw aanvraag verwerken.