Imagine building complex metal parts layer by layer with a focused beam of electrons, melting metal powder into a near-final shape. This isn’t science fiction; it’s the magic of Smelten met elektronenstralen (EBM) technology, a revolutionary 3D printing process transforming the manufacturing landscape.
This article delves deep into the world of EBM, exploring its inner workings, advantages, limitations, and real-world applications. So, buckle up and get ready to be amazed!
De kenmerken van Smelten met elektronenstralen
EBM falls under the umbrella of Additive Manufacturing (AM), also known as 3D printing. Unlike traditional subtractive manufacturing techniques that remove material to create a final product, EBM builds objects layer by layer, adding material until the desired form is achieved.
Here are some key characteristics that define EBM:
- Energy Source: EBM utilizes a high-powered electron beam generated within a vacuum chamber. This beam acts as a heat source, selectively melting metal powder to create the desired geometry.
- Material Feedstock: EBM primarily uses fine metal powders with specific particle sizes and flow characteristics. Popular materials include titanium alloys, stainless steel, Inconel, and even exotic materials like tantalum and tungsten.
- Vacuümomgeving: The entire EBM process takes place in a high-vacuum chamber. This eliminates oxidation and contamination, ensuring high-quality metal parts with exceptional mechanical properties.
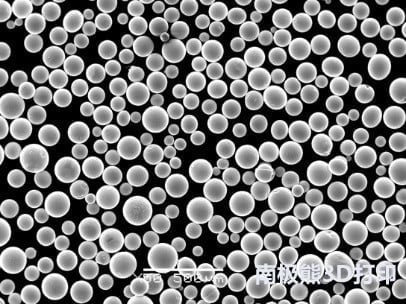
The Working Principle of EBM Technology
Now, let’s peel back the layers and understand how EBM technology works:
- Voorbereiding: A 3D model of the desired part is created using CAD software. This model is then sliced into thin layers, essentially a digital blueprint for the EBM machine.
- Powder Bed Deposition: A layer of metal powder is spread evenly across the build platform within the vacuum chamber. Think of it like laying the foundation for your metal masterpiece.
- Smelten met elektronenstralen: The electron beam, generated by an electron gun, scans the powder bed according to the sliced digital model. The beam melts the targeted areas of the powder, fusing them together to form the first layer of the part.
- Layer-by-Layer Building: The build platform lowers slightly, and a fresh layer of metal powder is deposited on top of the previous melted layer. The electron beam then scans and melts the designated areas in this new layer, fusing it with the previous one. This process repeats layer by layer until the entire part is built.
- Support Removal: Once the build is complete, the chamber cools down, and the built part is removed from the surrounding unmelted powder. Support structures, which are also printed from metal powder but designed to be easily removed, might be present depending on the part geometry.
- Nabewerking: The final step involves removing any remaining support structures and potentially performing additional finishing processes, such as heat treatment or machining, depending on the desired final properties of the part.
The Advantages and Disadvantages of EBM Technology
Embracing the Benefits:
EBM boasts several advantages that make it a compelling choice for various applications:
- Hoogwaardige onderdelen: The vacuum environment minimizes contamination, leading to parts with excellent mechanical properties like strength, fatigue resistance, and biocompatibility. This makes EBM ideal for demanding industries like aerospace, medical implants, and automotive.
- Complexe geometrieën: EBM excels at creating intricate geometries with internal features and overhangs that would be challenging or impossible with traditional manufacturing methods. Imagine printing a lightweight lattice structure for an aircraft component – EBM makes it possible.
- Material Freedom: EBM handles a wide range of reactive and refractory metals that are difficult to process with conventional techniques. This opens doors for applications requiring unique material properties, like high-temperature resistance or biocompatibility.
- Design Optimization: EBM allows for lightweight design with internal channels and lattices, reducing weight without compromising strength. This can be a game-changer for applications like prosthetics and aerospace components.
Considering the Limitations:
While powerful, EBM technology does have some limitations to consider:
- Kosten: EBM machines and processes can be expensive compared to some other 3D printing technologies. This upfront investment might not be suitable for all projects.
- Oppervlakteruwheid: Parts produced by EBM can have a rougher surface finish compared to other AM techniques like Selective Laser Melting (SLM). This might require additional post-processing for some applications.
- Build Size: Current EBM machines typically have a limited build volume compared to some other AM methods. This might restrict the size of parts that can be produced.
- Residual Stress: The high temperatures involved in EBM can lead to residual stress within the printed part.
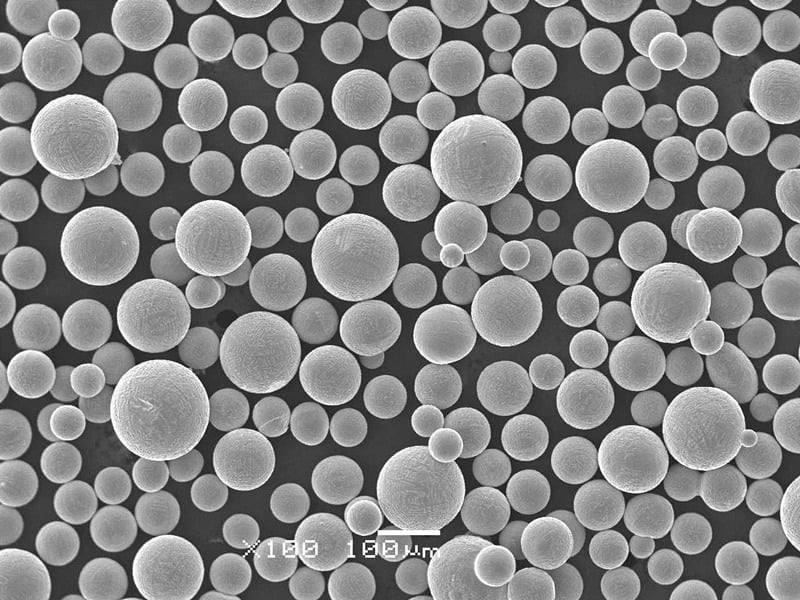
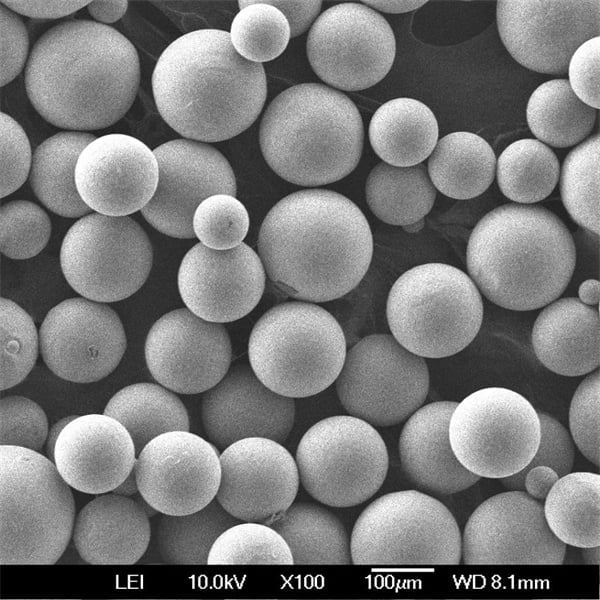
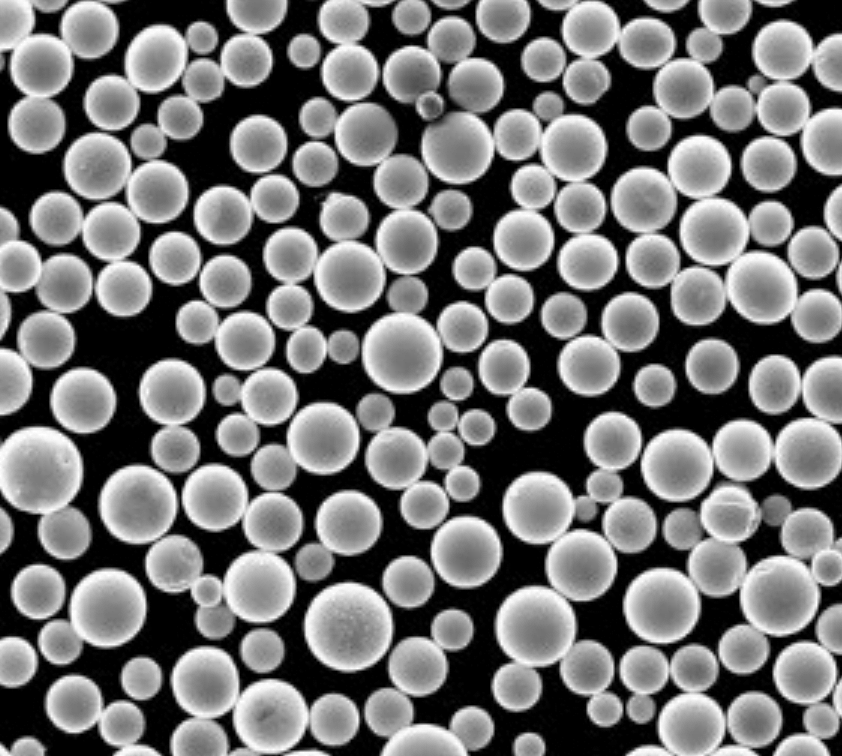
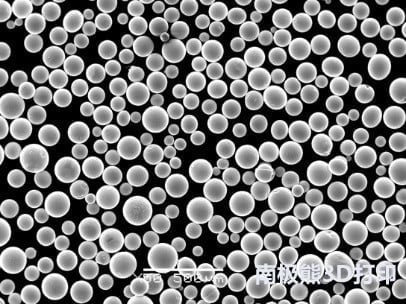
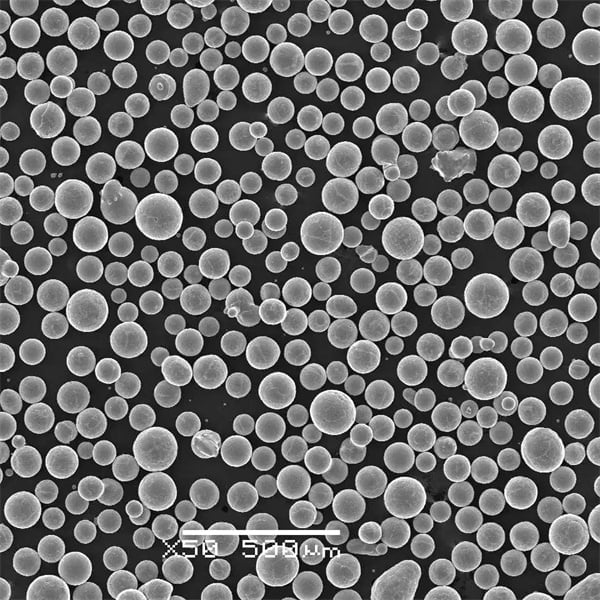
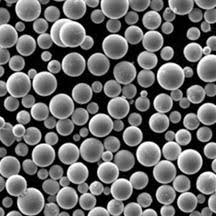
Technical Specifications of EBM Technology
Understanding the technical aspects of EBM provides valuable insights into its capabilities and limitations. Here’s a breakdown of some key parameters:
Materiaal compatibiliteit:
EBM thrives with a wide range of metal powders, including:
- Titanium Alloys: Widely used in aerospace, medical implants, and sporting goods due to their exceptional strength-to-weight ratio and biocompatibility. Popular examples include Ti-6Al-4V, Ti-6Al-4V ELI (extra low interstitial), and others.
- Roestvrij staal: A versatile material for various applications due to its corrosion resistance and mechanical properties. Common grades processed by EBM include 17-4PH, 316L, and others.
- Nickel-based Superalloys: Renowned for their high-temperature strength and oxidation resistance, making them ideal for jet engine components and other demanding environments. Inconel 625 and Inconel 718 are popular choices for EBM.
- Other Specialty Metals: EBM can handle reactive and refractory metals like tantalum, tungsten, and cobalt-chrome, expanding the possibilities for applications requiring unique properties.
Poeder Eigenschappen:
The properties of the metal powder significantly impact the EBM process and final part quality. Here are some crucial aspects:
- Deeltjesgrootte en -verdeling: EBM typically utilizes powders with a particle size range of 20-100 microns. A well-distributed particle size ensures optimal packing density and flowability within the powder bed.
- Sfericiteit: Spherical particles offer better flowability and packing density, leading to a more uniform melting process and improved part quality.
- Chemische samenstelling: The powder composition needs to be tightly controlled to ensure the final part meets the desired mechanical properties and avoids issues like cracking or porosity.
Process Parameters:
Several critical parameters influence the outcome of the EBM process:
- Beam Power and Scan Speed: These factors determine the depth and width of melting in each layer. Higher power and slower scan speeds lead to deeper melts, while lower power and faster speeds result in shallower melts. Selecting the right combination is essential for achieving optimal fusion and part quality.
- Beam Focus Diameter: This parameter influences the resolution and detail achievable in the printed part. A smaller focus diameter allows for finer features but might require slower build times.
- Build Platform Temperature: The build platform is typically preheated to a specific temperature to improve powder flow and enhance fusion between layers.
Benefits and Limitations Compared to SLM
Selective Laser Melting (SLM) is another popular 3D printing technology for metals that utilizes a laser beam for melting powder. Here’s a comparative analysis of EBM and SLM:
Functie | EBM | SALAAM |
---|---|---|
Energy Source | High-powered electron beam | Laser beam |
Environment | High vacuum | Inert gas atmosphere (typically Argon) |
Materiaal compatibiliteit | Wider range, including reactive metals | Limited to some reactive metals |
Afwerking oppervlak | Generally rougher | Can be smoother |
Bouwsnelheid | Faster | Can be slower |
Residual Stress | Higher due to higher processing temperatures | Lager |
Choosing between EBM and SLM depends on the specific application and desired part characteristics. EBM excels for applications requiring high-quality parts from reactive metals or intricate geometries, while SLM might be preferable for smoother surface finishes or cost-sensitive projects.
Applications of EBM Technology
EBM technology is revolutionizing various industries by enabling the creation of complex, high-performance metal parts. Here are some captivating examples:
- Lucht- en ruimtevaart: EBM is used to manufacture lightweight aircraft components like engine brackets, airfoils, and landing gear parts. The ability to design for minimal weight with internal lattices is a major advantage for fuel efficiency.
- Medische implantaten: EBM shines in creating custom-designed implants for knees, hips, and other body parts. The biocompatible nature of certain materials and the intricate geometries achievable with EBM prove highly beneficial for patient outcomes.
- Automobiel: EBM finds application in producing high-performance components for racing cars and luxury vehicles. Lightweight and strong parts like pistons, suspension components, and gearboxes can be created using EBM.
- Defense & Security: The ability to 3D print complex weapon components with unique properties makes EBM valuable in the defense sector. Additionally, EBM is used for creating customized armor components and other defense-related applications.
- Consumptiegoederen: EBM is increasingly used in high-end consumer products like sporting goods and luxury watches. The ability to create complex geometries with unique materials
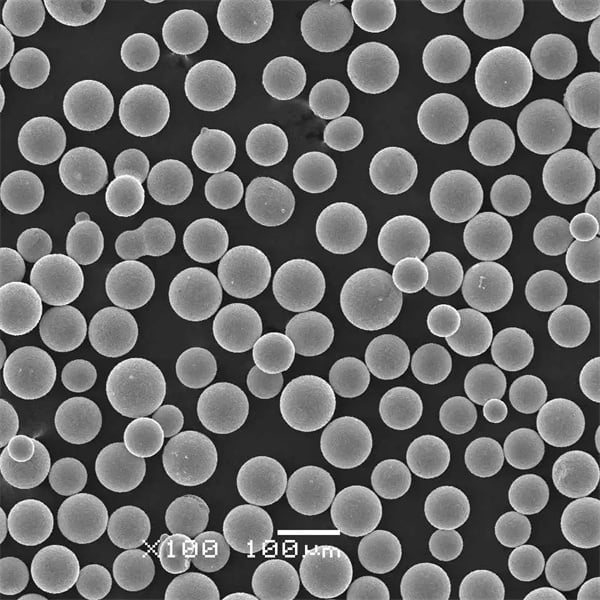
FAQ
EBM technology might spark a few questions. This FAQ section aims to shed light on some common inquiries:
Q: How strong are EBM-printed parts?
A: EBM parts boast excellent mechanical properties, including high strength, fatigue resistance, and good ductility depending on the material. The vacuum environment minimizes contamination, leading to parts with strong inter-atomic bonds.
However, residual stress can be a factor due to the high temperatures involved in the EBM process. Post-processing techniques like stress relieving heat treatment can help mitigate this.
Q: How does EBM compare to traditional manufacturing methods?
A: EBM offers several advantages over traditional methods like machining, casting, and forging:
- Ontwerpvrijheid: EBM allows for the creation of complex geometries that would be difficult or impossible with traditional methods. This opens doors for innovative designs and lighter weight parts.
- Minder afval: EBM is an additive manufacturing process, meaning material is added layer by layer to create the part. This minimizes waste compared to subtractive techniques like machining where material is removed to achieve the desired shape.
- Aanpassing: EBM is ideal for creating custom-designed parts or small batch production runs. The digital nature of the process allows for quick turnaround times for design modifications.
However, EBM also has some limitations compared to traditional methods:
- Kosten: EBM machines and processes can be expensive compared to traditional methods. This can make it less suitable for high-volume production runs.
- Build Size: Current EBM machines typically have a limited build volume compared to some traditional methods. This might restrict the size of parts that can be produced.
Q: What are the post-processing steps involved in EBM?
A: After the build is complete, several post-processing steps might be required:
- Support Removal: Depending on the part geometry, support structures used during printing need to be removed. This can be done mechanically or with chemical etching.
- Warmtebehandeling: Heat treatment can be used to improve the mechanical properties of the part by relieving residual stress or enhancing specific properties like strength or ductility.
- Bewerking: In some cases, additional machining might be required to achieve precise dimensional tolerances or surface finishes.
Q: Is EBM environmentally friendly?
A: Compared to traditional manufacturing methods, EBM can offer some environmental benefits:
- Minder materiaalafval: The additive nature of EBM minimizes material waste compared to subtractive techniques.
- Energie-efficiëntie: While EBM machines require energy, they can sometimes be more energy-efficient than traditional methods with extensive machining steps.
However, the environmental impact also depends on the specific materials used and the energy source powering the EBM machines.
Q: What’s the future of EBM technology?
A: The future of EBM looks bright! Here are some exciting possibilities:
- Advancements in Machine Technology: Developments in EBM machine technology, such as increased build volumes and faster build speeds, could make EBM more cost-competitive and suitable for a wider range of applications.
- Material Development: The exploration of new metal powders and their printability with EBM will expand the design possibilities and material properties achievable with this technology.
- Integratie met andere technologieën: Combining EBM with other technologies like in-situ machining or sensor integration could create even more functional and intelligent metal parts.
Over 3DP mETAL
Productcategorie
NEEM CONTACT OP
Vragen? Stuur ons nu een bericht! Na ontvangst van uw bericht gaan we met een heel team uw aanvraag verwerken.