Have you ever marveled at the intricate details of a 3D-printed prosthetic limb, the whisper-quiet efficiency of a jet engine turbine blade, or the lightweight strength of a high-performance bicycle frame? These marvels of modern engineering all share a common thread: they’re likely made from metal powders. But how exactly does a lump of solid metal get transformed into a fluffy cloud of tiny particles? Enter the fascinating world of gasverstuiverapparatuur.
An Overview of Gas Atomization
Gas atomization is a specialized technique for converting molten metal into a fine powder. Imagine a high-pressure stream of gas, like nitrogen or argon, blasting a molten metal stream into a million tiny droplets. As these droplets hurtle through a cooling chamber, they rapidly solidify into perfectly spherical metal particles, ranging in size from a few micrometers (millionths of a meter) to hundreds of micrometers.
This seemingly simple process unlocks a universe of possibilities. Metal powders boast unique properties compared to their bulk counterparts. They offer superior flowability, allowing for intricate shapes in additive manufacturing (3D printing). Their high surface area makes them ideal for applications like catalysis and battery electrodes. And their lightweight nature, combined with exceptional strength, opens doors for aerospace and automotive engineering.
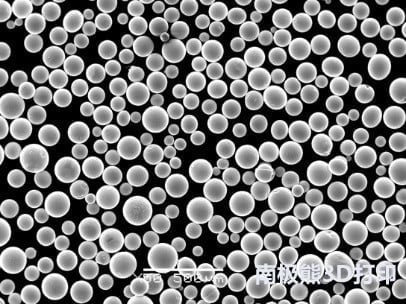
A Spectrum of Metal Powders
The world of metal atomized powders is as diverse as the applications they serve. Here’s a glimpse into some of the most popular metal powder models and their unique characteristics:
- Titanium Powder (CP Ti): This workhorse material offers a perfect blend of strength, low weight, and excellent corrosion resistance. It’s the go-to choice for aerospace components, medical implants, and high-performance sporting goods.
- Stainless Steel Powders (316L, 17-4PH): These versatile powders combine the strength and corrosion resistance of stainless steel with the design freedom of 3D printing. They find applications in everything from biomedical devices to chemical processing equipment.
- Aluminum Powders (AlSi10Mg, AA2024): Lightweight and readily recyclable, aluminum powders are revolutionizing the automotive and aerospace industries. AlSi10Mg offers excellent castability, while AA2024 boasts high strength for demanding applications.
- Nickel-based Superalloy Powders (Inconel 625, Inconel 718): These high-performance alloys can withstand extreme temperatures and harsh environments. They’re the heroes behind jet engine turbine blades, rocket engine components, and other high-heat applications.
- Cobalt Chrome Powders (CoCrMo): Biocompatible and wear-resistant, cobalt chrome powders are a mainstay in orthopedic implants like hip and knee replacements. Their exceptional strength ensures long-lasting performance in the human body.
- Koperpoeders: With their excellent electrical conductivity and thermal properties, copper powders are ideal for applications in electronics, heat sinks, and even electromagnetic shielding.
- Poeders van wolfraam: Dense and incredibly hard, tungsten powders are used in a variety of wear-resistant applications, such as drill bits, cutting tools, and armor-piercing projectiles.
- Tool Steel Powders (H13, M2): Known for their ability to hold a sharp edge, tool steel powders are perfect for creating complex cutting tools and dies used in manufacturing.
- Precious Metal Powders (Gold, Silver, Platinum): From intricate jewelry pieces to high-performance electrical components, precious metal powders offer a unique combination of aesthetics and functionality.
Toepassingen van Gasverstuiver Apparatuur
The applications of gas atomizer equipment are as vast as human imagination. Here’s a peek into some of the key industries leveraging this technology:
Industrie | TOEPASSINGEN |
---|---|
Additieve Productie (3D printen) | Complex metal parts, prosthetics, medical implants, aerospace components, lightweight automotive parts. |
Metaalspuiten Vormgeving (MIM) | High-volume production of intricate metal parts with near-net shape, gears, fasteners, electronic components. |
Thermisch spuiten | Coatings for wear resistance, corrosion protection, thermal management, turbine blade repair. |
Battery Technologies | Electrodes for lithium-ion batteries with high energy density and fast charging capabilities. |
Katalyse | High surface area catalysts for efficient chemical reactions in diverse industries. |
Sieraden | Creating intricate and lightweight jewelry pieces with precious metals. |
Voordelen van gasverstuivers
Gas atomization offers several advantages over traditional metal shaping techniques:
- Ongeëvenaarde ontwerpvrijheid: Metal powders enable the creation of complex geometries and intricate internal features, previously impossible with conventional manufacturing methods. This opens doors for innovation in everything from lightweight aircraft components to medical implants that perfectly mimic human bone structure.
- Superieure materiaaleigenschappen: The rapid solidification process inherent in gas atomization creates powders with unique microstructures. These microstructures can lead to improved strength, ductility, and corrosion resistance compared to conventionally manufactured metals.
- Reduced Waste and Improved Sustainability: Gas atomization offers minimal material loss compared to traditional techniques like machining or casting. This translates to reduced waste generation and a more sustainable manufacturing process.
- Massale aanpassingen: The ability to precisely control powder properties allows for the creation of metal powders tailored to specific applications. This enables engineers to optimize material performance for a particular need.
- High Powder Flowability: The spherical shape and smooth surface of gas-atomized powders make them flow freely, ideal for automated processes like additive manufacturing and metal injection molding.
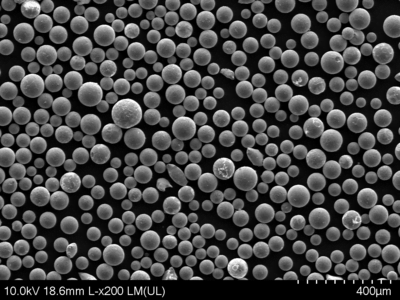
Nadelen van Gasverstuiver Apparatuur
While gas atomization offers a plethora of advantages, it’s important to consider its limitations:
- High Investment Costs: Gas atomizer equipment can be expensive to set up and maintain. This can be a barrier for smaller manufacturers or those entering new markets.
- Complexiteit van processen: Gas atomization is a complex process with several variables that need to be carefully controlled to ensure consistent powder quality. Expertise and experience are crucial for successful operation.
- Powder Safety Concerns: Metal powders can be flammable or explosive under certain conditions. Proper handling and storage procedures are essential to ensure operator safety.
- Beperkte materiaalkeuze: Not all metals are suitable for gas atomization. The process works best with materials that have good flow characteristics in the molten state.
- Potential for Internal Defects: Gas bubbles trapped within the molten metal during atomization can lead to internal voids or porosity in the powder particles. Careful process optimization is needed to minimize this risk.
Specificaties, maten, kwaliteiten en normen
The world of gas atomized powders is defined by a set of key specifications that influence their performance and suitability for specific applications:
Specificatie | Beschrijving |
---|---|
Particle Size Distribution (PSD): | This refers to the range of sizes present within the powder population. It is typically measured in micrometers (µm) and can be tailored for specific applications. |
Schijnbare Dichtheid: | This is the bulk density of the powder, measured in grams per cubic centimeter (g/cm³). It reflects how much powder can be packed into a given volume. |
Flowabiliteit: | This refers to the ease with which the powder flows. It is influenced by particle size, shape, and surface characteristics. |
Sfericiteit: | This describes how closely the powder particles resemble perfect spheres. Spherical particles generally offer better flowability and packing efficiency. |
Zuurstofgehalte: | The amount of oxygen present in the powder particles can affect their mechanical properties and oxidation resistance. |
Chemische samenstelling: | The specific elements and their proportions within the powder determine its overall properties. Gas atomization allows for precise control over chemical composition. |
Powder Grade: | Different grades of powder cater to varying application needs. Higher grades may involve tighter control over particle size, oxygen content, or chemical composition. |
Normen en voorschriften:
Several international standards govern the production and quality of gas-atomized powders. These standards ensure consistency, safety, and performance reliability. Some of the key standards include:
- ASTM International (ASTM): A widely recognized standards organization that publishes specifications for metal powders based on material type, particle size, and application.
- Specificaties luchtvaartmaterialen (AMS): A set of standards established by SAE International for aerospace materials, including metal powders for critical aerospace applications.
- Metal Powder Industries Federation (MPIF): A trade association that develops standards and guidelines for the metal powder industry.
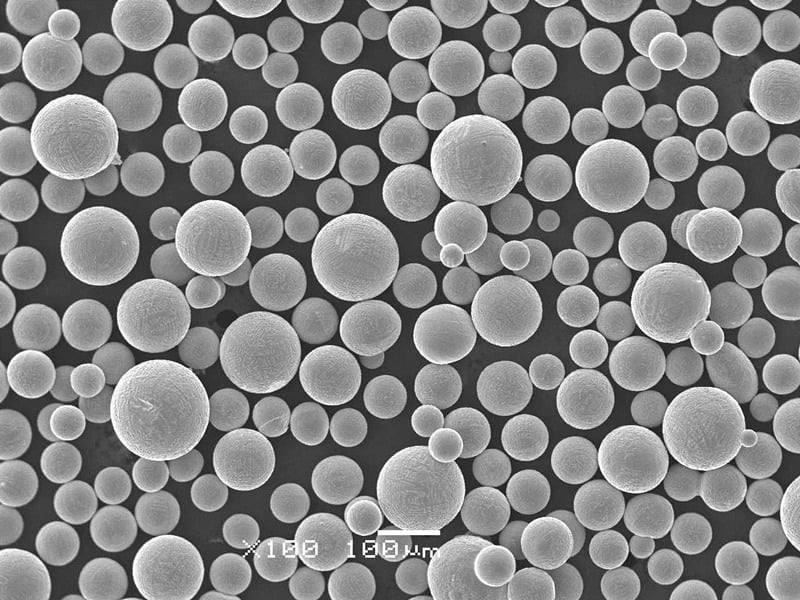
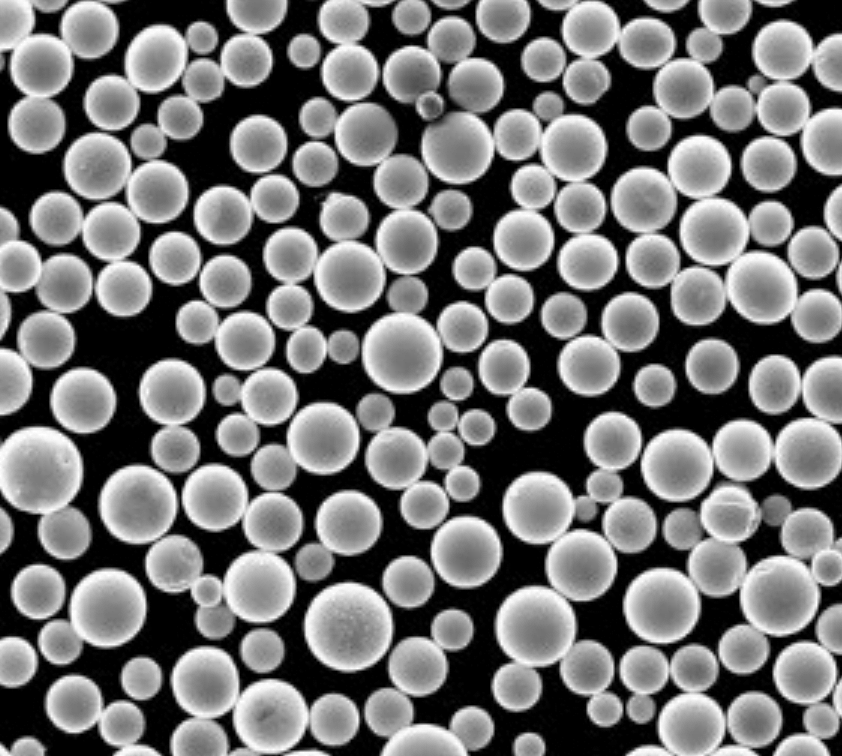
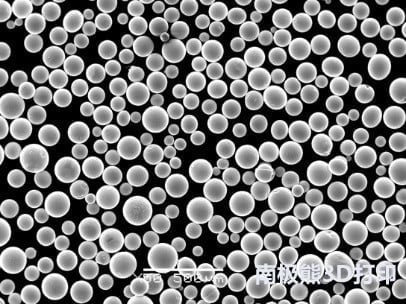
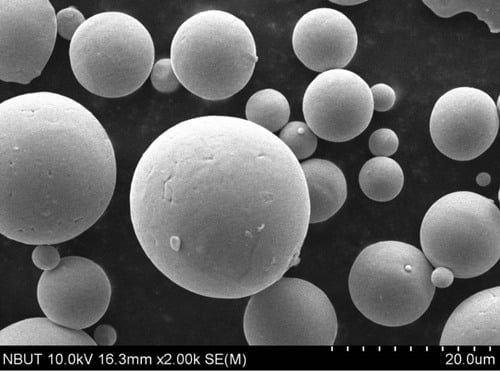
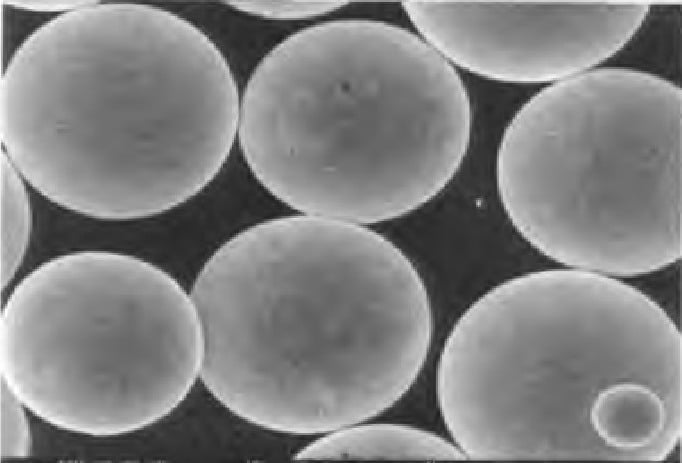
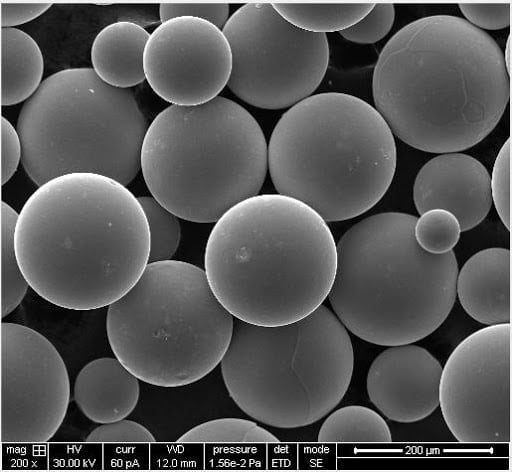
Leveranciers en prijzen
The global market for gas-atomized powders is vast and diverse. Here are some factors to consider when choosing a supplier:
- Material Availability: Ensure the supplier offers the specific metal powder you require in your desired grade and specifications.
- Reputation and Experience: Choose a supplier with a proven track record of producing high-quality gas-atomized powders.
- Prijzen en levertijden: Compare pricing structures and lead times from different suppliers to find the best fit for your budget and production schedule.
- Compliance with Standards: Ensure the supplier adheres to relevant industry standards for quality and safety.
A Look at Typical Pricing:
The cost of gas-atomized powders can vary significantly depending on several factors, including:
- Type materiaal: Exotic and high-performance metals like nickel superalloys and precious metals typically command a higher price compared to common metals like iron or aluminum.
- Powder Grade: Tighter control over particle size, chemical composition, and other parameters translates to a higher price for premium grade powders.
- Order Quantity: Bulk purchases often come with volume discounts compared to smaller orders.
Here’s a ballpark range for the cost of some commonly used gas-atomized powders (prices are subject to change and may vary depending on supplier):
- Titanium Powder (CP Ti): $10-30 per kilogram (kg)
- Stainless Steel Powders (316L, 17-4PH): $5-20 per kg
- Aluminum Powders (AlSi10Mg, AA2024): $3-10 per kg
- Nickel-based Superalloy Powders (Inconel 625, Inconel 718): $ 50-100 per kg
- Cobalt Chrome Powders (CoCrMo): $20-40 per kg
It’s important to note that these are just general ranges, and the actual price you pay will depend on the specific factors mentioned above.
Comparing Gas Atomization with Other Metal Powder Production Techniques
Gas atomization isn’t the only method for creating metal powders. Here’s a comparison with two other common techniques:
Metal Powder Production Technique | Voordelen | Nadelen |
---|---|---|
Gasverstuiving | High purity, spherical particles, good flowability, wide range of materials | High cost, complex process, potential for internal defects |
Verstuiven van water | Lower cost compared to gas atomization, suitable for some reactive metals | Irregular particle shapes, lower powder purity, limited material selection |
Elektrolytische afzetting | Ultrafine powders, good control over particle size and morphology | Slow production rate, limited material selection, high energy consumption |
The best choice for your specific application depends on factors like the desired powder properties, production volume requirements, and budget constraints.
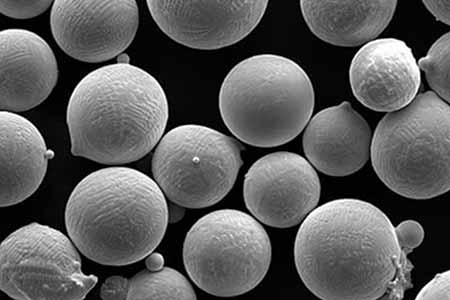
FAQ
Q: What are the safety considerations when working with gasverstuiverapparatuur?
A: Metal powders can be flammable or explosive under certain conditions. Proper ventilation, dust collection systems, and appropriate personal protective equipment (PPE) are crucial to ensure operator safety.
Q: Can gas atomization be used to create powders from any metal?
A: Not all metals are suitable for gas atomization. The process works best with materials that have good flow characteristics in the molten state. Refractory metals and some highly reactive metals may pose challenges.
Q: How does gas atomization compare to 3D printing directly from molten metal?
A: Both gas atomization and additive manufacturing using molten metal offer unique advantages. Gas atomization allows for the creation of a wider variety of metal powders with precise control over properties. These powders can then be used in various 3D printing technologies. Direct metal deposition (DMD) offers faster processing times but may be limited in material selection and may require stricter control over the printing environment.
Q: What is the future of gas atomization technology?
A: The future of gas atomization is bright. Advancements in automation and process control are expected to further improve powder quality and consistency. Additionally, research is ongoing to develop new atomization techniques for processing challenging materials and achieving even finer powder sizes. As the demand for lightweight, high-performance materials continues to grow, gas atomization is poised to play a key role in shaping the future of manufacturing.
Over 3DP mETAL
Productcategorie
NEEM CONTACT OP
Vragen? Stuur ons nu een bericht! Na ontvangst van uw bericht gaan we met een heel team uw aanvraag verwerken.