Imagine a world where complex objects are built layer by layer, with unparalleled design freedom and minimal waste. This is the reality of Laser Additive Manufacturing (LAM), a transformative technology rapidly reshaping various industries.
LAM, also known as 3D printing metals, utilizes a focused laser beam to melt and fuse together metal powder particles, meticulously building a 3D object from a digital blueprint. This revolutionary process offers a plethora of advantages over traditional subtractive manufacturing methods like machining, making it a highly sought-after technology for various applications.
the Power of Metal Powders in LAM
The foundation of LAM lies in the meticulously crafted metal powders used. These powders, with their unique properties and characteristics, significantly influence the final product’s quality and performance. Here’s a closer look at some of the most commonly used metal powders in LAM:
Metal Powders for LAM
Metaalpoeder | Beschrijving | Eigenschappen | TOEPASSINGEN |
---|---|---|---|
Titanium (Ti) | Lightweight, high strength-to-weight ratio, excellent corrosion resistance | Biocompatible, good for high-temperature applications | Aerospace components, biomedical implants, dental prosthetics |
Roestvrij staal (SS) | Various grades available, offering a balance of strength, corrosion resistance, and affordability | Workhorse material for LAM, readily available | General-purpose components, automotive parts, medical devices |
Aluminium (Al) | Lightweight, good machinability, high heat conductivity | Offers excellent weight savings | Aerospace components, heat sinks, automotive parts |
Inconel (Nickel-Chromium Superalloy) | Exceptional high-temperature performance, excellent resistance to oxidation and corrosion | Ideal for extreme environments | Turbine blades, rocket engine components, heat exchangers |
Cobalt Chrome (CoCr) | High strength, wear resistance, biocompatible | Popular choice for biomedical implants | Joint replacements, dental implants |
Gereedschapsstaal | Wide range of grades, offering varying combinations of hardness, toughness, and wear resistance | Used to create custom tools and dies | Cutting tools, punches, dies, molds |
Koper (Cu) | Uitstekende elektrische en thermische geleidbaarheid | Used for applications requiring high heat dissipation | Heat sinks, electrical components, busbars |
Niobium (Nb) | High melting point, good superconductivity properties | Emerging material for specialized applications | Superconducting magnets, nuclear reactor components |
Tantalum (Ta) | Hoog smeltpunt, uitstekende corrosiebestendigheid | Used in demanding environments | Chemical processing equipment, medical implants |
Molybdeen (Mo) | High melting point, good strength at high temperatures | Used for applications requiring high-temperature strength | Missile components, furnace parts |
This table provides a glimpse into the diverse range of metal powders used in LAM. Each powder offers unique properties that cater to specific application needs. When choosing a metal powder, factors like the desired mechanical properties, corrosion resistance, weight, and printability are crucial considerations.
For instance, when creating lightweight aerospace components, Aluminum might be the preferred choice due to its excellent strength-to-weight ratio. Conversely, for applications requiring high-temperature resistance, Inconel would be a more suitable option due to its exceptional performance at elevated temperatures.
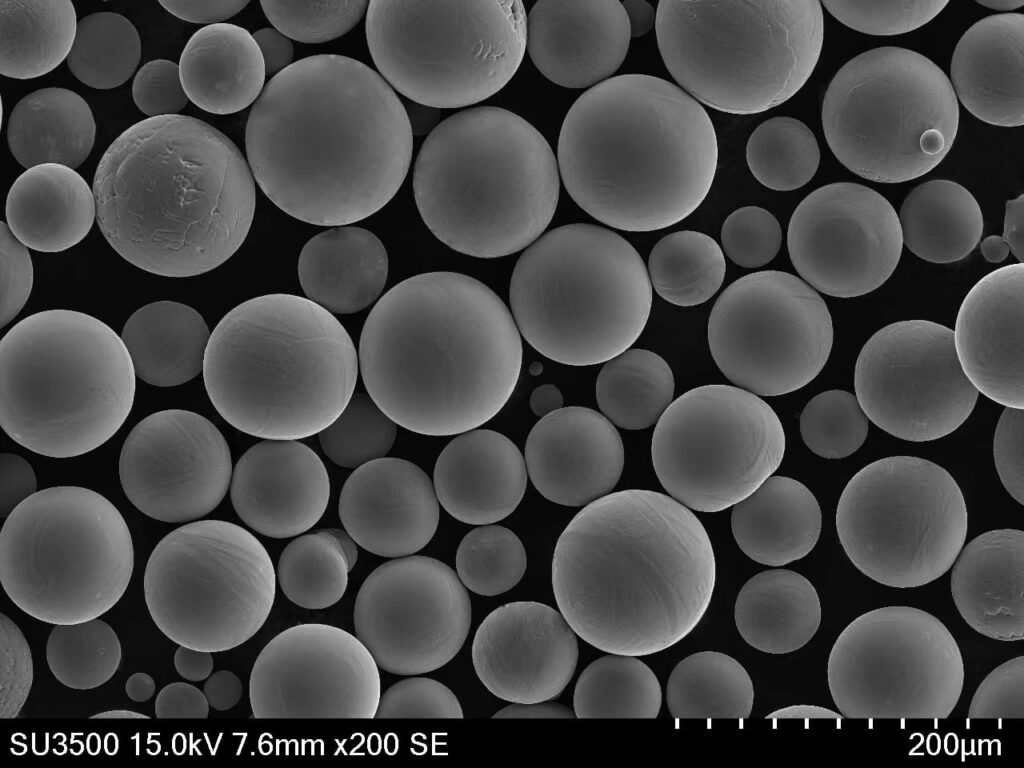
Toepassingen van LAM
LAM’s versatility extends across various industries, enabling the creation of complex and innovative components. Here are some prominent applications of LAM:
Applications of LAM
Industrie | Voorbeelden | Voordelen |
---|---|---|
Lucht- en ruimtevaart | Lightweight aircraft components, fuel nozzles, rocket engine parts | Weight reduction, improved fuel efficiency, design freedom for complex geometries |
Automobielen | Custom pistons, gear components, lightweight brackets | Performance optimization, weight reduction, rapid prototyping for new designs |
Medisch | Biocompatible implants (knee, hip), dental prosthetics, customized surgical instruments | Personalized medical devices, improved patient outcomes, complex lattice structures for bone ingrowth |
Consumptiegoederen | Jewelry, customized sporting goods, high-performance bicycle frames | Design freedom for intricate details, lightweight and durable products, mass customization |
Gereedschappen | Conformal cooling channels in molds, custom jigs and fixtures | Improved cooling efficiency, reduced production lead times, complex geometries for specialized applications |
The impact of LAM is evident across these diverse industries. From creating lightweight and high-performance aerospace components to personalized medical implants that improve patient outcomes, LAM is pushing the boundaries of what’s possible.
the Advantages of LAM
LAM offers a compelling set of advantages compared to traditional manufacturing methods:
Advantages of LAM
Voordeel | Beschrijving | Voordeel |
---|---|---|
Ontwerpvrijheid | LAM allows for the creation of complex geometries previously impossible with traditional techniques. Internal channels, intricate lattice structures, and undercuts can be readily incorporated into the design. | This opens doors for lighter, more efficient components, improved heat dissipation, and bone ingrowth in medical implants. |
Minimaal afval | Unlike subtractive manufacturing, LAM utilizes a near-net-shape approach, minimizing material waste. Only the necessary material is melted and fused, resulting in significant resource conservation. | This translates to cost savings, reduced environmental impact, and efficient use of often-precious materials. |
Mass Customization | LAM excels at producing customized parts with minimal additional setup costs. This enables the creation of personalized medical devices, unique sporting goods, and even custom jewelry. | This caters to the growing demand for individualized products and shortens production lead times for low-volume applications. |
Rapid Prototyping | LAM facilitates rapid prototyping, allowing designers to create functional prototypes quickly and iterate on designs efficiently. This significantly reduces development time and costs compared to traditional methods. | This fosters innovation and allows for faster product development cycles, bringing products to market quicker. |
Inventory Reduction | LAM’s ability to produce on-demand reduces the need for extensive inventory storage. This optimizes space utilization and reduces the risk of obsolescence for spare parts. | This translates to improved cash flow and reduced overhead costs associated with warehousing and managing large inventories. |
These advantages make LAM a highly attractive option for various industries seeking to streamline their manufacturing processes, reduce waste, and create innovative products.
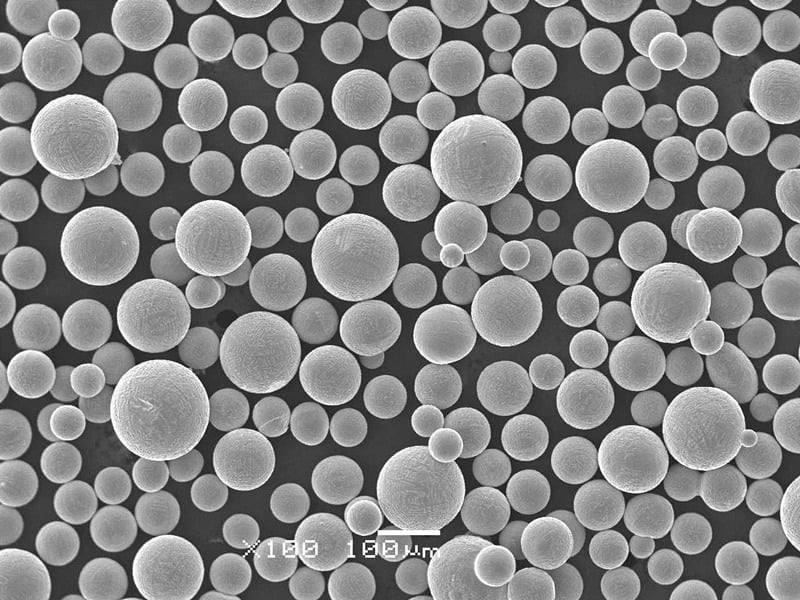
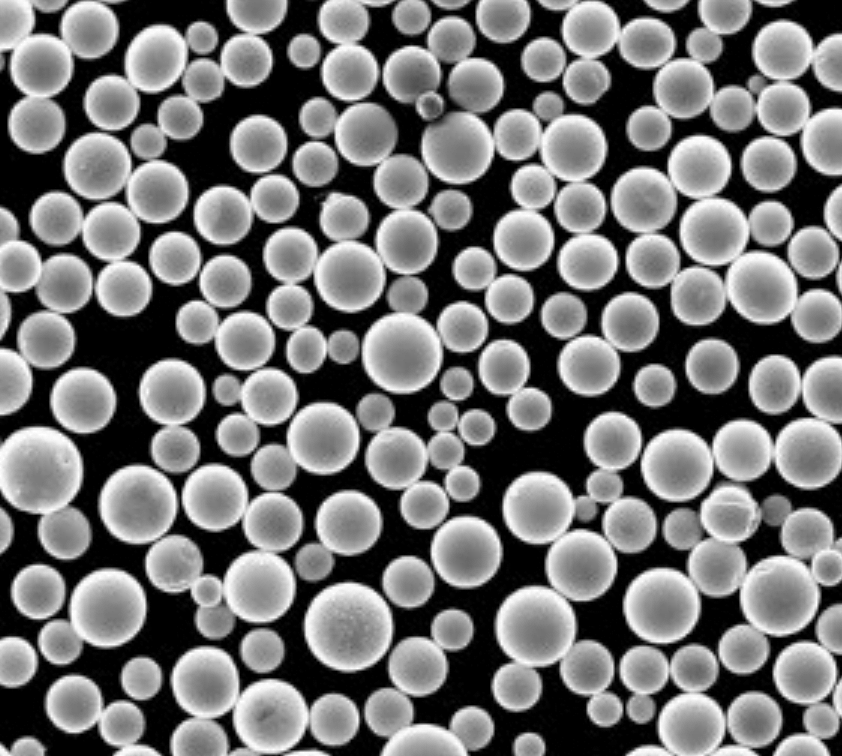
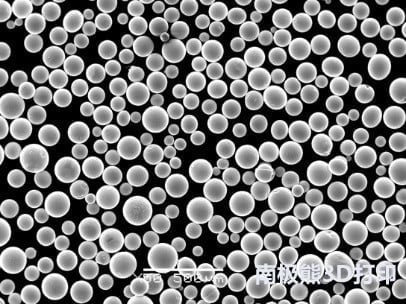
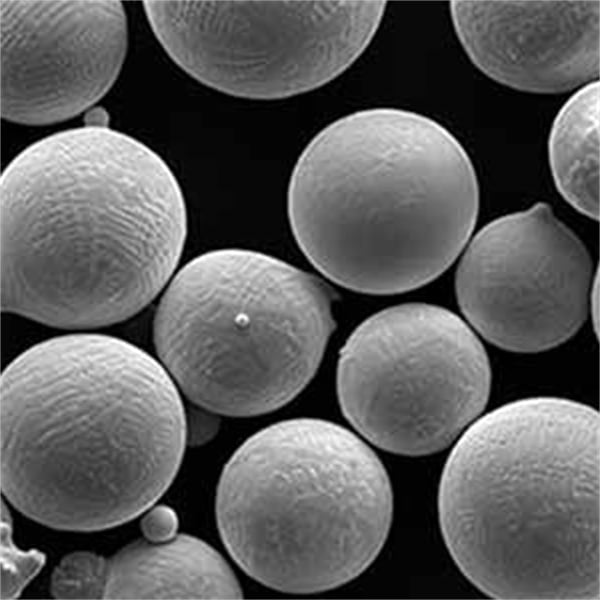
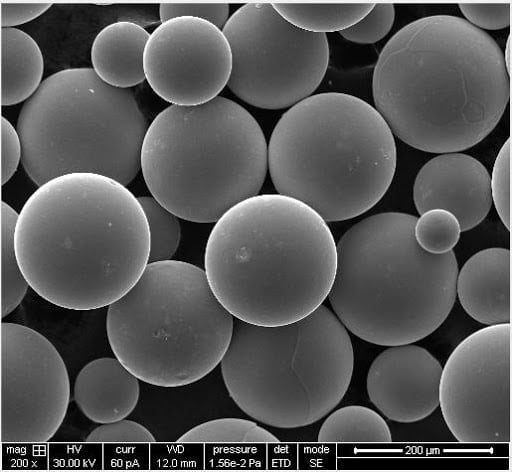
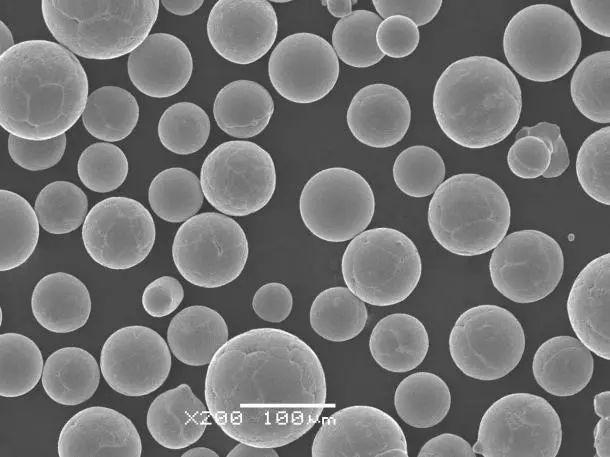
the Limitations of LAM (Disadvantages)
While LAM offers significant advantages, it’s essential to acknowledge its limitations:
Disadvantages of LAM
Nadeel | Beschrijving | Consideration |
---|---|---|
Machine and Material Costs | LAM machines can be expensive, and some metal powders are priced higher than their wrought counterparts. | This can be a barrier to entry for smaller companies, and careful cost analysis is crucial. |
Bouwsnelheid | Compared to traditional high-volume manufacturing techniques, LAM can be slower, especially for larger components. | This may not be suitable for mass production applications requiring high throughput. |
Afwerking oppervlak | LAM-produced parts may require additional post-processing steps to achieve desired surface finishes. | The level of surface roughness can impact certain applications and needs to be factored into the overall production process. |
Beperkte materiaalselectie | While the range of metal powders for LAM is expanding, it’s still not as vast as wrought materials available in traditional manufacturing. | This may limit the applicability of LAM for certain specialized applications requiring specific material properties. |
Process Qualification | For critical applications like aerospace and medical implants, stringent quality control and process qualification procedures are necessary. | This can add complexity and cost to the LAM process. |
Despite these limitations, LAM technology is continuously evolving. Machine costs are decreasing, build speeds are improving, and the availability of metal powders is expanding. As LAM matures, these limitations are expected to diminish, further solidifying its position as a transformative manufacturing technology.
Weighing the Pros and Cons: Is LAM Right for You?
The decision to adopt LAM depends on your specific needs and priorities. Here are some key factors to consider:
- Complexity of the design: If your design is intricate or requires internal channels, LAM might be the perfect solution.
- Productievolume: For high-volume production, traditional methods might be more cost-effective.
- Materiaalvereisten: Ensure the desired metal powder is available for your application.
- Budgetary constraints: Consider the upfront cost of LAM machines and metal powders.
- Lead time requirements: LAM excels at rapid prototyping but may not be ideal for high-volume, fast-turnaround production.
By carefully evaluating these factors, you can determine if LAM is the right fit for your manufacturing needs.
De toekomst van LAM
LAM is rapidly transforming the manufacturing landscape, ushering in an era of design freedom, resource efficiency, and mass customization. As the technology matures, we can expect to see:
- Reduced Machine Costs: Advancements in LAM technology are expected to bring down machine costs, making it more accessible to a wider range of manufacturers.
- Uitgebreide materiaalselectie: The availability of metal powders for LAM is continuously expanding, opening doors for new applications in various industries.
- Increased Build Speeds: Research and development efforts are focused on increasing build speeds, making LAM more viable for high-volume production.
- Verbeterde oppervlakteafwerkingen: Advancements in LAM processes and post-processing techniques will be instrumental in achieving smoother surface finishes, reducing the need for extensive post-processing steps.
- Standardization of Processes: As LAM adoption increases, expect to see standardization of processes and certifications, ensuring consistent quality and repeatability.
These advancements will further propel LAM’s adoption across diverse industries. Imagine a future where complex aerospace components are built on-demand, customized medical implants perfectly match a patient’s anatomy, and innovative consumer goods are produced with intricate details and lightweight designs. This is the future that LAM promises, a future where imagination becomes reality, layer by layer.
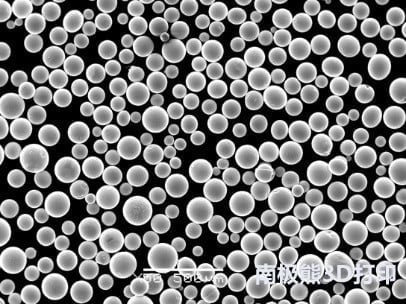
FAQ
Q: What is the difference between LAM and 3D printing?
A: LAM is a specific type of 3D printing that utilizes metal powders to create parts. 3D printing encompasses a broader range of technologies that can utilize various materials like plastics, polymers, and even ceramics.
Q: Is LAM safe?
A: LAM processes can involve high temperatures and metal fumes. However, proper safety protocols and ventilation systems minimize risks.
Q: How strong are LAM-produced parts?
A: The strength of LAM parts depends on the specific metal powder used and the build parameters. LAM parts can achieve strength comparable to traditionally manufactured parts.
Q: What are some of the environmental benefits of LAM?
A: LAM’s minimal waste approach and ability to produce parts on-demand contribute to a more sustainable manufacturing process. Reduced material consumption and lower energy requirements compared to traditional methods further enhance its environmental benefits.
Q: Where can I learn more about LAM?
A: Several resources are available to learn more about LAM, including industry associations, research institutions, and online publications dedicated to additive manufacturing.
Over 3DP mETAL
Productcategorie
NEEM CONTACT OP
Vragen? Stuur ons nu een bericht! Na ontvangst van uw bericht gaan we met een heel team uw aanvraag verwerken.