Additive manufacturing brengt een revolutie teweeg in de productiewereld door het mogelijk te maken om complexe, zeer gedetailleerde onderdelen direct vanuit digitale ontwerpen te maken. Onder de verschillende additieve productietechnieken, Laserpoederbedfusie (LPBF) is een van de populairste methoden geworden, vooral bij de productie van metalen onderdelen. Maar wat is LPBF precies en hoe werkt het? In deze uitgebreide gids duiken we diep in de wereld van LPBF en onderzoeken we het proces, de materialen, de toepassingen, de voordelen en de beperkingen. We nemen ook specifieke metaalpoeders die worden gebruikt in LPBF onder de loep en vergelijken ze aan de hand van verschillende parameters.
Overzicht van laser poederbedfusie (LPBF)
Laser Powder Bed Fusion is een geavanceerd additief fabricageproces waarbij een krachtige laser wordt gebruikt om fijne metaalpoederdeeltjes laag voor laag selectief samen te smelten tot een massief, driedimensionaal object. Deze technologie maakt deel uit van een bredere categorie van additieve productieprocessen die bekend staat als poederbedfusie (PBF), waartoe ook elektronenbundelsmelten (EBM) en selectief lasersinteren (SLS) behoren. LPBF is echter uniek in zijn vermogen om metalen onderdelen met hoge resolutie te produceren, met ingewikkelde geometrieën en superieure mechanische eigenschappen.
LPBF wordt veel gebruikt in verschillende industrieën, zoals lucht- en ruimtevaart, auto's, medische en industriële productie, waar precisie, sterkte en materiaalefficiëntie van het grootste belang zijn. Deze techniek maakt de productie mogelijk van complexe metalen onderdelen die onmogelijk of onbetaalbaar zouden zijn om te maken met traditionele methoden zoals machinaal bewerken of gieten.
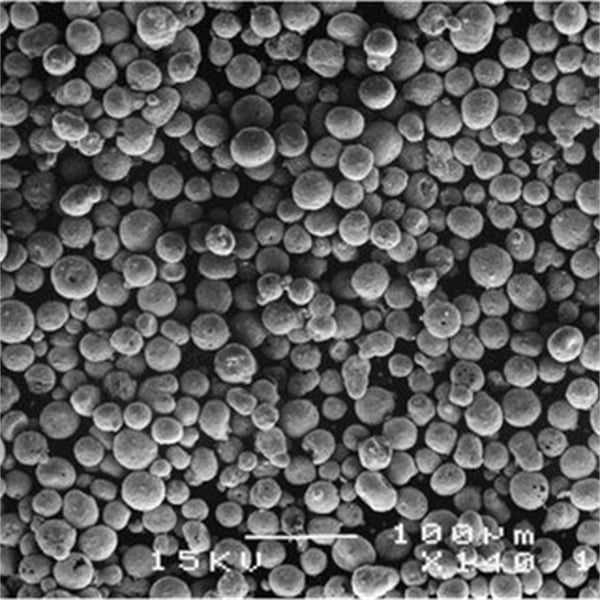
Hoe laser poederbedfusie werkt
LPBF omvat verschillende belangrijke stappen, van ontwerp tot eindproduct. Hier volgt een overzicht van het proces:
- Digitaal ontwerp: Het proces begint met het maken van een digitaal 3D-model met behulp van computerondersteunde ontwerpsoftware (CAD). Dit model dient als blauwdruk voor het te vervaardigen object.
- Poeder strooien: Een dunne laag metaalpoeder, meestal 20 tot 100 micron dik, wordt gelijkmatig over het bouwplatform verspreid. Het poeder wordt in een reservoir bewaard en verspreid met een overspuitmes of roller.
- Laserscannen: Een krachtige laserstraal versmelt de poederdeeltjes selectief volgens het digitale ontwerp. De laser wordt geleid door een set spiegels, bekend als galvos, die de beweging van de laser over het poederbed nauwkeurig regelen.
- Laag voor laag bouwen: Nadat een laag gesmolten is, zakt het bouwplatform met de dikte van een laag en wordt er een nieuwe laag poeder verspreid. De laser versmelt dan de nieuwe laag en hecht deze aan de vorige. Dit proces herhaalt zich totdat het hele object gebouwd is.
- Nabewerking: Als de opbouw voltooid is, wordt het overtollige poeder verwijderd en wordt het onderdeel onderworpen aan verschillende nabewerkingsstappen, zoals warmtebehandeling, machinale bewerking of oppervlakteafwerking, om de gewenste eigenschappen en oppervlaktekwaliteit te verkrijgen.
- Eindinspectie: Het afgewerkte onderdeel ondergaat grondige inspecties en testen om er zeker van te zijn dat het voldoet aan de vereiste specificaties en kwaliteitsnormen.
Belangrijkste voordelen van Laserpoederbedfusie
LPBF biedt verschillende voordelen ten opzichte van traditionele productiemethoden en andere additieve productietechnieken:
- Ontwerpflexibiliteit: Met LPBF kunnen zeer complexe geometrieën worden gemaakt die met conventionele methoden onmogelijk te maken zijn. Dit omvat interne structuren, roosters en ingewikkelde details die kunnen worden geoptimaliseerd voor gewicht, sterkte en functionaliteit.
- Materiaalefficiëntie: Omdat LPBF een additief proces is, wordt alleen het materiaal gebruikt dat nodig is om het onderdeel te maken, wat resulteert in minimaal afval. Dit in tegenstelling tot subtractieve methodes zoals machinale bewerking, waarbij materiaal wordt verwijderd uit een groter blok, wat vaak resulteert in aanzienlijk afval.
- Hoogprecisie: LPBF kan onderdelen produceren met extreem nauwe toleranties en fijne details, waardoor het ideaal is voor toepassingen waar precisie essentieel is.
- Rapid Prototyping: LPBF maakt een snelle productie van prototypes mogelijk, waardoor het ontwerp sneller kan worden aangepast en nieuwe producten sneller op de markt kunnen worden gebracht.
- Sterke, functionele onderdelen: LPBF produceert onderdelen met mechanische eigenschappen die vergelijkbaar zijn met die van traditionele productiemethoden. Dit maakt het geschikt voor de productie van functionele onderdelen voor eindgebruik, niet alleen prototypes.
Samenstelling van metaalpoeders gebruikt in laser poederbedfusie
De kwaliteit en samenstelling van het metaalpoeder dat gebruikt wordt in LPBF zijn cruciaal voor het succes van het proces en de eigenschappen van het uiteindelijke onderdeel. Hieronder bespreken we enkele van de meest gebruikte metaalpoeders in LPBF, samen met hun specifieke samenstellingen en eigenschappen.
Metaalpoeder | Compositie | Eigenschappen | TOEPASSINGEN |
---|---|---|---|
316L roestvrij staal | Fe, Cr (16-18%), Ni (10-14%), Mo (2-3%) | Hoge corrosiebestendigheid, goede mechanische eigenschappen, lasbaar | Medische implantaten, voedselverwerkende apparatuur, onderdelen voor de scheepvaart |
AlSi10Mg | Al (balans), Si (9-11%), Mg (0,2-0,5%) | Hoge sterkte-gewichtsverhouding, goede thermische geleidbaarheid | Ruimtevaartonderdelen, auto-onderdelen, warmtewisselaars |
Inconel 718 | Ni (50-55%), Cr (17-21%), Fe (balans) | Bestand tegen hoge temperaturen, uitstekende sterkte en corrosiebestendigheid | Gasturbines, ruimtevaartonderdelen, kernreactoren |
Ti6Al4V | Ti (90%), Al (6%), V (4%) | Hoge sterkte-gewichtsverhouding, uitstekende biocompatibiliteit | Medische implantaten, onderdelen voor de ruimtevaart, hoogwaardige auto-onderdelen |
Maragingstaal (1.2709) | Fe, Ni (18-19%), Co (8,5-9,5%), Mo (4,5-5,2%), Ti (0,6-0,8%) | Hoge sterkte, taaiheid, gemakkelijk te bewerken | Gereedschappen, luchtvaartonderdelen, onderdelen met hoge sterkte |
Kobalt-chroom (CoCr) | Co (balans), Cr (27-30%), Mo (5-7%) | Hoge slijtage- en corrosiebestendigheid, biocompatibel | Tandheelkundige implantaten, medische hulpmiddelen, turbineschoepen |
Hastelloy X | Ni (47%), Cr (22%), Mo (9%), Fe (18%) | Uitstekende sterkte bij hoge temperaturen, corrosiebestendigheid | Ruimtevaart, chemische verwerking, gasturbines |
Koper (Cu) | Cu (99,9%) | Hoge thermische en elektrische geleidbaarheid | Elektrische componenten, warmtewisselaars, inductoren |
Aluminium 6061 | Al (97,9-99%), Mg (0,8-1,2%), Si (0,4-0,8%) | Hoge sterkte-gewichtsverhouding, goede corrosiebestendigheid | Constructiedelen, auto-onderdelen, lucht- en ruimtevaart |
Gereedschapsstaal (H13) | Fe, Cr (4,75-5,5%), Mo (1,1-1,75%), V (0,8-1,2%) | Hoge hardheid, slijtvastheid, taaiheid | Gereedschappen, mallen, matrijzen, onderdelen met hoge sterkte |
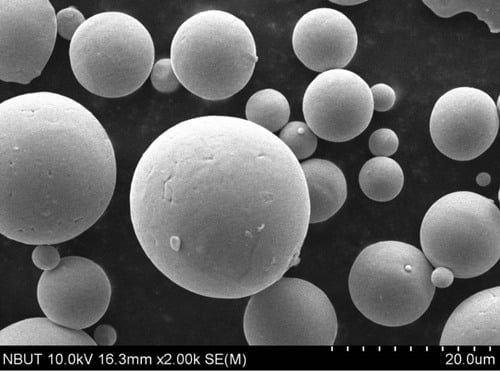
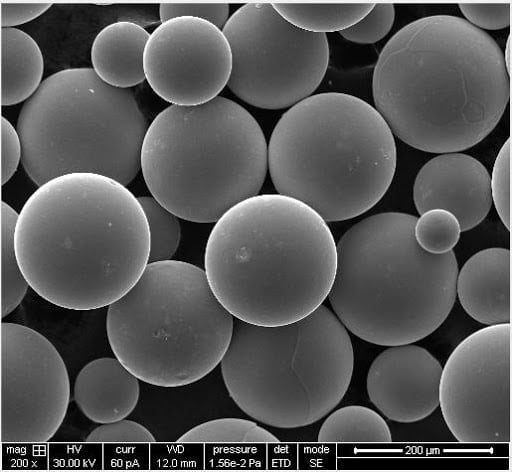
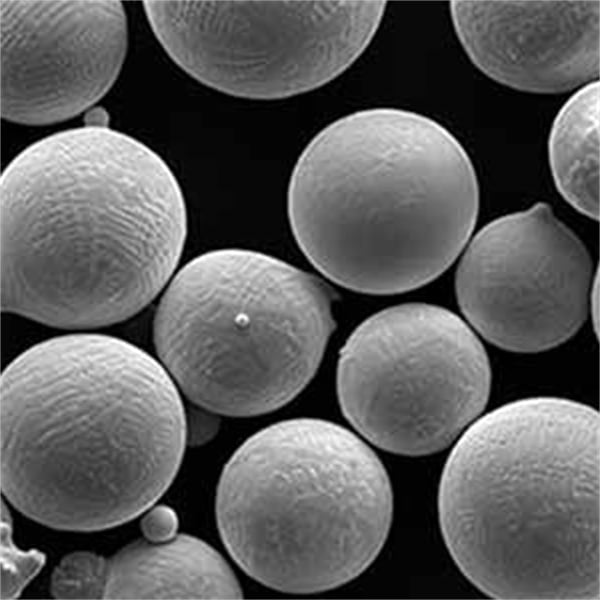
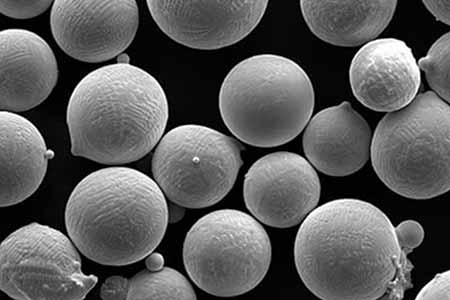
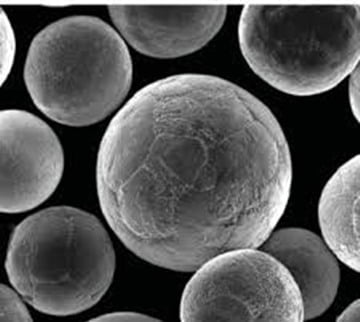
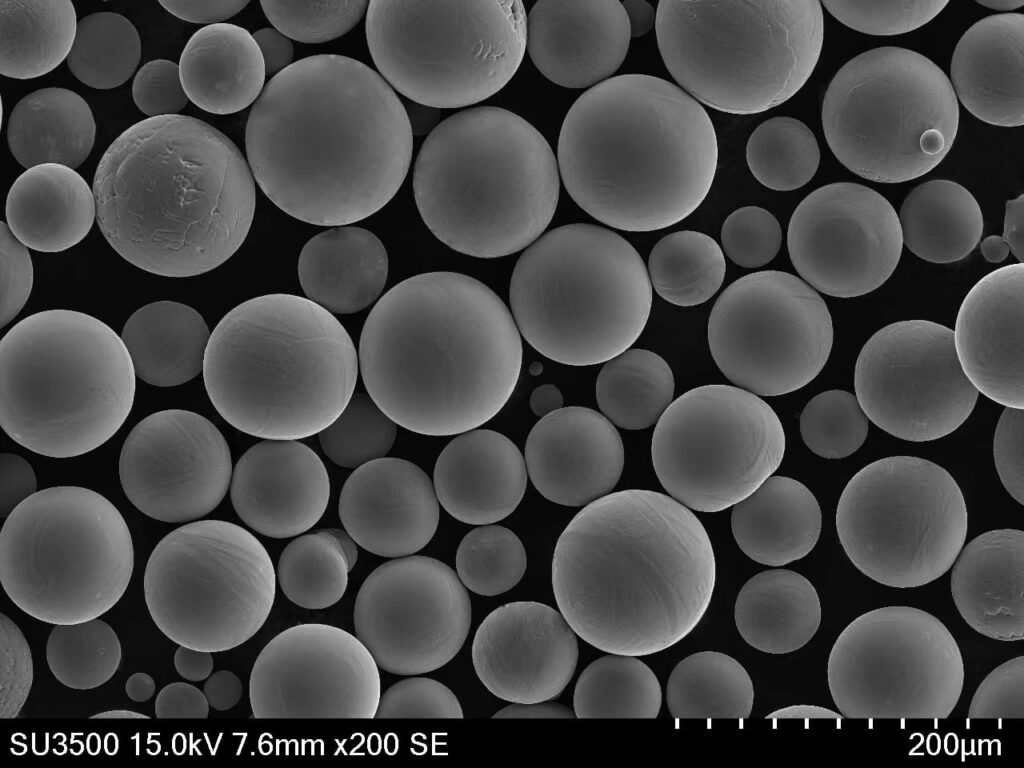
Kenmerken van laserpoederbedfusiematerialen
Bij het selecteren van een metaalpoeder voor LPBF is het essentieel om te kijken naar de eigenschappen van het materiaal en hoe deze overeenkomen met de vereisten van de toepassing. Hier zijn enkele kritieke eigenschappen waarmee rekening moet worden gehouden:
- Particle size distribution: De grootte en verdeling van poederdeeltjes hebben een grote invloed op de vloeibaarheid en verpakkingsdichtheid van het poeder, wat op zijn beurt de kwaliteit van het uiteindelijke onderdeel beïnvloedt. Over het algemeen wordt de voorkeur gegeven aan een smalle deeltjesgrootteverdeling voor een consistente laagafzetting en optimale dichtheid van de deeltjes.
- Morfologie: De vorm van de poederdeeltjes (bv. bolvormig, onregelmatig) beïnvloedt de vloeibaarheid en verpakkingsdichtheid van het poeder. Bolvormige deeltjes hebben over het algemeen de voorkeur in LPBF omdat ze beter vloeien en dichter zijn, wat leidt tot onderdelen van hogere kwaliteit.
- Chemische samenstelling: De chemische samenstelling van het poeder heeft een directe invloed op de mechanische eigenschappen, corrosiebestendigheid en andere prestatiekenmerken van het uiteindelijke onderdeel. Het is cruciaal om poeders te gebruiken met een consistente en gecontroleerde samenstelling om de gewenste materiaaleigenschappen te bereiken.
- Zuiverheid: Poeders met een hoge zuiverheid zijn essentieel voor het produceren van onderdelen met consistente mechanische eigenschappen en het minimaliseren van het risico op defecten. Onzuiverheden kunnen leiden tot problemen zoals porositeit, slechte mechanische prestaties en verminderde corrosiebestendigheid.
- Flowbaarheid: Het vermogen van het poeder om soepel en gelijkmatig te vloeien tijdens het overspuiten is essentieel voor het verkrijgen van een uniforme laagdikte en hoogwaardige werkstukken. Een slechte vloeibaarheid kan leiden tot inconsistente lagen, defecten en een verminderde kwaliteit van de onderdelen.
- Reactiviteit: Sommige metaalpoeders, vooral die met aluminium, titanium of magnesium, zijn zeer reactief en moeten voorzichtig worden behandeld en opgeslagen om oxidatie of verontreiniging te voorkomen. Tijdens het LPBF-proces wordt vaak een omgeving met inert gas gebruikt om deze risico's te beperken.
Toepassingen van laser poederbedfusie
LPBF is een veelzijdige technologie die toepassingen vindt in een groot aantal industrieën. Hier zijn enkele van de belangrijkste toepassingen waar LPBF een significante impact heeft:
Industrie | Applicatie | Details |
---|---|---|
Lucht- en ruimtevaart | Turbinebladen, structurele onderdelen | Hoge-temperatuurlegeringen zoals Inconel 718 en Hastelloy X worden gebruikt vanwege hun sterkte en hittebestendigheid. |
Automobielen | Motoronderdelen, lichtgewicht constructies | Aluminiumlegeringen en titanium worden gebruikt om gewicht te verminderen met behoud van sterkte |
Medisch | Implantaten, chirurgische instrumenten | Biocompatibele materialen zoals Ti6Al4V en kobalt-chroom worden gebruikt vanwege hun sterkte en compatibiliteit. |
Tandheelkundig | Kronen, bruggen, tandheelkundige implantaten | Kobaltchroom en titanium worden vaak gebruikt vanwege hun biocompatibiliteit en sterkte. |
Gereedschappen | Mallen, matrijzen, snijgereedschappen | Gereedschapsstalen zoals H13 en Maragingstaal worden gebruikt vanwege hun hardheid en slijtvastheid. |
Energie | Warmtewisselaars, turbineonderdelen | Superlegeringen op basis van koper en nikkel worden gebruikt voor hun thermische geleidbaarheid en prestaties bij hoge temperaturen. |
Sieraden | Aangepaste ontwerpen, ingewikkelde details | Edele metalen zoals goud en zilver kunnen worden gebruikt om unieke, gedetailleerde stukken te maken. |
Elektronica | Koellichamen, connectoren, spoelen | Koper- en aluminiumlegeringen worden gebruikt vanwege hun uitstekende thermische en elektrische geleidbaarheid |
Verdediging | Lichtgewicht pantser, gespecialiseerde onderdelen | Zeer sterke materialen zoals titanium en Inconel worden gebruikt vanwege hun duurzaamheid en gewichtsbesparing. |
Onderzoek en ontwikkeling | Prototyping, testen van materialen | Er worden verschillende materialen gebruikt om nieuwe toepassingen te verkennen en de grenzen te verleggen van wat LPBF kan bereiken. |
Voordelen en beperkingen van Laserpoederbedfusie
Hoewel LPBF talloze voordelen biedt, heeft het ook zijn beperkingen. Inzicht in deze voor- en nadelen is essentieel bij de beslissing of LPBF de juiste technologie is voor een bepaalde toepassing.
Voordelen | Beperkingen |
---|---|
Ontwerpvrijheid: Mogelijkheid om complexe, ingewikkelde geometrieën te creëren die onmogelijk zijn met traditionele methoden | Kosten: Hoge initiële investering in apparatuur en materialen |
Materiaalefficiëntie: Minimaal afval dankzij de additieve aard van het proces | Beperkingen in bouwgrootte: Beperkt door de grootte van de bouwkamer |
Hoogprecisie: In staat om onderdelen met nauwe toleranties en fijne details te produceren | Vereisten voor nabewerking: Onderdelen vereisen vaak extra nabewerking |
Sterke functionele onderdelen: Mechanische eigenschappen vergelijkbaar met traditioneel vervaardigde onderdelen | Beperkte materiaalopties: Niet alle materialen zijn geschikt voor LPBF |
Rapid Prototyping: Snelle doorlooptijd van ontwerp tot afgewerkt onderdeel | Afwerking oppervlak: Voor onderdelen kan oppervlakteafwerking nodig zijn om de gewenste kwaliteit te bereiken |
Aanpassing: Mogelijkheid om aangepaste, eenmalige onderdelen economisch te produceren | Behandeling van poeder: Vereist zorgvuldige behandeling en opslag van metaalpoeders vanwege reactiviteit en veiligheidsproblemen |
Specificaties, maten, kwaliteiten en normen voor LPBF-materialen
Wanneer u met LPBF werkt, is het essentieel om de specificaties, afmetingen, kwaliteiten en normen te begrijpen die van toepassing zijn op de materialen die in het proces worden gebruikt. Hier volgt een overzicht van enkele van de belangrijkste overwegingen:
Materiaal | Groottebereik (micron) | Algemene cijfers | Standaarden |
---|---|---|---|
316L roestvrij staal | 15-45, 45-105 | ASTM A240, A276, A312 | ASTM F3184, ISO 5832-1 |
AlSi10Mg | 20-63, 45-105 | EN AW-6082, EN AW-5083 | DIN EN 1706, ISO 3522 |
Inconel 718 | 15-45, 45-105 | AMS 5662, AMS 5663 | ASTM F3055, ISO 15156 |
Ti6Al4V | 15-45, 45-105 | ASTM B348, ASTM F136 | ASTM F2924, ISO 5832-3 |
Maragingstaal (1.2709) | 15-45, 45-105 | DIN 1.2709, AMS 6514 | ASTM A579, ISO 4957 |
Kobalt-chroom (CoCr) | 15-45, 45-105 | ASTM F75, F1537 | ASTM F2924, ISO 5832-4 |
Hastelloy X | 15-45, 45-105 | AMS 5754, AMS 5536 | ASTM B435, ASTM B572 |
Koper (Cu) | 15-45, 45-105 | C11000, C10100 | ASTM B170, ASTM B152 |
Aluminium 6061 | 15-45, 45-105 | ASTM B221, ASTM B308 | ASTM F3318, ISO 3522 |
Gereedschapsstaal (H13) | 15-45, 45-105 | ASTM A681, JIS SKD61 | ASTM A681, ISO 4957 |
Leveranciers en prijsinformatie voor LPBF metaalpoeders
Het vinden van betrouwbare leveranciers en het begrijpen van de prijsstructuur voor LPBF metaalpoeders is cruciaal voor planning en budgettering. Hier volgt een overzicht van enkele bekende leveranciers en de prijsklasse voor verschillende soorten metaalpoeders:
Provider | Metaalpoeder | Prijsklasse (per kg) | Details |
---|---|---|---|
Höganäs | Roestvrij staal, gereedschapsstaal, titanium | $80 – $200 | Biedt een breed assortiment metaalpoeders voor LPBF |
Carpenter Additive | Nikkellegeringen, roestvrij staal, titanium | $100 – $250 | Bekend om hoogwaardige poeders voor de ruimtevaart |
Sandvik Additive Manufacturing | Roestvrij staal, titanium, kobalt-chroom | $90 – $230 | Levert metaalpoeders geoptimaliseerd voor additieve productie |
GKN additief | Roestvrij staal, aluminium, gereedschapsstaal | $70 – $180 | Biedt metaalpoeders op maat voor LPBF-toepassingen |
LPW Technologie (Timmerman) | Inconel, Maragingstaal, Aluminium | $110 – $300 | Gespecialiseerd in hoogwaardige poeders voor kritische toepassingen |
AP&C (GE additief) | Titaan, aluminium, nikkellegeringen | $120 – $350 | Hoogwaardige poeders met focus op ruimtevaart en medische toepassingen |
Tekna | Titaan, aluminium, nikkellegeringen | $100 – $320 | Geavanceerde poeders met gecontroleerde deeltjesgrootte |
EOS | Divers (Nikkel, Aluminium, Roestvrij staal) | $90 – $250 | Biedt een verscheidenheid aan metaalpoeders die speciaal zijn ontworpen voor EOS-machines |
Renishaw | Roestvrij staal, titanium, inconel | $100 – $270 | Bekend om consistente poeders van hoge kwaliteit |
Aubert & Duval | Titanium, aluminium, gereedschapsstaal | $110 – $300 | Gespecialiseerd in metaalpoeders voor toepassingen onder hoge druk |
De voor- en nadelen van verschillende metaalpoeders voor LPBF vergelijken
Bij het kiezen van een metaalpoeder voor LPBF is het essentieel om de voor- en nadelen van elke optie af te wegen. Hieronder vindt u een vergelijkende tabel met de voordelen en beperkingen van enkele van de meest gebruikte metaalpoeders:
Metaalpoeder | Voordelen | Beperkingen |
---|---|---|
316L roestvrij staal | Uitstekende corrosiebestendigheid, goede mechanische eigenschappen, gemakkelijk te lassen | Relatief lagere sterkte in vergelijking met andere legeringen |
AlSi10Mg | Hoge sterkte-gewichtsverhouding, goede thermische geleidbaarheid, lichtgewicht | Lagere corrosiebestendigheid in vergelijking met roestvrij staal |
Inconel 718 | Bestand tegen hoge temperaturen, uitstekende sterkte en corrosiebestendigheid | Duur, moeilijk te bewerken |
Ti6Al4V | Hoge sterkte-gewichtsverhouding, uitstekende biocompatibiliteit, goede corrosiebestendigheid | Duur, zeer reactief, vereist inerte gasomgeving |
Maragingstaal (1.2709) | Hoge sterkte, taaiheid, gemakkelijk te bewerken | Corrosiegevoelig, warmtebehandeling vereist |
Kobalt-chroom (CoCr) | Hoge slijtage- en corrosiebestendigheid, biocompatibel | Duur, moeilijk te bewerken, beperkt verkrijgbaar |
Hastelloy X | Uitstekende sterkte bij hoge temperaturen, corrosiebestendigheid | Duur, moeilijk te bewerken, beperkt verkrijgbaar |
Koper (Cu) | Hoge thermische en elektrische geleidbaarheid, gemakkelijk om mee te werken | Hoge reactiviteit, oxidatierisico, moeilijk te verwerken met LPBF |
Aluminium 6061 | Hoge sterkte-gewichtsverhouding, goede corrosiebestendigheid, lichtgewicht | Lagere sterkte vergeleken met andere aluminiumlegeringen, niet zo hittebestendig als Inconel of Titanium |
Gereedschapsstaal (H13) | Hoge hardheid, slijtvastheid, taaiheid, goed voor gereedschapstoepassingen | Vatbaar voor barsten tijdens verwerking, vereist warmtebehandeling |
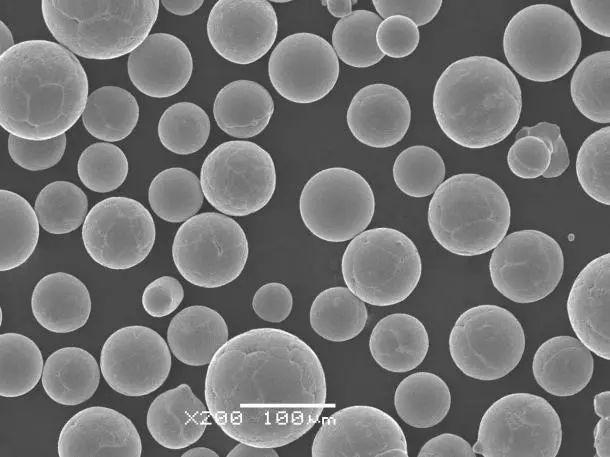
FAQ's
Om je meer inzicht te geven in Laser Powder Bed Fusion, hebben we een lijst samengesteld met veelgestelde vragen en gedetailleerde antwoorden.
Vraag | Antwoord |
---|---|
Wat is Laser Powder Bed Fusion (LPBF)? | LPBF is een additief productieproces waarbij een laser wordt gebruikt om metaalpoeder laag voor laag samen te smelten tot een massief object. |
Wat zijn de gebruikelijke materialen die worden gebruikt in LPBF? | Gangbare materialen zijn roestvrij staal, aluminiumlegeringen, titaanlegeringen, Inconel, maragingstaal en kobalt-chroom. |
Waarin verschilt LPBF van andere additieve productiemethoden? | LPBF is uniek in zijn vermogen om metalen onderdelen met hoge resolutie en ingewikkelde geometrieën te produceren, waarbij een laser wordt gebruikt om het poeder te versmelten. |
Wat zijn de voordelen van het gebruik van LPBF voor productie? | Voordelen zijn flexibiliteit in ontwerp, materiaalefficiëntie, hoge precisie, snelle prototyping en de mogelijkheid om sterke, functionele onderdelen te maken. |
Wat zijn de beperkingen van LPBF? | Beperkingen zijn onder andere hoge kosten, beperkingen in bouwgrootte, vereisten voor nabewerking en de behoefte aan gespecialiseerde materialen. |
Hoe kies ik het juiste metaalpoeder voor LPBF? | Houd rekening met factoren zoals de verdeling van de deeltjesgrootte, morfologie, chemische samenstelling, zuiverheid, stroombaarheid en reactiviteit. |
Welke sectoren profiteren het meest van LPBF? | Industrieën zoals lucht- en ruimtevaart, automobiel, medisch, tandheelkundig, gereedschap, energie en elektronica hebben veel baat bij LPBF. |
Is LPBF geschikt voor massaproductie? | Hoewel LPBF uitstekend is voor prototyping en kleine tot middelgrote productieruns, is het misschien niet de meest kosteneffectieve optie voor massaproductie. |
Welke invloed heeft de kwaliteit van het metaalpoeder op het uiteindelijke onderdeel? | De kwaliteit van het metaalpoeder beïnvloedt de mechanische eigenschappen, de oppervlakteafwerking en de algemene prestaties van het uiteindelijke onderdeel. |
Kan LPBF onderdelen van meerdere materialen produceren? | LPBF wordt voornamelijk gebruikt voor onderdelen die uit één materiaal bestaan, maar er zijn ontwikkelingen op het gebied van multimateriaal printtechnologieën. |
Conclusie
Laserpoederbedfusie is een krachtige additieve productietechnologie die ongeëvenaarde ontwerpvrijheid, materiaalefficiëntie en de mogelijkheid biedt om hoogwaardige metalen onderdelen met complexe geometrieën te produceren. Hoewel LPBF zijn uitdagingen en beperkingen kent, blijft het zich ontwikkelen, waardoor het een steeds haalbaardere optie wordt voor een breed scala aan toepassingen in verschillende industrieën. Of u nu een prototype wilt maken van een nieuw ontwerp, aangepaste onderdelen wilt produceren of de mogelijkheden van additive manufacturing wilt verkennen, LPBF is een technologie die het overwegen waard is.
Naarmate het gebied van additive manufacturing zich verder ontwikkelt, kunnen we verdere verbeteringen in de LPBF-technologie verwachten, waaronder nieuwe materialen, grotere bouwgroottes en verbeterde procesbesturing. Op de hoogte blijven van deze ontwikkelingen is de sleutel tot het benutten van het volledige potentieel van LPBF in uw productieactiviteiten.
Over 3DP mETAL
Productcategorie
NEEM CONTACT OP
Vragen? Stuur ons nu een bericht! Na ontvangst van uw bericht gaan we met een heel team uw aanvraag verwerken.